Automotive molds are vital in manufacturing plastic car parts efficiently and with high precision. They ensure consistency in producing parts like body panels and engine components.
This article covers the types of automotive molds, their role in the production process, and industry innovations.
What Is Automotive Mold?
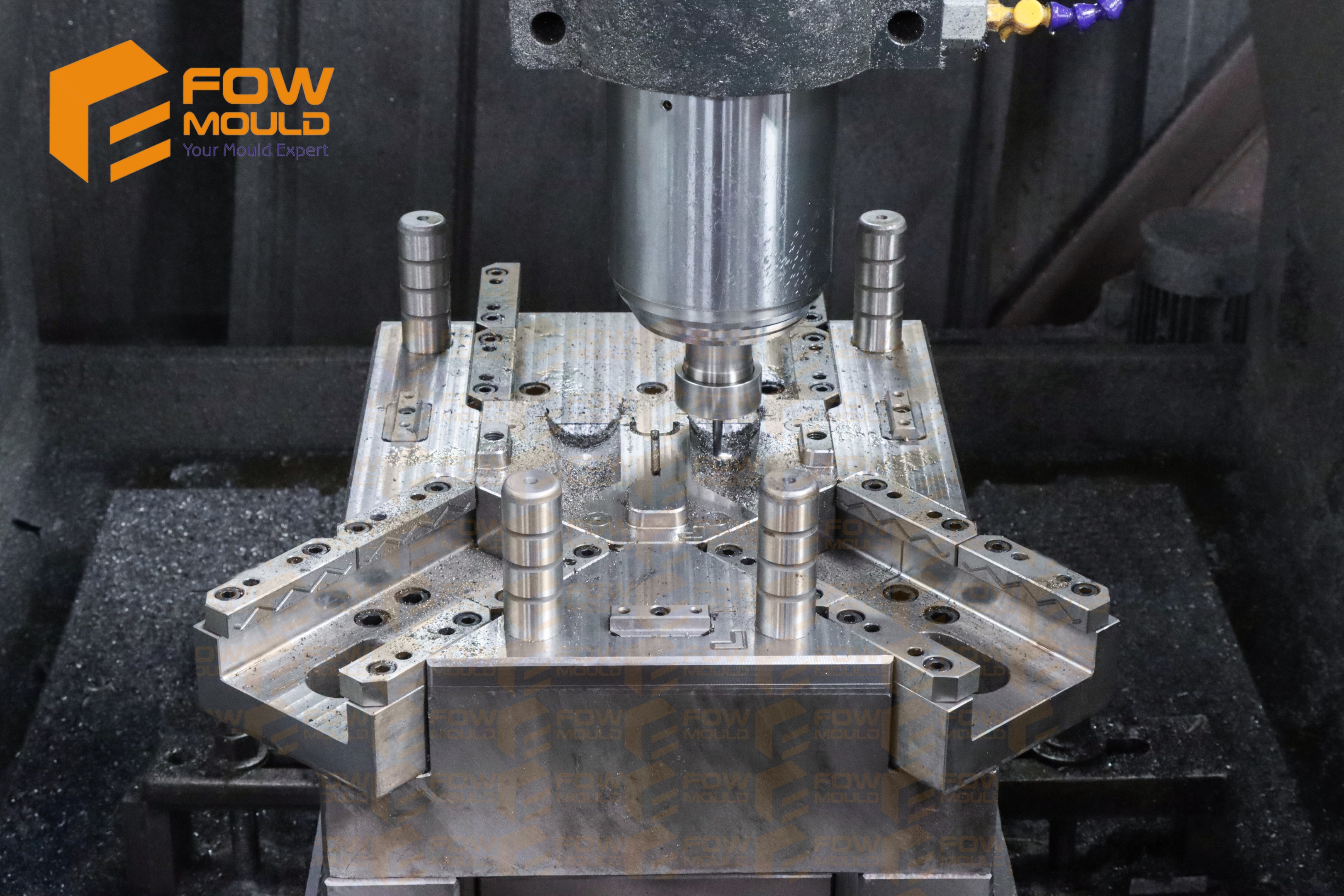
Automotive molds are essential to modern vehicle manufacturing, enabling precise and efficient production of injection molded parts critical for assembly.
Injection molding stands out for its accuracy, speed, and ability to create complex shapes with excellent finishes, benefiting electric, hybrid, and traditional vehicles for both OEMs and aftermarket sectors.
These specialized molds shape metal or plastic parts—like body panels, engine parts, and interiors—with high precision and consistency vital for large-scale production.
Advanced injection molding technology ensures complex automotive components meet strict quality standards with remarkable repeatability, making it indispensable for manufacturers facing tight schedules.
Importance of Automotive Mold
Firstly, automotive mold is the foundation of production efficiency in the automotive plastic injection molding industry, directly impacting the manufacturing speed and cost of components.
Through standardized and automated designs, molds enable high-speed, continuous production, significantly shortening production cycles and reducing production costs.
For example, stamping molds can complete the forming of body panels in seconds, greatly enhancing production efficiency. The durability of molds reduces the frequency of replacement and maintenance, optimizing the time and economic benefits of large-scale production.
Secondly, automotive molds ensure product quality. Through precise design and manufacturing, molds can control the tolerances of components, ensuring dimensional consistency and surface quality. Interior parts manufactured with precision molds can avoid burrs or deformation, while body parts produced with stamping molds ensure structural strength.
Moreover, molds support technological innovations, such as the application of lightweight materials and complex geometries, driving the automotive industry towards intelligent and green development. Therefore, automotive molds are regarded as an indispensable core element of modern automotive manufacturing.
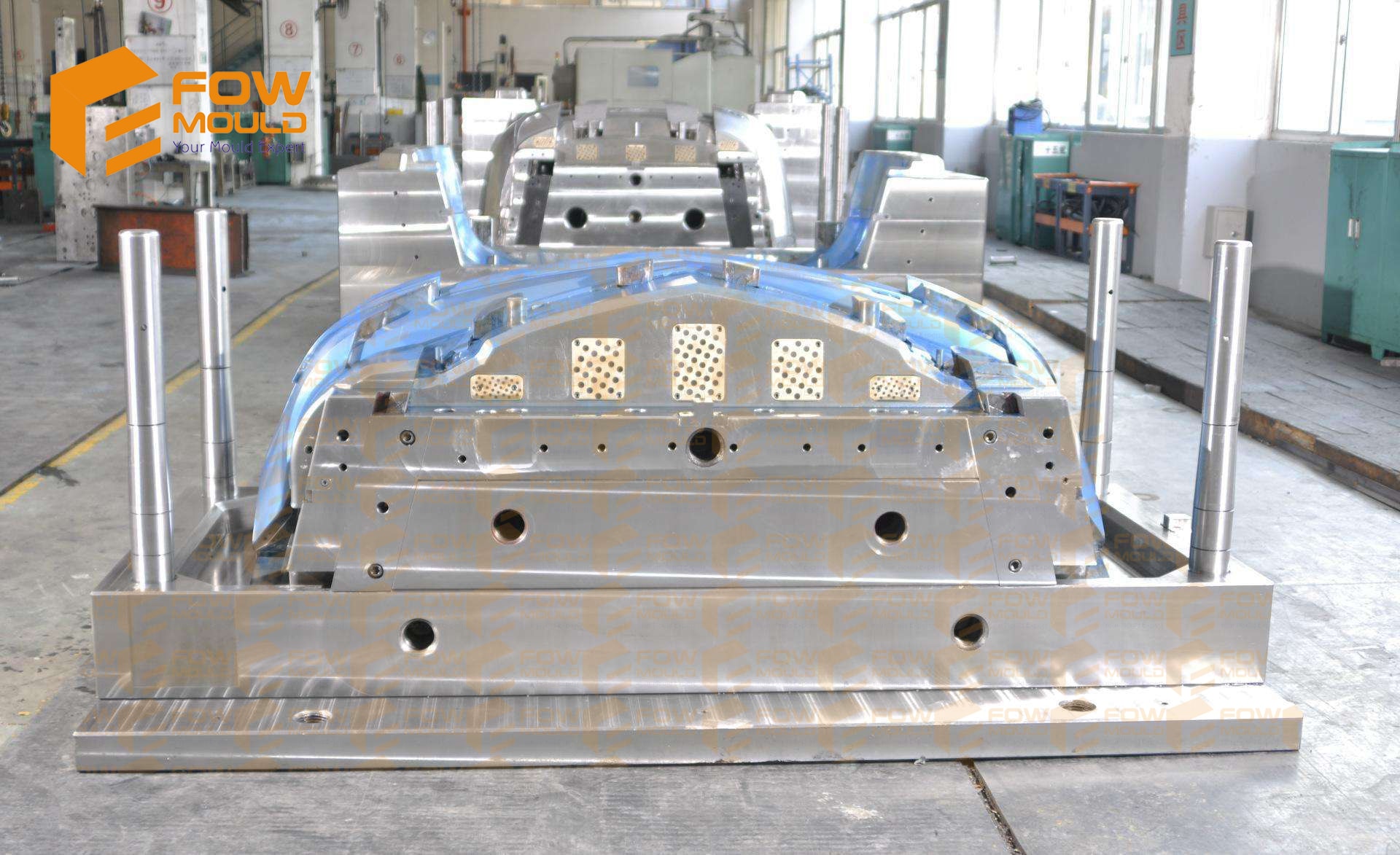
Type Of Automotive Mould
Automotive mold can be categorized into the following main types based on their purpose and processing techniques.
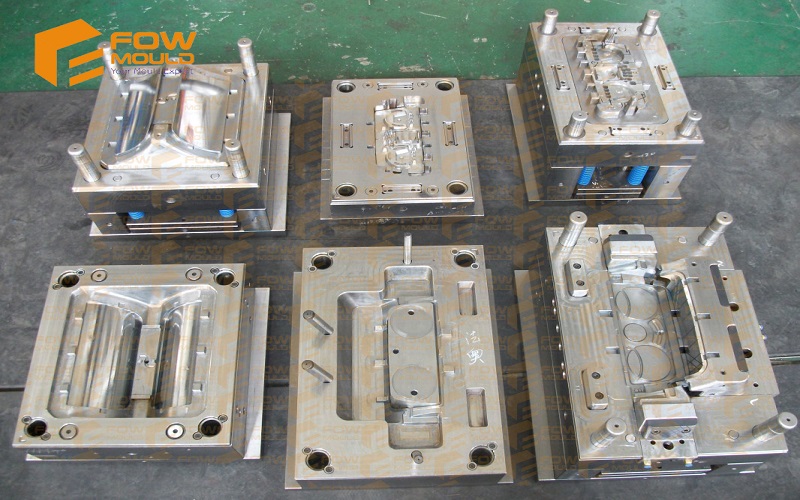
Stamping Mold
Stamping molds are used to shape metal sheets through pressure processing, commonly employed in manufacturing large components like car body shells, doors, and hoods. These molds require high strength and wear resistance to withstand repeated mechanical impacts.
Injection Mold
Injection mold form by injecting molten plastic into mold cavities and are widely used for producing plastic components such as interior parts (like dashboards) and exterior parts (like bumpers), emphasizing high precision and surface finish quality.
Casting Mold
Casting molds are used for casting metal liquids, mainly producing high-strength parts like engine blocks and transmission housings. These molds are suitable for complex structural components, such as sand molds and metal molds.
Forging Mold
Forging molds shape metal billets through high temperature and high pressure, used for manufacturing high-load parts such as crankshafts and connecting rods, requiring excellent heat resistance and deformation resistance.
Die-casting Mold
Die-casting molds use high pressure to inject molten metal (such as aluminum alloy) into the mold, suitable for producing lightweight parts like wheels and brackets, with high requirements for cooling systems and material selection.
Automotive Injection Mold Design Requirements
The design of automotive mold directly affects the quality and production efficiency of components, with requirements mainly reflected in three aspects.
Firstly, high precision is essential, as automotive molds must achieve micron-level accuracy (typically with tolerances within ±0.005 mm) to ensure the dimensional consistency and assembly compatibility of complex components such as body panels and engine parts. This high precision design relies on advanced CAD/CAM software and precision machining equipment.
Secondly, tolerance control is the core of mold design, balancing the functionality and manufacturability of parts. For instance, stamping molds must control the tensile deformation of metal sheets, while injection molds must avoid shrinkage deviations in plastic parts, ensuring that products meet design specifications and reduce the need for post-production adjustments.
Material selection is also a critical factor in automotive mold design. Mold materials need to possess high strength, wear resistance, and corrosion resistance, often using high-quality mold steel (such as P20, H13) or hard alloys.
For high-temperature processes (like die-casting), materials with strong heat resistance are necessary. Additionally, the trend towards lightweighting encourages the use of aluminum alloys or composite material molds to accommodate the production of new material parts.
These design requirements collectively ensure that automotive mold meet high-performance demands, extend their service life, and support the efficiency and stability of large-scale production.
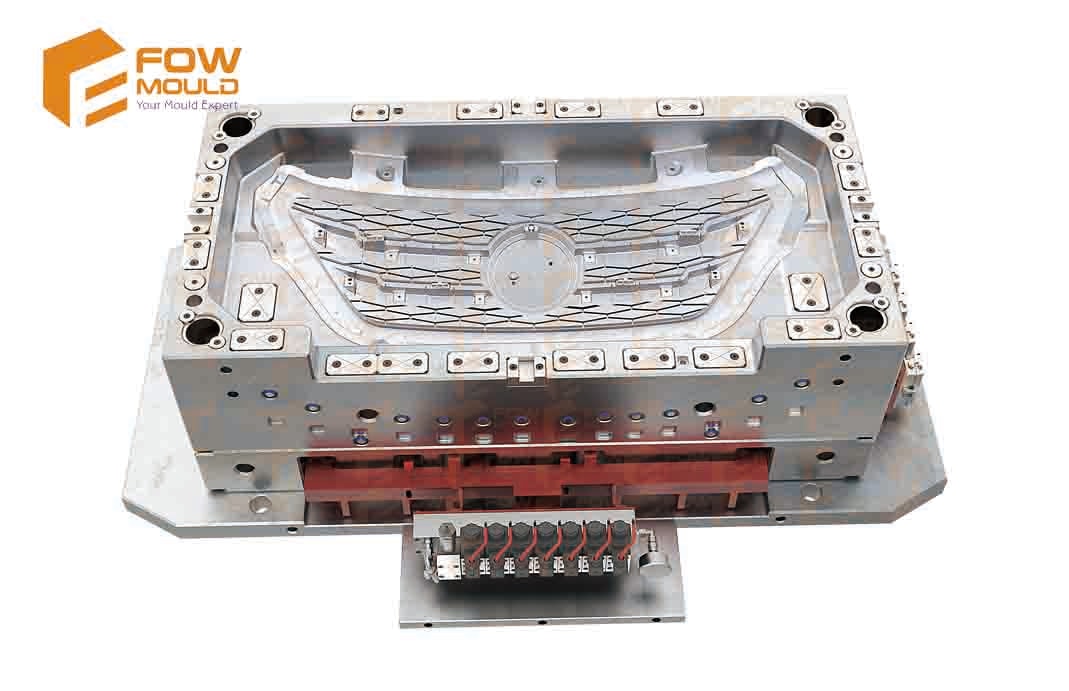
The Automotive Injection Molding Process
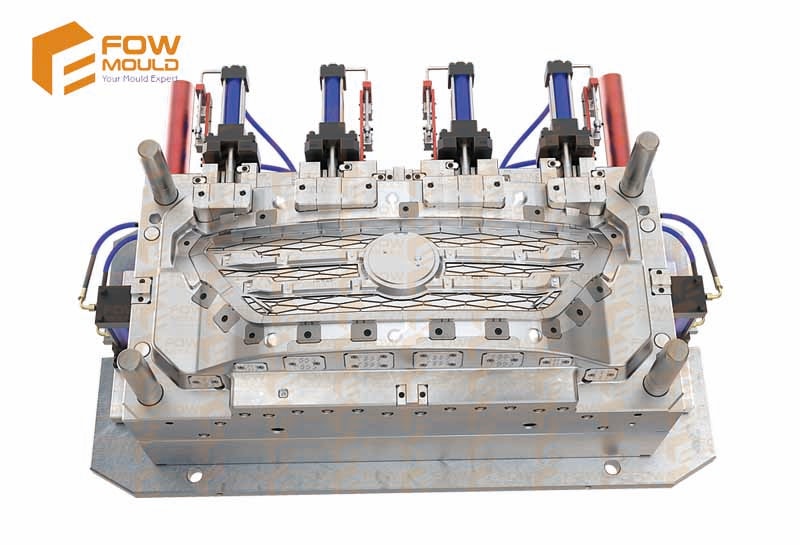
The automotive plastic injection molding process is a cornerstone of modern manufacturing for complex-shaped parts, providing flexibility in design and production. It follows five basic steps: setting the injection mold, injecting heated materials, cooling the piece, preparing resin for the next injection, and ejecting the finished piece. Plastic injection molding is essential in this context.
This rigorous process ensures that each part meets the high standards required in the automotive industry, from interior trims to engine components.
Tooling Design
The initial step in the automotive plastic injection molding process is tooling design, which significantly impacts the long-term production capabilities and the accuracy of the automotive parts being manufactured.
Designers face challenges in achieving the desired geometries, tolerances, and surface finishes, making it crucial to balance functional and aesthetic requirements alongside manufacturing limitations. Proper material flow and strategic injection points in mold design can minimize defects like flash, ensuring high-quality outcomes.
A well-designed mold ensures the production of high-quality components with consistent accuracy. Utilizing advanced technologies such as CNC machining and CAD software, designers can create molds that meet the stringent demands of automotive parts manufacturing. This meticulous process is the foundation for producing reliable and precise automotive components.
Molding Cycles
Efficient molding cycles are crucial for minimizing production time while maintaining high quality in automotive components. Using softer metals for mold production can accelerate parts production in low-volume scenarios, allowing manufacturers to quickly respond to market demands. This approach not only speeds up the production process but also reduces overall tooling costs, making it a cost-efficient solution for automotive manufacturers.
Quality Control
Quality control in automotive injection molding involves rigorous testing and adherence to strict industry standards to ensure product reliability. Companies like WIT MOLD and Immould maintain high precision and accuracy through strict quality controls and expert testing. High precision molding methods ensure that components meet the high standards of the automotive industry.
The integration of IoT in manufacturing allows for real-time monitoring and optimization of automotive mold production processes. By leveraging IoT and artificial intelligence, manufacturers can enhance predictive maintenance, reduce downtime, and ensure that each component meets the highest quality standards. This advanced approach to quality control guarantees that automotive parts are reliable, safe, and efficient.
The Critical Role of Automotive Mold in Automotive Plastic Molding
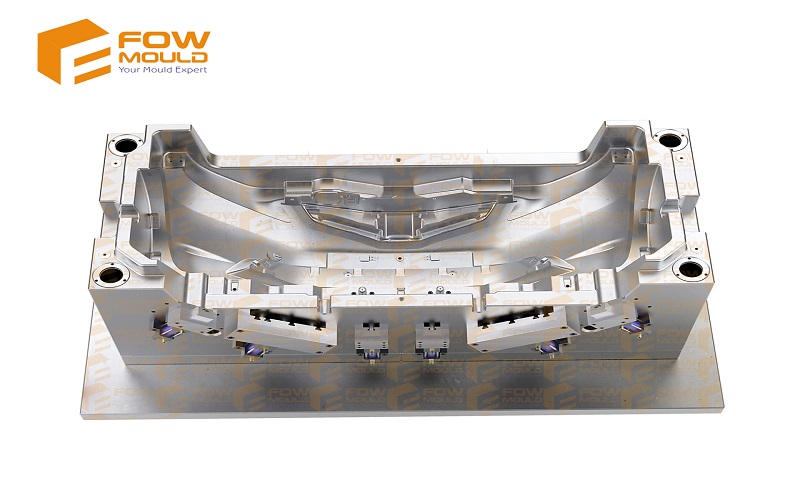
Automotive molds play a crucial role in manufacturing plastic car parts. They not only enhance production efficiency and product quality but also support the trend towards lightweight designs and technological innovations.
The following sections elaborate on production efficiency, product quality, the lightweight trend, and real-world examples.
Enhancing Production Efficiency
Automotive molds enable high-speed, continuous production of parts through standardized and automated designs. For instance, stamping molds can form body panels in seconds, significantly shortening production cycles.
The durability of molds reduces the frequency of replacements and maintenance, lowering long-term operational costs and optimizing the time and economic benefits of large-scale production. Additionally, injection molding technology effectively reduces material waste, thereby lowering production costs while increasing production speed.
The standardized design of molds allows for the rapid production of automotive components, with typical die-casting molds completing the forming process in a short time. This efficient production method not only boosts production efficiency but also provides a more cost-effective solution for automotive manufacturers. By optimizing production processes, automotive molds play an indispensable role in enhancing production efficiency.
Ensuring Product Quality
Precision molds control tolerances at the micron level, ensuring the dimensional consistency and surface quality of components. For example, interior parts manufactured with injection molds can avoid burrs or deformation, while body parts produced with stamping molds ensure structural strength. These features significantly reduce defect rates, enhancing vehicle safety and reliability, which directly relates to consumer safety.
The precise injection molding process ensures uniform thickness of components, reducing the risk of structural defects.
Supporting the Lightweight Trend
As the automotive industry pursues energy savings and emissions reduction, lightweight design has become a trend. Mold technology adapts to this demand, such as die-casting molds used for producing aluminum alloy wheels, reducing weight while maintaining strength. Injection molds combined with carbon fiber composites manufacture high-strength body structural parts.
These innovative molds drive the widespread application of lightweight materials. The innovation in mold technology allows automotive manufacturers to utilize lightweight materials, thus achieving higher fuel efficiency.
Case Analysis
Tesla uses giant die-casting molds, like the Giga Press, in its “Gigafactory” to form the rear underbody of the Model Y in one piece, replacing the traditional multi-piece welding process. This technology not only improves production efficiency but also enhances structural integrity. By forming parts in one go, Tesla’s Giga Press showcases the transformative role of modern molds in automotive production.
Volkswagen uses high-precision stamping molds to produce the body shells of its ID. series electric vehicles, ensuring a balance between lightweight design and crash safety. These cases demonstrate how renowned automotive brands rely on precision molds to achieve breakthroughs, driving innovation and efficiency improvements in automotive manufacturing.
Challenges in Automotive Injection Molding Technique
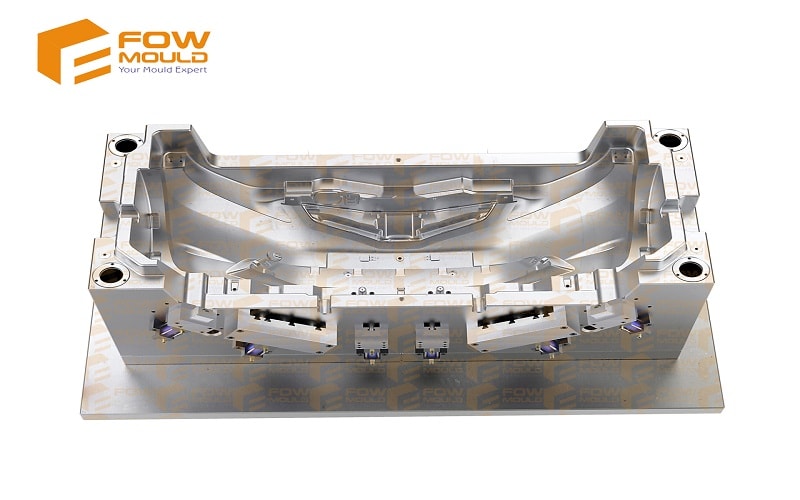
Injection molding automotive, while highly effective, faces several challenges that manufacturers must address to maintain quality, efficiency, and competitiveness.
Below are the key hurdles commonly encountered:
Precision and Tolerance Control
Achieving tight tolerances (often within ±0.005 mm) is critical for automotive parts to ensure proper fit and function, especially for complex components like dashboards or engine parts. Variations in temperature, pressure, or material flow during molding can lead to defects, requiring advanced simulation tools and precise mold design to minimize errors.
Material Selection and Performance
Selecting the right materials—such as heat-resistant plastics or reinforced composites—is challenging due to the diverse demands of automotive applications (e.g., durability, lightweighting, and thermal stability). Balancing cost, performance, and sustainability (e.g., using recycled plastics) adds complexity to the process.
High Initial Costs and Lead Times
Designing and manufacturing injection molds involves significant upfront investment in tooling and equipment. For intricate or large molds, lead times can extend, delaying production schedules—a critical issue for automakers facing tight deadlines in a fast-paced industry.
Complexity of Part Design
Modern automotive designs often feature intricate geometries and multi-material components, such as overmolded parts combining plastic and metal. These complexities increase mold design difficulty, risk of warping or shrinkage, and the need for multiple iterations during testing.
Applications of Automotive Plastic Parts
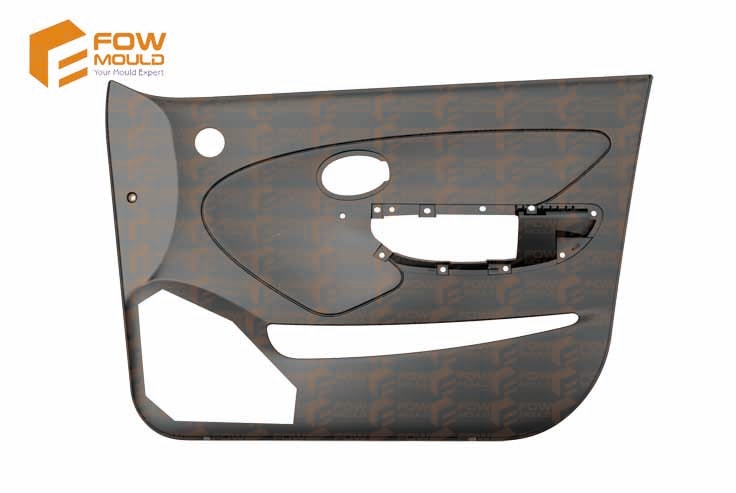
Injection molding automotive parts is widely utilized to produce a diverse range of vehicle components. Below, we explore its specific applications in manufacturing interior, exterior, and under-the-hood parts.
Interior Components
Injection molds are primarily used to craft interior automotive parts such as door panels, dashboards, and air vents.
These include seats, door trim, shift knobs, AC vents, and decorative strips, with specific parts like dashboards, glove boxes, instrument panels, door handles, and armrests produced through this method.
Exterior Components
Injection molding is a key technology for creating exterior automotive parts, including fenders, grilles, bumpers, door panels, and light covers.
These molded exterior panels enhance aerodynamic efficiency while maintaining visual appeal without adding unnecessary weight, making them essential for vehicle design and performance.
Under-the-Hood Parts
In the engine compartment, injection-molded components such as intake manifolds, covers, fluid reservoirs, battery casings, and air filter housings are made from heat-resistant plastics.
These materials optimize airflow and performance, increasingly replacing heavier metal parts to boost efficiency and reduce vehicle weight.
Innovations in Automotive Molding Technology
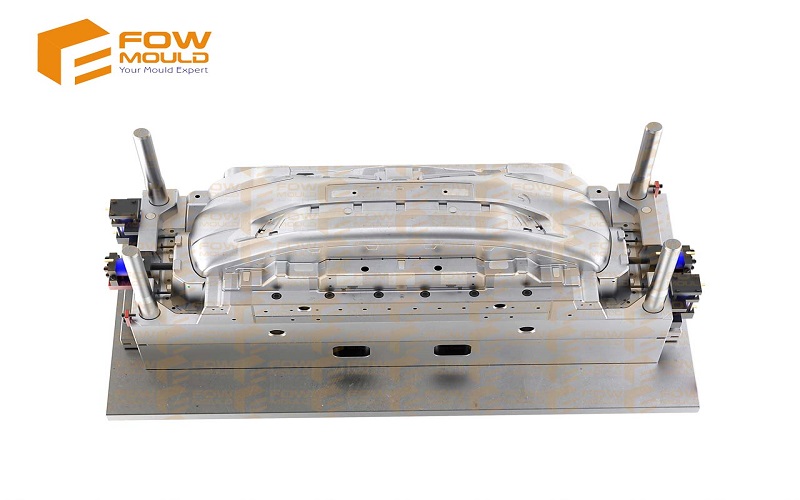
With technological advancements, innovations in the automotive mold production process have continually emerged, significantly enhancing production efficiency. The following sections will introduce the applications of 3D printing, rapid prototyping, and smart manufacturing in automotive mold technology.
3D Printing and Rapid Prototyping
3D printing and CNC machining are key technologies for producing prototype automotive plastic components. One major advantage of injection molding technology is the ability to create rapid prototypes, making it highly efficient for design testing.
Automotive manufacturers leverage fast, cost-effective aluminum molds for short-term prototyping, thereby enhancing the prototyping process.
Smart Manufacturing
Smart manufacturing utilizes advanced technologies such as the Internet of Things (IoT) and Artificial Intelligence (AI) to revolutionize the automotive mold production process, improving decision-making capabilities and efficiency. In recent years, advancements in automotive mold technology have enabled injection molding companies to achieve higher levels of production efficiency, thereby reducing time and costs in the molding process.
Choosing the Right Automotive Mold Manufacturer
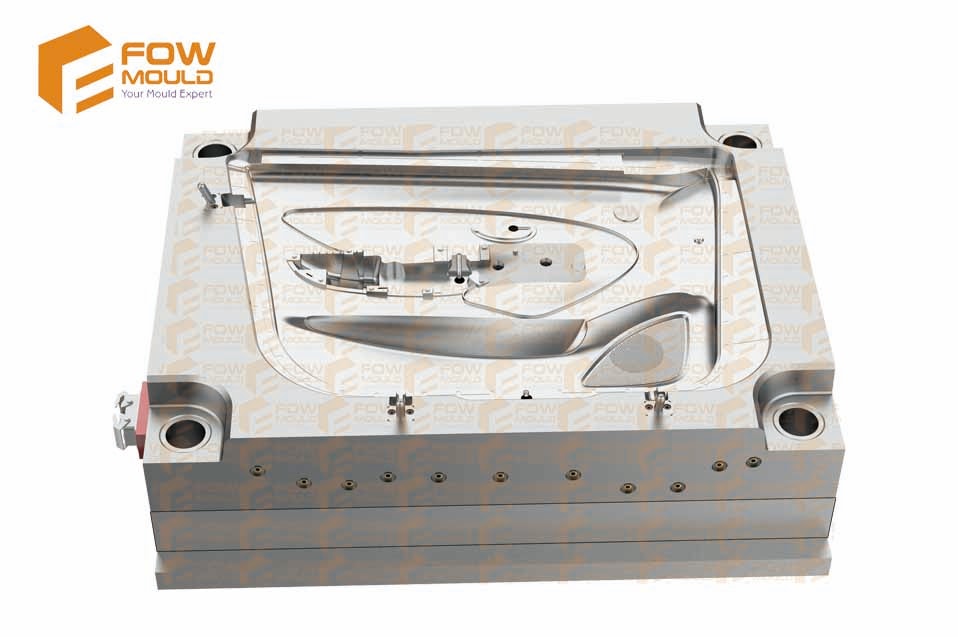
In the automotive industry, selecting the right automotive mold manufacturer is crucial for ensuring production efficiency, product quality, and cost control. The following sections will discuss the factors to consider when choosing a manufacturer, including technical capabilities, experience, precision and quality control, as well as production capacity and delivery time.
Technical Capabilities and Experience
A top-notch manufacturer should possess advanced design and manufacturing technologies, such as CNC machining, mold flow analysis, and 3D printing capabilities. Extensive industry experience means they can handle complex mold requirements and provide innovative solutions.
Choosing a manufacturer with these capabilities and experience ensures efficient and high-quality production.
Precision and Quality Control
Automotive molds require extremely high precision (e.g., tolerance control within 0.005 mm) to ensure the consistency and safety of components. A strict quality management system (such as ISO certification) is an important standard for measuring a manufacturer’s reliability.
Selecting a manufacturer with high precision and quality control capabilities ensures that each component meets stringent industry standards.
Production Capacity and Delivery Time
Manufacturers should have large-scale production capabilities and be able to deliver molds within specified timelines to meet the fast-paced demands of the automotive industry. Flexible production processes and quick response capabilities are particularly crucial. Choosing a manufacturer that can provide these services ensures projects are completed on time.
Conclusion
Precision automotive mold hold a central position in automotive companies, serving as the key support for the efficient and high-quality production of plastic auto parts and as a cornerstone for driving industry innovation. By ensuring production efficiency, enhancing product quality, and supporting the trend towards lightweight design, precision molds provide indispensable value to automotive manufacturing.
Technological innovation is propelling automotive molds toward greater precision and sustainability. As the automotive industry moves towards intelligence and green development, automotive molds will face more opportunities and challenges, becoming a significant force in leading industry transformation.
Whether you are pursuing high-precision components or optimizing production processes, FOWMOULD can provide you with automotive injection molding service. If you are looking for a reliable partner, consider contacting FOWMOULD for customized quotes and professional advice.
Frequently Asked Questions
What is the importance of automotive molds in manufacturing?
Automotive molds are crucial for ensuring the accurate and efficient manufacturing of plastic components, allowing for the production of complex shapes with superior quality. Their importance lies in enhancing both the precision of parts and the overall efficiency of the manufacturing process.
What are the different types of automotive molds?
Automotive molds encompass stamping molds, injection molds, casting molds, forging molds, and die-casting molds, each designed for specific manufacturing needs of various car components. Understanding these types can enhance efficiency in automotive production processes.
How do automotive molds enhance production efficiency?
Automotive molds enhance production efficiency by facilitating standardized and automated designs, which lead to high-speed, continuous production, thereby reducing both production cycles and operational costs.
Why is quality control crucial in automotive injection molding?
Quality control is crucial in automotive injection molding because it guarantees that components meet stringent quality standards, thereby enhancing product reliability and safety. This adherence to strict testing protocols is essential for maintaining industry standards.
How do innovations like 3D printing and smart manufacturing impact automotive molding?
Innovations like 3D printing and smart manufacturing significantly improve automotive molding by increasing production efficiency, enabling rapid prototyping, and optimizing manufacturing processes. These advancements lead to better decision-making and cost savings in the automotive industry.