Injection molded nylon is a preferred material for many industries due to its strength, flexibility, and chemical resistance.
This guide covers everything from its benefits and design considerations to common issues in the molding process. Discover why nylon is a top choice for high-performance parts.
Benefits of Injection Molded Nylon
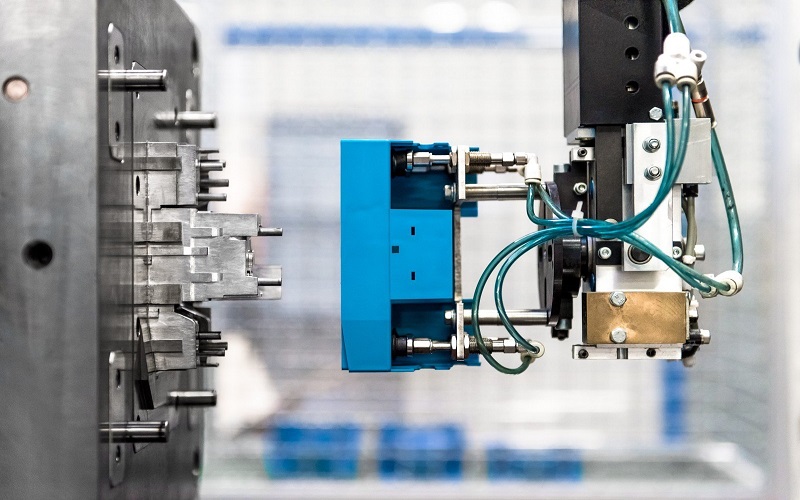
Nylon injection molding provides numerous advantages, making it a favored option across various industries. Its excellent mechanical properties include high tensile strength and impact resistance, suitable for demanding applications.
Nylon’s versatility and moldability enable the production of complex shapes and designs, catering to a wide range of uses from consumer goods to industrial components, including nylon plastic injection molding.
A notable feature of nylon plastic material is its chemical resistance, ensuring longevity and performance in various environments. This makes it ideal for applications involving exposure to different substances. These properties enhance the durability of nylon injection molded parts and reduce maintenance needs, adding to its cost-effectiveness.
The following subsections explore specific benefits like low friction and wear resistance, high tensile strength, and chemical resistance, highlighting why nylon is a superior choice for injection molding applications.
Low Friction and Wear Resistance
Nylon’s low friction makes it ideal for moving mechanical equipment parts, such as gears. This property reduces wear and enhances efficiency in mechanical systems, resulting in longer component life and reduced maintenance needs.
Automotive components and conveyor systems, for instance, benefit significantly from these properties, ensuring smooth and reliable operation.
High Tensile Strength
Nylon’s tensile strength, comparable to some metals, makes it a robust material for structural applications. Combined with excellent flexural strength, reinforced nylon and reinforced materials are ideal for components under stress.
Enhancements like adding glass fibers or increasing mold temperatures further improve nylon’s suitability for demanding applications.
Chemical Resistance
Nylon’s excellent wear resistance and excellent chemical resistance to chemicals, oils, solvents, and fuels makes it a reliable choice for various industrial applications, including those involving synthetic polymer components. This ensures that nylon parts remain durable and functional even when exposed to harsh substances.
This property is particularly beneficial in environments where versatile material degradation could compromise performance and safety.
Design Considerations for Nylon Injection Molding
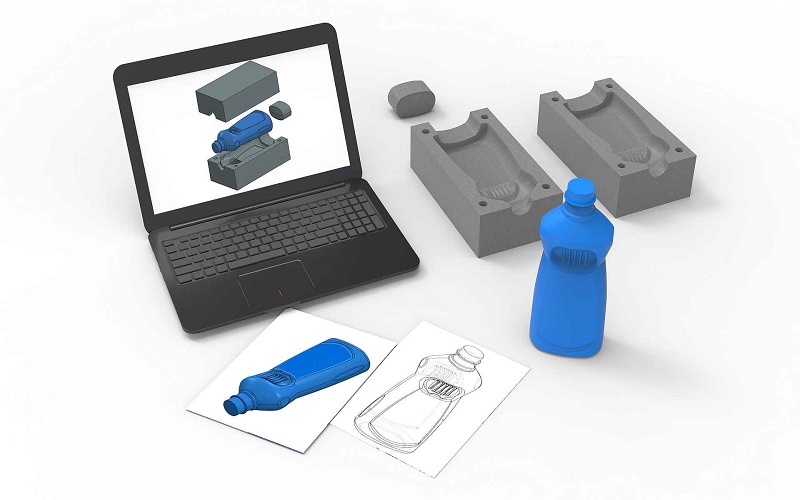
Designing for nylon injection molding requires several critical considerations to ensure optimal outcomes. Factors like wall thickness, draft angles, and radii and transitions are essential for maintaining part strength and dimensional stability. Precise process control and careful design can address nylon’s drawbacks, resulting in high-quality injection molded parts.
Integrating 3D printing with traditional nylon injection molding increases design flexibility, allowing for complex geometries and rapid prototyping. This integration reduces time and costs while enhancing the overall quality of the final product.
The following subsections provide detailed guidance on optimal wall thickness, draft angles, and radii and transitions, ensuring successful nylon injection molding applications.
Optimal Wall Thickness
Optimal wall thickness is crucial for part strength and dimensional stability in nylon injection molded parts. The recommended wall thickness for most nylon plastic parts is between 2-4 mm, with a maximum of 6 mm for specific applications.
Uneven wall thickness can exacerbate warpage; gradual changes in wall thickness should not exceed 15% between adjacent areas.
Draft Angles
Draft angles facilitate easy part ejection from molds and reduce stress in the parts. A larger draft angle is recommended for nylon parts to prevent sticking and ensure smooth ejection.
Designing bosses and ribs with appropriate draft angles and adequate wall thickness is necessary for effective molding.
Radii and Transitions
Smooth transitions and appropriate radii in nylon injection molding reduce stress concentrations that can lead to part failure. The minimum corner radius recommended for nylon parts is greater than 0.5 mm, with the ideal corner radius being 75% of the nominal wall thickness.
These design considerations ensure the durability, fatigue resistance, and performance of the final product.
Processing Parameters for Nylon Injection Molding
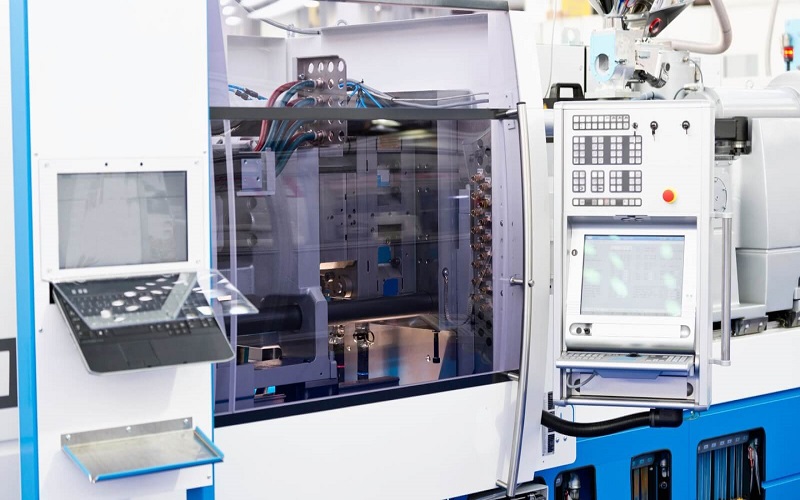
Key processing parameters for nylon injection molding include molding temperature, injection pressure, and cooling time. Proper control of these parameters is crucial for achieving high-quality injection molded parts within the mold cavity. Thorough drying of nylon before injection molding eliminates moisture content and prevents defects.
Recent advancements in the nylon injection molding process make the process more efficient and improve overall material properties. Innovations focus on enhancing tensile strength, managing moisture content, and reducing defects within the mold cavity.
The following subsections delve into specifics on molding temperature, injection pressure, and cooling time, providing detailed guidance for optimal nylon injection molding.
Molding Temperature
Proper temperature control in nylon injection molding ensures consistent melt viscosity, flow, and cooling. For nylon 6, the typical melting temperature ranges from 515°F to 565°F, while the mold temperature should be maintained between 120°F and 220°F.
Optimal molding temperatures prevent thermal degradation and ensure high temperatures parts.
Injection Pressure
Adequate injection pressure ensures complete mold filling and achieves the desired part shape with injection molds. Higher appropriate injection pressure, typically between 1,000 to 1,800 psi, is needed for nylon due to its higher viscosity.
Excessive injection pressure can lead to flash defects and turbulent flow, causing air bubbles in the product.
Cooling Time
Proper cooling time in nylon injection molding prevents warping and shrinkage. The cooling time is influenced by factors such as the thickness of the part and the effectiveness of the cooling system.
Extending the cooling time or uniformly designing wall thickness can counteract warpage effectively.
Types of Nylon for Injection Molding
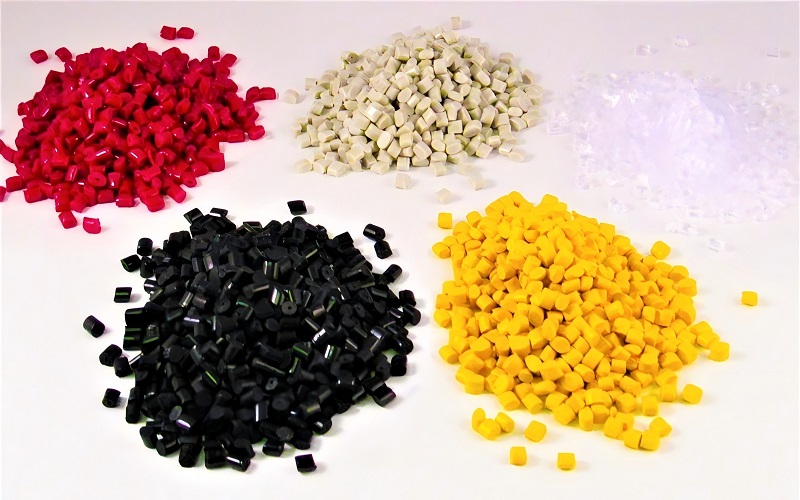
Several types of nylon are used in injection molding, each with distinct properties and applications. Common types include Nylon 6, Nylon 66, and glass-filled nylon. Understanding the specific characteristics of each type helps select the right material for different injection molding applications.
Nylon’s ability to blend with materials like glass fibers enhances its strength, making it suitable for demanding applications. Adding glass fibers reduces shrinkage nylon and improves dimensional stability, further enhancing the performance of nylon injection molded parts.
The following subsections provide detailed information on Nylon 6, Nylon 66, and glass-filled nylon, highlighting their properties and uses in injection molding.
Nylon 6 (PA6)
Nylon 6 is widely used in the injection molding industry due to its excellent mechanical properties and superior impact resistance. Its lower melting point facilitates processing, making it ideal for applications requiring toughness and durability.
Nylon 66 (PA66)
Nylon 66 offers improved mechanical properties, making it suitable for applications requiring high strength and durability. Its high strength, durability, and cost-effectiveness make it an excellent choice for automotive parts and other demanding applications.
Glass-Filled Nylon
Glass-filled nylon incorporates glass fibers to enhance its overall performance, significantly increasing its tensile strength while sacrificing some flexibility. This type of nylon is ideal for applications requiring high strength and rigidity, such as automotive and industrial components, particularly those utilizing glass fiber.
Preparation and Handling of Nylon Materials
Proper preparation and handling of nylon materials prevent defects and ensure high-quality injection molded parts. Nylon pellets should be preheated before molding to enhance flow and shaping. Thoroughly drying the material is also crucial, as moisture content can cause bubbles and other defects in the final product.
The following subsections focus on drying nylon pellets and controlling moisture content, providing guidelines for preparing nylon plastic for injection molding.
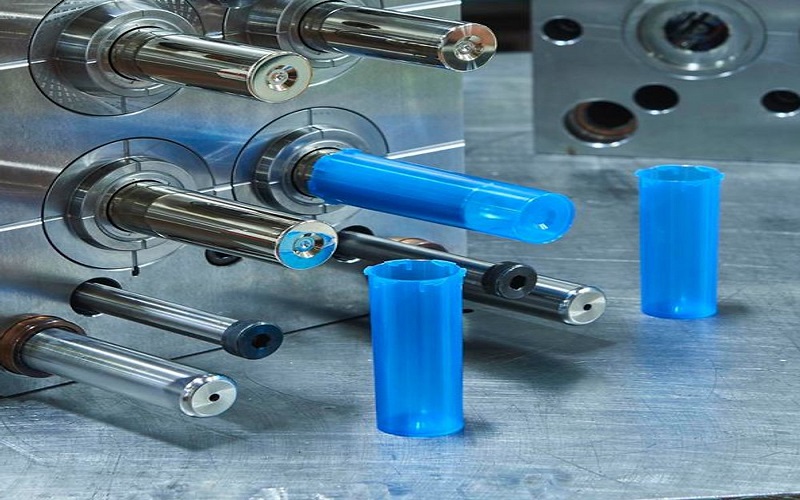
Drying Nylon Pellets
Thorough drying of nylon prevents defects during the molding process. Nylon’s high moisture absorption rate can lead to quality issues if not properly managed.
Vacuum drying is recommended for effective moisture removal, with drying times and drying temperature for nylon 1010 typically ranging from 20-24 hours using an ordinary oven.
Moisture Content Control
Excess moisture in nylon during injection molding can cause defects like voids and surface defects and surface irregularities. Maintaining optimal moisture levels during storage and processing water absorption absorbs moisture and prevents these issues.
Consistent monitoring and proper temperature control ensure high-quality nylon production.
Common Issues and Solutions in Nylon Injection Molding
Despite its benefits, nylon injection molding can present several challenges. Common issues include warpage, sink marks, and flash, which can compromise the quality and performance of the final product.
A comprehensive quality control plan and techniques like statistical process control (SPC) can help monitor and control the injection molding process for better quality.
The following subsections detail specific issues and their solutions, providing practical advice for minimizing defects in nylon injection molding.
Warpage
Warpage, or distortion of molded parts, is a common issue in nylon injection molding, primarily due to nylon’s shrinkage rate. Warpage is typically caused by uneven cooling and excessive internal stress.
Minimizing this issue requires proper cooling and optimizing mold design.
Sink Marks
Sink marks in molded nylon parts occur due to insufficient material flow and inadequate cooling. Adjustments in injection speed and pressure, along with optimized cooling, can significantly improve the final product’s surface quality.
Flash
Flash, defined as excess material forming thin protrusions on the part, can be avoided by ensuring the injection pressure is not excessively high. Proper mold clamping and precise control of injection parameters are also necessary to prevent this common defect.
Applications of Injection Molded Nylon
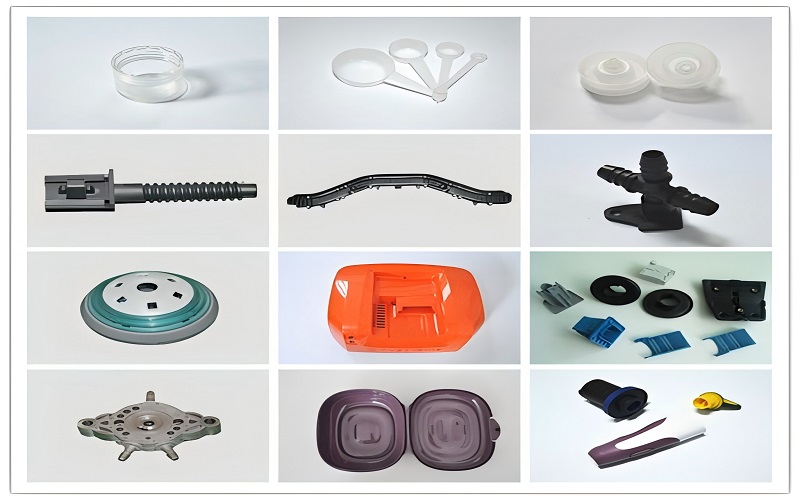
Injection molded nylon parts are used in various industries due to their durability, chemical resistance, and versatility. From automotive components that endure harsh conditions to intricate consumer goods, nylon’s properties make it an ideal choice. Its lightweight nature also contributes to lower shipping costs, making it a more sustainable manufacturing option.
Nylon’s biocompatibility and sterilizability extend its use into medical devices, while its precision and tight tolerances make it suitable for packaging solutions. The following subsections explore specific applications in automotive components, electrical connectors, and consumer goods.
Automotive Components
Nylon’s high strength and heat resistant properties make it ideal for manufacturing components in harsh automotive environments, including those that require molten nylon. It is often chosen for fasteners and clips due to its high melting point, lightweight nature, and durability.
These properties ensure that nylon components can withstand the demanding conditions of automotive applications.
Electrical Connectors
Nylon exhibits excellent insulating properties, making it suitable for electrical applications. Different types of nylon, including Nylon 6, Nylon 66, and glass-filled nylon, offer various mechanical and thermal properties beneficial for electrical connectors.
These properties are essential for reliable performance in complex electrical systems, such as those found in automotive components.
Consumer Goods
Nylon components are frequently found in consumer goods like sports equipment and household products due to their versatility. The ability of nylon to be molded into complex shapes is advantageous in the production of intricate consumer goods, ensuring high-quality and durable products.
Innovations in Nylon Injection Molding
Recent trends in nylon injection molding focus on the adoption of sustainable practices and enhancing material performance. Efforts are ongoing to develop recycling methods for nylon waste, promoting sustainability in the production process. These innovations aim to meet the increasing demands for high-performance materials while reducing environmental impact.
Integrating additive manufacturing, such as 3D printing, with traditional nylon molding enhances design flexibility and allows for complex geometries that are difficult to achieve with conventional methods. This integration signifies a progressive step in the manufacturing process, making the process more adaptable and efficient.
Additive Manufacturing Integration
The combination of 3D printing with traditional nylon molding enhances design flexibility and allows for the creation of complex geometries.
This integration not only supports rapid prototyping but also signifies a future where manufacturing is more adaptable and efficient, catering to custom designs and innovative applications.
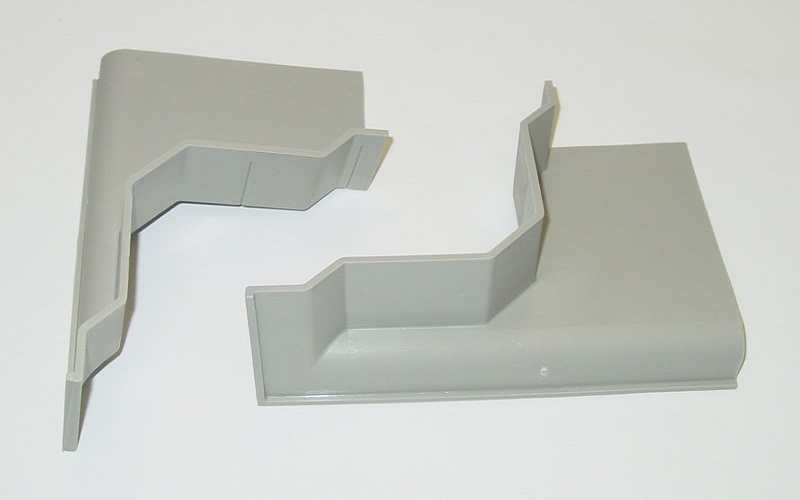
Sustainable Practices
Efforts to develop recycling methods for nylon waste are crucial for promoting sustainability in the production process. Recycling nylon reduces environmental impact by repurposing used materials rather than relying on new raw materials, contributing to resource conservation and environmental protection.
Summary
In summary, nylon injection molding offers numerous benefits, including excellent mechanical properties, chemical resistance, and versatility.
Proper design considerations and control of processing parameters are essential for achieving high-quality injection molded parts. Understanding the different types of nylon and their specific applications further enhances the effectiveness of this manufacturing process.
As we move forward, innovations such as additive manufacturing integration and sustainable practices will continue to shape the future of nylon injection molding. By embracing these advancements, manufacturers can meet the growing demands for high-performance and environmentally friendly materials, ensuring a bright future for nylon in various industries.
Frequently Asked Questions
What are the main benefits of using nylon in injection molding?
Nylon provides exceptional mechanical properties such as high tensile strength and impact resistance, along with excellent chemical resistance, making it an ideal choice for demanding applications and ensuring longevity in various environments.
How does nylon’s low friction and wear resistance benefit mechanical parts?
Nylon’s low friction and wear resistance significantly enhance the efficiency and durability of mechanical parts, resulting in longer component life and lower maintenance requirements. This makes it particularly effective for applications involving moving components, such as gears and conveyor systems.
What are the key design considerations for nylon injection molding?
Key design considerations for nylon injection molding include optimal wall thickness, appropriate draft angles, and smooth transitions and radii, as these ensure part strength, dimensional stability, and facilitate mold ejection. Prioritizing these elements is crucial for successful molding outcomes.
How do processing parameters like molding temperature and injection pressure affect nylon injection molding?
Processing parameters such as molding temperature and injection pressure significantly influence the quality of nylon injection molded parts. Optimal temperature ensures consistent melt viscosity and flow, while adequate injection pressure guarantees complete mold filling, avoiding defects like flash.
What are some common issues in nylon injection molding, and how can they be resolved?
Common issues in nylon injection molding, such as warpage, sink marks, and flash, can be effectively resolved by optimizing mold design, adjusting injection speed and pressure, and controlling injection pressure along with proper mold clamping. Implementing these strategies will enhance the overall quality of your molded parts.