Core cavity injection molding is fundamental in making precise plastic parts. The core shapes the inside, while the cavity forms the outside. Understanding their roles and placement techniques can significantly improve the quality of your molded products.
In this article, you’ll learn key differences, design principles, and practical tips to master core and cavity in injection molding.
Understanding Core and Cavity in Injection Molding
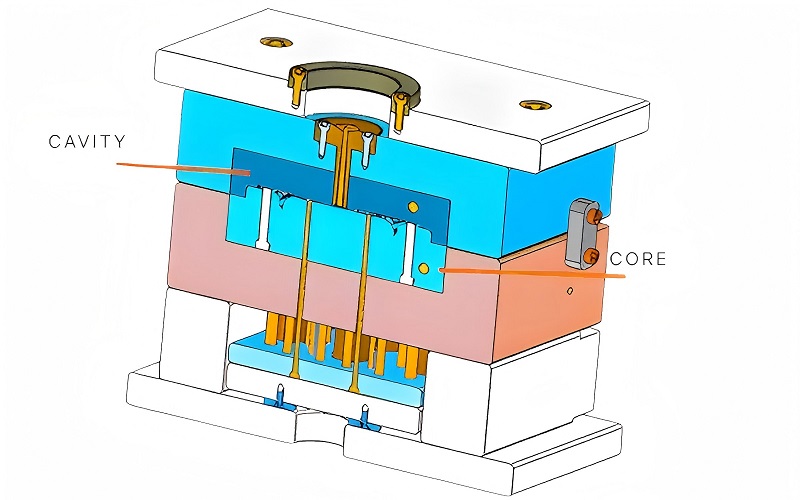
In the realm of injection molding, the core and cavity are the foundational elements that shape the final product. The core is responsible for forming the internal shape of the plastic part, while the cavity shapes its external shape. Together, they collaborate to create the overall geometry of the molded part, ensuring both internal and external precision.
The core and cavity design is a core technology in mold manufacturing, essential for producing high-quality molds. Accurate movements and a precise fit between the core and cavity during the molding process are crucial, with the cavity typically remaining stationary while the core moves and the mold cavities are carefully crafted to shape the molten plastic. Ejector pins are integrated to release the solidified part from the mold, ensuring smooth production.
This delicate dance between the core and cavity is what brings the intricate designs of modern plastic products to life.
Core vs. Cavity: Key Differences
The core and cavity each play distinct roles in the molding process, representing two halves of the overall design. The core is the male portion of the mold, creating the internal structure of the product, such as part joints and mold sleeves. Conversely, the cavity is the female portion, shaping the external form of the molding, where the mold cavity is ultimately formed.
This distinction is crucial for understanding how different parts of the mold contribute to the final product’s geometry.
Identifying Core and Cavity
Identifying the core and cavity components can be facilitated by specific markings, with cavities typically marked with ‘F’ or ‘1’ and cores with ‘R’ or ‘2’. The cavity endures higher pressures than the core, which generally withstands lower pressures.
Observing how the components fit together and understanding their construction can further aid in distinguishing between the assembled core and cavity.
Core and Cavity Placement Techniques
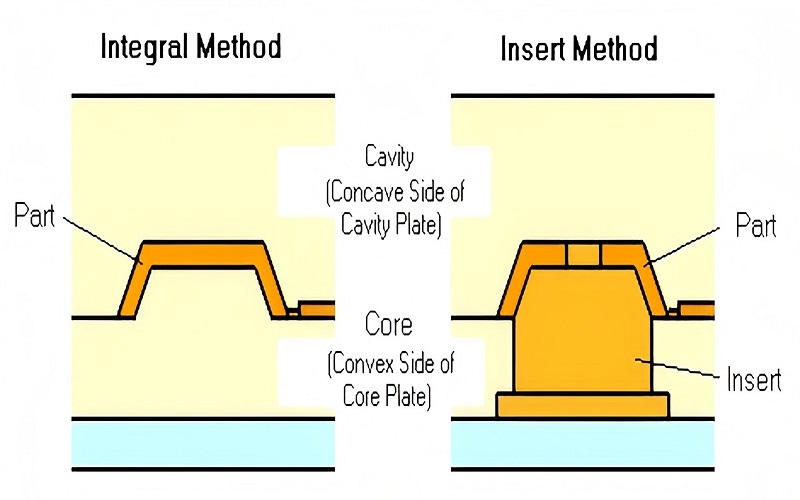
Effective core and cavity placement is crucial for achieving precise dimensions and enhancing productivity in the molding process. The collaboration between core and cavity forms the complete geometry of plastic parts, making their accurate placement a vital component of mold design, particularly when selecting the appropriate mold type.
This section will explore various techniques for core and cavity placement, including visual inspection, structural analysis, and material and weight considerations to choose core and cavity components effectively.
Visual Inspection
Visual inspection is a fundamental technique for recognizing the core and cavity by analyzing surface details and specific markings. By observing the shape of the product, the mating surfaces, and positioning pins, one can differentiate between the core and cavity.
This method relies on keen observation and a thorough understanding of the mold’s external and internal visible features, ensuring the mold is ready when it mold opens for part ejection.
Structural Analysis
Structural analysis plays a critical role in confirming the positions of core and cavity components. Parting lines and dowel pins offer different shapes that assist in guiding components into precise alignment.
Guide pillars and guide bushes ensure the alignment of the core and cavity during each injection molding cycle, allowing the mold to fill with molten plastic accurately. Techniques such as positioning, clamping, and pressure tests further enhance alignment accuracy. Ejection pins are strategically placed to facilitate smooth part removal when the mold opens, minimizing defects.
Material and Weight Considerations
Material density variations and weight differences between the core and cavity can be key factors in identifying their respective roles in the mold. Understanding the material characteristics and weight variations is vital for effective core and cavity design in injection molding applications.
These considerations ensure that the mold components function correctly under the rigors of the molding process, despite the high cost of precision manufacturing, and support the durability of the mold parts.
These techniques collectively ensure precise core and cavity placement, optimizing the injection molding process for high-quality outcomes.
Manufacturing Processes for Core and Cavity
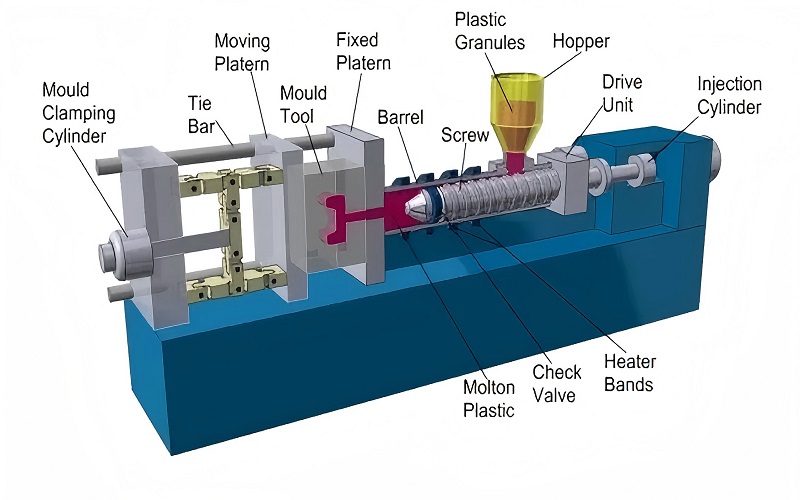
The manufacturing processes for core and cavity components involve a series of precise steps, including:
- CNC machining
- EDM
- Polishing
- Assembly
- Manufacture
Innovative techniques such as 3D printing and advanced machining enhance the precision and complexity of core and cavity designs. These advancements significantly improve the efficiency and quality of the molds produced, making them essential for modern injection molding.
Trial molding is a critical step in the manufacturing process, serving to identify and address potential defects before mass production starts. This process ensures that the mold operates correctly and produces products that meet quality standards. By assessing the functionality of the mold’s injection and ejection systems, trial molding helps detect any potential issues before full-scale production begins.
Material Preparation and Milling
Material prepared is the first step in manufacturing core and cavity components. Selecting the appropriate type and size of materials is essential, with initial machining performed on a milling machine to drill cooling holes, threading holes, and other necessary features.
Precision in this initial stage ensures that the core and cavity components meet the design requirements.
CNC Machining and Finishing
CNC machining is crucial for achieving dimensional accuracy and forming complex shapes in core and cavity components. This process allows for the machining of intricate features such as small holes and intricate contours, which are difficult to achieve with traditional methods.
CNC finishing is essential for mold cores. It is particularly important for cavities that demand higher precision.
Heat Treatment and Polishing
Heat treatment enhances the hardness and wear resistance of core and cavity components, making them more durable for the injection molding process. Nitriding, a specific heat treatment process, can improve the lifespan of the mold.
Surface polishing is also crucial, providing a smooth finish that enhances the quality of the polished plastic parts produced.
Design Principles for Core and Cavity
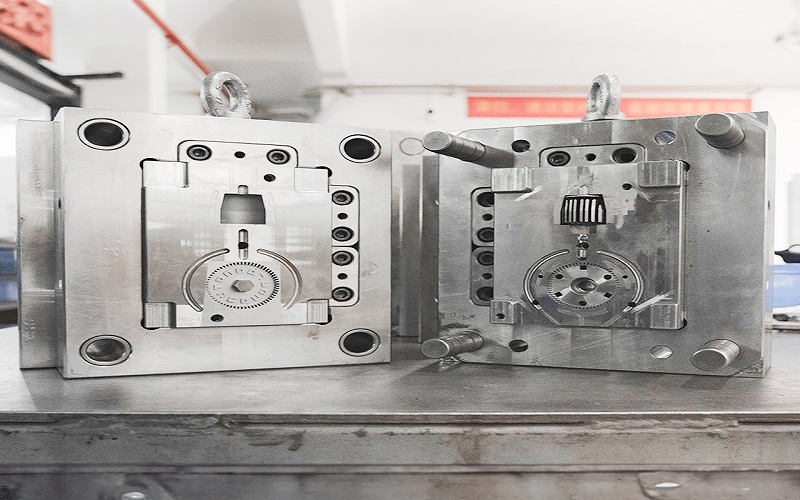
The arrangement of core and cavity significantly influences the precision and efficiency of the injection molding process. Effective core and cavity designs prioritize minimizing complexity while ensuring structural integrity to withstand the rigors of injection molding.
This section will delve into key design principles, focusing on thickness and strength considerations, as well as safety dimensions and tolerances.
Thickness and Strength Considerations
The thickness of mold components must balance weight, strength, and thermal efficiency to resist deformation under injection pressures. Designers should aim for uniform wall thickness to minimize defects such as sink marks and warping.
Using ribs can enhance the structural integrity of tall walls while still adhering to the recommended thickness ratios.
Safety Dimensions and Tolerances
Setting appropriate safety distances in mold dimensions can prevent collisions and enhance the longevity of the mold. Maintaining tight tolerances in mold design is essential to prevent production issues and ensure the final product meets specifications in the available space.
These considerations influence both mold performance and production costs.
Material Selection for Core and Cavity
Different materials used for core and cavity can vastly affect the overall performance and durability of the mold in injection molding applications. Selecting the right type and size of materials is crucial for the effectiveness of mold cores and cavities.
This section will explore common materials and specialized alloys used for metal cores and cavities, highlighting their properties and applications.
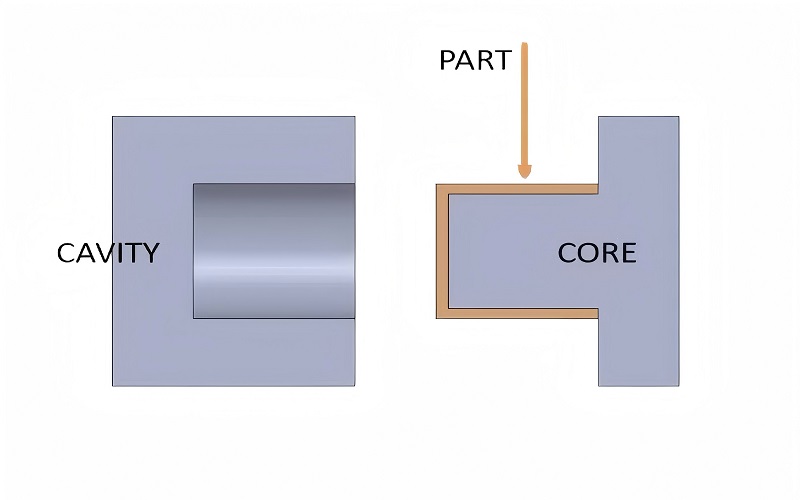
Common Materials
Common materials used for core and cavity in injection molding include P20, En 30B, S7, H13, or 420SS grade steel. P20 steel is often favored for its balance of hardness and cost-effectiveness.
NAK80 offers excellent electrical discharge machining and polishing properties, making it ideal for high transparency applications. S7 steel is known for its high shock resistance and is used in molds requiring tougher applications.
Specialized Alloys
Specialized alloys such as 2316 and 2344 are commonly utilized in injection molding for their enhanced properties. Alloy 2344 is particularly suitable for high production volumes due to its cost-effectiveness, with a mold life reaching up to 1 million cycles.
Importance of Cooling Systems
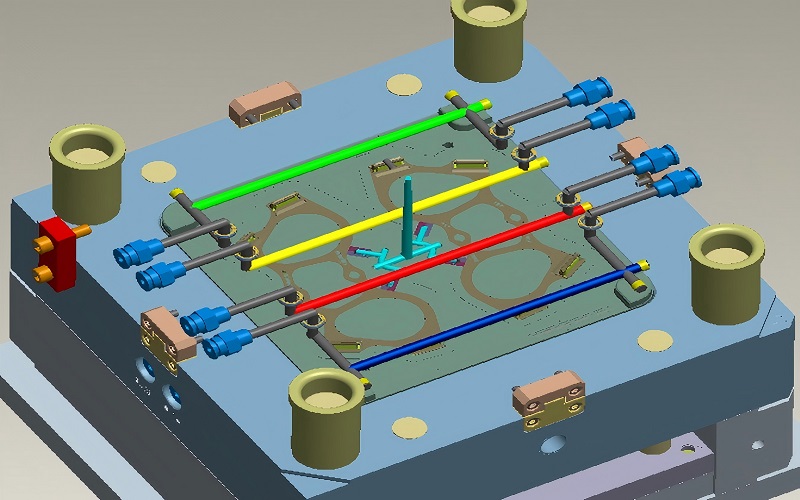
Cooling systems are critical in injection molding as they control the temperature of the mold, affecting the quality of the final product. Efficient cooling systems prevent defects in plastic parts caused by uneven temperature distribution.
This section will discuss the design of efficient cooling circuit and their impact on cycle time.
Designing Efficient Cooling Circuits
Efficient cooling circuits should prioritize turbulent flow in cooling channels for optimal temperature regulation. Conformal channels that follow the mold’s contours allow for more effective heat removal compared to traditional straight-line cooling, which cools more efficiently and is also considered cool.
The number and placement of cooling channels should be optimized to ensure effective temperature control across the mold.
Impact on Cycle Time
Properly designed cooling systems can significantly decrease the cycle time required for injection molding. Maintaining uniform cooling can prevent defects and improve overall production speed.
Ensuring Quality with Trial Molding
Trial molding is essential for verifying the machining quality and performance of the mold. Accurate placement techniques for core and cavity casting are crucial for producing high-quality molded parts.
This section will cover testing and adjustments, as well as troubleshooting common issues during trial molding.
Testing and Adjustments
During the trial molding process, critical aspects such as the mold’s gating system, cooling waterway functionality, and product design compliance are thoroughly checked. Mold polishing is important in mold manufacturing because it enhances surface quality and meets roughness requirements.
Adjustments may include modifying machine process parameters based on initial trial outcomes.
Troubleshooting Common Issues
During the trial molding process, it is critical to identify and address any issues to maintain product quality. Adjusting the injected injection mold speed can help mitigate problems such as short shots or incomplete molds, ensuring easy ejection.
When issues are discovered, adjustments and repairs should be made promptly to ensure smooth production.
Advanced Techniques in Core and Cavity Manufacturing
Advanced techniques in core and cavity manufacturing significantly enhance precision, efficiency, and the ability to create intricate designs. Employing these techniques not only improves product quality but also reduces manufacturing time and costs.
This section will explore Electrical Discharge Machining (EDM) and Wire Cutting Technology.
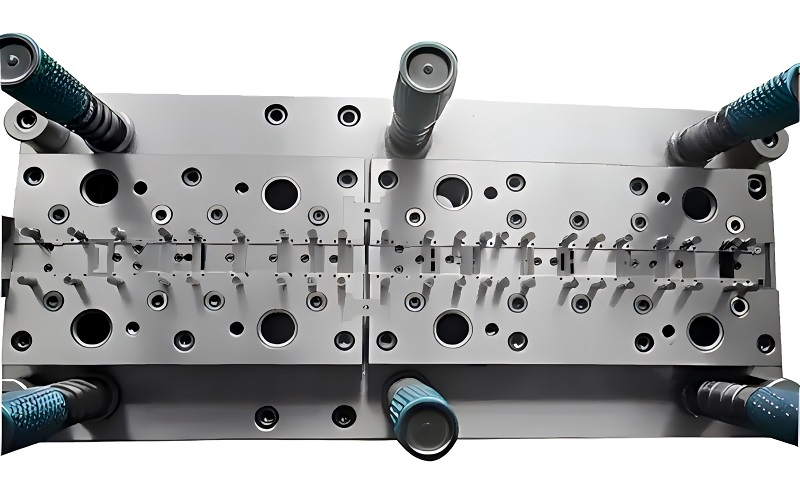
Electrical Discharge Machining (EDM)
Electrical Discharge Machining (EDM) is a powerful technique used to create fine grooves and narrow slots in core and cavity components. Unlike traditional machining methods, EDM works without direct contact, thereby minimizing mechanical stress on the workpiece.
This allows for the machining of complex shapes and intricate details, providing greater design flexibility and precision in the injection molding process.
Wire Cutting Technology
Wire cutting technology excels in creating highly accurate slots and holes in molds through the controlled movement of a thin wire. This method is particularly effective for producing precise cuts in hard materials, making it ideal for complex mold designs.
By allowing for high precision in shaping intricate mold features, wire cutting technology enhances the overall functionality and performance of the mold.
Summary
Mastering core cavity injection molding involves understanding the distinct roles of core and cavity, the importance of precise placement techniques, and the advanced manufacturing processes that bring these components to life.
Proper core and cavity design, material selection, and cooling systems are essential for creating high-quality molds that meet stringent production standards. Employing advanced techniques like EDM and wire cutting technology further enhances precision and efficiency, reducing manufacturing time and costs.
In conclusion, achieving excellence in injection molding requires a comprehensive approach that integrates innovative technologies, meticulous design principles, and thorough trial molding processes. By applying the knowledge and techniques outlined in this guide, manufacturers can optimize their molding processes, produce superior plastic parts, and maintain a competitive edge in the industry.
Frequently Asked Questions
What is the primary difference between the core and cavity in injection molding?
The primary difference between the core and cavity in injection molding is that the core defines the internal features of the molded part, whereas the cavity shapes its external configuration. Therefore, both components are essential for creating the complete form of the final product.
How can I identify the core and cavity components in a mold?
To identify core and cavity components in a mold, look for markings where cavities are usually labeled with ‘F’ or ‘1,’ and cores with ‘R’ or ‘2.’ Additionally, examining how the components fit together can provide further clarity.
Why are cooling systems important in injection molding?
Cooling systems are essential in injection molding as they regulate the mold temperature, ensuring uniform cooling which enhances product quality and minimizes defects. Proper temperature control is vital for achieving optimal results in the manufacturing process.
What are some common materials used for core and cavity in injection molding?
P20, En 30B, S7, H13, and 420SS grade steel are commonly used materials for the core and cavity in injection molding, each chosen for their unique properties and suitability for various applications.
What advanced techniques are used in core and cavity manufacturing?
Advanced techniques such as Electrical Discharge Machining (EDM) and Wire Cutting Technology are utilized in core and cavity manufacturing to improve precision and efficiency in the production of intricate mold designs. These methods enable the creation of complex geometries that are critical for high-quality manufacturing.