Aluminum injection molding is rapidly emerging as an important manufacturing process and is gaining prevalence in the manufacturing world today. Aluminum injection molding injects molten aluminum into molds at high temperature and pressure for fast production of complex and high quality aluminum parts. It allows for improved efficiencies in production and significantly reduces material waste and production costs.
Due to the process being faster, more efficient in production and cheaper when compared to more traditional processes including steel injection molding for the production of parts that could have applications in the automotive, aerospace, consumer electronics and medical device spaces.
While steel injection molding will also produce very durable parts the process will not be as efficient or as cost friendly to obtain parts compared to aluminum injection molding.
In this article we will review more of the basic concepts, advantages and applications for aluminum injection molding and help to understand how these advancements are advancing manufacturing and modern industry.
What Is Aluminum?
Definition of Aluminum
Aluminum, with the chemical symbol of “Al”, is a lightweight, corrosion-resistant metal existing as one of the most plentiful metals in the Earth’s crust, composing over 8% of it.
Due to the lightweight chemical properties of aluminum, it exhibits a level of ductility, combined with excellent thermal conductivity. Because of this, aluminum is commonly used in transportation, building, packaging and machinery.
Aluminum has a long history, but industrial extraction of aluminum did not occur at a large scale until the twentieth century. Large-scale production of aluminum began with modern manufacturing processes developed in 1886, which revolutionized aluminum acquisition and use.
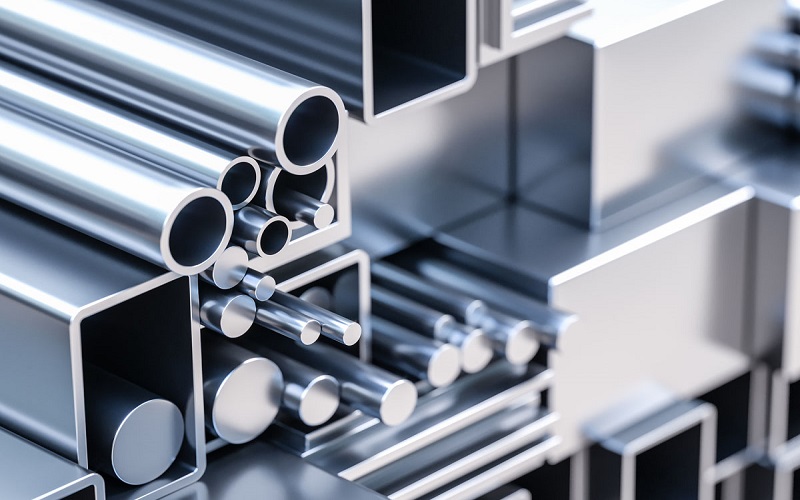
Properties of Aluminum
Aluminum’s physical and chemical properties:
Property | Value | Description |
Chemical Symbol | Al | The chemical symbol for aluminum |
Atomic Number | 13 | The position of aluminum in the periodic table |
Atomic Weight | 26.98 amu | The relative atomic mass of aluminum |
Density | 2.70 g/cm³ | The density of aluminum, representing mass per unit volume |
Melting Point | 660.3°C | The temperature at which aluminum melts |
Boiling Point | 2519°C | The temperature at which aluminum boils |
Color | Silver-white | The color of aluminum in its natural state |
Hardness | 2.75 (Mohs hardness) | The hardness of aluminum, indicating its wear resistance |
Electrical Conductivity | 37.7 × 10^6 S/m | The electrical conductivity of aluminum |
Thermal Conductivity | 237 W/(m·K) | The thermal conductivity of aluminum |
Chemical Stability | High | The resistance of aluminum to chemical reactions at room temperature |
Reactivity | Reacts with oxygen to form aluminum oxide (Al₂O₃) | Aluminum reacts with oxygen to form a protective layer of aluminum oxide |
What Is Aluminum Injection Molding?
Aluminum injection molding is an advanced manufacturing process that uses aluminum metal to produce complex aluminum parts in rapid cycles by injecting molten aluminum at a high temperature and pressure into a mold. It is especially valuable in prototyping and when producing certain complex geometries in industries such as automotive, aerospace, and industry.
Aluminum injection molding has multiple advantages. This process offers materials efficiencies in the production process, and is more efficient as it causes less material to be lost, uses less energy to heat the mold for producing molded parts, and offers some of the best thermal efficiency when laser etching aluminum parts.
Further benefits of aluminum injection molding is that the production costs of aluminum molds are more efficient than costs of steel molds. It has become more desired and valuable in a contemporary operational manufacturing context.
The Process Of Aluminum Injection Molding
Preparing The Aluminum For Pouring
- Raw Material: Start with aluminum ingots or pellets as the starting raw material.
- Melting: Place your aluminum in the furnace and apply heat until the aluminum reaches a temperature above its melting point (660.3 °C) to remove contaminants.
Pouring into Molds
- Preheating Molds: Since the aluminum will cool quickly in the molds, it is essential to preheat the molds before pouring.
- Pouring: Once the molds are preheated, you can pour molten aluminum into the molds using a pouring machine, ensuring that the aluminum is poured completely into the mold.
Cooling and Solidification
- Cooling: After pouring, quickly cool the aluminum in the molds, utilizing the cooling system.
- Solidification: Once cooled, allow the aluminum to solidify, and once the aluminum hardened, remove it from the mold for inspection.
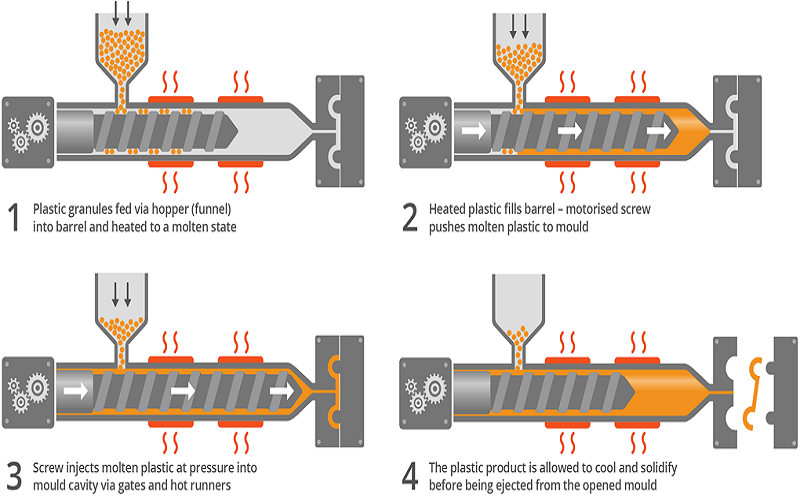
Advantages Of Aluminum Injection Molding
Cost-Effectiveness
The production of aluminum injection molds tend to be more cost-effective than that of steel molds. While the actual cost and return-on-investment regarding molds are influenced by use, aluminum molds are normally interchangeable at a lower cost.
Reduced Lead Time
Aluminum molds can significantly minimize lead-time to production. Depending on the complexity, the cycle from design to end-product can take merely a few days for aluminum molds, as opposed to possibly taking months for steel. This emphasis on speed has substantial implications for the product’s development timeline and market entry.
Best for Small Production Runs
Aluminum injection molds add more value than steel molds for smaller production runs. They involve a lower upfront cost and are capable of producing thousands of parts reliably, so they are a superior choice when manufacturing in small batches or considering short run work.
Less Processing Time
Aluminum molds use heat transfer more effectively than steel molds, allowing for shorter heating and cooling turnarounds. This results in a shortened injection molding cycle, which leads to the production of parts at a quicker rate.
Better Product Quality
Aluminum molds dissipate heat to surrounding air effectively, allowing for even heating/cooling of the mold. The even dissipation of heat helps to minimize molding defects such as dents, voids, and burn marks on the part’s surface. Overall, an aluminum mold can lead to a higher quality part while eliminating rejected products.
Higher Ease of Maintenance and Modification
Aluminum molds are easier to build, modify, and repair when compared to steel molds. Aluminum is a softer material than steel and the design of most aluminum molds is less complicated, so broken aluminum molds can be quickly and inexpensively repaired. This saves on repair time as well as costs associated with mold repairs and/or machines being out of operation.

Applications of Aluminum Injection Molding
Aluminum injection molding is an efficient, economical manufacturing solution that creates parts of excellent quality that is relied upon in many different industries.
In the automotive industry, this manufacturing method is used to make lightweight, durable components, such as engine parts and brackets, that improve fuel efficiency and performance.
In aerospace, aluminum’s strength and light weight are useful for making mission critical components such as aircraft structures, which reduce aircraft weight and fuel consumption.
Aluminum injection molding is used in consumer electronics to make high tolerance electronic device components, such as smart phones and laptops, combine power with aesthetics.
The medical industry also values aluminum injection molding as a source of accurately manufactured and reliable medical devices and instruments.
Further, aluminum injection molding is widely used in various types of industrial machinery, household products, communication equipment, and lighting fixtures.
Aluminum’s light weight and heat dissipation ability make it a useful element in the manufacture of durable, energy-efficient, and aesthetically enjoyable products. The ability to manufacture delicate products and components of high quality with aluminum injection molding makes it a unique option in manufacturing.
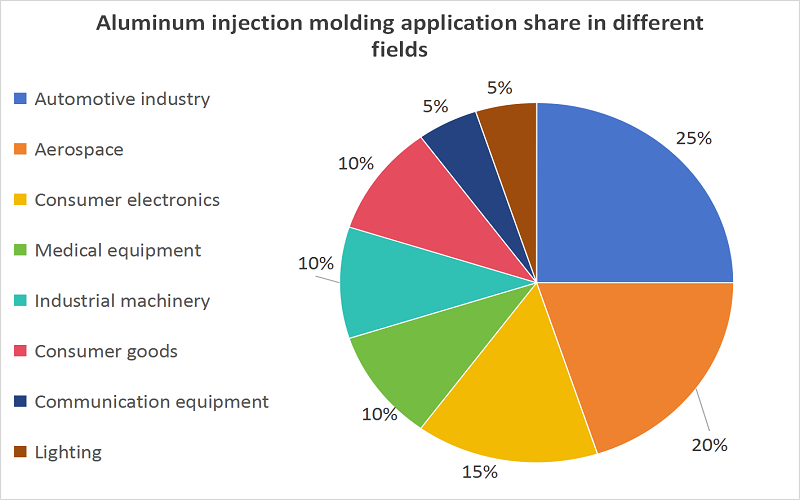
Aluminum Injection Molding VS Steel Injection Molding
Two fabrication technologies that are often used to manufacture parts are aluminum and steel injection molding. Both methods can product parts with a high degree of precision—but they differ on many levels.
Molds made from aluminum are much cheaper and faster to manufacture, making them the best choice for the production of small quantities of parts or proof-of-concept products.
Although steel molds are more expensive, they are much more durable, making them ideal for high-volume manufacturing. It is important to consider the pros and cons of related to each technology to help in their selection.
Cost
Aluminum injection molding is cheaper than steel molding and makes for a good decision for small-quantity or test production.
Overall cost-effectiveness may favor the use of steel molds for larger production quantities, although their initial cost is higher remaining durable and allowing for more cost-effective operation overtime.
Production cycle
Aluminum molds generally have a quick turnaround time; they will typically support mold production in days and are ideal for projects where time is limited.
Steel molds, on the other hand, tend to be a longer production time, often approaching four months and are better suited for a long-term large volume production effort.
Production efficiency
Compared to steel mold, aluminum molds allow for greater heating and cooling time (during the molding cycle), which may contribute to a larger boost in production. This may provide benefits specifically for small batch production and/or more rapid design iteration of products.
Although steel molds offer some operational advantages when the current designs are significant enough, operation efficiency would be potential benefits, generally.
Durability
Aluminum molds generally perish in intense heat and pressure, hence they are mainly used for small amount production runs and pilot tests.
Conversely, steel molds have a high life span and can be used over long periods of time even when subjected to high intensity hence they are most preferred for mass production purposes.
Surface quality
They have uniform heating and cooling capability that results into smooth surface on parts made from Aluminum molds. On the other hand, steel molds are preferable for large scale production because of their consistency with regard to quality during such manufacturing processes while still maintaining good surfaces.
General suitability of aluminum injection molding is towards quick production and short run requirements. Conversely, steel injection molding is suitable for mass volume long term productions. Your specific needs and budget dictate the choice among the technologies.
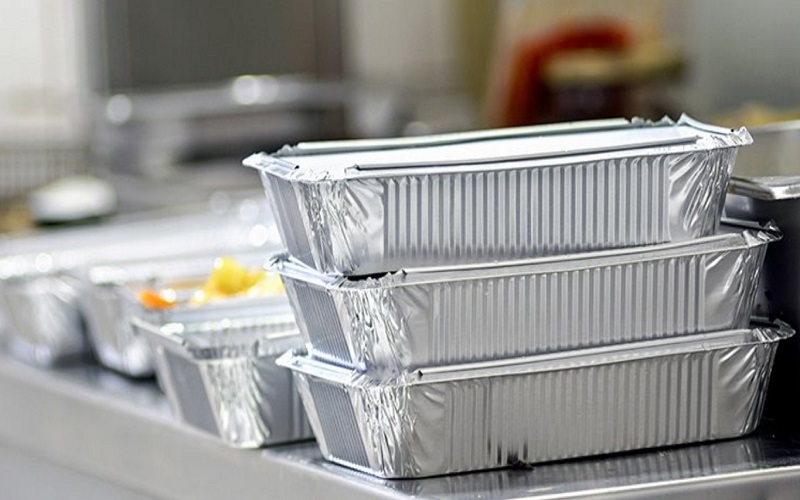
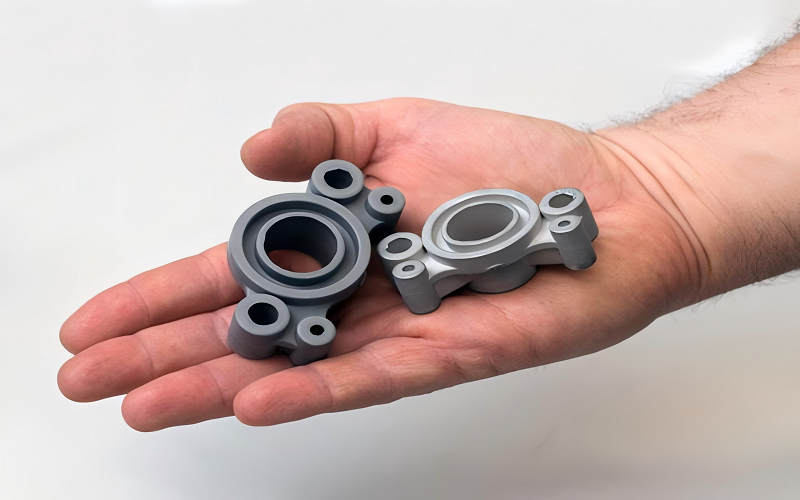
Conclusion
This article gives an overview of the basics, properties as well as design recommendations for aluminium injection moulding.
Aluminum prototype molds may seem complex although partnering with a manufacturer who understands this process well and has experience in product development will ensure that your product comes out correctly upon moulding.
We can provide quotations on your designs should you require manufacturing guidance or CAD files through our team at any time.
FAQs
Can Aluminum be Injection Moulded?
Of course, it is feasible to injection mold aluminum. Aluminum molds for injection molding are perfect for fast prototyping and short run productions.
Unlike harder metals, aluminum is more malleable hence easier and faster in machining during the production of the initial mold. This allows prototypes and small batch components to be produced quickly and at low cost.
Despite being less rugged than steel molds for high volume production, aluminum molds are widely preferred where speed and flexibility are critical.
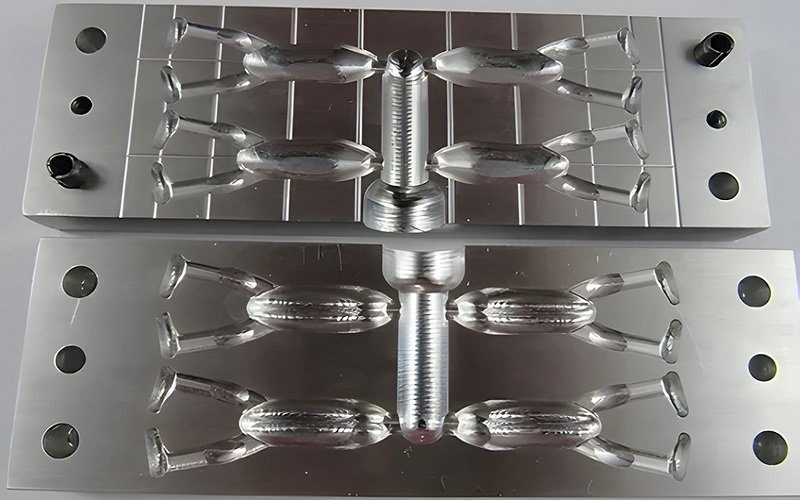
What Grade Of Aluminum Is Used For Injection Molding?
The most common grades of aluminum used in injection molding include:
Aluminum 6061: This versatile alloy has a good combination of machinability, strength, and corrosion resistance which makes it one of the most frequently selected alloys for making injection moulds. It is therefore often chosen as material for both prototype and production moulds.
Aluminum 7075: These grades are used in more demanding applications that require high strength with little deformation. It does not have same ease of machining as compared to 6061 but it performs well under conditions involving elevated stresses.
Aluminum 2024: Although not found commonly this grade has a quite impressive weight-to-strength ratio thus great fatigue performance used mostly in aerospace.
The selection of these aluminum grades is dictated by the specific needs of the molding process, encompassing factors such as strength, machinability, and corrosion resistance.
Is Aluminum Injection Molding A Better Option Compared To Steel Injection Molding?
Aluminum injection molding and steel injection molding each have their own advantages and disadvantages varying based on their specific use case.
There are several reasons you may choose aluminum injection molding.
First, aluminum molds are cheaper than steel molds, making aluminum ideal for small product batches.
Second, aluminum has a faster heat up and cooling time, allowing for faster product production. In addition to speed, aluminum is easier to manufacture, which means the mold can be made, changed and updated quicker than a steel injection mold.
A disadvantage of aluminum injection molding is that aluminum molds are not as stable or durable as steel molds. They are thus not well-suited for larger production runs. Aluminum also is not as strong as steel molds and thus is not suitable for parts that require strength.
In contrast, steel injection molding has excellent strength and durability.
Steel molds hold up to repeated use, especially with mass production parts. Steel’s strength allows manufacturers to create larger parts that last longer than an aluminum mold. An unfavorable aspect of steel injection molds is that they are more expensive to produce and are unsuitable for smaller runs.
The process of building a steel mold is also more difficult, takes longer, and is not as easily redesigned after the initial molding was done. Steel also has a slower heat up and cooling time compared to aluminum, adding to an overall longer production cycle.
Overall, if you want to produce a small amount of product quickly, aluminum injection molding may be the right choice. Alternatively, if your company needs molds that are durable and for producing parts on a large scale, steel injection molding would be a better choice.