Custom plastic injection molding is a precise manufacturing process where molten plastic is injected into molds to create specific parts.
This method is favored for its efficiency and ability to produce intricate designs at high volumes.
In this article, we’ll explain how custom plastic injection molding works, its benefits, and its uses across different industries.
Understanding Custom Plastic Injection Molding
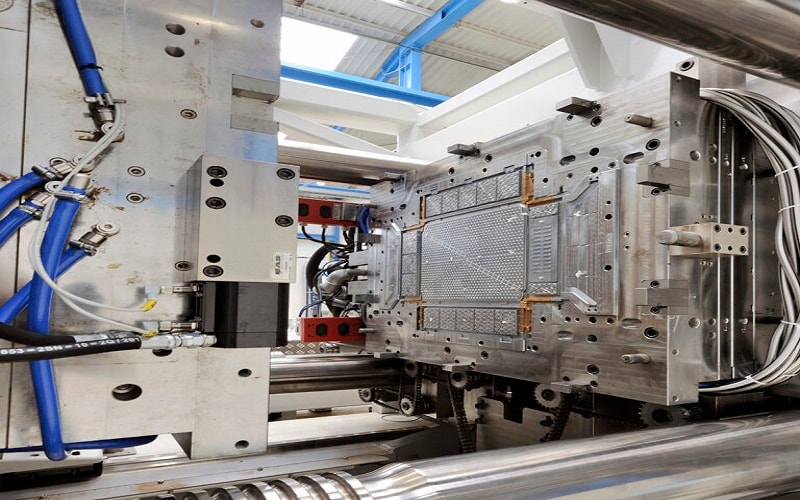
Custom plastic injection molding is a manufacturing process that creates billions of high-quality parts annually. This process involves injecting molten plastic into a mold cavity, where it cools and solidifies into the desired shape. The versatility and efficiency of plastic injection molding make it an appealing choice for producing custom plastic parts.
We’ll delve into the plastic injection molding process, its advantages, and its common applications in various industries.
The Plastic Injection Molding Process
The plastic injection molding process begins with loading resin pellets into a heated barrel, where they are melted and prepared for injection. Once molten, the plastic is injected into a mold cavity under high pressure, filling the entire space and taking the shape of the mold.
This is the main technique for manufacturing custom plastic parts, ensuring precision and repeatability. The cycle includes essential steps such as closing the mold, injecting the plastic, cooling, and ejecting the finished part.
After the plastic cools and solidifies, the molded parts are removed from the mold for further processing, packaging, or delivery.
Scientific molding techniques optimize the production process by documenting and refining each manufacturing stage, ensuring tight tolerances and repeatable quality throughout production.
This comprehensive feedback helps identify potential issues in mold design, enhancing overall efficiency.
Advantages of Custom Plastic Injection Molding
Custom plastic injection molding is known for its versatility, reliability, and straightforward approach, making it an excellent choice for numerous applications. The high production speed and accuracy of injection molding services contribute significantly to its advantages. Custom parts can be tailored to meet specific requirements, enhancing their functionality and performance.
Customizing plastic parts in various shapes, materials, additives, colors, and finishes makes this manufacturing method highly versatile.
After the initial setup, custom plastic parts manufacturing achieves remarkable production speeds, leading to enhanced efficiency.
Additionally, designing custom parts reduces the need for off-the-shelf components, simplifying assemblies and saving time and costs. Improved wear resistance extends product lifespan and reduces replacements.
Common Applications of Custom Plastic Parts
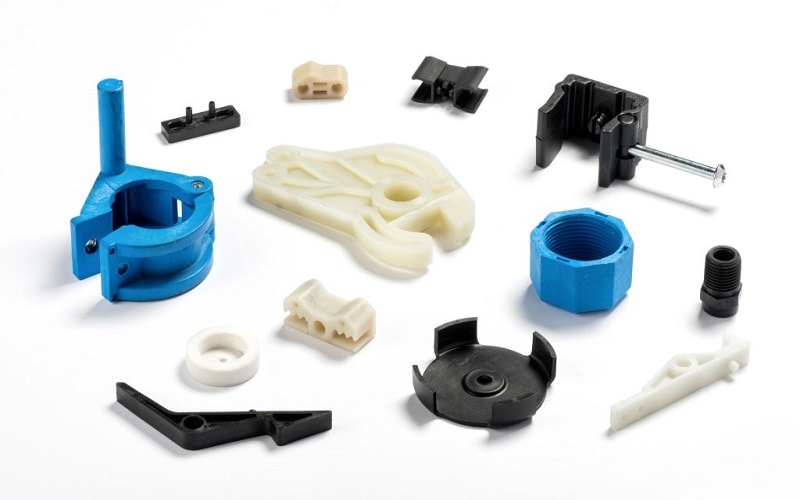
Custom plastic injection molding is widely used in industries such as automotive, medical devices, and consumer products.
The automotive industry, for example, relies on custom-injected molded plastic parts for their durability and precision in both interior and exterior applications.
ABS, a common material used, is utilized in automotive parts, electronic housings, and consumer goods like toys and kitchen appliances.
In the medical field, custom plastic parts are essential for creating intricate components that meet strict regulatory standards. Consumer products also benefit from the versatility of custom plastic injection molding, allowing for the creation of high-quality parts that meet specific market demands. The ability to produce identical parts with consistent quality makes this process ideal for various applications.
Key Materials Used in Plastic Injection Molding
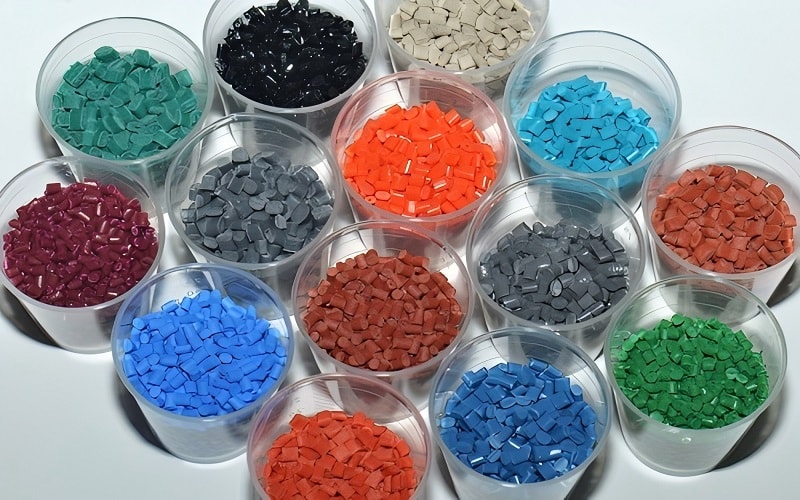
The choice of materials is crucial in plastic injection molding, as it directly impacts the performance and durability of the final product. Thermoplastic materials are a preferred choice due to their recyclability and ability to be shaped into complex designs.
We’ll explore some of the key materials used in the plastic injection molding process, including High-Density Polyethylene (HDPE), Acrylonitrile Butadiene Styrene (ABS), and Polypropylene (PP).
High-Density Polyethylene (HDPE)
High-Density Polyethylene (HDPE) is known for its good strength-to-weight ratio, high tensile strength, and high impact resistance. It also boasts a high melting point, making it suitable for applications requiring high heat resistance.
HDPE is commonly used in products like plastic pipes and cutting boards due to its durability and efficiency. Its ability to handle complex geometries while maintaining high strength makes it an ideal choice for various applications.
Acrylonitrile Butadiene Styrene (ABS)
Acrylonitrile Butadiene Styrene (ABS) is favored in manufacturing due to its robust impact resistance, providing enhanced durability for a variety of applications. This makes ABS a preferred choice in the automotive industry for parts requiring high durability and impact resistance.
It is also widely used in consumer products, from electronic housings to toys, thanks to its strength and versatility.
Polypropylene (PP)
Polypropylene (PP) is valued for its chemical resistance, food safety, and low cost. It has a high strength-to-weight ratio, making it suitable for a wide range of applications. PP is commonly used in the automotive, medical, and consumer goods industries due to its versatility and cost-effectiveness.
Its wear resistance further enhances its appeal for various manufacturing needs.
Cost-Effective Manufacturing Processes
Plastic injection molding is renowned for its efficiency and ability to produce high volumes of parts at a lower cost. Once the initial setup is complete, the production rates are rapid, significantly improving efficiency.
We’ll examine how efficient mold design and economies of scale contribute to the cost-effectiveness of the injection molding process.
Reducing Costs with Efficient Mold Design
Efficient mold design is crucial for reducing production costs in plastic injection molding. Selecting materials that match the required strength and functional properties of the final product helps manufacturers minimize defects like warping and sink marks.
Using design for manufacturing principles can significantly lower mold production costs and enhance overall production efficiency.
Economies of Scale in Injection Molding
Economies of scale play a significant role in the cost-effectiveness of injection molding. As production volumes increase, the per-unit cost of manufacturing each part decreases.
This reduction in per-unit costs allows manufacturers to spread fixed costs over a larger number of parts, leading to significant cost savings and higher overall profitability.
High-volume production runs in injection molding contribute to considerable cost savings. This efficiency makes it a preferred choice for many manufacturers.
This makes the process ideal for industries requiring large quantities of high-quality parts. By leveraging economies of scale, manufacturers can achieve cost-effective and high-quality production, catering to various market demands.
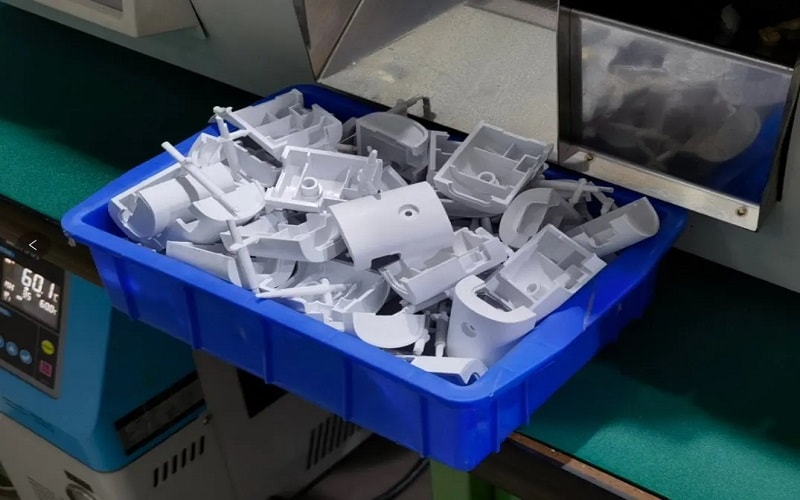
Quality Control in Custom Plastic Injection Molding
Quality control is a critical aspect of custom plastic injection molding, ensuring that each part meets the required standards and specifications. This involves multiple stages, including design review, mold inspection, in-process quality checks, and final inspection.
The following sections will explore the techniques used for quality assurance and the importance of choosing a trusted manufacturing partner.
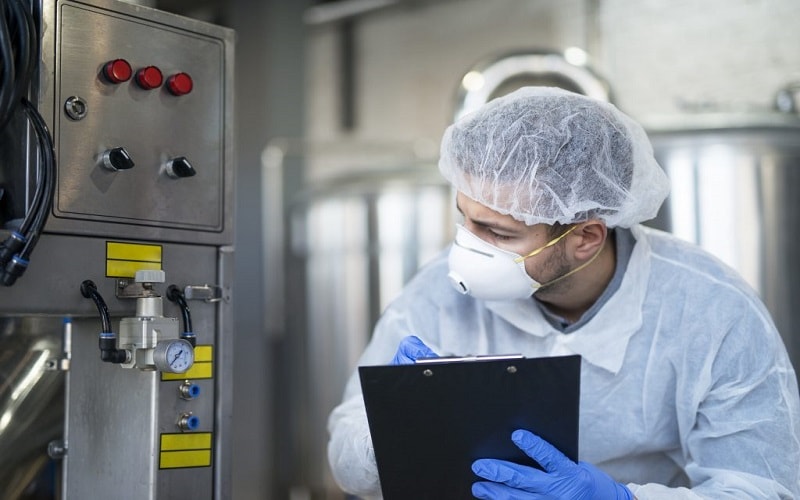
Quality Assurance Techniques
Quality assurance in plastic injection molding incorporates various techniques to ensure the reliability and performance of the final product. In-process quality control includes monitoring raw materials and the functioning of injection molding machines to prevent defects.
Visual inspections and measuring equipment are crucial during quality checks to ensure that dimensions and tolerances are met.
Effective quality assurance also involves functionality tests to ensure that parts fit together as intended. Trustworthy manufacturing partners often have extensive experience in quality control processes, enhancing product reliability and performance.
Importance of a Trusted Manufacturing Partner
Choosing a reliable manufacturing partner is essential for producing high-quality, cost-effective parts. A trusted partner ensures that designs meet requirements and adhere to industry standards, such as ISO and RoHS certifications.
Certifications like ISO 9001:2015 and ISO 13485 further validate the quality assurance processes in engineering and production, benefiting critical industries like automotive, aerospace, and medical.
Prototyping and Production Support
Prototyping is a crucial step in the product development process, allowing teams to visualize and refine designs before mass production begins. It helps ensure that products are manufacturable and meet quality standards, reducing the risk of costly production mistakes.
We’ll discuss the benefits of rapid prototyping services and the importance of engineering support for product development.
Rapid Prototyping Services
Rapid prototyping enables quick adjustments to designs, enhancing the overall development speed. This process allows for quick iterations and validations of concepts, helping to eliminate errors in the design phase and reducing the risk of costly production mistakes.
The overall benefits of rapid prototyping include faster development cycles and improved design accuracy, leading to lower production costs.
Rapid prototyping provides an accurate representation of the final product, helping teams visualize and refine their designs to ensure the end product meets the desired specifications. This iterative process is essential for producing high-quality custom plastic parts that meet market demands.
Engineering Support for Product Development
Engineering support is vital in optimizing designs for manufacturability, cost-effectiveness, and performance.
Early-stage consultation with experienced engineers can help identify and rectify weak spots, unnecessary complexity, and overlooked details in designs, avoiding costly mistakes and inefficiencies. Solid Works is commonly used design software for modifying part designs during the manufacturing process.
By offering design support to eliminate costly errors, engineering support aims to streamline custom plastic part production and maximize overall value. This collaboration ensures that the final product is not only of high quality but also cost-effective and efficient to produce.
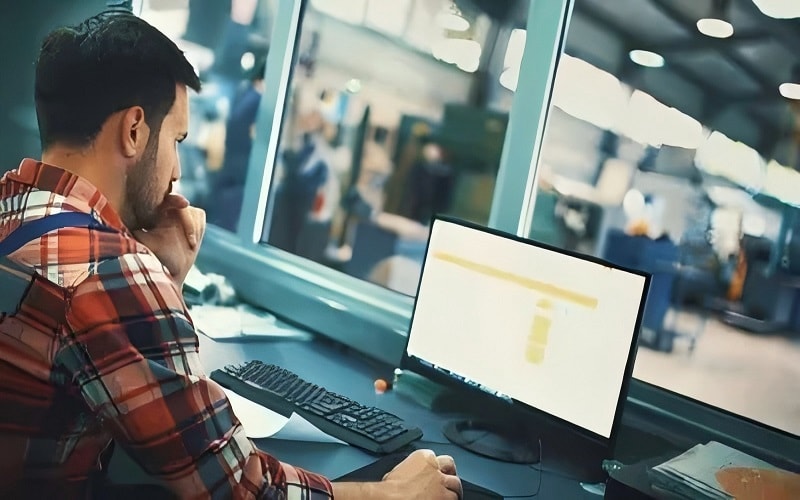
Custom Solutions for Specific Industries
Custom plastic injection molded parts find applications in various industries, from packaging and consumer goods to medical devices. A trusted manufacturing partner can help navigate the certifications required for specific industries, ensuring compliance and high-quality production.
We’ll explore the custom solutions provided for the automotive industry, medical devices, and consumer products.
Automotive Industry
The automotive industry heavily relies on custom molded plastic components for both interior and exterior applications. These parts are designed to withstand high stresses and rigorous conditions, offering durability and precision essential for vehicle safety and functionality.
Custom plastic components enhance design flexibility and reduce overall weight, contributing to the efficiency and performance of vehicles.
Medical Devices
Precision is critical in the manufacturing of medical devices, ensuring functionality and safety for patients. Custom plastic injection molding provides the necessary precision to produce intricate components required in medical devices, enhancing overall product quality.
Selecting the right materials for biocompatibility is essential to ensure that medical devices do not react adversely with body tissues. Custom solutions in medical device manufacturing lead to improved designs while meeting stringent regulatory standards.
Consumer Products
Consumer products benefit significantly from custom plastic parts that can be tailored to enhance both aesthetic appeal and functional performance. Customization allows for the creation of unique plastic components that cater to specific market demands, enhancing user experience through tailored design and functionality.
Brands can differentiate their offerings in the market by adapting plastic parts to meet aesthetic and functional requirements.
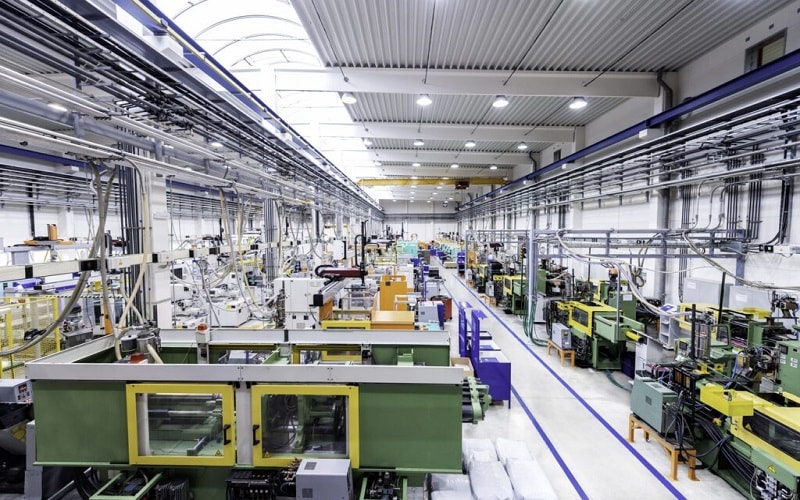
Selecting the Right Manufacturing Partner
Choosing the right manufacturing partner is crucial for the success of custom plastic injection molding projects. This section will guide you through evaluating the experience and capabilities of potential partners and highlight the importance of customer service and support in ensuring project success.
Evaluating Experience and Capabilities
When selecting a manufacturing partner, it is essential to assess their experience and capabilities to ensure they can handle your production volume, whether small runs or bulk orders. A potential partner’s production capacity should align with the project’s scale and complexity to ensure timely deliveries.
Evaluating a partner’s extensive expertise and capabilities is critical for ensuring project success. Considering these criteria will help you choose the right manufacturing partner for your custom plastic injection molding needs.
Importance of Customer Service and Support
Excellent customer service and support are vital in custom plastic injection molding, as they significantly enhance the partnership experience during the manufacturing process. Effective communication and timely responses to inquiries can ensure that any issues are promptly addressed, contributing to the overall success of the project.
A manufacturing partner that provides excellent customer service helps ensure project success and client satisfaction.
Summary
In summary, custom plastic injection molding offers a versatile, efficient, and cost-effective solution for producing high-quality parts across various industries.
From understanding the process and materials used to exploring cost-effective manufacturing techniques and the importance of quality control, this guide provides a comprehensive overview of custom plastic injection molding.
By selecting the right manufacturing partner and leveraging rapid prototyping and engineering support, businesses can achieve remarkable results. Consider custom plastic injection molding for your next project to experience the benefits of precision, customization, and efficiency.
Frequently Asked Questions
What is custom plastic injection molding?
Custom plastic injection molding is a precise manufacturing technique that involves injecting molten plastic into a mold to produce high-quality, solidified parts in various shapes. This process allows for efficient production and detailed customization of components for diverse applications.
What are the advantages of custom plastic injection molding?
Custom plastic injection molding offers high production speed, precision, complete customization, and cost savings, making it an efficient choice for manufacturing. These benefits streamline processes and enhance product quality.
What materials are commonly used in plastic injection molding?
Plastic injection molding commonly utilizes materials such as High-Density Polyethylene (HDPE), Acrylonitrile Butadiene Styrene (ABS), and Polypropylene (PP). These materials are favored for their versatility and durability in various applications.
How does rapid prototyping benefit the manufacturing process?
Rapid prototyping benefits the manufacturing process by enabling quick design adjustments, which minimizes costly production errors and enhances development speed and precision. This leads to a more efficient manufacturing cycle.
Why is it important to choose a trusted manufacturing partner?
Choosing a trusted manufacturing partner is crucial for ensuring adherence to quality standards and certifications, ultimately enhancing project success and client satisfaction. This partnership is key to delivering reliable outcomes and maintaining your reputation in the industry.