HDPE moulding is a key process for producing durable and versatile plastic components. In this article, we’ll cover what HDPE plastic injection molding is , its key advantages, and essential best practices for achieving high-quality results.
Whether you’re new to this field or looking to refine your techniques, this guide will provide valuable insights into mastering HDPE moulding.
Key Takeaways
- HDPE is well-suited for injection molding due to its chemical resistance, impact resistance,thermal stability, and excellent strength-to-weight ratio, making it an ideal choice for various applications.
- The injection molding process for HDPE requires meticulous control of temperature, pressure, and mold design to ensure high-quality, defect-free parts.
- Adhering to best practices, such as maintaining uniform wall thickness and optimizing cooling and post-processing techniques, is essential for achieving optimal results in HDPE molding.
Understanding HDPE Moulding
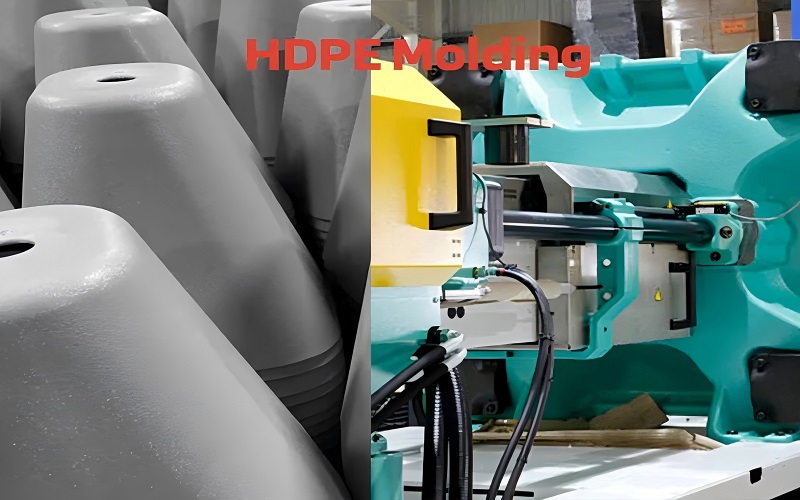
High density polyethylene (HDPE) is a versatile thermoplastic material derived from petroleum. This commodity resin is widely used across various industries, thanks to its favorable characteristics.
In the realm of injection molding, HDPE stands out as a material of choice due to its ease of processing and robust performance. Additionally, low density polyethylene is another important material utilized in various applications.
The journey of HDPE molding begins with the material being melted into a moldable state. The injection molding process involves injecting this molten HDPE at high pressure into a pre-designed mold. Once the material fills the mold cavity, it cools and solidifies almost immediately, forming the desired part.
After cooling, the mold opens, and the molded HDPE part is ejected, making way for the next cycle. This repetitive process allows for the efficient production of high-quality parts in large quantities.
Grasping the fundamentals of HDPE molding is essential for manufacturers. Mastering its properties and injection molding process enables unlocking the full potential of this versatile thermoplastic polymer. The following sections will delve deeper into the key properties of HDPE, the intricacies of the injection molding process, and the numerous advantages it offers.
Key Properties of HDPE for Injection Molding
High-Density Polyethylene (HDPE) boasts a unique set of properties that make it particularly well-suited for injection molding applications. One of its standout material properties is its excellent resistance to chemicals, which ensures durability and longevity in demanding environments.
This chemical resistance, combined with HDPE’s high strength-to-weight ratio, contributes to the production of durable and reliable parts.
HDPE also exhibits impressive thermal stability, capable of handling both high and low temperatures without compromising its integrity. This makes it an ideal material for applications that require exposure to varying temperature conditions.
Furthermore, HDPE’s good wear and friction properties enhance its usability in a wide range of applications, ensuring that the parts produced are not only strong but also resilient to wear and tear.
The material’s excellent electrical insulating properties make it a preferred choice for electronic and electrical applications. HDPE’s ability to maintain its mechanical properties hdpe under different environmental conditions underscores its versatility as a thermoplastic polymer.
Leveraging these key properties allows manufacturers to produce high-quality, injection-molded parts that meet stringent industry requirements.
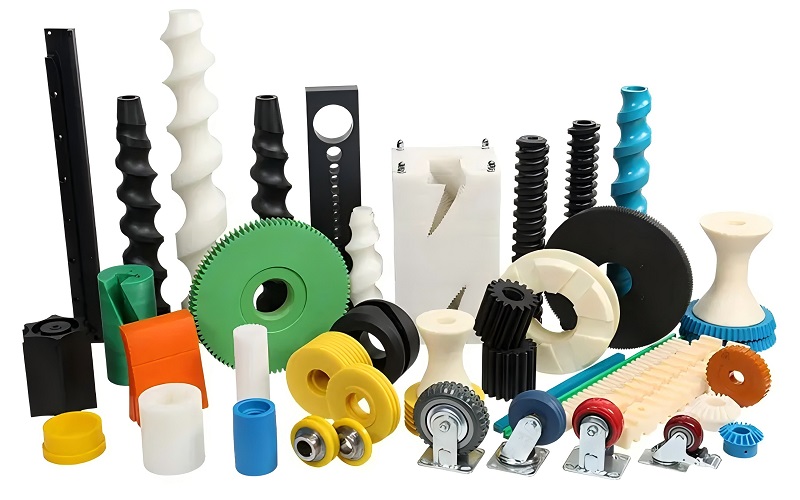
The Injection Molding Process for HDPE
The injection molding process for HDPE involves several critical steps, each contributing to the quality and precision of the final product. It begins with the injection of molten HDPE into a carefully designed mold. This step requires high pressure to ensure that the material fills the mold cavity completely, forming the intended shape.
Mold design plays a pivotal role in the injection molding process. A well-designed mold influences material flow, cooling, and part removal, ultimately determining the quality of the molded parts.
High-quality molds can significantly enhance the surface finish and dimensional accuracy of HDPE products, ensuring that they meet the desired specifications.
Temperature and pressure control are crucial elements of the injection molding process. The typical melt temperature range for HDPE is approximately 220°C to 280°C, while mold temperatures can vary between 20°C and 60°C.
Injection speeds and pressures must be carefully managed to optimize flow performance and avoid defects in the final parts. Maintaining these parameters within optimal ranges ensures consistent, high-quality results.
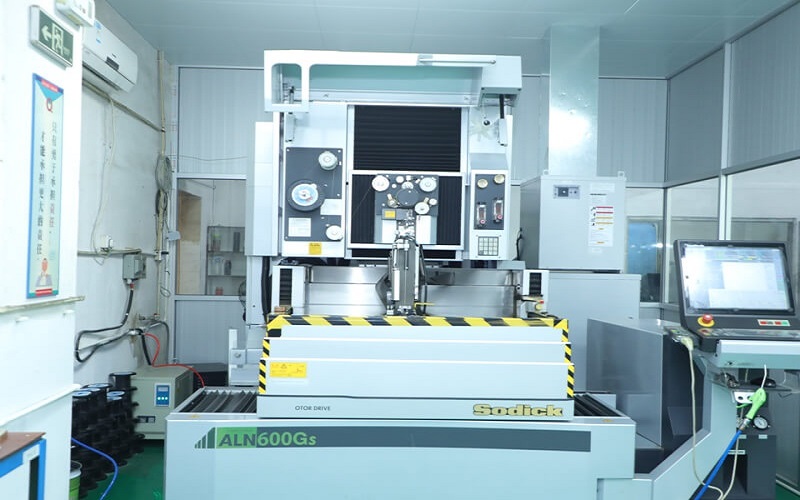
Advantages of HDPE Moulding
One of the primary advantages of HDPE molding is its cost-effectiveness. HDPE is readily available and offers excellent performance benefits, making it an economically viable choice for manufacturers.
The unit cost of HDPE decreases with high-volume production, allowing manufacturers to produce large quantities of high-quality parts at a lower cost per piece.
The injection molding process for HDPE can be automated, further enhancing production efficiency and reducing the need for human intervention.
This automation leads to faster cycle times and higher productivity, enabling manufacturers to meet the demands of various industries effectively. HDPE’s versatility also allows it to be used in a wide range of applications, from consumer products to industrial components.
In addition to its economic benefits, HDPE offers superior performance characteristics. Its excellent greater chemical resistance, durability, and thermal stability make it a preferred material for many applications. Leveraging these advantages allows manufacturers to produce high-quality parts that meet stringent industry requirements.
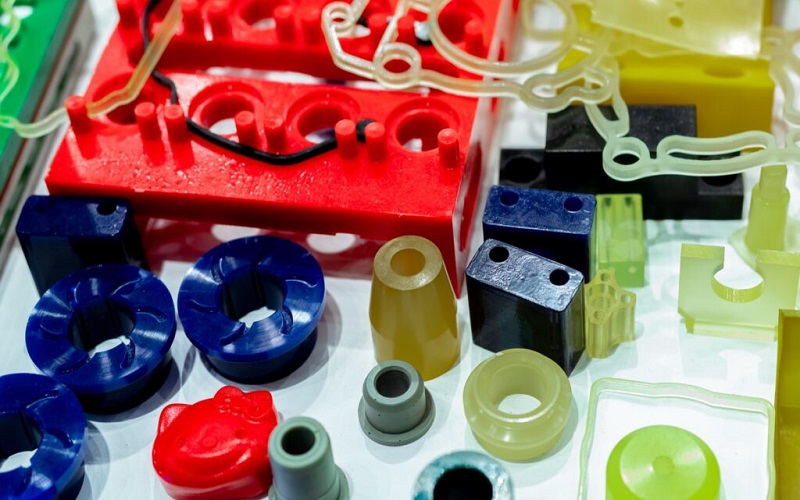
Common Applications of HDPE plastic
HDPE is widely used in the production of various consumer and industrial products. Its durability and non-leaching properties make it an ideal material for manufacturing water bottles, milk jugs, lotion bottles, and food storage containers. These products benefit from HDPE’s excellent chemical resistance and strength, ensuring safety and longevity.
In industrial applications, HDPE pipes are highly favored due to their strength and ability to withstand extreme temperatures. The material’s robustness and thermal stability make it suitable for demanding environments, ensuring reliable performance over time.
HDPE is also popular in the USA for packaging and industrial products, further demonstrating its versatility and wide acceptance in various markets.
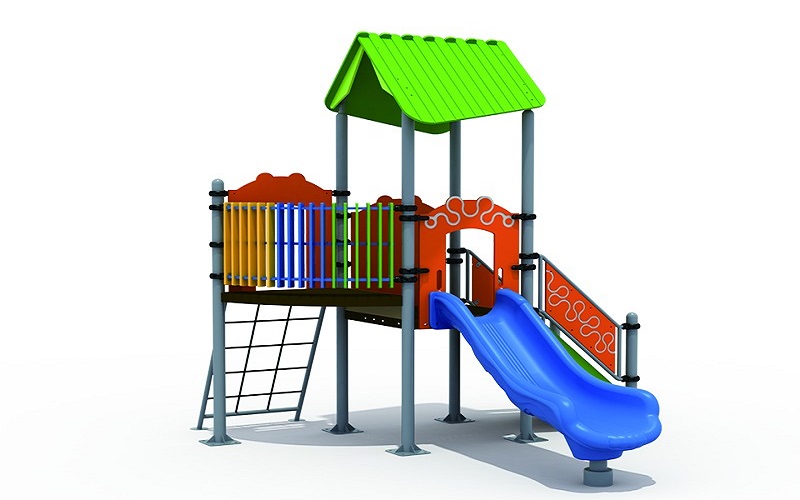
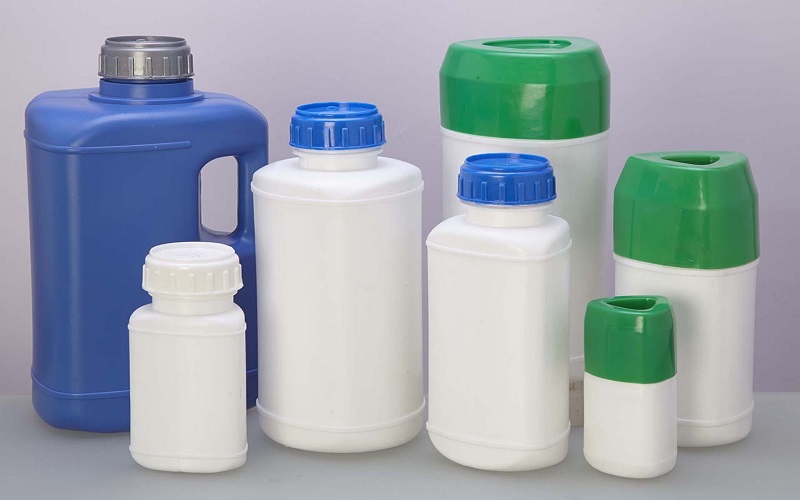
Challenges and Solutions in HDPE Moulding
While HDPE injection molding offers numerous benefits, it also presents some challenges. One common issue is high mold shrinkage, which can lead to dimensional inaccuracies in the molded parts. Unequal shrinkage can also cause warping, affecting the overall quality and functionality of the parts.
Addressing these challenges requires effective quality control during the molding process. This helps identify defects early, allowing for necessary adjustments and maintaining production efficiency.
Closely monitoring the molding process and making real-time adjustments minimizes shrinkage and warping, ensuring consistent quality in HDPE products.
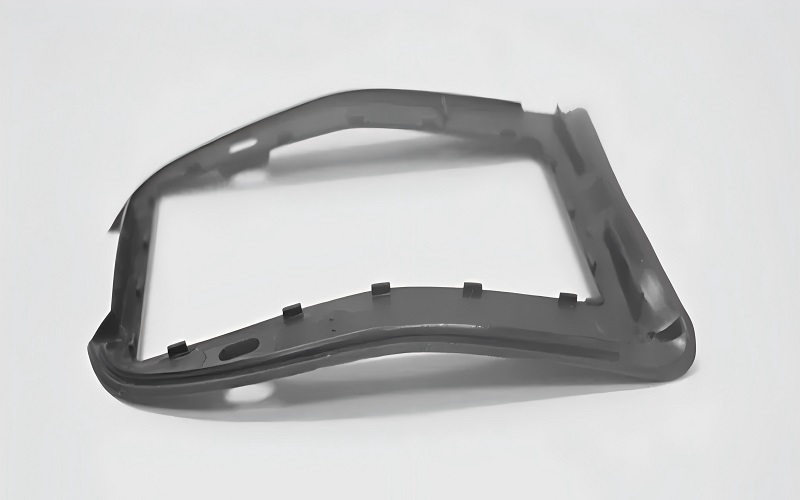
Best Practices for Optimal HDPE Moulding
Achieving optimal results in HDPE molding requires adherence to several best practices. Uniform wall thickness in HDPE products is critical to prevent warping and ensure consistent strength throughout the part. Efficient cooling is also crucial to ensure even part quality and dimensional stability.
Appropriate melt temperatures prevent material degradation and ensure the quality of the final product. Overheating HDPE can adversely affect its properties, leading to inferior parts.
Additionally, optimizing the design of gates can enhance the filling process and reduce defects. Stress-relieving treatments can also mitigate internal stresses that cause warping.

Post-Processing Techniques for HDPE Parts
Post-processing is an integral part of the HDPE molding process, enhancing the finish and functionality of the final parts. Trimming is essential to remove excess material left from the molding process, ensuring a clean and precise finish. Sanding is often employed to achieve a smoother surface finish, enhancing the aesthetic appeal of HDPE parts.
Coating can further improve the aesthetic and functional properties of HDPE parts, providing added protection and improved appearance. Applying suitable post-processing techniques enhances the quality and performance of HDPE parts, meeting specific application requirements.
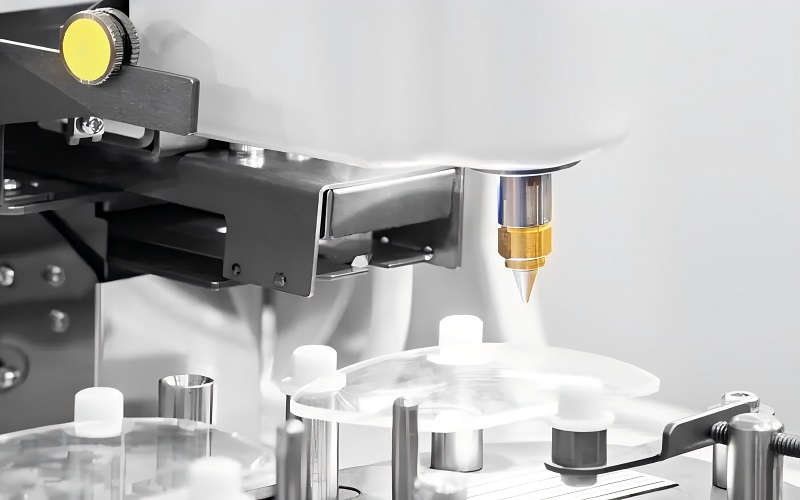
Choosing the Right Injection Molder for HDPE Projects
Selecting the right injection molder for HDPE projects is crucial for achieving high-quality results. Prioritize molders with proven expertise in handling high-density polyethylene materials. Their experience and knowledge can significantly impact the quality and efficiency of the molding process.
Consider the production capacity of the injection molders, especially for larger projects that require significant output capabilities. Additionally, cost assessment should encompass not just the mold price but also estimates for raw materials and operational expenses.
Careful evaluation of these factors helps manufacturers choose the right partner for their HDPE molding projects.
Environmental Considerations in HDPE Moulding
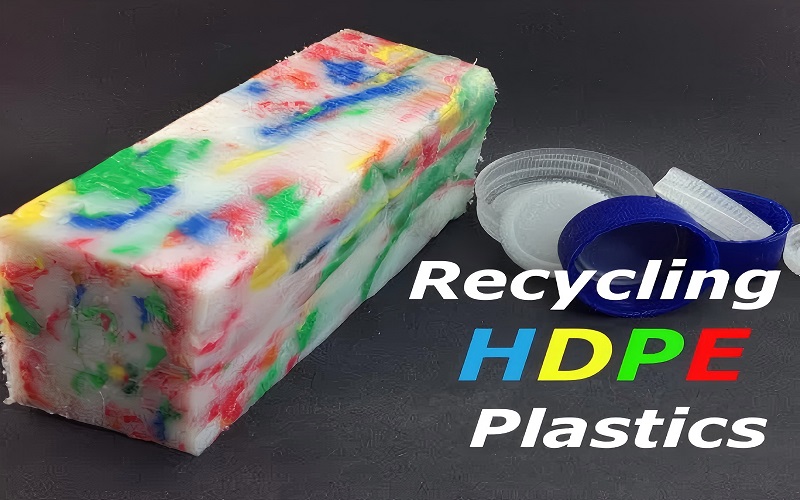
HDPE stands out as an environmentally friendly material due to its recyclability and energy-efficient production process. The material can be reprocessed without significant loss of properties, making it highly recyclable. Recycling bins are often made from HDPE, highlighting its durability and recyclability.
The production of HDPE is energy-efficient, consuming less energy compared to many other plastics. Additionally, HDPE’s durability reduces the need for frequent replacements, contributing to its low environmental impact over its lifecycle.
Choosing HDPE allows manufacturers to minimize their environmental footprint while benefiting from its excellent properties.
Summary
High-Density Polyethylene (HDPE) stands as a cornerstone in modern manufacturing, offering a unique blend of cost-effectiveness, durability, and versatility.
From understanding its basic properties and the injection molding process to recognizing the broad spectrum of applications, HDPE proves to be an invaluable material in various industries. By mastering the best practices and addressing potential challenges, manufacturers can optimize their production processes and achieve exceptional results.
In conclusion, HDPE’s benefits extend beyond its mechanical properties and cost advantages. Its environmental friendliness and recyclability make it a sustainable choice for the future.
As we continue to innovate and improve manufacturing techniques, HDPE will undoubtedly remain a pivotal material, driving efficiency and quality in production.
Frequently Asked Questions
What makes HDPE an ideal material for injection molding?
HDPE is an ideal material for injection molding because of its excellent chemical resistance, high strength-to-weight ratio, and thermal stability, ensuring the production of durable and reliable molded parts.
How does mold design impact the quality of HDPE molded parts?
Mold design significantly impacts the quality of HDPE molded parts by optimizing material flow, cooling, and part removal processes. High-quality molds result in better surface finishes and improved dimensional accuracy, ultimately leading to superior parts.
What are some common applications of HDPE molded products?
HDPE molded products are commonly used for water bottles, milk jugs, food storage containers, industrial pipes, and medical devices, owing to their durability and versatility. These applications highlight the material’s practicality across multiple sectors.
What are the challenges in HDPE injection molding, and how can they be addressed?
High mold shrinkage and warping are significant challenges in HDPE injection molding. These issues can be addressed by optimizing molding parameters such as temperature and pressure, alongside implementing effective quality control measures.
How does HDPE contribute to environmental sustainability?
HDPE significantly contributes to environmental sustainability through its recyclability and energy-efficient production. Its durability minimizes replacements, further lowering its overall environmental impact.