Plastic custom parts are components made to meet specific requirements in different industries. They are often manufactured using techniques like injection molding and extrusion.
This article explores these manufacturing methods, material options, and the benefits of using custom plastic parts.
Custom Plastic Part Manufacturing Processes
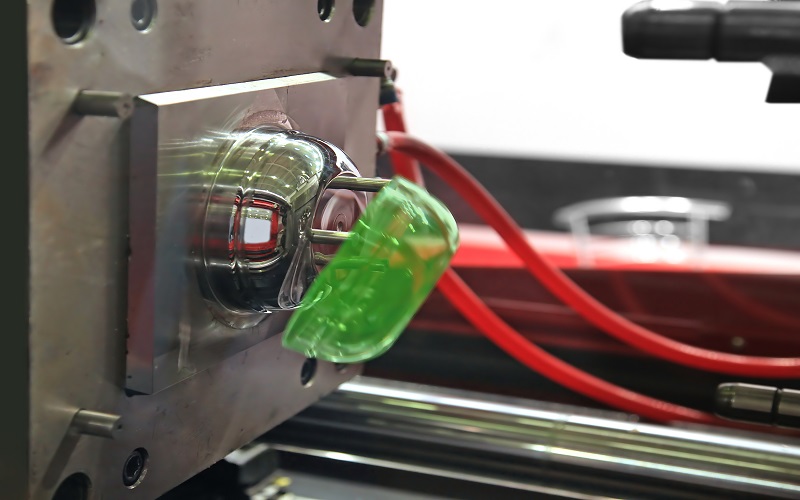
Custom plastic parts can be manufactured through various processes, including plastic manufacturing processes and other plastic manufacturing processes, each tailored to meet specific application needs.
These methods range from low-volume prototypes to large-scale production runs, ensuring flexibility and adaptability in the manufacturing process. The primary processes include injection molding, blow molding, and plastic extrusion, each offering unique benefits.
These manufacturing techniques not only enhance the efficiency of production but also allow for the creation of complex geometries and high-quality parts suitable for diverse industries.
Whether you’re looking to produce robust automotive components or lightweight consumer goods, selecting the appropriate manufacturing process is crucial for achieving the desired outcome.
Injection Molding Process
Injection molding is a cornerstone in custom plastic part manufacturing, known for its precision and high production speed. This process involves injecting molten plastic into a mold cavity, where it cools and solidifies into the desired shape. The plastic injection molding process is highly efficient, allowing for the production of large volumes of parts with consistent quality and minimal waste.
The advantages of injection molding extend beyond speed and accuracy. This method offers unparalleled design versatility, enabling the creation of intricate and detailed components. From automotive parts to packaging items, injection molded parts are integral to numerous industries due to their reliability and cost-effectiveness.
Blow Molding Techniques
Blow molding is another vital technique used in custom plastic manufacturing, particularly for producing lightweight hollow products. This process involves inflating a hollow plastic tube, known as a parison, into a mold to create items such as bottles and containers.
Blow molding is highly cost-effective for high-volume production, making it ideal for industries that require large quantities of hollow plastic parts.
Plastic Extrusion Methods
Plastic extrusion is a manufacturing method that excels in producing continuous profiles like tubing and gaskets. In this process, plastic material is forced through a die, resulting in a consistent cross-section along the length of the profile.
This method is advantageous for applications requiring uniformity in shape and size, making it suitable for a variety of industrial applications.
Material Selection for Custom Plastic Parts
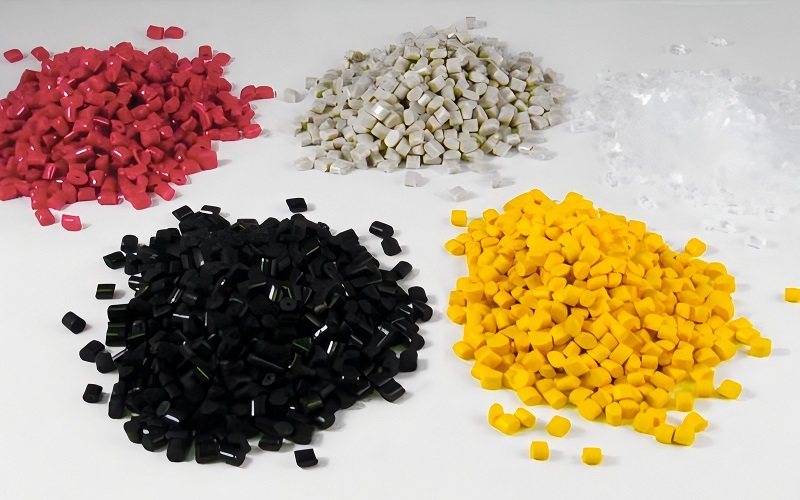
Choosing the right materials for custom plastic parts is crucial to their performance and functionality. The material selection process involves understanding the specific requirements of the application and selecting materials that meet those needs. Custom plastic parts can be designed with various materials and finishes, catering to diverse sectors such as medical, military, and industrial.
Manufacturers with strong engineering support can assist in material selection and design optimization, ensuring that the chosen materials meet safety and performance criteria. This collaborative approach helps in creating durable, high-quality parts tailored to specific applications.
Common Plastics Used
Common plastics such as High-Density Polyethylene (HDPE), Polypropylene, and PVC are frequently used in custom plastic part manufacturing due to their beneficial properties. HDPE is known for its strength-to-weight ratio and impact resistance, making it suitable for applications like plastic pipes and cutting boards.
Polypropylene offers chemical resistance, high-temperature tolerance, and affordability, which makes it ideal for food-safe applications and consumer products. PVC’s chemical resistance and durability make it a popular choice for plumbing and construction applications.
Additionally, materials like Nylon 6, Nylon 66, and Polycarbonate are valued for their tensile strength, heat resistance, and transparency, respectively, making them suitable for automotive components and electronic housings. Understanding these common plastics and their applications is essential for selecting the right material for your custom plastic parts.
Thermoplastic Materials
Thermoplastic materials, such as Polyphenylsulfone (PPSU) and Acrylonitrile Butadiene Styrene (ABS), offer exceptional performance and versatility. PPSU is highly resistant to heat and chemical exposure, making it ideal for demanding environments. ABS, on the other hand, is known for its impact resistance and durability, making it suitable for a wide range of applications, including automotive and consumer products.
Selecting the right thermoplastic material ensures the longevity and effectiveness of custom plastic parts in various applications.
Additives for Enhanced Properties
Additives play a crucial role in enhancing the properties of custom plastic parts. By incorporating ribbing and other structural reinforcements, the strength and wear resistance of plastic parts can be significantly improved. Additionally, designing for wear resistance involves optimizing shapes to reduce stress concentration and improve material flow.
Protective coatings and surface treatments can also be applied to enhance the durability and longevity of custom plastic components.
Advantages of Custom Plastic Parts
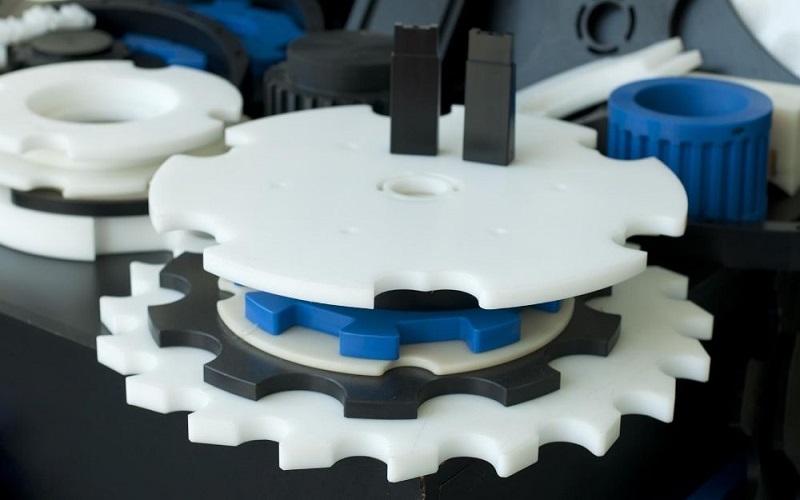
Custom plastic parts offer numerous benefits, making them a preferred choice across various industries. Here are some key advantages:
- Cost-effective, providing significant savings in manufacturing processes
- Rapid production speeds enabled by setup optimization and automation
- High accuracy and consistency in custom plastic part manufacturing
Moreover, the ability to customize parts to specific needs enhances their value and applicability in diverse sectors, from automotive to medical.
Cost Efficiency
The cost efficiency of custom plastic parts is a major advantage for manufacturers. High-volume production runs in injection molding lead to substantial cost savings, making these parts more affordable. Streamlined production processes contribute to competitive pricing, enhancing the overall cost-effectiveness of custom plastic parts.
This makes them an attractive option for industries looking to optimize their production costs and achieve significant cost savings.
High Accuracy & Repeatability
High accuracy and repeatability are critical benefits of custom plastic parts. Injection molding, for example, can achieve a tolerance level as precise as 0.005 inches, ensuring that parts meet exact specifications.
This precision is essential for applications where dimensional accuracy is crucial, ensuring that custom plastic parts fit and function as intended.
The consistent quality achieved through these manufacturing processes makes it possible to produce custom plastic parts a reliable choice for various applications.
Versatility in Applications
The versatility of custom plastic parts is another significant advantage. These parts find applications in diverse industries, including automotive, healthcare, and consumer goods. Materials like ABS and Polypropylene are used in automotive parts, electronic housings, and medical devices, showcasing their adaptability.
The ability to customize shapes, materials, additives, colors, and finishes further enhances the versatility of custom plastic parts, making them suitable for a wide range of applications.
Quality Assurance in Custom Plastic Manufacturing
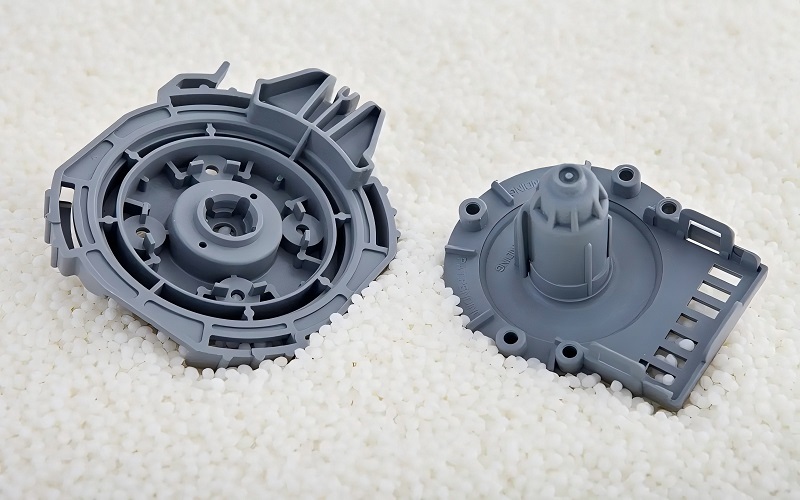
Quality assurance is paramount in custom plastic manufacturing to ensure that parts meet exact specifications and perform reliably. Effective quality control protocols minimize defects and ensure that custom plastic products meet the highest standards.
Advanced measuring instruments and in-house metrology services play a crucial role in maintaining precision during production, reducing delays and ensuring timely delivery of quality parts.
ISO Certifications
ISO certifications are a testament to a manufacturer’s commitment to quality. ISO 9001:2015, for instance, ensures that manufacturers maintain a structured approach to quality management, enhancing customer satisfaction.
These certifications help establish trust and demonstrate compliance with international quality standards, ensuring consistent and reliable production of custom plastic parts.
Rigorous Testing Procedures
Rigorous testing procedures are essential to ensure that custom plastic parts meet exact specifications.
Xometry’s comprehensive testing process includes plastic prototyping services like 3D printing and urethane casting to validate designs before full-scale production.
The injection molding process itself is known for its consistent and repeatable quality, achieving an accuracy level of up to 0.005 inches.
These stringent testing protocols ensure the production of high-quality custom plastic parts.
Choosing the Right Manufacturing Partner
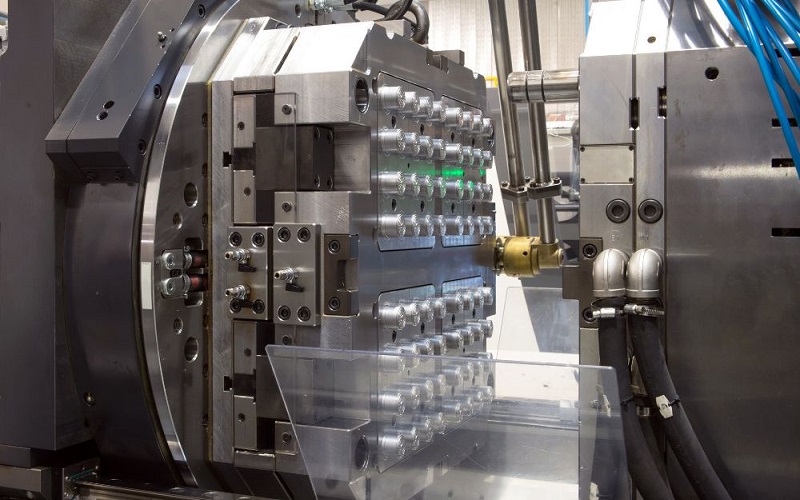
Selecting the right manufacturing partner is crucial for the success of custom plastic part projects. A reliable partner should offer comprehensive support, from design optimization to material selection, ensuring the manufacturability and quality of custom parts.
The qualification process for suppliers, ISO certifications, and a proven track record are key factors to consider when choosing a manufacturing partner. Collaboration between teams can significantly enhance the efficiency and effectiveness of the production process.
Expertise in Design and Engineering
Expertise in design and engineering is essential for optimizing the manufacturability of custom plastic parts. Engineers play a critical role in identifying and addressing potential design issues, ensuring that parts are both functional and cost-effective. During the prototyping phase, experienced engineering teams collaborate with clients to refine designs, maximizing the quality and durability of the final product.
Evaluating manufacturers for their forming techniques and advanced equipment is also crucial for supporting design and engineering needs.
Proven Track Record
A proven track record is indicative of a manufacturing partner’s reliability and quality of service. Client testimonials can provide valuable insights into the manufacturer’s performance and ability to deliver high-quality custom plastic parts consistently.
Partnering with a trusted manufacturer ensures that your projects are completed efficiently, cost-effectively, and to the highest standards.
Cost Considerations for Custom Plastic Parts
Cost considerations play a significant role in custom plastic part manufacturing. Factors such as tooling costs, production volume, and material selection can greatly impact overall expenses. Understanding these cost factors helps in pricing custom plastic parts accurately and managing expenses effectively.
Automation of tasks and efficient manufacturing processes lead to reduced labor costs, enhancing the cost-effectiveness of custom plastic parts.
Tooling Costs
Tooling costs are a major component of custom plastic part production expenses. Injection molding typically incurs high tooling costs due to the need for custom-built molds. However, thermoforming offers a more affordable alternative with lower tooling costs and greater flexibility for modifications.
Understanding the impact of tooling costs is crucial for managing the overall budget of custom plastic part projects.
Production Volume Impact
Production volume significantly impacts the cost efficiency of custom plastic parts. High-volume production runs benefit from economies of scale, reducing the per-unit cost and making the parts more affordable. However, for smaller quantities, optimizing design for manufacturability and selecting cost-effective materials are essential strategies to manage expenses.
Understanding these dynamics helps in planning and budgeting for custom plastic part manufacturing projects.
Efficient Production Timelines
Achieving efficient production timelines is crucial in custom plastic manufacturing to meet project deadlines and market demands. Rapid turnaround times enable manufacturers to respond swiftly to urgent needs without compromising on quality.
Factors such as prototyping and tooling can affect lead times, but streamlined manufacturing processes can significantly reduce delays and improve overall production efficiency.
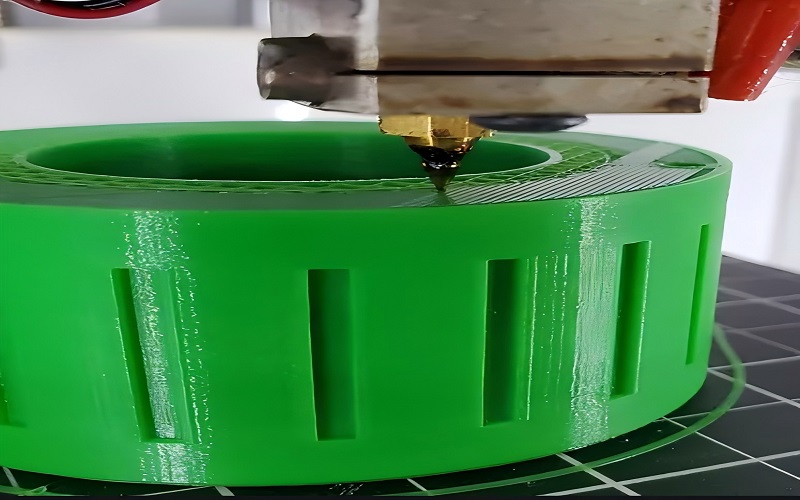
Rapid Prototyping Services
Rapid prototyping services play a pivotal role in accelerating the production of custom plastic parts. By quickly creating functional prototypes, manufacturers can validate designs and make necessary adjustments early in the development process.
Engaging manufacturing partners early in the design phase ensures a more efficient development process, leading to faster production timelines and high-quality final products.
Streamlined Manufacturing Processes
Streamlined manufacturing processes are essential for reducing lead times and improving production efficiency. By focusing on efficient design and manufacturing practices, manufacturers can enhance the performance of the final product.
Implementing effective design strategies and optimizing production cycles lead to a more efficient and cost-effective manufacturing process.
Wear Resistance and Durability
Wear resistance and durability are critical factors in the performance of custom plastic parts. These properties ensure that parts can withstand mechanical actions and harsh conditions without losing their functionality. Custom plastic components can be designed with specific features to enhance their wear resistance, thereby increasing their operational lifespan.
Non-destructive testing procedures, including stress tests, are employed to verify the thickness and surface properties of custom plastic components, ensuring they meet client specifications.
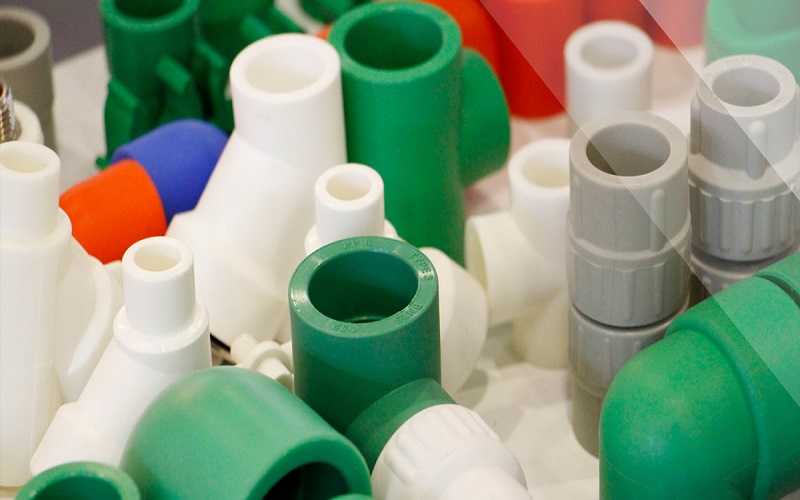
Material Choices for Wear Resistance
Selecting the right materials is crucial for enhancing the wear resistance of custom plastic parts. Materials like Nylon thermoplastics and PEEK are known for their exceptional wear resistance and ability to perform under high-stress conditions.
Other materials, such as tungsten carbide and Stellite cobalt-chromium, also offer superior wear resistance, making them suitable for demanding applications.
Choosing the right plastic materials ensures the durability and longevity of custom plastic parts in various industrial environments.
Design Considerations
Designing custom plastic parts with wear resistance in mind is essential to extend their lifespan and enhance performance. Techniques such as optimizing geometry and incorporating structural reinforcements can significantly improve wear resistance. Selecting materials known for their hardness and toughness is also crucial for enhancing the durability of custom plastic parts.
By combining effective design strategies with the right material choices, manufacturers can ensure that custom plastic parts perform reliably in demanding applications.
Summary
In conclusion, custom plastic parts offer a wealth of advantages across various industries, from cost efficiency and high accuracy to versatility and durability. Understanding the manufacturing processes, material selection, and quality assurance practices is crucial for producing high-quality custom plastic parts that meet specific application needs.
By partnering with experienced manufacturers and focusing on efficient production timelines, businesses can achieve significant cost savings and deliver reliable, high-performance products to the market.
Embrace the potential of custom plastic parts to enhance your manufacturing capabilities and stay ahead in a competitive market.
Frequently Asked Questions
What are the main manufacturing processes for custom plastic parts?
The primary manufacturing processes for custom plastic parts are injection molding, blow molding, and plastic extrusion, each tailored to specific applications and offering distinct advantages. Selecting the right method is crucial for achieving optimal results in your project.
How do I choose the right material for my custom plastic parts?
Selecting the appropriate material for your custom plastic parts is crucial and should be based on the specific requirements of your application. Common options such as HDPE, Polypropylene, PVC, PPSU, and ABS each possess unique properties that align with different functional needs.
What are the advantages of using custom plastic parts?
Custom plastic parts provide significant benefits including cost efficiency, high accuracy, and versatility across various industries such as automotive and healthcare. Their repeatability ensures consistent quality, making them an optimal choice for many applications.
How important is quality assurance in custom plastic manufacturing?
Quality assurance is essential in custom plastic manufacturing, as it ensures that products meet precise specifications and function reliably.
Implementing effective quality assurance protocols and rigorous testing is vital for maintaining high standards and reducing defects.
What factors should I consider when choosing a manufacturing partner for custom plastic parts?
Choose a manufacturing partner based on their design and engineering expertise, track record, ISO certifications, and comprehensive support in material selection and design optimization.
A reliable partner guarantees the quality and manufacturability of your custom plastic parts.