Wall thickness in injection molding is vital for ensuring product strength and quality. This article explains how to achieve optimal wall thickness, covers design tips, and shows how to prevent defects.
Understanding Wall Thickness in Injection Molding
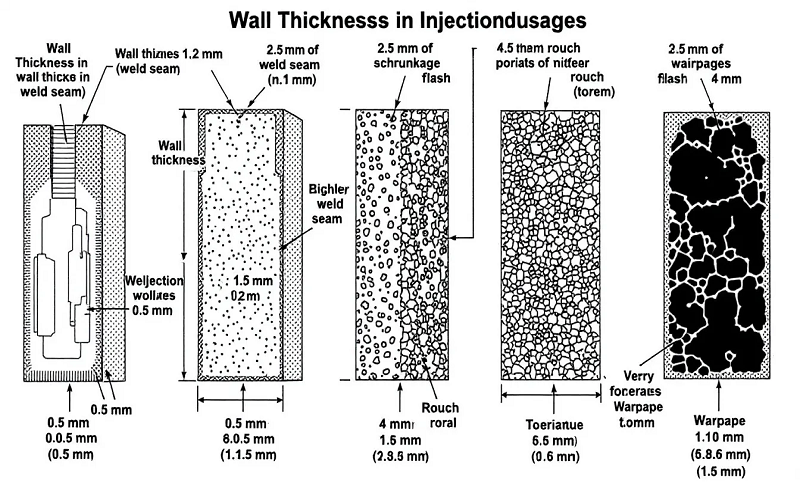
Wall thickness in plastic injection molding measures the distance between a plastic product’s outer and inner surfaces. This dimension is crucial for the strength and durability of the final product, influencing both its design and functionality.
Proper wall thickness impacts not only aesthetics but also the structural integrity and overall performance of the molded part, especially in an injection molding project.
Wall thickness in injection molding typically ranges from 1.5 mm to 4.5 mm, varying with the type of plastic. Some materials need thicker walls for proper flow and solidification, while others perform well with thinner walls.
Knowing these nuances helps achieve a balance between strength and efficiency in the injection mold, particularly when considering thick wall injection, wall thicknesses, and avoiding issues like sharp internal corners that can lead to stress concentrations.
Product size, shape, and usage requirements significantly influence the ideal wall thickness. Wall thickness also affects mechanical performance, production cost, and molding cycle. Consistent wall thickness ensures smoother production and effective injection, reducing defects and enhancing overall product quality in any injection molding project.
Importance of Uniform Wall Thickness
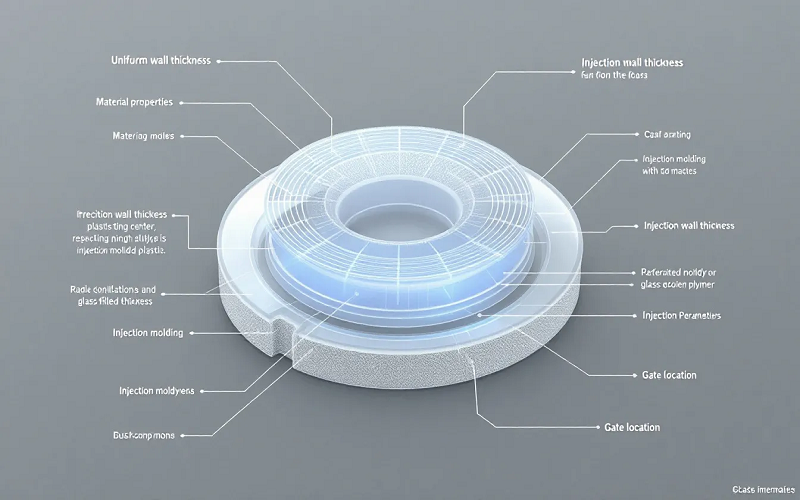
Uniform wall thickness is essential for high-quality injection molded parts. Inconsistent wall thickness can cause defects like sink marks, warping, and short shots, compromising both the aesthetic appeal and functional integrity of the parts.
Uniform wall thickness enhances part-to-part consistency, ensuring that each piece produced meets the same thickness quality standards. This uniform thickness improves stress distribution within the part, reducing the likelihood of structural failures, leading to consistent walls and offers superior light transmission.
Additionally, uniform wall thicknesses contribute to overall product reliability, highlighting the importance of supporting material attributes in large structural components.
Maintaining uniformity also streamlines the production process, making it easier to predict and control each molding cycle’s outcome.
Designing for Optimal Wall Thickness
Designing for optimal wall thickness requires balancing strength and moldability. Ideally, the recommended wall thickness should be 40% to 60% of adjacent walls to ensure structural integrity, maintain consistency, and prevent defects from uneven cooling or internal stresses. The maximum thickness of the recommended thickness ranges is crucial in achieving this balance.
For larger products, increased wall thickness often enhances strength and stability but must be balanced with efficient mold filling, especially for complex shapes. Avoiding long unsupported spans in part geometries is crucial for maintaining consistency. Using ribs effectively can strengthen tall walls without increasing wall thickness important.
The Design for Manufacturability (DFM) process offers valuable insights into wall thickness variations and suggests modifications for optimal moldability. DFM analysis provides recommendations for wall thickness and draft angles, ensuring the final product is robust and easy to manufacture.
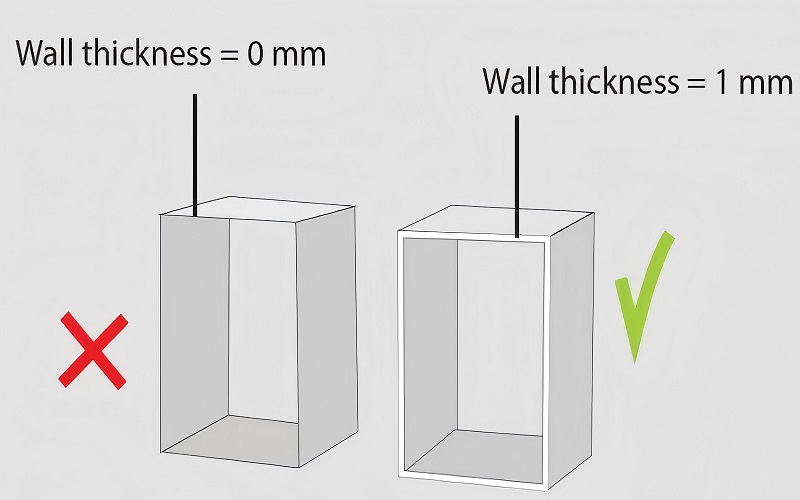
Minimum and Maximum Wall Thickness Guidelines
Following minimum and maximum wall thickness guidelines, including relative wall thickness, avoids production issues and ensures product quality in plastic parts. The minimum wall thickness for injection-molded products is typically 0.6 mm to prevent ejection problems in the mold cavity. Generally, recommended wall thickness ranges from 1.5 mm to 4.5 mm, depending on the product’s characteristics and maximum operating temperatures online.
Specific materials have additional considerations. For example, ABS materials should not exceed 6 mm in wall thickness to avoid filling problems, and care should be taken to avoid sharp corners that can cause stress points. Maintaining relative wall thickness between 40% to 60% of adjacent walls is crucial to prevent defects and improve structural integrity.
These guidelines help maintain uniform cooling and minimize warping, ultimately enhancing the overall quality of molded plastic parts while adhering to molding design guideline rules for the mold cavity.
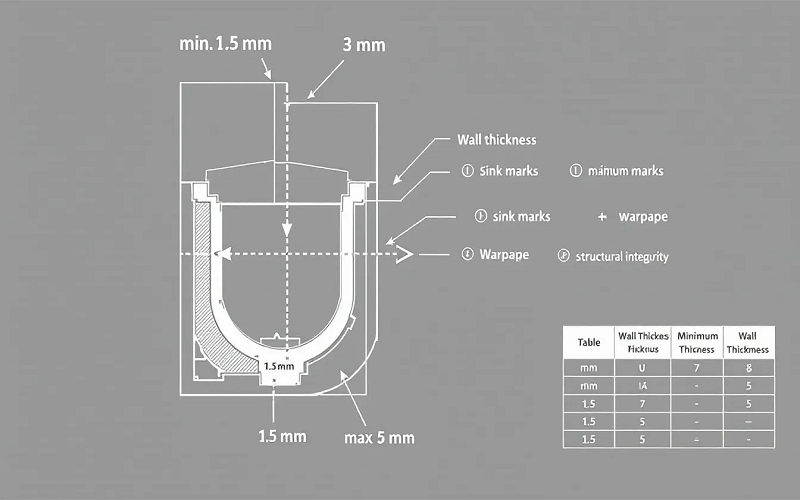
Material-Specific Wall Thickness Recommendations
Selecting the right material for injection molding is crucial, considering its flow properties and dimensional requirements. Different materials have specific wall thickness recommendations based on their characteristics, often requiring techniques like removing wedge shaped slices to optimize design. For instance, ABS plastic should have a wall thickness between 0.045 inches and 0.140 inches, and can be enhanced by adding glass fiber filler for improved strength.
Other materials have their optimal ranges: Nylon (0.030 to 0.115 inches), Polycarbonate (0.040 to 0.150 inches), Polypropylene (0.025 to 0.150 inches), and Acrylic (0.025 to 0.500 inches), all benefiting from properly designed walls to ensure structural integrity, especially when using glass filled material to boost durability.
Long fiber reinforced plastics, such as liquid crystal polymer, should have a wall thickness between 0.030 inches and 0.120 inches. These recommendations account for the unique flow properties and dimensional stability of each plastic material, often enhanced by properly designed walls.
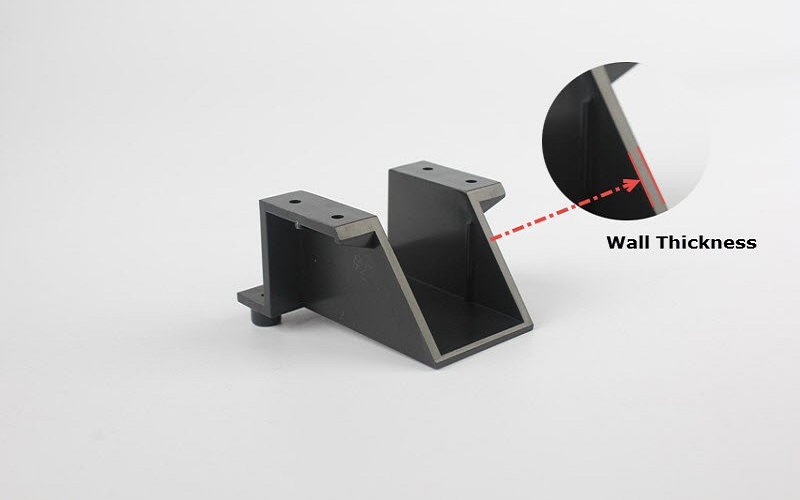
Techniques to Maintain Consistent Wall Thickness
Maintaining consistent wall thickness involves various design techniques to ensure uniformity and structural integrity. One effective method is coring parts to reduce material usage and weight while preserving strength, particularly in thick sections.
Using gussets to reinforce box lids with thin walls ensures structural integrity. Designing parts with radiused internal corners helps reduce stress and prevent warping during the injection molding process.
Shapes like dumbbells and sewing bobbins can alleviate internal stress issues with wall thickness and alleviate internal stress, enhancing overall part stability.
Impact of Wall Thickness on Cooling and Cycle Times
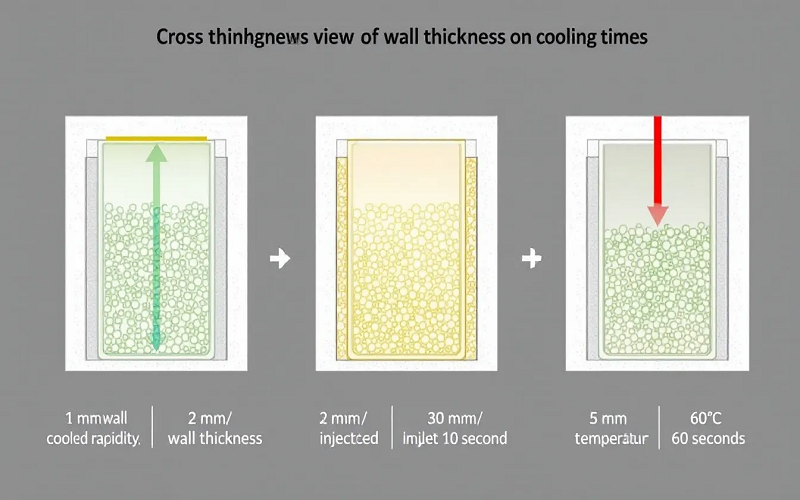
Wall thickness significantly affects the cooling process and cycle times in injection molding. Thicker sections take longer to solidify, increasing cycle times and requiring longer holding times in the mold for proper cooling before ejection. Uneven wall thickness, especially when combined with sharp external corners, can complicate this process, extending cooling times and production duration.
Wall thickness influences the flow of molten plastic, often favoring thicker areas and complicating cooling. An optimal flow length-to-thickness ratio helps reduce cycle times and enhance production efficiency, ensuring proper material flow and avoiding solidification issues.
Addressing Thick Sections and Thin Walls
Addressing thick sections and thin walls in design requires strategic adjustments in part geometry. Using rounded internal corners can reduce stress and prevent warping. Avoiding abrupt transitions in wall thickness helps prevent warping and other defects. Incorporating a thick section can also enhance structural integrity.
Excessively thick walls may cause underfilling during the injection process. Conducting flow analysis is essential to identify potential knit lines and pressure points in areas with varied wall thickness, especially when using glass fiber filler.
Modifying the location of parting lines can significantly enhance the cosmetic quality, appearance, and functionality of an injection molded part in custom injection molded parts.
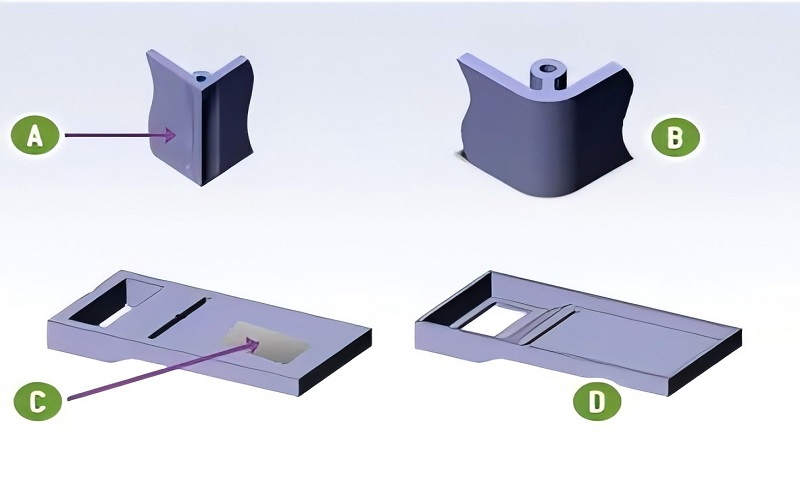
Flow Length-to-Thickness Ratio Considerations
The flow length-to-thickness ratio is crucial in injection molding, influencing molten plastic behavior during the process. The ideal ratio typically ranges from 90 to 270. Properly managing this ratio ensures efficient plastic flow and solidification, affecting the final product’s quality.
Performing flow analysis helps identify pressure points around gate areas, essential for optimizing the injection molding process. This analysis ensures proper material flow through the mold, reducing defects and improving overall part quality.
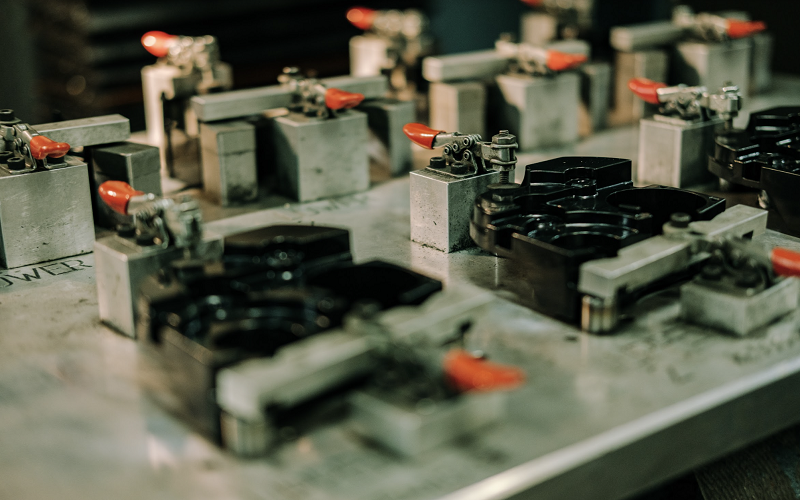
Design Tips for Ribs and Bosses
Ribs and bosses are essential design elements in injection molding, providing strength and stability. Ribs can reinforce tall walls while maintaining the proper wall thickness ratio. Rib thickness should not exceed 60% of the part’s nominal wall thickness to ensure proper flow and solidification.
To avoid warpage, ribs should be spaced at least 2.5 to 3 times the nominal wall thickness. Reinforcing ribs should be less than three times the base wall thickness to prevent underfilling during molding. Including a radius at the intersection of ribs and walls enhances strength and reduces stress.
For reinforced bosses, ensure the internal and external diameters allow ample clearance for screws, maintaining a spacing of 0.05mm between screw boss surfaces. The maximum recommended depth for blind holes in bosses is three times the hole diameter. Avoiding multiple ribs intersecting at the same point prevents excessive thickness at rib intersections.
The Role of Draft Angles in Wall Thickness
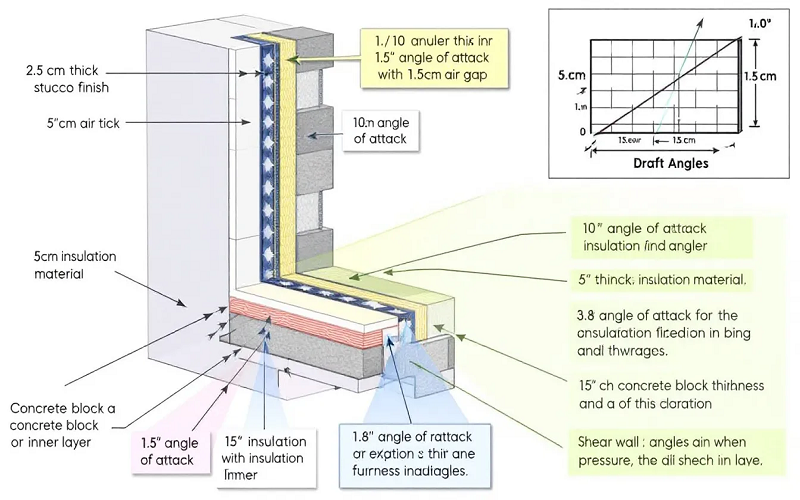
Draft angles are crucial for ensuring parts can be smoothly ejected from the mold without damage. Recommended draft angles are 0.5% to 1% per side for walls, 0.5-1.5 degrees for bosses, and 0.5-1.5 degrees for reinforcing ribs.
Factors influencing draft angle size include experience, product depth, molding method, wall thickness, and choice of plastic. Adding radii to internal corners in part geometry ensures smooth ejection from molds and prevents damage.
A suggested radius for rounding the bottom of ribs is 0.25 times the base wall thickness to aid in mold release.
Common Defects Related to Wall Thickness Variations
Inconsistent wall thickness can cause defects like warping, flow lines, and sink marks, affecting both aesthetic appeal and functional integrity. Overly thick walls can lead to issues like shrinkage, air bubbles, or vacuum voids.
Variations in wall thickness can increase rejection rates due to quality defects. Thin wall, uniform walls are generally less prone to warping during cooling, making them a preferred choice for many injection molding applications.
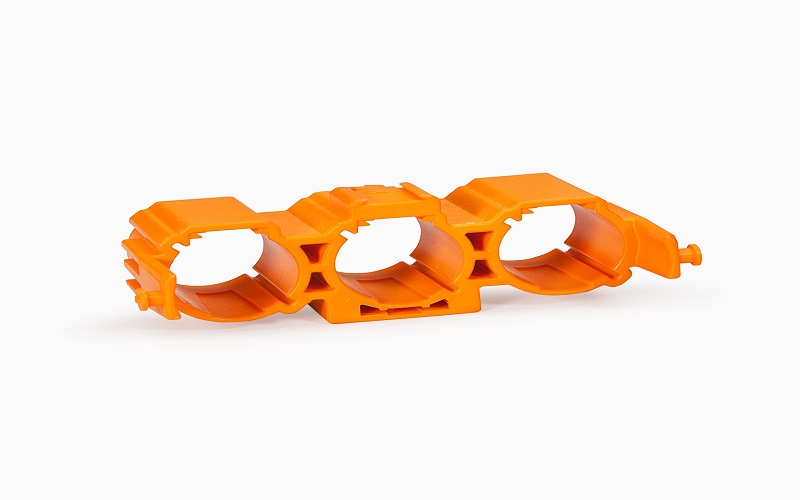
Summary
Mastering wall thickness in injection molding is a multifaceted challenge that requires careful consideration of material properties, design principles, and manufacturing techniques.
By understanding the importance of uniform wall thickness, adhering to guidelines, and employing best practices, you can significantly enhance the quality and efficiency of your injection molded parts.
Remember, the journey to perfection in injection molding is continuous. Stay informed, keep experimenting, and never stop learning. Your commitment to excellence will undoubtedly lead to superior products and satisfied customers.
Frequently Asked Questions
Why is uniform wall thickness important in injection molding?
Uniform wall thickness is crucial in injection molding as it prevents defects like sink marks and warping, thereby ensuring the quality and consistency of the molded parts. This attention to thickness ultimately leads to improved manufacturing reliability.
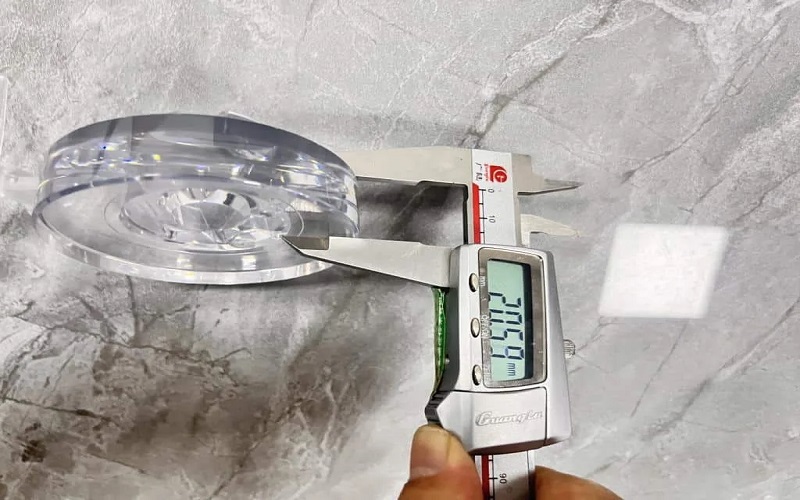
What is the typical range for wall thickness in injection molding?
The typical range for wall thickness in injection molding is 1.5 mm to 4.5 mm, depending on the product’s characteristics and the materials utilized. This variability ensures that the final product meets both functional and aesthetic standards.
How does wall thickness affect cooling and cycle times in injection molding?
Wall thickness significantly impacts cooling and cycle times in injection molding; thicker sections increase solidification time, leading to longer cycle times, while uneven wall thickness further complicates the cooling process. Thus, careful design of wall thickness is essential for optimizing efficiency in injection molding.
What are some techniques to maintain consistent wall thickness in injection molding?
Maintaining consistent wall thickness in injection molding can be achieved through techniques like coring parts, incorporating gussets, and designing with radiused internal corners. These methods not only ensure uniformity but also help reduce internal stress.
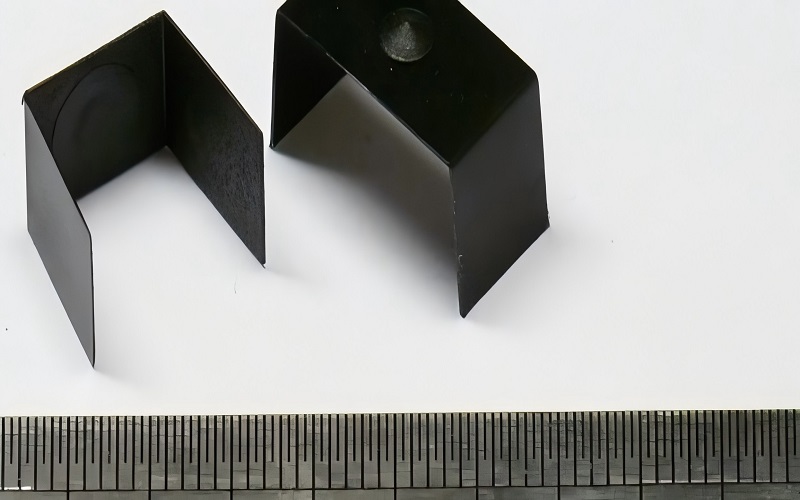
What are the recommended draft angles for walls and ribs in injection molding?
The recommended draft angles for walls in injection molding range from 0.5% to 1% per side, while for ribs, it is advisable to use 0.5 to 1.5 degrees.