Silicone rubber is a durable and flexible material made from silicon, oxygen, carbon, and hydrogen. Known for its resistance to extreme temperatures and environments, it is widely used in industries like medical and automotive.
This guide explores what silicone rubber is, its types, manufacturing processes, and applications. Overall, silicone rubber is an essential material in various fields due to its unique properties.
What Is Silicone Rubber?
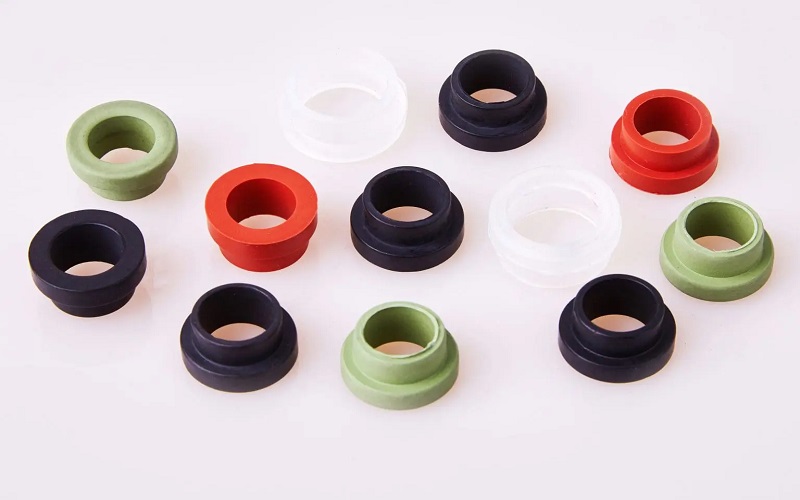
Silicone rubber is a versatile elastomer distinguished by a polymer chain composed of silicon, oxygen, carbon, and hydrogen. This unique chemical structure, featuring a backbone of silicon-oxygen (Si-O) chains, imparts exceptional flexibility and thermal stability to the material.
Such a configuration allows silicone rubber to maintain its mechanical properties across a broad temperature range, making it invaluable in various industrial applications, including processes like thermoplastic injection molding where precise molding of durable components is required.
Notably, silicone rubber exhibits remarkable temperature resistance, chemical resistance, and biocompatibility. These properties render it suitable for environments that demand durability and reliability, such as medical devices, automotive components, and consumer products. Whether it’s enduring the heat under a car’s hood or remaining stable in a sterilized medical setting, silicone rubber proves its mettle time and again.
Types of Silicone Rubber
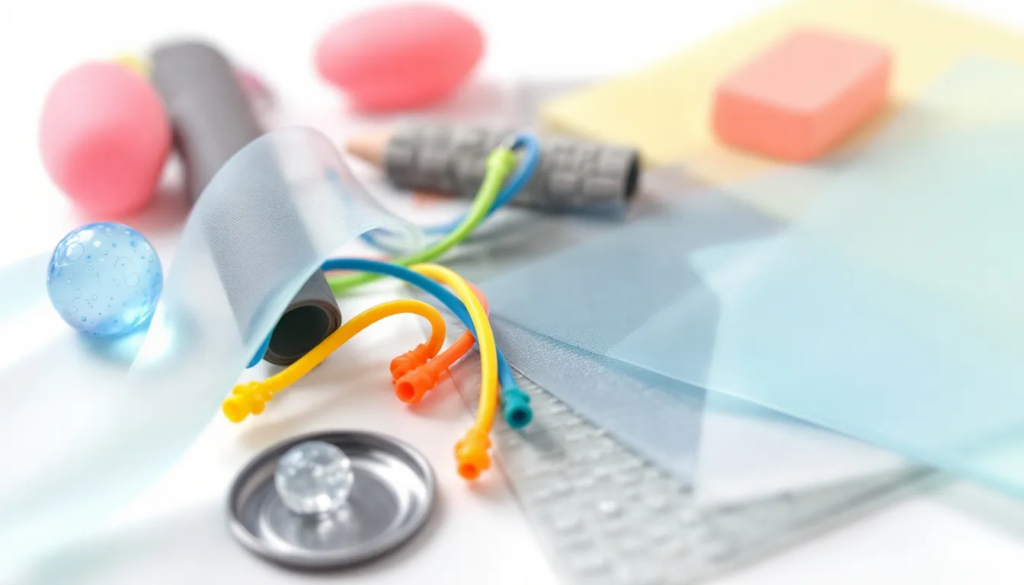
Silicone rubber is not a one-size-fits-all material; it comes in several types, each tailored for specific applications. Liquid Silicone Rubber (LSR) stands out for its low viscosity and higher curing temperature, making it ideal for automated injection molding processes. LSR’s ability to fill intricate mold designs with precision makes it a preferred choice in industries that demand detailed and complex components.
High Consistency Rubber (HCR), also known as Millable Type Silicone Rubber, consists of silicone polymer and silica, enhanced with various additives. HCR is particularly suited for applications that require high mechanical strength and durability. On the other hand, Room Temperature Vulcanizing (RTV) silicone rubbers provide flexibility for applications that do not necessitate high-temperature curing.
Each type of silicone rubber—LSR, HCR, and RTV—possesses unique characteristics that cater to different industrial needs. For instance, LSR is frequently used in automotive lighting components due to its heat resistance and environmental durability. Understanding these distinctions is crucial for selecting the right material for your specific application.
The Manufacturing Process of Silicone Rubber
The journey of transforming liquid silicone rubber into functional components involves sophisticated manufacturing processes. Among the most prominent methods are liquid injection molding and compression molding. Each process has its unique advantages and applications, depending on the product characteristics, batch sizes, and economic considerations.
Liquid silicone rubber injection molding is prevalent in industries such as medical, automotive, and consumer goods due to its ability to produce high-precision and temperature-resistant items. This method employs advanced technology to ensure consistent product quality and high production efficiency through liquid silicone injection molding, liquid silicone rubber material, liquid silicone rubber molding, and liquid silicone rubbers.
On the other hand, compression molding is particularly effective for producing larger parts that cannot be made using extrusion techniques.
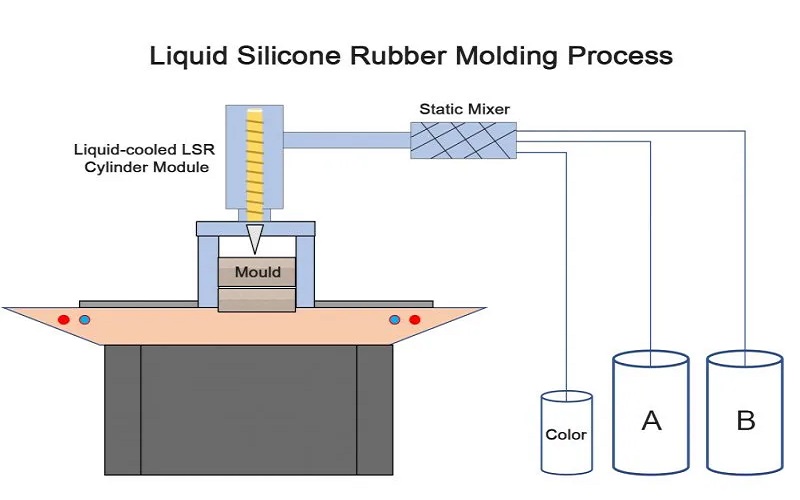
Liquid Injection Molding Process
Liquid injection molding stands out for its ability to produce intricate, temperature-resistant items with high precision and design flexibility. The process begins with the uncured liquid silicone, a combination of base-forming silicone and a platinum catalyst, which is noted for its low viscosity and ease of pumping. This mixture is then injected into a preheated mold using a liquid injection molding machine, where pressure is maintained to fill the mold cavity progressively.
This method is particularly cost-effective for high-volume production, minimizing waste while ensuring consistent product quality. The two-component platinum-curing process silicone is mixed and pumped into the mold using a dynamic or static mixer, ensuring thorough and even distribution. The entire process is automated, making it ideal for large-scale manufacturing.
The precision and efficiency of liquid silicone rubber injection molding make it an invaluable process in creating components that require detailed designs and stringent quality standards. Industries ranging from medical to automotive rely on this method to produce parts that meet their exacting requirements.
Compression Molding Process
Compression molding is another vital process in the manufacturing of silicone rubber components. This method involves placing pre-vulcanized silicone between heated mold halves, which are then sealed and compressed to form the desired shape. The heated mold ensures that the silicone cures and takes on the intended form.
This process is particularly effective for producing larger parts that are not feasible to manufacture using extrusion techniques. The compression molding process allows for the creation of robust and durable components, making it suitable for a variety of industrial applications.
Properties of Silicone Rubber
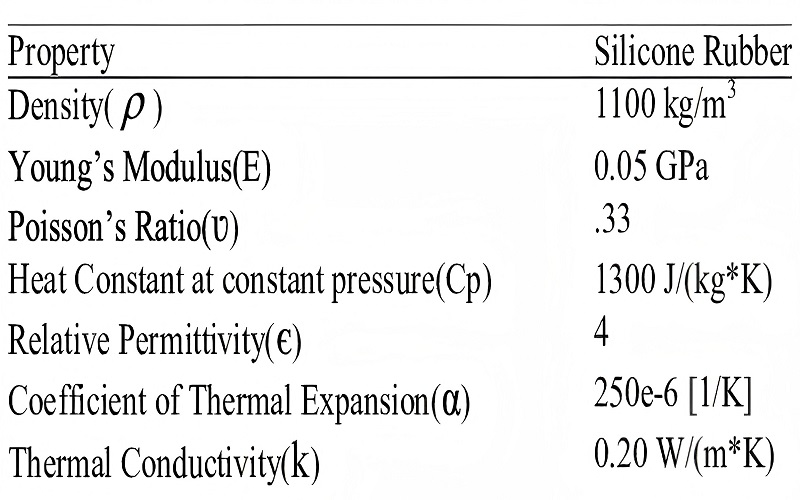
Silicone rubber is renowned for its remarkable properties, which make it a preferred material in numerous applications. One of its most notable features is its ability to withstand extreme temperatures, maintaining its properties from -100°C to 305°C. This high thermal stability ensures that silicone rubber retains its structure and flexibility across a wide range of temperatures.
Additionally, silicone rubber exhibits exceptional resistance to a variety of chemicals, oils, and solvents, making it suitable for harsh chemical environments. Its mechanical properties remain consistent, offering excellent insulating properties and durability.
This versatility is why silicone rubber is trusted in critical applications, from medical devices to automotive components.
Applications of Silicone Rubber
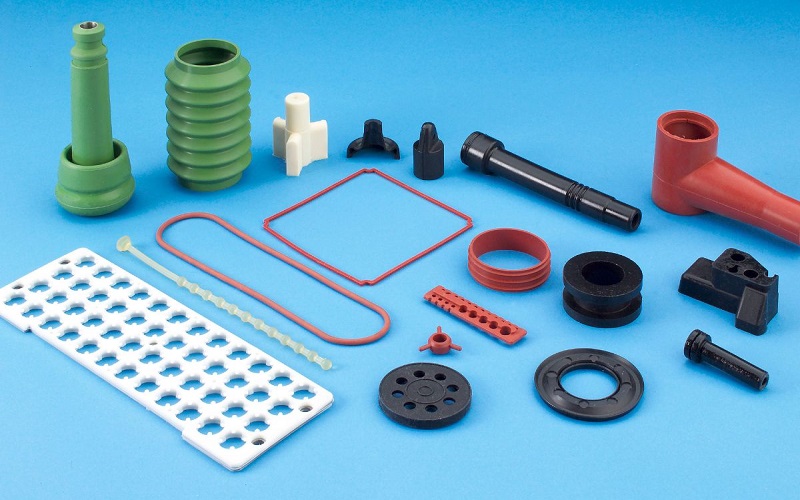
The applications of silicone rubber are as diverse as its properties. Its longevity and ability to endure harsh conditions make it invaluable in a wide range of industries. From sealing components in the aerospace sector to medical devices and automotive parts, silicone rubber proves its worth in every application.
Specific applications are explored in the following subsections.
Medical Applications
Silicone rubber’s biocompatibility and compliance with FDA standards make it a top choice for medical applications. It is commonly used in catheters and drug delivery systems due to its compatibility with human tissue and resistance to bacteria. This material is tasteless, odorless, and can be sterilized, ensuring it meets the rigorous demands of the medical industry.
Moreover, silicone rubber is employed in a variety of medical devices, confirming its versatility and effectiveness. Common quality standards for silicone products include ISO 10993 for medical device biocompatibility and FDA regulations for manufacturing practices. These standards ensure that silicone rubber products are safe and reliable for medical use.
Automotive Components
In the automotive industry, liquid silicone rubber is used for:
- Seals
- Connectors
- Assemblies
- Electronic covers
- A/C vent cushions
This material’s mechanical properties make it ideal for components that need to withstand high temperatures and exposure to harsh environments. Parts made from LSR are suitable for use under the hood of cars, where they encounter high temperatures and proximity to engines.
Using liquid silicone for windshield wiper blades, for instance, provides a longer lifespan and avoids scratching the windshield compared to traditional rubbers. Additionally, LSR is utilized in wire harness seals, connectors, bellows, gaskets, vibration dampeners, housings, and sensors, showcasing its versatility in automotive applications.
Consumer Products
Silicone rubber’s excellent weathering resistance, including protection against UV light, ozone, and other environmental factors, makes it ideal for consumer products. Items such as kitchen tools, baby products, and personal care items are often made from liquid silicone rubber due to its durability and safety.
This material is non-toxic and water-repellent, contributing to its appeal in various consumer goods. Whether it’s a spatula that can withstand high cooking temperatures or a baby bottle nipple that is safe for infants, silicone rubber proves to be an excellent choice for consumer products.
Advantages of Using Silicone Rubber
The advantages of using liquid silicone rubber (LSR) are manifold. The lsr injection molding process offers high-volume production, consistent part quality, and improved productivity. Fully automated LSR injection molding cells enhance precision and production capabilities, ensuring that each component meets stringent quality standards.
Moreover, LSR molding produces nearly zero material waste, eliminates trimming operations, and results in significant savings in material costs. Successful molding of LSR components requires advanced technology and a robust quality system, ensuring consistent output and high-quality products.
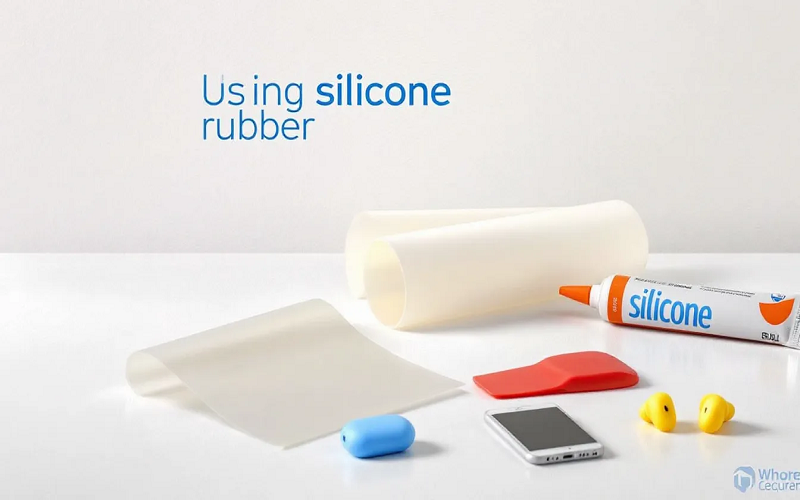
Design Considerations for Silicone Rubber Parts
Designing silicone rubber parts involves several critical considerations. Part geometry, heat application, filling, curing, tolerances, and wall section variations are all essential factors. The recommended minimum draft angle for parts designed for liquid injection molding is between 0.5° to 5°.
These considerations ensure that the parts are efficiently produced and meet the desired specifications. Proper design can significantly impact the functionality and durability of the final product, making it crucial to understand and implement these guidelines effectively.
Quality Standards for Silicone Rubber Products
Maintaining high-quality standards is paramount in the production of silicone rubber products. Key certifications include ISO 9001, ISO 13485, and IATF 16949, which demonstrate a commitment to quality and regulatory compliance. SIMTEC, for instance, holds these certifications, ensuring that their products meet stringent quality requirements.
Advanced technologies are employed to ensure high purity and consistent performance in silicone products. With a rejection rate of less than 1%, companies like InterSil exemplify the high standards expected in the industry.
Custom Silicone Rubber Solutions
Custom silicone rubber solutions offer businesses the flexibility to tailor materials to meet specific requirements and performance standards. There are millions of combinations of materials and finishes available, enabling extensive customization.
SIMTEC provides a range of services, including prototyping, high-volume LSR production, LSR multi-shot, and LSR over-molded parts production. Leveraging advanced technology and expertise is crucial for successfully implementing custom silicone rubber solutions.

Summary
Silicone rubber, with its diverse types, remarkable properties, and wide-ranging applications, stands as a cornerstone of modern manufacturing. From the intricate processes involved in its production to the stringent quality standards it must meet, this material demonstrates exceptional versatility and reliability.
As we’ve explored, the advantages of using silicone rubber are numerous, making it an invaluable resource across various industries. Embracing this material’s potential can lead to innovative solutions and superior products, solidifying its place in the future of manufacturing.
Frequently Asked Questions
What are the main types of silicone rubber?
The main types of silicone rubber include Liquid Silicone Rubber (LSR), High Consistency Rubber (HCR), and Room Temperature Vulcanization (RTV) silicone rubbers. Each type has distinct properties suited for various applications.
What makes liquid silicone rubber ideal for injection molding?
Liquid silicone rubber is ideal for injection molding due to its low viscosity, which enables it to fill intricate mold designs effectively, along with its higher curing temperature that supports automated processes. This combination ensures precision and efficiency in manufacturing.
Why is silicone rubber used in medical applications?
Silicone rubber is utilized in medical applications due to its biocompatibility, resistance to bacteria, and ability to be sterilized, ensuring safety and efficacy in healthcare settings. Its tasteless and odorless properties further enhance its suitability for such uses.
How does liquid silicone rubber benefit the automotive industry?
Liquid silicone rubber significantly benefits the automotive industry by providing durability and reliability for components exposed to high temperatures and harsh environments, such as seals, connectors, and gaskets. This enhances overall vehicle performance and longevity.
What are the quality standards for silicone rubber products?
The quality standards for silicone rubber products include ISO 9001, ISO 13485, and IATF 16949, which ensure high purity and consistent performance. Compliance with these standards is essential for maintaining product quality and reliability.