Undercuts in injection molding are design features that complicate the mold but allow for complex parts. Understanding how to work with undercuts injection molding is crucial for effective molding.
This article dives into what undercuts are, their importance, and techniques for incorporating them.
Importance of Undercuts in Injection Molding
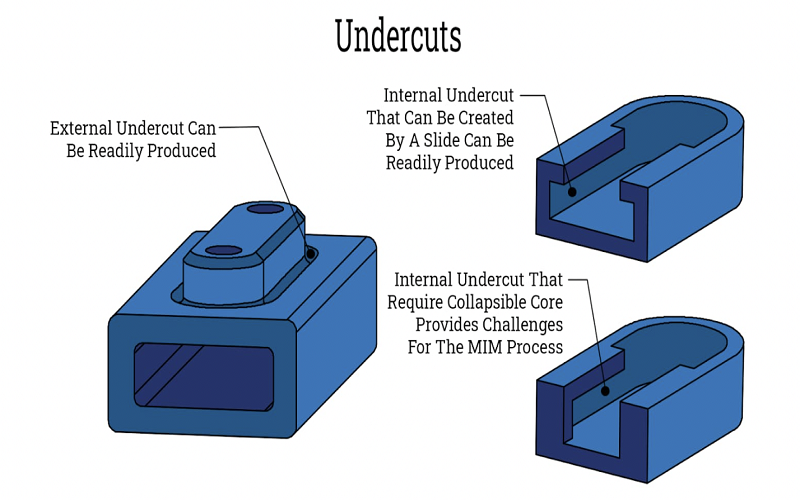
Undercut injection molding generally increases the ability to craft intricate designs across multiple industries. The ability to incorporate complex shapes and features, such as external undercuts and interior undercuts, that would otherwise be impossible with standard molding techniques sets injection molding undercuts apart. This capability allows for better integration of components, leading to improvements in overall design and functionality.
One of the primary benefits of using undercuts is their ability to enhance the functionality of molded parts. In the automotive sector, undercut molding is utilized for components that require precise fit and functionality, such as clips and fasteners, often incorporating custom inserts for added strength and precision.
Additionally, undercuts support assembly processes by enabling the creation of interlocking features, which can improve fluid flow and overall product performance.
However, the complexity introduced by undercuts also generally increases manufacturing costs and lead times. Effective design agility requires careful consideration of these complexities to ensure that the designs are practical and reliable.
Despite these challenges, the benefits of undercuts in creating high-quality, functional parts make them an invaluable tool in the injection molding arsenal.
Techniques to Implement Undercuts in Injection Molded Parts
Creating undercuts in injection molded parts can be achieved through several techniques, each suited to different part designs, geometries, and production volumes. The main methods include:
- Adjusting parting lines
- Utilizing side actions
- Employing bump offs
- Using hand-loaded inserts
Each technique offers unique advantages and challenges, making it an essential process to choose the right approach based on specific project requirements.
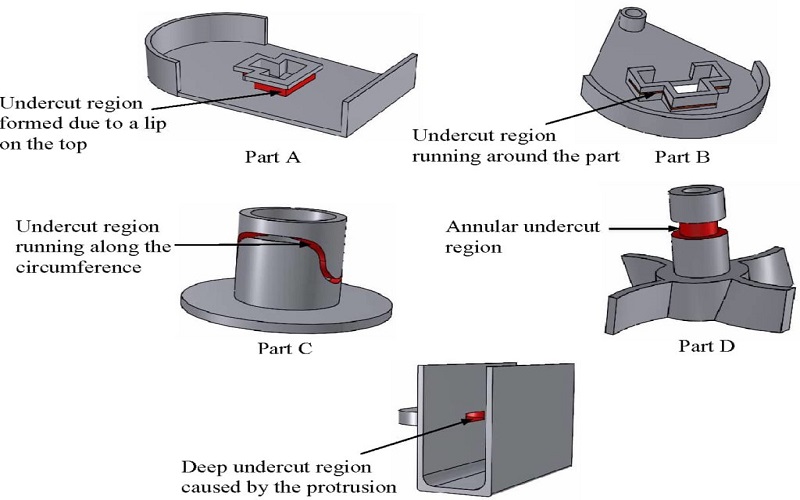
Adjusting Parting Lines
Parting lines, which divide the mold into one half and two halves, are vital for creating undercuts and features like side holes. Adjusting these lines can overlap an undercut feature, simplifying the ejection process without additional mechanisms.
This method can be particularly effective for parts with complex shapes, such as lens covers, as it allows for a more straightforward mold design, mold’s parting line, and part ejection, while maintaining consistent wall thickness.
Zigzagging the parting lines or using lifters that operate perpendicularly to the mold’s parting line can facilitate the ejection of parts with undercuts. Such adjustments manage material flow and part geometry, ensuring the molded parts retain their integrity and functionality. The ejector plate plays a critical role in this process by providing the necessary force to release the part from the mold.
Utilizing Side Actions
Side actions involve incorporating additional components into the mold that move laterally to release undercuts and features like side holes. These side action cores engage from the side of the mold, preventing undercuts during the injection molding process and allowing for easier parting.
The most common type of side action cam is the cam pin slide, which ensures the side action core operates effectively and smoothly, maintaining uniform wall thickness in complex parts like lens covers.
Implementing side actions adds complexity and associated costs to the mold design, but it significantly improves design compatibility and minimizes waste. This technique is particularly beneficial for rigid materials like nylon, acetal, and polycarbonate, which do not adhere easily to the mold and can be challenging to eject, especially when supported by a well-designed ejector plate.
Employing Bump Offs
Bump offs allow parts to deform slightly during mold exit without causing damage, making them ideal for flexible and elastic materials like polyethylene and thermoplastic elastomer (TPE). This technique involves using a machined insert bolted into the mold, which creates ‘wiggle room’ that facilitates easier part removal to bump off the parts.
A lead angle between 30° to 45° and a smooth radius on the leading edge of undercuts are crucial for effective part removal in bump offs. However, if the part is not elastic enough, it may break during the removal process, highlighting the importance of material selection and design considerations.
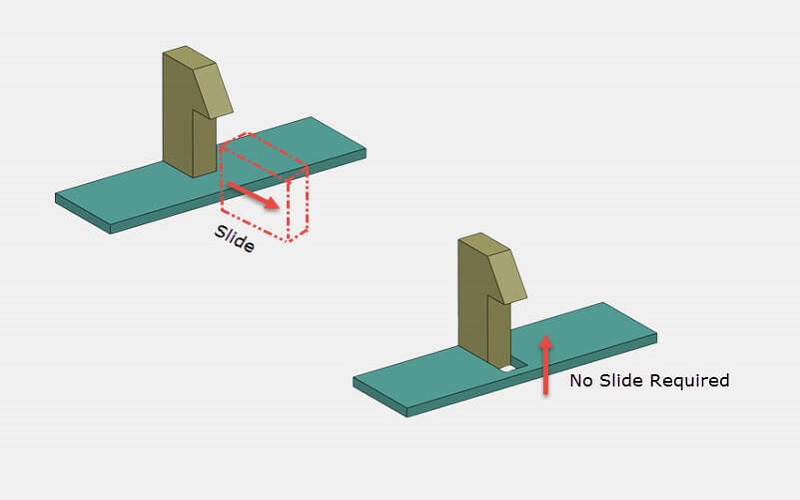
Using Hand Loaded Inserts
Hand-loaded inserts manually create internal undercuts in injection molding, suitable for low production volumes and delicate parts. The design must allow space for removal without obstruction and ensure a tight shut-off for effective molding, especially when using a single insert.
Common products that use hand-loaded inserts include:
- Nozzles
- Toys
- Bearers
- Grips
While labor-intensive, this method provides the precision needed for parts with complex geometries and delicate features.
Overcoming Challenges in Undercut Injection Molding
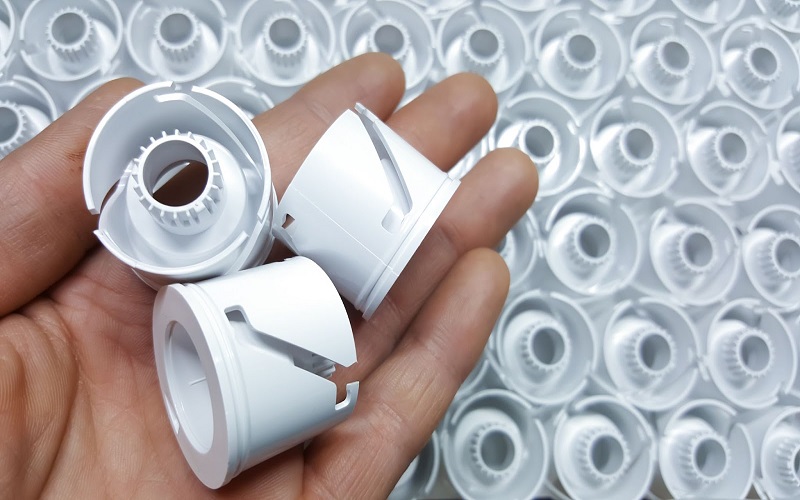
Undercut injection molding presents challenges like design complexity, material rigidity, and aesthetic requirements. Undercuts occur when features, such as latch features, prevent straightforward part ejection, requiring a well-planned approach and expert guidance to ensure practical and cost-effective designs involving plastic injection, plastic injection molding, and injection mold, often utilizing tools like a milling machine for precise mold fabrication along the draw line.
Managing Lack of Draft
Controlling draft angles optimizes undercut performance in injection molding. Maximizing draft angles aids in the smooth and efficient extraction of tougher materials, such as low density polyethylene, from molds, particularly when using mechanisms like an angled pin.
The recommended minimum draft angle for shutoff designs is three degrees, ensuring enough space for part ejection without causing damage.
Insufficient draft can lead to difficulties in removing parts from the mold, especially for harder materials with latch features. Ensuring sufficient draft or taper is necessary to avoid scraping during ejection along the draw line, maintaining the quality and integrity of the injection molded parts with as much draft as possible.
Handling Difficult Material Removal
Glass-filled plastic material and other rigid materials pose significant challenges during the molding process due to their rigidity. Addressing these challenges requires the design, often refined using a milling machine, to allow the ejector to penetrate the part’s surface without causing damage, possibly necessitating slight part deformation during extraction.
Material flexibility and elasticity are critical factors in facilitating the removal of these challenging materials, especially for materials like low density polyethylene that balance flexibility and strength.
Ensuring Aesthetic Quality
Maintaining the aesthetic quality of parts with many undercuts successfully can be challenging. To achieve desired surface finishes and part appearances, it is essential to avoid undercut complications introduced by designing undercuts and undercut features, which can lead to an undercutting problem.
Careful consideration of parting lines and mold design solutions meets aesthetic requirements without compromising functionality.
Applications of Undercut Injection Molding
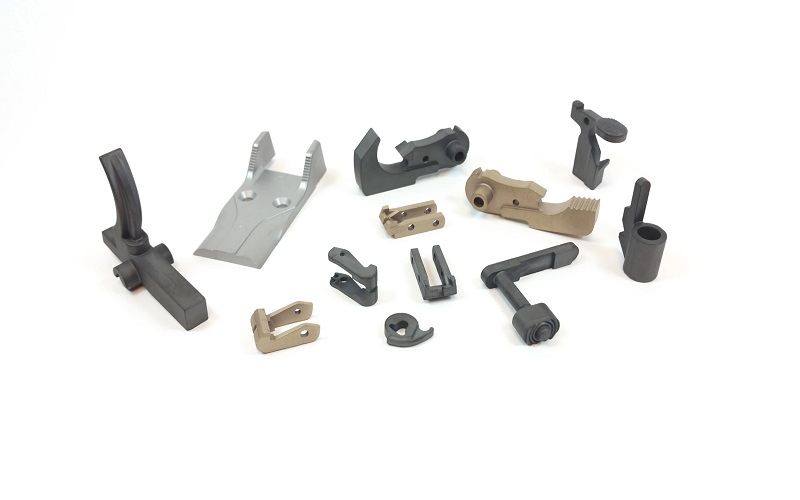
Undercut injection molding is widely used in industries such as medical devices and consumer electronics. The ability to create interlocking features, vertical threads, and barb fittings enhances assembly efficiency and product functionality.
Medical Devices
Undercuts in medical devices ensure secure connections and enhance usability. Features like grips and securing mechanisms often require undercuts to function effectively. Common applications include life-saving devices and oxygen delivery units, which rely on complex geometries for optimal performance.
Integrating undercuts in medical devices can challenge maintaining aesthetic quality, particularly with visible parting lines affecting the device’s final appearance. Design considerations like including a lip in barb fittings ensure proper function and alignment during molding.
Consumer Electronics
In consumer electronics, undercuts are used to accommodate ports, connectors, and other components, enhancing both functionality and design aesthetics. Smartphones, for example, employ undercuts to embed sensors and buttons within their sleek designs, making them more user-friendly and visually appealing.
Leveraging Expert Support for Undercut Injection Molding
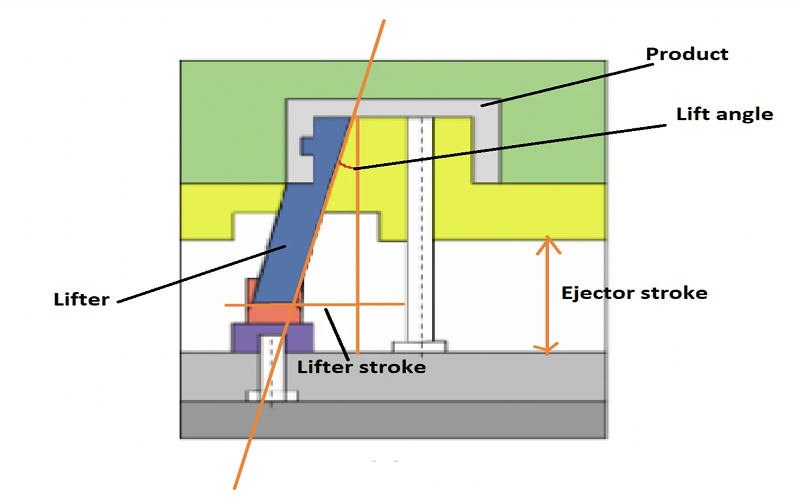
Design complexity increases the chances of complications during the injection molding process. Consulting with experts can help optimize designs, reduce costs, and shorten project timelines. Companies like Fictiv, Protolabs, RapidDirect, and WayKen offer invaluable support, providing design for manufacturability (DFM) feedback and utilizing state-of-the-art equipment to ensure successful undercut injection molding.
Engaging with these experts typically involves uploading design files and configuring material requirements through their platforms, providing customized and precise solutions to undercut challenges.
Summary
Undercut injection molding is a powerful technique for creating intricate and functional designs across various industries. By understanding the importance of undercuts, implementing effective techniques, and addressing common challenges, manufacturers can enhance their product offerings and achieve superior results.
Leveraging expert support further ensures the success of undercut designs, making the process more efficient and cost-effective. Embrace the potential of undercuts in your next injection molding project to unlock new possibilities in design and functionality.
Frequently Asked Questions
What are undercuts in injection molding?
Undercuts in injection molding are features that obstruct the ejection of parts from the mold without specialized techniques. These may necessitate the use of side actions or inserts for successful molding.
Why are undercuts important in injection molding?
Undercuts are crucial in injection molding as they enable the production of complex shapes and interlocking features, thereby enhancing the functionality and design of molded parts across various industries. Their importance cannot be overstated, as they contribute significantly to the versatility and performance of the final products.
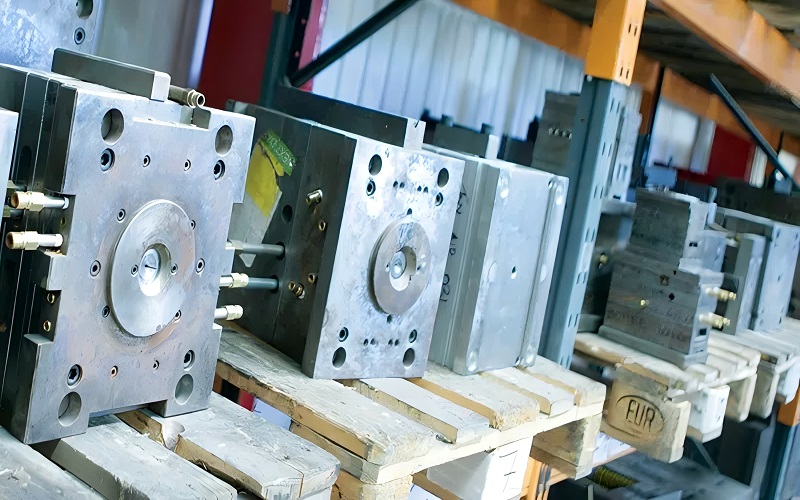
What challenges do undercuts present in injection molding?
Undercuts in injection molding present challenges such as increased design complexity, material rigidity, and potential impacts on aesthetic quality. Effectively managing these issues is crucial to controlling manufacturing costs and lead times.
How can I overcome the challenges of undercut injection molding?
To overcome the challenges of undercut injection molding, optimize draft angles, choose appropriate materials, and consult with experts for efficient mold designs and effective part ejection. These strategies will enhance your molding process and improve outcomes.
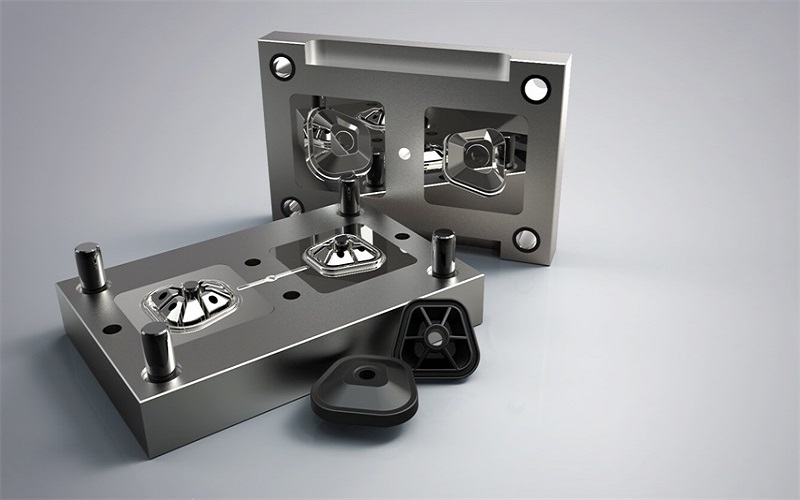
What industries commonly use undercut injection molding?
Undercut injection molding is predominantly utilized in the medical devices and consumer electronics industries, where detailed and functional designs are essential.