CNC plastic machining is the process of using CNC machines to accurately cut and shape plastic materials into complex parts.
It’s highly precise and cost-effective, suitable for both prototyping and small-scale production. Popular materials include ABS, PEEK, polycarbonate, and HDPE.
In this article, you’ll learn about selecting the right material and the advantages of CNC plastic machining.
Introduction to CNC Plastic Machining
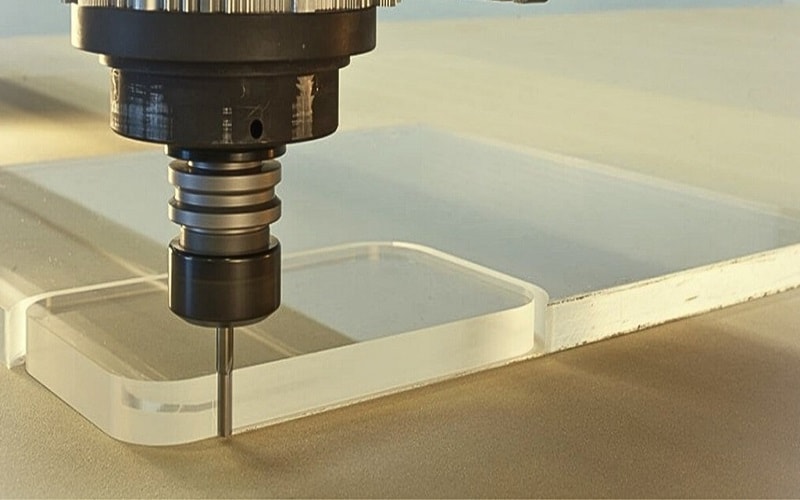
CNC plastic machining involves the use of CNC machines to precisely cut and shape raw plastic materials. This subtractive method removes unwanted geometry from the plastic, transforming it into complex components with high precision. CNC machining typically utilizes 3-, 4-, and 5-axis machines to achieve intricate designs and tight tolerances.
One of the primary advantages of CNC plastic machining is its adaptability compared to metal machining. The process offers tighter tolerances and a broader range of polymer materials than other methods like 3D printing and injection molding.
This makes CNC machining particularly cost-effective for low-volume manufacturing, providing an economical alternative to injection molding, especially for rapid prototyping and small-scale production runs.
CNC plastic machining is widely used across various industries due to its flexibility and precision. From automotive parts to medical devices, the applications are vast and varied, making it a preferred choice for engineers and manufacturers seeking reliable and durable plastic components.
Popular CNC Machined Plastics
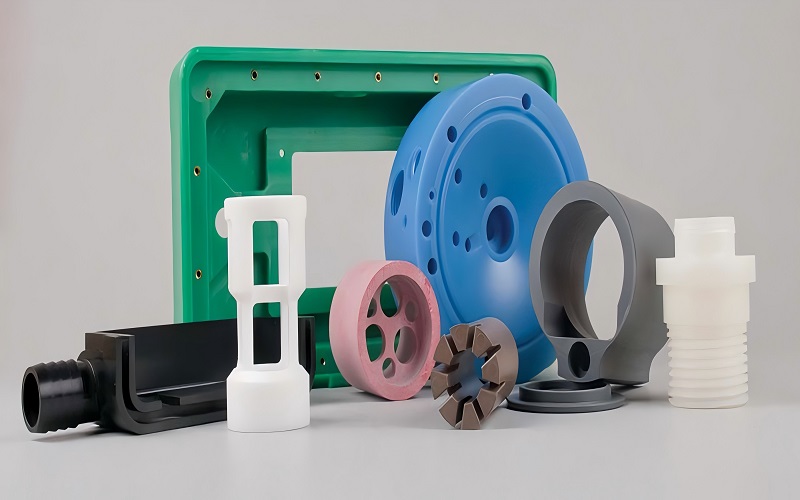
When it comes to CNC plastic machining, certain plastics stand out due to their unique properties and versatility. The most commonly used plastics include:
- ABS
- PEEK
- Polycarbonate
- HDPE
Each of these materials offers distinct advantages, making them suitable for various applications.
Understanding the key properties of these popular plastics can help you make informed decisions for your projects. In the following sections, we’ll delve into the specifics of each material, highlighting their strengths and common uses in CNC machining.
ABS (Acrylonitrile Butadiene Styrene)
ABS is a versatile engineering plastic known for its low weight, good machinability, and high impact resistance. Its excellent heat resistance and abrasion resistance make it a popular choice for rapid prototyping and manufacturing electronic enclosures. ABS can be easily processed through CNC machining, allowing for precise cutting and engraving using a CNC milling machine.
This durable plastic is often used in applications where strength and reliability are crucial. Its ability to withstand physical stress and its compatibility with various surface treatments make it an ideal choice for a wide range of products, from consumer electronics to automotive parts.
PEEK (Polyether Ether Ketone)
PEEK is highly regarded in high-performance sectors such as aerospace and medical due to its exceptional mechanical strength and chemical resistance. This engineering plastic can withstand high temperatures and harsh chemical environments, making it ideal for demanding applications.
In addition to its mechanical properties, PEEK offers biocompatibility, making it suitable for medical implants and devices. Despite its poor UV resistance and susceptibility to certain chemicals, PEEK’s resilience and durability make it a reliable choice for critical components in various industries.
Polycarbonate (PC)
Polycarbonate is prized for its combination of transparency and toughness, making it a popular choice for safety equipment and optical applications. Its high impact resistance and stiffness ensure that it can withstand significant physical stress without deforming.
Common applications for polycarbonate include optical disks, safety glasses, and mobile phone casings. However, it is vulnerable to hydrocarbon wear and prolonged UV exposure, which can lead to yellowing over time. Despite these drawbacks, polycarbonate remains a versatile and durable plastic for many CNC machining projects.
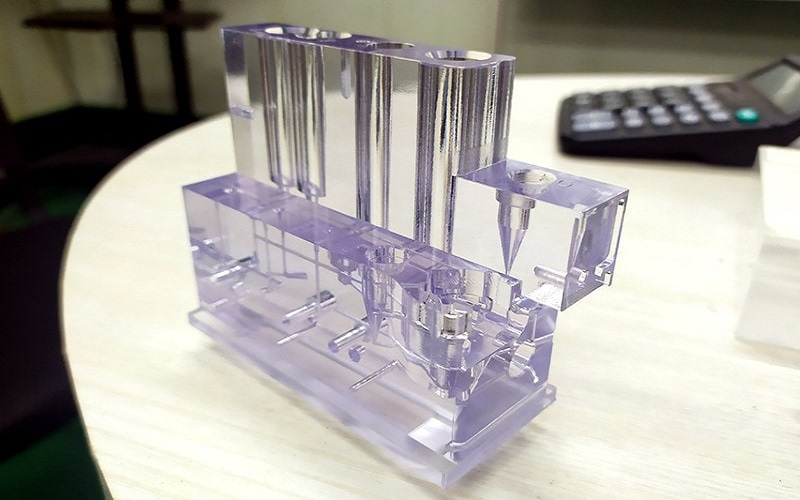
HDPE (High-Density Polyethylene)
HDPE is known for its strength, chemical resistance, and excellent electrical insulation. This durable plastic is widely used in applications that require resistance to moisture and chemicals, such as fluid systems and packaging.
One of HDPE’s key benefits is its flexibility, making it suitable for weight-sensitive or electrically sensitive applications. However, it has poor UV resistance and is susceptible to stress cracking, which should be considered when selecting this material for outdoor or high-stress environments.
Key Factors in Selecting CNC Plastics
Selecting the right plastic material for CNC machining requires careful consideration of various factors. Functionality, appearance, and durability are crucial elements that can significantly impact the success of your project.
Different plastics exhibit unique machinable properties, and understanding these differences is essential to avoid dimensional inaccuracies and other issues. Key factors to consider include mechanical properties, chemical resistance, and thermal properties, which will be discussed in the following subsections.
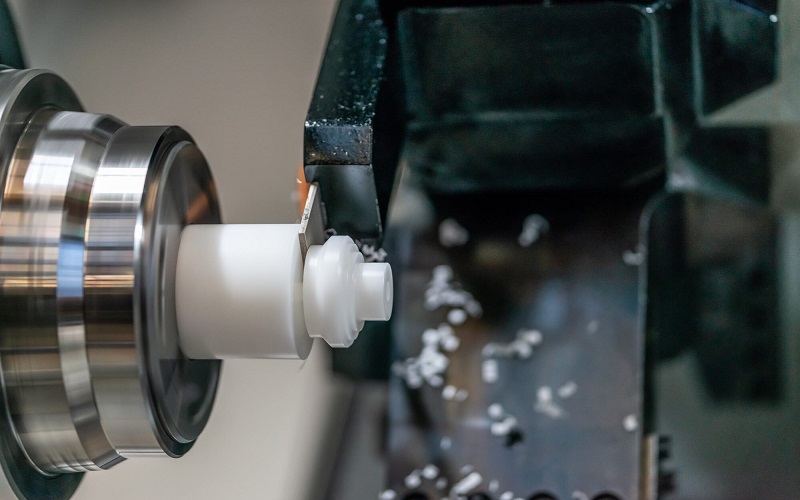
Mechanical Properties
Mechanical properties like impact strength and dimensional stability are vital for effective use of CNC machined plastics. Hardness and strength must match the application’s requirements to ensure optimal performance.
Techniques such as reinforcing with fillers and applying surface treatments can significantly enhance the mechanical properties of plastic materials. Fillers like glass fibers can improve wear resistance, durability, and thermal stability, making the material more suitable for high-stress applications.
Chemical Resistance
Chemical resistance is a critical factor in selecting CNC plastics, especially for applications involving exposure to harsh chemicals or corrosive environments. Some plastics, such as nylon and acrylic, can absorb moisture, leading to dimensional changes and reduced stability, impacting their corrosion resistance.
Understanding the chemical resistance properties of different plastics can help you choose the most suitable material for your specific needs. This will ensure that your machined parts maintain their integrity and performance over time.
Thermal Properties
Managing heat is crucial in CNC machining of plastics to prevent dimensional shifts and stress cracking due to thermal expansion. Thermal expansion can affect the dimensional stability of plastic parts, making it essential to consider the material’s heat resistance.
Incorporating fillers like glass fibers or carbon can enhance the thermal stability of plastics, ensuring that your machined parts can withstand high temperatures and maintain their integrity.
Advantages of CNC Plastic Machining
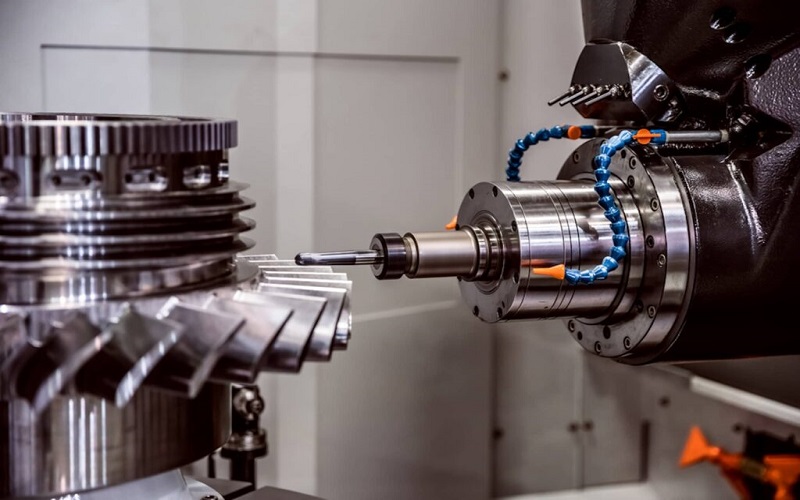
CNC plastic machining offers numerous advantages, making it a preferred choice for manufacturing complex components. Its versatility allows for the use of various rigid materials, including thermoplastics, thermosets, and elastomers. Engineers favor CNC machining for its compatibility with a wide range of plastics and the ability to produce high-quality parts with tight tolerances.
The process is also cost-effective, especially for low-volume manufacturing, and provides faster lead times compared to other methods like injection molding. These benefits make CNC plastic machining an excellent option for both prototyping and mass production.
Precision and Accuracy
CNC machining can achieve incredibly tight tolerances, often as precise as +/- 0.0005 inches, depending on the material used. The use of multi-axis CNC machines enhances precision by allowing multiple angles and complex shapes to be machined in a single setup.
Selecting the right cutting tools is crucial for achieving high-quality results. Proper tool geometry and coatings can significantly improve the dimensional accuracy and surface finish of the final product.
Cost-Effectiveness
The complexity and size of the part impact the cost of CNC plastic machining. Additionally, the type of plastic used also plays a role in determining the price. HDPE, for example, is an affordable and durable choice, making it a cost-effective option for various applications.
CNC machining provides significant low cost benefits for both low and high-volume production runs due to its efficiency and precision. This makes it an economical alternative for manufacturers looking to optimize their production processes through cnc machining services.
Versatility
CNC plastic machining enables the production of complex geometries and custom parts, making it versatile for a variety of applications. Good machinability allows for intricate designs and custom configurations to be developed efficiently, enhancing the versatility of plastic cnc machining, machining plastics, and CNC plastics.
This adaptability makes CNC machining an excellent choice for projects requiring unique and precise components. The ability to work with a wide range of plastic materials further extends its application potential.
Industries Leveraging CNC Plastic Machining

CNC plastic machining finds extensive applications across various industries due to its precision and versatility. From the automotive and medical sectors to consumer electronics, the adaptability of CNC machining to different plastic materials allows for the production of high-quality, durable components.
Industries such as aerospace, marine, and energy also benefit from CNC plastic machining, utilizing it for complex parts that require tight tolerances and superior mechanical properties. The following subsections will delve into specific industries and their use of CNC machined plastic parts.
Automotive Industry
In the automotive industry, CNC machined plastics are used to manufacture a variety of components, including dashboards, instrument panels, and other interior and exterior parts. Polymers like ABS, PVC, and polycarbonate offer impact resistance, low weight, and durability, making them ideal for such applications.
The precision and reliability of CNC machining ensure that these automotive parts meet the stringent quality standards required for vehicle safety and performance. This has made CNC plastic machining an indispensable tool in the automotive sector.
Medical Devices
CNC machined plastics play a crucial role in the medical industry, where biocompatible materials are essential for instruments and implants. Plastics like polyethylene, ABS, and acrylic are commonly used to manufacture medical devices due to their safety and effectiveness.
The precision of CNC machining ensures that medical devices meet the high standards required for patient safety. This technology is vital for producing components such as surgical instruments, dental implants, and diagnostic equipment.
Consumer Electronics
The consumer electronics industry relies heavily on CNC machining for creating durable, precise housings and casings for devices like mobile phones, laptops, and tablets. The precision achieved through CNC machining is vital for the assembly and functionality of electronic components, ensuring that they fit together perfectly and operate reliably.
By using CNC machined plastics, manufacturers can produce high-quality electronic devices that meet consumer expectations for durability and performance.
Best Practices for CNC Plastic Machining
Achieving the best results in CNC plastic machining requires adhering to best practices tailored to the unique properties of plastics. This includes careful consideration of tool selection, heat management, and material handling to maintain the integrity and precision of the final parts.
Understanding the sensitivity of different plastics to moisture and chemicals is also critical. The following subsections will provide detailed guidance on these best practices.
Tool Selection
Using the correct cutting tools is essential for effective CNC plastic machining. Proper tool geometry and special coatings can significantly enhance cutting effectiveness and surface quality. This reduces tool wear and improves the finish quality of the machined parts.
Selecting tools designed specifically for the plastic being machined ensures optimal performance and longevity, contributing to the overall success of the machining process.
Heat Management
Managing heat during CNC plastic machining is crucial to prevent part rejection and maintain dimensional stability. Techniques such as using coolant, flood cooling, or air cooling can effectively regulate temperatures and reduce the risk of warping. Maintaining low temperatures during machining helps prevent stress cracking and ensures that the final parts meet the required specifications.
Material Handling
Maintaining the dimensional stability and quality of plastic materials during CNC machining depends on proper handling and storage. These factors are crucial for achieving optimal results. Preconditioning materials and ensuring effective heat removal help preserve the integrity of the machined parts.
Incorrect handling techniques can introduce stress and deformation, resulting in out-of-tolerance parts. Therefore, careful material handling is essential for achieving the best results in CNC plastic machining.
Customizing CNC Plastic Parts
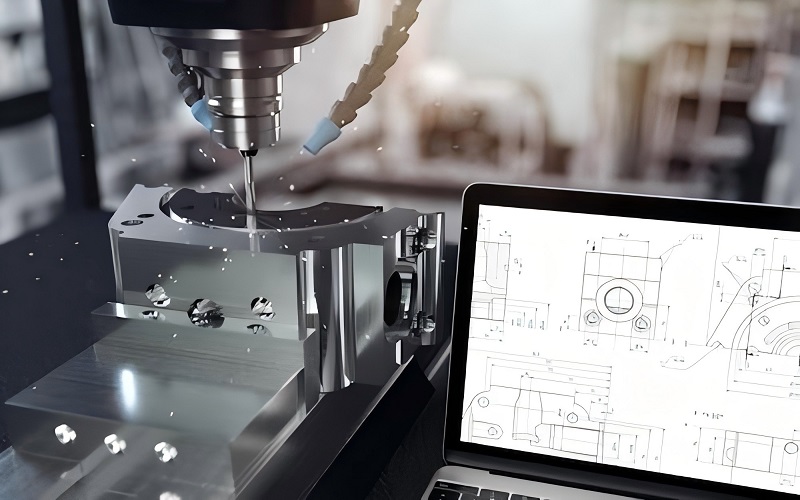
Customization in CNC plastic machining is vital for tailoring material properties to specific application requirements. Techniques such as surface treatments and reinforcement with fillers can enhance the performance of CNC machined plastics, making them suitable for demanding applications.
These customization methods can result in parts with improved strength, durability, and other desired properties, ensuring they meet the specific needs of various industries.
Surface Treatments
Applying surface treatments to CNC machined plastics can significantly improve their appearance, wear resistance, adhesion, and paintability. Techniques like vapor polishing can enhance the surface finish, providing both aesthetic and functional benefits.
These treatments make the plastic parts more suitable for a wider range of applications, ensuring they meet the desired specifications and performance standards.
Reinforcement with Fillers
Incorporating fillers into CNC machined plastics can enhance their mechanical properties, thermal stability, and wear resistance. Fillers like glass fibers are commonly used to improve the strength and durability of the plastic parts.
These reinforcements make the materials more suitable for high stiffness applications, extending their range of use and ensuring reliable performance in demanding environments.
Environmental Impact and Sustainability
The environmental impact of CNC plastic machining can be mitigated through recycling and the use of eco-friendly alternatives. Recycling CNC machined plastics is crucial for minimizing waste and reducing the ecological footprint of manufacturing processes.
Eco-friendly alternatives such as biodegradable and bio-based plastics offer additional benefits, reducing long-term pollution and contributing to sustainability efforts. The following subsections will explore these topics in more detail.
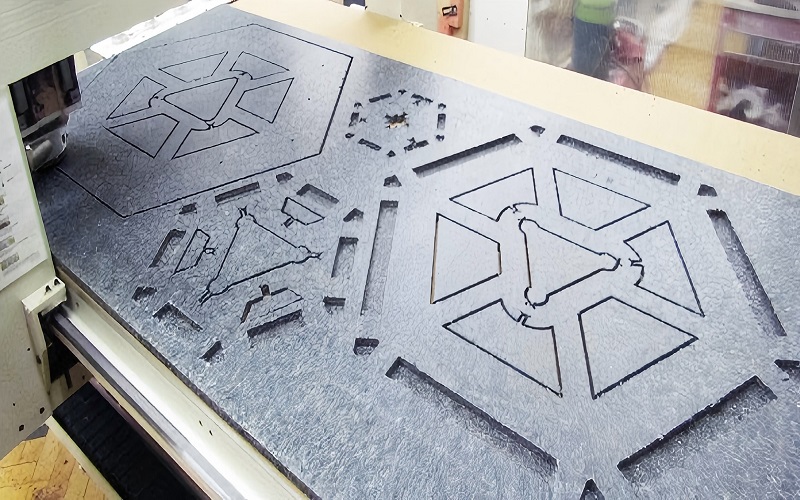
Recycling CNC Plastics
Recycling CNC machined plastics is essential for environmental sustainability. Methods like mechanical reprocessing and closed-loop recycling allow for the repeated use of plastics with the same chemical composition, minimizing waste and reducing environmental harm.
Recycling extends the lifecycle of plastic materials and lowers energy consumption, making it a cost-effective and environmentally friendly solution.
Eco-Friendly Alternatives
Bio-based and biodegradable plastics are increasingly being used as eco-friendly alternatives to traditional plastics. These materials are derived from renewable sources and are designed to decompose more quickly, reducing long-term pollution and landfill waste.
By incorporating these sustainable materials into CNC plastic machining, manufacturers can reduce their environmental impact and contribute to a more sustainable future.
Summary
In summary, CNC plastic machining offers numerous advantages, from precision and cost-effectiveness to versatility and customization. Understanding the key factors in selecting the right plastic materials and adhering to best practices can significantly enhance the quality and performance of CNC machined parts.
By leveraging the benefits of CNC plastic machining and considering environmental sustainability, manufacturers can produce high-quality, reliable components that meet the demands of various industries. Whether you’re working in automotive, medical, or consumer electronics, CNC plastic machining can provide the solutions you need for your projects.
Frequently Asked Questions
What are the key properties of ABS used in CNC machining?
The key properties of ABS used in CNC machining include low weight, good machinability, impact resistance, and high heat resistance, making it suitable for applications such as rapid prototyping and electronic enclosures.
Why is PEEK favored in high-performance sectors?
PEEK is favored in high-performance sectors due to its exceptional mechanical strength, chemical resistance, and capability to withstand high temperatures, making it ideal for demanding applications in industries such as aerospace and medical.
How does CNC machining benefit the automotive industry?
CNC machining benefits the automotive industry by providing impact-resistant, lightweight, and durable plastics for manufacturing components like dashboards and instrument panels. This enhances overall vehicle performance and safety.
What are the best practices for managing heat in CNC plastic machining?
The best practices for managing heat in CNC plastic machining include utilizing coolants, flood cooling, or air cooling to effectively regulate temperatures and prevent issues such as warping or stress cracking. Implementing these methods ensures optimal machining performance and enhances the quality of the final product.
What are the environmental benefits of recycling CNC plastics?
Recycling CNC plastics significantly extends their lifecycle, reduces energy consumption, and minimizes environmental harm. This process contributes to sustainability and decreases the ecological footprint associated with manufacturing.