Molding over molding combines two materials into one product, enhancing performance and durability while cutting down assembly steps. Discover how this works, where it’s used, and what to keep in mind for a successful process.
Understanding Molding Over Molding
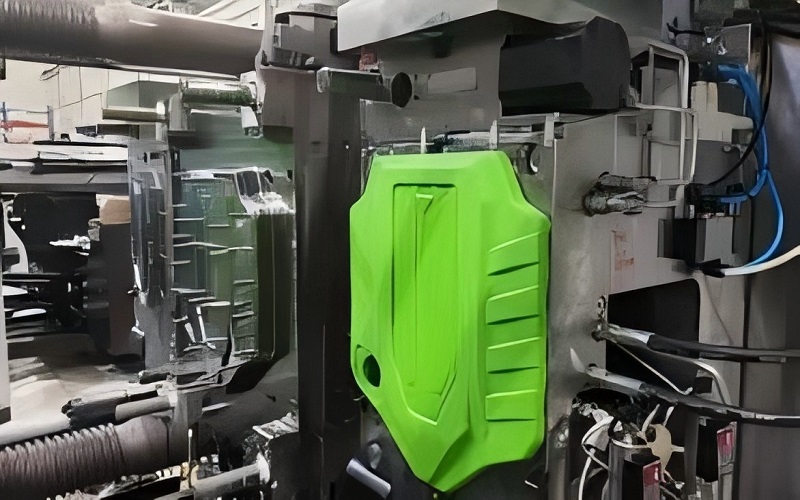
Molding over molding is a sophisticated manufacturing process that involves combining two separate materials to create a single, cohesive product.
This process is particularly advantageous when different materials are needed to achieve specific properties or functionalities, such as combining a rigid plastic substrate with a flexible overmold. The primary goal is to produce a product with enhanced performance, aesthetic appeal, and durability, often incorporating metal components for added strength.
Unlike conventional injection molding, which typically uses a single material, molding over molding allows for the integration of multiple materials in a single manufacturing cycle. This technique is often used in conjunction with insert molding, where threaded inserts or other insert components are placed into the injection mold cavity before the secondary injection molded material is injected, utilizing multi-material molding with an injection molding machine.
The result is a robust, multi-material product that eliminates post-molding assembly, thereby reducing costs and improving efficiency.
The Process of Molding Over Molding
The process of molding over molding is a multi-step operation that combines two components into a single solid piece. This intricate process involves creating a substrate part, applying a secondary material, and then cooling and ejecting the final product. Each step is crucial to ensuring the quality and performance of the molded part.
Let’s delve into each stage to understand how this versatile process unfolds.
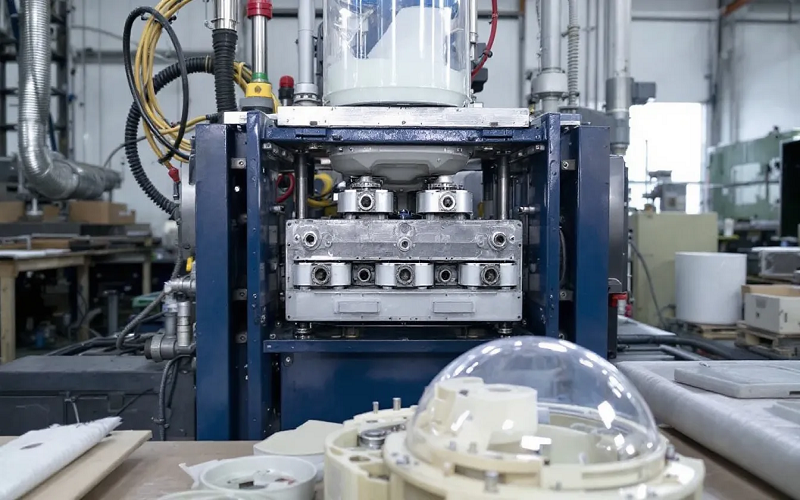
Step 1: Create the Substrate Part
The first step in the molding over molding process is to create the substrate part, which serves as the foundational layer for additional materials. This initial phase typically involves the injection of one type of plastic into a mold, forming the base component that will later receive the secondary material. The substrate part is primarily made of plastic and is designed to provide the necessary structure and support for the insert molding overmolding process, often resulting in precise injection molded parts.
In this stage, the selected plastic is melted and injected into a mold cavity under high pressure. Once the molten plastic cools and solidifies, the mold opens, and the substrate part is ejected. This base component must be precisely formed to ensure proper alignment and bonding with the secondary material in the subsequent steps.
Step 2: Apply Secondary Material
The next step involves applying the secondary material over the substrate part. This is typically done using injection molding or compression molding techniques.
During the injection molding process, the thermoplastic resin involves melting at high temperatures, ranging from 300° to 650° Fahrenheit, and is injected into the mold under high pressure. This high-pressure injection ensures that the secondary material bonds effectively to the substrate, creating a strong and durable final product, often incorporating features like soft seals for enhanced functionality.
The secondary material is often chosen for its specific properties, such as flexibility or durability. Thermoplastic elastomers (TPE) are commonly used due to their rubber-like plastic characteristics, which provide enhanced grip and comfort.
Proper venting during the injection process is essential to push out air and achieve complete mold filling, ensuring a firm bond between the materials.
Step 3: Cooling and Ejection
Once the secondary material has been applied, the molded part must cool before it can be ejected from the mold. Cooling is a vital step that solidifies the molded part, ensuring its structural integrity and preventing deformation. The cooling time varies depending on the materials used and the complexity of the mold.
After cooling, the mold opens, and the part can be removed either manually or via automated ejection systems. Automated ejection systems enhance efficiency by quickly removing the molded parts once they have cooled. Careful detachment from the sprues is essential to avoid damaging the molded part and ensure a high-quality finish.
Materials Used in Molding Over Molding
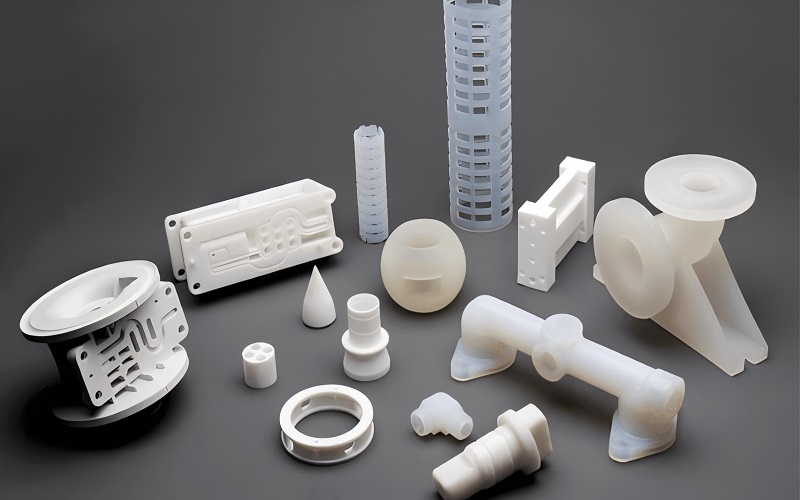
The choice of materials in molding over molding is crucial to achieving the desired properties and performance of the final product.
Common materials for the substrate part include various thermoplastics such as ABS, Nylon, Polycarbonate, and elastomers like silicone. These materials provide the necessary strength, durability, and flexibility required for different applications.
Thermoplastic elastomers (TPE) are frequently chosen as the secondary material for their rubber-like properties, offering flexibility and durability. High-density polyethylene (HDPE) is another popular choice due to its favorable mechanical properties. The selection of materials is driven by the specific requirements of the final product, ensuring compatibility and effective bonding between the substrate and the overmold.
Design Considerations for Molding Over Molding
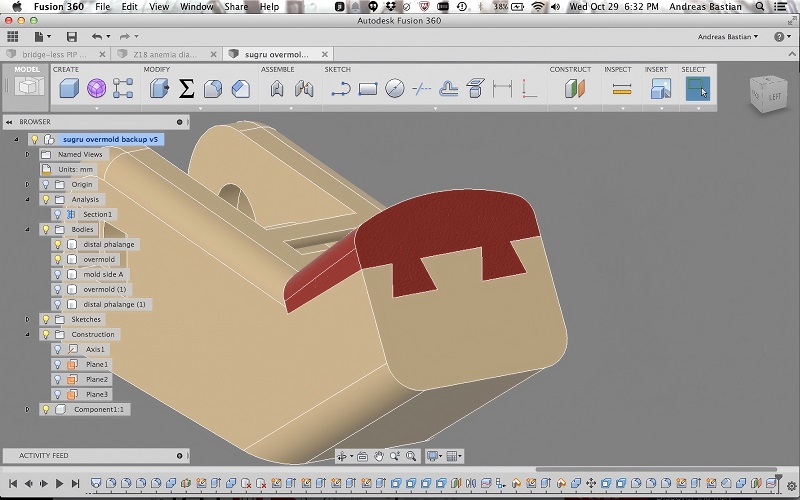
Designing for molding over molding requires careful consideration of various factors to ensure the quality and functionality of the final product. Key considerations include material compatibility, mold design, and cost implications. Each of these elements plays a critical role in the success of the molding process and the performance of the molded part, following molding design guidelines.
Material Compatibility
Ensuring material compatibility is paramount in overmolding. The materials used must bond effectively to achieve a durable and high-performing product. Incompatibility between materials can result in poor adhesion, leading to product failure and excess material.
Manufacturers often enhance adhesion by incorporating mechanical bonding techniques, such as adding holes or grooves at the edges of the overmolded area. Chemical bonding is another method used to achieve strong adhesion between different materials.
The selection of compatible materials and bonding techniques ensures that the final product meets the desired performance standards and longevity requirements.
Mold Design
Choosing the appropriate mold design is crucial for ensuring product quality and structural integrity. Short shots, where the injection is insufficient, can result in aesthetic flaws, necessitating thoughtful gate location design to avoid such defects in plastic components.
Flash can occur due to excessive gaps in the mold cavity or improper gate design, requiring careful adjustments to injection pressure and mold fit. A precise fit between the substrate and the injection molds is essential, with an ideal gap of 0.01 to 0.03 mm to prevent issues like flash or surface indentations, especially around sharp corners. Additionally, utilizing a complex two-shot mold, supported by an efficient injection unit, can further enhance the efficiency of the manufacturing process.
Proper mold design also involves considering the cooling phase to reduce shrinking effects and prevent backflow. Maintaining appropriate holding pressure during cooling ensures uniform solidification and high-quality molded parts.
Cost Implications
Overmolding is generally more expensive due to the variety of materials and the complexity of the process. The overall expense increases because multiple molds are required, particularly in compression molding processes.
However, the benefits of reduced assembly costs and improved product performance often justify the higher initial investment.
Managing costs in overmolding involves optimizing material usage and production efficiency. By carefully selecting materials and refining the manufacturing process, manufacturers can achieve cost-effective production while maintaining high-quality standards and considering the cost element.
Advantages of Molding Over Molding
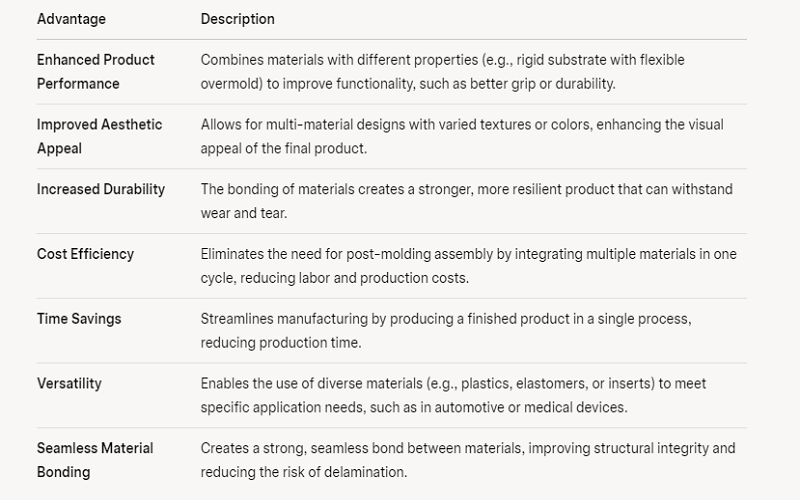
Molding over molding offers several significant advantages, making it a preferred choice in various industries. These advantages include enhanced product strength, increased design flexibility, and reduced assembly costs.
Each of these benefits contributes to the overall effectiveness and efficiency of the manufacturing process.
Enhanced Product Strength
One of the primary benefits of molding over molding is the enhanced strength of the final product. Combining materials enables manufacturers to produce parts with enhanced strength and durability. Integrating metal inserts within plastic further improves the overall strength, providing added support and structural integrity. Metal inserts strengthen the product’s performance.
This combination of materials enhances resistance to wear and corrosion, ensuring a longer lifespan for the product.
Increased Design Flexibility
Molding over molding offers unparalleled design flexibility, allowing for the creation of intricate and multifunctional parts. The ability to seamlessly transition from molded plastic to typically metal parts enables innovative design solutions that would be challenging to achieve with traditional manufacturing methods.
This process enhances the aesthetic appeal and functionality of the final product, making it more versatile and efficient.
Reduced Assembly Costs
By integrating multiple components into a single molded part, molding over molding eliminates the need for post-molding assembly. This reduction in labor and assembly processes leads to significant cost savings and addresses the need for cost sensitive parts.
Additionally, the streamlined manufacturing process minimizes material waste and complexity, resulting in more efficient production and lower overall costs.
Applications of Molding Over Molding
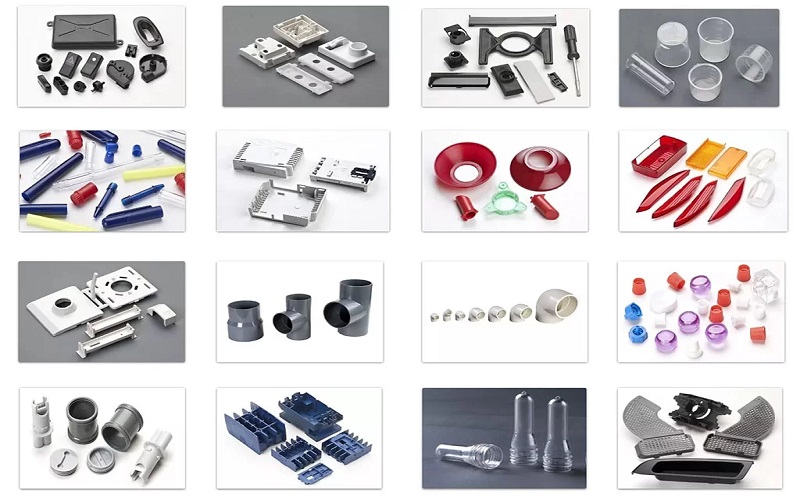
Molding over molding is utilized in a wide range of industries, including automotive, consumer electronics, and medical devices. This versatile process allows for the creation of products with enhanced functionality, durability, and aesthetic appeal.
Automotive Industry
In the automotive industry, molding over molding is essential for producing lightweight and durable components. The use of overmolding contributes to fuel economy by reducing the weight of parts, while also lowering assembly costs.
Plastic insert molding parts are more durable and lighter weight compared to their plastic parts counterparts, enhancing automotive manufacturing efficiency.
Consumer Electronics
Overmolding in the consumer electronic industry enhances product durability and provides aesthetic appeal, making devices more visually attractive. The process helps avoid the use of fasteners and solders, streamlining production in electronic devices.
In consumer electronics, typical examples of insert molding parts include digital control panels and knobs for appliances. Additionally, rubber-covered electrical wires are also produced using this method.
Medical Devices
Insert molding is used to create various types of medical devices, including molding inserts such as dental instruments, tubes, components for medical equipment, prosthetics, enclosures, knobs, surgical instruments, and an insert molded part for metal insert molding. For further insights, refer to the insert molding design guide.
Overmolding in medical equipment components allows for the creation of components that are resistant to contaminants and facilitate easier sterilization.
Molding Over Molding vs. Insert Molding
Molding over molding is a more complex and costly process compared to the insert molding process, which is typically a single-shot process. Integrating metal inserts into plastic through insert molding boosts the overall strength and durability of the final product.
Insert molding leads to a streamlined and cost-effective manufacturing approach by eliminating the need for separate assembly processes, especially when considering overmolding vs insert molding and overmolding and insert molding.
While both processes have their advantages, the choice between molding over molding and insert molding vs insert molding depends on the specific requirements of the product and the desired properties of the final component. Products like surgical instruments and implantable devices benefit from insert molding due to the ability to produce complex geometries in a single operation.
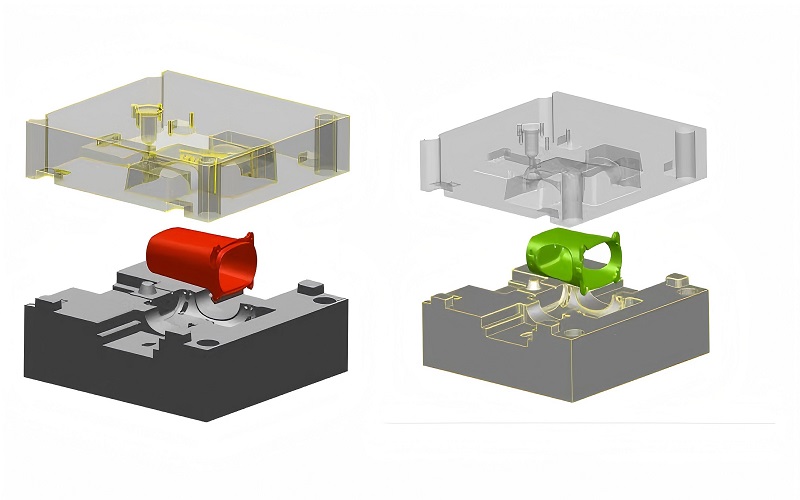
Challenges and Solutions in Molding Over Molding
Despite its advantages, molding over molding presents several challenges. These include ensuring material compatibility, achieving precise mold design, and managing higher production costs. Overmolding is utilized in various sectors, including aerospace, medical, and industrial applications, to enhance product functionality.
Solutions to these challenges involve careful material selection, optimizing mold design, and refining the manufacturing process to improve efficiency and reduce costs. Incorporating mechanical and chemical bonding techniques can enhance material adhesion, while advanced mold design can prevent defects like flash and short shots.
Choosing Between Molding Over Molding and Other Techniques
Choosing the right manufacturing technique depends on various factors, including production volume, material requirements, and cost considerations. Overmolding with injection molding is typically used for higher production quantities, offering efficiency and consistency.
Comparing molding over molding with other techniques like CNC machining and 3D printing can help determine the best approach for specific applications. Consulting with industry experts at an early stage can provide valuable insights and help identify the optimal molding process for a given product.
Understanding the product’s application and desired properties is crucial in making an informed decision about the most suitable manufacturing technique.
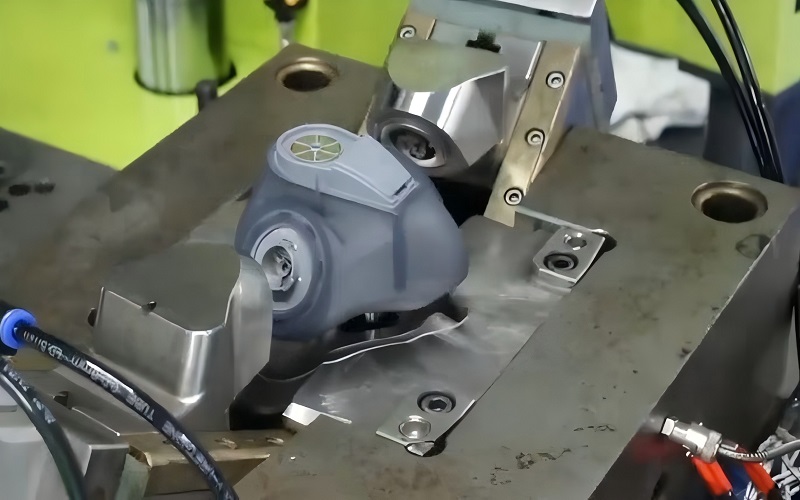
Summary
In summary, molding over molding is a versatile and innovative manufacturing process that combines multiple materials to create robust, multifunctional products.
By understanding the intricacies of each step, from creating the substrate part to applying the secondary material and ensuring proper cooling and ejection, manufacturers can achieve high-quality results that meet specific performance requirements. The careful selection of materials and adherence to design considerations are crucial to the success of this process, enhancing product strength, design flexibility, and cost efficiency.
As we have explored, molding over molding finds applications across various industries, including automotive, consumer electronics, and medical devices, offering numerous advantages over conventional methods.
By overcoming challenges and leveraging the unique benefits of this technique, manufacturers can produce innovative, high-performance products that set new standards in their respective fields. The future of molding over molding looks promising, with continued advancements and applications driving the evolution of product design and manufacturing.
Frequently Asked Questions
What is the main difference between molding over molding and insert molding?
The main difference between molding over molding and insert molding is that molding over molding is a two-shot process that combines multiple materials, whereas insert molding uses a single-shot process to integrate a metal insert for added strength and durability.
What are the common materials used in molding over molding?
Common materials used in over molding include thermoplastics such as ABS, Nylon, and Polycarbonate, as well as elastomers like silicone and thermoplastic elastomers (TPE) for their flexibility and durability. These materials ensure strong bonding and effective functionality in the final product.
How does molding over molding benefit the automotive industry?
Molding over molding enhances the automotive industry by creating lightweight and durable components, which ultimately improve fuel economy and lower assembly costs. This innovation contributes to more efficient and cost-effective vehicle production.
What are the key design considerations for molding over molding?
Key design considerations for over molding include ensuring material compatibility, optimizing mold design for effective bonding, and analyzing cost implications. These factors are essential for achieving high-quality results in the molding process.
What challenges are associated with molding over molding, and how can they be addressed?
Molding over molding presents challenges such as material compatibility and precise mold design, along with increased production costs. These can be addressed through careful material selection, optimizing mold design, and refining manufacturing processes for better efficiency.