In industries such as healthcare and electronics, where part size and precision are critical, micro injection molding is playing an integral role – providing a key support for innovation in these industries by enabling the precise manufacture of extremely small, highly accurate parts.
This guide provides an in-depth look at microinjection molding: first, what it is; second, a detailed look at the core differences between it.
Understanding Micro Injection Molding
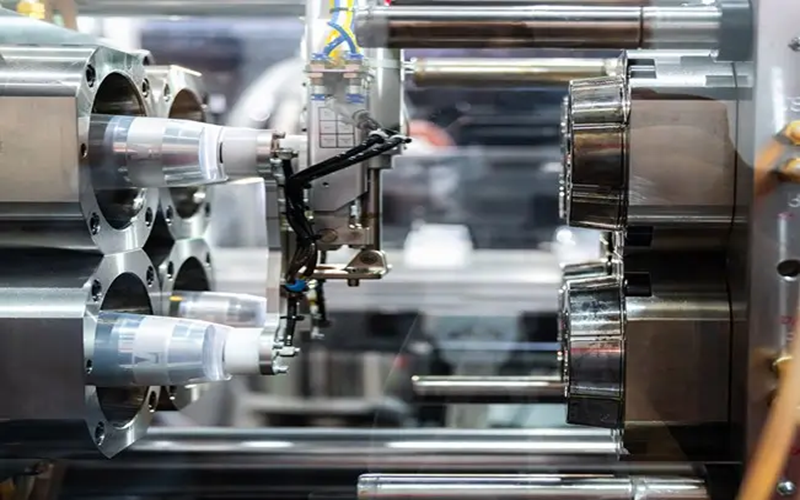
Micro injection molding is a specialized manufacturing process designed to produce very small parts with high precision and tight tolerances. This technique is capable of creating components with complex features and dimensions often measured in millimeters.
What sets micro injection molding apart is its ability to maintain the integrity of intricate designs while enabling high-volume production.
The components produced through this method can weigh less than one gram and may include micro holes and a thin wall, with a small part of the process beginning with a precise amount of resin being melted and injected into a mold.
This molding process integrates advanced technologies such as CNC and EDM machining, which are crucial for achieving micron-level tolerances.
With its broad adaptability to materials—ranging from thermoplastic resins to special composite plastics materials—micro injection molding and plastic injection molding meet diverse performance requirements across different scenarios.
Another critical aspect of micro injection molding is the stringent control over parameters such as temperature and pressure during production. This control is essential for ensuring consistent product quality.
The molds used are typically made of high-strength alloy materials and undergo precision machining to ensure both mold longevity and the consistency of molded parts, including over molding.
This combination of advanced technology and meticulous control makes micro injection molding an ideal choice for producing small, precise components using micro tooling and automation.
Micro Plastic Injection Molding vs Conventional Injection Molding
While both micro molding and traditional injection molding involve the design, prototyping, and molding of thermoplastics, the differences between the two are significant. One of the primary distinctions lies in the level of precision required:
- Tooling design in micro injection molding is highly intricate.
- Steel tolerances must be maintained within a few microns.
- This precision is necessary to produce micro-sized parts.
- These parts must meet the stringent requirements of industries such as healthcare and electronics.
Another key difference is the placement of the gate location in the mold, which is crucial for ensuring the strength and uniform flow of the injected material.
In traditional injection molding, the placement of the gate is important, but in micro injection molding, it becomes even more critical due to the small scale and tight tolerances involved. This separation in gate placement significantly impacts the overall quality of the molding process.
Additionally, material behavior in micro injection molding differs significantly due to the small scale, necessitating precise control over temperature and injection pressure.
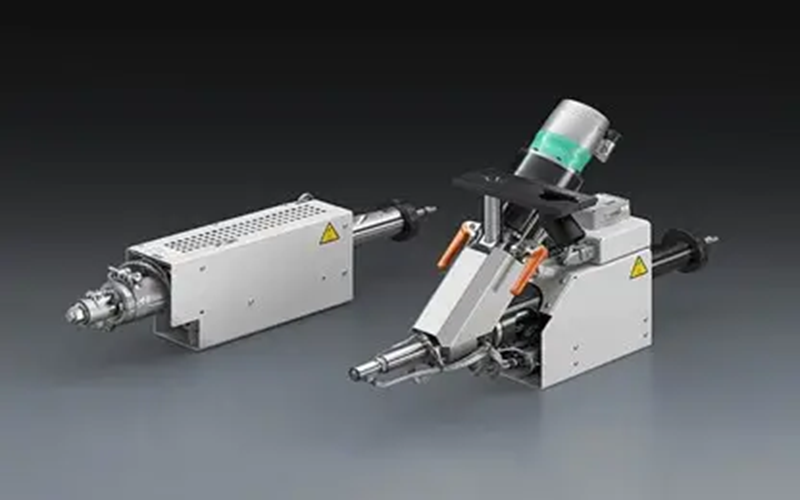
The Critical Role of Precision in Micro Molding
Precision is the cornerstone of successful micro molding. This process is particularly effective in producing small parts with high precision and accuracy, which is essential for industries like electronics and healthcare.
In these fields, even the slightest deviation from specified dimensions can lead to part failure or system malfunction. Therefore, achieving tight tolerance micron tolerances is not just a goal but a necessity in micro injection molding.
The focus on precision extends to every aspect of the molding process, from the initial design to the final production. High precision ensures that the parts produced are consistent, reliable, and meet the exacting standards required by various industries.
This high degree of accuracy is achieved through the integration of advanced technologies such as CNC and EDM machining, which allow for the creation of molds and parts with extremely tight tolerances.
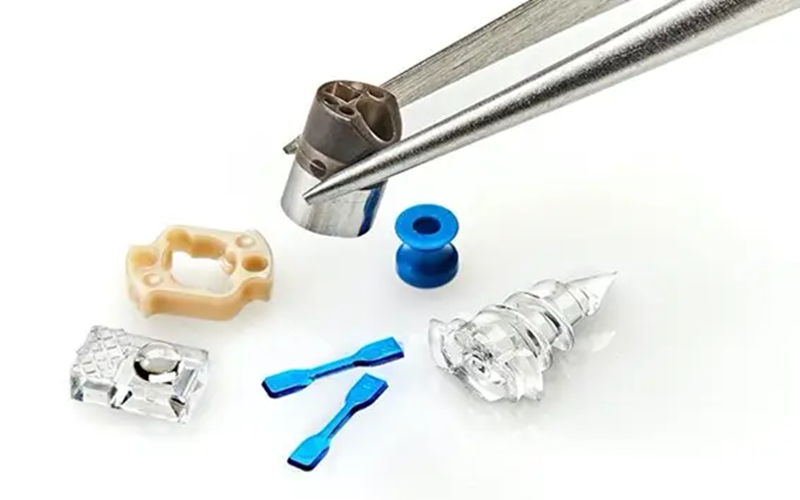
Specialized Equipment for Micro Injection Molding
Micro injection molding requires:
- Specialized machinery that provides higher precision and accuracy than conventional methods.
- An injection unit integrated into the machine specifically designed for micro injection molding.
- Precise control over temperature and injection pressure due to the different material behavior at a small scale.
The precision in micro molding relies heavily on the design and fabrication of ultra-precision molds that can maintain tolerances as tight as single microns. A robust Quality Management System (QMS), such as ISO 9001, is essential for ensuring the reliability and quality of injection molding tools.
The production environment for micro injection molding often requires stricter cleanliness standards compared to traditional injection molding.
Steps in the Micro Injection Molding Process
The micro injection molding process involves several critical steps, starting from design and prototyping, moving through tooling and mold development, and finally reaching production and quality control.
Each stage is meticulously planned and executed to ensure the successful creation of micro-sized parts that meet the highest standards of precision and quality.
Design and Prototyping
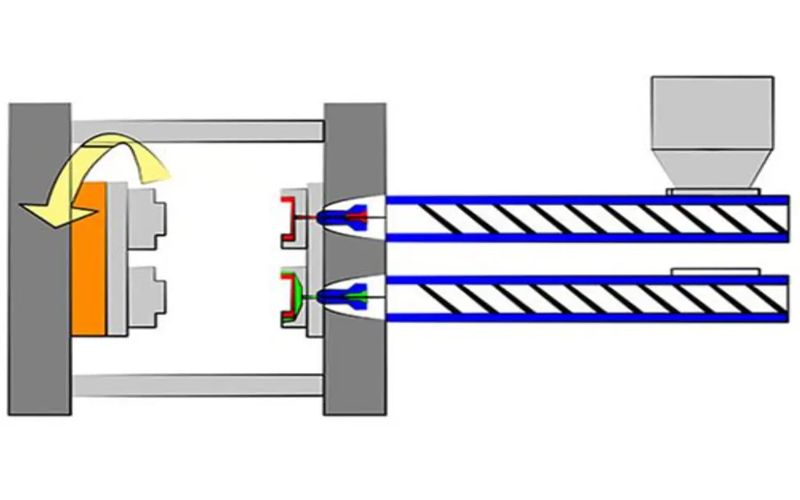
The design and prototyping stage in micro injection molding is crucial for ensuring the success of the entire process. Effective design considerations must account for multiple details, such as:
- Optimizing runner dimensions to reduce material waste and pressure loss.
- Precisely determining gate locations to avoid defects like weld lines.
- Ensuring uniform flow of molten material in multi-cavity molds to enhance part consistency across cavities.
Prototype fabrication holds irreplaceable value in micro injection molding. It enables functional testing and performance validation of designs through physical models before large-scale production. For instance, it can:
- Assess the filling effect of microstructures
- Evaluate the compatibility of materials and processes
- Identify design flaws in time for iterative optimization
The micro-injection molding module is equipped with an 8 mm injection screw, designed for producing extremely small injection volumes weighing less than 1 gram.
This precision screw ensures stable injection of minute material quantities under high-pressure conditions, providing core assurance for the molding accuracy of millimeter- or even micrometer-scale parts.
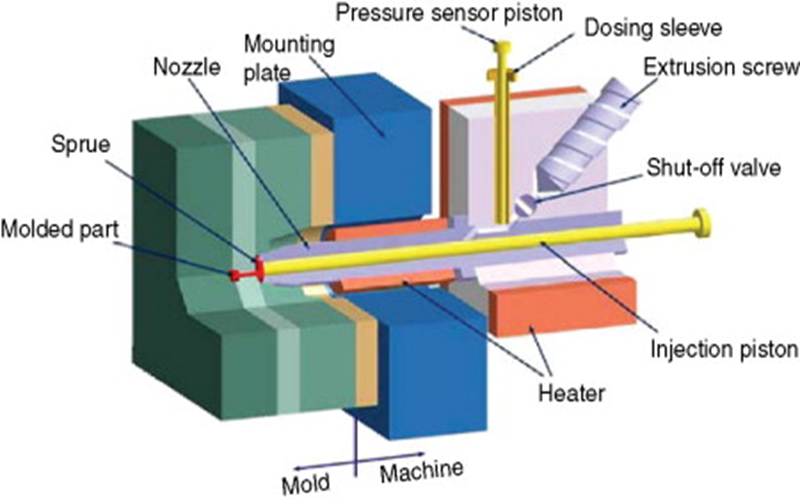
In micro-molding projects, mold design and maintenance are critical to risk reduction. The industry generally prioritizes an in-house development model to meet micron-level precision requirements, allowing for more direct control over mold design details and maintenance standards.
The mold manufacturing process strictly adheres to the “design-first” principle, ensuring consistency between the mold and design requirements from the outset.
Micro-injection mold fabrication demands extremely high precision and technical expertise. It requires specialized equipment such as high-precision CNC machining centers and electrical discharge machines, combined with precision measurement tools like coordinate measuring machines, including insert molding techniques.
Interchangeable cavity molds, with their modular design, enable rapid cavity replacement without disassembling or adjusting the entire mold, significantly reducing switchover time for multi-variety products and improving the efficiency of connectors.
Production and Quality Control
Quality control is a critical component in micro-injection molding, especially because micro-molded parts are often used in fields with extremely high precision requirements. Stringent quality control measures ensure that every part precisely meets rigorous specification standards.
Effective quality control maintains consistent quality across every batch through real-time monitoring and adjustments across the entire production process.
Before full-scale production begins, the first article undergoes CT scanning. This high-precision inspection method provides a comprehensive view of the part’s internal structure and external dimensions, accurately verifying compliance with design drawings and checking for critical features, internal defects, and detail.
Implementing strict quality control processes minimizes the production of defective parts from the outset, enhancing customers’ satisfaction through stable and reliable product quality.
Applications of Micro Injection Molding
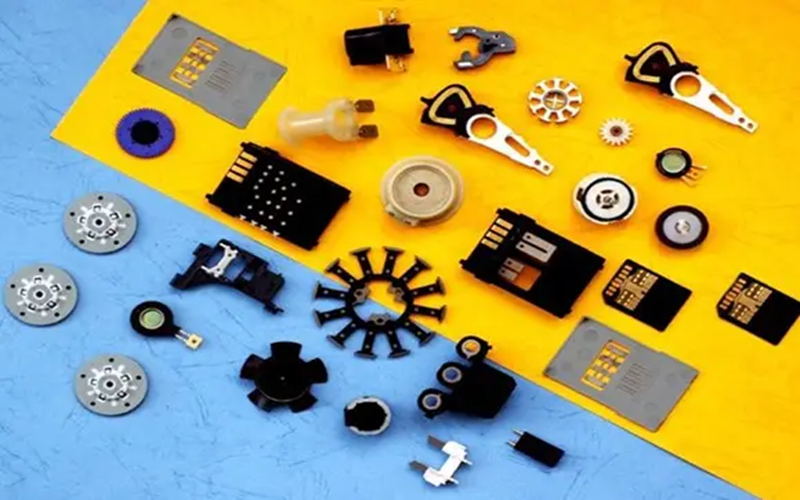
Micro injection molding has a wide range of applications across various industries. It is particularly suited for fields that require high-precision components, such as healthcare and Medical devices.
In these industries, even the smallest deviations in part dimensions can lead to significant issues, making the precision offered by micro injection molding invaluable.
Effective quality control measures are critical pillars for ensuring the stability and reliability of micro-molded part production. By establishing standardized inspection processes, including:
- Incoming raw material checks
- In-process online dimensional inspections
- Comprehensive performance validation of finished parts consistent quality is maintained across every batch. This makes micro injection molding ideal for producing high-precision parts required in demanding applications.
Benefits of Micro Injection Molding
Micro injection molding offers several benefits, including:
- Cost optimization at scale.
- Precise control of injection parameters and automated production processes that can reduce the defect rate to below 1%.
- Shortening the product development cycle from design finalization to mass market launch by over 30%, significantly enhancing market responsiveness.
The rapid production cycle of micro-injection molding demonstrates strong practical value:
- Single-cycle production times can be compressed to seconds.
- When paired with multi-cavity mold designs, it enables the manufacture of large quantities of components in a short time.
- This process is more cost-effective than traditional precision machining methods.
- It reduces per-unit manufacturing costs by 40%-60%.
Additionally, high-precision metering systems and optimized mold runner designs achieve material utilization rates above 95% at high speed, significantly reducing material waste.
Selecting A Micro Injection Molding Partner
Selecting the right micro-injection molding partner is critical to project success. Their expertise directly impacts overall efficiency from mold development to mass production, determines whether the final product meets stringent quality standards, and influences project cost control and market competitiveness.
A partner’s mastery of complex molding details is paramount, including precise control over material flow characteristics during micro-part molding and proficient application of specialized processes.
Choosing a supplier with both professional design capabilities and in-house custom mold packaging manufacturing ensures seamless integration from product design optimization to mold fabrication.
Regular feedback on production data and collaborative optimization of process parameters enable rapid responses to production issues, laying a solid foundation for long-term mutual success as an engineer and manufacturers.
Summary
Micro injection molding represents a significant advancement in the field of manufacturing, offering unparalleled precision and efficiency for creating small, intricate parts.
Throughout this guide, we have explored the fundamental principles, critical role of precision, specialized equipment, and detailed process steps involved in micro injection molding.
The benefits of micro injection molding are clear, from cost optimization and rapid production cycles to high material utilization rates. By selecting the right partner, businesses can achieve superior outcomes and maintain a competitive edge in their respective markets.
Embrace the potential of micro injection molding and unlock new possibilities in small part manufacturing.
Frequently Asked Questions
What is micro injection molding?
Micro injection molding is a precise manufacturing technique that creates small parts with tight tolerances, making it ideal for applications in healthcare and electronics. This method ensures high-quality production of miniature components.
How does micro injection molding differ from traditional injection molding?
Micro injection molding differs from traditional injection molding primarily in its need for higher precision and tighter tolerances, often within a few microns, as well as more complex gate placement and stricter control over temperature and injection pressure. These factors make it particularly suited for manufacturing small and intricate parts.
Why is precision so critical in micro injection molding?
Precision is critical in micro injection molding because any minor deviations in part dimensions can result in failures in high-precision industries like electronics and healthcare. Achieving micron-level tolerances is necessary for ensuring reliable and consistent performance.
What specialized equipment is needed for micro injection molding?
Micro injection molding requires specialized machinery with an injection unit tailored for precision, along with ultra-precision molds that maintain tolerances of up to a single micron. This ensures high accuracy and quality in small-scale production.
What are the benefits of micro injection molding?
Micro injection molding offers significant advantages such as cost efficiency, quick production cycles, and high material utilization, making it perfect for producing intricate small components with reduced defects and shorter development timelines.