Gating in injection molding is crucial for ensuring the quality of your final products. It involves choosing the right entry points for molten plastic to efficiently fill the mold cavities.
In this article, we will explore various types of gating injection molding gates, their specific purposes, and how to select the best one for your project.
Understanding Injection Molding Gates
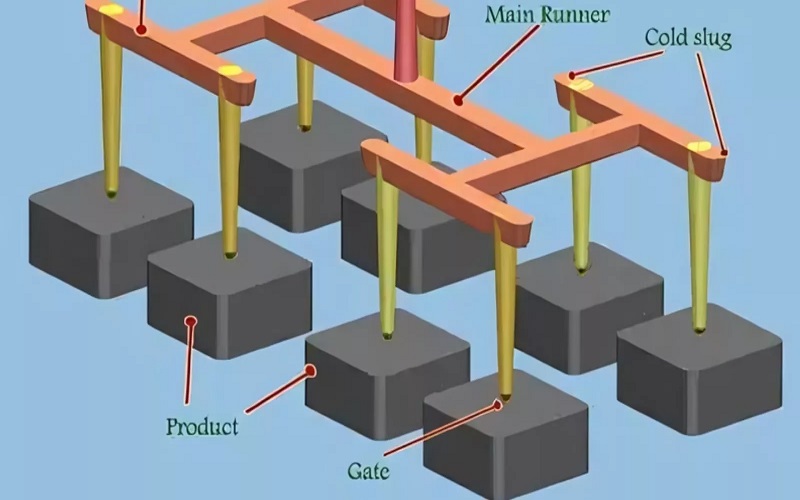
Injection molding gates serve as the crucial entry points for molten plastic to flow into the injection molding machine’s mold cavities, fundamentally affecting the quality of the final product.
Acting as the last checkpoint before the plastic material fills the mold, these gates control molten plastic’s flow and ensure that the mold is filled uniformly and efficiently. Different types of gates exist, each with unique characteristics that influence the processing conditions and the final part quality.
The primary function of injection molding gates is to regulate the molten plastic as it enters the mold cavity. This regulation is vital for preventing defects such as air traps, incomplete filling, and uneven cooling, all of which can compromise the structural integrity and appearance of the final product. By selecting the appropriate injection molding gate design and placement, manufacturers can achieve consistent part dimensions and properties, leading to higher-quality injection molded parts.
Grasping the different types of injection molding gates is key to refining the injection molding process. Each type offers distinct benefits and drawbacks, necessitating the choice of the appropriate gate based on the part’s specific needs and material used, while also considering the removal of excess gate material to ensure a clean finish.
In the following sections, we’ll explore how to select the right gate type and delve into the popular gate designs used in the industry.
Choosing the Right Gate Type
Choosing the correct injection molding gate is a critical step in ensuring the success of your injection molding project. The gate type you select can significantly influence the flow and quality of the molded parts, as well as the overall efficiency of the production process. Factors such as mold design, material selection, part orientation, and production functionality all play a role in determining the optimal gate type at the gate point.
The right gate type helps manage the flow of molten plastic into the mold, preventing issues like flow marks, warping, gate blemishes, and incomplete filling. On the flip side, improper gate selection can lead to defects that compromise the quality and functionality of the final product. An informed decision requires considering both the material properties and the part design, particularly in the gate area.
In the upcoming subsections, we will explore the material considerations and part design influences that play a crucial role in gate selection. Understanding these factors leads to better choices, enhancing part quality and streamlining production.
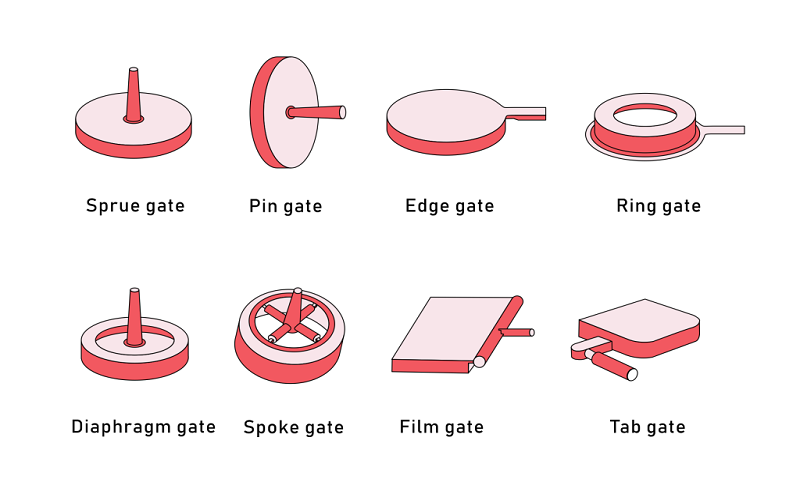
Material Considerations
The type of particular plastic resin used in your plastic injection molding project significantly impacts the choice of gate type. Each plastic material has unique flow properties that must be considered when designing the gate.
For instance, some resins flow easily and can fill molds quickly, while others may require more precise control to ensure proper filling of molten plastic material. Additionally, understanding the role of plastic injection in the process is crucial for optimal results.
To enhance efficiency, gate dimensions should be adjusted based on the specific flow characteristics of the material and the mold design. In some cases, employing co-injection molding techniques can help improve part strength and overall flow by allowing different materials to be injected simultaneously.
Knowing the material flow properties helps in selecting a gate type that maximizes part quality and production efficiency.
Part Design Influence
The design of the part being molded plays a crucial role in gate selection. The shape and size of the molded part determine the optimal gate type needed to ensure effective filling and minimize defects. For example, complex part designs with features like undercuts may require specific gate types to achieve proper filling and avoid issues such as air traps or incomplete filling, particularly when considering molding parts.
The parting line, which is the line where the two halves of the mold meet, also influences gate placement and type. Proper alignment with the parting line helps in achieving a smooth flow of molten plastic and reducing visible gate marks.
Considering the part design allows manufacturers to choose gate types that improve the quality and appearance of the final product, ensuring it meets required specifications.
Popular Types of Injection Molding Gates
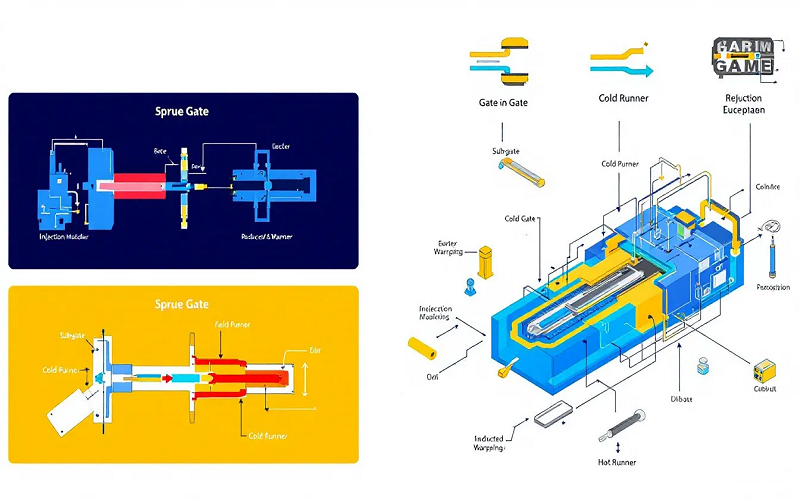
Injection molding gates come in various designs, each suited for different applications and part requirements. Understanding the popular types of gates and their specific applications can help you select the best option for your injection molding projects. The primary categories of gates include restrictive gates and non-restrictive gates, each influencing how the molten plastic reaches the mold cavities.
Some of the most commonly used injection molding gates include:
- Direct sprue gates
- Edge gates
- Submarine gates
- Cashew gates
- Diaphragm gates
- Fan gates
- Pin gates
Each gate type has its advantages and limitations, making it crucial to choose based on the specific needs of your project.
Next, we’ll detail each gate type, discussing their design, applications, and benefits.
Direct Sprue Gates
Direct sprue gates are among the most common gate designs used in injection molding, particularly for manufacturing consumer products and home appliances. Their simple design allows for efficient flow of molten plastic into the mold, making them suitable for large parts that require less injection pressure.
Positioned at the parting line, these gates typically require less injection pressure and produce minimal gate vestiges, which helps reduce defects during the molding process. Additionally, direct gates can enhance the overall efficiency of the injection molding process.
However, one potential drawback of direct sprue gates is that they can leave visible marks on the molded part, which may be undesirable for products where aesthetics are important. Despite this, their ability to ensure symmetrical filling and ease of use makes them a popular choice for single cavity molds.
Edge Gates
Edge gates, also known as side or rectangular gates, are widely used due to their adaptability and cost-effectiveness. These gates are particularly effective for flat parts and ensure smooth plastic flow throughout the mold, reducing the overall production costs. Placed on the part’s edge, they allow for easy removal and minimal gate vestiges.
One of the key benefits of edge gates is their ability to provide a cost-effective solution for many projects, especially those involving flat parts. Their design and placement help in achieving uniform filling, minimizing defects, and enhancing the quality of the final product, particularly with an edge gate.
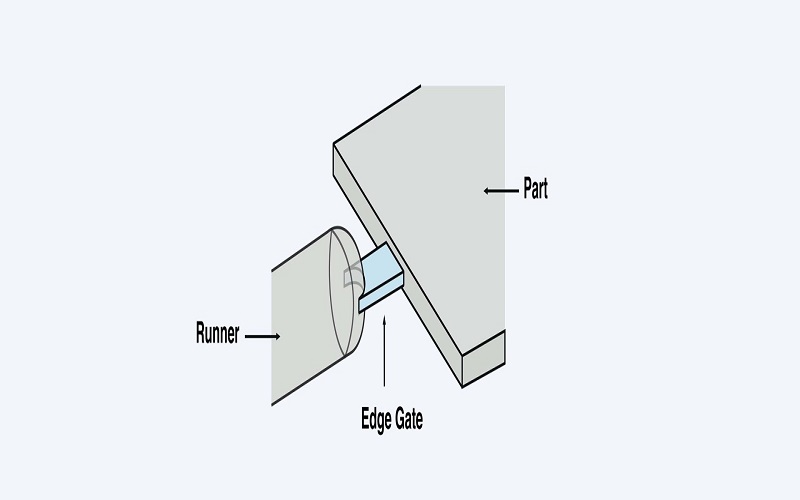
Submarine Gates
Submarine gate, also known as tunnel gates, are designed to automatically trim during the ejection phase, making them ideal for high cavitation molds and small components.
Positioned below the parting line, submarine gates have a conical shape and are typically angled between 20° to 40° relative to the cavity, leaving a gate vestige. Additionally, sub gates offer unique advantages in specific applications.
While submarine gates are efficient for molding small components, they have limitations when used for larger parts, including longer cycle periods and potential surface finish issues. Despite these challenges, their automatic trimming capability makes them a valuable choice for high-volume production.
Cashew Gates
Cashew gates are named for their curved structure that resembles a tree nut, allowing them to access hard-to-reach areas of the mold. These gates are particularly useful for products that can be disfigured during gate removal, ensuring part integrity during ejection. The cashew gate design enhances functionality in various applications.
However, cashew gates can be challenging to de-gate and may risk breaking off during ejection due to the pulling of plastic. Despite these challenges, their versatility and ability to work with various plastic resins make them a valuable option for a wide range of injection molding applications.
Diaphragm Gates
Diaphragm gates are designed to distribute plastic evenly in large, cylindrical parts, making them ideal for achieving uniform flow and minimizing defects. These gates are particularly effective for large, open-diameter parts, ensuring even plastic flow throughout the mold.
Diaphragm gates evenly distribute molten plastic, maintaining the structural integrity and overall quality of the molded parts. The diaphragm gate design makes them suitable for applications where part strength and uniformity are critical. This diaphragm gate design is essential for achieving optimal results.
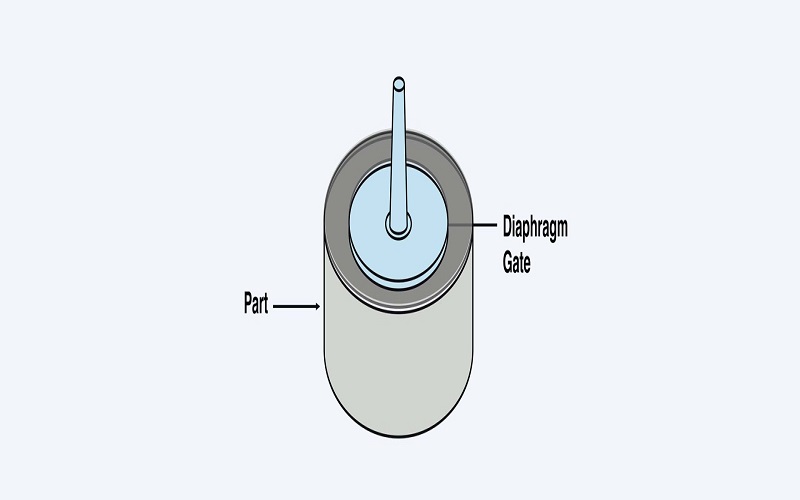
Fan Gates
Fan gates have a gradually expanding design that resembles a folding fan, ensuring even distribution of molten plastic over a wider area. This design minimizes stress and defects in large, thin parts, making fan gates ideal for such applications.
Typically, the gate depth for a fan gate ranges from 0.25mm to 1.5mm, with the width being 1/4 of the cavity width at the gate and a minimum of 8mm. Polycarbonate plastics are commonly used with fan gates due to their suitability for achieving even flow and minimizing defects.
Pin Gates
Pin gates are small and precise, often used in three-plate molds to facilitate multiple flow directions, enhancing design flexibility. The precision and small size of pin gates make them ideal for complex geometries in molds.
However, one drawback of using pin gates is the higher scrap rates during the molding process, as large runners are required to achieve proper filling. Despite this, their ability to handle complex designs makes them a popular choice for intricate injection molding projects, especially when considering the role of the ejector pin.
Hot Runner Systems
Hot runner systems maintain a consistent temperature throughout the molding process, improving efficiency and reducing waste. These systems include hot runner system hot tip gates and valve gates, which provide uniform flow and enhanced control, respectively.
Valve gates, in particular, offer improved cycle times and part quality, making them an excellent choice for high-volume production. A valve gate hot runner thermal gate works without a shut-off mechanism, making them compatible with various resin types and enhancing their versatility.
Gate Placement Strategies
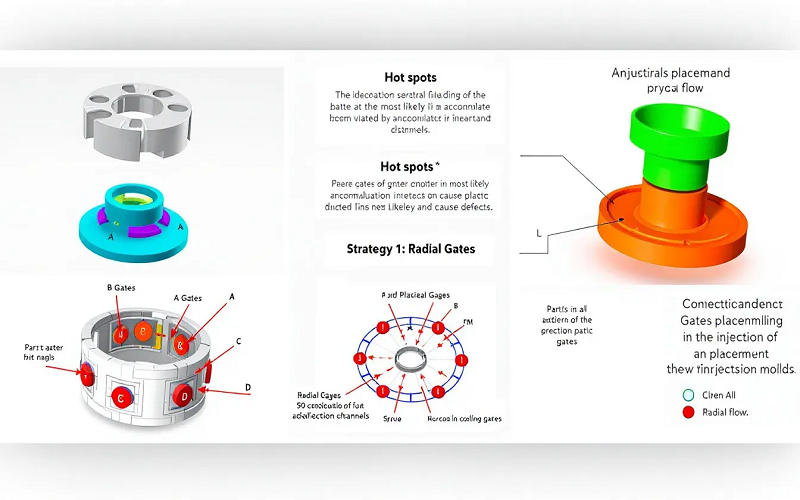
Proper gate placement is crucial for achieving optimal part quality, as it directly affects the difficulty of separation, deformation, and surface finish. Incorrect gate placement can lead to deformities and surface defects, undermining the overall quality of the molded parts. Considering aesthetics and structural integrity enhances the final product’s appearance and functionality.
When placing gates, it’s essential to avoid visible surfaces to minimize visible gate marks and enhance the overall appearance of the final product. Additionally, thoughtful gate placement helps ensure consistent flow and minimizes defects, aligning with overall mold design efficiency.
Avoiding Visible Surfaces
Proper gate placement can significantly influence the final aesthetic quality of molded parts by reducing visible joint marks. Selecting various gate locations minimizes marks on the final product, enhancing its overall appearance. It is essential to understand how gate placement matter in this process and the importance of gate location in achieving optimal results.
Balancing Flow Paths
Balanced flow paths in injection molding are essential to maintain uniform correct filling of the mold, reducing the risk of defects like warping and sink marks. Uneven filling can lead to visible flaws on the surface, diminishing the aesthetic and functional integrity of the parts, as molten plastic flows can impact the overall quality. Additionally, ensuring that molten plastics flow correctly is crucial for achieving optimal results.
Thoughtful gate placement ensures consistent flow, enhancing the final product’s quality.
Gate Size and Geometry
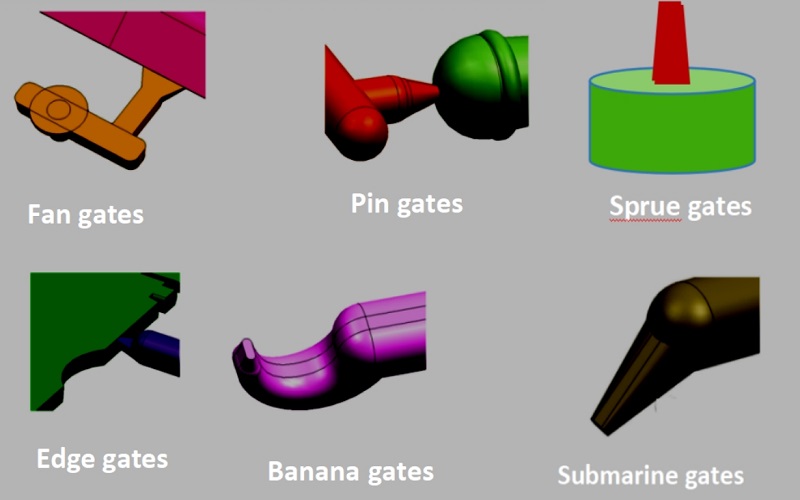
The design and size of injection molding gates are critical in ensuring the uniform flow of molten plastic and preventing defects in molded parts. The size of the gate affects shear heating, where smaller gates can increase flow pressure and lead to material overheating, while larger gates can improve filling rates but may cause uneven filling.
The ideal gate size should consider the part’s wall thickness, material viscosity, and required flow rate to ensure effective filling.
Shear Heating Concerns
Using a small gate for larger components can lead to material overheating, causing degradation before the mold is fully filled. Tab gates are designed to absorb shear stress safely without compromising part quality, ensuring consistent melt temperature and preventing premature solidification that can lead to weld lines.
Techniques like conformal cooling channels maintain uniform mold temperatures, reducing weld line formation.
Optimizing Gate Dimensions
The gate size is defined by its width, which is influenced by the volume of the mold cavity. The depth is based on the nominal wall size. Optimizing gate dimensions is crucial as too large gates can cause uneven filling and defects, while too small gates can lead to short shots and high residual stress.
Inappropriate gate size can lead to increased flow pressure, which may create excessive shear heating, degrading the plastic. Even plastic flow is essential for ensuring consistent shrinkage and enhances the overall strength of molded parts, while improper gate design can further complicate these issues.
Manual vs. Automatic Trimming
Manual and automatic trimming methods each have their advantages and disadvantages. Manually trimmed gates require operators to physically separate parts from runners for each cycle, which can increase labor costs and handling time.
In high-volume applications, manual trimming is less feasible, leading to robotic gate cutting or switching to automatically trimmed designs.
Automatically trimmed gates eliminate the need for human intervention by shearing parts from runners during mold ejection, improving part quality, reducing defects, and enhancing productivity. Examples of automatically trimmed gates include hot tip gates, submarine gates, and pin gates, which are particularly effective in high-volume production due to reduced labor costs and increased efficiency.
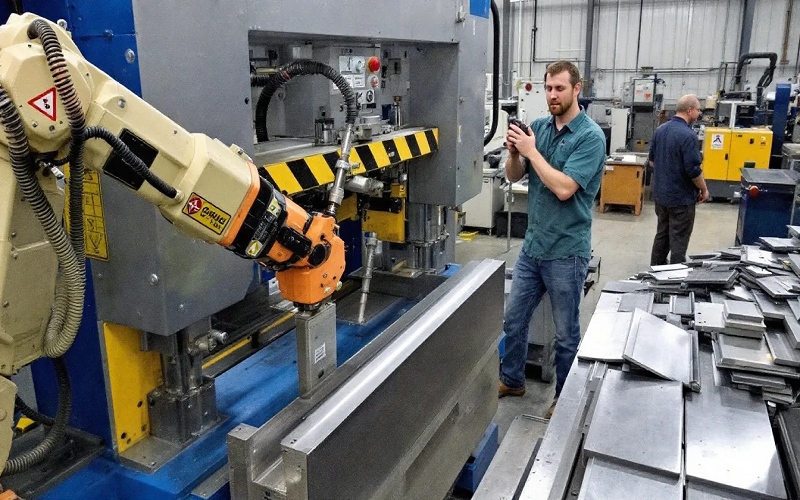
Manually Trimmed Gates
Types of manually trimmed gates include:
- Edge gates, which are commonly used for flat parts, providing a cost-effective solution for proper filling
- Fan gates, which spread molten plastic across wide areas, minimizing defects in large, thin parts
- Tab gates, which connect to the molded part at a single point, allowing for easy removal but requiring careful placement.
However, manually trimmed gates can increase labor costs due to the additional handling required for trimming.
Automatically Trimmed Gates
Automatically trimmed gates include several types. Some examples are hot tip gates, submarine gates, and hot tip gate pin gates. These gates improve part quality, reduce defects, and enhance productivity by requiring no human intervention.
The use of valve gates in automatically trimmed systems can lead to improved cycle times in production, while hot runner valve gates maintain pressure and temperature for even mold filling, supporting the effectiveness of automatically trimmed gates.
Advanced Tips for Gating Injection Molding
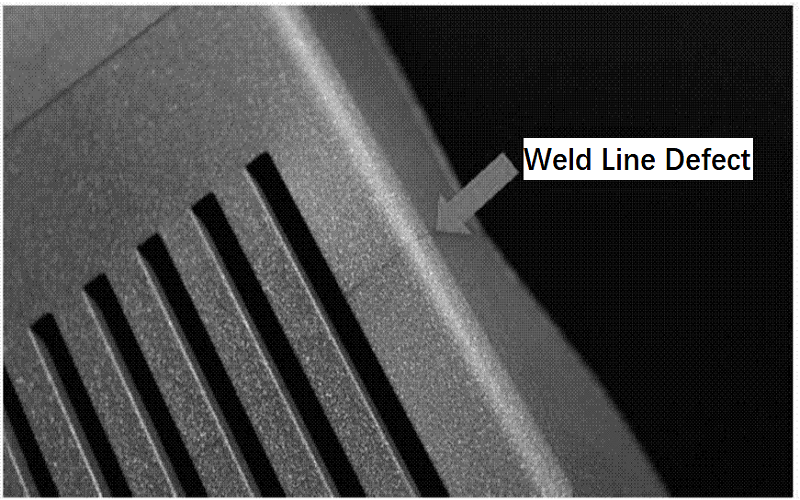
Proper design and placement of gates ensure even flow of molten plastic, prevent defects, and affect overall product quality. Common defects in injection molding include sink marks, flow lines, and warping. Other issues can be surface delamination, short shots, and jetting.
Understanding these issues and using advanced gating techniques allows manufacturers to optimize the injection molding process and produce higher-quality parts.
Minimizing Weld Lines
Minimizing weld lines is essential in injection molding to ensure part quality and structural integrity. Diaphragm gates can leave noticeable gate marks on the inner edge of parts, which may affect aesthetics, while pin gates can lead to a high scrap rate due to the large runners required.
Appropriate gate selection is critical for reducing weld lines and enhancing the overall quality of molded parts.
Enhancing Part Strength
Diaphragm gates ensure even plastic flow, making them suitable for large open diameter parts and allowing a small opening for a large amount of plastic to flow into the cavity, which improves part integrity.
Fan gates prevent defects and maintain stability in the final product, contributing to enhanced part strength. Choosing the right gate type is crucial for enhancing part strength in injection molding.
Summary
In conclusion, the choice and design of injection molding gates play a pivotal role in the quality and efficiency of the molding process. From understanding the basic functions of gates to selecting the right type based on material and part design, every decision impacts the final product. Proper gate placement, size, and trimming methods further enhance the overall outcome, ensuring high-quality injection molded parts.
By implementing advanced tips and strategies, such as minimizing weld lines and enhancing part strength, manufacturers can optimize their injection molding projects.
With the knowledge gained from this guide, you are well-equipped to make informed decisions that will improve your injection molding operations and achieve superior results.
Frequently Asked Questions
Why is gate placement important in injection molding?
Gate placement is essential in injection molding because it directly impacts part quality, influencing separation ease, deformation, and surface finish. Proper positioning helps prevent defects and ensures the final product meets both aesthetic and functional standards.
What are the common types of injection molding gates?
The common types of injection molding gates include direct sprue gates, edge gates, submarine gates, cashew gates, diaphragm gates, fan gates, and pin gates, each tailored to specific applications. Selecting the appropriate gate type is crucial for optimizing performance and product quality.
How does material selection influence gate design?
Material selection significantly influences gate design, as different plastic resins possess unique flow properties that necessitate adjustments in gate dimensions. This ensures efficient filling and the production of high-quality parts.
What are the advantages of automatically trimmed gates?
Automatically trimmed gates significantly enhance productivity and part quality while reducing defects, making them particularly advantageous for high-volume production environments.
How can I minimize weld lines in injection molding?
To minimize weld lines in injection molding, focus on proper gate selection and placement to ensure even flow, and consider implementing advanced cooling techniques. This approach will enhance part quality by reducing visible weld lines.