Low-density polyethylene (LDPE) is a very common plastic in our daily lives.
It can be found in food packaging, plastic bags, containers, and squeeze bottles. Because it is so widely used, people have begun to worry about its safety, especially its possible impact on health and the environment.
So, today we will talk about the characteristics of LDPE, whether its application in the food and medical fields has any safety risks, and its impact on the environment. In addition, we will also look at whether there are better alternative materials than it.
What is LDPE ?
LDPE, in simple terms, is low-density polyethylene, a type of plastic made from ethylene gas.
Its structure is quite special, with many long branches on the molecular chain, which prevents its molecules from being tightly together.
It is widely used in packaging materials that need to be bent or stretched, such as plastic bags, stretch films, and other products.
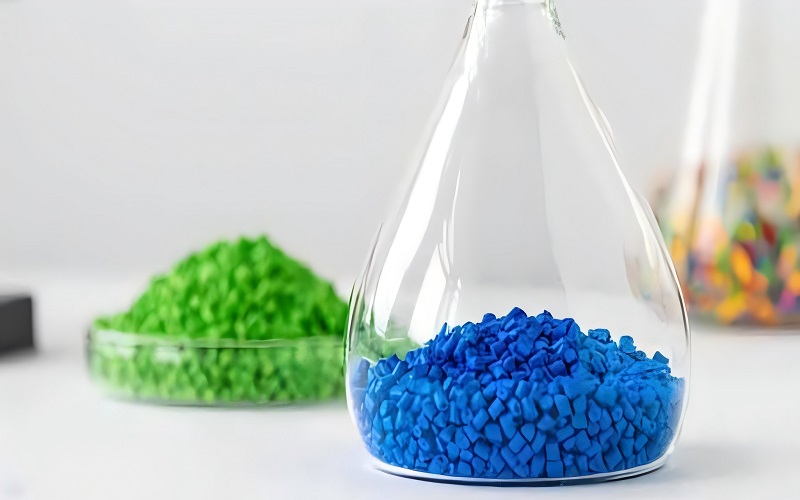
LDPE Properties
LDPE (Low-density polyethylene) is a common plastic that has many unique properties. Here are some of the key properties of LDPE:
- Flexibility
- Low density
- Chemical resistance
- Water resistance
- Heat resistance
- Recyclability
- Low cost
- Transparency
Here are some key properties about LDPE to help you better understand this material.
Property | Description |
Density | 0.910 – 0.925 g/cm³ |
Tensile Strength | 8 – 20 MPa |
Tear Strength | 40 – 80 N/mm |
Elongation at Break | 300% – 700% |
Heat Deflection Temperature | 60 – 80 °C |
Service Temperature Range | -40 °C to 80 °C |
Chemical Resistance | Good (resistant to acids, bases, and salts) |
Recyclability | Recyclable (usually marked as “4”) |
Melt Flow Index | 0.5 – 2.0 g/10 min (varies by specific type) |
How is LDPE Manufactured?
The manufacturing process of LDPE is actually very simple.
It is made through a process called free radical polymerization, which basically reacts ethylene gas under very high pressure (about 1400 to 3000 atmospheres) and high temperature (200-300 °C).
This high pressure environment causes the ethylene molecules to form polymer chains with long chain branches, which is why LDPE is soft and-flexible.
Once the reaction is complete, the LDPE is cooled to a solid state and then cut into small pellets.
These pellets can be made into products such as plastic bags, films, and containers through different processes such as blow molding, injection molding, and extrusion.
Antioxidants or UV stabilizers are sometimes added to enhance performance.
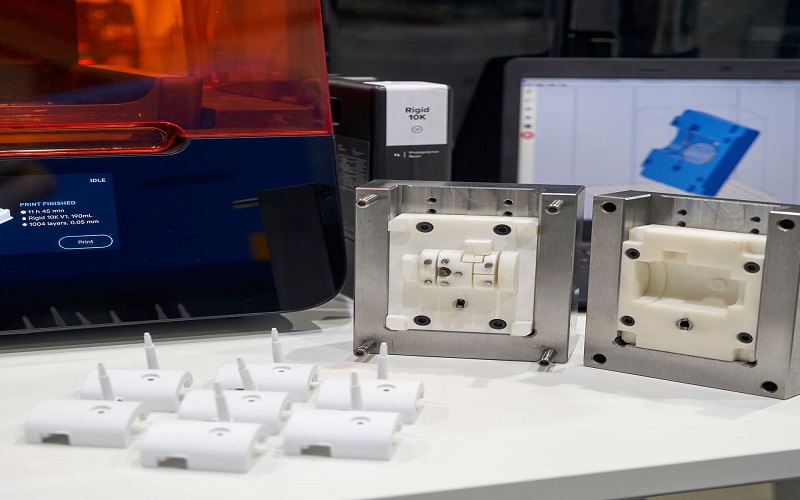
Is LDPE Safe for Food Packaging?
One of the most common questions about LDPE is whether it is safe to use in food packaging, especially now that more and more people are worried about whether plastics will leach harmful substances into food.
FDA Approval and Food Safety Authority
When asked if LDPE (low-density polyethylene) is safe, many people wonder if the FDA (US Food and Drug Administration) has approved it.
The good news is that the FDA has confirmed that LDPE is safe for food packaging. This means that, under certain conditions, LDPE is good for coming into contact with food and does not release anything that could harm us.
Food safety authorities in many countries have similar regulations to ensure that the plastic materials we use meet safety requirements.
Non-Toxic and Chemically Stable
LDPE (low-density polyethylene) is a non-toxic, odorless plastic that is also chemically stable, meaning it won’t leach harmful substances into food.
Compared to other plastics, such as polyvinyl chloride (PVC) or polycarbonate, LDPE doesn’t contain potentially harmful additives, such as bisphenol A (BPA) and phthalates. You may have heard of BPA, which can cause some health problems, but LDPE doesn’t contain this chemical, making it a safer choice for food packaging.
Another reason LDPE is widely used for food packaging is that it doesn’t react with food. Even in hot or humid environments, LDPE doesn’t change with food, making it ideal for direct food contact. You can safely place food in packaging made of LDPE, whether it’s at room temperature, in the refrigerator or in the freezer, and it won’t release harmful substances.
Looking at other plastics, such as polycarbonate, this plastic often contains BPA, which makes many people worry about its safety. There is also polystyrene, which may release styrene when heated and is a possible carcinogen.
In comparison, LDPE’s stability and lack of harmful additives really make it a better choice for food packaging.
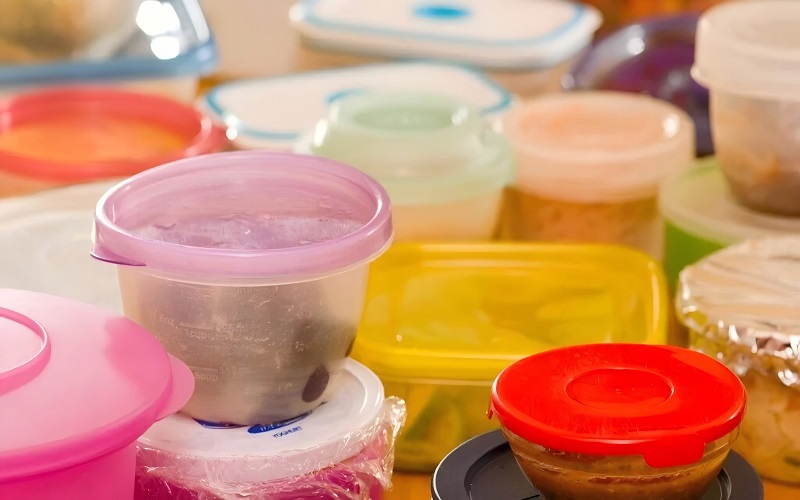
LDPE in the Medical Industry: A Safe and Reliable Material
LDPE is not only used to package food; its safety and stability also make it very useful in the medical field.
For example, medical-grade LDPE is often used in products such as IV bags, medical tubing, and syringes.
Because in a medical environment, it is very important to maintain sterility and non-reactivity, and LDPE meets these requirements. It will not react with drugs or body fluids, which ensures that it is safe in medical applications.
Moreover, this medical-grade LDPE has passed strict safety standards, so it is a very reliable choice in healthcare.
In short, you can rest assured about the application of LDPE in the medical field.
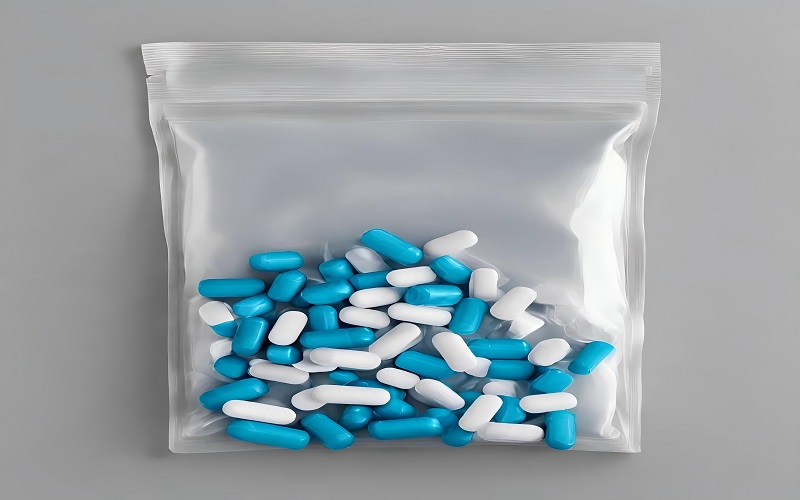
Environmental Impact: Is LDPE Safe for the Planet?
Although LDPE is generally considered safe for human use, its impact on the environment is indeed a big problem. We use a lot of LDPE in disposable products and packaging, resulting in serious waste and pollution.
LDPE and Plastic Pollution
A big problem facing LDPE right now is its contribution to plastic pollution.
We often see LDPE in plastic bags, food packaging and disposable containers, but these things are thrown away after use, resulting in more and more plastic in landfills and oceans.
LDPE is non-biodegradable, which means it can stay in the environment for hundreds of years. Over time, it breaks down into smaller particles called microplastics.
These microplastics can be accidentally eaten by animals and then enter our food chain, which has a big impact on marine ecosystems.
Recycling Challenges
LDPE (low-density polyethylene) can be recycled, and the recycling symbol is usually represented by the number 4.
Although LDPE (low-density polyethylene) can be recycled, it is actually quite troublesome to recycle.
Because LDPE is very soft and easily gets stuck in recycling machines, many places simply do not accept this type of plastic bags and films. Although some places offer special LDPE recycling, such programs are not common, so a lot of LDPE ends up in landfills and may even pollute the environment.
In addition, many people actually don’t know much about the recycling logo of LDPE and don’t know how to recycle these materials correctly.
In general, although LDPE can be recycled, there are many problems in its actual operation, which makes it have a greater impact on the environment.
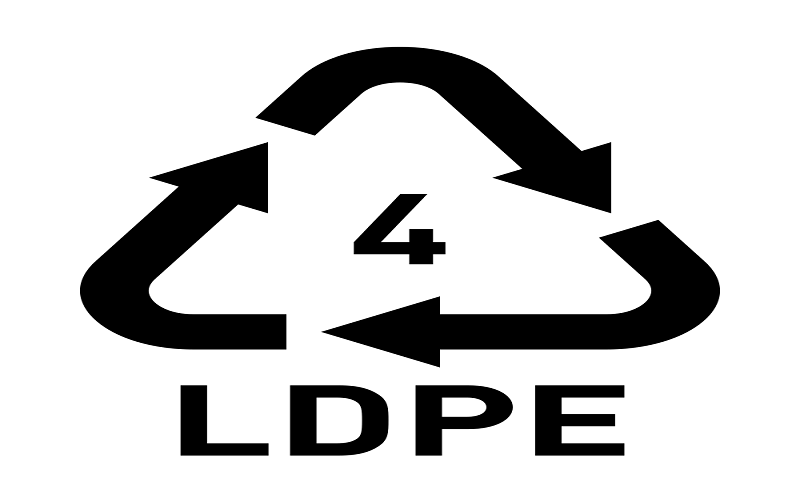
How to Use LDPE Responsibly
In the field of engineering, it is very important to use LDPE responsibly. Here are some simple ways to help us reduce LDPE waste in our engineering projects and reduce its impact on the environment:
- Reduce unnecessary use: If LDPE is not particularly necessary, use as little as possible, especially if more environmentally friendly alternative materials are available. For example, you can use more durable and reusable materials instead of using LDPE only once.
- Optimize design: When designing, find a way to use materials as efficiently as possible. This reduces waste and avoids unnecessary consumption, such as accurate cutting and design, so that LDPE is not wasted.
- Recycling: LDPE waste used in the project must be recycled. The LDPE recycling symbol is number 4. The engineering team needs to know this symbol and send it to a dedicated recycling point to prevent this waste from being dumped directly into the landfill.
- Reuse: In engineering, if LDPE parts are still usable, try using them multiple times instead of using them once and throwing them away. This can extend its service life and reduce unnecessary waste.
- Avoid high-temperature use: If possible, try not to expose LDPE to high temperatures or consider adding some thermal protection during design. This reduces the risk of aging materials and the release of harmful substances.
Exploring Alternative Material to LDPE
As concerns about plastic pollution grow, many industries are looking for alternatives to LDPE. In fact, there are some great options that are gradually becoming more environmentally friendly alternatives. For example:
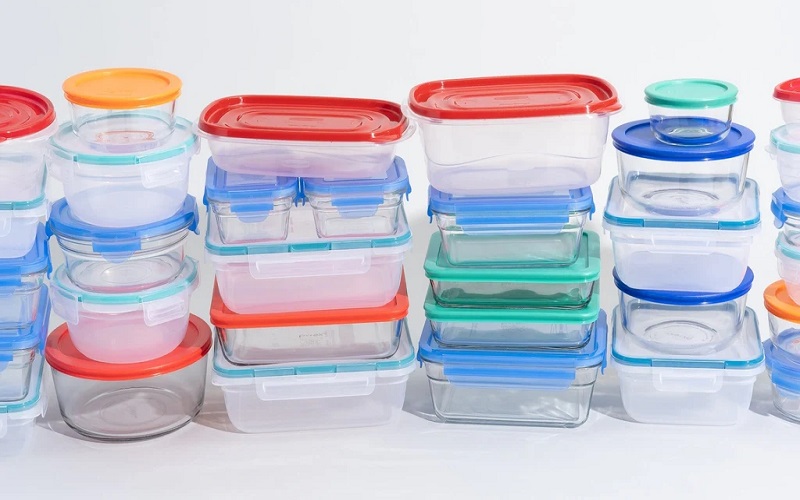
First of all, polypropylene (PP), highly heat-resistant and robust, is suitable for many applications where durability is required. PP is stronger than ldpe and can withstand higher temperatures. It is often used in automotive parts and household appliances.
Compared to LDPE, nylon (polyamide) is much more durable, with excellent abrasion resistance and high strength, making it ideal for mechanical parts and textiles, though it is relatively more expensive.
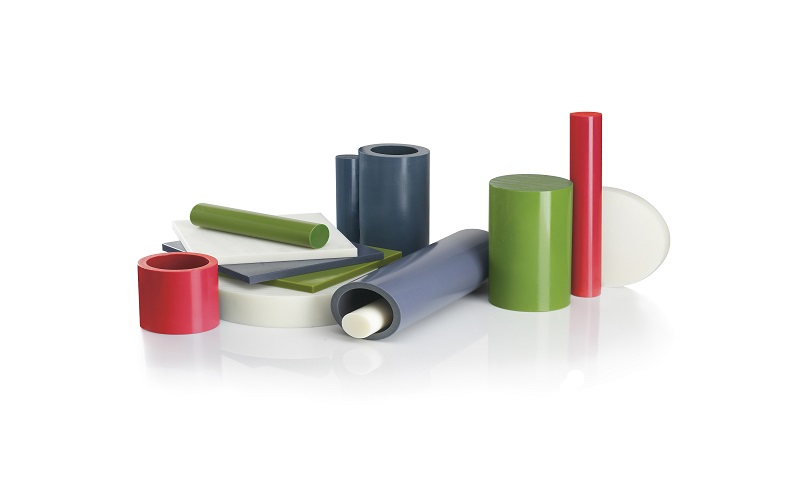
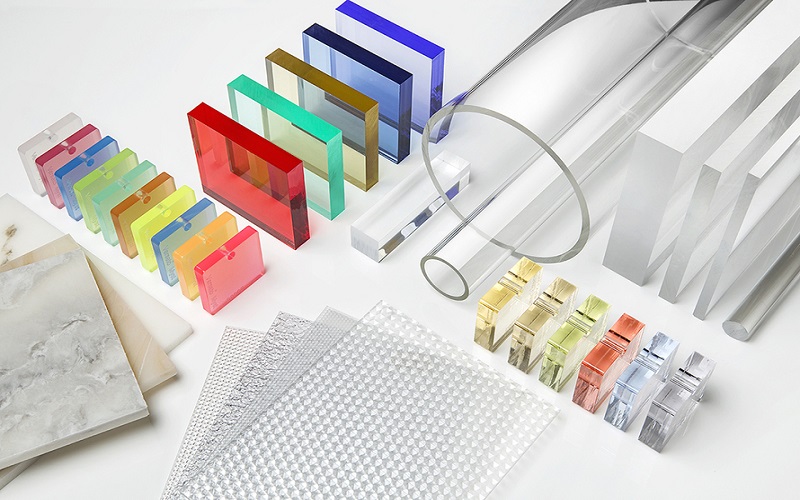
Compared to LDPE, polycarbonate (PC) is much more impact-resistant and highly transparent, making it ideal for optical devices and consumer products, but it’s less environmentally friendly and not as flexible as LDPE.
Finally, there are bio-based plastics, such as polylactic acid (PLA), which is made from renewable resources. While PLA may not be as strong or heat-resistant as LDPE, it is biodegradable, environmentally friendly, and better suited for some short-term applications.
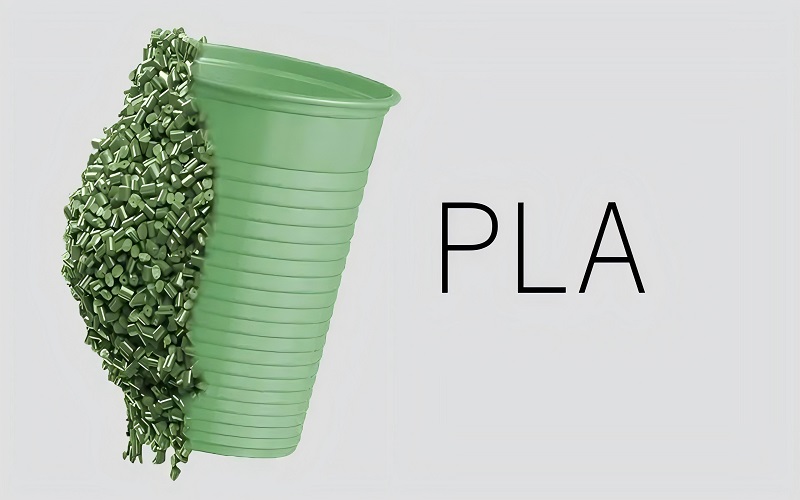
Conclusion: Is LDPE Safe?
LDPE is reliable in terms of safety.
It is non-toxic and chemically stable. It is widely used in food packaging and medical products. It does not release harmful substances in contact with food. It has been FDA-approved.
However, the environmental impact of LDPE cannot be ignored, especially its contribution to the challenge of plastic pollution and recycling.
Therefore, despite the safe use of LDPE, we still have to try to reduce the use of single-use products and choose reusable alternatives to protect the environment.
If you are planning to start a new project using LDPE materials, please contact Otivic! We will provide you with fast, efficient and custom manufacturing solutions to help you save costs.