In the field of plastic manufacturing, engineers and designers often face the choice between ABS and Nylon.
ABS, with its superior mechanical properties and ease of processing, is widely used in the production of automobiles, electronic appliances, and consumer goods.
On the other hand, Nylon is known for its high strength and wear resistance, making it a key material in industrial machinery, automotive components, and textiles.
This article will focus on the theme of “ABS vs Nylon,” delving into the differences between these two materials in terms of physical properties, advantages and disadvantages, and application areas.
ABS
ABS (Acrylonitrile-Butadiene-Styrene copolymer) is a thermoplastic polymer formed by the copolymerization of three monomers: acrylonitrile, butadiene, and styrene.
ABS combines the properties of its three components: acrylonitrile enhances oil resistance and chemical corrosion resistance, providing a certain degree of surface hardness; butadiene imparts rubber-like toughness to ABS, improving its impact toughness; styrene gives ABS good flowability, making it suitable for thermoplastic molding processes.
The history of ABS dates back to the 1940s when it was first synthesized by Swiss chemists.
In 1954, Borg-Warner Corporation introduced ABS to the commercial market, and it gradually became an important engineering plastic.
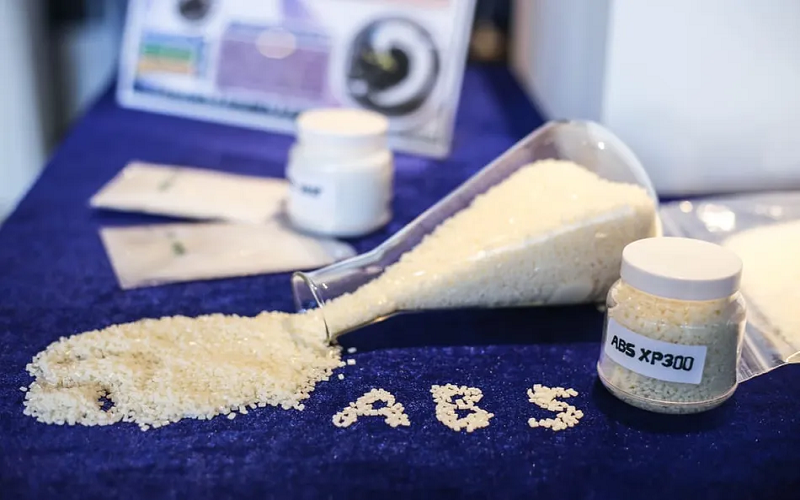
Nylon
Polyamide plastics (abbreviated as PA) are a large class of polymer compounds containing many repeating amide groups in the main chain, commonly known as nylon.
The American company DuPont was the first to develop nylon resin for fiber use, achieving industrial production in 1939.
In the 1950s, nylon began to be used for injection molding products to replace metal, meeting the downstream industries’ needs for lightweight and cost-effective solutions.
Nylon’s wear resistance is ten times higher than that of cotton, and it possesses excellent heat resistance, self-lubricating properties, and a low friction coefficient. Additionally, nylon is easy to process and can be compounded with glass fibers and other fillers to further enhance its properties.
Currently, nylon 6 and nylon 66 account for over 95% of the global nylon demand, holding a dominant position in the market.
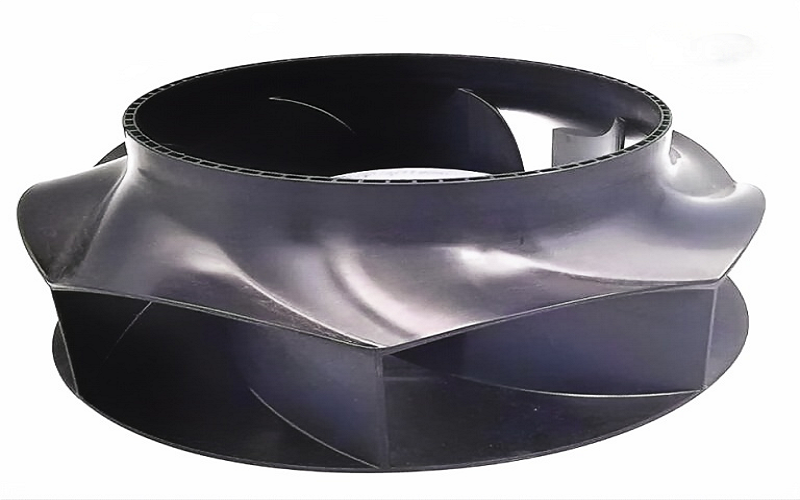
ABS vs Nylon:Properties
ABS has an opaque, ivory-colored granular appearance. It is non-toxic, odorless, and has low water absorption.
It exhibits greater impact resistance and a slightly higher heat distortion temperature compared to HIPS.
ABS plastic is lightweight, strong, has a high surface hardness, and offers a glossy finish.
It is dimensionally stable and resistant to creep.
In contrast, nylon is a translucent to opaque polymer with a slightly yellow or milky white crystalline appearance.
It possesses excellent wear resistance, self-lubricating properties, and a low friction coefficient.
Additionally, nylon demonstrates good chemical and corrosion resistance, effectively withstanding most chemicals, oils, and solvents.
Property | ABS | Nylon |
Density(g/cm3) | 1.05-1.18 | 1.13 |
Melting point(℃) | 200-250 | 210-225 |
Tensile Strength(MPa) | 30-50 | >60 |
Flexural Strength(MPa) | 50 | 90 |
Elongation(%) | 10-40 | >30 |
Heat deflection temperature(℃) | 93-118 | 80-120 |
Shrink rate (%) | 0.4-0.7 | 0.5-2.0 |
Hardness | 108 | 70-120 |
Water Absorption(%) | 0.2-0.8 | 1-3.5 |
The Advantage And Disadvantages Of ABS & Nylon
When choosing between these two materials, the pros and cons of ABS and nylon are significant factors to consider.
Advantages of ABS
- High strength, hardness, and toughness
- Excellent electrical insulation
- Good processing performance
- High surface gloss
- Good resistance to diluted acids and alkalis
Disadvantages of ABS
- Poor weather resistance
- Limited heat resistance
- Not flame-retardant
- Not resistant to organic solvents and strong acids and alkalis
Advantages of Nylon
- Outstanding wear resistance
- Good corrosion resistance
- High tensile strength
- Self-lubricating properties
- High temperature resistance
Disadvantages of Nylon
- High water absorption
- Prone to static electricity
- Poor light resistance
- Flammable
Overall, ABS offers high strength, good toughness, and excellent chemical and electrical properties, but it has poor weather and heat resistance, is not flame-retardant, and is not resistant to organic solvents and strong acids.
Nylon excels in wear and corrosion resistance with higher tensile strength than ABS, but it absorbs water, generates static electricity, has poor light resistance, and is flammable.
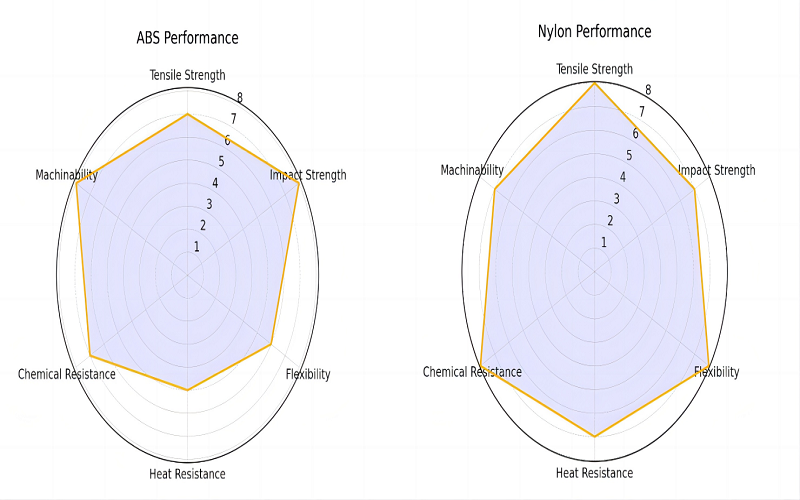
How to Process ABS or Nylon?
Exploring the differences between ABS and nylon materials requires not only an understanding of the materials themselves but also their different performances in processing and manufacturing.
ABS plastic has excellent processing performance and can be molded using injection molding machines, extruders, and other plastic forming equipment for injection molding, extrusion, blow molding, calendering, laminating, foaming, and thermoforming.
It can also be welded, coated, electroplated, and mechanically processed. Among these, injection molding is the most common processing method for ABS plastic.
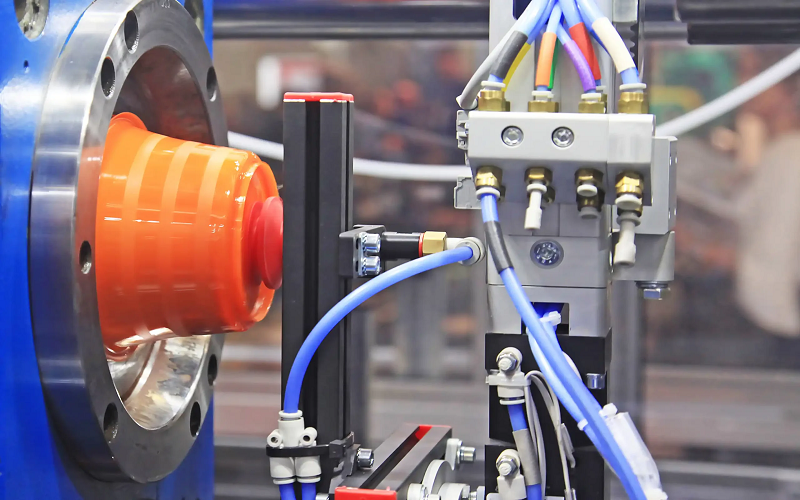
Nylon’s processing performance mainly benefits from its plasticity, allowing it to be formed through various methods, including but not limited to extrusion, injection molding, and mechanical processing.
In injection molding, nylon is sometimes filled with 10% to 40% glass fibers to enhance its tensile strength.
For example, plastic hooks use nylon with over 40% glass fiber. Additionally, due to nylon’s high hygroscopicity, thorough pre-drying is required before processing to ensure smooth molding.
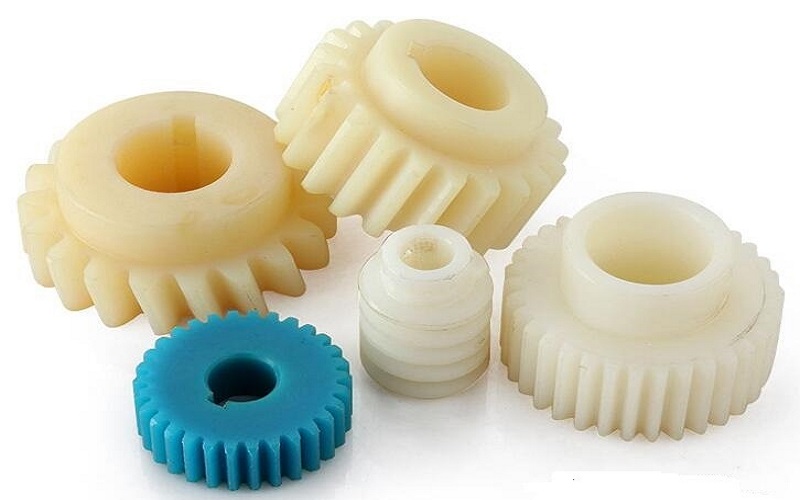
Parameter | ABS Injection Molding | Nylon Injection Molding |
Injection Temperature (℃) | 210-250 | 240-300 |
Mold Temperature (℃) | 50-80 | 80-100 |
Injection Pressure (MPa) | 50-70 | 70-140 |
Injection Speed | Medium to High | Medium |
Cooling Time (s) | 20-60 | 20-40 |
Drying Temperature (℃) | 80-90 | 80-90 |
Drying Time (hrs) | 2-4 | 4-6 |
Nylon vs ABS:3D Printing
In 3D printing, ABS and nylon are commonly used materials, but their printing characteristics and applications are quite different.
ABS is easy to process and has a lower cost, with the ability to achieve a smooth surface finish, making it suitable for applications with high aesthetic requirements.
However, ABS tends to warp and shrink during printing and may release unpleasant and harmful gases, requiring good ventilation and avoidance in food-contact applications.
Additionally, ABS has poor layer adhesion, which can affect the overall strength of the printed part.
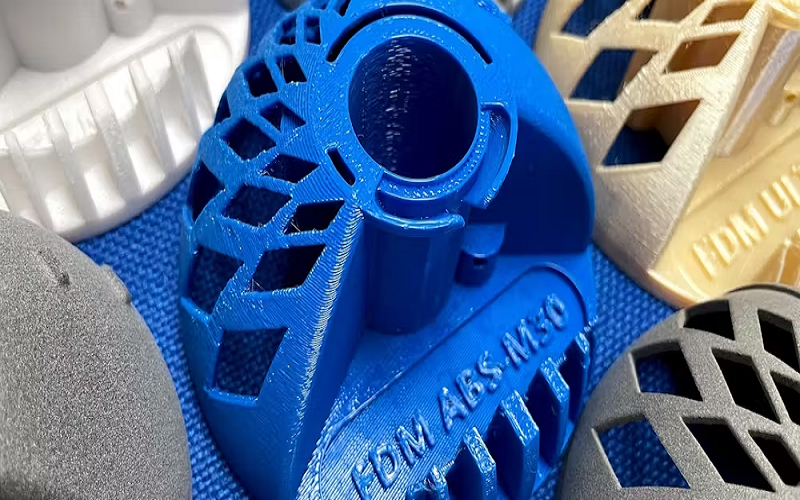
In contrast, nylon exhibits excellent wear resistance and high tensile strength in 3D printing, making it ideal for manufacturing wear-resistant parts.
However, nylon has high hygroscopicity, requiring thorough drying before printing, and it demands more stringent printing conditions.
Moreover, nylon has a higher printing cost, and achieving a smooth surface finish is more challenging compared to ABS.
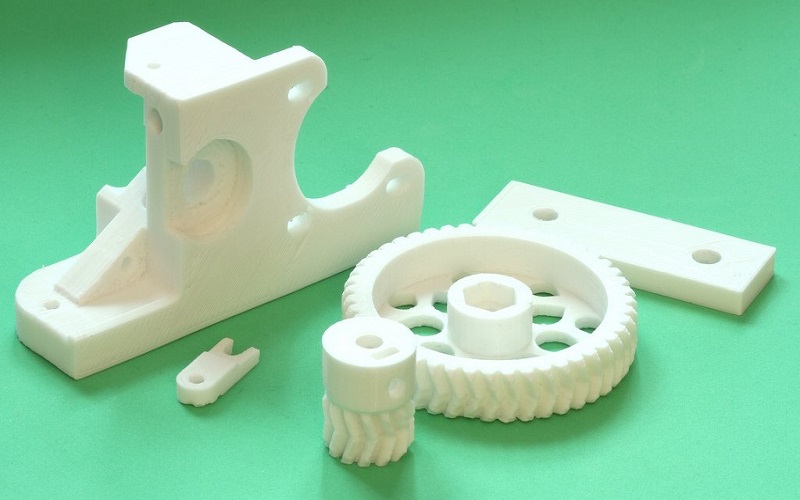
Overall, nylon is better suited for applications requiring high performance, while ABS offers advantages in cost and ease of use.
Applications Of ABS And Nylon
Different properties determine the applications of materials, and ABS and nylon each have their specific areas of suitability.
ABS materials are widely used, covering a range of fields from daily necessities to high-tech products:
- Automotive Parts: Dashboards, body panels, steering wheels
- Electronics and Appliances: Housings and internal structural components for refrigerators, computers, copiers, etc.
- Construction Industry: ABS pipes, sanitary ware, decorative panels
- Engineering Plastic Alloys: PC-ABS
- Others: Toys, office equipment
Nylon products, with their lightweight, excellent mechanical strength, wear resistance, and good corrosion resistance, have become important materials for replacing steel, iron, copper, and other metals, and have a wide range of uses:
- Mechanical Parts: Bearings, gears, pump impellers
- Medical Field: Surgical sutures, medical catheters, stents, and instrument components
- Construction Engineering: Door and window seals, pipe insulation sleeves
- Textiles: Clothing, socks
- Industrial Goods: Tire cords, industrial fabrics, ropes, conveyor belts
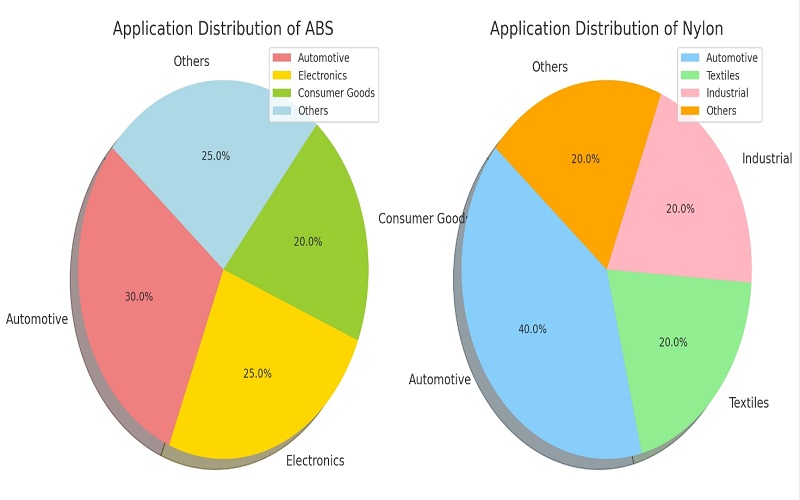
Safety Considerations for ABS and Nylon
Theoretically, both ABS and nylon are considered safe materials, but they do present certain safety risks in specific environments and applications.
ABS material is non-toxic and odorless, with good chemical stability, and under normal conditions, it does not release harmful gases.
However, during high-temperature processing, ABS may release harmful gases such as styrene monomers, so good ventilation is necessary.
Additionally, ABS combustion produces toxic smoke and gases, such as carbon monoxide and hydrogen cyanide, which requires careful fire safety measures.
Nylon has good stability and durability, and under normal conditions, it is non-toxic and does not pose a direct threat to human health, nor does it release toxic substances at high temperatures, making it generally considered safe.
However, if additives are introduced during the processing of nylon products, these additives may release toxic substances at high temperatures or in specific environments, posing health risks.
Long-term use of improperly treated nylon products, such as clothing made from nylon polyester synthetic fibers, may cause discomfort or skin allergies.
Therefore, when using ABS and nylon materials, it is essential to pay attention to the usage environment and implement appropriate protective measures.
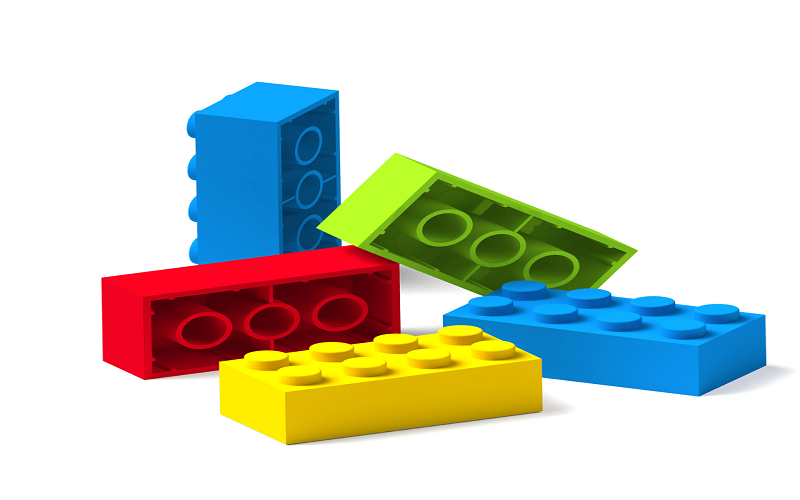
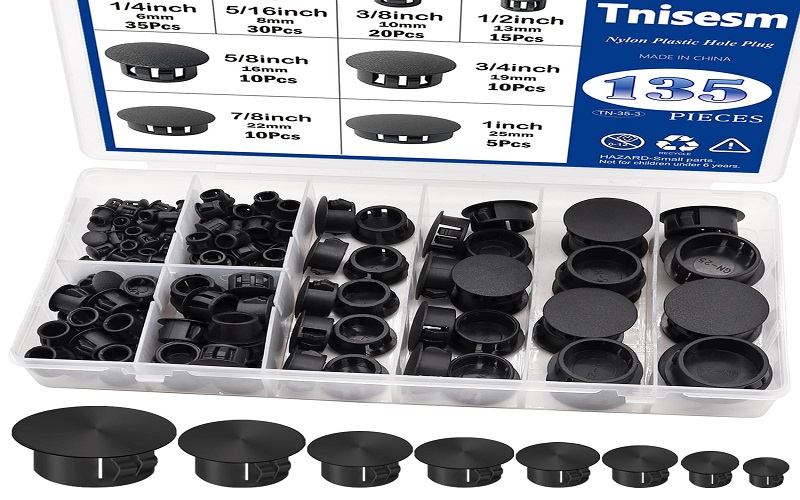
Can ABS and Nylon Be Recycled?
ABS, derived from petroleum, is inherently non-renewable, but it is a recyclable plastic.
The recycling process involves collecting, sorting, cleaning, crushing, and melting into pellets, which can then be used to produce new products.
Thus, recycling waste ABS plastic not only helps conserve resources but also reduces environmental pollution.
Nylon, as a widely used synthetic fiber, can be recycled through both physical and chemical methods.
Physical recycling involves mechanically processing waste nylon into new products, while chemical recycling breaks down nylon into monomers through depolymerization, which are then repolymerized into new nylon materials.
Diverse recycling methods not only aid in environmental protection but also offer significant economic value. They save a substantial amount of raw materials and energy, providing an effective solution for the circular use of nylon.
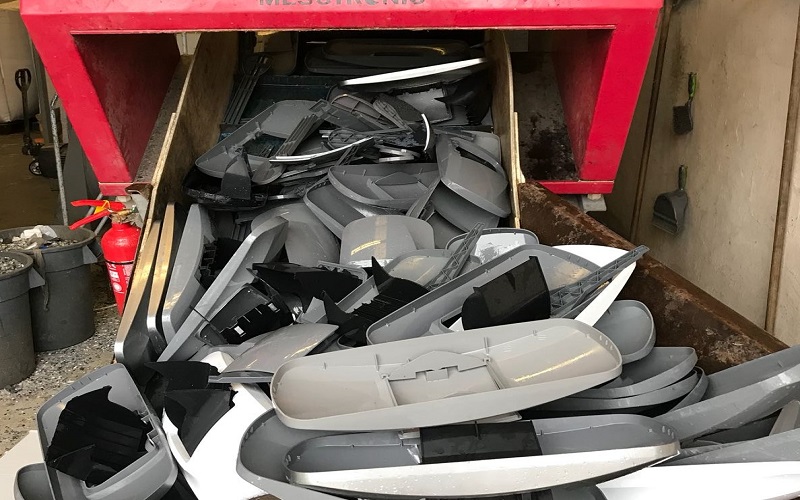
Is Nylon More Expensive Than ABS?
In terms of material price, nylon is more expensive than ABS. For example, commonly used Nylon 6 pellets are priced at around $1.80 to $2.20 per kilogram, while Nylon 6 fibers cost about $2.12 to $2.50 per kilogram.
In comparison, high-quality ABS pellets are typically priced between $1.50 and $2.00 per kilogram.
Conclusion
In summary, ABS and nylon each have their own strengths, showcasing unique performance and application capabilities.
ABS offers excellent dimensional stability and dyeability, is very easy to process and print, but has a lower heat distortion temperature and poor weather resistance, making it suitable for cost-sensitive and general applications.
In contrast, nylon has higher strength, better wear resistance, and superior chemical and heat resistance, making it ideal for high-strength and wear-resistant applications.
However, nylon has high hygroscopicity and requires drying during the molding process.
If your project considers both performance and manufacturing costs, ABS is the more suitable choice; if strength and wear resistance are the primary concerns, nylon is the best option.