Choosing the right manufacturing method is crucial in 21st century business management. As technology advances, each manufacturing method has its own advantages and disadvantages, bringing different conveniences and challenges to manufacturers.
Today, 3D printing and injection molding are the two main methods for manufacturing complex plastic parts. Although they each have their own advantages and disadvantages, they are now seen as complementary rather than competing.
Next, we will talk about when 3D printing is appropriate, when injection molding is more suitable, and how to combine these two technologies to improve production efficiency.
3D Printing
What is 3D Printing?
3D printing is a type of rapid prototyping technology, also known as additive manufacturing. It is a technology that builds objects by printing layer by layer based on a digital model file.
Using bondable materials such as powdered metals or plastics, 3D printing creates physical objects through an additive process, allowing for complex designs and detailed structures to be produced efficiently.
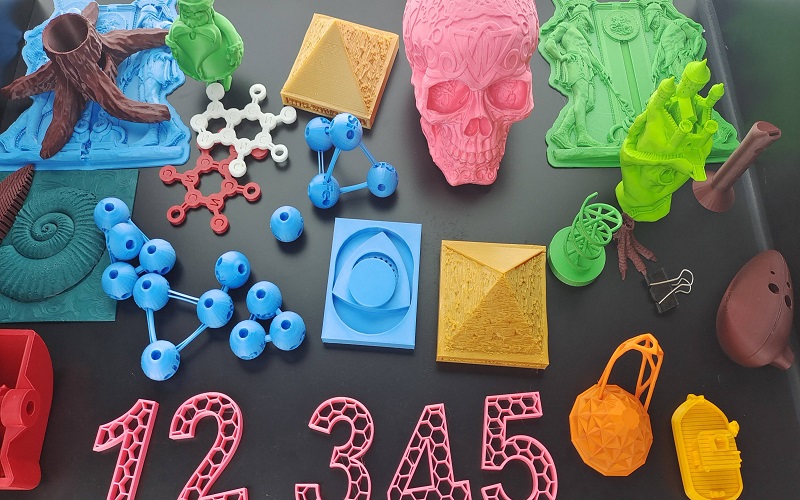
Advantages of 3D Printing
There are several different benefits one can appreciate about the practicality of 3D printing in the production processes.
Design flexibility: First serves the argument about the advantage of 3D printing technology which is its ability to make different geometries and mass employ molding of complex shapes with simple means and circumvent elaborate tooling.
Such enhancement adds more possibilities in the way design and alterations are performed.
Rapid prototyping: The technology also enables very efficient conversion of the design stage into its physical model, which ensures visual results during the product development projects in a shorter period of time so that such exercises can be modified at the right time.
Low upfront costs: Another factor that needs to be highlighted is the relative low cost which eventually the user incurs during initial investments with regard to 3D printing, as there is no need to produce expensive tooling thus it can be appropriate for low volume or single production run orders.
Material diversity: The 3D technology has the capability expansion from use of a limited range of materials such plastics, metals, ceramics, resins to utilizing wider arrays of materials means therefore many objects can be constructed using the technology.
Easy to iterate and test: Its capability enables fast testing and modifications to designs, with the benefit of 3D printing providing an opportunity to quickly print an object to see how it works, allowing the designer opportunity to modify based on actual performance. Utilizing these advantages can save time and money, and improve subsequent iterations of product design.
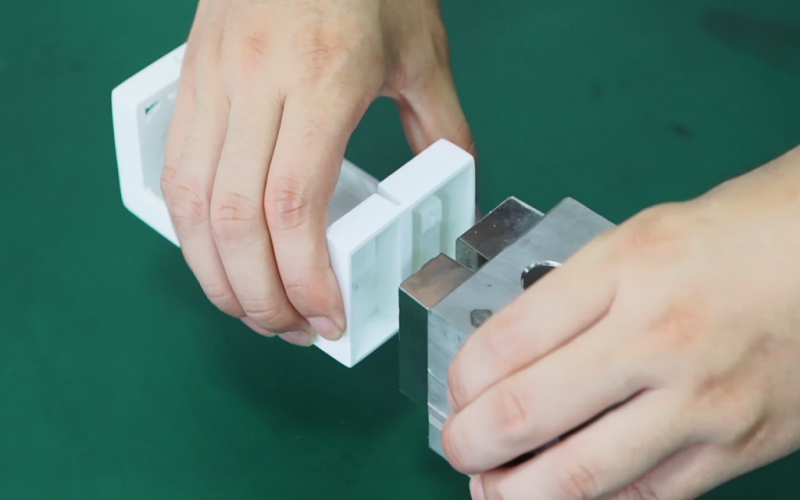
Injection Molding
What is Injection Molding?
Injection molding is a manufacturing technology that forms products by injecting molten material into a mold and cooling and solidifying it.
This method combines injection and compression molding processes and is suitable for mass production, especially for products with complex shapes.
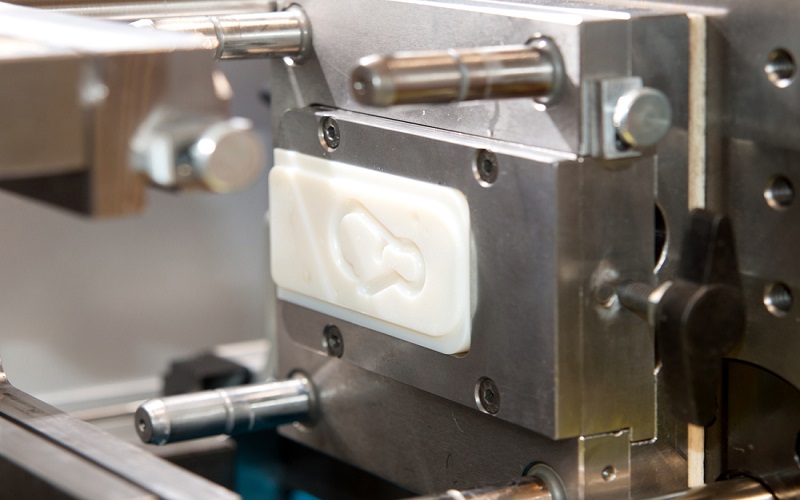
Although the mold making cost is high, the unit production cost is low, the production speed is fast, the efficiency is high, and it can be automated. Therefore, injection molding is widely used to manufacture precise and complex parts.
Advantages of Injection Molding
Injection molding has become a very popular process in manufacturing because of the the technical advantages it offers.
First, it is the best process for mass production, since it allows for the quick manufacture of thousands of identical parts, at a much lower cost per part in high volumes of production; this notwithstanding the molds for injection molding are expensive – this is the basis of much of its cost efficiency.
Second, the materials suitable to injection molding are numerous and many possess high strengths and other properties (like polypropylene, polyethylene and nylon); many of these material can meet high performance requirements. A part weight, flexibility and durability can be adjusted depending on which materials or additives are selected.
In addition, injection molding offers a high precision and repeatability which makes it ideal for producing complex parts. Injection molding also makes it easy to add details and create strengthen in parts giving it an edge over other processes.
Overall, injection molding is an efficient, cost-effective, and accurate process that is well suited for high-performance materials and mass production requirements.
3D Printing vs Injection Molding: Application Scenario
Applicable Scenarios of 3D Printing
3D Printing is exceptionally applicable in circumstances listed below given its potential for adaptability and customization:
1.Prototyping:
- At the beginning of product development, 3D printing enables rapid production of models from design concepts. This allows designers and engineers to provide quick feedback and iterate, addressing problems early and reducing time to market.
2.Customized Products:
- 3D printing is favorable for creating unique products or short runs of production. This is especially helpful for creating custom medical products, jewelry, and artistry where part fabrication costs related to molds can be avoided, and customization for an individual is much easier.
3.Low-Volume Production:
- For the production of low quantities of products with a complex shape, 3D printing provides a cost benefit for both complexity and low quantities. 3D printing is also useful for providing a way to test the market or pursue short runs of production for intro products.
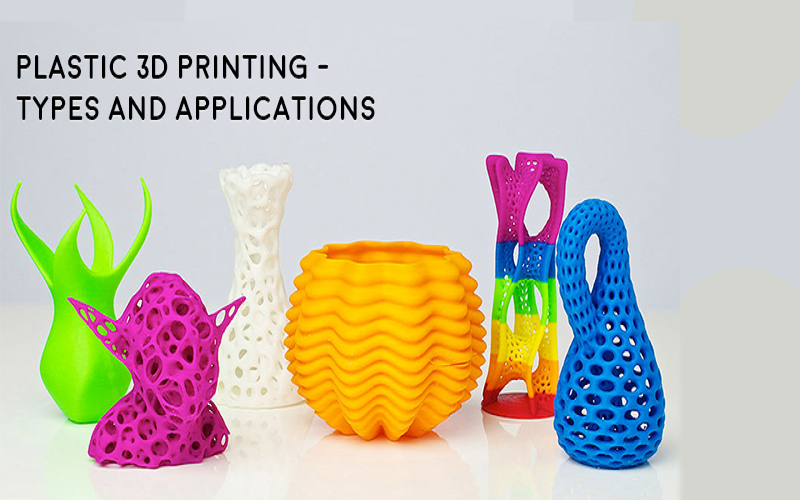
Applicable Scenarios of Injection Molding
Injection molding is particularly effective in the following situations due to its efficiency and low unit cost:
1.High Volume Production:
- Injection molding is ideal for producing large quantities of the same product. Although making the mold can be expensive, the cost per unit drops significantly in mass production. This method is commonly used for consumer goods, automotive parts, electronics, and more.
2.Precision Manufacturing:
- Injection molding offers high precision and consistency, making it perfect for products with strict size and quality requirements. It’s well-suited for items like medical devices, electronic components, and precision mechanical parts.
3.Standardized Products:
- For products with uniform shapes and sizes, injection molding ensures consistent quality. Once the mold is made, it can produce identical products throughout the production run, which is ideal for industries needing reliable quality and repeatability, such as packaging, household goods, and industrial parts.
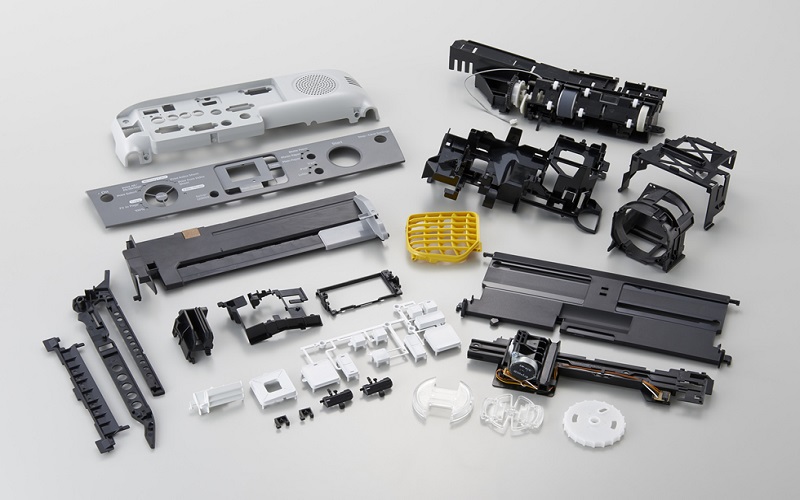
3D Printing vs. Injection Molding: What Sets Them Apart
3D printing and injection molding represent distinct manufacturing approaches that differ in their respective processes and uses.
Within the context of manufacturing process:
3D printing utilizes the additive method, functioning similarly to how building blocks are stacked on top of one another to make a model. The additive process allows anyone to create a real object directly from a computer design, and the production of complex shapes that would normally require additional molds can easily be performed without the additional cost or time of producing molds.
In injection molding, the system consists of formulating a mold and injecting melted material into this mold. After several minutes, the mold will have cooled, and the material will have solidified uniformly to provide the same product every time. The process offers an extremely precise and consistent result each time it is used, making it advantageous for generating products with uniformity in large quantities.
Regarding production speed:
3D printing is considered relatively slow in the embodiment of larger models or larger reflection arrangements, as each layer of the product must be printed at a time. However, it is advantageous for producing a few samples or prototypes relatively quickly, particularly because design elements can quickly be changed and implemented into the prototype with ease.
Injection molding offers a significantly efficient approach, as the bulk of the injection mold can take some time, but once the mold is completed, all molds are relatively quick, making it ideal for manufacturing in bulk.
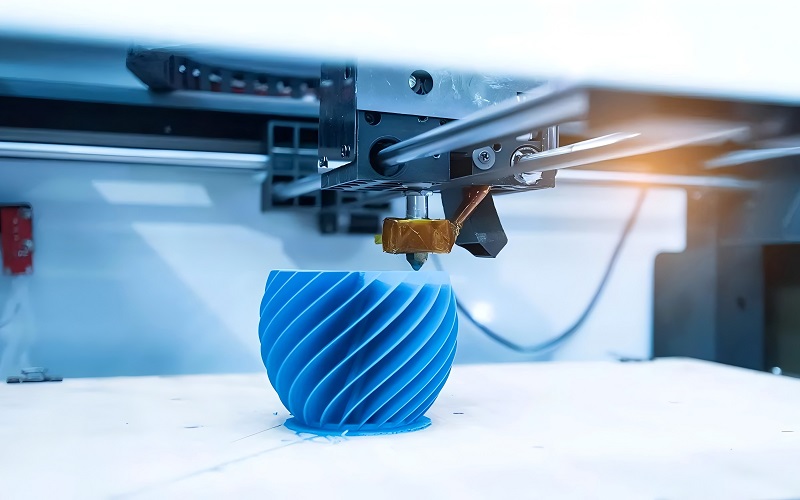
In discussing cost structure:
The initial cost of an injection mold is very high, and most of the expense in the production process is concentrated in the up-front manufacturing of the mold. However, once the mold is made, subsequent products can be produced in large quantities at very low cost.
3D printing does not require the use of molds, which results in lower upfront costs. However, the overall cost can be higher than injection molding due to the consumption of materials and time.
3D printing is particularly well suited to the production of complex, personalized products because of its ability to quickly adapt to changes in design and reconfigure the product in a short period of time. This flexibility is far greater than injection molding, which takes longer and costs more with each adjustment.
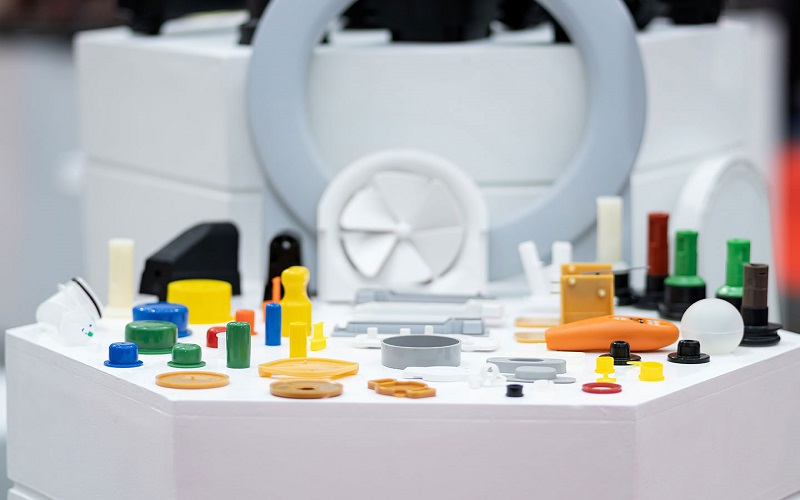
How to Choose: Injection Molding or 3D Printing?
Choosing between 3D Printing and Injection Molding involves weighing a number of considerations in order to establish which of these methods would be most appropriate.
Production Volume
In the case that a lot of identical examples should be produced, Injection Molding is on the whole the better option.
It is meant for so-called large scale manufacturing since the price for each item produced in bulk is kept on the lower side even though the molds are expensive to produce.
For small batch production or custom products, for example, 3D Printing is more reasonable. It is great for manufacturing a few pieces or producing prototypes rather quickly without using any molds.
Design Complexity
In case you need to make a product that has such a unique outer design or such unusual inner parts, then 3D Printing is mostly the most suitable choice. Building a structure in layers without the use of special molds when called for can easily accommodate complicated shapes.
And even though Injection Molding can also produce complex shapes, the ability always comes with detailed expensive molds.
So while weighing in on this debate, 3D printing vs injection molding for complex parts, 3D printing for the most part takes it.
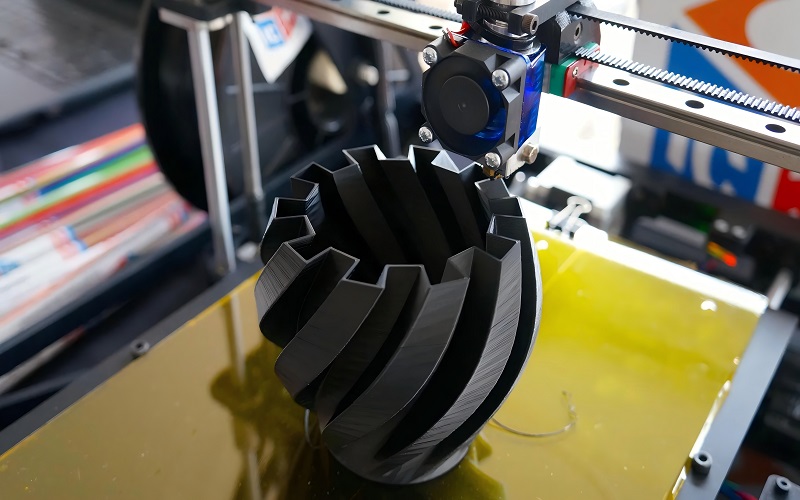
Cost
Injection molding has high upfront costs because making the molds is expensive, but it’s cheaper per unit for large quantities.
3D printing doesn’t require molds, but it can be more expensive per item, especially for large runs.
However, for smaller or more customized orders, 3D printing might be more cost-effective.
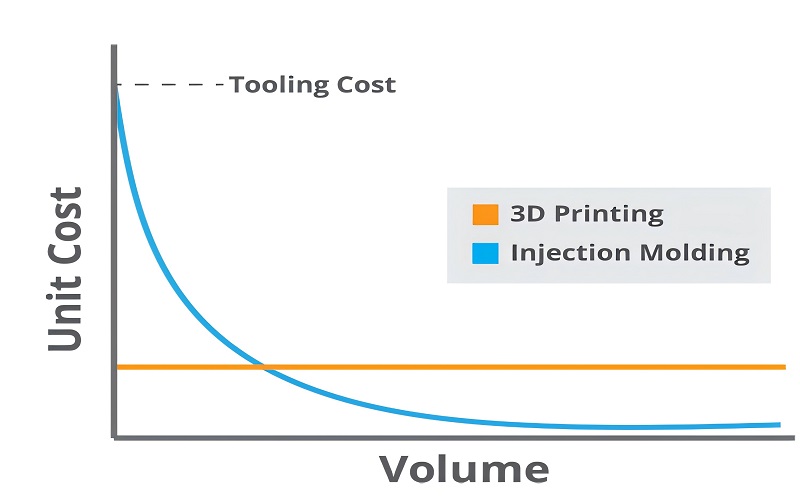
Production Velocity
Overall, during injection molding,once your molds are complete, products can be made at a faster rate: this is very useful in mass production of the particular product.
3D Printing, however, is not as effective since it is time-consuming especially on large and intricate items because it entails constructing the item in layers.
If at any moment you need to release items to the market at high speed and in bulk, then the option of Injection molding would often be quicker.
Design Changes
In case your design needs frequent changes or even the making of its prototypes, then 3D printing is the way to go since it offers you facilities.
Injection molding requires replacing today standard with new one for every more or less substantial shift, which can be rather tedious and costly.
In situations where modification of the design is required very frequently, 3D printing will be more efficient.
Materials and Performance
Different methods use different materials that affect the final product’s quality. Injection molding typically uses strong plastics that are great for durable items.
3D printing can work with a variety of materials, including some high-performance ones.
Comparing 3D Printing vs Injection Molding materials will help you choose the best method based on the material properties you need.
Environmental Impact
Lastly, consider the environmental impact. 3D printing usually produces less waste because it only uses the material needed to build the product. Injection molding can create more waste and requires more energy to make the molds. If being eco-friendly matters to you, think about the environmental impact of 3D printing vs injection molding.
By considering factors like production volume, design complexity, cost, production speed, design iteration, materials and performance, and environmental impact, you can determine whether 3D printing or injection molding is the best choice for your project.
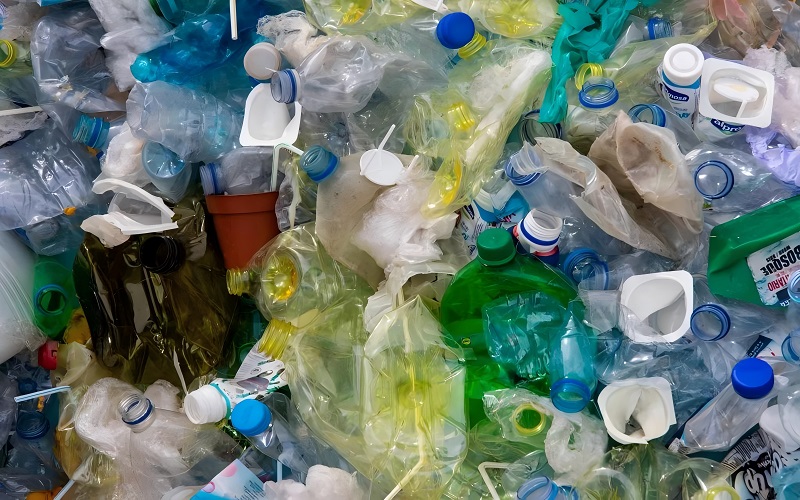
Conclusion
Selecting between 3D Printing and Injection Molding boils down to your project requirements.
Injection molding is generally more cost-effective and efficient for high volumes of production. It is also superior in terms of durability and physical properties. Conversely, 3D printing will be slower and more costly on a per-object basis in mass production situations, but it’s a great choice for complexity and customizing.
It is important to consider your total production volume, your anticipated quality requirements, and your overall budget in order to weigh which method might be best for your next project.
Both options have their own benefits, so once you understand those benefits, you can make the most effective decision.