Plastic is truly ubiquitous in our lives and brings us a lot of convenience. From daily necessities to industrial production, plastic’s lightweight, durable, inexpensive and easy-to-process characteristics make it an indispensable material in modern society. However, the environmental problems brought by plastics are also getting more and more serious, affecting the ecological balance and human health.
However, despite the fact that plastics are everywhere in modern life, most people don’t realize how or where they are made.
Therefore, understanding the production process of plastic and its impact on the environment is crucial for us to make greener choices.
Raw Materials for Plastic Production
Wide Range of Sources:
The primary raw materials for plastic production come from fossil fuels, such as crude oil, natural gas, and coal. Take crude oil as an example: after being extracted from the ground, it’s transported to refineries for processing.
Through a series of complex steps, crude oil is refined into a substance called “naphtha.” Naphtha is a key raw material for making plastic, packed with hydrocarbon compounds that serve as the “building blocks” for plastic production.
The Critical Role of Hydrocarbons:
Hydrocarbons are compounds made up of carbon and hydrogen, essentially the “basic bricks” of plastic molecules.
In naphtha, these hydrocarbons undergo chemical reactions—like cracking and reforming—to transform into small molecular units called monomers, such as ethylene and propylene.
These monomers then link together through a process called polymerization, forming the various types of plastics we see around us, like polyethylene or polypropylene.
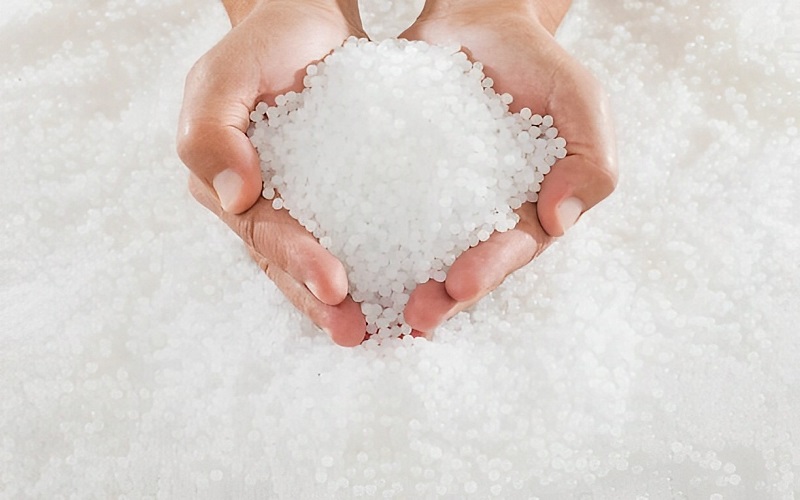
Types of Plastics
Thermoplastic Plastics
These soften when heated for shaping and harden when cooled, a process that can be repeated. This happens because molecular chains move when heated and align when cooled. Representatives include polyethylene (PE, for plastic bags), polypropylene (PP, for tableware), polyvinyl chloride (PVC, for pipes), and polystyrene (PS, for foam boxes), processed by injection molding or extrusion.
Thermosetting Plastics
During molding, they form a stable, cross-linked network structure that can’t be reshaped or softened by reheating. Representatives include phenolic resin (for Bakelite), epoxy resin (for adhesives), and unsaturated polyester resin (for fiberglass), ideal for strong, heat-resistant products like insulation parts and brake pads.
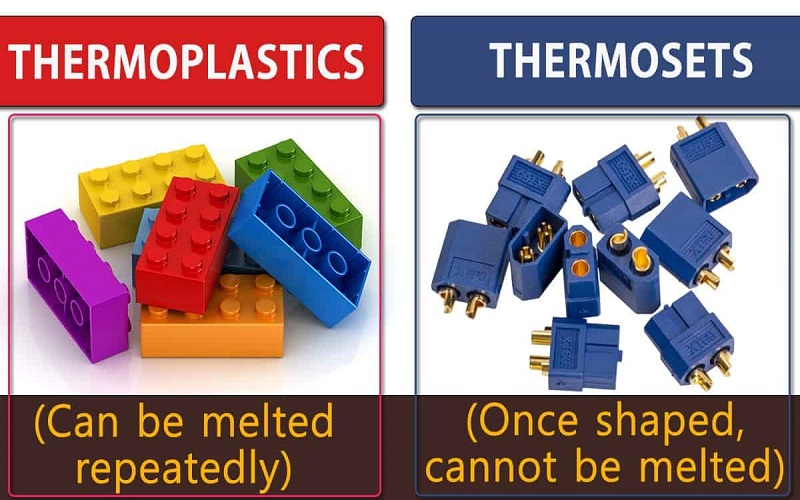
Plastic Production Process
Raw Material Extraction
The raw materials for plastic primarily come from fossil fuels, including crude oil, natural gas, and coal, each extracted through different methods.
Crude oil is typically obtained via offshore or onshore drilling platforms.
Natural gas is sometimes found alongside crude oil in the same oil fields, while at other times it exists in separate gas fields, requiring specialized equipment for extraction.
As for coal, it is mainly extracted through large-scale mining operations in coal mines, after which it is transported to processing plants.
These fossil fuels form the foundation of plastic production. Although their sources differ, they all provide the hydrocarbon compounds necessary for manufacturing plastics.
Among them, crude oil stands out as the most important raw material for plastic production.
Refining Crude Oil
Crude oil goes to a refinery, where it’s heated and split into parts in a tower. Light parts become gasoline or kerosene, and the middle part, naphtha, is taken out for making plastics.
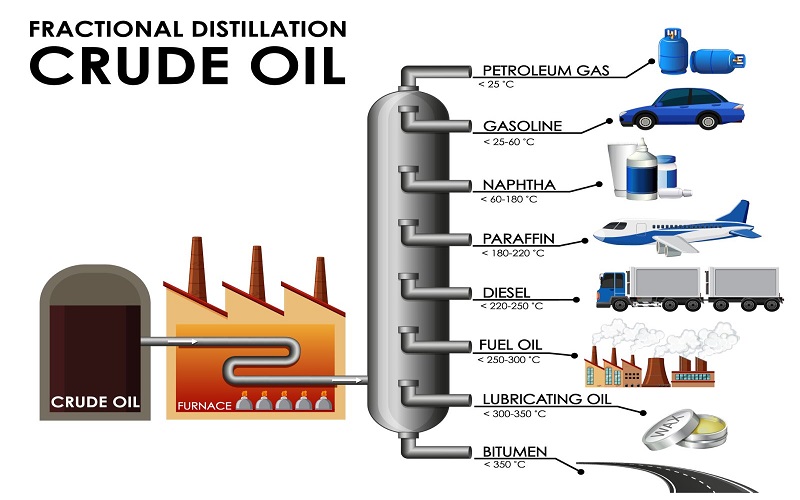
Breaking It Down
Naphtha is heated up and broken into small pieces, like ethylene and propylene. Natural gas can also be broken down into similar pieces. These are the building blocks of plastic.
Making Plastic
These small pieces are linked together into long chains, turning into plastics, like polyethylene for plastic bags.
Shaping Products
The plastic is melted and shaped into things like bottles or bags.
Polymerization of plastics
Polymerization reactions are particularly critical in the manufacture of plastics, and largely determine what properties and structures plastics have. Through the polymerization reaction, those small monomer molecules are linked into large polymer molecules, which gives plastics a variety of properties.
Common Polymerization Methods
Addition Polymerization
Addition polymerization uses small molecules with double bonds (e.g., ethylene, derived from crude oil). When the double bonds break, these monomers link together into a long chain without producing byproducts. For example, ethylene polymerizes into polyethylene, a flexible and stable material often used for plastic bags.
Condensation Polymerization:
Condensation polymerization involves two types of monomers (e.g., hexamethylenediamine and adipic acid) that connect into a long chain while releasing small byproducts, such as water. This process resembles a chemical bonding that sheds excess. For instance, hexamethylenediamine and adipic acid react to form nylon, which is strong and wear-resistant, suitable for mechanical parts and textile fibers.
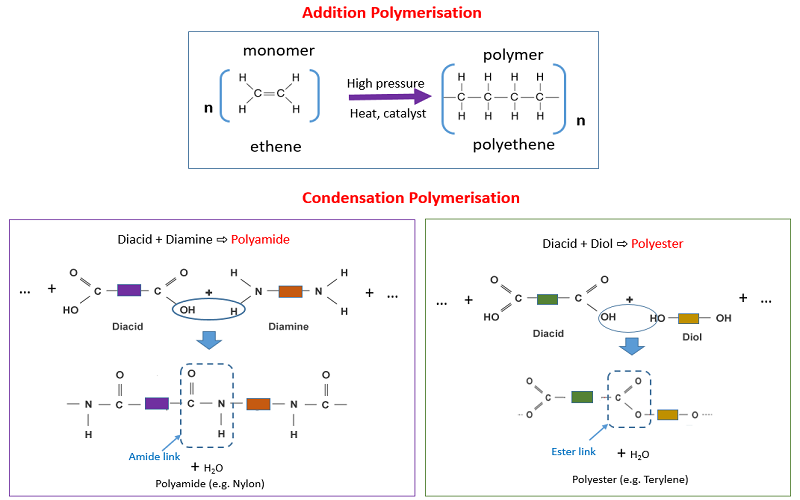
Common Plastic Polymers
- Polyethylene (PE):
Depending on the polymerization method and density, it is divided into high-density polyethylene (HDPE) and low-density polyethylene (LDPE). HDPE is sturdy and rigid, while LDPE is soft with high transparency.
- Polypropylene (PP):
It has high strength and heat resistance, capable of withstanding temperatures between 100°C and 150°C for extended periods.
- Polyvinyl Chloride (PVC):
It comes in rigid and soft forms. Rigid PVC is chemically stable and hard, while soft PVC, with added plasticizers, becomes flexible and elastic.
- Polystyrene (PS):
It is lightweight, offers good insulation, and is easy to mold. Ordinary PS is often used for disposable tableware and packaging materials, while high-impact polystyrene (HIPS), designed to resist impact, is used for appliance housings and toys.
Additives in Plastic Manufacturing
Additives play a crucial role in plastic production, enhancing performance and expanding applications.
Common additives include plasticizers, antioxidants, flame retardants, antistatic agents, colorants, and fillers.
Each serves a unique purpose: plasticizers make plastics more flexible, antioxidants delay aging, flame retardants reduce fire risks, antistatic agents prevent static buildup, colorants add vibrant hues, and fillers improve strength while lowering costs.
It’s these additives that make plastics more durable, safer, and suitable for a wide range of uses.
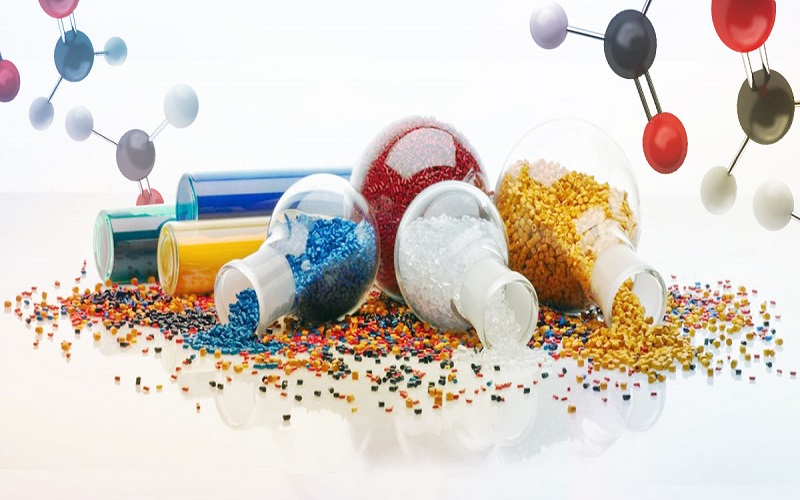
Plastic Molding Processes Mainly Include
Extrusion Molding:
Suitable for continuous-shaped products like pipes and sheets. Plastic melts under heat and is pushed by a screw through a shaped die, solidifying into the desired cross-section upon cooling.
Injection Molding: Used for complex, high-precision products like toys and electronic casings. Molten plastic is injected into a mold at high pressure and speed, then cooled and ejected. It offers high efficiency and dimensional accuracy.
Blow Molding:
Ideal for hollow products like bottles and containers. A preform is heated and inflated with compressed air to conform to the mold’s shape, producing stable, high-quality items.
Compression Molding:
Suited for high-temperature, high-strength products like electrical components and engine parts. Plastic is placed in a heated mold, compressed, and solidified, making it durable for harsh environments.
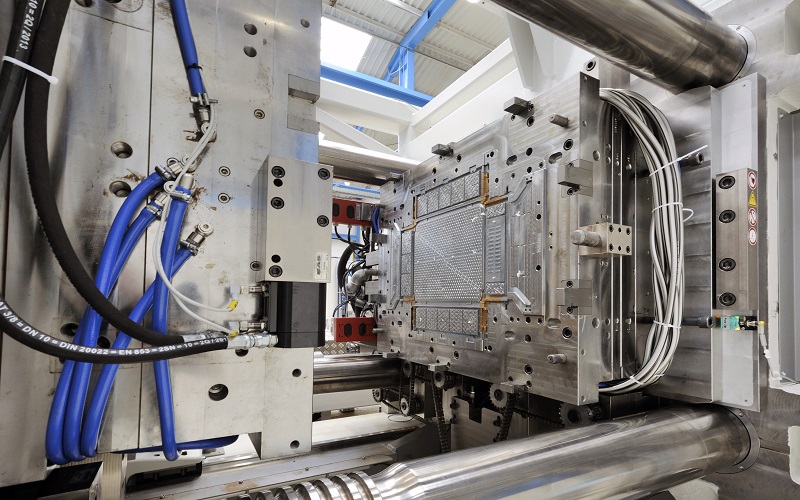
Conclusion
Plastic is made from polymers with added ingredients and processed through various molding techniques. It’s lightweight, durable, easy to shape, and widely used in everyday life and industry.
Otivic is dedicated to producing high-quality, precision plastic products — from everyday packaging to complex engineering components. With advanced craftsmanship and strict quality control, we help our customers make their products even better.
FAQs
What are the main raw materials for plastic production?
The main raw materials for plastic are synthetic resins, such as polyethylene (PE), polypropylene (PP), polyvinyl chloride (PVC), and polystyrene (PS). To improve performance, additives like plasticizers (to increase flexibility), stabilizers (to prevent aging), colorants (for coloring), and fillers (to enhance strength) are also added.
What environmental measures are taken in the plastic manufacturing process?
To reduce pollution, factories recycle waste plastic for reuse, switch to more eco-friendly biodegradable plastics, and reduce harmful gas emissions. Additionally, production equipment is improved to enhance energy efficiency and minimize wastewater, exhaust gases, and solid waste.
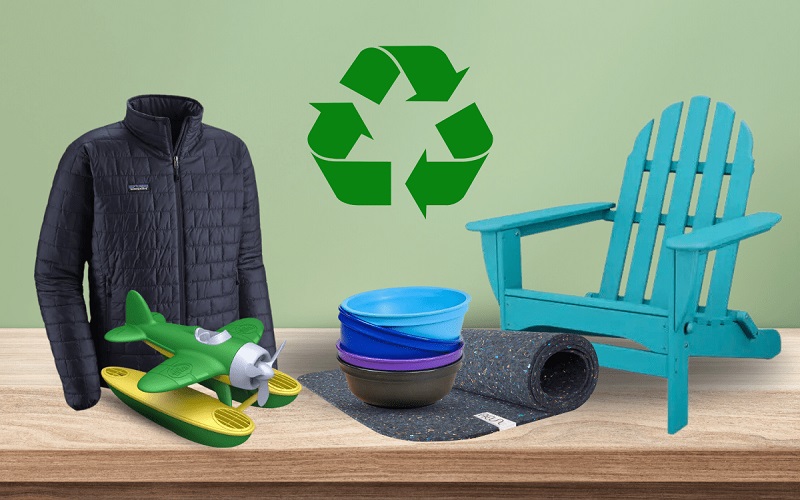
How do the molecular structure differences of different types of plastic determine the choice of molding process?
The molecular structure of plastic affects its melting point, fluidity, and toughness. For example:
Linear structures (like PE, PP) melt easily and are suitable for extrusion and blow molding.
Branched structures (like PVC) have a low melting point and are suitable for injection molding.
Cross-linked structures (like thermosetting plastics) do not melt when heated and are suitable for compression molding.
How can process parameters be adjusted to improve the transparency of plastic during manufacturing?
By increasing processing temperature, adding injection pressure, and speeding up the cooling rate, the transparency of plastic can be improved. These methods help reduce air bubbles, ensure uniform filling, and prevent excessive crystallization, thus enhancing transparency. Additionally, choosing transparent materials like polycarbonate (PC) also helps.
What are the causes and symptoms of plastic aging?
Plastic aging occurs due to exposure to sunlight, oxygen, high temperatures, or chemicals, which damages its molecular structure. Aged plastic may change color, become brittle, crack, or lose its gloss. Stabilizers are often added to delay aging.