Looking to streamline your pallet production? A plastic pallet making machine can revolutionize your manufacturing process by ensuring consistent quality and high productivity.
In this article, we’ll explore everything you need to know about these machines, from their key features and working principles to their benefits and real-world applications.
What is a Plastic Pallet Making Machine?
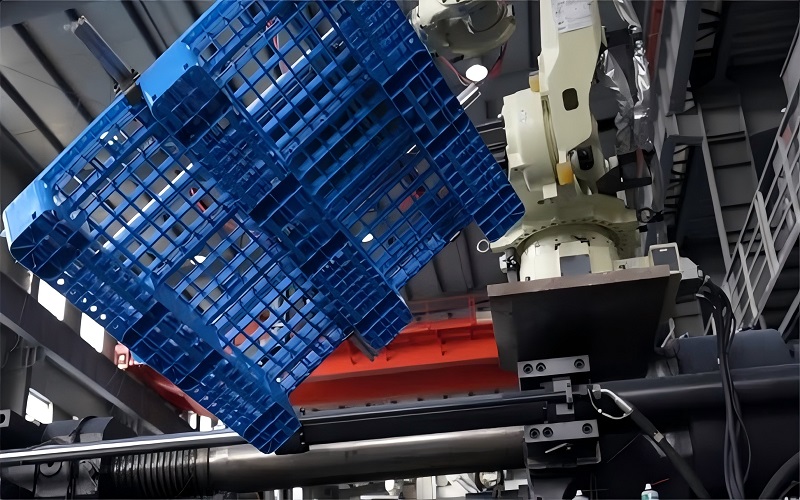
Plastic pallet making machines are specialized equipment designed to manufacture pallets used in storage, transportation, and logistics. These machines are the backbone of an efficient and reliable supply chain, ensuring that pallets are produced to precise specifications and uniform quality.
Unlike traditional methods, which often involve manual labor and variability, an automatic pallet making machine streamlines the manufacturing process by automating key steps, thereby enhancing productivity and consistency. Additionally, investing in quality pallet equipment can further optimize production efficiency.
The rise of automation in pallet manufacturing has brought about significant improvements. These machines speed up production and ensure each pallet meets stringent quality standards by removing manual intervention. This consistency is crucial for businesses that rely on high-quality pallets to protect their goods during delivery and storage.
Moreover, plastic pallets can be manufactured to exact dimensions, ensuring uniformity in pallet sizes and weight, which is vital for efficient stacking platform and handling.
Key Features of Plastic Pallet Making Machines
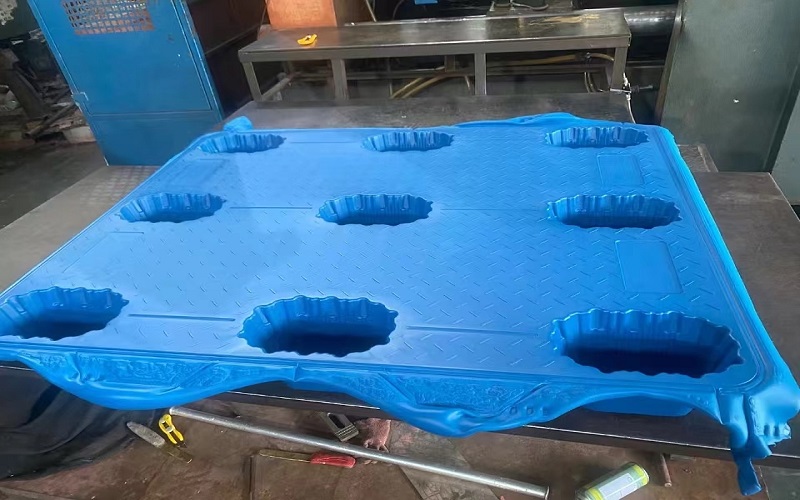
The key features of plastic pallet making machines are what truly set them apart from traditional pallet manufacturing methods. Here are some standout attributes:
- Full automation, eliminating the need for manual intervention
- Ensures consistent quality
- Significantly boosts productivity
- Designed for high output while maintaining low energy consumption
- Efficient and cost-effective
These features make plastic pallet making machines a superior choice for modern manufacturer pallet making.
Many modern plastic pallet machines come equipped with advanced hydraulic servo control systems. These systems provide quick response times and energy savings, enhancing the overall efficiency of the production process. Another notable feature is the two-platen injection molding mechanism, which offers both flexibility and efficiency, making it a popular choice among manufacturers.
Speed and precision are also critical in the production of high-quality pallets. Fast mold opening speeds shorten the production cycles, while large mold opening strokes offer increased flexibility to accommodate various production requirements and quick changeovers. Advanced parison control systems ensure precise weight and thickness regulation, contributing to the production of standardized pallets that comply with international standards.
These features collectively ensure that plastic pallet making machines are the ideal tool for producing high-quality pallets efficiently.
Working Principle of Plastic Pallet Making Machines
Understanding the working principle of plastic pallet making machines provides insight into their efficiency and reliability. The process begins with feeding waste plastic into an extruder, where it undergoes plasticization. This step transforms the raw materials into a malleable state suitable for molding. After plasticization, the material is stored and measured precisely to ensure the correct amount is supplied to the mold.
Once the material is in the mold, a hydraulic press applies pressure to form the plastic pallets. This press ensures that the pallets are shaped accurately and consistently. After molding, the cooling system solidifies the pallets, ensuring they maintain their shape and strength.
Finally, an automated removal device extracts the finished pallets from the production line, ready for use in various industries. This streamlined process highlights the efficiency and technological advancement embedded in modern pallet machinery, including automatic nailing.
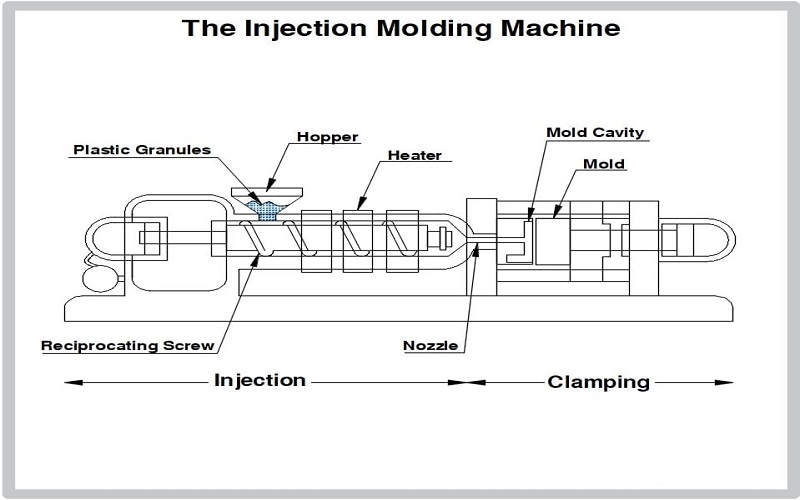
Technical Specifications of Popular Models
When it comes to choosing the right plastic pallet making machine, understanding the technical specifications of popular models is essential. The Stringer-Mate Model SS200, for example, features a hydraulic system requiring 110 volt, single head electricity. On the other hand, the PASS-ONE Pallet Dismantler is equipped with a 7.5 HP hydraulic power pack, highlighting its robust capabilities.
Other notable models include the CAM-WOOD 1AM-1180 Pallet Notcher, which has a power requirement of 10 HP and is wired for 220V, 3-Ph, with an option for 440V, 3-Ph. The Cherrys Industries pallet inverter has a 3 HP hydraulic package, and the Smart Machine Tool #64 boasts an output capacity of over 500 pallets per 8-hour shift, utilizing a pallet nailing machine.
These specifications provide a glimpse into the variety and capabilities of different models, helping businesses select the ideal tool for their specific service needs.
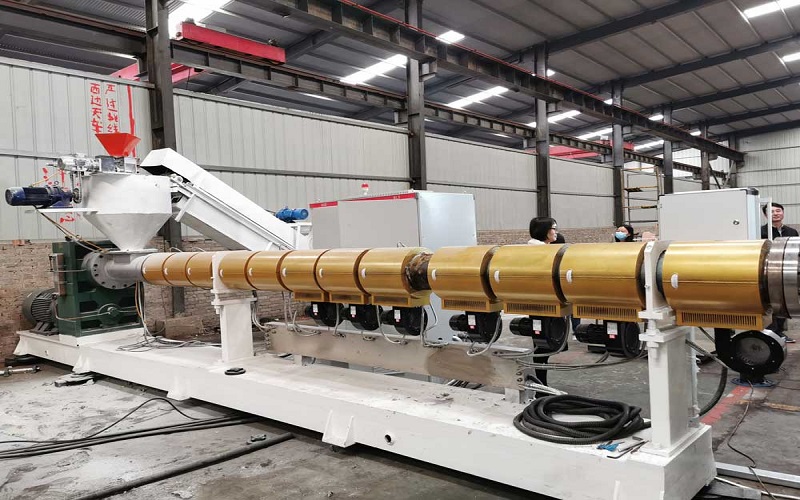
Types of Plastic Pallets Produced
Plastic pallets come in various designs to meet different industry needs. Common pallet types include stackable, rackable, and nestable models. A stacker pallet is designed to be stacked on top of one another, often utilizing automatic stacking features in a pallet nailer system, saving space and improving storage efficiency. Rackable pallets, on the other hand, are built to fit into racks, providing stability and support for heavy loads, and can be produced with extra nail guns for added durability during manufacturing.
Nestable pallets are particularly useful for saving space when not in use, as they can fit inside one another, benefiting from automatic feeding in the production process to ensure consistent assembly.
Additionally, block pallets and stringer pallets offer tailored solutions for different load capacities and applications, often crafted using a pallet nailer to meet specific requirements. These various types of plastic pallets ensure that businesses can find the right solution for their specific transportation and storage requirements.
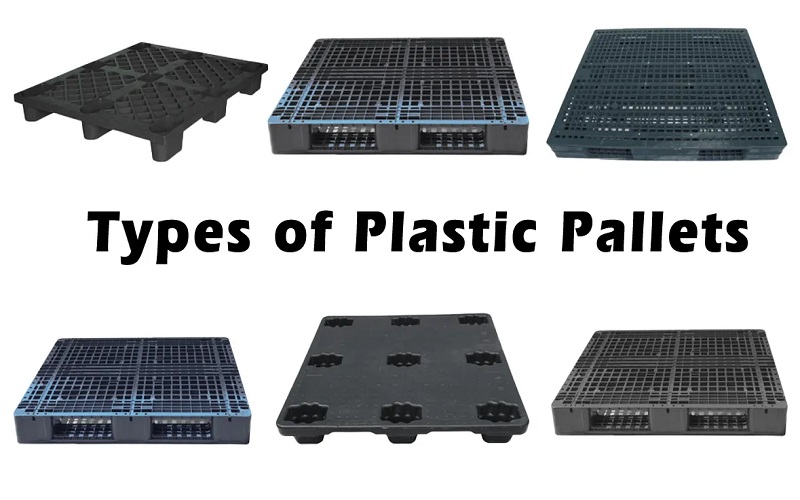
Benefits of Using Plastic Pallets
The benefits of using plastic pallets over traditional wooden pallets are numerous and significant. One of the primary advantages is their resistance to breakage, leading to a longer lifespan and reduced replacement costs. Plastic pallets can withstand extreme temperatures without deforming, making them a durable option for various industries, especially when produced with efficient systems like an outfeed conveyor to streamline post-production handling.
Another critical benefit is hygiene. Plastic pallets are non-porous and can be sanitized effectively, making them suitable for industries that require strict hygiene standards, such as food and pharmaceuticals. Their easy-to-clean surfaces ensure that they do not harbor bacteria or contaminants, maintaining a high level of hygiene.
Additionally, plastic pallets are preferred in the food and beverage sector due to their moisture resistance and easy sanitation, often benefiting from production setups that allow manual feeding for custom or small-batch runs.
Environmental benefits also play a significant role in the growing demand for plastic pallets. They are lightweight, reducing transportation costs and emissions. Furthermore, the process of compression molding used in their production requires minimal raw material processing, making it energy-efficient and environmentally friendly.
The transition to recyclable pallets has also helped businesses enhance their sustainability efforts while lowering shipping expenses, with systems like an outfeed conveyor ensuring efficient movement during manufacturing.
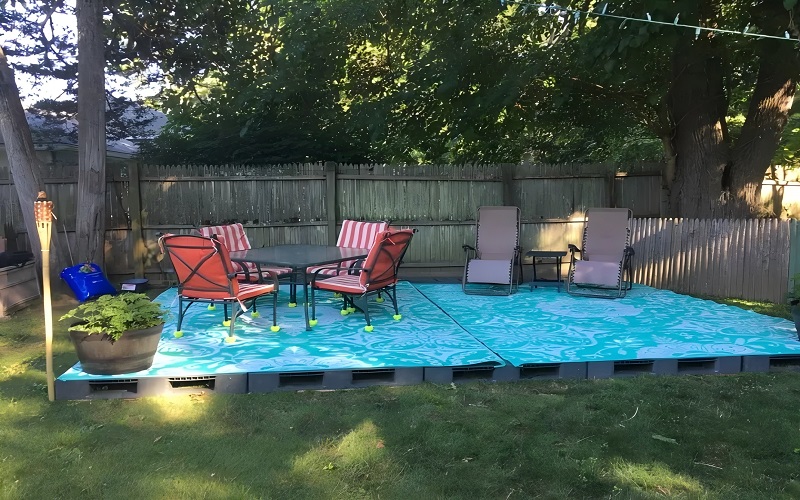
Applications of Plastic Pallets
Plastic pallets are utilized across various industries due to their versatility and durability. In the food and beverage industry, their lightweight design enhances inventory management and transportation efficiency. Similarly, the pharmaceutical industry benefits from the hygienic and sturdy nature of plastic pallets, which are ideal for transporting sensitive medical supplies.
The electronics sector uses plastic pallets as antistatic platforms to safely transport electronic components, minimizing static damage. In the construction industry, plastic pallets are valued for their durability and lightweight properties, making them ideal for transporting materials such as bricks and tiles.
Additionally, the textile industry relies on plastic pallets for transporting fabric rolls and garments, as their smooth surfaces prevent snags and damage. These diverse applications demonstrate the wide-ranging utility of plastic pallets in modern industries.
Cost Considerations and ROI
Investing in plastic pallet making machines involves significant costs, but the potential return on investment (ROI) can be substantial. The price includes installing a robotic palletizing system that can range from $175,000 to $550,000, depending on the complexity of the system. However, the advanced technology in these machines often results in lowered operational costs due to improved maintenance and energy efficiency.
Real-world examples highlight the financial benefits of automating pallet production. For instance, Sager Foods automated their palletizing process using cobot palletizers, achieving a payback period of just over a year by reallocating three operators to more valuable tasks. Similarly, Rev-A-Shelf realized a return on investment in less than 20 months after implementing two industrial robot palletizers, which helped them manage over 5,700 SKUs and reallocate eight operators.
The longevity and durability of plastic pallets also contribute to cost savings. They can last over 250 trips compared to just 5-7 for wooden pallets, significantly reducing waste and replacement costs. Their lighter weight reduces transportation costs, and their non-splintering nature ensures safer handling and less product damage. These factors collectively enhance the cost-effectiveness of investing in plastic pallet making machines.
Maintenance and Longevity
Maintaining plastic pallet making machines is crucial for ensuring their long-term reliability and performance. Regular cleaning of the machine area helps prevent debris accumulation that can hinder operation. Conducting visual inspections of components can identify potential issues before they lead to significant breakdowns, allowing for timely maintenance.
Lubricating the drive system using the correct type of lubricant is essential to operate smoothly. Additionally, replacing worn belts or chains promptly can prevent major mechanical failures.
Following the manufacturer’s recommendations for maintenance frequency and tasks is vital for keeping the machines in very good condition. Overall, consistent maintenance practices enhance the longevity and efficiency of plastic pallet making machines.
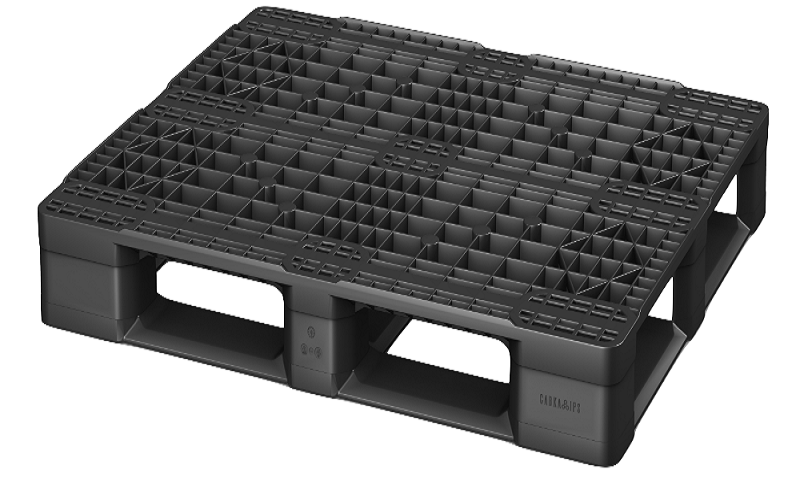
Choosing the Right Plastic Pallet Making Machine
Selecting the right plastic pallet making machine involves considering several key factors. One important aspect is the machine’s footprint. Choosing a machine that occupies less floor space can lead to reduced rental costs for manufacturing facilities. Evaluating the production volume is also crucial to ensure the machine can meet specific business demands.
Another factor to consider is the type of plastic pallets that can be produced. Different industries have varying needs, and it’s essential to select a machine that aligns with those requirements.
For instance, businesses in the food industry might prioritize hygiene and durability, while those in construction might focus on load capacity and strength. Ensuring the machine can produce the desired types of pallets is vital for achieving optimal results.
Case Studies and Success Stories
Real-world case studies and success stories highlight the tangible benefits of integrating plastic pallet making machines into business operations. Many businesses have adopted these machines to enhance their production capabilities and overall efficiency. For example, companies have reported significant improvements in workflow and output after implementing these advanced machines.
Achieving a favorable ROI often involves assessing the increase in productivity and reduction in labor costs against the initial investment. Businesses have experienced increased satisfaction and competitiveness in the market, showcasing the positive impact of adopting plastic pallet making machines.
These success stories provide valuable insights for customers considering selling this investment.
Future Trends in Plastic Pallet Manufacturing
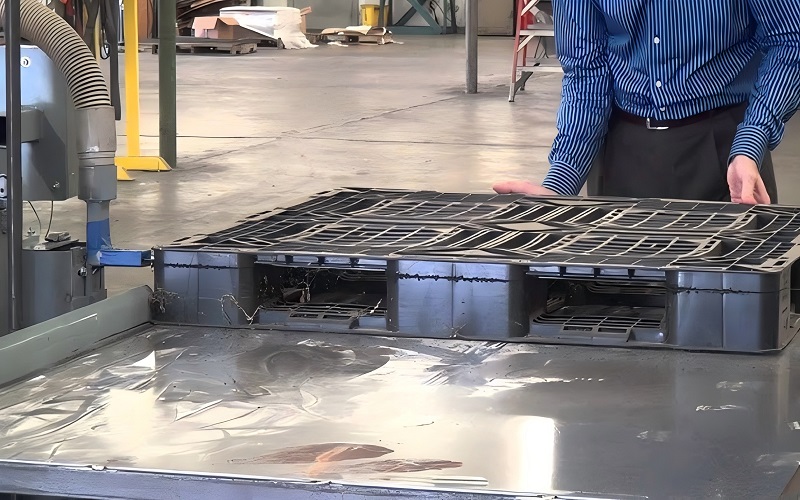
The future of plastic pallet manufacturing is set to be shaped by several emerging trends and technological advancements. One significant trend is the move towards closed-loop recycling systems, where the high recovery rates of materials contribute to sustainability. Despite the challenges of melting plastic for recycling, efforts are being made to enhance the eco-friendliness of this process.
Automation is another key trend, with projects that have approved capital funding expediting the automation process and significantly impacting ROI timelines. Operating robotic systems continuously, such as on two or more shifts, is ideal for maximizing ROI from automation investments and allowing for easy changeovers. Manufacturers also consider factors like labor availability and safety in their return on investment calculations.
These trends indicate a future where plastic pallet manufacturing becomes increasingly efficient and sustainable.
Summary
In summary, plastic pallet making machines represent a significant advancement in the manufacturing industry. They offer numerous benefits over traditional wooden pallets, including durability, hygiene, and cost-effectiveness.
The automation and advanced features of these machines ensure consistent quality and high productivity, making them a valuable investment for businesses across various industries.
As we look to the future, trends such as closed-loop recycling and increased automation promise to further enhance the efficiency and sustainability of plastic pallet manufacturing. By considering the insights and examples shared in this blog post, businesses can make informed decisions about investing in plastic pallet making machines, ultimately improving their operations and competitiveness.
Frequently Asked Questions
What are the main benefits of using plastic pallets over wooden pallets?
The main benefits of using plastic pallets over wooden pallets include greater durability, resistance to extreme temperatures, and improved sanitation, making them particularly suitable for industries such as food and pharmaceuticals.
How does automation in pallet making machines improve production?
Automation in pallet making machines enhances production by eliminating manual intervention, ensuring consistent quality, and significantly increasing productivity.
What factors should be considered when choosing a plastic pallet making machine?
Consider the machine’s footprint, production volume, and the specific types of plastic pallets it can manufacture to ensure it meets your operational needs.
Can plastic pallets be recycled?
Yes, plastic pallets can be recycled, contributing to environmental sustainability through a melting process. This recycling helps reduce waste and promotes the reuse of materials.
What are some of the future trends in plastic pallet manufacturing?
Future trends in plastic pallet manufacturing focus on closed-loop recycling systems and increased automation, which significantly enhance both efficiency and sustainability. Embracing these innovations will be crucial for adopting eco-friendly practices in the industry.