Plastic often requires joining during processing, and the methods of connection are varied, including threaded connections, adhesive bonding, and mechanical fastening.
Among these, plastic welding stands out for its greater strength and aesthetic appeal.
As the demands for plastic welding techniques continue to rise, mastering this skill has become essential to ensuring the quality and functionality of plastic products.
This article will provide an in-depth introduction to the basic principles, methods, and applications of plastic welding, offering a professional and practical guide for readers unfamiliar with how to weld plastic.
What Is Plastic Welding?
Plastic welding refers to a joining method in which the contact surfaces of two plastic parts are melted through heating, fusing them into a single unit.
This welding technique is only applicable to thermoplastic materials, which can soften when heated, unlike thermosetting plastics that cannot be softened by heat.
The basic principle of plastic welding involves using an external heat source or mechanical motion to melt the plastic contact surfaces, followed by applying pressure to bond the melted plastic tightly together.
Welding can be performed with or without a filler rod. When a filler rod is used, its molten material fills the seam, connecting the two parts through the melted rod.
Without a filler rod, the plastic contact surfaces are heated directly and then pressed together vertically until they fuse seamlessly.
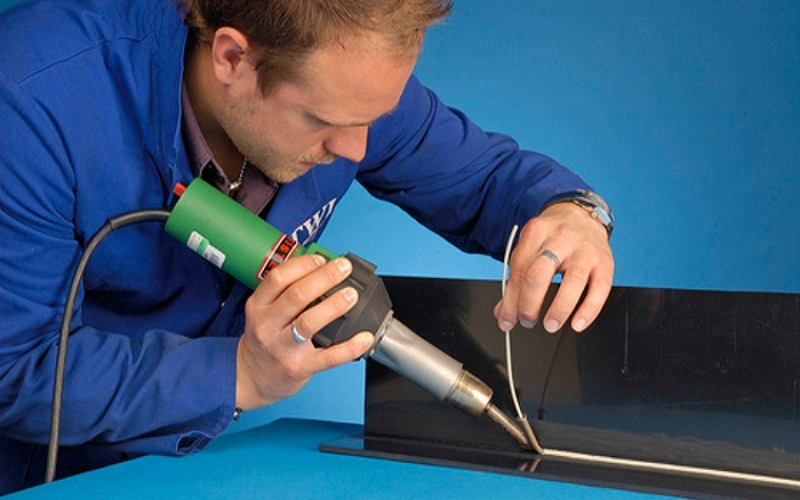
Main Method Of Welding Plastic
Plastic welding methods are categorized into three types: softening by external heat sources, mechanical motion, and electromagnetic effects. Details are as follows:
- External Heat Sources
1.Hot Plate Welding
A flat heating plate melts the surfaces to be joined, then is quickly removed, and the surfaces are pressed together until cooled.
2.Hot Air Welding
Hot air is blown onto the seam, melting a filler rod of the same material as the base plastic, which fuses with the melted plastic to form a weld.
3.Hot Bar and Pulse Welding
These similar techniques press two films together and use instant heat from a hot bar or nichrome wire to complete the weld.

- Mechanical Motion
4.Friction Welding
Heat generated from friction under pressure melts the contact surfaces, which are aligned and held until solidified. It includes linear (for straight or flat seams) and rotational (for circular seams) types.
5.Ultrasonic Welding
High-frequency mechanical energy (20 or 40 kHz ultrasound) melts thermoplastic seams.
Parts are held under pressure, and a transducer converts vibrations into mechanical energy, generating heat through friction to fuse molecules and complete the weld.
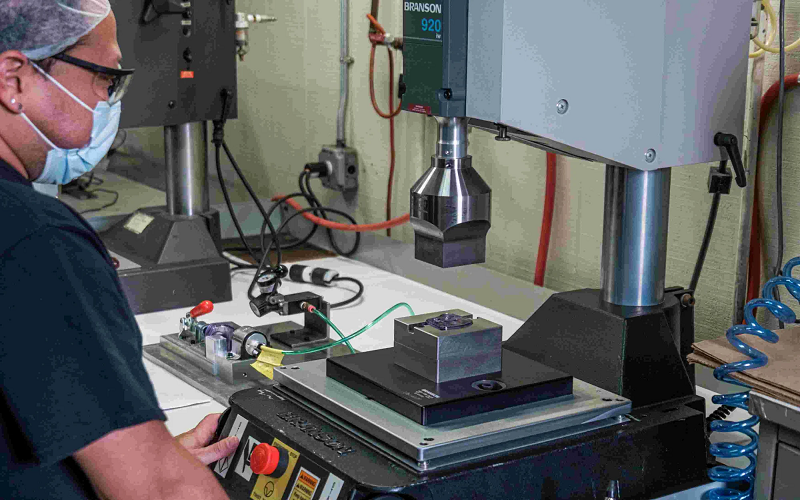
- Electromagnetic Effects
6.High-Frequency Welding
High-frequency induction heating penetrates the plastic, warming embedded inductors or magnetic plastics.
The weld area melts in a rapidly alternating electric field, filling gaps, and is perfected with mechanical assistance.
7.Infrared Welding
Parts are positioned near a heating plate without contact, melted by thermal radiation, then joined and pressed together after the heat source is removed.
8.Laser Welding
Laser beams generate heat to melt plastic contact surfaces, bonding thermoplastic sheets, films, or molded parts together.
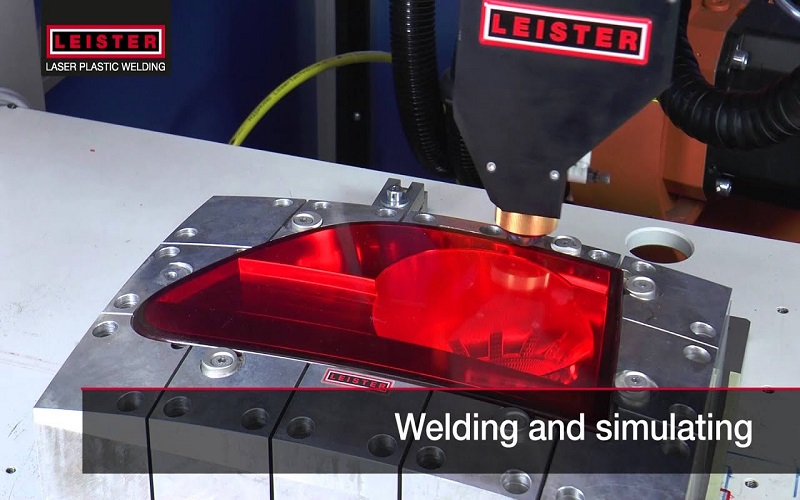
Category | Method | Features | Applications |
External Heat | Hot Plate Welding | Simple equipment, high strength | Large plastic parts with big weld areas |
Hot Air Welding | Lightweight, skill-dependent | Flexible welding scenarios | |
Hot Bar/Pulse Welding | Suitable for thin materials | Thin plastic film welding | |
Mechanical Motion | Friction Welding | Fast, versatile | Straight, circular, or flat seams |
Ultrasonic Welding | Fast, stable, no fumes or flux needed | Small precision parts | |
Electromagnetic | High-Frequency Welding | Efficient, precise | Stationery holders, inflatable items, waterproof clothing and blood bags |
Infrared Welding | No slag, no pollution, high strength | High-precision pipelines (e.g., PVDF, PP) | |
Laser Welding | Fast, precise, easy automation, low cost | Special materials or complex structures |
How To Weld Plastic: Specific Steps
The process of plastic welding generally includes the following steps:
Step 1: Determine Plastic Type and Welding Method
Identify the type of plastic (e.g., thermoplastic or thermoset) and select the appropriate welding technique.
Step 2: Surface Preparation
Clean the surfaces of the plastic parts to be welded, removing dust, grease, or other impurities. This can be achieved using specialized cleaners, alcohol, or sandpaper.
Step 3: Equipment Selection and Setup
Choose the suitable plastic welding tools and equipment based on the method (e.g., hot plate, soldering iron, ultrasonic welder), and adjust the welding parameters, such as temperature, pressure, and duration.
Step 4: Heat and Fusion
Heat the plastic surfaces using tools (e.g., hot plate or soldering iron) until they melt, then press the two parts together, ensuring the molten areas fully contact each other.
For ultrasonic welding, high-frequency vibrations melt the plastic while pressure is applied to bond it.
Step 5: Cooling and Solidification
Maintain pressure until the welded area fully solidifies. After cooling, remove clamps or pressure to complete the welding process.
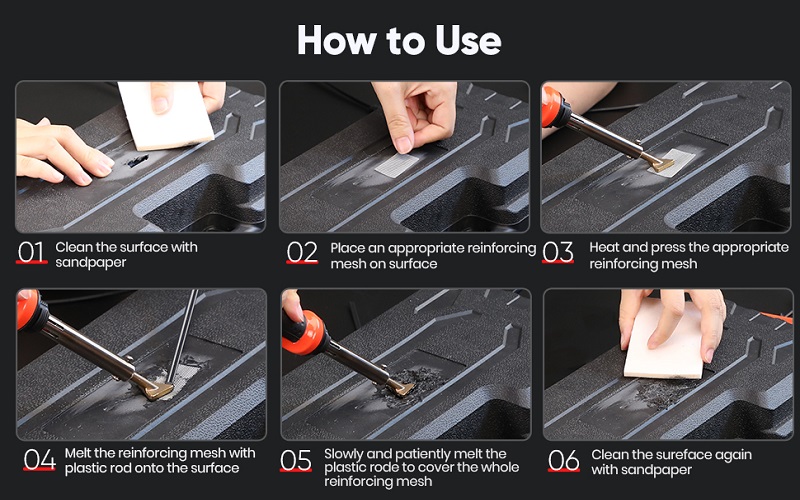
Factors Affecting Plastic Welding Quality
When performing plastic welding, three key elements—pressure, time, and heat absorption (melt volume)—are critical to ensuring weld quality.
- Pressure
Applying appropriate pressure to the welding surfaces transitions the material from elastic to plastic states.
This also facilitates molecular diffusion and expels residual air from the weld seam, enhancing the sealing performance of the joint.
- Time
Adequate heating time and sufficient cooling time are essential. The welding surfaces must absorb enough heat to reach a fully molten state, allowing thorough molecular diffusion and fusion. Likewise, sufficient cooling time is necessary to ensure the weld achieves adequate strength.
- Melt Volume
Proper coordination of heating time and power is required to achieve the optimal melt volume. This ensures sufficient intermolecular fusion, eliminating issues like incomplete welds (cold joints).
Beyond welding equipment and operator skill, various internal and external factors related to the plastic itself can influence welding quality.
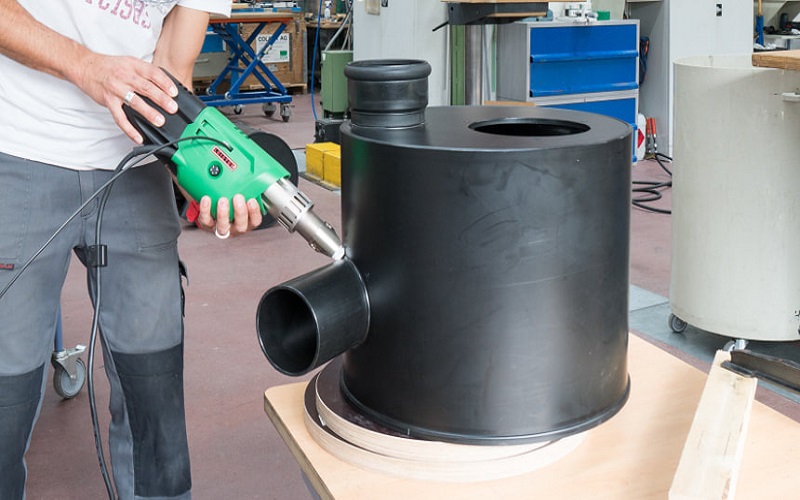
Applications of Plastic Welding Techniques
Plastic welding technology, with its advantages of efficiency, strength, and flexibility, is widely applied across various industries.
Below are its primary application areas:
- Automotive Manufacturing
In automotive production, plastic welding is used to create interior components (e.g., dashboards, door panels), exterior parts (e.g., bumpers), and functional elements (e.g., fuel tanks, pipelines).
Its high strength and seamless bonding enhance component durability and safety.
- Medical Devices
Plastic welding plays a critical role in producing disposable medical equipment (e.g., IV tubes, syringes) and implantable devices, ensuring sterile, robust seams that meet stringent hygiene and quality standards.
- Electronics
Consumer electronics (e.g., smartphones, laptops) rely on plastic welding to assemble plastic casings and internal components, achieving a seamless appearance and precise alignment of parts.
- Industrial Piping Systems
In chemical and water treatment industries, plastic welding connects pipes and valves (e.g., PVDF, PP materials), offering corrosion-resistant, high-strength solutions suited to demanding environments.
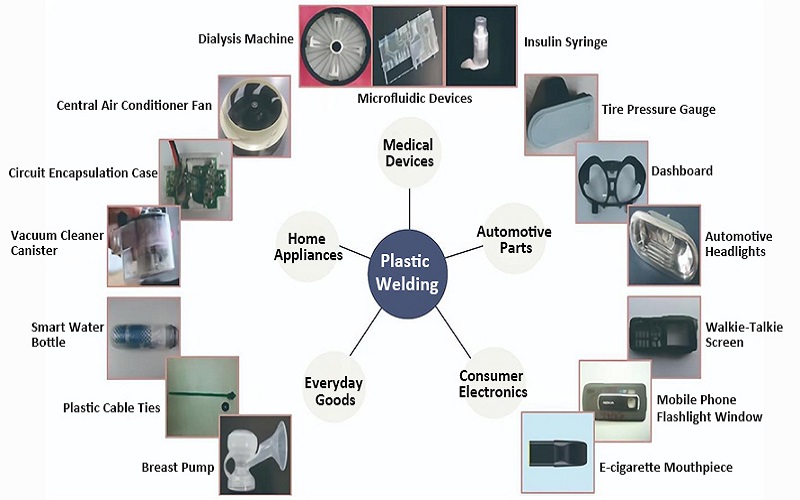
Operating Procedures For Plastic Welding Process
- Handle the welding gun with care to avoid damaging the heat-resistant ceramic strip inside.
- During welding, keep the nozzle and tip of the gun away from your body, clothing, and the power cord to prevent burns or melting of the cord.
- Strictly refrain from using the welding gun for purposes other than welding, such as a hairdryer.
- If unusual noises or issues occur during welding, immediately turn off the gun or disconnect the power supply.
- After welding, follow the correct shutdown sequence and allow sufficient cooling time to avoid damaging the gun.
Additionally, when welding plastic parts, prioritize personal safety. Especially during ultrasonic welding, wear appropriate protective gear to shield yourself from potential harm caused by ultrasonic waves.
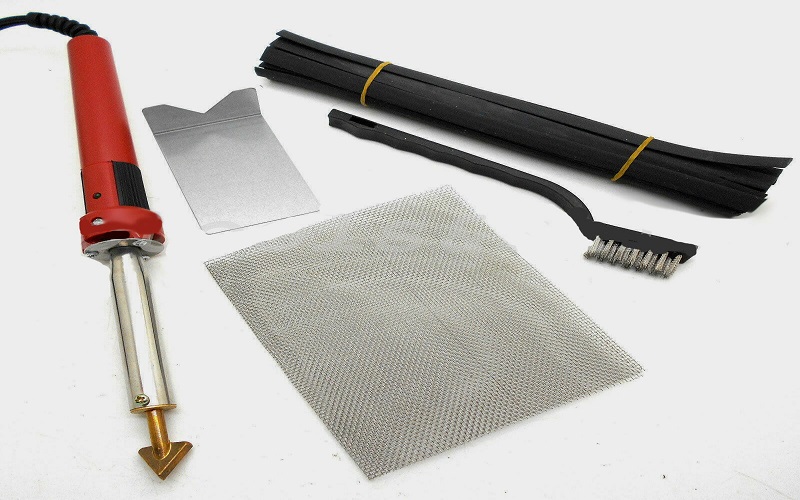
Conclusion
In conclusion, plastic welding, an efficient and durable joining technique, leverages standardized procedures and refined processes to effectively address the challenge of “how to weld plastic.”
Mastering the proper methods of plastic welding enhances production efficiency and product quality while fueling innovation and sustainable growth.