Gas assist injection molding uses pressurized gas to improve plastic part molding. This process reduces weight and enhances structural integrity. Learn how it works and its top benefits.
Understanding Gas Assist Injection Molding
Gas assisted molding is a low-pressure technique that uses pressurized nitrogen gas to improve the molding process. The three main steps include injecting the plastic melt into the mold cavity, infusing the molten plastic with nitrogen gas through gas injection points, and maintaining gas pressure during cooling.
This approach enhances structural integrity and reduces product weight through gas assisted injection molding, accommodating designs with differing wall thickness.
Initially, the molten plastic fills 70% to 95% of the mold cavity. Pressurized nitrogen gas is then injected, pushing the molten resin against the cavity walls and distributing the gas pressure evenly. This maintains the shape and quality of the part during cooling, resulting in high-quality, lightweight parts without the common defects of traditional injection molding.
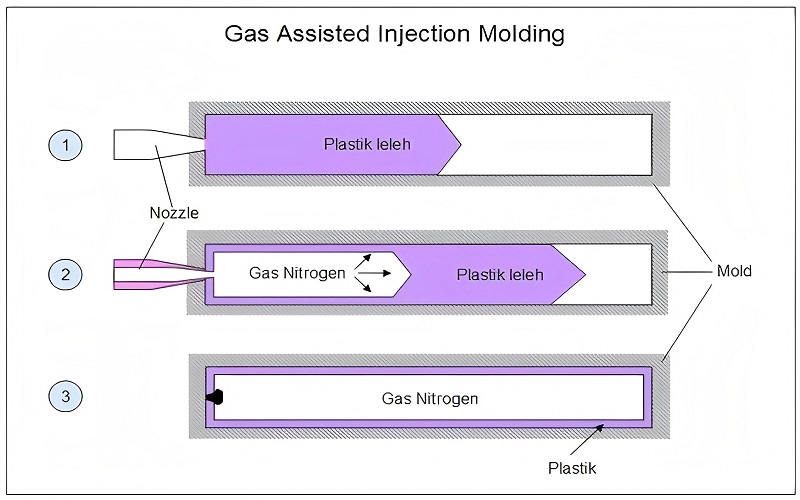
Key Benefits of Gas Assist Injection Molding
Gas assist injection molding offers significant advantages, including up to 35% savings in material usage, which lowers raw material costs and freight expenses. Additionally, cooling times can be reduced by up to 50%, resulting in faster production cycle time and greater efficiency.
Constant gas pressure during cooling prevents shrinkage and reduces internal stresses, improving single part quality. This process also eliminates defects like warping and sink marks, enhancing both the appearance and functional performance of the parts.
Improved dimensional stability from gas assist injection molding often reduces or eliminates the need for costly secondary operations like sanding and priming, preventing issues such as a short shot.
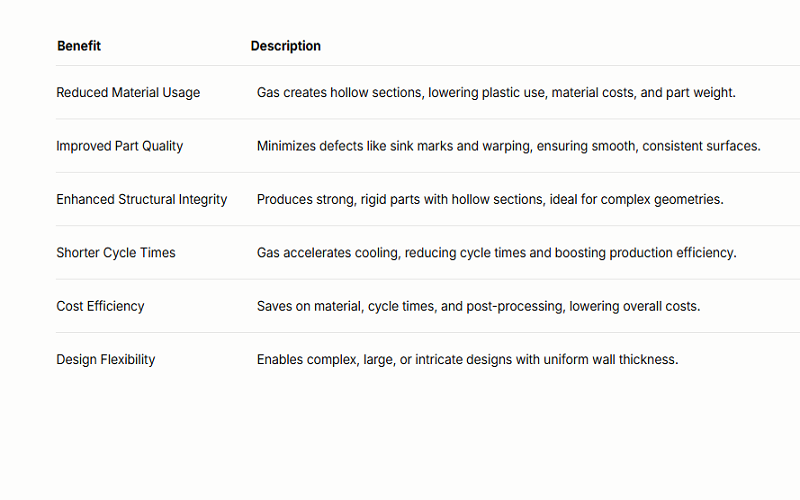
Materials Suitable for Gas Assist Injection Molding
Selecting the right materials is vital for successful gas assist injection molding. Thermoplastics like PA (polyamide) and PBT (polybutylene terephthalate) are particularly well-suited due to their compatibility. Commonly used plastics include PA6, PA66, and glass fiber reinforced PP (polypropylene), which provide the necessary strength and stability for high-quality parts.
Materials with low shrinkage and good dimensional stability are preferred to avoid defects and ensure product integrity. The versatility of using a wide range of thermoplastics makes gas assist injection molding adaptable for various applications.
Equipment Required for Gas Assist Injection Molding
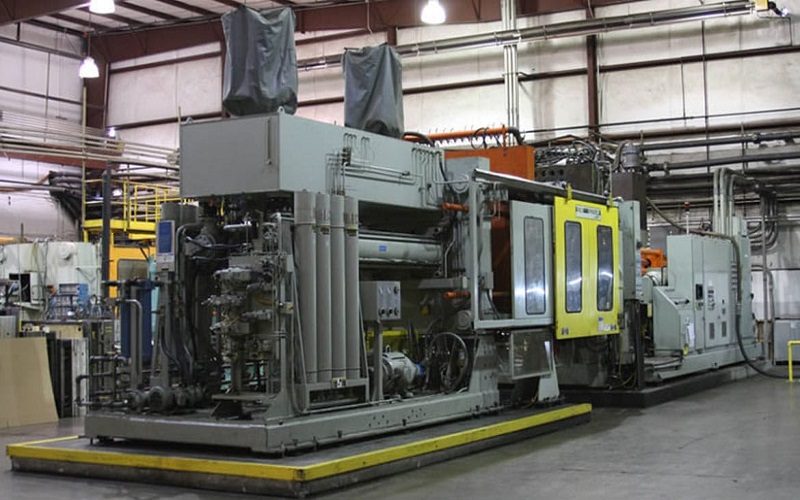
Equipment for gas assist injection molding integrates seamlessly with existing systems. The gas-assist control unit operates independently, linking through an injection signal connection. It can manage multiple machines simultaneously due to its multi-group gas path design, utilizing gas assist technology.
A crucial component is the nitrogen gas generation device, which supplies the necessary inert gas. The gas-assist gas control unit manages the timing and pressure of the gas injection, ensuring precise and consistent results with each cycle.
The Gas Assist Injection Molding Process
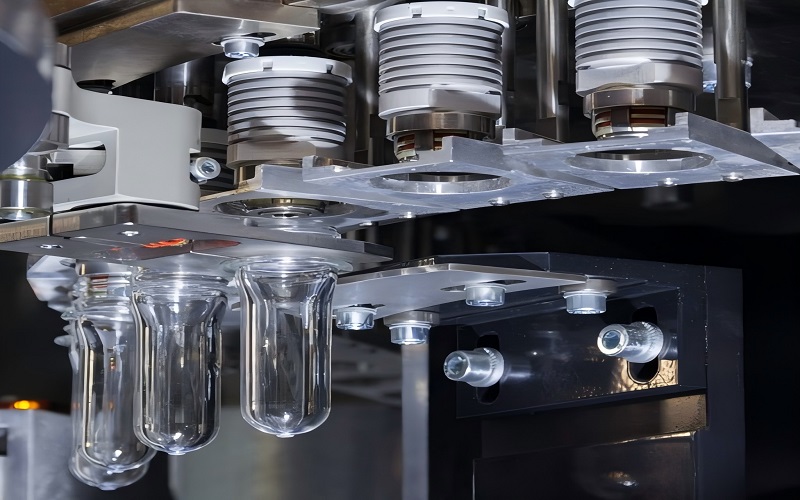
The gas assist injection molding process includes three stages: injecting the polymer melt, introducing the gas, and cooling the part under pressure. Initially, the molten plastic fills 70% to 95% of the mold cavity, allowing for the subsequent introduction of compressed nitrogen gas, at which point gas is injected to drive the molten material toward the mold extremities.
Maintaining gas pressure during cooling promotes adherence to the mold walls and compensates for shrinkage, providing pressure. This low-pressure process ensures the final parts are lightweight, structurally sound, and free from defects like sink marks and warping.
Design Considerations for Gas Assist Injection Molding
Designing molds for gas assist injection molding requires careful consideration of gas channels and cross section. Larger cross sections facilitate easier gas penetration, ensuring uniform pressure distribution and improved part quality. Integrating gas channels into the mold design achieves consistent results and reduces the need for extensive finishing processes.
Parts converted to gas assist injection molding can incorporate design features like support ribs and bosses, streamlining manufacturing and enhancing structural integrity.
Applications of Gas Assist Injection Molded Parts
Gas assist injection molding is ideal for producing large, complex, or structurally strong plastic parts. It creates hollow areas within parts, enhancing strength while reducing weight and minimizing the need for secondary processes. This technique can replace traditional metal parts like enclosures and access doors, offering better quality and reduced corrosion.
The method is particularly beneficial for automotive applications, where materials like glass-filled PBT (polybutylene terephthalate) offer excellent electrical properties. Reinforced polymers like glass-fiber-reinforced PA6 and PA66 are also popular, enhancing performance and durability.
Weight reduction achieved through gas assist injection molding contributes to overall efficiency and cost savings.
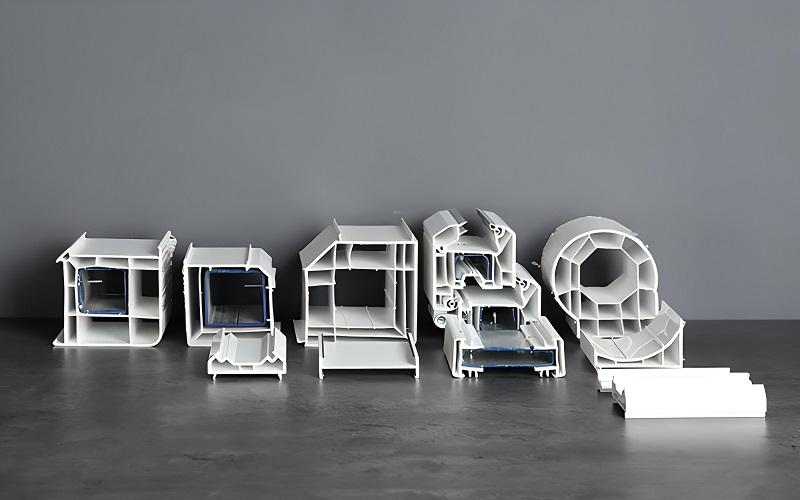
Challenges and Limitations of Gas Assist Injection Molding
Despite its advantages, gas assist injection molding introduces complexity due to the two-phase flow of polymer melt and gas. This can lead to higher initial investment costs compared to traditional methods. Design mistakes can increase costs and reduce productivity, making careful planning and execution essential.
Understanding these challenges and limitations helps manufacturers effectively implement gas assist injection molding and maximize its benefits.
Cost Efficiency and Economic Impact
Gas assist injection molding offers significant material savings, up to 35%, by creating thicker sections and hollow sections within molded parts. This is particularly beneficial for tubular or rod-shaped parts, with material savings ranging between 20% to 40%. The lower clamping force requirements allow for smaller, less expensive machinery, enhancing cost efficiency.
Reduced time and cost in manufacturing processes allow OEMs to maintain quality and expand design options. The economic impact of gas assist injection molding is substantial, making it an attractive option for various industries.
Innovations in Gas Assist Injection Technology
Recent innovations in gas assist injection technology have boosted production efficiency by addressing previous limitations. These advancements minimize defects like sink marks and surface blemishes, which often require additional finishing. Continuous improvements in gas injection technology are expanding application possibilities across various industries.
The rapid evolution of this technology introduced a viable solution for manufacturers seeking to enhance production efficiency and product quality.
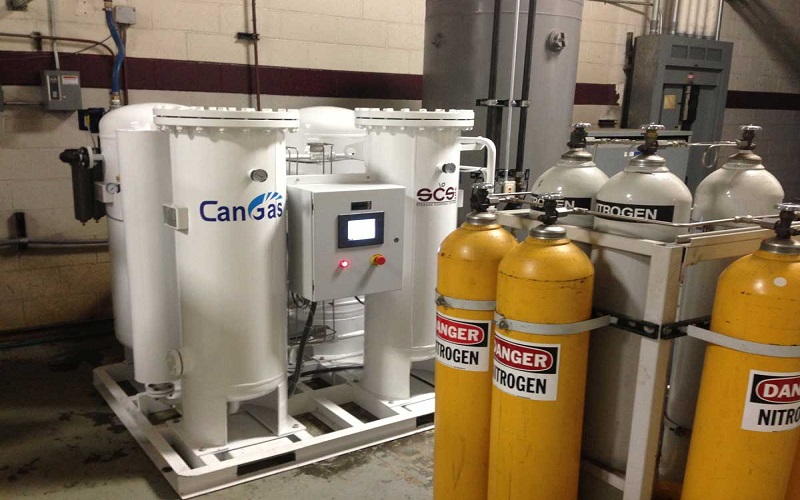
Converting Existing Parts to Gas Assist Injection Molding
Converting existing parts to gas assist injection molding offers better quality alternatives to large metal parts, eliminating heavy and corrosion-prone components. This process suits covers, enclosures, access doors, panels, and injection molded part, offering improved quality and reduced weight through conventional injection molding.
The conversion process enhances structural integrity and streamlines manufacturing, making it a cost-effective solution for various applications.
Secondary Operations and Finishing Techniques
Gas assist injection molding often eliminates labor-intensive secondary processes, resulting in significant cost savings. However, secondary operations might still be necessary for complex designs, particularly those requiring tight tolerances and special finishes.
Combining gas assist injection molding with selective secondary operations can enhance the overall quality and functionality of the final product, optimizing production efficiency and achieving superior results.
Environmental Benefits of Gas Assist Injection Molding
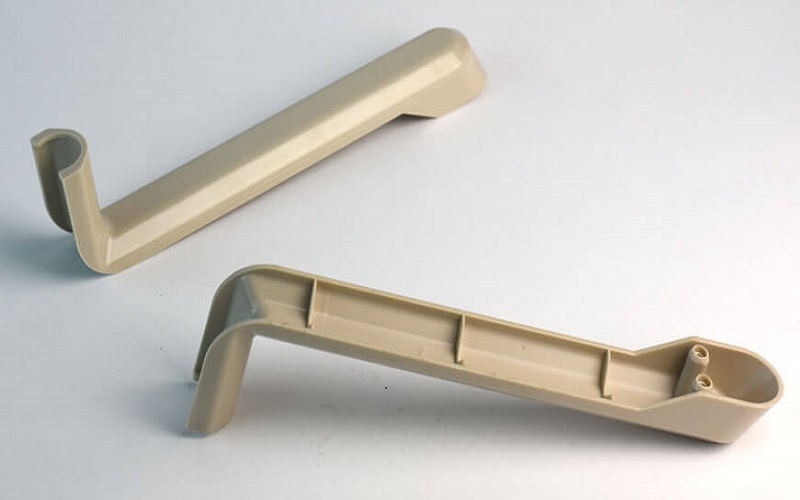
Gas assist injection molding is environmentally friendly, minimizing waste by using only the necessary amount of plastic. This method reduces material consumption and contributes to more sustainable manufacturing practices, making it an eco-conscious choice for modern industry.
Summary
In summary, gas assist injection molding offers numerous advantages over conventional injection molding, including material savings, reduced cooling times, and improved part quality.
By understanding the process, suitable materials, required equipment, and design considerations, manufacturers can effectively implement this technique to enhance their production operations.
The continued innovations and environmental benefits further solidify gas assist injection molding as a transformative technology in the plastic injection molding industry.
Frequently Asked Questions
What are the disadvantages of gas-assisted injection molding?
Gas-assisted injection molding presents disadvantages such as increased process complexity, challenges in applying it to multi-cavity molds, and a need for precise control requiring experienced operators. Additionally, it is unsuitable for clear or transparent materials due to potential aesthetic deterioration.
What is Gas Assist Ltd?
Gas Assist Ltd is a leading company specializing in new boiler installations across the UK, based in Poole, Dorset. They utilize online technology to streamline the buying process and offer impressive warranties alongside their services.
What is gas assist injection molding?
Gas assist injection molding is a process that utilizes pressurized nitrogen gas to improve the structural integrity and reduce the weight of plastic parts during low-pressure injection molding. This technique leads to enhanced quality and efficiency in the production of complex shapes.
What are the key benefits of gas assist injection molding?
Gas assist injection molding offers significant advantages, including material savings of up to 35%, reduced cooling times by up to 50%, enhanced part quality, and the elimination of defects like warping and sink marks. These benefits can lead to more efficient production processes and higher-quality products.
What materials are suitable for gas assist injection molding?
Suitable materials for gas assist injection molding include thermoplastics such as polyamide (PA), polybutylene terephthalate (PBT), PA6, PA66, and glass fiber reinforced polypropylene (PP). These materials enhance the efficiency and effectiveness of the molding process.