Two shot injection molding, also known as dual injection or 2K molding, is a manufacturing process that combines two different plastics into a single, multi-material component.
This method allows for complex designs and enhanced functionality without needing additional assembly steps.
In this article, we’ll explore how this innovative process works, its benefits, and its common applications.
Understanding Two Shot Injection Molding
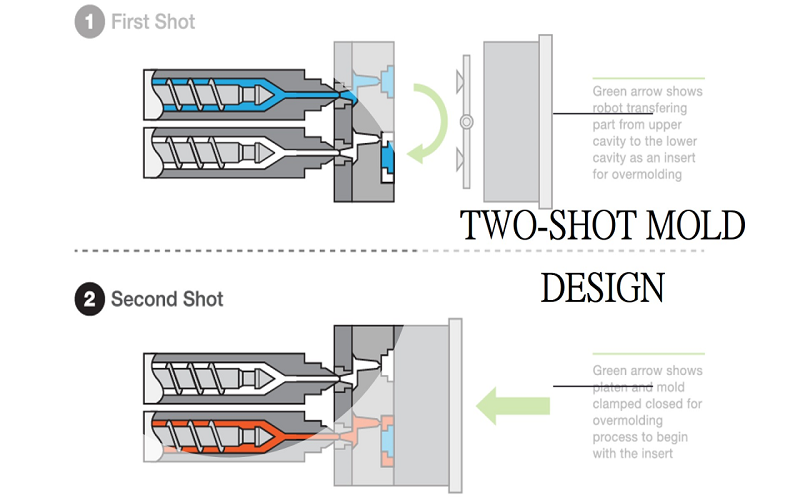
Two-shot injection molding, also known as double injection molding, dual injection, multi-shot, or 2K molding, is a sophisticated manufacturing process designed to create composite components from two different plastics.
This method’s primary purpose is to produce multi-material components that combine the best properties of each material in a single, cohesive product. Injecting two types of polymers into the same mold through separate injections enables intricate designs and enhanced functionality without additional assembly steps.
The process involves using a specialized molding machine equipped with two or more injection units, each responsible for injecting different materials. These machines must be precisely calibrated to ensure that the molds bond easily and align correctly, preventing defects and ensuring high-quality final products. Unlike traditional injection molding, which typically uses a single material, two-shot molding integrates two separate plastic resins in one machining cycle, offering significant advantages in terms of product complexity and design. A standard injection molding machine can also be utilized for various applications.
Additionally, two-shot injection molding combines different materials and colors within a single component. This capability allows for the creation of visually appealing and functionally superior products. Precise control over material placement and bonding ensures each part meets stringent quality standards, making this process ideal for high-demand applications across various industries.
The Two Shot Molding Process
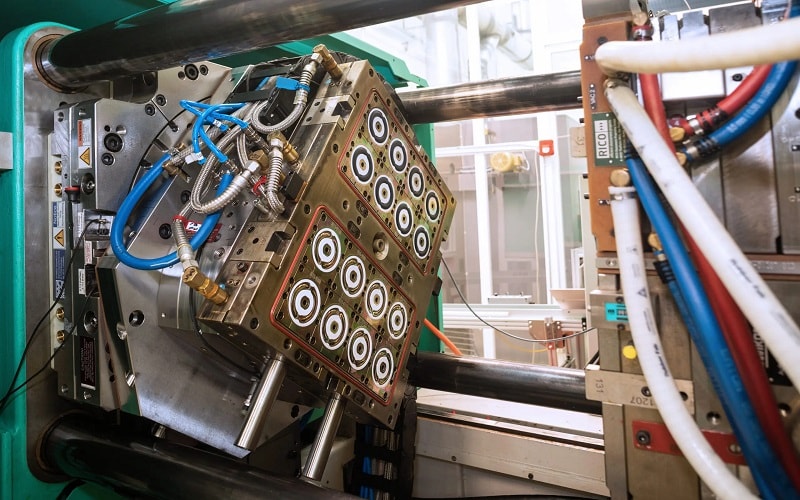
The two-shot molding process is a marvel of modern manufacturing, involving the injection molding process of two distinct plastic resins to create a complex final part in a single machining cycle.
This intricate molding processes can be broken down into three primary steps: the first injection phase, mold rotation or transfer, and the second injection phase.
Each step is meticulously orchestrated to ensure precise alignment and bonding of materials, resulting in a high-quality product that meets exact specifications.
First Injection Phase
The journey begins with the first injection phase, where the initial material is injected into the mold. This phase sets the foundation for the final product.
The resin is introduced into the mold via an injection molding nozzle, filling the mold cavity and taking on its shape. Once the resin is injected, it undergoes a cooling process where it solidifies into a solid component.
This cooling period is vital as it ensures the structural integrity of the first shot, which will act as the substrate for the subsequent steps. Controlling the cooling speed and time is crucial for achieving high-quality final products, preventing defects and ensuring the material has the desired properties for the next phase.
Mold Rotation or Transfer
Following the initial injection and cooling, the semi-finished product must be positioned correctly for the second injection. This is achieved through mold rotation or transfer, a critical step that ensures precise alignment. Various methods such as robotic arms, rotary planes, or even manual transfer can be employed to move the product to the appropriate position in the other mold chamber.
This step maintains the integrity of the product and ensures the second material bonds correctly with the first material.
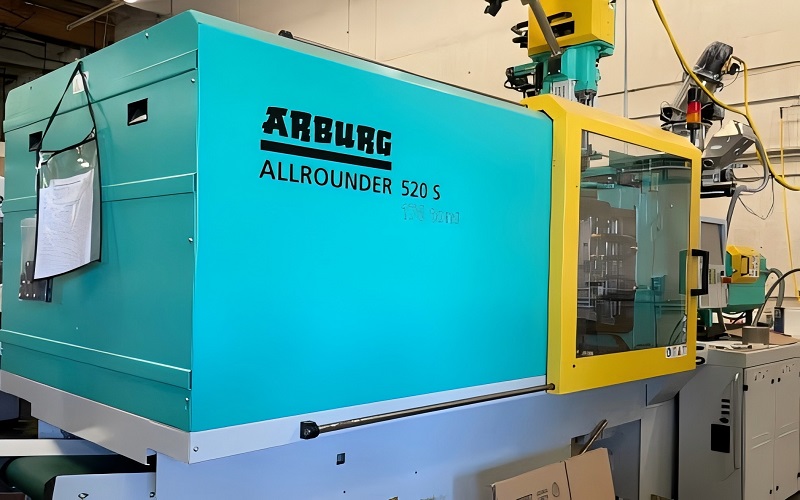
Second Injection Phase
The second injection phase is critical. In this stage, a different material is injected into the mold, bonding with the previously molded substrate to form a cohesive final product. This phase ensures the two materials adhere effectively, providing enhanced functionality and durability.
Meticulous calibration is required during this phase to ensure seamless bonding without defects. The injection units must be meticulously calibrated to ensure that the materials bond seamlessly without any defects.
The result is a high-quality, multi-material component that meets the stringent requirements of various applications, from automotive parts to consumer electronics.
Advantages of Two Shot Injection Molding
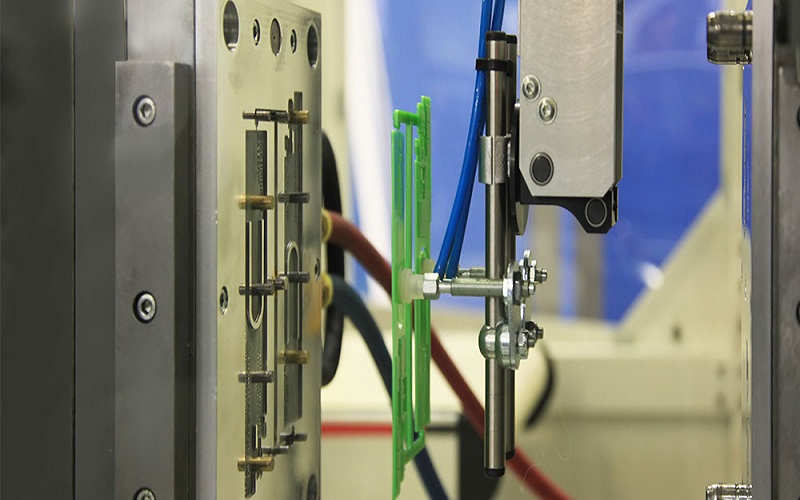
The advantages of two-shot injection molding are manifold, offering significant enhancements in product quality, cost efficiency, and design flexibility.
This innovative process allows for the creation of complex, multi-material, and multi-colored parts in a single machining cycle, eliminating the need for additional assembly steps and reducing production time.
The following subsections will delve into these benefits in greater detail.
Enhanced Product Quality
One of the most compelling advantages of two-shot injection molding is the enhanced product quality it delivers. Carrying out operations within a single tool allows for lower tolerances and more precise control over the final product. This precision is crucial for producing high-quality products that meet stringent industry standards.
Rigid plastics in two-shot molding significantly enhance the strength and stability of multi-material components. These plastic resin materials provide the necessary structural integrity, making them ideal for applications requiring high durability.
Integrating advanced quality improvement mechanisms and using durable materials ensures the final products are functional and long-lasting.
Cost Efficiency
Cost efficiency is another significant advantage of two-shot injection molding. This method reduces the number of separate components needed in a product assembly, resulting in substantial cost savings. For example, it can save up to $40,000 in development costs per added part, significantly optimizing expenses.
Labor savings are achieved by lowering assembly costs. This advantage is particularly evident in large production runs. The single machining cycle in two-shot molding significantly reduces time and cost, making it more cost-effective when produced in higher volumes.
This process reduces costs and labor while increasing production efficiency compared to traditional methods.
Design Flexibility
Two-shot injection molding offers significant design flexibility. This process allows for combining different colors or types of plastics in one component, offering more possibilities for product design and functionality. The ability to create intricate designs that incorporate multiple materials and colors in a single component is a significant advantage.
Parts can be designed with multiple colors or materials for specific applications, enhancing functionality and efficiency. For instance, in consumer electronics, two-shot injection molding enables the creation of multi-color and multi-material parts, enhancing the aesthetics and appeal of the final product.
Common Applications of Two Shot Injection Molding
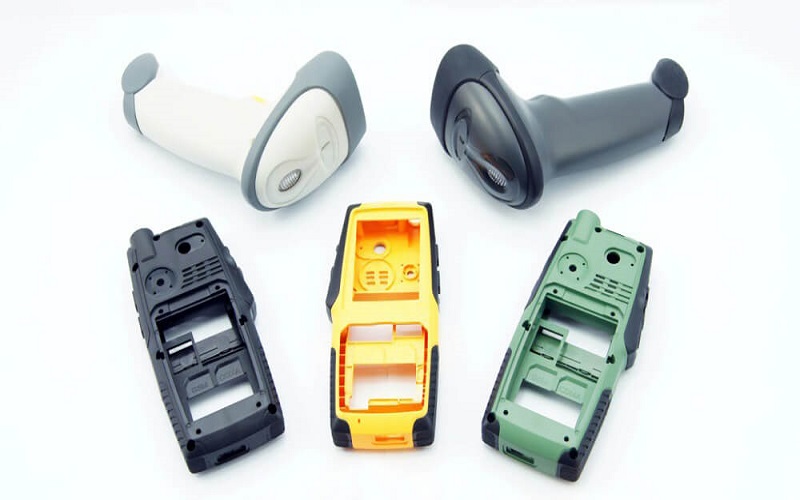
Two-shot injection molding is a versatile process with applications spanning various industries. This technique is employed in automotive components, consumer electronics, and medical devices to create high-quality, multi-material parts that meet specific requirements.
Here are some common applications explored in greater detail.
Medical Devices
In the medical field, precision and reliability are paramount. Two-shot injection molding ensures various medical devices meet stringent quality standards. Common medical devices produced using this method include pacemakers and implantable cardioverter-defibrillators, which require precise manufacturing to function correctly.
Combining different materials in one component without additional assembly steps is particularly beneficial in medical applications. This ensures that the devices are not only reliable but also durable, providing patients with the best possible outcomes.
Consumer Electronics
In consumer electronics, two-shot injection molding enhances product functionality and aesthetics. This technique allows for the creation of intricate designs that combine multiple materials in one component, improving both durability and appearance.
Examples include smartphone cases and electronic device housings that require both flexibility and strength. This process significantly contributes to the overall quality and consumer appeal of electronic products.
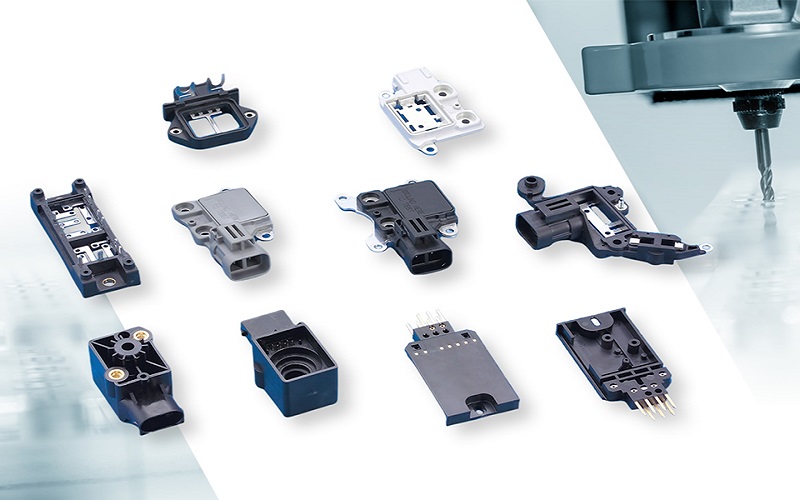
Automotive Components
The automotive industry uses two-shot injection molding for components like interior trims and exterior panels. This process produces lightweight parts that meet rigorous safety standards, enhancing performance and safety.
Durability and lightweight design in automotive parts are crucial for modern vehicles, improving fuel efficiency and overall performance. Two-shot injection molding improves the performance and safety of automotive components.
Material Considerations in Two Shot Injection Molding
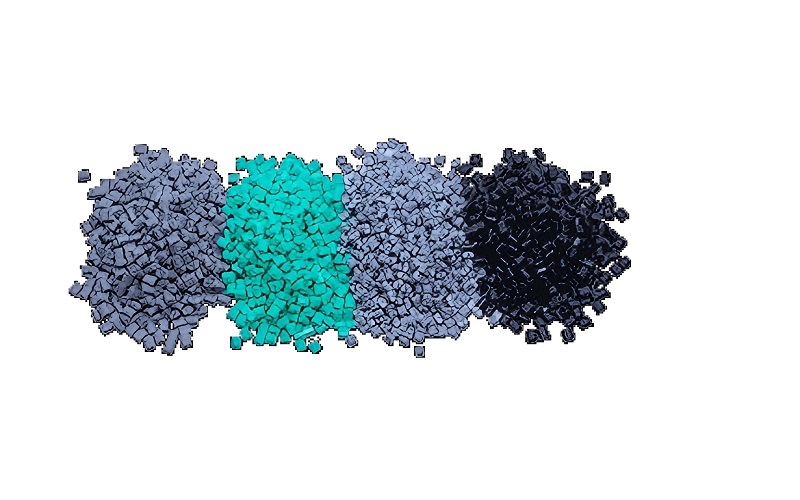
Selecting the right materials ensures a successful bond and prevents adverse reactions in two-shot injection molding. The compatibility of materials is essential for achieving the desired properties in the final product.
The following subsections will discuss the properties and benefits of thermoplastic elastomers and rigid plastics in two-shot molding.
Thermoplastic Elastomers
Thermoplastic elastomers are popular for their flexibility and durability. These materials provide excellent resistance to environmental factors, extending the life of the molded products.
Thermoplastic elastomers enhance the overall performance of the final product, ideal for applications requiring both flexibility and durability. This makes them preferred in industries like automotive and consumer electronics.
Rigid Plastics
Rigid plastics provide robustness and necessary structural integrity for various applications. Rigid plastics in multi-material parts enhance durability and overall product performance using plastic materials.
Industries like automotive and consumer electronics heavily rely on rigid plastics for their strength and integrity. Benefits of rigid plastics include reduced weight while maintaining high strength, essential for modern manufacturing.
Key Differences Between Two Shot Injection Molding and Overmolding
Though often compared due to their similarities, two-shot injection molding and overmolding have distinct differences. Two-shot injection molding allows the creation of complex parts without additional assembly steps, while overmolding involves wrapping a substrate with another material.
Overmolding can be performed using standard injection molding machines, making it easier to implement compared to two-shot molding. Two-shot molding is ideal for larger production runs, offering superior design flexibility by combining multiple materials into one structure.
Two-shot injection molding requires a significant initial investment in setup and tooling, whereas overmolding typically has lower startup costs.
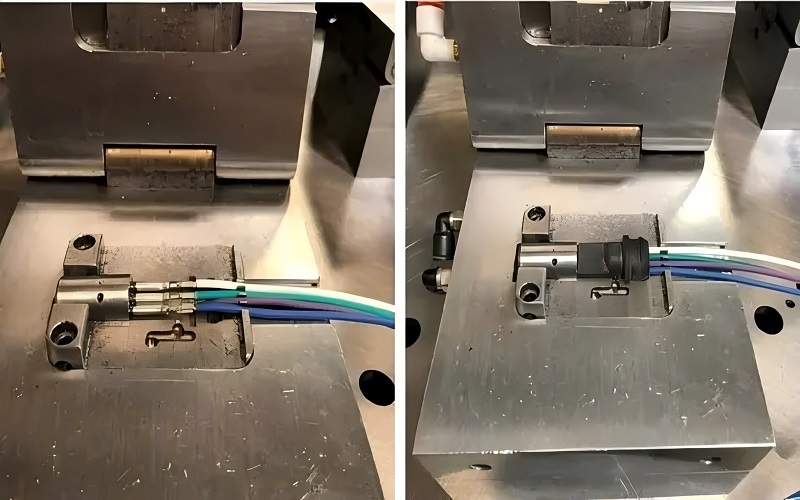
Choosing the Right Manufacturing Partner
Selecting the right manufacturing partner is crucial for successful two-shot injection molding projects. Choose a partner with the expertise to navigate the complexities of two-shot molding and ensure high-quality products. Evaluating the partner’s experience and their ability to handle advanced automation and state-of-the-art equipment can significantly enhance production efficiency and quality.
Discuss scalability with your manufacturing partner to ensure they can meet future production demands. A reliable partner provides valuable insights and support throughout the manufacturing process, helping achieve your production goals.
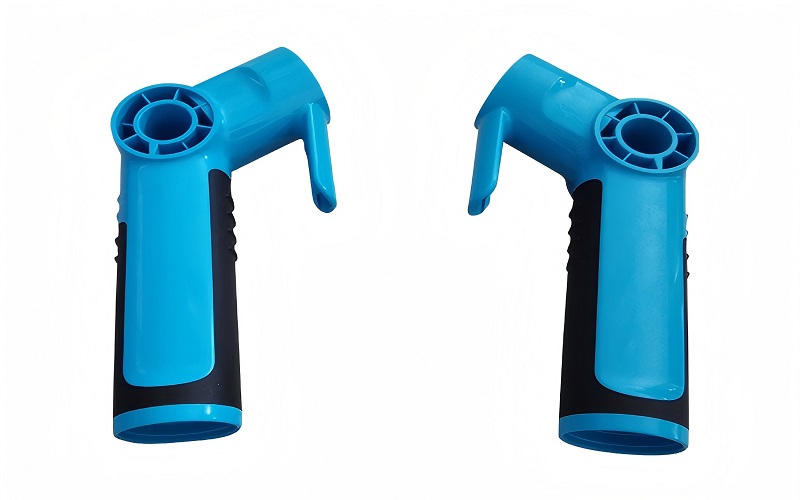
Summary
In summary, two-shot injection molding offers numerous advantages, including enhanced product quality, cost efficiency, and design flexibility.
This innovative process is widely used across various industries, from automotive to consumer electronics and medical devices.
By selecting the right materials and manufacturing partner, you can leverage the benefits of two-shot injection molding to create high-quality, multi-material products that stand out in the market.
Frequently Asked Questions
What is two-shot injection molding?
Two-shot injection molding is a manufacturing process that combines two different plastics into a single component by injecting them sequentially into the same mold. This technique allows for enhanced functionality and aesthetic appeal in the final product.
What are the key benefits of two-shot injection molding?
The key benefits of two-shot injection molding are enhanced product quality, cost efficiency, and design flexibility. These advantages make it an attractive option for manufacturers seeking to optimize production processes.
How does two-shot injection molding differ from overmolding?
Two-shot injection molding produces complex parts in one cycle without the need for assembly, whereas overmolding involves applying a secondary material over an existing substrate. This distinction highlights two-shot molding’s efficiency in creating integrated components.
What materials are commonly used in two-shot injection molding?
Commonly used materials in two-shot injection molding include thermoplastic elastomers and rigid plastics, selected for their compatibility and specific properties needed in the final product.
How do I choose the right manufacturing partner for two-shot injection molding?
Choose a manufacturing partner with proven expertise in two-shot injection molding, advanced technology, and the capacity to scale production as needed. Ensuring these qualifications will help meet your project’s demands effectively.