Why is polypropylene for injection molding the go-to material? Polypropylene offers flexibility, strength, and cost-efficiency.
This article will explore its unique properties, the injection molding process, and key considerations for using polypropylene for injection molding in diverse applications.
Understanding Polypropylene (PP)
Polypropylene, often abbreviated as PP, is a thermoplastic polymer made from propylene monomers. As a thermoplastic addition polymer, polypropylene can be melted and reformed multiple times without significant degradation, making it an ideal material for injection molding, particularly when using cold runner molds to manage the flow of molten plastic efficiently.
The chemical structure of polypropylene, represented by the formula (C3H6)n, contributes to its remarkable properties, including toughness, flexibility, and resistance to fatigue and chemical corrosion. Additionally, it is a type of plastic polymer that showcases these beneficial characteristics.
There are two main types of polypropylene: homopolymers and copolymers. Homopolymers consist of polymerized propylene monomers, while copolymers contain a combination of propylene and other monomers, such as ethylene. Impact copolymers, which have a significant ethylene content, offer enhanced impact resistance, making them suitable for applications requiring higher durability.
Polypropylene’s versatility extends to various applications, from everyday items like food trays, cups, and plates, to industrial and medical components such as outdoor furniture, kitchenware, piping systems, and medical supplies. Its chemical resistance and compatibility with steam sterilization make it particularly suitable for medical uses.
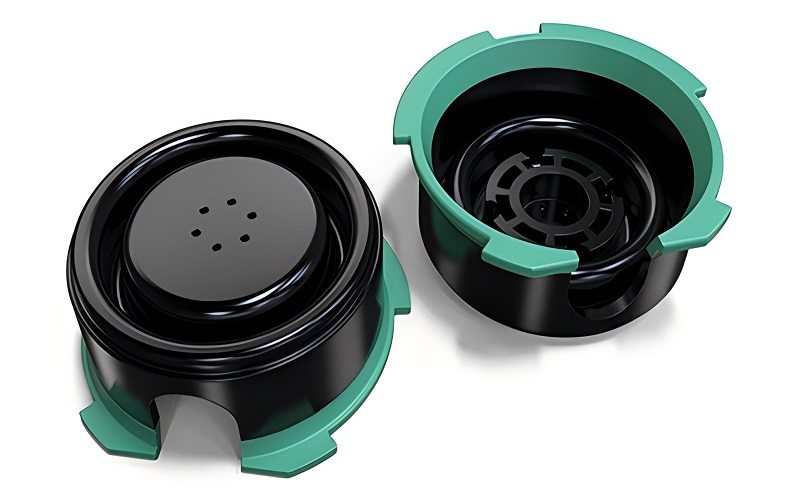
Why Choose Polypropylene for Injection Molding?
Polypropylene’s cost-effectiveness and easy availability make it a preferred choice for injection molding. Its low melt viscosity facilitates quicker mold filling, reducing cycle times and production costs in injection molding plastic processes.
This means manufacturers can produce thousands or even millions of identical parts with a single mold, ensuring consistent quality and efficiency.
The material’s durability and resistance to fatigue and chemical corrosion further enhance its appeal. Polypropylene’s unique qualities, such as flexibility and strength, allow it to be used in a wide range of applications, from automotive parts to consumer goods and medical supplies. These properties make polypropylene injection molding a practical and efficient method for producing high-quality plastic components.
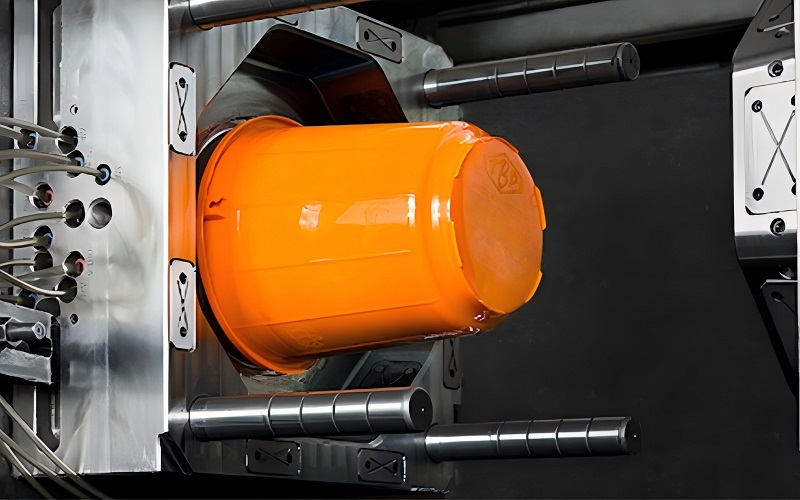
The Injection Molding Process for Polypropylene
The pp injection molding process for polypropylene involves several critical steps:
- Feeding
- Melting and plasticization
- Injection
- Pressure holding and cooling
- Ejection
Each step plays a vital role in ensuring the production of high-quality injection molded products.
Let’s take a closer look at each stage of the process.
Feeding
The feeding process begins with dispensing polypropylene pellets into the hopper, which funnels them into the barrel for processing. This stage prepares the material for melting and plasticization.
The consistent and efficient feeding of pellets is essential for maintaining the overall quality of the final product.
Melting and Plasticization
Once the polypropylene pellets enter the barrel, they are gradually warmed by the heating bands encircling the barrel. The rotating screw inside the barrel propels the pellets forward, melting them progressively. The low melt viscosity of polypropylene is particularly beneficial during this stage, as it allows for smooth and efficient melting.
The ideal temperature range for melting polypropylene pellets is between 450 to 500°F. Unlike some other plastics, polypropylene does not need to be dried before injection molding, simplifying the process. Proper melting and plasticization ensure that the material is in the right condition for the subsequent injection phase.
Injection
During the injection phase, the molten polypropylene is introduced into the injection mold cavity through the sprue and runner system. The sprue serves as the entry point, guiding the material into the mold cavity efficiently.
The gate allows the molten material to enter the mold cavity, ensuring proper fill. Accurate attachment between the nozzle tip and the sprue base is crucial to prevent material leaks and ensure consistent quality.
Ensuring the proper injection molding conditions, including the right injection pressure and speed, produces high-quality molded parts. Any deviation can lead to defects, impacting the final product’s quality and performance.
Pressure Holding and Cooling
Once the mold cavity is filled, maintaining pressure during the cooling phase helps ensure that the molded parts achieve their intended shape without defects. The screw continues to force molten plastic into the mold, compensating for shrinkage as the material cools and solidifies.
The cooling temperature for ejected polypropylene molded parts is around 54°C, and the cooling process is essential for preserving the structural integrity and quality of the final product.
Ejection
The final step in the polypropylene injection molding process is ejection. Once the mold is unlocked, ejector pins push the finished part out of the mold. The piece and runner are then dropped outside, completing the ejection process.
Proper ejection avoids damaging the part and ensures it is ready for subsequent use or packaging.
Key Parameters in Polypropylene Injection Molding
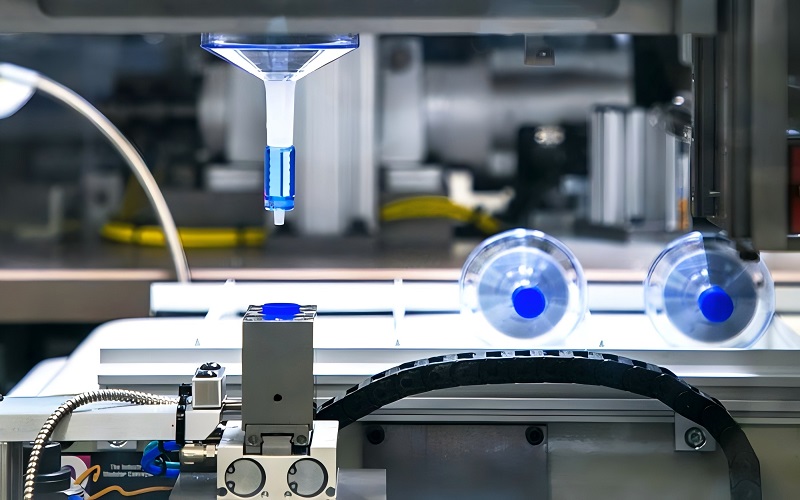
Several key parameters influence the success of polypropylene injection molding. These include mold temperature, injection pressure, and injection speed. Understanding and controlling these parameters are critical for achieving consistent quality and performance in the final product.
Let’s explore these parameters in more detail.
Optimal Mold Temperature
The recommended temperature range for molds during polypropylene injection is between 40 to 80 degrees Celsius. Maintaining the proper mold temperature significantly influences the crystallization of polypropylene, affecting the final product’s surface finish and performance.
Optimal crystallinity leads to better surface quality and overall product integrity.
Injection Pressure
The recommended injection pressure for polypropylene injection molding is around 180 MPa. The recommended injection pressure for polypropylene is around 180 MPa to avoid surface imperfections and ensure structural integrity. Inadequate pressure can lead to defects, compromising the quality and performance of the final product.
Injection Speed
Fast injection speeds minimize internal stresses and enhance part quality. However, balancing the speed with processing conditions avoids issues like burning, thermal decomposition, and surface defects.
A fast speed helps achieve proper mold filling, but it must be carefully controlled to maintain the quality and integrity of the final product.
Common Applications of Polypropylene Injection Molding
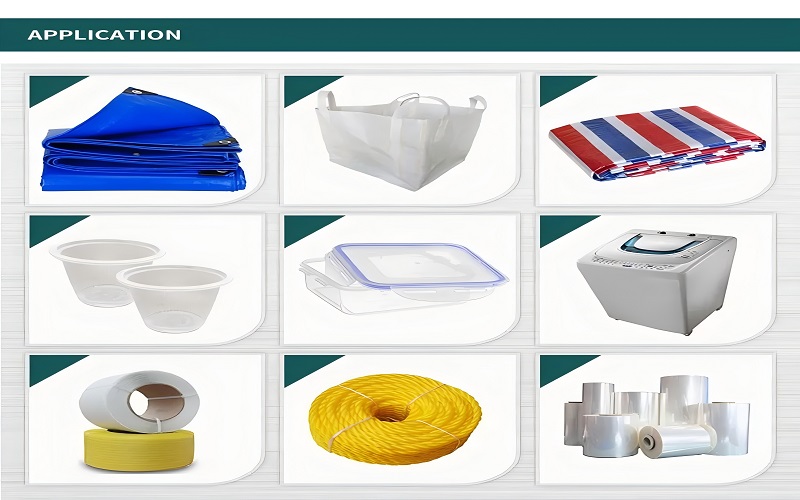
Polypropylene injection molding is widely used across various industries due to its versatility, durability, and cost-effectiveness. Common applications include automotive parts, consumer goods, plastic injection molding, and medical supplies, particularly in pp injection molding and polypropylene pp injection molding.
Let’s explore these applications in more detail.
Automotive Parts
In the automotive industry, polypropylene is used for parts like car battery cases, dashboards, instrument panels, and door trims. Its affordability and ease of molding make it ideal for high-quality injection molded parts.
Blending recycled polypropylene with virgin materials can enhance compatibility and improve overall performance.
Consumer Goods
Polypropylene’s tough and flexible properties and flexibility make it ideal for consumer goods like kitchen appliances, home appliances, toys, furniture, carpets, and mats made from polypropylene plastic.
The material’s durability and versatility make it a preferred choice for various consumer products.
Medical Supplies
In the medical field, polypropylene’s chemical resistance and sterilization compatibility make it ideal for syringes, vials, and other medical supplies, ensuring safety and sterility.
The material’s properties make it an essential component in the healthcare industry.
Design Considerations for Polypropylene Injection Molding
Designing for polypropylene injection molding involves factors like gate and runner design, wall thickness, and shrinkage management to ensure optimal performance and quality.
Let’s delve into each of these considerations.
Gate and Runner Design
Efficient gate and runner design are crucial for smooth material flow and minimizing defects during the injection molding process. The most common location for placing the gate is the thickest wall segment. The ideal diameter range for pin gates is 1 to 1.5 mm, with the possibility of being as small as 0.7 mm.
An efficient design ensures smooth material flow into the mold, reducing defect risks.
Wall Thickness
Maintaining uniform wall thickness is essential in injection molding to prevent warping and ensure the part’s structural integrity. Non-uniform wall thickness can lead to issues such as warping, sink marks, and overall part failure.
Material selection, including polypropylene, and appropriate CAD modeling techniques help achieve uniform wall thickness and enhance the aesthetic quality of molded parts.
Shrinkage Management
Managing shrinkage during cooling maintains part dimensions. Factors like holding pressure and melt temperature impact polypropylene’s shrinkage rate.
Designing parts with slightly larger dimensions and controlling cooling rates can help compensate for shrinkage and ensure accurate final dimensions.
Challenges and Solutions in Polypropylene Injection Molding
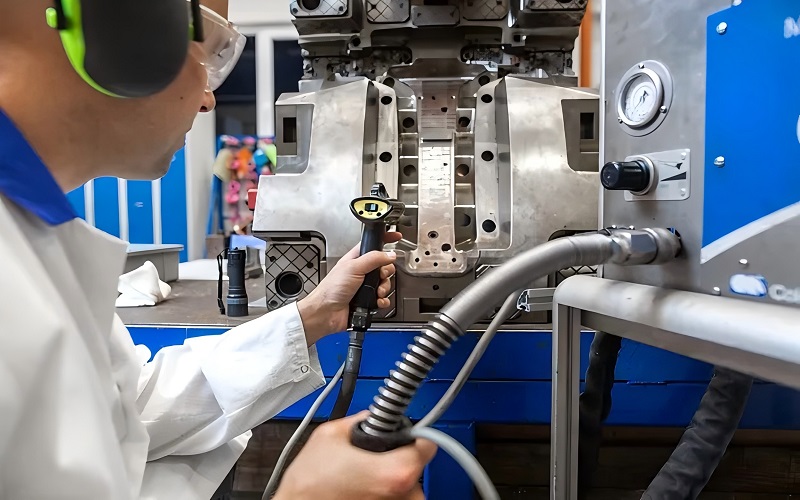
Polypropylene injection molding presents several challenges, including thermal degradation, surface defects, and material compatibility issues. Addressing these challenges maintains the quality and performance of the final product.
Thermal Degradation
Thermal degradation is a significant concern in polypropylene injection molding. Managing temperatures below 280°C maintains the material’s quality.
The high thermal expansion coefficient of polypropylene limits its applications in high-temperature environments, making temperature management essential during the molding process.
Surface Defects
Surface defects can occur during the cooling process at the gate, leading to imperfections in the final product. Proper cooling and optimal injection molding conditions minimize these defects, ensuring a smooth, even surface on molded parts.
Material Compatibility
Material compatibility maintains the properties of polypropylene. Its chemical resistance is variable, with poor resistance to chlorinated solvents and aromatics.
Compatibility with other materials, such as additives, must be considered to avoid compromising the final product’s quality and performance.
Summary
Polypropylene injection molding is a versatile and efficient process that offers numerous advantages across various industries. From its cost-effectiveness and ease of availability to its durability and flexibility, polypropylene has proven to be an invaluable material for manufacturing high-quality plastic components.
Understanding the injection molding process, key parameters, and design considerations is essential for achieving optimal results and maintaining the quality of the final product.
Addressing challenges such as thermal degradation, surface defects, and material compatibility ensures that the injection molding process runs smoothly and produces consistent, high-quality parts.
By following best practices and leveraging the unique properties of polypropylene, manufacturers can create a wide range of products that meet the demands of various applications. Embracing these insights and techniques will undoubtedly lead to success in the ever-evolving plastic industry.
Frequently Asked Questions
What makes polypropylene a preferred material for injection molding?
Polypropylene is a preferred material for injection molding due to its cost-effectiveness, availability, and exceptional durability and flexibility. Additionally, its low melt viscosity enables faster mold filling, thus lowering cycle times and production costs.
What are the key steps in the polypropylene injection molding process?
The polypropylene injection molding process consists of feeding, melting and plasticization, injection, pressure holding and cooling, and ejection, all crucial for producing high-quality parts. Adhering to these steps is essential for achieving optimal results in manufacturing.
How does mold temperature affect the quality of polypropylene injection molded parts?
Mold temperature significantly impacts the quality of polypropylene injection molded parts; maintaining a temperature between 40 to 80 degrees Celsius optimizes crystallinity, resulting in improved surface finish and overall performance.
What are common applications of polypropylene injection molding?
Polypropylene injection molding is commonly used in automotive parts, consumer goods, and medical supplies, due to its versatility and durability. These characteristics enable the production of a diverse array of high-quality products.
How can manufacturers address thermal degradation in polypropylene injection molding?
Manufacturers can effectively address thermal degradation in polypropylene injection molding by keeping the injection molding temperatures below 280°C and taking the thermal properties of polypropylene into account during the process. This ensures the material retains its integrity and performance.