Glass filled nylon is nylon mixed with glass fibers, improving its strength and durability. This article will explain what glass filled nylon is, its benefits, drawbacks, and typical uses.
Understanding Glass Filled Nylon
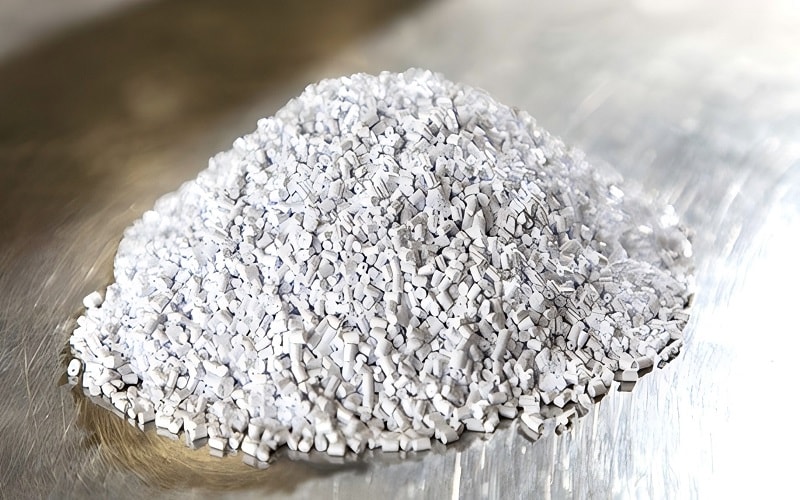
Glass-filled nylon is a synthetic polyamide thermoplastic made by incorporating powdered glass or glass fibers into nylon resin. This composite material features short glass fibers distributed within a nylon matrix, significantly enhancing its structural integrity.
One common type is polyamide 66 (PA66-GF), renowned for its strength and durability. Due to these enhanced properties, glass-filled nylon finds applications in various industries, including automotive, electrical, and industrial markets, and is often produced using glass filled nylon filaments.
Incorporating glass fibers into nylon creates a composite material that meets the high performance and durability demands of various engineering applications. From automotive components to industrial machinery, glass-filled nylon has become a go-to material for industries requiring robust and reliable solutions.
Composition of Glass Filled Nylon
Glass-filled nylon is composed of a blend of nylon resin and glass fibers, combining the advantageous properties of both materials. Common formulations typically utilize Nylon 6 or Nylon 66 as the base material.
The glass fiber content in these formulations can vary widely, usually ranging from 10% to 50%, depending on the specific application and desired properties. A typical blend features around 30% glass fibers, but different glass-filled variants can be tailored to meet specific requirements.
The addition of glass fibers enhances the strength, stiffness, and resistance to various forms of stress in the final material. However, increasing the glass fiber content can also make the material more brittle, reducing its impact resistance.
The glass fibers slow down the movement of polymer chains in nylon, contributing to the overall strength and rigidity of the composite. The fibers can be integrated during production through mixing, extrusion, or by adding glass beads.
Types of Glass Fibers Used
Different types of glass fibers are used to create glass-filled nylon, each offering unique benefits. The material can incorporate powdered glass particles, small spherical glass beads, and short glass fibers. Powdered glass particles enhance surface area but may affect flow properties during processing.
On the other hand, short glass fibers significantly improve the tensile strength and rigidity of the nylon, making it suitable for demanding applications.
Key Properties of Glass Filled Nylon
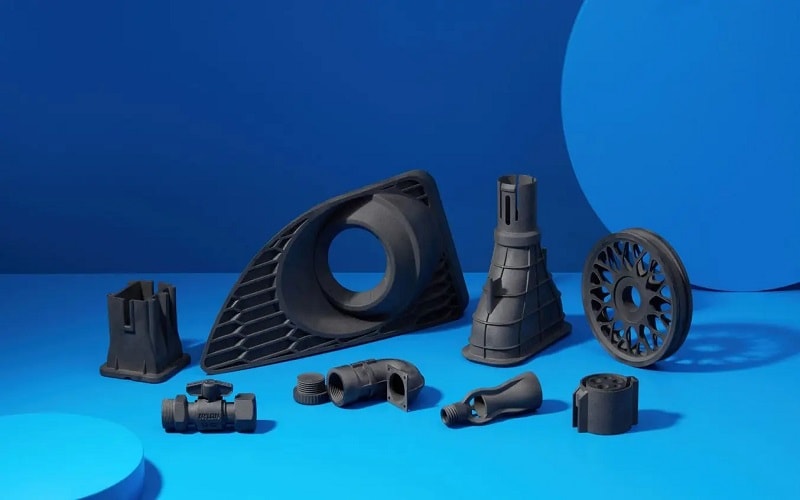
Adding glass fibers to nylon enhances its mechanical, thermal, and chemical properties, making it a high-performance material suitable for various applications. Glass-filled nylon can withstand high temperatures, making it ideal for applications under static loads for extended periods.
Compared to traditional nylon, it offers greater strength, lower moisture absorption, and improved dimensional stability. The inclusion of glass increases the hardness and rigidity of nylon, resulting in a robust material with excellent wear resistance.
Mechanical Properties
The mechanical properties of glass-filled nylon are significantly enhanced by the addition of glass fibers. This material can achieve up to a 70% increase in tensile strength compared to traditional nylon.
The tensile properties are directly affected by the glass content, which increases the overall strength and rigidity. Flexural strength can reach values above 300 MPa, providing significant rigidity. Short glass fibers contribute to the overall strength, making the material well-suited for high-wear applications.
Parts made from glass-filled nylon exhibit enhanced fatigue strength, excellent resistance to abrasion, and superior wear resistance, which are critical for maintaining structural integrity in demanding conditions. However, the presence of glass fibers can make the material more susceptible to sudden impacts, leading to potential cracking.
Thermal Properties
The incorporation of glass fibers enhances the material’s overall strength and heat resistance, giving glass-filled nylon superior thermal properties.
Glass-filled nylon has a significantly lower thermal expansion rate compared to unfilled nylon, minimizing dimensional changes under temperature variations. The material can exhibit up to 50% lower thermal expansion, making it more stable at high temperatures.
Chemical Resistance
Glass-filled nylon offers excellent chemical resistance and minimal moisture absorption, contributing to its performance in various applications.
It can withstand exposure to a variety of chemicals, making it suitable for demanding environments. However, strong acids and bases can negatively affect its chemical resistance.
Compared to fiberglass-reinforced polypropylene, glass-filled nylon may show slightly less resistance to chemical attacks.
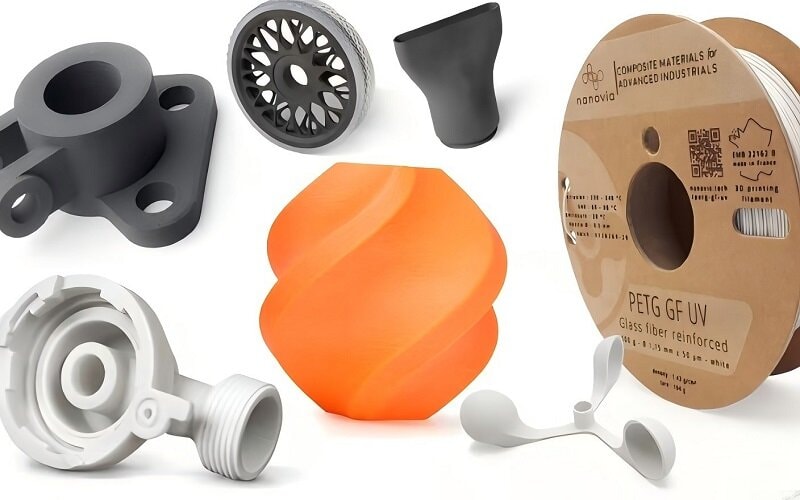
Benefits of Glass Filled Nylon
The use of glass in nylon significantly enhances its mechanical properties, making it suitable for various demanding applications.
Glass-filled nylon is generally stronger than standard nylon due to the reinforcement from glass fibers. This material possesses higher tensile strength, greater rigidity, and enhanced creep resistance compared to unfilled nylon.
Additional benefits include improved hardness, stiffness, rigidity, heat resistance, and chemical resistance, as well as excellent electrical insulation and high-temperature resistance.
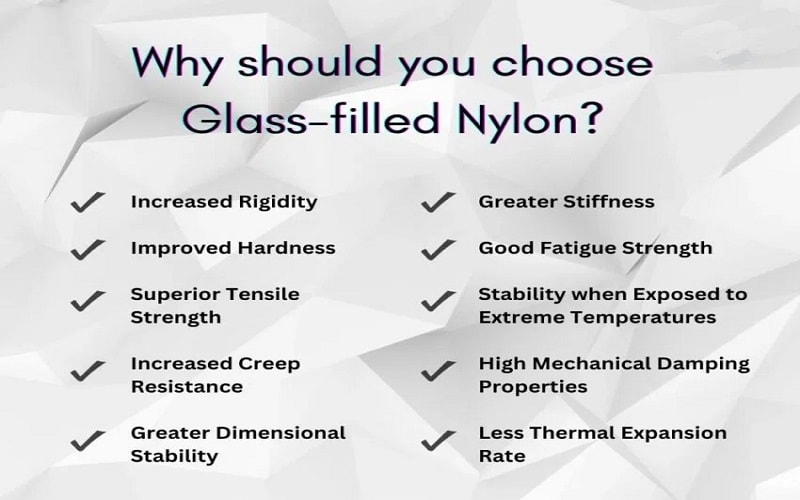
Enhanced Strength and Rigidity
Adding glass fiber reinforcement to nylon significantly improves its strength, stiffness, and toughness. The flexural strength of glass-filled nylon ranges from 50 to 300 MPa or higher, making it a robust material.
It can achieve tensile strength levels up to 70% higher than those of traditional nylon, ranging from 50 to 200 MPa. The inclusion of glass fibers increases rigidity by up to 80%, enhancing performance in load-bearing applications.
Glass-filled nylon’s superior strength-to-weight ratio makes it ideal for automotive applications, enhancing both performance and efficiency. The extra strength provided by glass-filled nylon is also advantageous in cable management applications, ensuring durability under stress.
Improved Dimensional Stability
Glass-filled nylon has greater resistance to creep, allowing it to maintain its shape under long-term load. The addition of glass fibers reduces the coefficient of thermal expansion in nylon, enhancing dimensional stability during temperature changes.
This stability is crucial for materials used in applications subjected to high dimensional stability, stress, and varying temperatures.
Superior Wear and Fatigue Resistance
Glass-filled nylon demonstrates increased durability due to the presence of glass fibers, enhancing its structural integrity and resistance to wear.
The combination of nylon and glass fibers results in a long-lasting material that can withstand harsh industrial environments.
This material provides excellent fatigue resistance, allowing components to endure repeated loading cycles without failing. Its structural composition ensures reliable performance across prolonged usage.
Limitations of Glass Filled Nylon
Despite its numerous benefits, glass-filled nylon presents some limitations. The addition of glass fibers can lead to increased brittleness, making the material more susceptible to cracking under stress.
Glass-filled nylon’s abrasiveness can cause wear on tooling and machining equipment, necessitating specialized processes to manage this characteristic. Additionally, the cost of glass-filled nylon is often higher than that of standard polymers due to the additional expense of glass fiber reinforcement.
Increased Brittleness
The addition of glass fibers to nylon significantly increases its brittleness, altering the material’s ability to withstand impact without failure. Glass-filled nylon is generally more brittle than unfilled nylon, meaning it is more prone to cracking or breaking under stress.
Abrasiveness
The abrasive nature of glass-filled nylon can lead to increased wear on machining tools and other equipment during processing. This higher abrasiveness can affect the lifespan and performance of molds used in production.
Overall, the abrasiveness necessitates careful consideration in manufacturing processes to maintain tool longevity and production efficiency.
Higher Cost
Glass-filled nylon is generally more expensive than standard nylon due to the use of additives and additional processing costs. Cost factors often include expenses for specialized manufacturing processes.
While carbon fiber-filled nylon provides superior mechanical properties, it typically comes at a higher cost than glass-filled nylon.
Common Applications of Glass Filled Nylon
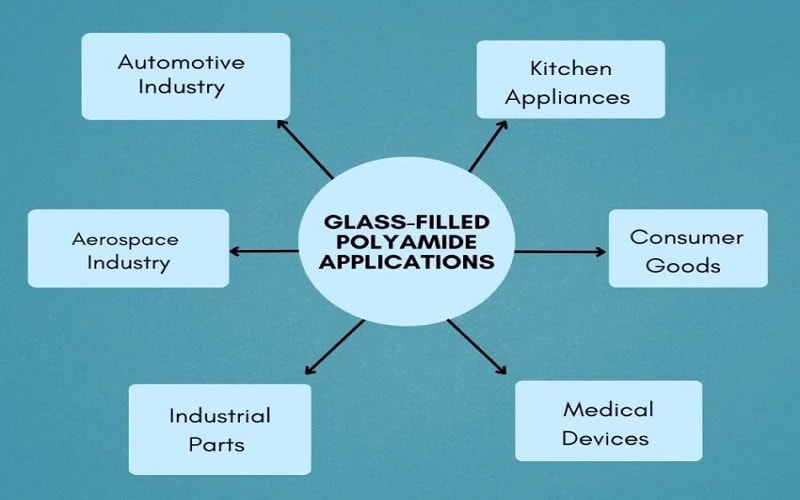
Glass-filled nylon is utilized in a wide range of applications due to its excellent properties. In the automotive industry, it is used for fuel tank caps, gears, bearings, and fan blades. The material’s dimensional stability and wear resistance make it a reliable choice for automotive applications.
In electrical components, it is used for wire housings and connectors due to its excellent insulation properties. Additionally, glass-filled nylon is used in various industrial components, consumer goods, cable ties, clips, and clamps.
Automotive Components
Glass-filled nylon is widely used in various automotive components due to its superior mechanical properties and durability. Examples of automotive parts made from glass-filled nylon include engine covers, speedometer gears, and windshield wiper parts.
The material’s durability and heat resistance make it ideal for brake fluid reservoirs, ensuring they can withstand the harsh conditions under the hood.
The use of glass-filled nylon in automotive components provides enhanced strength and heat resistance, which are critical in performance applications. Its superior strength and rigidity also contribute to reduced weight in vehicles, improving fuel efficiency and overall performance.
Electrical and Electronics
Glass-filled nylon is an excellent electrical insulator, making it a popular choice for electrical and electronic applications. It exhibits low thermal expansion and a high heat distortion point, which enhances its insulation properties. Common applications include transformer coil bobbins with a glass content of 30%, PCB connectors, automotive connectors, and MIL-spec components.
Glass-filled nylon is also frequently used in industrial control boxes for its stability and insulation properties, particularly glass filled nylon’s benefits. Additionally, glass filled nylons offer enhanced strength and durability.
Industrial Machinery
In industrial machinery, glass-filled nylon is extensively used for manufacturing precision parts and structural components that require enhanced strength and durability.
The material’s increased tensile strength and wear resistance make it suitable for demanding applications such as gears, housings, and supports.
Its excellent durability and fatigue resistance ensure a longer service life for parts manufactured from glass-filled nylon.
Manufacturing Processes for Glass Filled Nylon Parts
Glass-filled nylon can be produced through several methods. These include injection molding, CNC machining, and 3D printing. Due to its moisture sensitivity, it is essential to dry the material before processing to prevent structural weaknesses.
The increased abrasiveness of glass-filled nylon necessitates the use of specific tooling and equipment to enhance machining and processing efficiency.
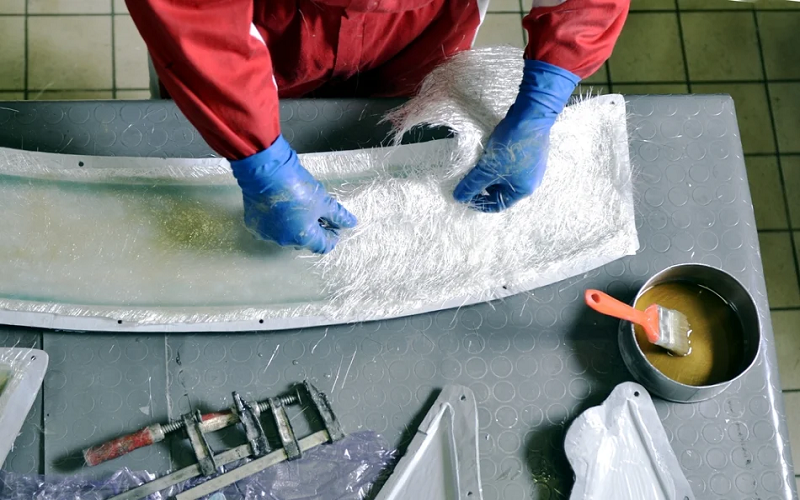
Injection Molding
The primary process for creating strong and durable parts from glass-filled nylon is injection molding. This method is widely utilized in manufacturing.
The most common grade used in this process is glass-filled nylon 66, which typically has fiber reinforcement ratios ranging from 10% to 50%. When molding glass-filled nylon, it is essential to consider increased mold wear and higher injection pressures due to the presence of glass fibers.
Molded glass-filled nylon is commonly used in automotive components, gears, and structural housings. Tools made of harder steel are recommended for the injection molding process to withstand the increased wear caused by the glass fibers.
CNC Machining
The abrasive nature of glass-filled nylon presents significant challenges during machining, leading to rapid tool wear. Glass filler causes cutting tools and inserts to wear down rapidly, increasing the need for careful machining strategies.
Using ceramic or carbide tools is recommended to combat tool wear from the glass content. Choosing the right tool material is essential for effective machining of glass-filled nylon.
3D Printing
Selective laser sintering (SLS) is the most common 3D printing method for glass-filled nylon, offering fast production of functional parts. The most common nylon grade for SLS is PA 12.
Another option for glass-filled nylon material mentioned for SLS is Nylon 3200 glass-filled material. It is recommended to use hardened steel nozzles when 3D printing with glass-filled nylon due to its abrasiveness.
Comparing Glass Filled Nylon to Other Reinforced Plastics
Glass-filled nylon generally provides superior strength and durability compared to many other polymer options. It is often contrasted with other reinforced plastics due to differences in properties such as stiffness, weight, chemical resistance, and glass filled polymers.
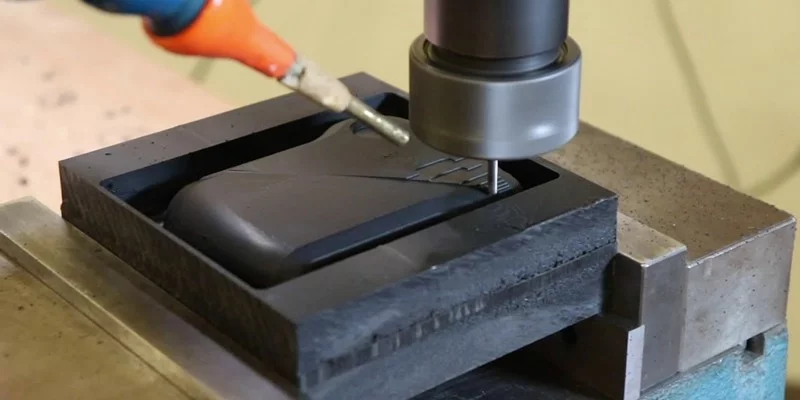
Carbon Fiber-Filled Nylon
Carbon fiber-filled nylon serves as a key alternative to glass-filled nylon, offering superior stiffness and strength. This material provides enhanced strength compared to glass-filled nylon. The weight of carbon fiber-filled nylon is lower, making it advantageous for weight-sensitive applications.
Carbon fiber-filled nylon exhibits enhanced impact resistance, outperforming glass-filled nylon in that aspect. Its higher tensile strength and enhanced thermal stability make it suitable for applications requiring significant load-bearing capability and high-temperature performance.
Fiberglass-Reinforced Polypropylene
Fiberglass-reinforced polypropylene (PP) provides excellent chemical resistance and lower weight compared to glass-filled nylon. One of the key advantages of fiberglass-reinforced polypropylene is its superior chemical resistance, making it suitable for diverse industrial applications.
This material is often lighter than glass-filled nylon, providing a significant advantage in weight-sensitive designs. Additionally, fiberglass-reinforced polypropylene exhibits lower thermal expansion compared to glass-filled nylon.
Best Practices for Working with Glass Filled Nylon
Utilizing adequate personal protective equipment (PPE) is critical to safeguard against potential health risks when working with glass-filled nylon. The material’s abrasiveness creates difficulties during machining and 3D printing. It necessitates the use of hardened tools and wear-resistant nozzles.
Also, Nylon 6 (PA 6) with 30% filler is commonly used for FDM 3D printing of glass-filled nylon.
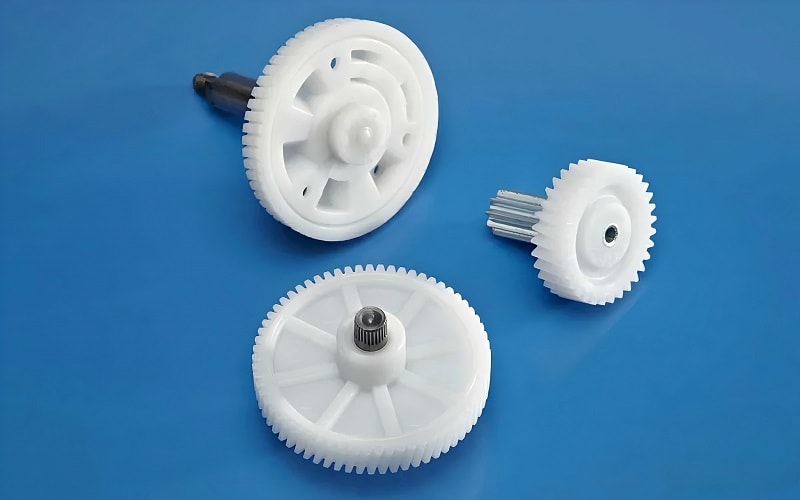
Tooling and Equipment
Ceramic or carbide tools are recommended for machining glass-filled nylon due to their superior wear resistance compared to traditional steel tools. Machining is trickier and more difficult due to the abrasive nature of glass filler.
Using slower cutting speeds can help improve machining outcomes when working with glass-filled nylon. Hardened tools are necessary to withstand the rapid wear caused by glass filler in nylon.
Material Handling and Storage
Glass-filled nylon should be stored in a clean and dry environment to prevent moisture absorption. Keeping it in a dry environment prevents moisture absorption that can affect its mechanical performance.
Ensuring a moisture-free environment is critical for preserving the performance of glass-filled nylon. Proper storage conditions are essential for maintaining the material’s properties.
Summary
Glass-filled nylon stands out in the manufacturing world due to its enhanced mechanical, thermal, and chemical properties. This material combines the strength of glass fibers with the versatility of nylon, offering greater tensile strength, rigidity, and wear resistance.
Its applications span across various industries, from automotive to electronics and industrial machinery, making it a valuable choice for demanding environments.
Despite its numerous benefits, glass-filled nylon does have limitations, including increased brittleness, abrasiveness, and higher costs. However, by following best practices for tooling, equipment, and storage, these challenges can be managed effectively.
Whether you’re an engineer, manufacturer, or industry professional, understanding the properties, benefits, and limitations of glass-filled nylon will help you make informed decisions and optimize your projects.
Frequently Asked Questions
What is glass-filled nylon, and what are its primary components?
Glass-filled nylon is a synthetic polyamide thermoplastic that consists of nylon resin combined with powdered glass or glass fibers, which significantly improve its strength and performance characteristics.
What are the main benefits of using glass-filled nylon in manufacturing?
The main benefits of using glass-filled nylon in manufacturing are its enhanced strength and rigidity, improved dimensional stability, superior wear and fatigue resistance, and excellent thermal and chemical properties. These attributes make it an ideal choice for demanding applications.
What are the common applications of glass-filled nylon?
Glass-filled nylon is widely utilized in automotive components, electrical and electronics sectors, and industrial machinery, thanks to its exceptional durability, strength, and insulating properties. This versatility makes it a preferred material in various demanding applications.
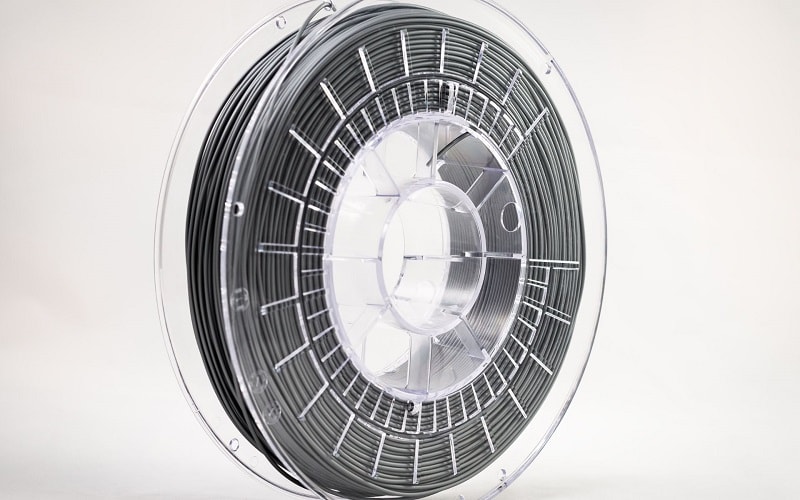
What are the limitations of glass-filled nylon?
Glass-filled nylon is limited by its increased brittleness, abrasiveness during processing, and higher costs compared to standard nylon. These factors can impact its suitability for certain applications.
How does glass-filled nylon compare to other reinforced plastics?
Glass-filled nylon offers superior strength and durability compared to many other reinforced plastics; however, alternatives like carbon fiber-filled nylon and fiberglass-reinforced polypropylene may provide advantages in weight and chemical resistance.