The manufacturing of products is the process of turning raw materials into finished goods. Understanding these processes is crucial for improving efficiency and product quality. In this article, we’ll explore key manufacturing methods, their impact on costs, and the role of advanced technologies in modern manufacturing.
Understanding Manufacturing Processes
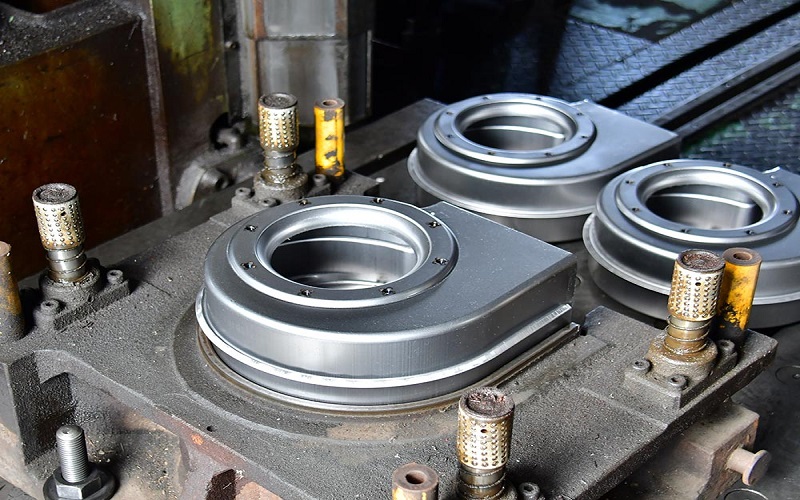
Manufacturing is the transformative process of converting raw materials into finished products to manufacture consumer goods, adding significant value along the way. The modern manufacturing sector is shaped by advances in machinery, robotics, and computer-aided design, all of which increase efficiency and precision to meet consumer demand and sell products effectively.
Quality control remains a critical component, involving inspections, testing, and monitoring to ensure that the final product meets the desired standards. Various factors, including complexity, production volume, consumer demand, and the chosen manufacturing method, influence the time required to manufacture consumer products while striving to increase efficiency.
Aligning Manufacturing with Business Strategy
To achieve operational efficiencies and maintain a competitive advantage, aligning manufacturing processes with business strategy is essential. This alignment requires considering needs from various departments, including logistics and workforce optimization, to implement effective manufacturing processes.
The selection of manufacturing methods is influenced by market demand and resource availability, ensuring that the chosen processes support the overall business objectives, including the production of large quantities. Engaging with manufacturing experts early during the product design phase can minimize costs, enhance alignment with business strategy, and reduce the risk of product recall.
Core Types of Manufacturing Processes
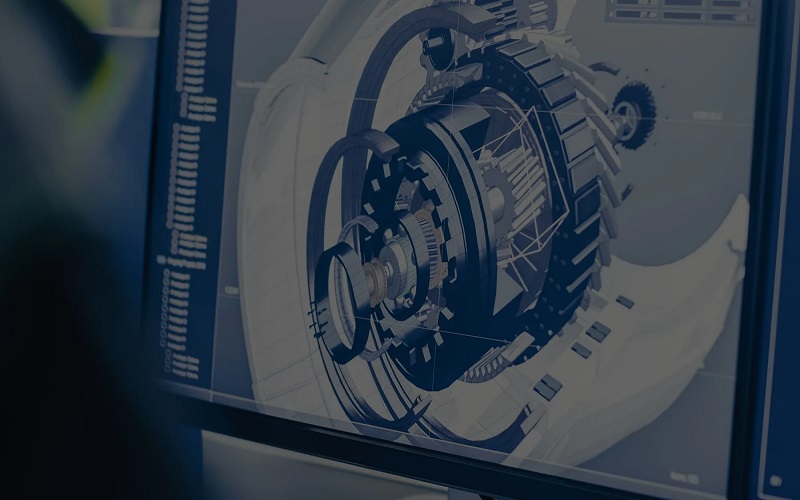
Manufacturing processes convert raw materials or components into finished goods through various methods. Selecting the right manufacturing process is crucial for efficient and cost-effective production, with factors such as product type, desired quality, production volume, material properties, and final products playing significant roles. The choice of manufacturing processes directly impacts the speed and efficiency of commercial production, including its integration with e-commerce platforms.
Four core types of manufacturing processes include discrete manufacturing, repetitive manufacturing, batch manufacturing, and continuous manufacturing, each serving different production needs and product types across different stages.
Discrete Manufacturing
Discrete manufacturing involves the production of distinct items based on a detailed Bill of Materials (BOM), which lists all components, parts, and materials required. This method is commonly used for products such as computers, household appliances, furniture, and machinery.
Discrete manufacturing allows for frequent changeovers, making it suitable for producing diverse items with distinct specifications.
Repetitive Manufacturing
Repetitive manufacturing focuses on producing standardized goods in high volumes through dedicated production lines that operate continuously. This method is well-suited for products that experience stable and predictable demand. It works particularly well for mass-produced items. The main goal is to achieve high efficiency and consistency, although it does limit the ability to customize or vary the production process.
Batch Manufacturing
Batch manufacturing involves producing goods in groups or batches, following specific instructions to ensure consistency and quality. This method provides enhanced flexibility, allowing manufacturers to create products in varying quantities while maintaining high standards of quality control.
Batch manufacturing is particularly useful for products that require frequent adjustments or for smaller production runs.
Continuous Manufacturing
Continuous manufacturing is characterized by the non-stop creation of fast moving consumer goods, often using raw materials in liquid or gas form. This method offers consistent quality and reduced production times, making it highly efficient.
While the initial investment in automation and infrastructure is significant, continuous manufacturing reduces production costs per unit due to economies of scale, though it does not readily allow for variations or customizations.
Essential Manufacturing Methods
Modern manufacturing methods blend machinery with automated systems to enhance efficiency and reduce errors. Essential methods include machining, casting, and molding, each shaping raw materials into structures using mechanical or thermal techniques.
These methods are foundational to many industries, providing the precision and versatility required to produce a wide range of consumer products and services, including examples for consumers in the industry, across broad categories.
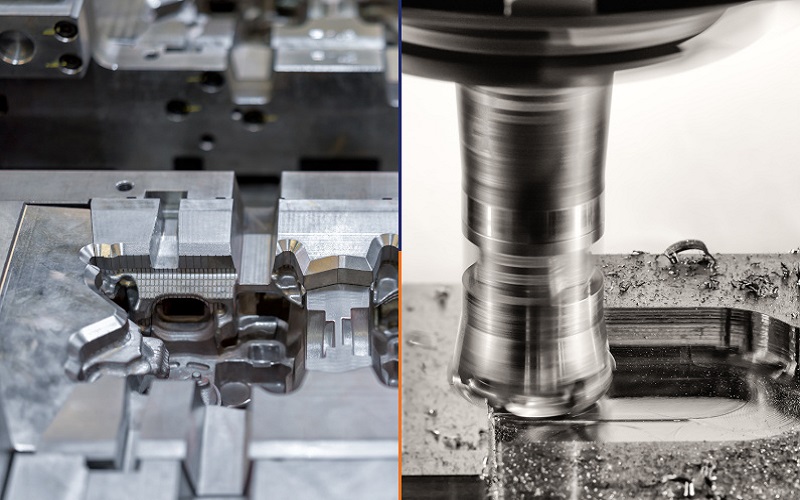
Machining
Machining involves shaping and removing material from a workpiece to create precision parts. This process is applicable to a range of materials. It includes metals, plastics, and composites, highlighting its versatility for various applications.
Machining is crucial for producing components that require high accuracy and fine details, such as those found in automotive and aerospace equipment industries.
Casting
Casting entails pouring liquid material into a mold to create solid objects, allowing for the production of components with intricate designs and complex geometries. This method is particularly effective for products that require detailed structural features, such as engine parts and artistic sculptures. For example, casting is widely used in the automotive industry to produce engine components.
Casting provides manufacturers and distributors with the ability to produce large volumes of components efficiently and economically for the manufacturer.
Molding
Molding shapes material in a semi-liquid state by pouring it into a mould, with techniques like injection and blow molding widely used to manufacture consistent and identical products. This method is prevalent in producing plastic bottles, toys, and various consumer goods, offering cost-effective solutions for mass production with high consistency and quality in beverage containers.
Advanced Manufacturing Techniques
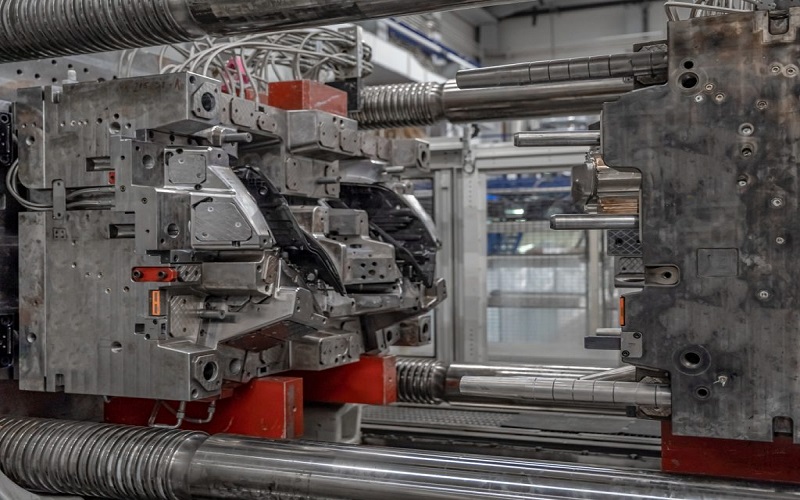
Advanced manufacturing techniques incorporate cutting-edge technologies to enhance production efficiency and product customization. Techniques such as additive manufacturing, lean manufacturing, and AI-driven processes are transforming the manufacturing landscape, allowing for greater flexibility, reduced waste, and improved quality.
Additive Manufacturing
Additive manufacturing, or 3D printing, creates objects by building them layer by layer from digital designs. This method is particularly useful for producing complex shapes, prototypes, customized jewelry, and medical implants.
One of its significant benefits is the ability to make rapid changes and improvements during the design process, as well as producing items with minimal waste.
Lean Manufacturing
Lean manufacturing focuses on minimizing waste and costs, improving lead times, and increasing customer satisfaction. Originating in Japan, this method has evolved to include innovations like autonomous robots, machine learning, and manufacturing software.
Lean manufacturing’s primary goal is to enhance operational efficiencies while maintaining high-quality standards.
Artificial Intelligence (AI) in Manufacturing
AI in manufacturing enhances production efficiency and quality by reducing downtime and enabling predictive maintenance. AI-driven robots are capable of executing repetitive tasks with great precision. This capability boosts speed and minimizes the need for human involvement.
Automated inspection systems identify defects in real-time, allowing for immediate corrective actions, while AI enables mass customization by analyzing customer data for personalized products.
Material Selection in Manufacturing
Selecting the right materials is crucial for ensuring optimal performance, longevity, and cost-effectiveness in manufacturing. Common materials include metals, plastics, composites, ceramics, and elastomers, each with unique properties that influence their selection based on strength, durability, thermal properties, and more.
Material sourcing involves researching suppliers and ensuring quality and availability, with costs influenced by production volume, manufacturing method, and product complexity.
Metals in Manufacturing
Metals such as steel and copper are essential in manufacturing due to their unique properties that enhance product performance and durability. Steel is valued for its strength, durability, and adaptability, while copper is favored for its excellent ductility, allowing it to be easily shaped into various forms.
Plastics and Polymers
Plastics and polymers offer versatility, lightweight characteristics, durability, and ease of customization in manufacturing. Commonly used plastics include PVC for pipes and window frames, PE for packaging and bottles, and PP for food containers and automotive parts.
Molding processes such as injection molding are employed to create casings and structural parts. Plastics like PE and PP are selected for their low cost and adaptability across a broad range of applications.
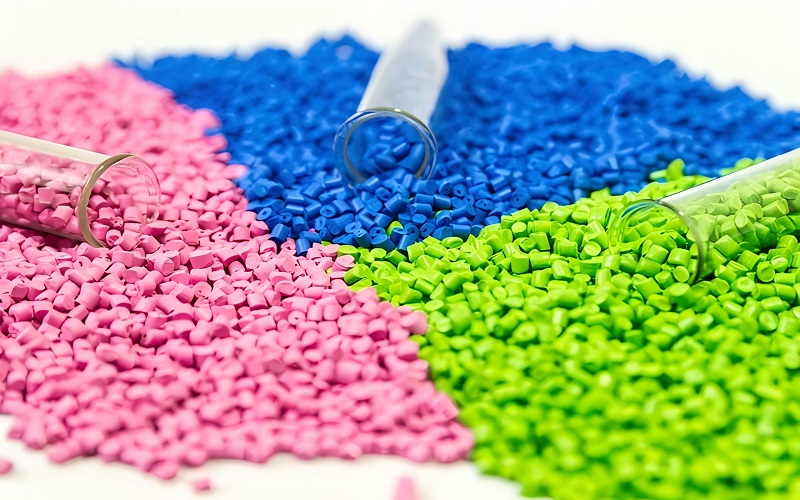
Elastomers and Ceramics
Elastomers are utilized to produce components that are flexible and durable. They also offer resistance to temperature, making them suitable for various consumer products. Their flexibility and resilience make them crucial in manufacturing.
Ceramics provide exceptional strength and are often utilized for their appealing designs in various products, combining durability with aesthetic qualities.
Ensuring Quality in Manufactured Products
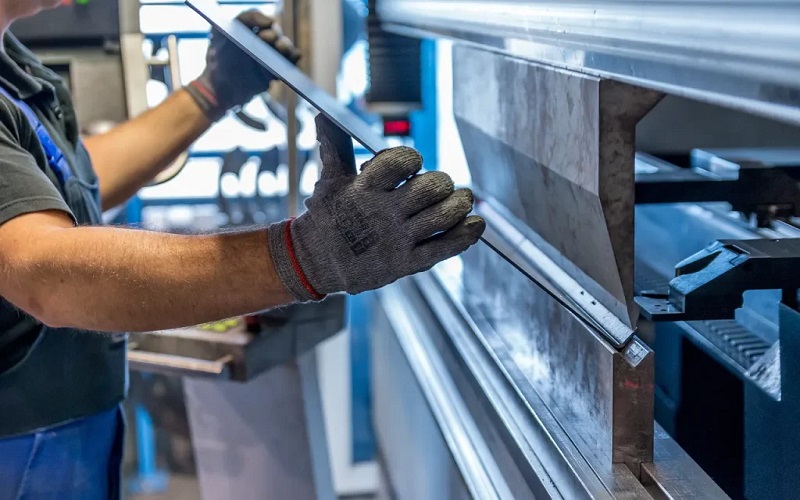
Effective quality control during high-volume production is essential to avoid costly rework and maintain customer satisfaction, especially for brands in industries like clothing or beverages such as coca cola. Batch manufacturing allows for tracking distinct units and enhancing flexibility in quality control. The goal of finishing in manufacturing is to refine the final product to meet design and performance standards.
Key elements that affect customer satisfaction include accuracy, quality, and competitive price.
Quality Control Processes
Quality control processes are essential in manufacturing to ensure product reliability and safety. Rigorous quality control processes and inspections at different production stages are necessary to maintain product quality, particularly for clothing items produced by renowned brands.
Design for Manufacturing (DFM) analysis leads to improved quality, increased productivity, and greater customer satisfaction.
Importance of Prototyping
Prototypes serve to test and validate design, functionality, and manufacturability before mass production. The purpose of prototype development is to test and refine product design, reducing the risk of costly errors later on, which is crucial for maintaining price competitiveness.
During the product design phase, detailed specifications, sketches, or digital models guide developing prototype development for products like clothing by various brands.
The Role of Supply Chains in Manufacturing
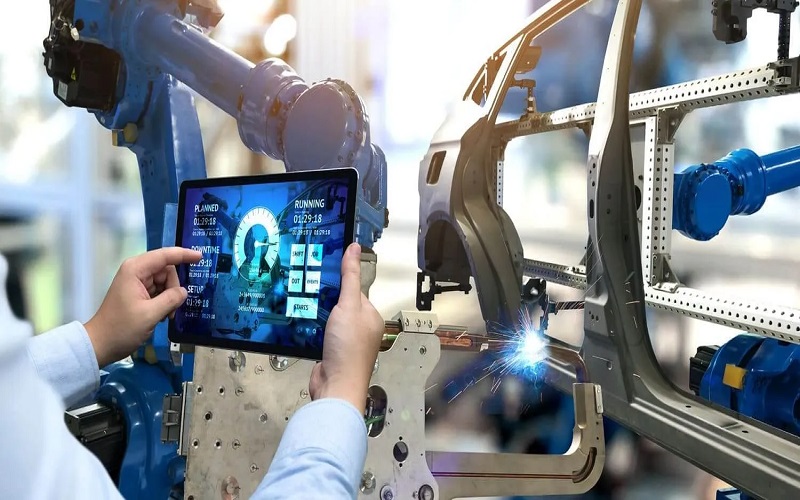
Supply chains significantly influence the manufacturing industry’s efficiency by ensuring timely delivery of essential materials and components. Effective logistics coordination is crucial to ensure timely delivery and efficiency in manufacturing operations.
Companies are urged to transition from Just-In-Time to Just-In-Case inventory strategies to better manage supply chain disruptions and sell robust risk management practices that can significantly reduce downtime in supply chains.
Managing Supply Chain Challenges
Supply chain management often faces challenges such as delays in delivery, inventory shortages, and demand fluctuations, particularly in the electronics sector. External factors like geopolitical issues and natural disasters can disrupt supply chains and create additional challenges. Implementing robust risk management processes helps anticipate potential disruptions and create contingency plans.
Leveraging technology to gain better visibility across the supply chain allows for proactive responses to emerging issues. On the flip side, utilizing just-in-time inventory practices can minimize downtime by reducing holding costs and ensuring materials arrive as needed, though it may increase vulnerability to sudden disruptions.
Leveraging Cloud Computing
Cloud-based platforms in manufacturing connect design and production processes. They also facilitate the management of manufacturing operations. Cloud manufacturing leverages technologies such as cloud computing, data analytics, and the Internet of Things (IoT) to reduce costs, enhance operational efficiencies, and reduce downtime.
Cost Considerations in Manufacturing
Cost considerations in manufacturing encompass direct costs, indirect costs, and overheads. Geopolitical instability and cybersecurity threats are increasingly impacting supply chains, necessitating a rethink in material sourcing strategies and highlighting the importance of robust risk management practices.
Efficient cost management ensures that manufacturers can maintain competitiveness while delivering high-quality products for the company.
Impact of Production Volume
Higher production volumes generally lead to a decrease in cost per unit due to optimized processes and economies of scale. Factors like labor efficiency and the specific manufacturing techniques utilized significantly influence production costs.
Increasing production volumes can reduce overall manufacturing expenses, enhancing cost-effectiveness and profitability.
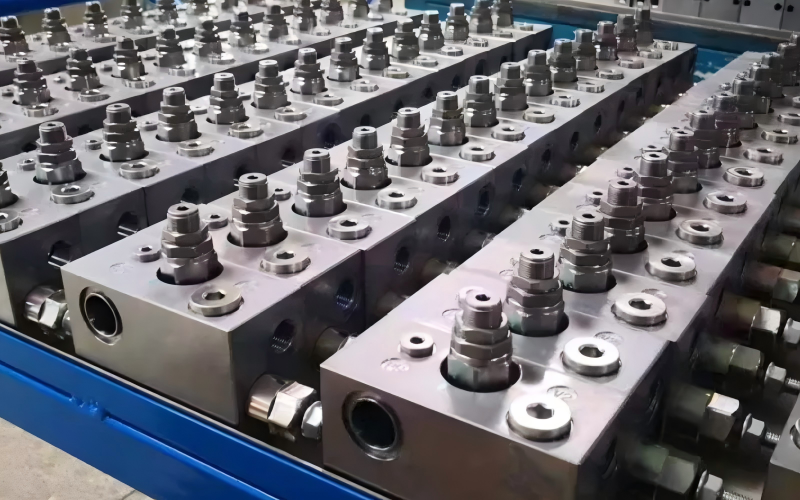
Reducing Labor Costs
Automation helps to lower labor costs by maintaining consistent performance and reducing the need for large manual labor forces. Streamlining production processes through automated systems can enhance operational efficiencies and reduce downtime, ultimately improving profit margins.
Summary
In summary, the manufacturing sector is a complex, multifaceted industry that requires strategic alignment with business goals, careful selection of methods and materials, and rigorous quality control to succeed. From discrete to continuous manufacturing processes, each method offers unique benefits and challenges.
Advanced techniques like additive manufacturing and AI are revolutionizing production, while effective supply chain management and cost considerations remain critical to maintaining competitiveness.
By understanding and implementing these top methods, manufacturers can enhance efficiency, reduce costs, and deliver high-quality products that meet market demands and foster customer loyalty.
Frequently Asked Questions
What is the importance of aligning manufacturing with business strategy?
Aligning manufacturing with business strategy is crucial as it enhances operational efficiencies, meets market demand, and optimizes resource use, thereby strengthening competitive advantage.
What are the core types of manufacturing processes?
The core types of manufacturing processes are discrete manufacturing, repetitive manufacturing, batch manufacturing, and continuous manufacturing, each designed for specific production requirements and product categories. Understanding these processes is essential for optimizing manufacturing efficiency.
How does additive manufacturing benefit the production process?
Additive manufacturing significantly enhances the production process by enabling the creation of complex shapes with minimal waste and allowing for rapid design changes and customization. This leads to increased overall production efficiency.
Why is material selection crucial in manufacturing?
Material selection is essential in manufacturing as it directly influences product performance, durability, and cost-effectiveness. By carefully choosing materials based on their properties, manufacturers can ensure reliability and quality in their products.
How can manufacturers manage supply chain challenges effectively?
Manufacturers can effectively manage supply chain challenges by implementing strong risk management processes, utilizing technology for enhanced visibility, and adopting just-in-time inventory practices to reduce downtime and holding costs. These strategies ensure a more resilient and efficient supply chain.