PEEK injection molding is a specialized process of creating parts from high-performance PEEK plastic. This article explains what makes PEEK injection molding essential for critical applications, describes the material’s unique properties, and outlines best practices for achieving high-quality results.
Understanding PEEK Plastic
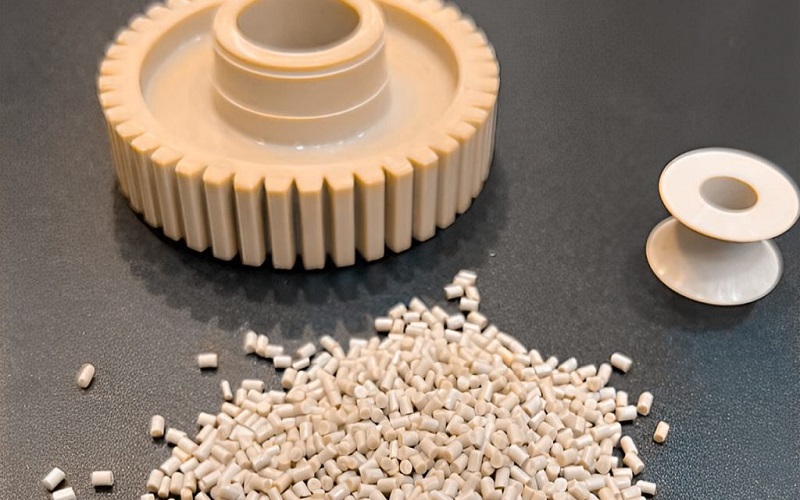
PEEK plastic is a high-performance thermoplastic known for its exceptional mechanical, thermal, and chemical properties. Its unique characteristics, such as the ability to form thin walls while maintaining strength, make it a preferred choice in various demanding applications.
PEEK’s resilience and stability under extreme conditions distinguish it from other high performance thermoplastics and high performance polymers, making it invaluable in the manufacturing sector.
Industries such as aerospace industries, automotive, medical applications, and oil and gas heavily rely on the versatility of PEEK. From aerospace components that endure high altitudes and temperatures to medical implants that require biocompatibility and durability, unfilled PEEK plays a crucial role in the medical industry.
Its ability to withstand harsh environments while maintaining structural integrity makes it indispensable across these sectors.
Key Properties of PEEK Material
PEEK materials have a high melting point ranging between 260°C to 300°C, making them ideal for high-temperature applications with high temperature resistance. This high melting point allows PEEK to maintain its mechanical properties even under extreme heat, which is critical for applications in aerospace and automotive industries where thermal stability is paramount.
Additionally, understanding PEEK material properties is essential for optimizing their use in various applications.
Another exceptional properties of PEEK is its chemical resistance peek. It can withstand exposure to nearly all chemical reagents except concentrated sulfuric acid, making it suitable for use in harsh chemical environments.
This resistance ensures longevity and reliability of components made from PEEK, significantly reducing maintenance costs and downtime. Additionally, PEEK’s excellent mechanical properties and wear resistance make it ideal for dynamic applications involving moving parts, such as gears and bearings.
PEEK is also biocompatible, which means it is inert and stable over time, does not elicit an immune response, and is transparent to X-rays. These properties make it highly suitable for medical devices, including implantable medical devices and surgical instruments.
The biocompatibility of PEEK ensures that it can be safely used within the human body for extended periods without adverse effects.
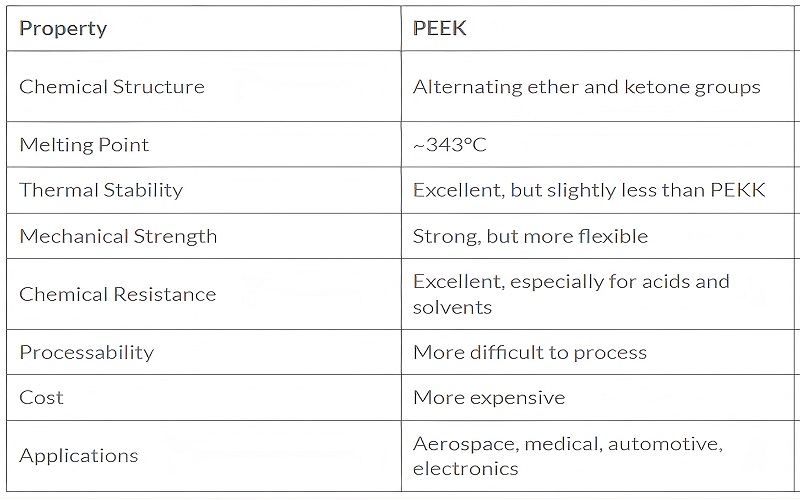
The PEEK Injection Molding Process
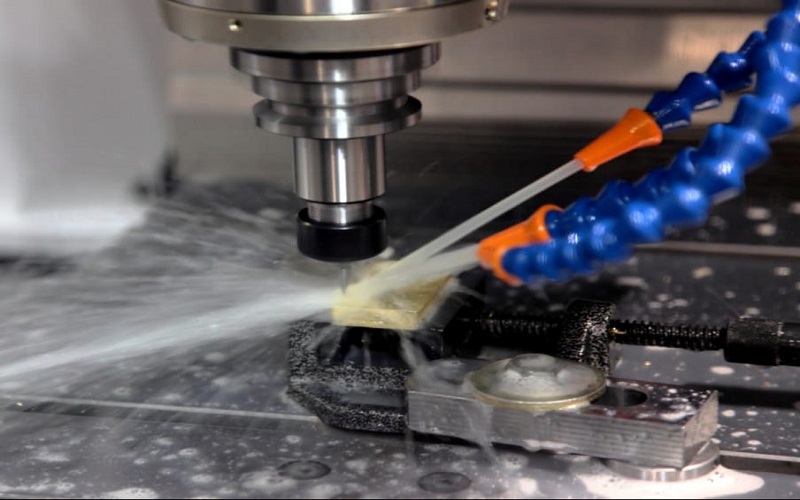
The PEEK injection molding process involves injecting molten PEEK resin into molds to create parts of various shapes and sizes. This process is highly precise and consistent, allowing for the production of complex components with tight tolerances.
Unlike lower temperature processing polymers, PEEK requires higher temperatures due to its exceptional thermal stability, ensuring the parts produced through injection molded PEEK are known for their high strength, stiffness, and dimensional stability, making them suitable for critical applications.
Achieving high-quality PEEK parts requires meticulous control of process parameters such as temperature, pressure, and cooling time. The appropriate range of injection pressure for PEEK molding is typically between 800-1500 bar, which helps in achieving the desired part characteristics. The precision in controlling these parameters is crucial to avoid defects and ensure the production of high-quality PEEK parts.
It is also essential to ensure that the PEEK polymer does not contact a cooler mold before reaching its melting point, as this can impact the molding process.
Strict control over the injection molding process, especially when compared to lower temperature processing polymers, is vital in achieving the desired properties of PEEK parts, making this manufacturing process highly specialized and skill-intensive.
Essential Equipment for PEEK Injection Molding
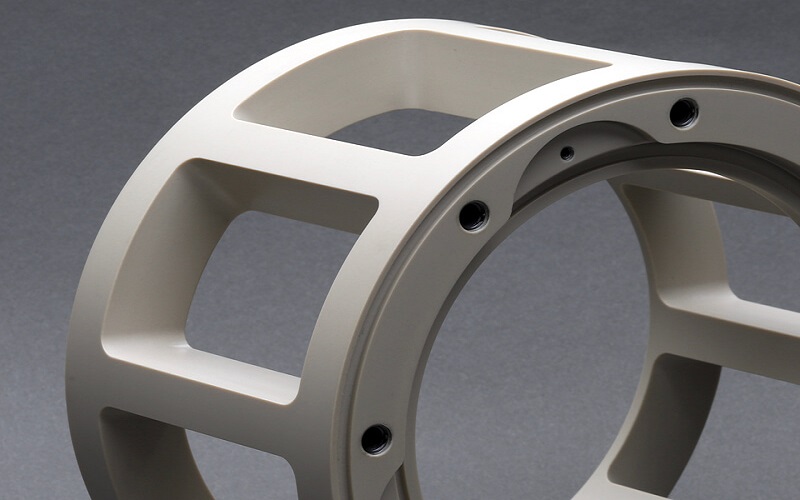
Standard injection molding machines are generally capable of handling PEEK without requiring significant modifications. However, specific equipment like ceramic heater bands are essential to ensure stable and consistent processing temperatures, which are crucial for molding PEEK effectively.
Additionally, smooth and highly polished metallic components are necessary to prevent material hang-ups during the molding process. These polished surfaces help in maintaining the quality of the molded plastic parts by ensuring that the PEEK resin flows smoothly through the mold, reducing the risk of defects and promoting low friction.
Importance of Drying PEEK Resin
Properly drying PEEK resin is a critical step in the injection molding process. Reducing the moisture content to below 0.02% is essential to prevent defects such as silver streaks and compromised mechanical properties in the final parts.
Common methods for drying PEEK resin include using dehumidifying dryers and oven drying at a temperature of 160°C for 2 to 3 hours.
During the drying process, it is crucial to maintain a temperature below the softening point of PEEK and ensure the dryer maintains a dew point of -40°C. Inadequate drying can lead to significant quality issues, including defects in the final parts and compromised mechanical properties.
Proper drying techniques are indispensable for achieving high-quality PEEK parts.
Maintaining Cleanliness in PEEK Processing
Maintaining a clean environment during PEEK processing is crucial to avoid contamination that could affect the quality of the parts. This involves inspecting and cleaning all equipment, including hoppers and injection molds, before starting the molding process. Using dedicated equipment for regrinding PEEK can help mitigate contamination risks.
Contaminants can lead to visible defects such as black specs and discolorations in the final products. Proper drying techniques also improve the surface quality of PEEK parts by minimizing defects caused by residual moisture content.
Cleanliness and proper handling of PEEK resin are essential for producing high-quality parts.
Optimal Gate Design for PEEK Parts
Larger gates in the mold design are crucial for achieving better filling and packing of PEEK components. This is particularly important due to PEEK’s high shrinkage compared to amorphous thermoplastics. Larger gates help in fully packing the component, ensuring dimensional stability and reducing shrinkage.
Factors such as part volume and geometry influence the size and design of the gate. Common gate designs in PEEK injection molding include tab, side, or fan gates, depending on the specific requirements of the part.
Avoiding sharp radii and elongated structures in the gate design prevents stress concentrations and ensures the integrity of the PEEK parts.
Temperature Control in PEEK Molding
Effective temperature management is crucial for successful PEEK processing. Maintaining a precise melt temperature of 380-400°C, which falls within PEEK’s processing temperatures, is necessary to avoid product failure.
Keeping the mold temperature between 170-200°C, also part of PEEK’s processing temperatures, achieves the desired crystallinity in PEEK parts, while also considering the saturation temperature.
Barrel blankets are recommended to maintain heat and enhance energy efficiency during PEEK processing. Electrical insulation boards and packing materials help provide heat insulation and achieve even temperature distribution, which is critical for producing high-quality parts and energy cost savings. Inadequate temperature management can lead to inferior quality components due to rapid cooling, making good temperature control essential.
Tools and techniques such as ceramic heater bands and thermal insulation boards are crucial for uniform temperature distribution and preventing heat loss during the PEEK injection molding process.
These measures ensure that the PEEK resin remains at the optimal temperature within PEEK’s processing temperatures throughout the molding cycle, resulting in high-quality parts
Common Challenges in PEEK Injection Molding
PEEK requires high processing temperatures, often between 350°C and 400°C, complicating the molding process. The material also has higher processing temperature and higher cooling demands compared to amorphous plastics, adding another layer of complexity.
Proper processing peek grades temperatures are essential, as deviations can lead to fatigue and stress cracking in the semi crystalline polymer, especially at much higher processing temperature. This material is known for its most consistent processing, including semi crystalline peek components.
Defects in molded parts can arise from unsound procedures during the PEEK injection molding process. Silver streaks, for example, can occur due to gases or moisture, high screw speed, and insufficient drying. Gas voids are typically caused by mold quality issues and flow dead angles. To avoid such defects, maintain the moisture content level in PEEK below 0.2%.
Common challenges in molding PEEK include proper mold design, processing parameters, material handling, and maintenance. To reduce shrinkage in PEEK injection molding, increasing injection pressure and holding pressure is recommended. Addressing these challenges ensures the production of high-quality PEEK parts.
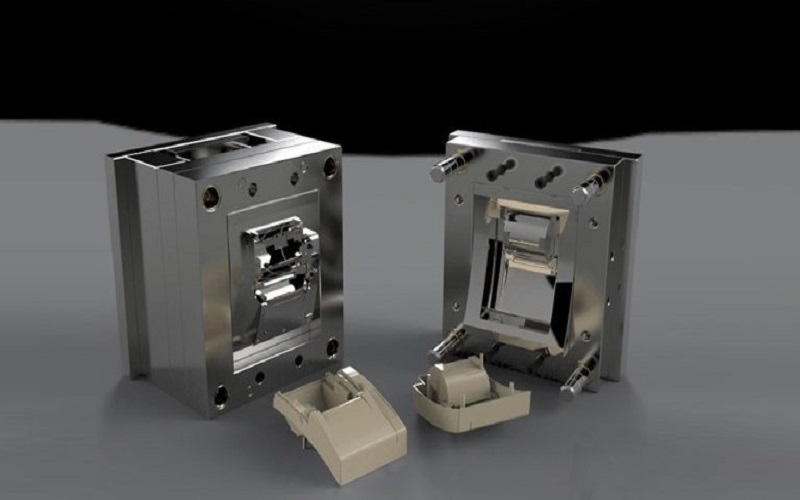
Applications of PEEK Injection Molded Parts

PEEK is known for its long lifespan and reliability, making it suitable for critical applications across various industries. In the medical sector, PEEK is frequently used for manufacturing implants and surgical instruments due to its biocompatibility and durability.
The aerospace industry values PEEK for its mechanical robustness and heat resistance, making it ideal for high-stress components.
The oil and gas industry employs PEEK for components that require exceptional chemical and thermal stability. PEEK is also suitable for creating gears, bearings, and manifolds due to its strength and durability. Its high-performance characteristics allow it to replace heavier, less sustainable materials, promoting lighter and more efficient designs.
Sustainability and Environmental Considerations
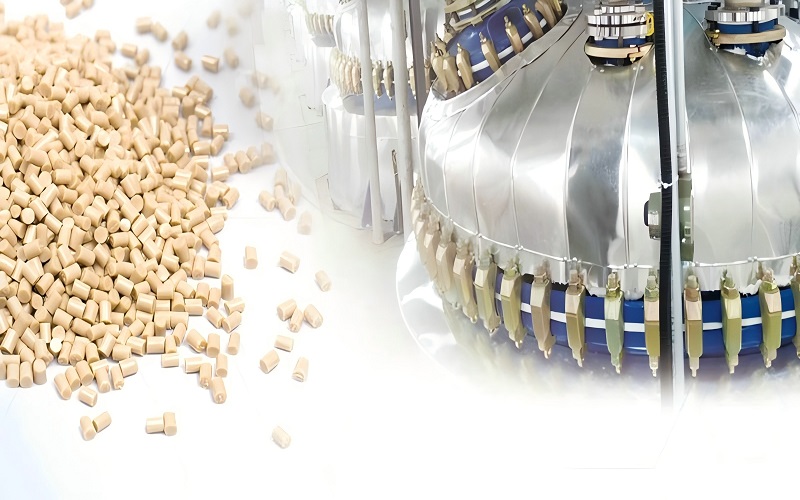
The durability of PEEK significantly reduces the frequency of replacements needed for components, ultimately lessening the environmental impact. Using PEEK components can improve system reliability and safety, thus minimizing potential environmental risks.
Additionally, PEEK can be recycled and repurposed efficiently, contributing to reduced waste in manufacturing processes.
The recyclability of PEEK enables it to be reused in certain applications, enhancing sustainability. PEEK does not emit harmful toxins during its lifecycle, including when exposed to fire. Using sustainable materials like PEEK in manufacturing processes promotes environmental responsibility.
Selecting a PEEK Injection Molding Service Provider
Selecting a reliable PEEK injection molding service provider is critical for ensuring quality and efficiency in the manufacturing process. Providers like Sungplastic, with many years of experience specializing in high-precision complex parts, offer valuable expertise and services, including design, engineering, tooling, production, and peek molded parts.
Fictiv is another example, offering expert DFM feedback and a network of injection molding partners to ensure quality assurance. Choosing an experienced provider can significantly impact the quality of the final PEEK parts, making it essential to select a partner with a proven track record.
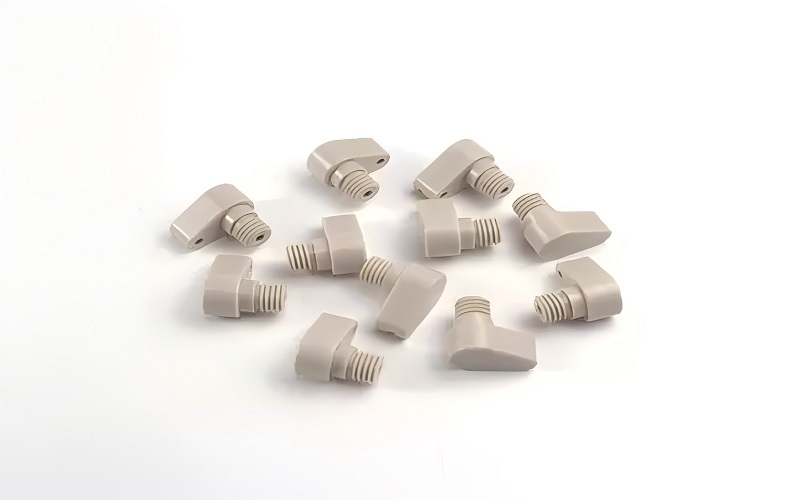
Summary
In summary, PEEK injection molding is a complex but highly rewarding process that requires meticulous attention to detail. From understanding the unique properties of PEEK to managing the injection molding process and selecting the right equipment, each step is crucial to achieving high-quality parts. The importance of drying the resin, maintaining cleanliness, designing optimal gates, and controlling temperature cannot be overstated.
As industries continue to demand high-performance materials, PEEK stands out for its exceptional properties and wide range of applications. By mastering the intricacies of PEEK injection molding, manufacturers can produce reliable, durable, and high-quality parts that meet the stringent requirements of various sectors.
We hope this guide has provided you with valuable insights and inspiration to excel in the world of PEEK injection molding.
Frequently Asked Questions
Why is drying PEEK resin so important?
Drying PEEK resin is essential to minimize moisture content to less than 0.02%, thereby avoiding defects like silver streaks and ensuring optimal mechanical properties in the final components. Failure to dry the resin adequately can lead to significant performance issues.
What are some common challenges in PEEK injection molding?
Common challenges in PEEK injection molding include the need to maintain high processing temperatures, manage significant cooling demands, and prevent defects that may arise from inadequate drying and suboptimal mold design. Addressing these issues is crucial for achieving quality results.
What industries commonly use PEEK injection molded parts?
PEEK injection molded parts are commonly utilized in the aerospace, medical, automotive, and oil and gas industries owing to their high strength, chemical resistance, and thermal stability. These attributes make them ideal for demanding applications in these sectors.
How does temperature control affect PEEK injection molding?
Temperature control significantly impacts PEEK injection molding by ensuring the appropriate melt and mold temperatures, which are vital for achieving optimal crystallinity and minimizing defects caused by rapid cooling. This precision is crucial for producing high-quality PEEK components.
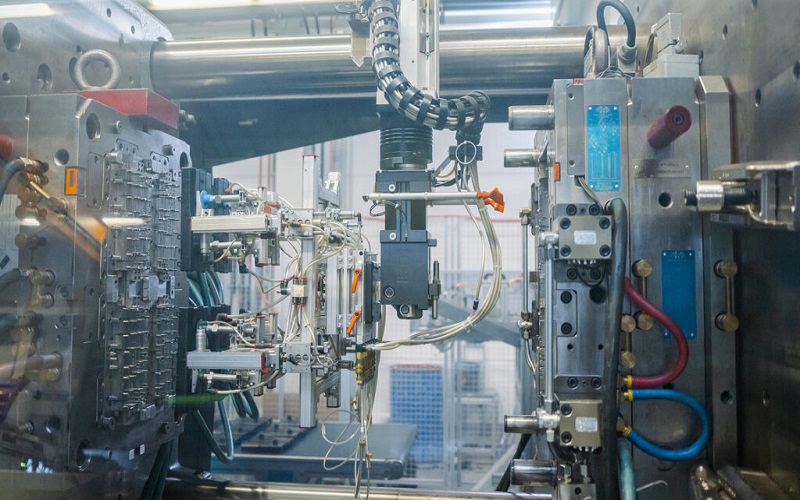
What should be considered when selecting a PEEK injection molding service provider?
When selecting a PEEK injection molding service provider, it is essential to consider their experience, design and engineering capabilities, and quality assurance processes to ensure high-quality output. Providers with a proven track record, such as Sungplastic and Fictiv, are recommended for reliable service.