Injection molded nylon is essential in manufacturing for its strength and chemical resistance. This guide explains what it is, its types, benefits, and uses in different industries. You’ll also learn tips for optimizing the injection molding process.
What is Injection Molded Nylon?
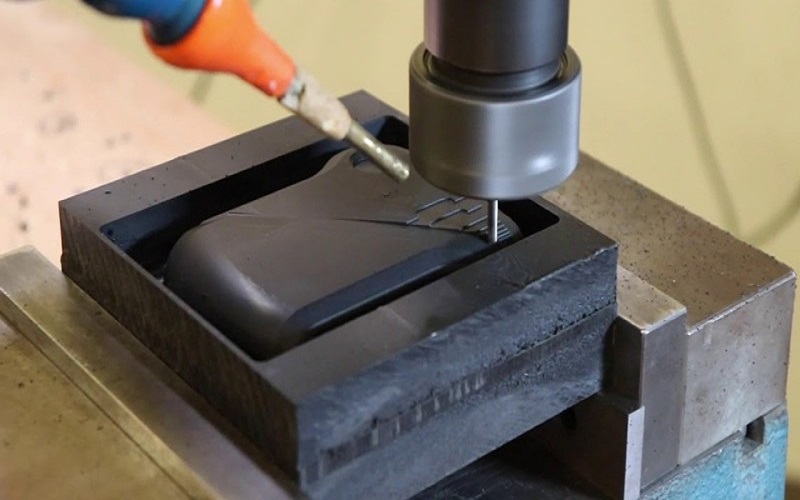
Injection molded nylon plastic is a synthetic polymer and a synthetic thermoplastic polymer commonly created by injecting molten nylon resin into molds to form desired parts through injection moulding.
This process, often referred to as nylon molding, is a cornerstone of modern manufacturing, allowing for the mass production of complex components with high precision. Nylon production, as a material, boasts high strength, low friction, and exceptional chemical and abrasion resistance, making it ideal for various applications.
One of the standout features of nylon is its ability to be reused without losing its properties after being melted for injection moulding, thanks to its high melting point (typically around 220–265°C, depending on the grade).
This not only makes it a cost-effective material but also aligns with sustainability goals. From automotive parts to household items, the versatile material of reinforced nylon, which includes additives like glass or carbon fibers for enhanced strength, in nylon molding is unmatched.
Types of Nylon Used in Injection Molding
The world of nylon injection molding is diverse, with several types of nylon used depending on the specific requirements of the application.
Common types include Nylon 6 (PA6), Nylon 66 (PA66), and modified nylon variants. PA6 is known for its good strength, stiffness, and excellent wear resistance, making it a popular choice in many industries.
PA12, on the other hand, offers excellent chemical resistance, flexibility, and impact resistance, making it suitable for more specialized applications. Nylon 66 is more heat resistant and has better mechanical properties compared to Nylon 6, making it ideal for high-performance requirements.
Additionally, modified nylons incorporate additives that enhance performance for specific needs, further broadening the material’s applicability.
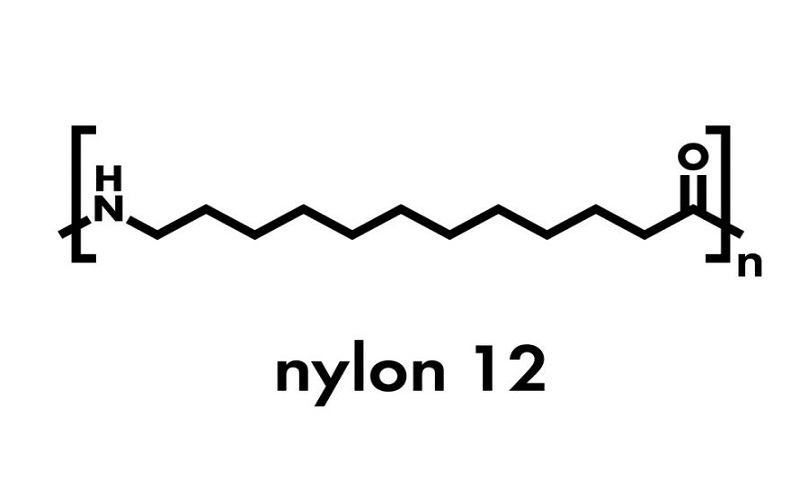
Advantages of Using Nylon for Injection Molding
Nylon injection molding offers a plethora of advantages that make it a preferred material in various manufacturing sectors. Here are some of the primary benefits:
- High tensile strength, which can be further augmented with specialized additives.
- Glass fiber is often blended with nylon to enhance its tensile and flexural strength.
- This makes nylon a suitable alternative to some metals in certain applications.
Moreover, nylon exhibits high resistance to various chemicals, including acids and solvents, which ensures longevity and durability in harsh environments. Its ability to withstand prolonged exposure to temperatures approaching 150°C makes it ideal for high-temperature applications.
The lightweight nature of nylon also contributes to sustainability in injection molded products by reducing material usage and energy consumption during production, compared to other materials.
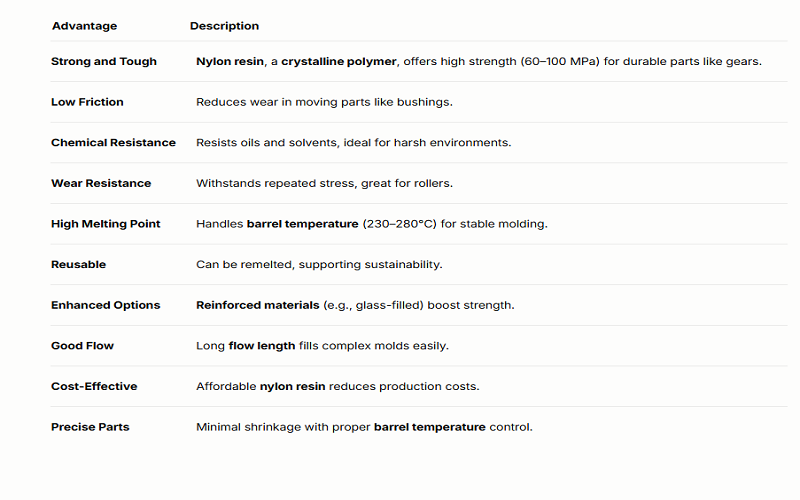
Key Factors in the Nylon Injection Molding Process
Several key factors play a crucial role in the nylon plastic injection molding process, each contributing to the quality and performance of the final product. Temperature control is paramount, as it affects everything from material flow to material’s crystallinity and mechanical properties.
The manufacturing process of injection pressure is equally important, ensuring that the molten nylon fills the mold accurately. Mold design considerations, such as gate location and wall thickness, also significantly impact the final product’s quality, including potential scrap-producing defects, particularly when using reinforced materials like glass-filled or carbon-filled nylon.
Temperature Control
Maintaining proper cylinder temperature control is crucial for achieving consistent quality and preventing defects in nylon injection molding. The melting temperature range for nylon typically falls between 230°C and 280°C, but it’s essential to stay within these limits to prevent thermal degradation.
Proper management of mold temperature can significantly influence the crystallinity and mechanical properties of nylon parts. Higher mold temperatures result in less shrinkage and allow for the production of thin-walled parts, which are often required in various applications.
Higher temperatures can also influence cooling time; insufficient cooling can lead to warping or shrinkage, compromising the dimensional stability of the molded parts. To reduce shrinkage, maintaining optimal molding temperature is essential.
Injection Pressure
Injection pressure plays a pivotal role in the nylon injection molding process. Nylon, a crystalline polymer, has a higher viscosity. As a result, it needs a higher injection pressure than some other plastics.
The typical pressure range during nylon injection molding is 75 to 125 MPa, and for Nylon 66 specifically, it can range from 60 to 200 MPa. Balancing the appropriate injection pressure is crucial; too much pressure can cause overflow or flashing defects, while too little can lead to incomplete mold filling, limiting the flow length of the molten material.
Adjusting the injection speed is also vital for filling the mold efficiently and avoiding defects like warping or flow marks. Optimizing injection speed, alongside precise barrel temperature control, helps achieve uniform filling and enhances the surface quality of the molded product.
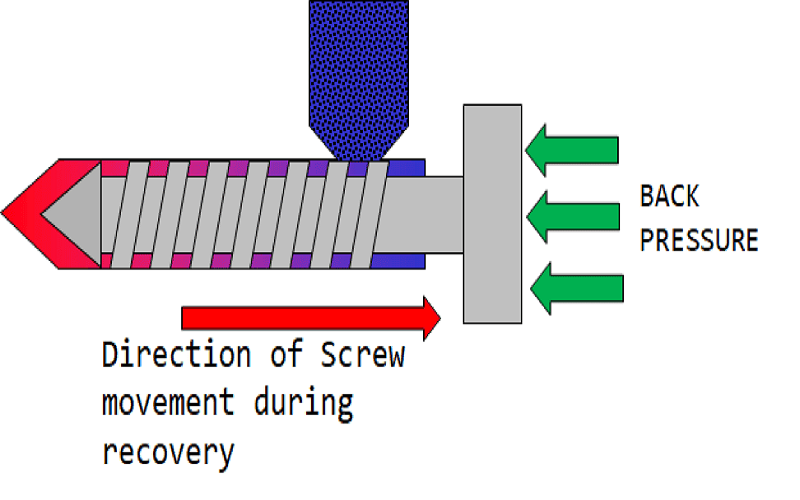
Mold Design Considerations
Mold design is a critical aspect of the nylon injection molding process. Key factors to consider include:
- Gate location
- Part ejection mechanisms
- Venting
- Mold wall thickness
Proper gate design facilitates smooth material flow and prevents issues like air entrapment. Understanding the shrinkage characteristics of nylon and its material properties is vital for designing molds that maintain dimensional accuracy, making it an ideal material for such applications.
Venting is necessary to prevent gassing issues that can lead to surface defects in the final product. Additionally, nylon’s low melt viscosity allows for effective molding of parts with thin features, supporting faster injection speeds.
Common Challenges in Nylon Injection Molding
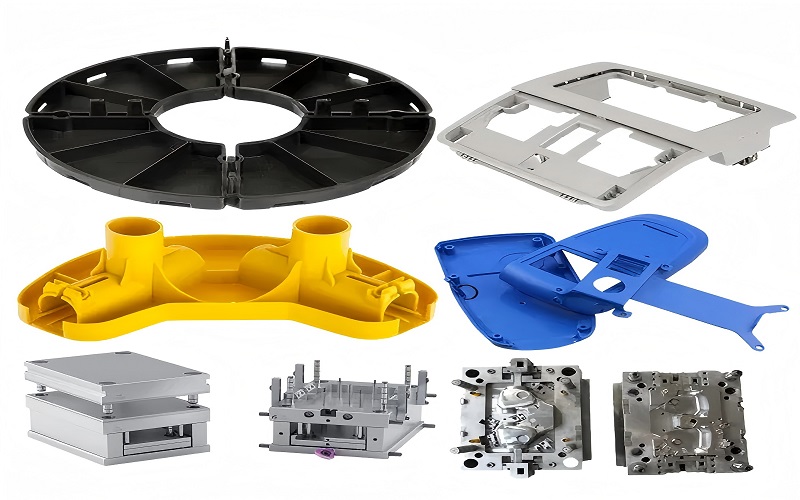
Nylon injection molding, while advantageous, comes with its own set of challenges. Moisture absorption and water absorption are significant issues; excessive moisture content can lead to brittleness in injection molded nylon products. Too much moisture can also cause voids and surface defects during the molding process. Therefore, drying nylon pellets before molding is crucial to prevent these issues, as it absorbs moisture effectively.
Shrinkage nylon is another common challenge in nylon injection molding, causing dimensional inconsistencies and warping. Nylon’s higher shrinkage rate compared to most thermoplastics can make maintaining tight tolerances difficult. Surface imperfections, such as bubbles and black spots, can result from improper injection pressure or overheating during the injection process.
Best Practices for Drying Nylon Pellets
Properly drying nylon pellets is essential for minimizing defects in the final product. Vacuum drying is highly recommended, with optimal temperatures between 80-120°C to prevent oxidation or discoloration. Nylon pellets should ideally be dried to a moisture level of 0.15% to 0.2% to prevent processing issues, typically needing around 16 hours at 80°C.
Hot-air drying can also be effective, but its efficacy is influenced by the initial moisture content, drying temperature, and relative humidity of the intake air. Utilizing dehumidifiers can enhance moisture removal, ensuring the pellets are adequately dried before the injection molding process.
Applications of Injection Molded Nylon
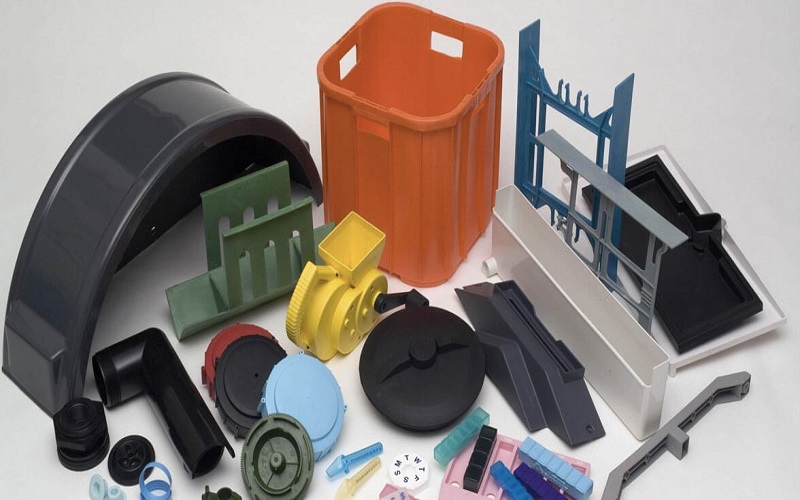
Nylon injection molding is employed across a wide array of industries due to its versatility and durability. In the automotive sector, it is used for creating engine parts, bearings, and fuel system components that withstand high temperatures and wear. Common automotive injection molding applications include engine covers, intake manifolds, and interior trim.
In the electronics industry, nylon material provides strong and durable industrial components for protective housings and electrical connectors, showcasing excellent mechanical properties of nylon polyamide and electronic components.
Industrial applications include gears, seals, and conveyor belts, which require high wear resistance and mechanical equipment strength. Nylon is also used in medical device manufacturing due to its strength and ability to be sterilized.
Comparing Nylon with Other Plastics for Injection Molding
When comparing nylon with other plastics like ABS, several factors come into play. Nylon demonstrates superior tensile strength, with values ranging from 70-100 MPa, whereas ABS is between 30-45 MPa. Nylon also has a higher heat deflection temperature, making it more suitable for high-temperature applications.
In terms of chemical resistance, nylon outperforms ABS by resisting a wider range of chemicals, including oils and solvents. However, ABS is generally more cost-effective, making it a preferred choice for mass production of consumer goods. Additionally, nylon’s higher processing temperatures can lead to longer cycle times in injection molding compared to ABS.
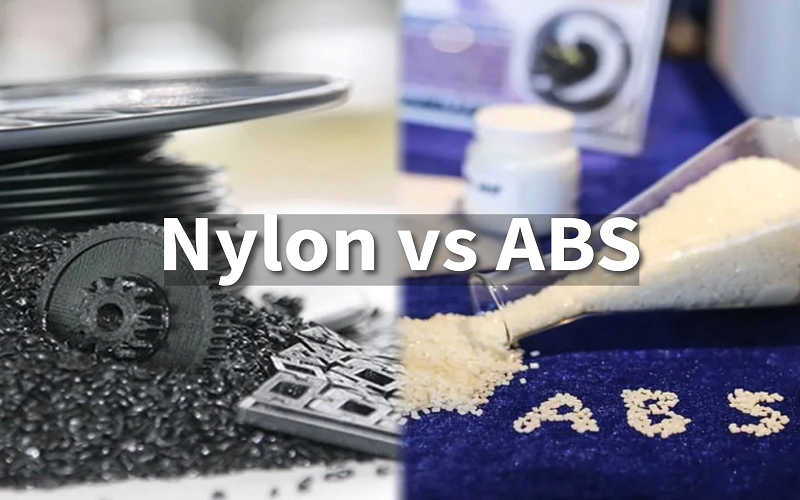
Tips for Optimizing Nylon Injection Molding
Optimizing nylon injection molding involves maintaining appropriate molding temperatures to ensure quality and minimize defects. Proper injection pressure is essential for accurately filling the mold cavity and achieving the desired part dimensions. Key mold design considerations include gate location, wall thickness, and venting to prevent defects.
Addressing challenges like moisture absorption is critical; guidelines on drying nylon pellets help prevent moisture-related defects. By following these best practices, manufacturers can optimize their nylon injection molding processes to produce high-quality parts consistently.
Summary
In summary, nylon injection molding offers numerous advantages, from high tensile strength and chemical resistance to versatility and cost-effectiveness. Understanding the key factors in the molding process, such as temperature control, injection pressure, and mold design, is crucial for achieving high-quality results. Common challenges like moisture absorption and shrinkage can be mitigated through proper drying and process optimization.
By applying the best practices and tips outlined in this guide, manufacturers can optimize their nylon injection molding operations, ensuring consistent quality and performance. Embrace the potential of nylon injection molding and take your manufacturing processes to the next level.
Frequently Asked Questions
Can nylon be injection molded?
Yes, nylon can be injection molded, as it is a synthetic thermoplastic polymer known for its versatility, durability, and high melting temperature, making it suitable for various applications. This makes nylon a popular choice in the manufacturing industry.
What is the difference between nylon 46 and nylon 66?
Nylon 46 differs from Nylon 66 primarily in its chemical structure and performance, offering superior heat resistance and mechanical strength, while Nylon 66 is more cost-effective and easier to process. This results in Nylon 46 having a higher melting temperature and crystallinity, enhancing its overall performance in demanding applications.
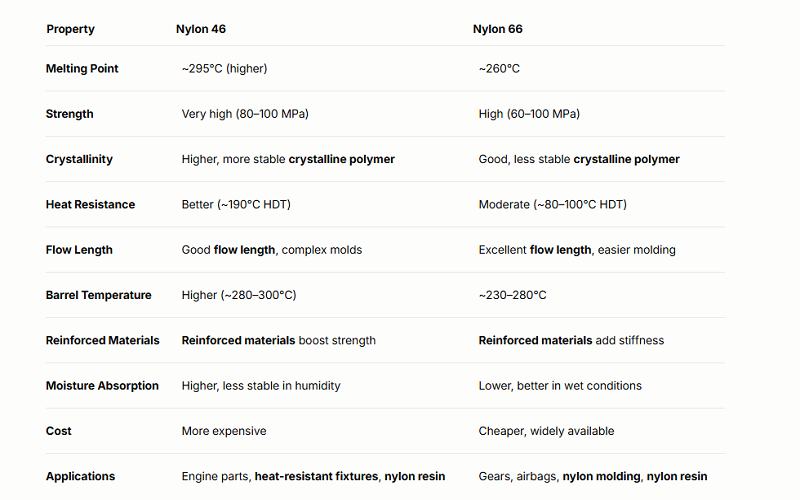
What is injected nylon?
Injected nylon is a type of high-performance thermoplastic that is commonly used in injection molding due to its strong mechanical properties and thermal stability, making it suitable for various engineering applications.
What is the best nylon for injection molding?
The best nylon for injection molding is Nylon 66 due to its superior mechanical properties and more ordered molecular structure compared to other types. This makes it ideal for applications requiring durability and strength.
What is the typical temperature range for nylon injection molding?
The typical temperature range for nylon injection molding is between 230°C and 280°C. Maintaining this range is crucial for achieving optimal material flow and part quality.