MIM metal injection molding uses a mix of metal powders and plastic binders to create intricate, high-precision parts. In this article, we break down the MIM process, discuss its benefits and drawbacks, and explore its applications in different industries.
Understanding MIM Metal Injection Molding
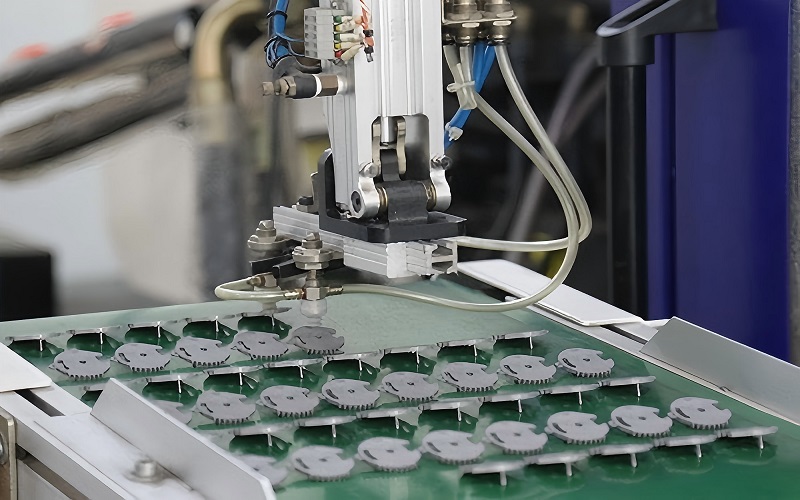
At its core, Metal Injection Molding (MIM), also known as powder injection molding, is a sophisticated process that merges the principles of powder metallurgy with the techniques of plastic injection molding, as metal injection molding combines the fabrication of solid metal parts.
The journey of MIM begins when the mim process starts with:
The blending of fine metal powders and plastic binders to create a feedstock.
The feedstock is then injected into molds.
The injected parts are debound.
Finally, the parts are sintered to achieve near-theoretical density.
The MIM process has evolved significantly since its inception in the 1970s. Adapting plastic injection molding technology for metal substrates, MIM enables the production of complex metal parts with precision and efficiency. This process is particularly valuable for creating components that require high density, intricate geometries, and tailored physical properties.
Understanding MIM requires exploring its key stages:
- Compounding metal powders
- The injection molding process
- Debinding techniques
- Sintering
Each stage is vital in transforming raw materials into high-quality wrought materials metal parts through the manufacturing process.
Compounding Metal Powders
A MIM part’s journey begins with the careful compounding of fine metal powder and plastic binders. This step creates a uniform feedstock for the metal injection molding process.
Typically, the feedstock comprises a blend of fine metal powders and metal powder particles with a diameter of about 20 microns and thermoplastic binders in a 60:40 volume ratio.
After blending, the mixture is cooled and granulated into pellets, ready for the next stage. The compounding phase is tightly controlled to ensure consistent quality and performance of the MIM feedstock.
Injection Molding Process
In the injection molding stage, the feedstock pellets are first heated until they melt. This molten feedstock is then injected into molds with multiple cavities using injection molding machines, forming what are known as ‘green parts’. The mold shapes the feedstock, and its design is optimized to ensure proper flow and avoid defects like sink marks and warping, especially for complex features like internal and external threads.
The mold design’s precision directly impacts the final product’s quality. The green parts, still containing the plastic binder, are then ready for the next stage: debinding of the molded part in the mold cavity. The green part is crucial in this process.
Debinding Techniques
Debinding, a crucial step in MIM, involves carefully removing the plastic binder from the green parts during the binder removal process. Two primary methods are used: catalytic and solvent debinding.
Catalytic debinding employs acid gases like nitric or oxalic acid, making it suitable for polyacetal-containing thermoplastic binder material that is uniformly coated around metal powders, resulting in shorter processing times. Binder removal is essential for achieving the desired properties in the final product, using only enough binder to ensure structural integrity during molding.
Alternatively, solvent debinding involves soaking green parts in solvents such as acetone or heptane. Although slower, this method is effective for different binder systems. Advanced techniques like supercritical fluid debinding offer economical and environmentally friendly options.
Post-debinding, the parts, now called ‘brown parts,’ are ready for sintering.
Sintering in MIM
Sintering is the transformative stage in MIM, known as the sintering process. It involves heating the debound parts to a high temperature furnace in thermal furnaces, often following a catalytic process to ensure thorough binder removal. The heat causes the metallic particle components to bond together, significantly enhancing the density and mechanical properties of the final product.
During sintering, the parts undergo partial melting, allowing the finely powdered metal and any remaining binders to fuse into a solid form. This step is critical for achieving the desired properties and ensuring that the metal injection molded parts meet stringent quality standards.
Advantages of MIM Metal Injection Molding
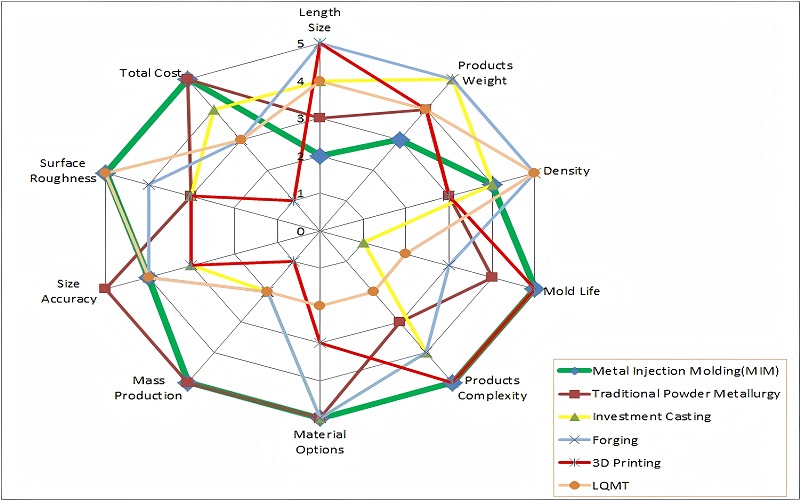
Metal Injection Molding offers a host of advantages that make it a preferred choice for many industries. Here are some key benefits:
- Ability to produce complex geometries with high precision
- Often eliminates the need for additional machining or finishing processes
- Reduces production costs
- Enhances material efficiency by minimizing waste
These advantages contribute to its popularity in various manufacturing applications.
Additionally, MIM is highly scalable and ideal for high-volume production runs. Its integration of automation enhances production efficiency, ensuring consistent quality across large batches of parts. These advantages make MIM a cost-effective solution for manufacturing intricate components.
High Volume Production
The ability of MIM to handle high volume production is one of its standout features. By integrating powder metallurgy with plastic injection molding, MIM can produce large quantities of parts at relatively low costs, comparable to traditional wrought metals manufacturing. Automation in the MIM process further enhances productivity by reducing cycle times and increasing output.
This efficiency makes MIM ideal for industries requiring mass production of intricate components. The process ensures consistent quality, allowing manufacturers to meet high demand without compromising on precision.
Precision and Complexity
MIM excels in producing parts with tight tolerances and complex geometries. The process allows for intricate designs that would be challenging or costly to achieve with other manufacturing methods, such as those relying on liquid phase processing. This capability is especially valuable for small, intricate parts that require high precision.
MIM allows manufacturers to achieve the desired mechanical properties and dimensional accuracy directly from the mold, often enhanced by hot isostatic pressing to improve density, reducing the need for additional finishing processes and enhancing production efficiency.
Material Efficiency
Material efficiency defines the MIM process. By converting a significant amount of input material into usable parts, MIM minimizes material waste and optimizes resource use. The process can achieve a material utilization rate of up to 98%, making it highly efficient compared to other methods like investment casting and die casting.
High material efficiency reduces costs and aligns with sustainable manufacturing practices, making MIM an environmentally friendly option for producing metal parts while promoting less material waste.
Challenges and Limitations
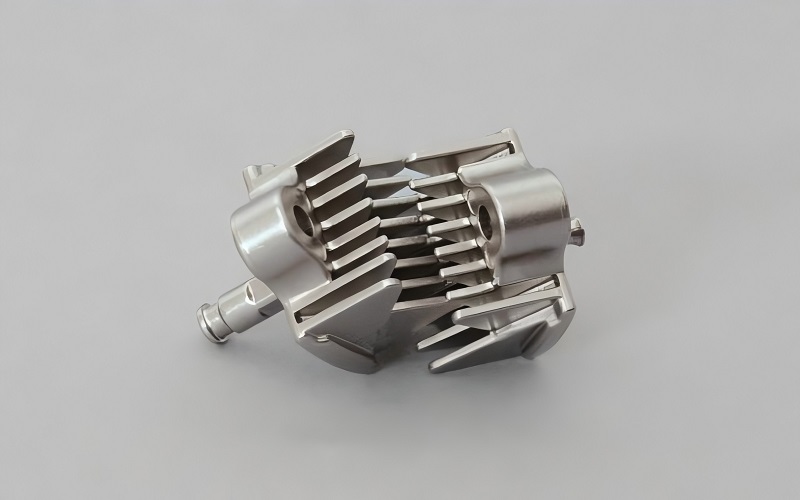
While MIM offers numerous advantages, it also has its challenges and limitations. One significant limitation is the range of materials that can be processed through MIM. Not all metals are suitable for this process, particularly those that are reactive, toxic, or have low melting points.
Additionally, MIM parts can be prone to defects such as warping and sink marks during the injection and sintering stages. These defects can often be mitigated through thoughtful design and process control, but they represent a potential challenge for manufacturers.
Unsuitable Metals
Certain metals are not well-suited for MIM due to their reactivity or toxicity. Metals that are highly reactive can pose safety risks during processing and may lead to undesirable chemical reactions. Additionally, materials like aluminum alloys, which have lower melting points, are generally not used in MIM.
Selecting the right material is crucial for the MIM process’s success. While MIM offers a wide range of material options, understanding the limitations can help manufacturers make informed decisions and avoid potential issues.
Potential Defects
Defects such as warping and sink marks are common in MIM but can be minimized through careful design and process control. Distortion during the debinding and sintering stages can lead to significant defects, impacting the quality of the final product.
Maintaining consistent wall thickness and avoiding overly complex geometries can eliminate defects. Thoughtful design considerations can greatly enhance the quality and performance of MIM parts, ensuring they meet the desired specifications.
Applications of MIM Metal Injection Molding
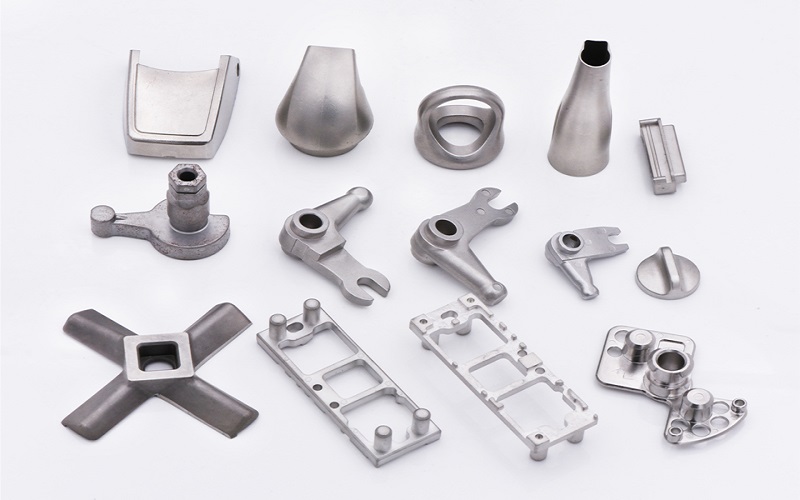
The versatility of MIM makes it suitable for a wide range of applications across various industries. In the medical field, MIM is used to create biocompatible implants that integrate well with the human body, offering a significant advantage for medical device manufacturers.
In the aerospace industry, MIM produces lightweight parts with complex geometries, enhancing fuel efficiency and performance. The technology also supports the production of intricate components in the automotive and electronics industries, where precision and durability are paramount, showcasing the advantages of mim technology.
Beyond these sectors, MIM is used in consumer goods, sporting equipment, and even jewelry. Its ability to produce detailed designs and complex shapes makes it a valuable tool for creating innovative products across different sectors.
Secondary Operations and Finishing
Secondary operations refine MIM parts to meet specific performance, dimensional, and aesthetic standards. Common secondary operations include coining, machining, surface treatments, and heat treatments. These processes enhance the dimensional accuracy, surface finish, and mechanical properties of the final parts.
Automated dimensional inspection and non-destructive testing ensure the quality of MIM parts and dimensional tolerances during secondary operations. These steps help manufacturers maintain high standards and meet the specific requirements of different applications.
Comparing MIM with Other Manufacturing Processes
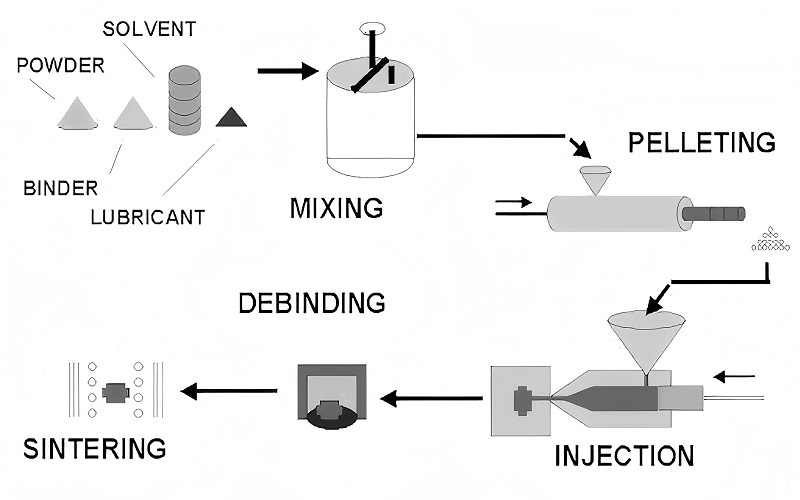
Compared to other manufacturing processes, MIM efficiently produces small, complex metal components. While die casting is faster and ideal for high-volume production, MIM remains a cost-effective choice for medium to high volumes, especially for intricate designs. The integration of powder metallurgy and plastic injection molding gives MIM a unique edge in terms of precision and material efficiency.
MIM is generally more economically favorable than casting, forging, and machining for producing complex components. Minimizing material waste and reducing required operations further enhances its cost-effectiveness, especially in a mim operation.
Design Considerations for MIM Parts
Design considerations are critical for optimizing MIM parts. Choosing the right wall thickness is crucial, as excessively thin walls can lead to warping and filling issues. Effective venting and gate designs are also essential to ensure proper mold filling and air evacuation.
Rounded corners are preferred over sharp corners to avoid defects, and strategic placement of parting lines can minimize their impact on the part’s function and appearance. Understanding these design principles can help manufacturers produce high-quality MIM parts with fewer defects.
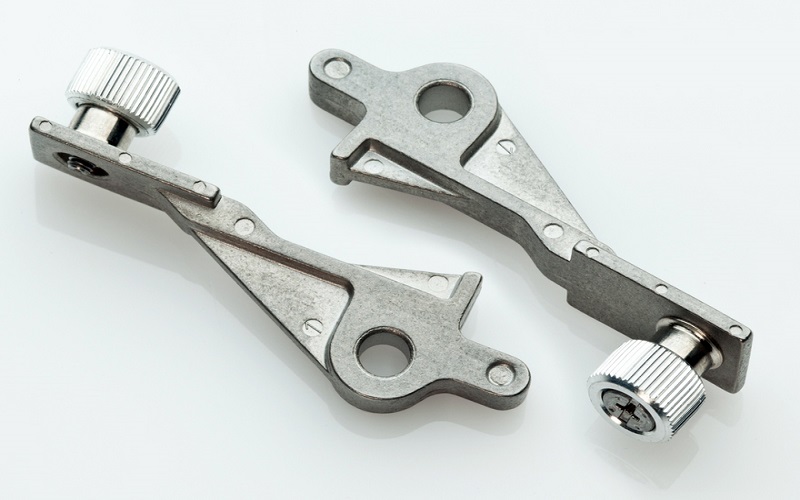
Summary
In summary, Metal Injection Molding (MIM) is a powerful manufacturing process that combines the best of powder metallurgy and plastic injection molding. It offers numerous advantages, including high precision, complex geometries, and material efficiency.
Despite its challenges, such as material limitations and potential defects, MIM remains a cost-effective and versatile solution for producing intricate metal parts.
By understanding the intricacies of the MIM process, manufacturers can unlock new possibilities for innovation and efficiency. As MIM technology continues to evolve, it will undoubtedly play a crucial role in shaping the future of manufacturing.
Frequently Asked Questions
What is Metal Injection Molding (MIM)?
Metal Injection Molding (MIM) is an advanced manufacturing technique that merges powder metallurgy with plastic injection molding to efficiently produce high-density metal components with intricate shapes and precise dimensions. This process allows for the mass production of complex metal parts with exceptional accuracy.
What types of metals are used in MIM?
MIM primarily utilizes fine metal powders including stainless steel, titanium alloys, and cobalt alloys, while avoiding reactive, toxic, or low melting point metals like aluminum alloys. This ensures optimal performance and safety in the manufacturing process.
What are the main advantages of using MIM?
The main advantages of using Metal Injection Molding (MIM) include its ability to produce complex geometries with high precision, high-volume production efficiency, and minimized material waste, making it a cost-effective solution for intricate parts that might require extensive machining otherwise.
What are the potential defects in MIM parts and how can they be avoided?
Potential defects in MIM parts, such as warping and sink marks, can be avoided by implementing design best practices like ensuring uniform wall thickness and simplifying geometries. This proactive approach leads to higher quality finished products.
What industries benefit the most from MIM?
Industries such as medical devices, aerospace, automotive, electronics, consumer goods, and jewelry benefit the most from MIM due to its capacity to produce complex, high-precision parts essential for intricate designs and high-performance applications.