Curious about the different types of plastic injection molding? This article will provide a detailed look at various methods like hot runner molds, cold runner molds, multi-cavity molds, and specialized techniques. You’ll learn which method is best suited for your production needs.
Overview of Plastic Injection Molding

Plastic injection molding is a manufacturing process revered for its ability to produce manufacturing plastic parts in large quantities with exceptional consistency and strength. This technique is pivotal in modern manufacturing due to its efficiency, minimal waste, and reduced need for post-processing, making it ideal for high-volume production. The process, often executed using an injection moulding machine, involves heating plastic materials, including plastic resin, until they become molten plastic, which is then injected into a mold cavity where the part takes shape. The result is a highly repeatable production process capable of creating complex designs.
The injection molding process begins with the preparation of molten plastic. This involves heating the plastic material and pushing it towards the mold using a screw plunger, ensuring optimal flow and minimal defects under controlled injection pressure. The molten plastic flows then fill the mold cavity, where it cools and solidifies into the desired shape. This precise control over the injection process is crucial for achieving high-quality finished products, whether they’re medical devices, mechanical components, or consumer goods.
Automation plays a significant role in enhancing the accuracy and efficiency of plastic injection molding. Modern injection molding machines, including hydraulic injection molding machines, electric injection molding machines, and hybrid injection molding machines, offer diverse capabilities to meet various production requirements. Selecting the right mold type and machine, often complemented by cnc machining for precise mold fabrication, allows manufacturers to greatly influence production speed, costs, and product quality.
Classification Based on Feeding Systems
In the realm of injection molding, the feeding system, also known as the runner system, is crucial for directing molten plastic from the injection machine to the mold cavity. The design of this system significantly influences the quality, physical properties, and dimensional accuracy of the molded product. There are three primary types of feeding systems: hot runner, cold runner, and insulated runner systems.
Each feeding system offers unique advantages and challenges, catering to different production needs. Here are the types of feeding systems:
- Hot runner systems: These prevent plastic waste and allow for quicker production cycles, making them ideal for high-volume manufacturing.
- Cold runner systems: These are simpler but produce more waste.
- Insulated runner systems: These offer a cost-effective balance between efficiency and material usage.
Understanding these injection system is crucial for optimizing the injection molding process.
Hot Runner Injection Mold
Hot runner injection molds feature a heated runner system encased within a stationary manifold plate, preventing the plastic from solidifying in the runners. This design ensures a constant flow of molten plastic and molten material, reducing waste and improving production efficiency during each injection cycle. By maintaining the plastic in a molten state throughout the injection process, hot runner molds, supported by the injection unit, enable quicker production cycles and higher quality parts with minimal post-processing requirements.
Hot runner systems are particularly beneficial for high-volume production runs, where the cost savings from reduced waste and increased injection speed can be substantial. These molds, often incorporating durable metal components for enhanced longevity, are compatible with various types of injection molding machines, including hydraulic, electric, and hybrid machines, making them versatile for different manufacturing settings.
Hot runner molds help manufacturers achieve superior product consistency and efficiency.
Cold Runner Injection Mold
Cold runner injection molds use unheated runners to deliver molten plastic to the mold cavities. While this system is simpler and less expensive to set up compared to hot runner systems, it produces significant waste due to the solidified plastic left in the runners after each cycle. This waste needs to be manually removed and either recycled or discarded, adding to the overall production cost and time.
Despite the waste issue, cold runner molds are favored for their ease of maintenance and ability to facilitate quick material changes. They are suitable for smaller production runs and applications where the cost of a hot runner system cannot be justified.
Manufacturers must weigh the trade-offs between initial setup costs and ongoing waste management when choosing cold runner molds.
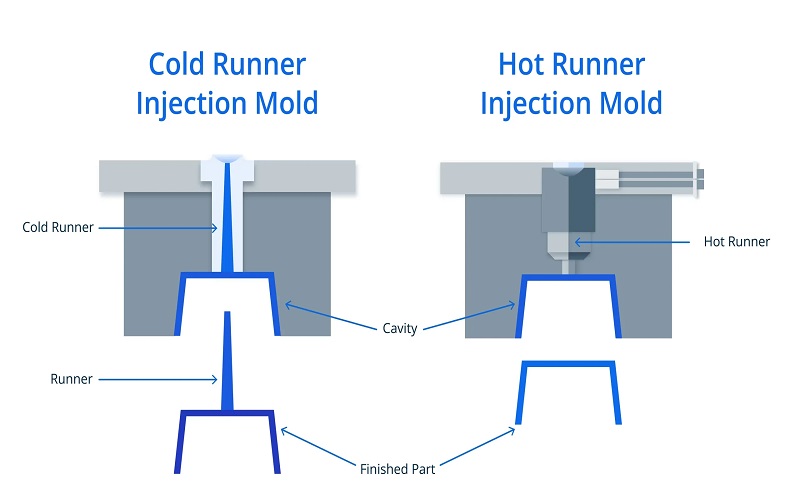
Insulated Runner Injection Mold
Insulated runner injection molds utilize heated elements to maintain a molten layer around the plastic flow, optimizing temperature management and reducing waste. This system creates a surrounding layer of molten plastic, ensuring that the material remains fluid throughout the injection process. As a result, insulated runner molds combine the benefits of hot and cold runner systems, offering a cost-effective solution for various production needs.
One of the primary advantages of insulated runner molds is their lower cost compared to hot runner systems, making them accessible for a wider range of manufacturers. Additionally, these molds allow for easier material changes, enhancing flexibility in production. Careful management of temperature and flow in insulated runner molds results in high-quality parts with minimal waste.
Classification by Number of Cavities
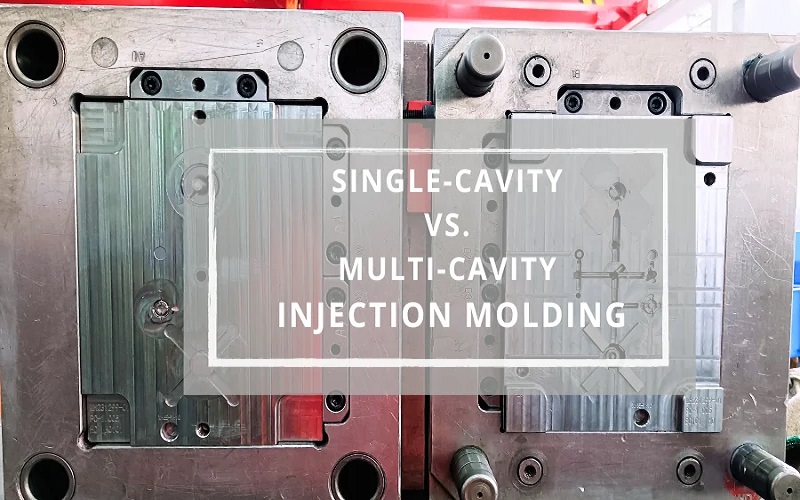
Mold designs can be classified based on the number of cavities they contain, which directly impacts production efficiency and cost. The three main categories are single cavity molds, multi-cavity molds, and family molds. Each type serves specific production needs, from low-volume, high-precision tasks to high-volume, cost-effective manufacturing.
Single cavity molds produce one part per molding cycle, making them ideal for low-volume production where quality and precision are paramount. In contrast, multi-cavity molds can produce multiple identical parts simultaneously, significantly enhancing production speed and reducing per-unit costs.
Family molds offer the unique advantage of producing different parts within the same mold, optimizing time and cost for projects requiring diverse components.
Single Cavity Mold
A single cavity injection mold produces one part per cycle, making it suitable for low-volume productions where quality takes precedence. These molds offer high-quality parts with better process control, reducing the likelihood of defects compared to multi-cavity molds. The tooling costs associated with single cavity molds are also lower, making them an economical choice for small-scale production.
Manufacturers often use multiple single cavity tools to maintain continuous production. This approach ensures a steady output while maintaining the flexibility to produce high-quality parts. Single cavity molds are particularly advantageous for custom or prototype production runs, where cost per part and process control are critical factors.
Multi-Cavity Mold
Multi-cavity injection molds are designed for high-volume production, capable of producing multiple identical parts in a single cycle. This design significantly enhances production efficiency, making it suitable for medium to large volumes of the same part. The unit part cost is lower with multi-cavity molds due to the simultaneous production of several components.
However, multi-cavity molds come with higher initial costs and require more maintenance compared to single cavity molds. They are also more prone to defects, necessitating balanced feed systems to ensure uniform filling of all cavities.
Despite these challenges, the efficiency gains make multi-cavity molds a preferred choice for mass production.
Family Mold
Family molds are designed to produce different parts simultaneously within the same mold. This capability allows manufacturers to optimize production time and cost, especially for projects requiring multiple components. By combining different parts in a single mold, family molds offer significant cost savings and improve overall production efficiency.
Unlike multi-cavity molds, which produce identical parts, family molds are ideal for diverse production needs. This versatility makes them a valuable asset for manufacturers looking to streamline their production processes and reduce lead times.
Family molds are particularly useful in industries where multiple small parts are required for assembly.
Classification Based on Mold Plate Design
The design of mold plates significantly impacts the efficiency, cost, and quality of the injection molding process. The three primary types are two-plate molds, three-plate molds, and stack molds, each offering unique advantages for different production scenarios. Understanding these designs helps manufacturers choose the most suitable option for their specific needs.
Two-plate molds are the simplest and most commonly used, featuring a single parting line. Three-plate molds introduce an additional stripper plate for automatic runner separation, enhancing efficiency. Stack molds consist of multiple parallel mold plates, allowing for increased production output without requiring larger machines. Each design serves distinct purposes, catering to various production volumes and complexities.
Two Plate Mold
Two-plate molds are commonly employed for simple components and typically feature a straightforward single-parting line. These molds are particularly effective for producing parts with less complexity, ensuring easier setup and maintenance. The simplicity of two-plate molds, which can be seen as having two primary components, makes them a cost-effective choice for various manufacturing applications.
By aligning the gate and runner system and parting line precisely, two-plate molds ensure consistent product quality. This alignment is crucial for achieving high precision and reducing potential defects in the final product.
Two-plate molds are versatile and can be used with various types of injection molding machines and an injection molding machine, making them a popular choice in the industry.
Three Plate Mold
The three-plate mold design is commonly used in multi-cavity molds, featuring an additional stripper cavity plate for automatic runner separation. This design improves the efficiency of the molding process by facilitating the automatic removal of runners, reducing manual labor and post-processing time.
Three-plate molds are ideal for complex parts and high-volume production runs, where efficiency and automation are crucial. By incorporating an additional plate, these molds provide greater flexibility in mold design and part ejection.
This feature makes three-plate molds a preferred choice for manufacturers seeking to optimize production cycles.
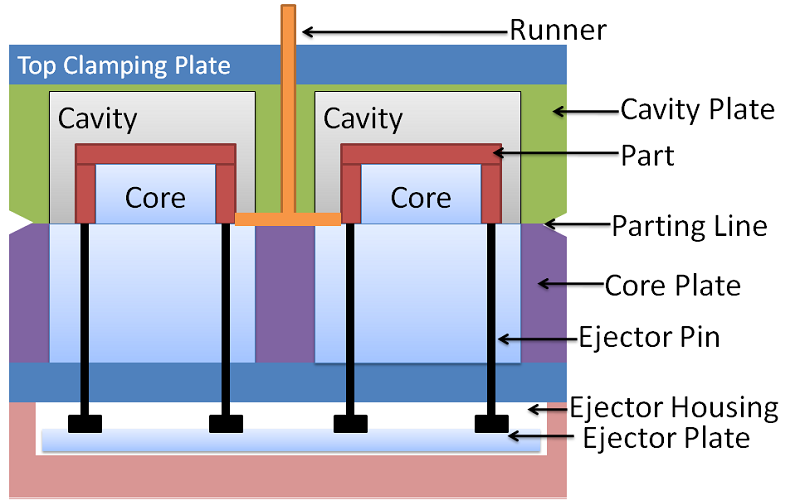
Stack Mold
Stack molds consist of multiple parallel mold plates, typically featuring two to four levels. This design allows for increased production output without necessitating larger molding machines, optimizing space and resources. Stack molds are particularly advantageous for high-volume production runs where maximizing efficiency is essential.
However, stack molds come with higher upfront costs and require longer build times due to their complex construction. Despite these challenges, the benefits of increased output and space optimization make stack molds a valuable investment for large-scale manufacturing operations.
By leveraging stack molds, manufacturers can achieve higher production volumes without compromising on quality.
Specialized Injection Molding Techniques
Specialized injection molding techniques enable the creation of intricate shapes and designs that may be challenging to achieve through traditional methods. These advanced techniques offer high precision and customization, catering to complex product requirements. The three main techniques include gas-assisted injection molding, thin-wall molding, and liquid silicone injection molding.
Each technique serves specific purposes, from creating hollow sections with gas-assisted molding to producing lightweight, durable parts with thin-wall molding. Liquid silicone injection molding is particularly useful for medical and electronic components, offering high durability and flexibility.
Understanding these techniques allows manufacturers to choose the best method for their unique production needs.
Gas-Assisted Injection Molding
Gas-assisted injection molding injects pressurized gas into the mold after molten plastic to create hollow sections. This technique is ideal for producing lightweight, complex parts, including an injection molded part, with reduced material usage and enhanced structural integrity. The gas creates internal channels within the part, improving strength and reducing weight.
Gas-assisted molding is commonly used in automotive parts and consumer goods industries, where lightweight and durable parts are essential. This technique enables high production efficiency and cost savings, making it a valuable addition to the injection molding process.
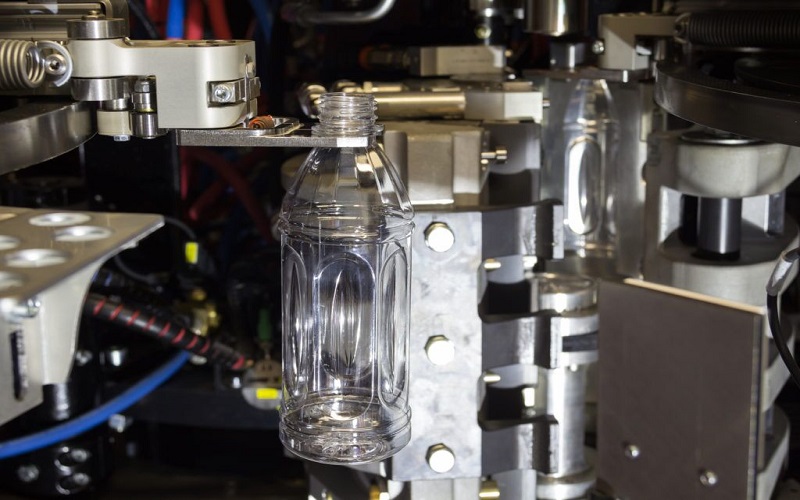
Thin-Wall Molding
Thin-wall molding is a specialized injection molding technique used to create parts with very thin walls, maintaining structural integrity while reducing weight. This process requires precise and advanced machinery capable of maintaining the correct temperatures and pressures, key to producing high-quality thin-walled parts. The result is lightweight yet strong products, ideal for applications where weight reduction is critical, such as in automotive and consumer electronics.
The benefits of thin-wall molding extend beyond weight savings. Reducing material usage with this technique also lowers production costs and enhances cycle times, resulting in a highly efficient manufacturing process. Manufacturers can produce complex and detailed parts with narrow dimensional tolerances, ensuring superior quality and performance.
Liquid Silicone Injection Molding
Liquid silicone injection molding is primarily used to produce silicone rubber parts, making it ideal for applications in medical and electronic components. This process allows for the creation of highly durable and flexible silicone parts required in sensitive applications such as healthcare. The liquid silicone injection molding process utilizes heated molds for shaping and curing silicone, ensuring precise dimensioning and rapid cycle times due to the quick curing properties of liquid silicone.
Additionally, this technique minimizes waste as melted silicone is used directly in the molds without the need for additional fillers. The molds are engineered specifically to withstand high temperatures and facilitate the flow of silicone effectively. Liquid silicone injection molding allows manufacturers to achieve high efficiency and precision in producing quality silicone parts.
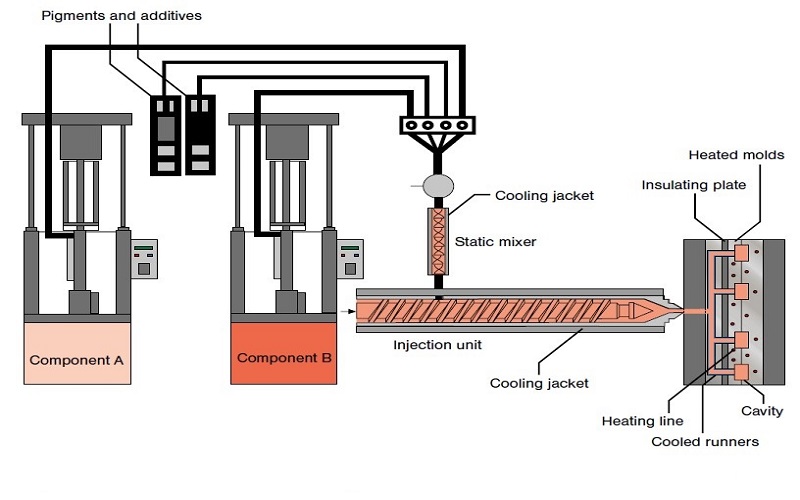
Key Components of Injection Molds
Injection molds consist of several key components that are essential for shaping plastic products. These components include the types of injection molds, the mold base, the mold cavity, ejector pins, and the sprue and runner system, as well as injection molding molds.
Each part plays a crucial role in ensuring the efficiency and quality of the injection molding process.
The mold base serves as the structural framework for the mold, typically constructed from various steel plates to ensure durability. The mold cavity determines the shape of the final product and can exhibit single or multi-cavity designs for different production needs, including mold opening.
The feeding systems in injection molds include essential channels like gates, sprues, and runners which direct the molten plastic into the mold. Other structural components, such as clamping plates, ensure that the mold halves are securely attached during the injection process and properly aligned.
Mold Cavity
A mold cavity is the space within the mold where the plastic part is formed. Single-cavity molds feature one mold cavity, making them suitable for low-volume production with better process control. Multi-cavity molds have multiple cavities, allowing for the simultaneous production of identical parts, thereby enhancing manufacturing efficiency.
Choosing the right mold design, whether single or multi-cavity, is crucial to meet production demands and cost-effectiveness. The mold cavity’s design directly impacts the shape, size, and quality of the final product, making it a key consideration in the injection molding process.
Ejector Pins
Ejector pins are essential for removing cooled parts from the mold. Once the injection process is complete, the ejector pins push the finished part out of the mold cavity, ensuring a smooth ejection process. This stage is critical as it prevents damage to the part and ensures consistent quality.
Ejector plates serve to mount ejector pins and facilitate their movement during the ejection process, utilizing an ejection system. Various features such as pins, blades, or other mechanisms can be used to release the molded part, depending on the part’s complexity and design requirements.
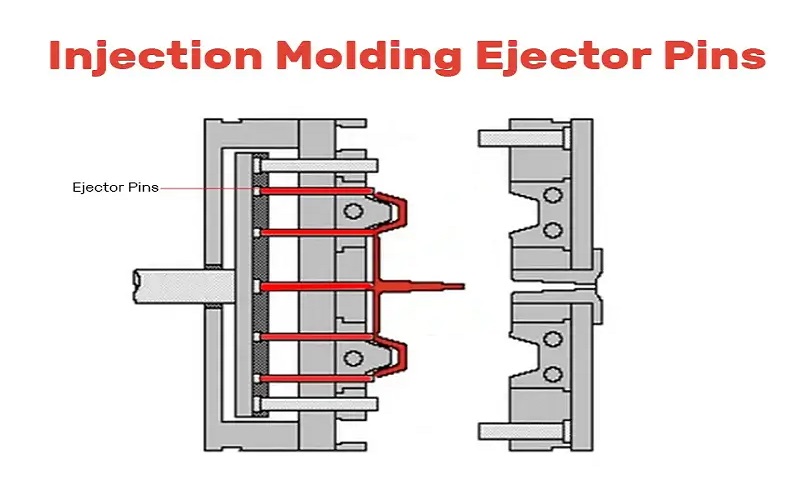
Sprue and Runner System
The sprue and runner system channels molten plastic to the mold cavities. The sprue distributes liquid plastic into the mold, while the runners guide the plastic flow from the sprue bushing to the gate. Proper design and location of these elements are crucial as they affect the appearance, dimensions, and warping of the molded parts.
Gating determines how material will flow into and fill the cavity, impacting the final product’s quality and potentially leading to excess material. Optimizing the sprue and runner system enhances production speed and ensures consistent part quality.
Choosing the Right Injection Mold for Your Project
Selecting the appropriate injection mold for your injection molding project is a critical decision that influences production efficiency, cost, and product quality. Understanding the quantity of parts to be produced is crucial in determining the appropriate mold type. Different stages of project development require varying mold types, from low-cost prototypes to high-quality production molds.
Transparent communication about budget and timelines aids manufacturers in guiding mold selection effectively. The Plastics Industry Association has established a classification system to help buyers compare molds based on quality and expected lifespan. This system provides a benchmark for evaluating mold options and ensuring that the chosen mold meets the project’s specific requirements.
Part complexity may necessitate the use of specific materials for mold construction, such as hardened steel. Injection molding is highly cost-effective for mass production due to reduced per-unit costs as production volume increases. Considering these factors and collaborating with mold suppliers allow manufacturers to make informed decisions that optimize production processes.
Why Injection Molding is Essential for Manufacturers
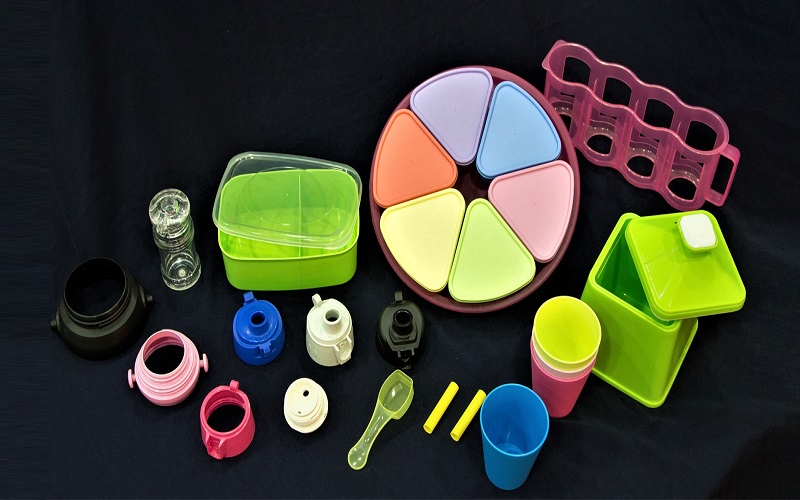
Injection molding is recognized for its efficiency and cost-effectiveness in large-scale production. The process allows for rapid production cycles, making it suitable for both small and large manufacturing runs. Often, injection molding is the most economical production method for large volumes of parts.
This manufacturing method guarantees high precision and consistency, crucial for industries needing exact specifications. Plastic injection molding is used across various industries, including automotive, consumer goods, medical, and aerospace. Recent technological advancements in injection molding, including smart manufacturing, have further improved operational efficiency.
Summary
In conclusion, plastic injection molding is a cornerstone of modern manufacturing, offering unparalleled efficiency, precision, and versatility. By understanding the various types of injection molds and their specific applications, manufacturers can optimize their production processes and achieve high-quality results. From the simplicity of two-plate molds to the complexity of stack molds, each type serves unique purposes tailored to different production needs.
Choosing the right injection mold involves careful consideration of production volume, part complexity, and budget. By leveraging the insights provided in this guide, you can make informed decisions that enhance your manufacturing capabilities and drive cost-effective, high-quality production. Embrace the power of injection molding and unlock new possibilities for your manufacturing projects.
Frequently Asked Questions
How many types of injection molding are there?
There are various types of injection molding, including two-color molds, overmolding, and family molds, each providing distinct advantages based on their characteristics and functions. Understanding these different types can enhance efficiency in the production process.
What is the hardest plastic for injection molding?
Polycarbonate (PC) is the hardest plastic for injection molding, known for its exceptional strength and shatter-resistant properties. This makes it an ideal choice for applications requiring durability and transparency.
What is the best plastic for injection molding?
The best plastic for injection molding is often considered to be low-density polyethylene (LDPE) due to its flexibility, moisture resistance, and ease of processing. Alternatively, polycarbonate is an excellent choice for applications requiring high strength and shatter resistance.
What are the 5 types of plastic molding?
The five types of plastic molding are extrusion molding, compression molding, blow molding, injection molding, and rotational molding. Each method offers unique benefits suited to various manufacturing needs.
What is the main advantage of using a hot runner injection mold?
The main advantage of using a hot runner injection mold is the reduction of plastic waste and the acceleration of production cycles, as it maintains a constant flow of molten plastic, preventing solidification in the runners.