Injection molding hot runner systems maintain molten plastic flow into multiple mold cavities, boosting efficiency and reducing waste.
This article discusses their benefits, key components, operational principles, and compares hot runners to cold runners.
Understanding Hot Runner Systems
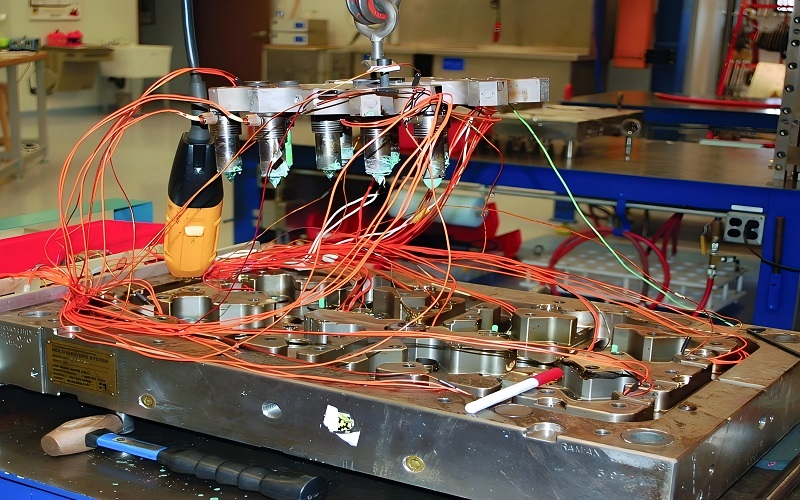
A hot runner system is a sophisticated mechanism designed to deliver liquid plastic to multiple mold cavities using a heated manifold. Unlike cold runner molds, which allow plastic to solidify in the runners, hot runner systems maintain a continuous flow of molten plastic from the injection molding machine to the mold gate location.
This prevents the material from solidifying within the manifold, improving efficiency and effectiveness in the injection molding process.
Components of Hot Runner Systems
Key components of any hot runner system include the hot manifold, nozzles, temperature controllers, and heaters. The manifold plays a crucial role in keeping the plastic in a molten state, while the nozzles facilitate the flow of plastic into the mold cavities.
Dedicated temperature controllers maintain precision temperature control, ensuring consistent quality and efficiency in the injection molding process.
How Hot Runners Work
By injecting molten plastic directly into mold cavities, hot runners minimize waste and significantly improve cycle times. The plastic remains in a molten state as molten plastic flows through the runner system, ensuring a continuous and efficient plastic injection molding process. This process is crucial for understanding plastic flow dynamics.
Emerging technologies enhance the speed and consistency of hot runners, making them indispensable in modern injection molded injection molding.
Benefits of Using Hot Runner Systems
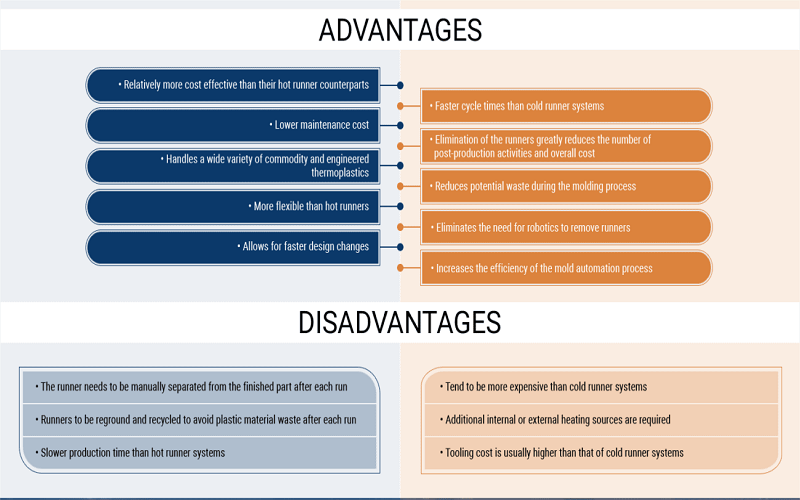
The benefits of hot runner systems in injection molding are manifold. They enhance production efficiency, improve part quality, and reduce material waste. Hot runners improve processing efficiency and produce higher quality molded parts by eliminating waste and reducing cycle times.
The adoption of hot runner systems is expected to grow significantly as demand for efficient and cost-effective injection molding solutions increases.
Enhanced Production Efficiency
Hot runners enhance production efficiency by allowing more effective material flow control, reducing cycle times, and speeding up processing. Additionally, hot runner systems demand less energy due to their smaller barrel sizes, contributing to overall energy savings.
Calibrating temperature settings during installation achieves consistent melt quality and part accuracy, further boosting production efficiency.
Superior Part Quality
Hot runner systems improve molded part quality by ensuring a consistent flow of molten plastic, reducing defects, and enhancing dimensional accuracy and surface finish.
An optimized hot runner design achieves better dimensional accuracy in molded parts, making them ideal for high-precision applications.
Reduced Material Waste
One of the standout benefits of hot runner systems is the reduction of material waste. Hot runners minimize scrap material by eliminating solidified runners during the injection molding process. The continuous flow of molten material reduces the need for regrinding runners, resulting in less waste and faster production times.
Advancements in hot runner technology aim to lower energy usage and minimize material waste, promoting sustainable manufacturing.
Comparing Hot Runner and Cold Runner Systems
Hot runner systems offer advantages in efficiency, quality, and cost-effectiveness compared to cold runner systems.
Hot runners eliminate the need for cold runners by injecting molten plastic directly into injection mold cavities, reducing plastic waste.
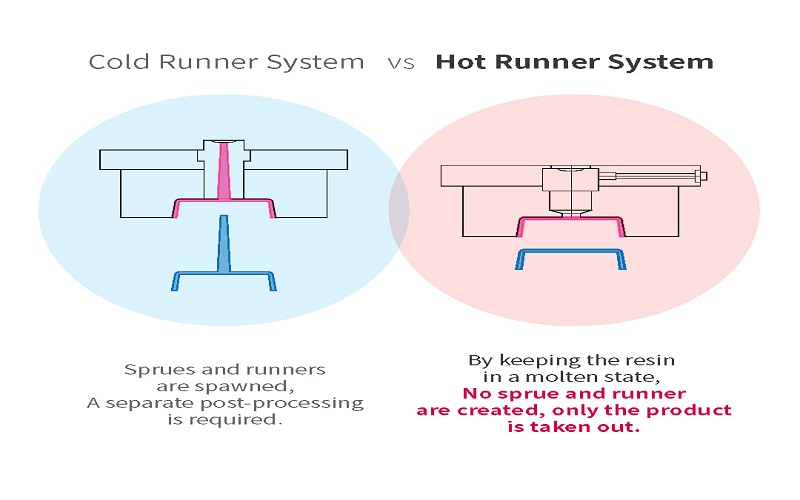
Cold Runner System Limitations
Cold runner systems can impact efficiency and quality by prolonging cycle times since the melt is supplied to the cavity during the pack phase.
Cold runners are a costly waste of resin that must be discarded or recycled. Plastic products formed with cold runners often have more blemishes due to larger gates, and gun-drilled runner manifolds in cold runner systems can have dead spots where material cures.
Hot Runner vs Cold Runner: Key Differences
The efficiency and quality of molded parts are key differences between hot runner and cold runner systems. Injecting plastic directly into mold cavities, hot runners promote continuous flow and reduce cycle times. Well-designed hot runner gate placement improves surface quality and eliminates the need for runner trimming.
Hot runner molds are ideal for high-volume production because they eliminate surface imperfections and minimize material waste.
Types of Hot Runner Systems
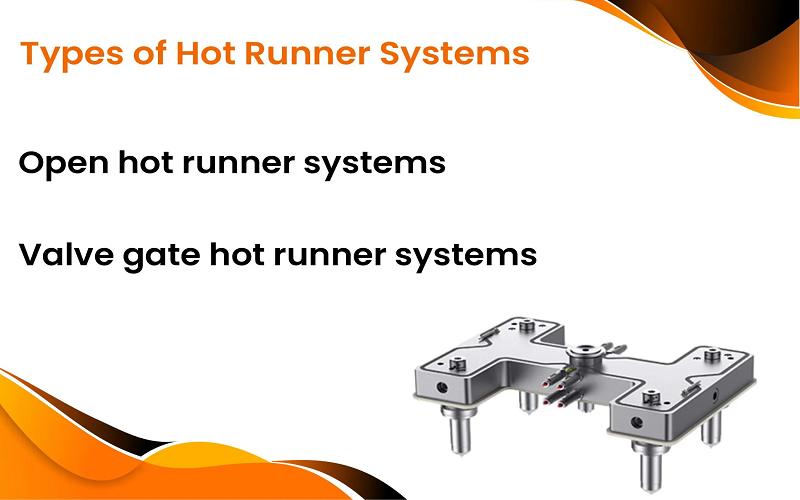
Hot runner systems come in two main types: hot tip and valve gate, each serving different applications and allowing manufacturers to choose the best option based on specific needs.
Hot Tip Hot Runner Systems
Hot tip hot runner systems are a standard, general-purpose type that use a hot manifold to keep the material molten. They are more economical than valve gate systems, making them a cost-effective option for manufacturers. Hot tip hot runner systems are ideal for mass-producing simple parts due to their efficient operation.
Advancements in nozzle design, such as heated nozzle flanges, have improved the precision and efficiency of hot runner systems.
Valve Gate Hot Runner Systems
Valve gate hot runner systems are suitable for highly aesthetic projects, featuring a mechanical valve that prevents visible marks on the molded part, ensuring precise control and superior surface quality.
Choosing the Right Hot Runner System
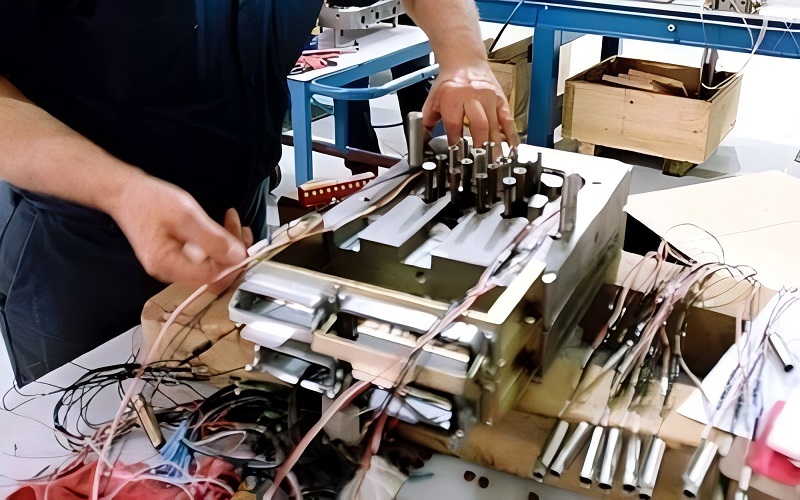
Selecting the appropriate hot runner system requires careful consideration of several factors that must align with production requirements. Regular cleaning of hot runner molds prevents clogs that can lead to production defects.
Factors to Consider
Price, quantity, delivery time, and technical aspects are factors to consider when selecting a hot runner system. Though initial investment and maintenance costs for hot runner systems are generally higher than for cold runners, they are considered investments in efficiency and quality.
Standard hot runner systems are more readily available, cost less, and have shorter delivery times compared to custom solutions.
Collaborating with Suppliers
Working with reputable suppliers is crucial for achieving optimal performance and compatibility of hot runner systems. Discussing hot runner systems with your service provider is important. Determine which manufacturer they use and why.
Understanding support and compatibility issues ensures seamless integration into the manufacturing process.
Implementing Hot Runner Systems in Injection Molding
Implementing hot runner systems in injection molding requires seamless integration with existing machinery to optimize performance. Proper installation and setup are vital for effective operation and longevity of the system.
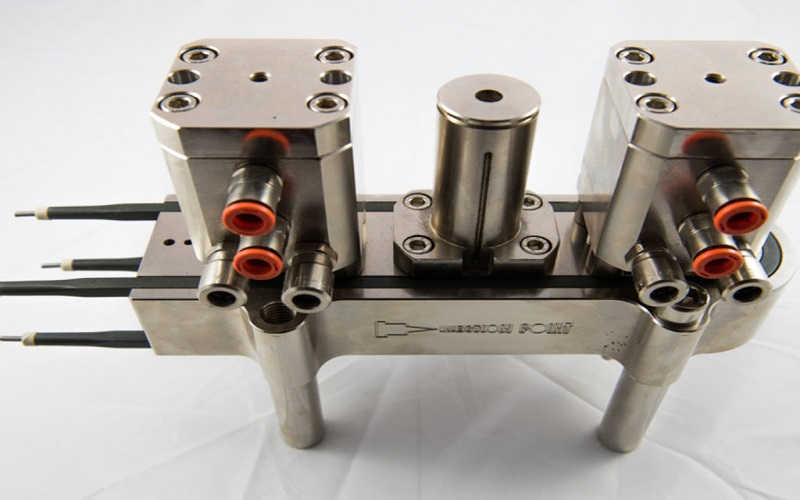
Installation and Setup
To optimize performance, install the hot runner system on a stable, level surface to prevent misalignment. Proper alignment with the mold ensures effective operation by allowing molten plastic to flow efficiently into the mold cavities.
Maintenance and Troubleshooting
Routine cleaning of hot runner systems prevents clogs and ensures uninterrupted production. Using appropriate thermal insulation during installation enhances the efficiency of hot runner systems.
Recent developments integrate sensor technology into hot runner systems, enabling real-time monitoring of temperature and pressure to enhance process control. These advancements help identify potential issues early, minimizing downtime and maintaining high production standards.
The Future of Hot Runner Technology

The future of hot runner technology holds great potential. Emerging trends focus on reducing resin use and improving speed and consistency, shaping the landscape of injection molding.
Increased awareness of hot runner systems will lead to more informed decisions by molders, fostering further advancements in the field.
Innovations in Temperature Control
Recent developments enhance temperature control technologies, improving the precision and reliability of hot runner systems. Effective temperature control ensures consistent melt temperatures and minimizes defects in hot runner systems used in injection molding.
Innovations in temperature control achieve greater precision in maintaining consistent melt temperatures, critical for part quality and overall efficiency.
Sustainability and Efficiency Improvements
Advancements in hot runner technology focus on both efficiency and sustainability. Thermal insulation around hot runner components enhances energy efficiency by minimizing heat loss. Energy efficiency reduces manufacturing costs and minimizes environmental impacts.
Adopting energy-efficient practices promotes sustainable manufacturing, lowers operational costs, and reduces the carbon footprint.
Summary
In conclusion, optimizing your injection molding hot runner system involves understanding its components, benefits, and types, as well as implementing proper installation, maintenance, and collaboration with suppliers. Hot runner systems offer significant advantages in production efficiency, part quality, and material waste reduction.
As technology advances, innovations in temperature control and sustainability will continue to shape the future of hot runner technology.
By staying informed and proactive, manufacturers can leverage these advancements to achieve superior performance and sustainability in their injection molding processes.
Frequently Asked Questions
What is a runner in injection molding?
A runner in injection molding is a channel within the mold that facilitates the flow of plastic from the nozzle to the cavity. Understanding the influence of flow channel dimensions on pressure is crucial for optimizing the molding process.
Which is better hot runner or cold runner injection molding?
If you prioritize speed and efficiency in large volumes, a hot runner system is better, while a cold runner system is more suitable for heat-sensitive polymers. Your specific production needs should guide your choice.
What are the main components of a hot runner system?
The main components of a hot runner system consist of the hot manifold, nozzles, temperature controllers, and heaters. These elements work together to maintain the temperature of the molten plastic, ensuring efficient injection molding.
How do hot runner systems improve production efficiency?
Hot runner systems improve production efficiency by lowering cycle times and reducing energy consumption, resulting in faster processing and significant cost savings.
What are the key differences between hot runner and cold runner systems?
The key difference is that hot runner systems facilitate continuous flow of plastic directly into mold cavities, which reduces cycle times, while cold runner systems involve a sprue and runners, leading to more waste and longer cycle times. This makes hot runners more efficient for high-volume production.