Draft angles in injection molding are critical for smooth part ejection. These slight tapers on the mold walls prevent sticking, reduce defects, and lower production costs. Mastering draft angles ensures efficient, high-quality manufacturing.
Understanding Draft Angles in Injection Molding
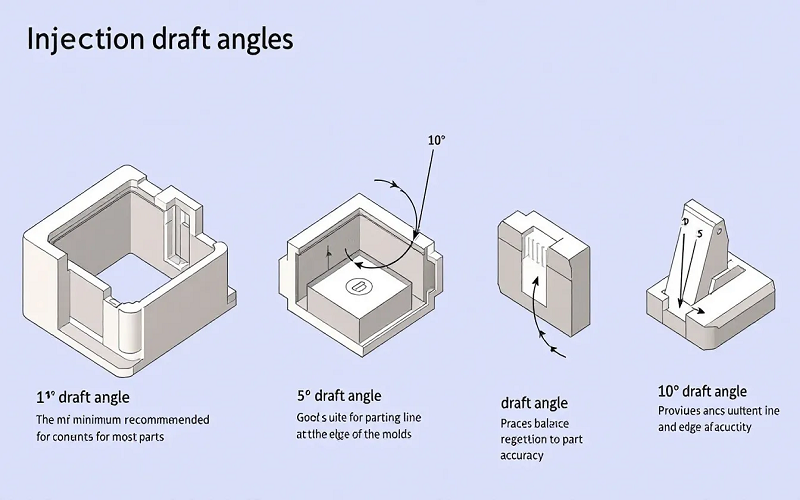
Draft angle injection molding is a geometric feature indicating the taper of the mold’s walls along the drawing direction. Its primary purpose is to facilitate the removal of the molded part from the mold using the core cavity approach.
Without a draft angle, the frictional resistance during part ejection can complicate removal and potentially damage the part. Additionally, the concept of draft angle in plastic injection molding is crucial for ensuring efficient production.
Draft angles create a slight taper on vertical surfaces, which minimizes friction, reduces ejection force, and speeds up the ejection process. Draft angles allow air to fill the cavities, preventing vacuum formation that can cause warping during part ejection.
A general rule guideline suggests using 1 degree of draft for every inch of cavity depth to aid in part ejection.
Importance of Draft Angles for Injection Molded Parts
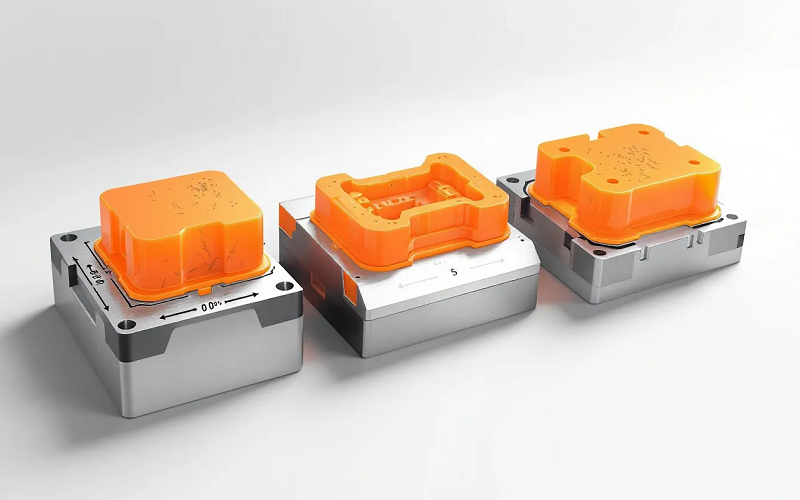
Draft angles are essential for enhancing the moldability of parts, affecting both cosmetic finish and structural integrity, particularly when considering a single draft angle.
Incorporating draft angles in injection molding designs offers several benefits:
- Prevents part warping
- Minimizes production costs
- Extends the lifespan of injection molds
- Reduces maintenance and replacement costs over time.
Properly designed larger draft angle facilitate part removal, meet quality standards, and improve overall production efficiency. Draft angles ensure parts are easily ejected without damage, directly improving production efficiency and reducing the likelihood of defects.
Reducing Friction and Easing Part Ejection
Draft angles help reduce the contact area between the molded part and mold walls, minimizing friction during ejection. Without a draft angle, such as a zero degree draft angle, the plastic part may stick to both the cavity or deform, complicating the ejection process and potentially damaging the part.
Minimizing frictional force is crucial for successful part ejection in injection molding. Draft angles are necessary for conventional ejection of large bore diameters, highlighting their role in preventing sticking and ensuring smooth ejection. Ejector pins are also important in this ejection method.
Enhancing Surface Finish and Reducing Defects
Effective draft angle design, combined with optimized wall thickness, can significantly enhance the surface finish of molded plastic parts. Draft angles prevent parts from rubbing against the mold, preserving surface quality and preventing scratches during the ejection process, especially when molds are crafted using cnc machining for precision.
Effective draft angles prevent surface scratches by enabling smooth part ejection from the mold. This results in a high-quality surface finish and a mirror finish, crucial for maintaining the cosmetic and functional integrity of the molded parts.
Designing Effective Draft Angles
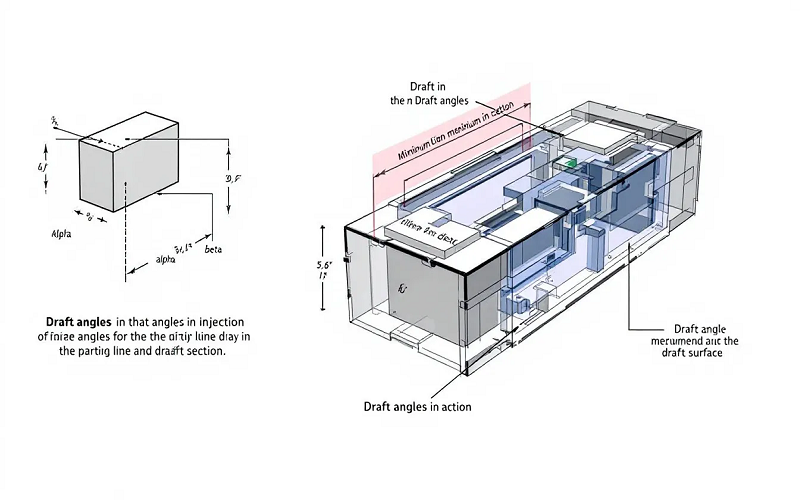
Designing draft angles presents challenges as designers often prefer straight, perpendicular models. Typically, the draft angle is designed by a structural engineer or a mold engineer, who must consider the specific situation and optimize draft angles effectively.
Designing draft angles is sensitive and requires fine-tuning by mold designers for optimal results. Higher shrink rates in plastics necessitate larger draft angles to facilitate proper ejection, and cooling of thermoplastic resin causes shrinking, leading to surface tension that may impede smooth ejection. Additionally, understanding how molten resin flows can further enhance the design process.
Calculating the Correct Degree of Draft
Draft angles are determined by the depth of features and the minimum thickness required for proper ejection. As a guideline, up to 2 degrees of additional draft can be added per inch of mold cavity depth, with a general recommendation of 1 degree for standard mold depths.
Most injection molded materials require a minimum draft angle of 0.5 degrees, particularly for vertical faces.
For surface roughness, increase the draft angle by 0.4 degrees for each 0.1 mm of roughness. Textured molds usually need an additional 1.5° for every 0.001 inches of texture depth.
Adapting Draft Angles for Different Part Features
All vertical components, including ribs and bosses, should be designed with appropriate draft angles. Factors determining the amount of draft to apply include material, part features, surface finish, mold design, and the deep rib approach.
Higher draft angles are needed for rougher textures to prevent scraping. For heavily textured surfaces like a leather or snakeskin finish, a draft angle of 10° or more may be necessary. For screw bosses, a draft angle between 0.5° and 1.0° is recommended.
Material Considerations for Draft Angles
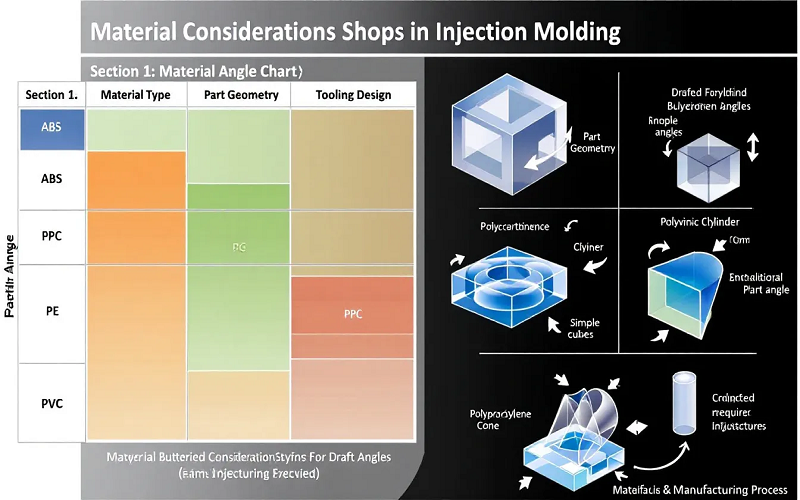
Understanding how different materials behave under cooling is critical to appropriately designing draft angles. Materials with high thermal shrinkage often necessitate greater draft angles to accommodate their properties.
Adequate draft angles minimize cooling time, enhancing efficiency and reducing costs. This understanding is essential for optimizing the injection molding process and ensuring high-quality parts.
Best Practices for Common Materials
For ABS, a draft angle of at least 1 to 2 degrees is commonly advised to facilitate ejection. Polypropylene typically requires a draft angle of approximately 1 to 3 degrees depending on the part’s complexity.
Choosing the appropriate injection molding draft angle is crucial for optimal ejection and part quality in injection molding. Different nylon formulations may require varying draft angles due to their specific properties.
Impact of Draft Angles on Injection Mold Design
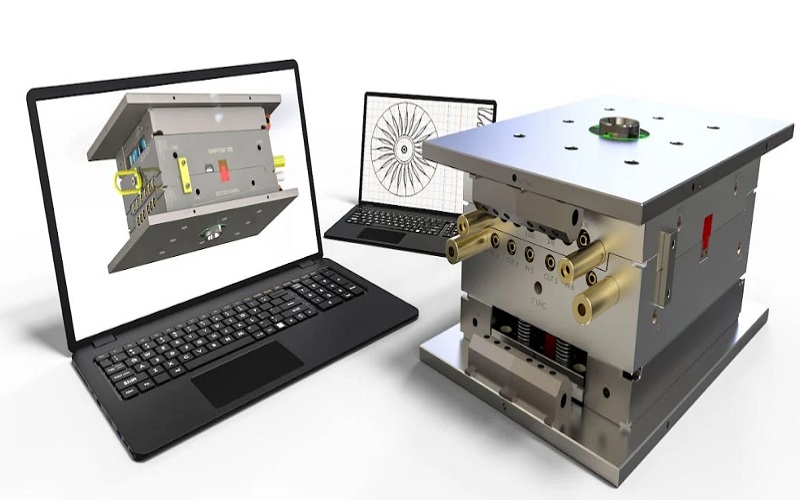
Draft angles significantly influence parting lines in mold designs by determining contact points between the mold’s cavity and core, particularly on the outer surface of the part. Aligning features such as diameters with the parting line can ensure consistent part separation, which reduces deep draw challenges and is essential for effective mold operation.
Incorporating proper draft angles, tailored to the material characteristics of the plastic, can lead to increased tool life by reducing wear and tear on the mold during the ejection process. Effective use of draft angles enhances mold cavity design, contributing to better ejection and improved part quality in the mold involves intricate geometries, while maintaining tight dimensional tolerances.
Aligning Draft Direction with Mold Separation
Aligning the draft direction with the parting line prevents damage during the ejection process. Draft angles affect how smoothly parts release from the mold, reducing the risk of sticking, especially for features that are not perfectly straight.
Molded parts should have draft angles directed toward both the core and cavity sides to minimize the risk of damage. This alignment, often complemented by a light texture on the surface, ensures a smooth ejection process and extends the lifespan of the closed mold as the mold opens, facilitating mold release actions.
Managing Deep Draw Issues
Adequate draft angles are vital in deep draw applications to prevent parts from adhering to the mold. Effective draft angles accommodate variations in mold and part geometries, ensuring efficient production.
Draft angles reduce contact between the molded part and the mold walls, eliminating friction during ejection. Metal sleeves made of low-friction materials can enhance the effectiveness of draft angles in mold design.
Injection Molding Standards and Guidelines
Industry standards for surface finishes in injection molding are defined by organizations such as the Society of the Plastics Industry (SPI) and the Society of German Engineers (VDI). The mandatory draft angle for heavy textures in injection molding is 5 degree measurement or more. Typically, 3 degrees of draft are required for metal-on-metal molding functions.
Draft angles minimize wear on mold components, extending their lifespan.
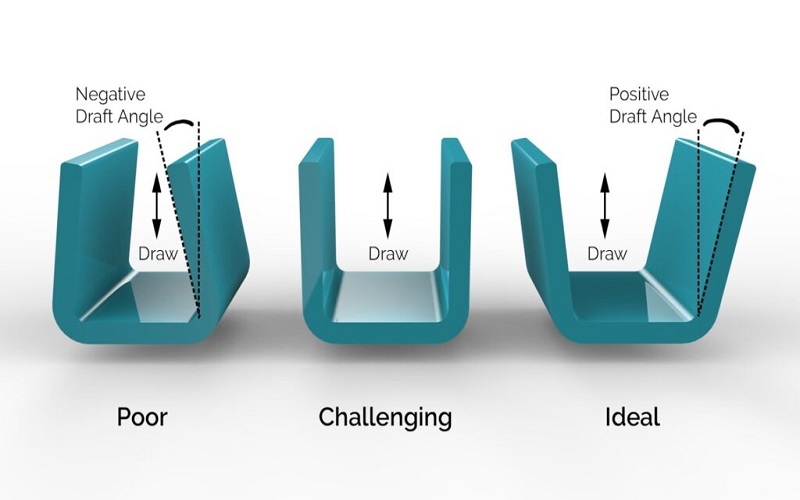
Tips for Optimizing Draft Angles
Proper draft angles minimize defects, enhance part quality, and contribute to lower manufacturing costs. Adding draft angles during the initial design phase prevents moldability issues later.
Draft angles enhance mold efficiency by facilitating easier part ejection and reducing power requirements, especially when utilizing more generous draft angles. Collaboration between designers and engineers is key for optimizing draft angles.
Early Integration in the Design Process
Designing for draft can help avoid costly redesigns and ensure smoother production processes. Integrating draft into your design early is crucial as it helps reduce costs and incorporate draft add draft more draft better than no draft zero draft shorten lead time.
Incorporating draft angles early in the design phase can prevent costly changes later. Early incorporation of draft angles reduces production costs and expedites manufacturing.
Collaboration Between Designers and Engineers
Communication and cooperation between structural engineers and design engineers are essential for effective draft angle design. Collaboration ensures both aesthetic and functional needs for draft angles are met, particularly when aligning features along the vertical axis of the mold.
Different companies, including injection molders, may prioritize structural integrity or visual appeal differently when applying draft angles. This collaboration helps balance these priorities, leading to a more successful injection molding project.
Case Studies: Successful Draft Angle Applications
Parts with complex textures generally require steeper draft angles to ensure proper ejection from the mold. Draft angles play a vital role in the successful ejection of parts during the injection molding process.
Adequate draft angles significantly reduce the risk of damage during ejection, improving part quality. In contrast, inadequate draft angles can lead to complications. Best practices in draft angle design include considering part texture and complexity early in the design phase, along with generous draft angles.
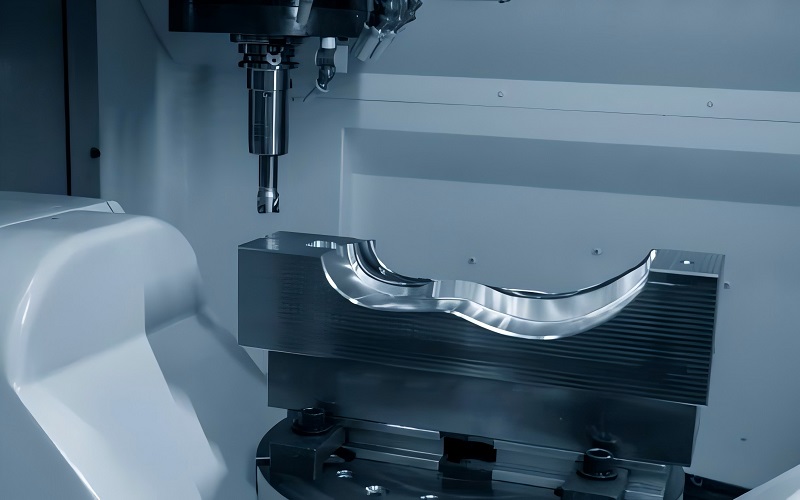
Summary
Mastering draft angles is crucial for the success of injection molding projects. By understanding their importance, designing them effectively, and considering material properties, you can enhance part quality, reduce costs, and extend mold lifespan.
Remember, the key to perfection lies in the details. Embrace these practices, and watch your injection molding projects soar to new heights.
Frequently Asked Questions
What is the typical draft angle for casting?
The typical draft angle for casting is generally between 1.5 to 2 degrees, facilitating easier ejection of parts. For textured surfaces, a draft angle of 2.5 to 3 degrees is recommended, while vertical surfaces should have at least 0.5 degrees.
What is the draft angle in drawing?
The draft angle in drawing refers to the taper or degree of inclination of the mold’s walls in the direction of drawing, typically measured in degrees. Engineers generally use a draft angle of approximately 1.5 degrees for optimal mold design.
What is a good draft angle?
A good draft angle is generally at least 1 degree per inch of cavity depth, with 0.5 degrees recommended for all vertical faces to facilitate easier removal from molds. Adhering to these guidelines can enhance the manufacturability of the part.
Why are draft angles important in injection molding?
Draft angles are critical in injection molding as they enable smooth part ejection, minimize friction, prevent warping, and enhance surface quality. Their proper implementation is vital for achieving optimal production efficiency and product integrity.
How do you determine the correct degree of draft?
To determine the correct degree of draft, consider the depth of features, material properties, and surface texture, following the guideline of approximately 1 degree of draft for each inch of cavity depth. This ensures effective mold release and optimal finishing.