Aluminum injection molds are a cost-effective way to produce precise plastic parts. In this article, learn about how aluminium injection mold technology works, their benefits, and why they might be perfect for your manufacturing needs.
Understanding Aluminium Injection Molds
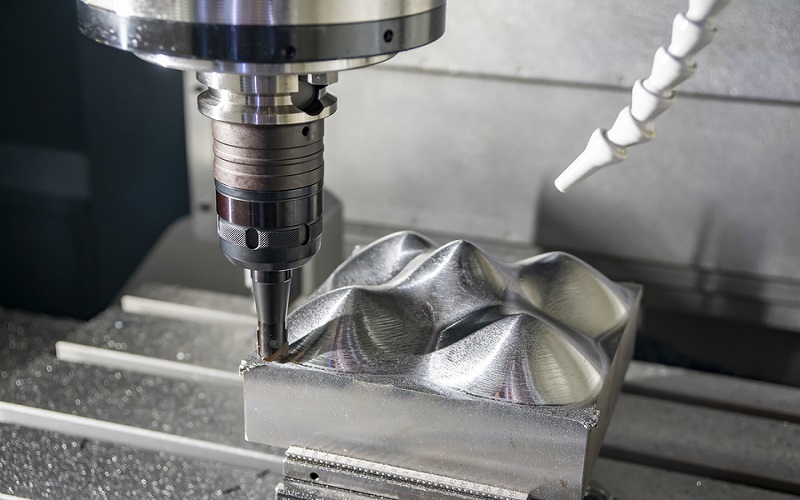
Aluminum injection molds consist of aluminum cores and cavities, supported by steel mold bases that provide increased rigidity and structural stability.
This combination offers a versatile tooling option suitable for producing both prototypes and real products across various industries, including the use of aluminum injection mold technology.
The mechanical properties of aluminum, such as its rigidity and low production costs, make it a preferred choice for manufacturers aiming to simplify processes and achieve better products at lower costs.
The Aluminium Injection Molding Process
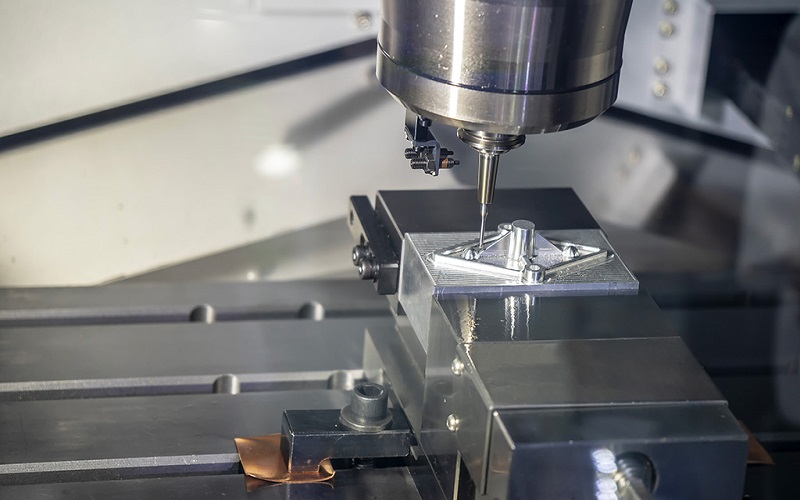
The aluminum injection molding process is a streamlined method comprising three main stages: injection, cooling, and ejection. These stages collectively ensure the efficient production of high-quality parts, with each stage playing a critical role in the overall success of the process when you choose aluminum injection molds. Compared to traditional steel molds, aluminum molds offer faster heat transfer, which can enhance the cooling stage and reduce cycle times.
Injection Phase
During the injection phase, molten plastic is introduced into the pre-designed injection mold aluminum mold cavity at high pressures to ensure complete filling, often leaving excess material known as flash.
This phase is crucial as it determines the initial shape and integrity of the injection molded part, setting the stage for subsequent cooling, ejection, and flash formation, especially when compared to steel counterparts. Additionally, plastic injection molding plays a significant role in this process, benefiting from advancements in mold manufacturing techniques.
Cooling Phase
Aluminum’s superior thermal conductivity significantly impacts the cooling phase, allowing molds to dissipate heat quickly and reduce overall cycle times, especially when you create molds with this material.
This efficient cooling not only enhances production efficiency for varying production volume but also ensures that parts are produced with minimal defects, maintaining high quality throughout the process. Additionally, adding steel inserts or brass thread inserts to aluminum molds can improve durability and precision in high-wear areas.
Ejection Phase
Once the part solidifies, the mold opening occurs to release the finished product, completing the ejection phase. Aluminum’s rapid cooling properties allow the mold to open sooner after solidification, speeding up the production cycle and enabling quicker turnaround times.
Comparing Aluminium and Steel Injection Molds
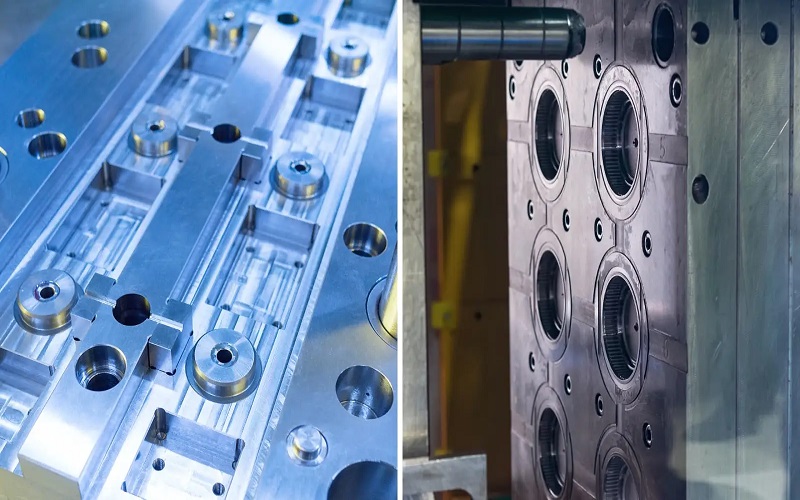
When comparing aluminum and steel injection molds, key considerations include cost, durability, and application suitability. Each material has its unique advantages and limitations, which make them more suitable for different production needs.
Cost Comparison
Aluminum injection molds generally offer a more cost-effective solution compared to steel molds. On average, they can be 20-40% cheaper due to reduced machining time and lower initial manufacturing costs. This cost advantage makes aluminum molds particularly attractive for projects with tighter budgets or shorter production runs.
Durability and Lifespan
While aluminum injection molds typically last between 10,000 to 100,000 cycles, steel molds can withstand approximately 100,000 to 1,000,000 cycles, making them more durable.
Factors such as specific alloy selection and heat treatment can influence the durability of aluminum molds, but generally, steel molds offer longer lifespans and greater wear resistance.
Application Suitability
Aluminum molds are particularly suitable for smaller production runs and simpler product designs, whereas steel molds handle tougher materials and more complex geometries better.
For instance, materials like ABS and PP are well-suited for aluminum molds, making them ideal for low-volume production and rapid prototyping. Additionally, understanding different mold materials can enhance the selection process.
Advantages of Aluminium Injection Molds
Aluminum injection molds offer several advantages, including lower initial costs, faster processing times, and efficient heat dissipation. These benefits make them an attractive option for many manufacturers, especially those engaged in prototyping and low volume injection molds and medium-volume production.
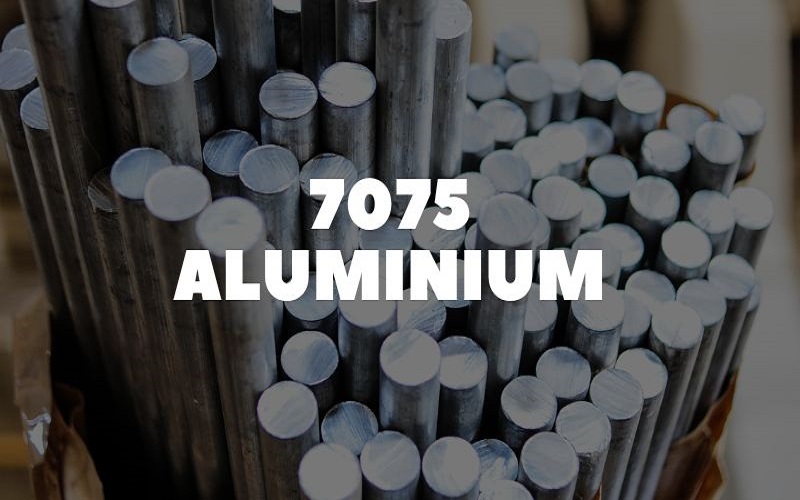
Rapid Prototyping
The lower initial costs and faster production cycles associated with aluminum molds make them ideal for rapid prototyping. The ability to produce aluminum prototype molds in as little as 40 to 70 seconds enables quick iterations and adjustments, ensuring high-quality prototypes or parts with fine detail and shorter production cycles.
Efficient Heat Dissipation
Aluminum’s excellent heat dissipation properties lead to rapid cooling during the injection molding process, significantly reducing cycle times and enhancing production efficiency. This uniform heat distribution also decreases the likelihood of product defects, maintaining high quality and consistency in production.
Cost-Effectiveness
The overall cost benefits of using aluminum molds and aluminum tooling are significant. They can be produced more quickly and at a lower cost than steel molds, enhancing turnaround times for initial tooling.
Additionally, their lighter weight simplifies handling and installation, making them a cost-effective choice for many manufacturing processes.
Challenges with Aluminium Injection Molds
Despite their many advantages, aluminum injection molds come with certain challenges, such as limited surface finishes, complexity in design, and the need for regular maintenance and repair.
Addressing these challenges requires careful planning and consideration during the mold design and production stages.
Limited Surface Finishes
While aluminum molds can achieve good surface finishes, they cannot attain the same level of polish as steel molds, which can affect the surface quality of the molded parts.
Understanding these limitations is crucial for manufacturers to ensure the right choice of mold for their production needs.
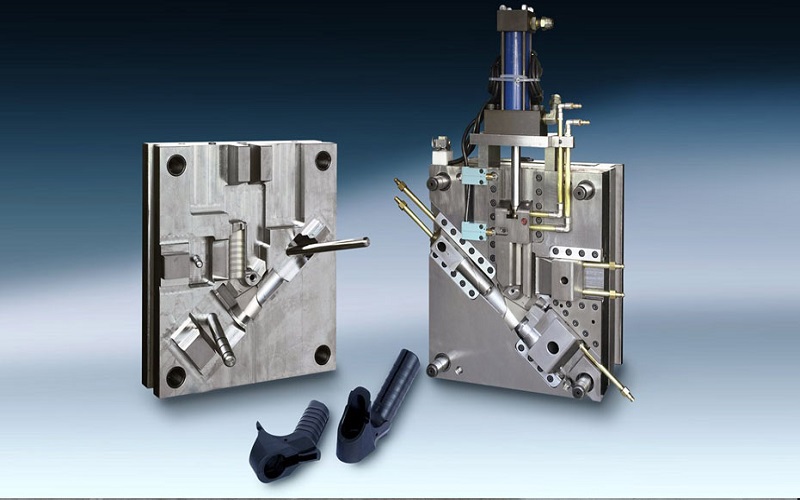
Complexity in Design
Aluminum’s soft nature makes it unsuitable for intricate designs, as it lacks the necessary structural strength for thin walls and intricate geometries. Designing complex parts with softer metal aluminum molds presents specific challenges that can hinder production quality.
Maintenance and Repair
Aluminum molds require regular maintenance to keep them in optimal condition, as poor upkeep can lead to significant wear and reduce mold life, ultimately affecting mold’s lifespan.
Additionally, repairing aluminum molds can be costlier and time-consuming due to the material’s poor welding capabilities.
Best Practices for Aluminium Mold Design
Implementing best practices in aluminum mold design can significantly improve durability and efficiency. Key practices include ensuring uniform wall thickness, selecting suitable alloys, and incorporating inserts.
Ensuring Uniform Wall Thickness
Maintaining consistent wall thickness is essential for preventing defects such as warping and sink marks during the injection molding process. Designing components with gradual transitions between different wall thicknesses and incorporating gussets and ribs can enhance structural integrity while ensuring uniform cooling.
Draft angles and generous corner radii also support the ejection of parts and reduce the risk of defects, especially when avoiding sharp corners.
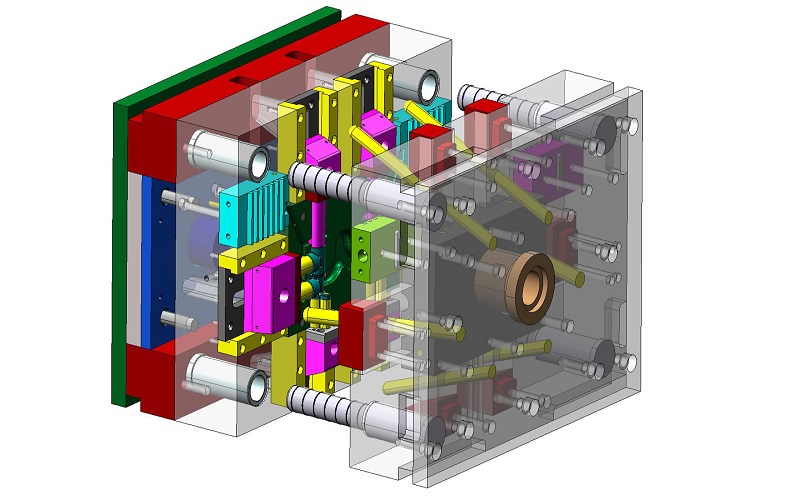
Alloy Selection
Choosing the right aluminum alloys is crucial for enhancing mold strength and durability. Aluminum alloys with a short freezing range are ideal for achieving better mold performance, allowing for easier modifications and faster adjustments during the production process.
Incorporating Inserts
Incorporating steel inserts into aluminum molds enhances their durability and reduces wear in high-stress areas. Inserts are particularly useful for manufacturing parts that experience high friction or heat, such as automotive components.
Designing inserts requires precise engineering to ensure they fit properly and function as intended.
Extending the Life of Aluminium Molds
Extending the life of aluminum molds involves implementing regular maintenance and applying surface treatments to enhance durability and performance. These strategies can significantly reduce the frequency of mold replacements and ensure consistent production quality over time.
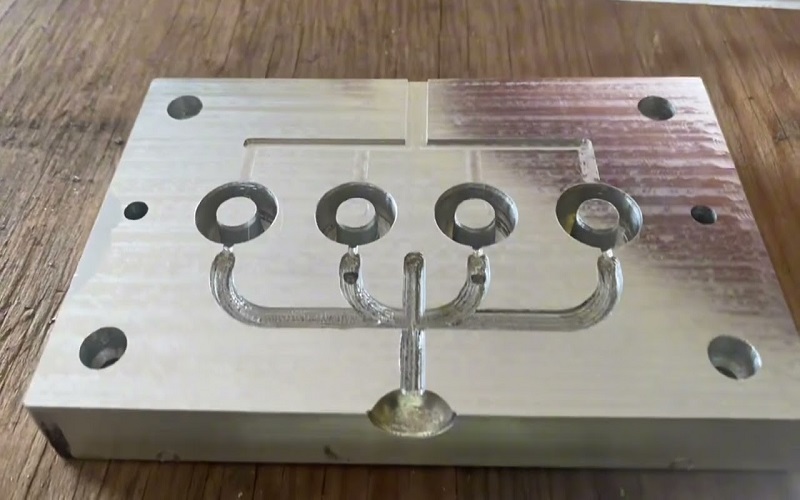
Regular Maintenance
Regular maintenance is crucial to extend the lifespan of aluminum molds. More frequent maintenance, along with routine inspections, helps manage the higher wear rates of aluminum molds, allowing for timely repairs and upkeep.
Regular checks for wear and galling should be part of the maintenance process whenever molds are removed from the press. Tailoring routine maintenance practices to factors like resin type and mechanical actions in the mold can further enhance mold longevity.
Surface Treatments
Surface treatments like nickel plating and anodizing can significantly prolong the lifespan of aluminum molds by enhancing their hardness and providing additional wear and corrosion resistance.
Applying a Nibore surface finish coating, which acts as a release agent, also facilitates easier part ejection from the mold and provides oxidation resistance, further extending mold life.
Cost Breakdown of Aluminium Injection Molding
Understanding the cost breakdown of aluminum injection molding is essential for making informed decisions. Key cost components include initial tooling costs, maintenance and replacement costs, and overall savings for small runs, which collectively make aluminum molds a cost-effective solution for many applications.
Initial Tooling Costs
The initial tooling costs for aluminum injection molds are significantly lower than for steel molds. Aluminum’s lower cost and shorter lead times make it an attractive choice for prototyping and low to medium production runs. The manufacturing time for aluminum injection molds typically ranges from 10 to 15 days, considerably faster than for steel molds, which take longer due to their rigidity and hardness.
CNC machining, the primary manufacturing process for aluminum molds, further reduces setup costs and production time.
Maintenance and Replacement Costs
While aluminum molds have lower initial costs, they incur higher maintenance and replacement costs over time due to the need for more frequent repairs and replacements. However, regular maintenance and timely repairs can help manage these costs and prolong the lifespan of aluminum molds.
Overall Savings for Small Runs
Aluminum molding is ideal for low to medium-volume production runs, offering substantial cost savings due to lower upfront costs and reliable part production. The lower setup costs and easier machining of aluminum make it a preferred choice for rapid prototyping and small production runs, providing better value for manufacturers.
Real-World Applications of Aluminium Injection Molds
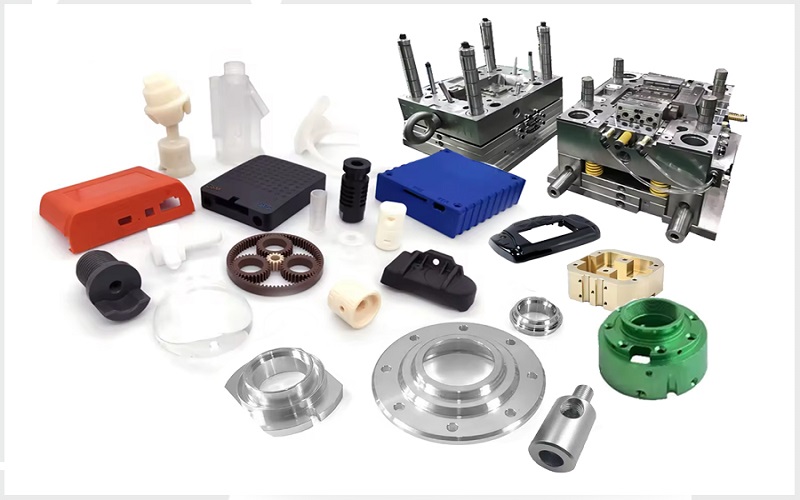
Aluminum injection molds are widely utilized across various industries, including aerospace, automotive, medical devices, and consumer electronics. Their versatility and cost-effectiveness make them a popular choice for rapid prototyping and small to medium production runs.
Automotive Industry
Aluminum injection molding is utilized in the automotive industry to create a range of parts. This includes engine components, interior trim, and structural elements. The use of aluminum parts improves vehicle efficiency and maintains durability, making it a valuable manufacturing process for the industry.
Medical Devices
Aluminum molds are utilized in creating precise medical tools and devices, which often require intricate shapes and high precision to meet strict health standards. This application highlights the importance of aluminum molds in producing complex medical devices with consistent quality and reliability.
Consumer Electronics
Aluminum molds play a crucial role in the consumer electronics sector. They are utilized to produce lightweight components that effectively dissipate heat, including heat sinks and housings.
Their rapid cooling properties enhance production efficiency, making aluminum molds ideal for quick prototyping and small production runs in the electronics industry.
Conclusion: Making the Right Choice
Choosing between aluminum and steel molds depends on specific project requirements, budget considerations, and production needs. Aluminum molds offer a cost-effective solution with faster turnaround times, making them ideal for rapid prototyping and low to medium-volume production runs.
Understanding the benefits and challenges of each material will help you make an informed decision that best suits your manufacturing goals.
Frequently Asked Questions
What are the main advantages of aluminum injection molds?
The primary advantages of aluminum injection molds lie in their lower initial costs, expedited processing times, and effective heat dissipation, which make them particularly suitable for rapid prototyping and low to medium-volume production.
How do aluminum molds compare to steel molds in terms of cost?
Aluminum molds are typically 20-40% less expensive than steel molds, primarily because of their reduced machining time and lower initial manufacturing costs. Therefore, choosing aluminum molds can be a more cost-effective solution for many applications.
What are the common challenges with aluminum injection molds?
Common challenges with aluminum injection molds include limited surface finishes, design complexity, and the necessity for regular maintenance and repair. These factors can impact production efficiency and product quality.
How can the lifespan of aluminum molds be extended?
To extend the lifespan of aluminum molds, implement regular maintenance and inspections, and consider surface treatments such as nickel plating and anodizing. These measures effectively enhance durability and longevity.
In which industries are aluminum injection molds commonly used?
Aluminum injection molds are commonly used in the automotive, medical devices, and consumer electronics industries because of their versatility and cost-effectiveness.