Blowing moulding is essential for creating hollow plastic products like bottles, containers, and automotive parts. It involves inflating heated plastic into a mould. This article will dive into the techniques, materials, and advancements in blowing moulding, highlighting its benefits and varied applications.
Understanding Blowing Moulding
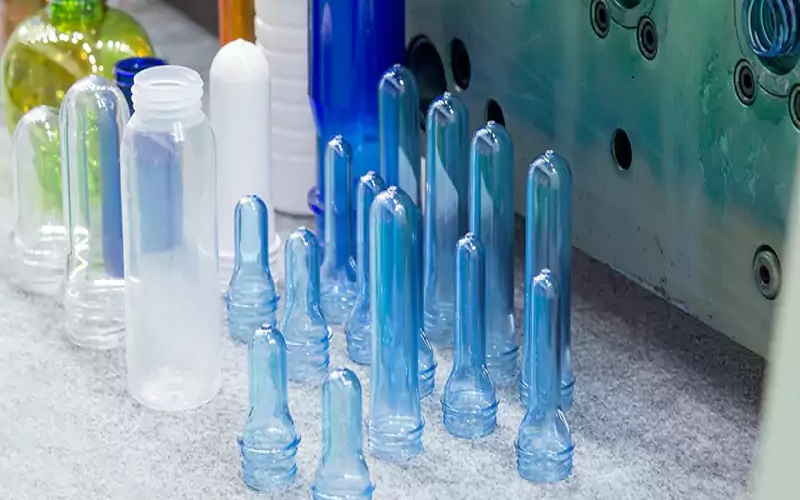
Blow molding is a manufacturing technology for producing various hollow plastic products. This versatile process, where the blow molding process begins with inflating a heated plastic tube known as a parison, is used to create everything from simple bottles and containers to complex shapes like tanks and automotive parts. At its core, plastic blow molding involves inflating the parison with pressurized air until it conforms to the mold’s contours. The parison, a crucial component in this process, is placed between two dies to form the desired shape.
The efficiency and precision of blow molding make it a preferred method in the plastics industry, distinct from processes like glass blowing, which uses molten glass instead of plastic. The process involves heating preforms to a precise temperature, ensuring they maintain structural integrity during inflation, often utilizing molten thermoplastic.
This is essential in various plastic forming processes, including the plastic forming process. To understand the advantages, one can compare blow molding with other methods like rotational molding, which involves rotating a mold to evenly distribute molten plastic without using air pressure.
Cooling is equally important, as uneven cooling can lead to defects in the final product. Multiple molds can include intricate designs and textures, allowing manufacturers to create unique hollow shapes and branding elements for their products, creating hollow plastic products. This meticulous attention to detail ensures high-quality hollow plastic parts, essential for various applications in everyday life.
Extrusion Blow Moulding Process
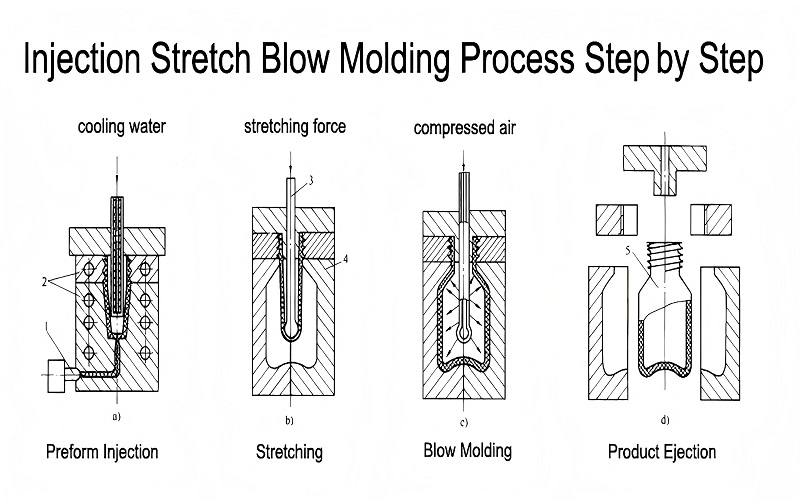
Extrusion blow molding is one of the most common blow molding processes. It begins with the formation of a hollow tube called a parison. This parison is extruded from melted plastic pellets through an extruder barrel.
Once the parison is in place, the mold closes around it, and compressed air is introduced, inflating the parison until it conforms to the final product’s shape and the mold’s contours. The interaction between the molten parison and the mold is crucial for creating high-quality blow molded products, with excess plastic trimmed off to achieve precise shapes.
Extrusion blow molding can be either continuous, where the parison is extruded nonstop, or intermittent, which involves periodic extrusion. This versatility allows for the production of a wide range of hollow plastic parts, from simple containers to more complex shapes like industrial drums.
The process is particularly effective for producing large volumes of products quickly and efficiently, making it a staple in the plastics industry.
Injection Blow Moulding Techniques
Injection blow molding is a widely used technique, primarily for producing small medical containers, single-serve bottles, and other hollow parts. There are three main steps in the process: injection, blowing, and ejection. During the injection phase, injection molded plastic pellets, sometimes combined with materials like natural rubber for specific applications, are melted and injected into a preform mold to create a preform using injection molding.
This preform is then transferred to a blowing station, where it is inflated with compressed air to fill the mold’s shape, ensuring the wall thickness is maintained. A core rod supports the preform during blowing, ensuring it maintains its shape and channels air pressure into it.
Once the product is formed, it is cooled and ejected from the mold, finalizing the injection blow molding process and determining the final product’s shape. This method is particularly efficient and produces high-quality blow molded products, making it ideal for precision containers like medical and cosmetic bottles.
Injection Stretch Blow Moulding Methods
Injection stretch blow molding is a method that emerged in the 1970s, significantly impacting the beverage industry. This process involves stretching the heated material, often thermoplastic elastomers, to form a hollow shape and can be executed in one or two steps.
The two main methods are Single-stage and Double-stage. In the Single-stage process, the preform is made and blown in one continuous process within a granular storage unit that feeds the material, increasing surface area contact, reducing porosity, and enhancing barrier strength.
In the Double-stage method, preforms are first made and then transferred to another machine for reheating and blowing. This method allows for better control over the final product’s quality and consistency.
Injection stretch blow molding is particularly useful for creating containers and high-quality plastic bottles, offering superior strength and clarity.
Commonly Used Plastics in Blow Moulding
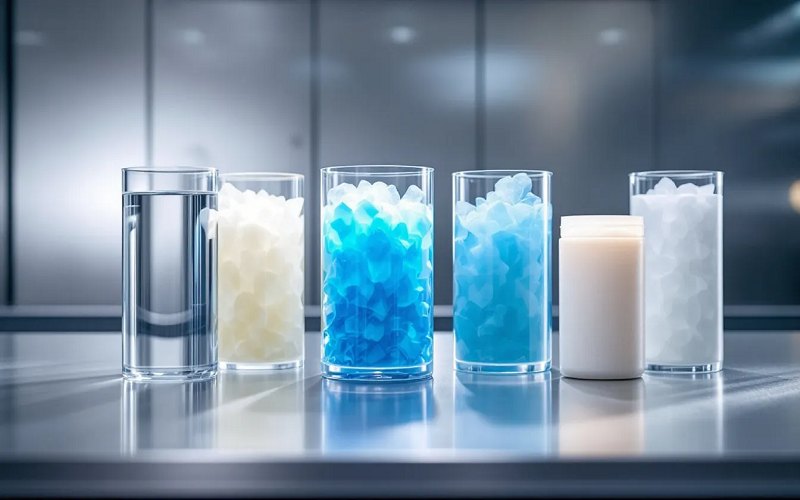
Before: Blow molding utilizes a variety of plastics, each chosen for its specific properties and applications. Common materials consist of several types.
These include polyethylene (HDPE and LDPE), polypropylene (PP), polyethylene terephthalate (PET), polyvinyl chloride (PVC), among others.
These materials are selected based on their chemical properties, recyclability, and suitability for creating different types of blow molded products. After: Blow molding utilizes a variety of plastics, each chosen for its specific properties and applications. Common materials consist of several types:
- Polyethylene (HDPE and LDPE)
- Polypropylene (PP)
- Polyethylene terephthalate (PET)
- Polyvinyl chloride (PVC)
These thermoplastic materials are selected based on their chemical properties, recyclability, and suitability for creating different types of blow molded products.
High Density Polyethylene (HDPE) is the most commonly used plastic in blow molding, known for its strength and chemical resistance. Polypropylene (PP) is valued for its low density and high-temperature resistance, making it suitable for applications like dishwasher components.
Polyvinyl Chloride (PVC) is often used in its soft plastic resin form for medical parts and traffic cones. Each of these materials plays a crucial role in the versatility and efficiency of the blow molding process.
High Density Polyethylene (HDPE)
High Density Polyethylene (HDPE) is a popular choice in blow molding due to its chemical inertness and FDA approval, making it safe for food and beverage containers. HDPE is also highly recyclable, contributing to its popularity as an environmentally friendly option. Its strength and durability make it ideal for producing containers, bottles, and various packaging solutions.
HDPE’s properties ensure that it maintains structural integrity under stress, making it suitable for high-volume production of hollow plastic products. Its versatility and reliability make it a cornerstone material in the blow molding industry.
Low Density Polyethylene (LDPE)
Low Density Polyethylene (LDPE) is characterized by its flexibility, stress crack resistance, and chemical inertness, which makes it molder-friendly and easy to color. LDPE has several common applications. These include squeeze bottles, traffic channelizers, and boat fenders. Its primary usage is in blown film for plastic bags, showcasing its adaptability in various forms and functions.
LDPE’s properties make it suitable for products that require flexibility and durability. Its ease of molding and coloring further enhances its appeal in the plastics industry, ensuring it remains a widely used material in blow molding processes.
Polypropylene (PP)
Polypropylene (PP) is valued for its low density and effectiveness in high-temperature applications, such as dishwasher components. Its resilience and versatility make it a preferred material for various blow molded products. PP is particularly effective for applications that require strength and durability under high temperatures.
The low density plastic of PP makes it easier to mold compared to other plastics, enhancing its versatility and making it suitable for a wide range of products. Its properties ensure that it remains a key material in the blow molding industry, contributing to the production of high-quality, durable products.
Variations in Blowing Moulding Processes
Blow molding processes vary widely, each suited to different applications and product requirements. There are three main types of blow molding. These include extrusion, injection, and injection stretch blow molding.
Extrusion blow molding can be either continuous or intermittent, depending on the specific production needs. Injection stretch blow molding involves stretching the heated material and can be executed in one or two steps.
Choosing the right blow molding process is crucial for achieving the desired product quality and efficiency in the manufacturing process. Choosing blow molding methods helps manufacturers select the best approach for their specific applications.
Contacting an expert or reviewing detailed case studies can provide valuable insights into the most suitable blow molding methods.
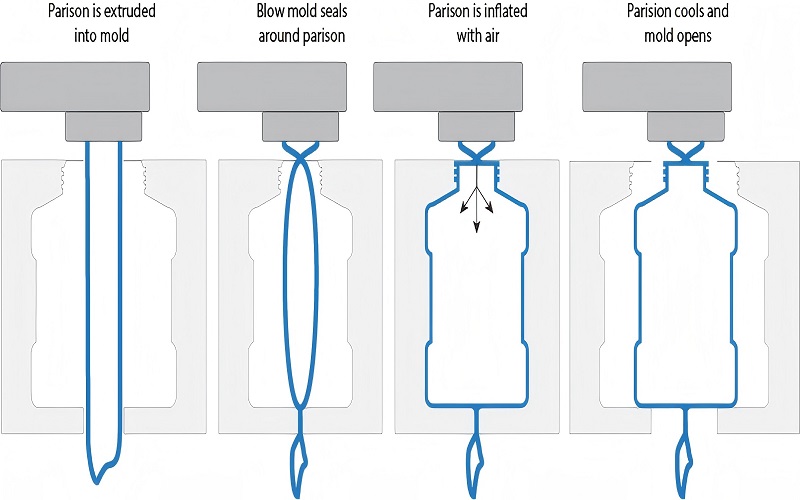
Benefits and Challenges of Blow Moulding
Blow molding offers numerous benefits, including high production speed and cost-effectiveness. Single-stage blow molding can reduce heating costs by utilizing latent heat during manufacturing. Two-stage molding improves wall distribution in the final product by cooling preforms before reheating.
However, blow molding also presents challenges, such as cooling time limitations and the need for precise control over the process. Despite these challenges, advancements in blow molding machinery have significantly reduced energy consumption and improved operational efficiency, making it a highly competitive manufacturing technique.
Innovations in Blowing Moulding Technology
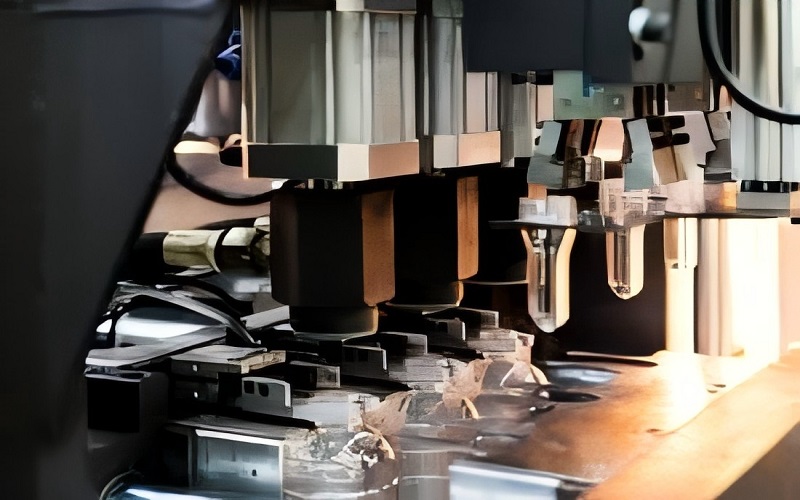
Recent innovations in blow molding technology are revolutionizing the industry with innovative solutions. Automation and artificial intelligence are enhancing precision and speed, leading to reduced operational costs and improved product quality, including high heat resistance in molded parts. These technologies enable real-time adjustments, reducing downtime and enhancing operational efficiency.
Sustainability is also a growing focus, with manufacturers incorporating biodegradable and recyclable materials with controllable mechanical properties to meet specific performance needs. Energy-efficient machinery minimizes waste, making these innovations not only beneficial for the environment but also contributing to more cost-effective and efficient production processes.
Choosing the Right Blow Moulding Supplier
Choosing the right blow molding supplier is crucial for ensuring high-quality products and efficient production. Start by shortlisting three to five suppliers and requesting product samples. Request quotes from multiple suppliers to compare costs and services. Verify the supplier’s track record and customer reviews to assess their reliability.
Evaluate the supplier’s production capabilities, lead times, and ability to meet specific volume and quality requirements. Assess their communication and customer service to ensure a smooth collaboration. Customization options are also important for meeting specific market demands.
Applications of Blow Moulded Products
Blow molding technology has produced a wide range of items, from beverage bottles to industrial plastic tanks and fuel tanks. Common blow molded products include HDPE bottles, polypropylene medical parts, and PVC applications like bellows, often featuring thin walls for lightweight yet durable designs. The process is highly efficient for mass production, capable of quickly producing large volumes of hollow plastic items.
The versatility of blow molding allows it to cater to diverse industries, including packaging, automotive, and agriculture. This adaptability makes blow molding applications a critical process in the plastic manufacturing industry.
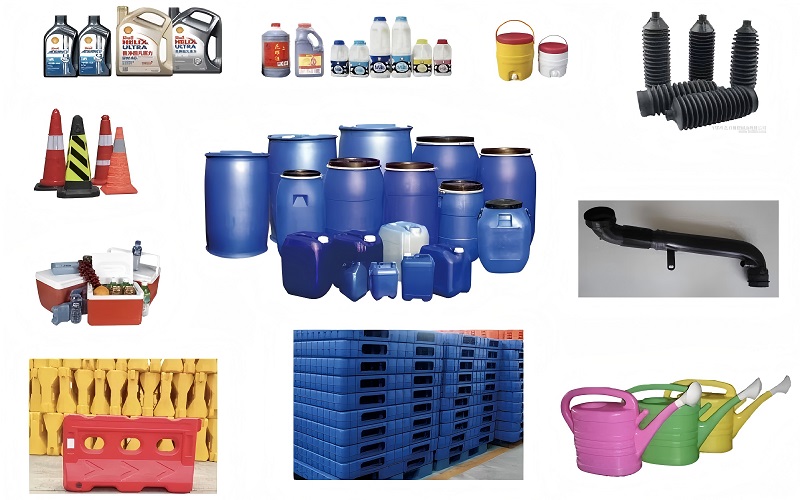
Design Considerations for Blow Moulding
Designing for blow molding requires careful consideration of material selection, part integrity, and structural features. Requesting a design consultation or submitting a CAD file for feedback can optimize the product design. Ensuring sufficient air space between inner and outer walls is crucial for proper part formation.
Incorporating ribs and curves in designs can significantly enhance the strength and stability of blow molded parts. 3D printing technology is becoming increasingly important for rapid prototyping, reducing costs and production times significantly.
Leading Blow Moulding Machines
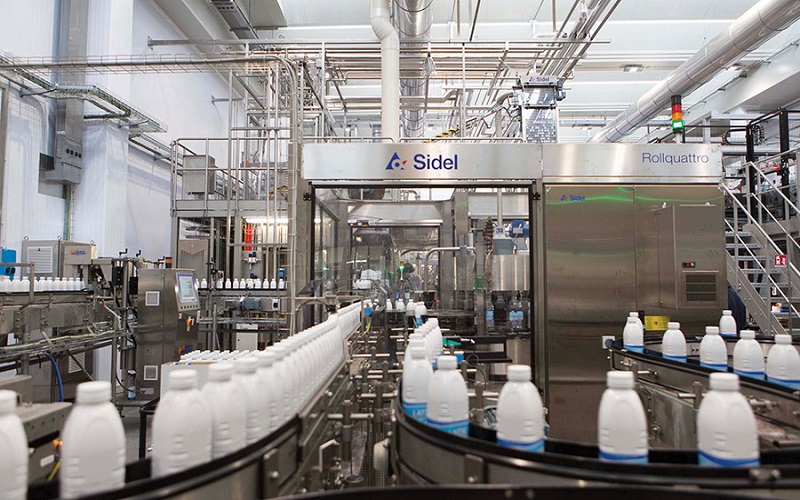
Several companies are at the forefront of blow molding machine manufacturing:
- R&B Plastics Machinery specializes in efficient blow molding systems for various industries.
- Wilmington Machinery offers high-speed rotary blow molding equipment tailored for large plastic parts and beverage containers.
- Uniloy provides a range of precision blow molding machines for food, medical, and automotive applications.
FGH Systems focuses on the food packaging and pharmaceutical industries, providing tailored solutions for their clients. Mirage Packing Industries manufactures turnkey blow molding machines for water and beverage production. These companies, along with others like The Japan Steel Works and Pet All Manufacturing, contribute significantly to the advancements in blow molding technology.
Future Trends in Blow Moulding
The future of blow molding is set to be shaped by emerging technologies like:
- AI and 3D printing, which are expected to enhance customization and efficiency
- More tailored products and reduced production time, benefiting manufacturers and consumers alike
- Sustainability, which will play a crucial role, with advancements in automation and material science driving the industry towards more eco-friendly practices
As the industry continues to evolve, manufacturers will need to stay ahead of these trends to remain competitive. The focus on innovation and sustainability will ensure that blow molding remains a vital process in plastic manufacturing.
Summary
Blow molding is an essential and versatile process in the plastics industry, enabling the mass production of a wide range of hollow plastic products. From extrusion blow molding to injection stretch blow molding, each technique offers unique advantages and applications.
Understanding the materials used, such as HDPE, LDPE, and PP, is crucial for optimizing product quality and performance. Innovations in automation, AI, and sustainable materials are driving the industry forward, making blow molding more efficient and environmentally friendly.
Choosing the right blow molding supplier, understanding design considerations, and staying ahead of future trends are critical for success in this field. By leveraging the latest technologies and best practices, manufacturers can produce high-quality, cost-effective products that meet the evolving demands of the market.
The future of blow molding is bright, with continued advancements promising even greater efficiency and sustainability.
Frequently Asked Questions
What are the main types of blow molding processes?
The main types of blow molding processes are extrusion blow molding, injection blow molding, and injection stretch blow molding. Each offers unique applications and benefits tailored to different production needs.
What materials are commonly used in blow molding?
Blow molding primarily employs materials such as High Density Polyethylene (HDPE), Low Density Polyethylene (LDPE), Polypropylene (PP), Polyethylene Terephthalate (PET), and Polyvinyl Chloride (PVC). These materials are favored for their versatility and performance in manufacturing.
What are the benefits of using blow molding for manufacturing?
Blow molding offers significant benefits such as high production speed, cost-effectiveness, and the capacity to efficiently manufacture large volumes of hollow plastic products. Additionally, advancements in technology have enhanced energy efficiency and product quality.
How do I choose the right blow molding supplier?
To select the right blow molding supplier, it is essential to shortlist potential candidates, request product samples, and evaluate their production capabilities. Additionally, checking customer reviews and assessing their communication and customization options will help ensure you make an informed decision.
What are the future trends in blow molding?
The future of blow molding will be shaped by increased automation and artificial intelligence, along with a shift towards biodegradable and recyclable materials, complemented by advancements in 3D printing for rapid prototyping and customization. These trends indicate a move towards more sustainable and efficient manufacturing processes.