Injection molding tolerance is all about the acceptable range of dimensional accuracy for molded parts. It’s crucial for ensuring components fit and function correctly.
In this article, you’ll learn about different types of tolerances, why they matter, and how to achieve them effectively.
Defining Injection Molding Tolerances
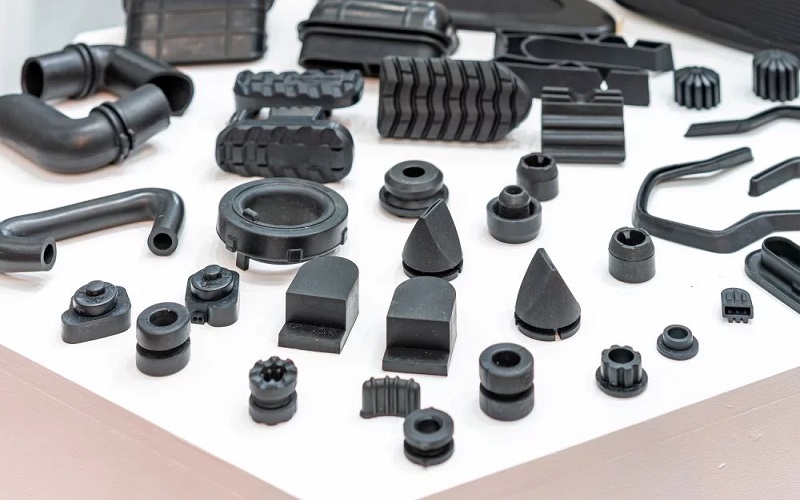
Plastic injection molding tolerances refer to the acceptable ranges of dimensional accuracy for molded parts. These tolerances are essential in ensuring that injection molded parts fit and function correctly within their intended applications.
The components of tolerances in injection molding include the nominal dimension, upper and lower tolerances, which together define the range within which a part’s dimensions must fall. Injection molding tolerances important in achieving high-quality results.
There are two primary types of tolerances relevant in injection molding: machining tolerance and resin tolerance. Machining tolerance typically maintains a precision of +/- 0.003 inches, while resin tolerance can be up to +/- 0.002 inches per inch. The distinction between these two types lies in the material and process used, with machining tolerance generally being more precise due to the controlled nature of the machining process.
Tight tolerances in injection molding ensure the effective functioning of assembled products. Tight tolerances help prevent part underperformance or failure, which can arise from dimensional deviations. The required precision for the part determines the type of injection molding tolerance needed, necessitating the application of appropriate tolerances for each specific application.
The Importance of Injection Molding Tolerances
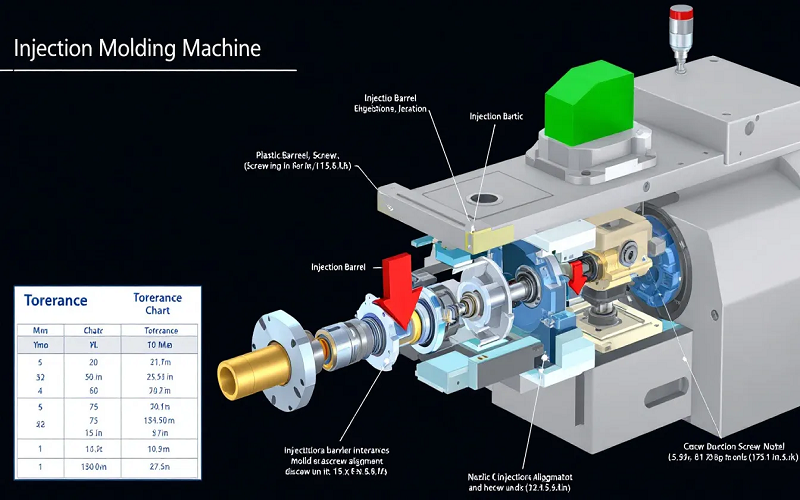
Precise tolerances ensure that injection molded parts fit and function correctly in their intended applications. Parts manufactured with tight tolerances fit together seamlessly, ensuring the final product’s overall functionality and reliability. In assemblies with multiple components, even minor dimensional deviations can cause significant issues.
Dimensional variations from molds, machines, materials, and the environment necessitate tight tolerances. Issues in product use can arise from inappropriate tolerance values, indicating insufficient knowledge in injection molding. Selecting the right material and determining optimal tolerance ranges early in the design phase avoids costly redesigns and ensures the final product’s quality and functionality.
For larger components and assemblies with multiple parts, tight tolerances prevent fitting issues. Errors in the location and size of holes on plastic molded parts can result in assembly errors and loss of function. Higher shrink rates make tolerances harder to control, which poses a challenge in maintaining tight tolerances. Choosing appropriate tolerances for injection molded parts ensures quality and functionality, ultimately leading to successful injection molding projects.
Standards for Injection Molding Tolerances
Standards play a crucial role in defining and maintaining injection molding tolerances. ISO 2768 serves as a well-recognized standard for general tolerances in various manufacturing processes, including injection molding. This standard provides guidelines for acceptable dimensional deviations, ensuring consistency and quality across different manufacturing environments.
The DIN 16901 standard outlines tolerance specifications specifically for injection molded components, providing more detailed guidance on dimensional tolerances for this manufacturing process. Typical tolerances for injection molded components can range up to +/- 0.1 mm, while tight tolerances are generally defined as being within +/- 0.002 inches, falling within the established acceptable range of the desired tolerance range and a larger tolerance range.
For critical applications, standard injection molding tolerances are typically around 0.025 mm, ensuring high precision and reliability in the final parts, which often require tight tolerance.
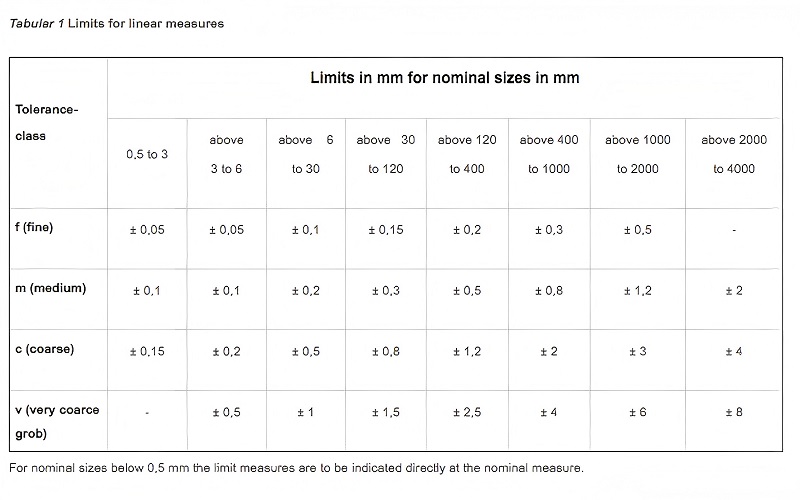
Key Factors Affecting Injection Molding Tolerances
Several key factors influence achieving precise injection molding tolerances. Material shrinkage, part design, and injection mold quality are the primary elements that significantly influence the final dimensions of injection molded parts and injection molds.
Addressing these factors collectively optimizes injection molding tolerances and ensures high-quality parts with consistent dimensional accuracy.
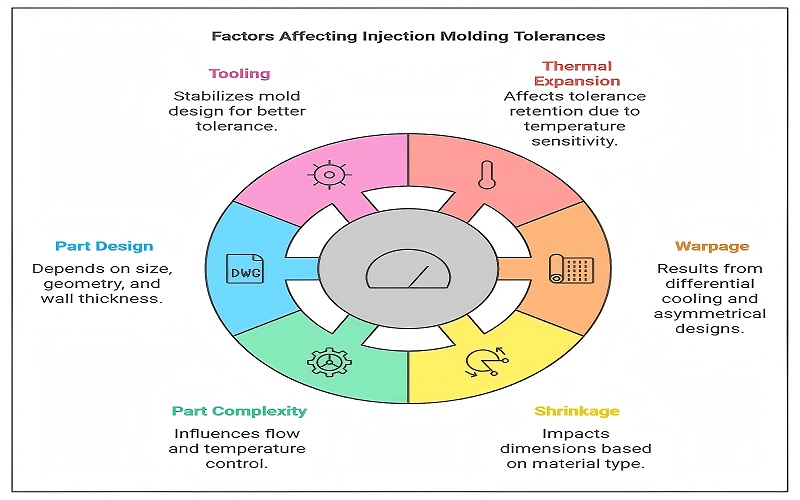
Material Shrinkage
Material shrinkage is a critical factor that affects dimensional tolerances in injection molding. The shrinkage rate of injection molded parts is heavily influenced by the type of plastic used, with different resins exhibiting varying shrinkage behaviors.
Understanding the mold shrinkage rates of a chosen plastic resin is crucial for accurate tooling and part design. As plastic is injected into a mold, it cools and shrinks, with the rate of shrinkage depending on the resin used. This cooling and shrinking process can lead to potential variances in final dimensions, making it essential to account for these properties, including shrinkage variation, in design and processing.
Semi-crystalline resins, for example, have higher shrinkage rates than amorphous resins. Consider shrinkage rate differences during the design phase to ensure parts meet desired dimensional tolerances. Additives can also affect shrinkage rates, further complicating the ability to achieve precise tolerances.
Selecting the right injection molding material and understanding its shrinkage characteristics are crucial for maintaining tight tolerances in injection molding.
Part Design
Part design significantly influences the achievable tolerances in the final product. Larger dimensions make it more challenging to control tight tolerances, as different sections of the plastic parts may shrink at varying rates. Understanding part geometry is vital for producing high-quality injection molded components.
Part complexity affects material flow, tooling design, filling speed, and cooling management, all of which are crucial for maintaining tight tolerances and enabling rapid adjustments in cnc machining. Design features like support ribs can enhance strength without increasing material thickness, aiding in maintaining tolerances.
Using coring bosses improves load distribution and the part’s rigidity, further contributing to achieving precise dimensions. Considering size during the design phase minimizes distortions that affect tolerances, ensuring that parts meet the required specifications.
Mold Quality
The quality of the mold tooling is paramount in achieving targeted injection molding tolerances. The design of the mold tool, including the layout of cooling channels, is crucial for ensuring consistent heating and cooling, which in turn maintains dimensional accuracy and mold temperature. Regular maintenance of molds is necessary to preserve precision and prevent dimensional drift over time. Achieving tight tolerances requires careful control of injection pressure to minimize warpage during the cooling phase.
Mold quality directly affects the final dimensions of injection molded parts. High-quality molds, designed and maintained with precision, ensure that parts are produced with consistent tolerances, reducing the likelihood of defects and improving overall product quality during the molding process.
Manufacturers aiming to hold tight tolerances must invest in superior mold quality.
Optimizing Injection Molding Tolerances
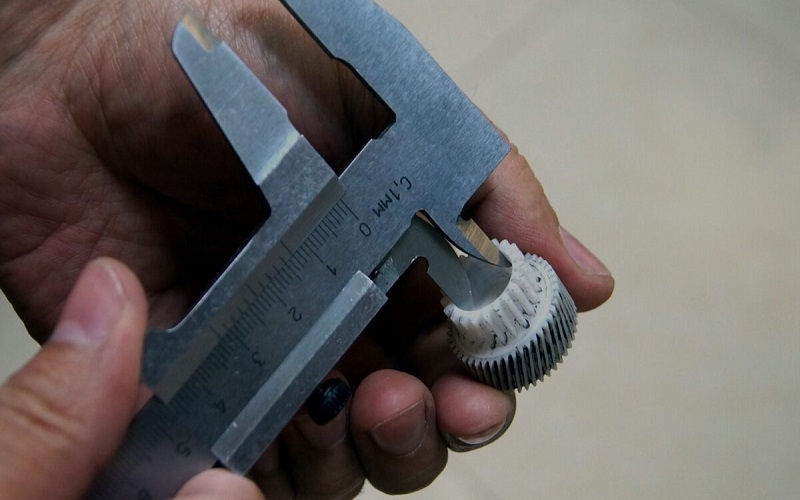
Optimizing injection molding tolerances involves a multifaceted approach, incorporating design considerations, material selection, and process control to optimize injection molding tolerances. By focusing on these key areas, manufacturers can enhance the precision and reliability of their injection molded parts, ensuring they meet the desired specifications and functional requirements.
Design Considerations
Consistent wall thickness during injection molding avoids imperfections and ensures dimensional accuracy. Uniform wall thickness helps reduce warping and improves shrinkage stability, leading to better control over tolerances. Proper draft angles are necessary for effective ejection from the mold, impacting the overall tolerances of the part. A generally suitable range for draft angles in injection molding is between 10 to 20 degrees.
Design for manufacturability (DFM) assessments can help ensure that parts are capable of being produced within specified tolerances. Mold flow simulation conducted during the design phase helps identify potential geometry issues that could affect achieving tight tolerances.
Aligning mold design with material characteristics is essential to ensure the desired precision and accuracy in the final parts.
Material Selection
Material selection plays a critical role in maintaining tolerances due to differing shrink rates among various plastic materials. Each material used in injection molding has varying shrink rates, which must be considered during the design of the mold. Resin selection significantly impacts the ability to maintain precise tolerances due to these varying shrinkage rates.
Choosing the right material is crucial for achieving desired tolerances in injection molded parts. Different materials and their shrinkage behaviors must be thoroughly understood to ensure that the final parts meet the required specifications. Carefully selecting the appropriate resin allows manufacturers to optimize injection molding processes and achieve consistent, high-quality results.
Process Control
Process controls monitor and adjust production variables to manufacture parts within specified tolerances consistently. Minimizing deviations in part quality involves the use of process controls that monitor critical production variables, such as temperature and pressure. Real-time monitoring of these variables maintains consistent quality in injection molded parts.
Technology such as temperature and pressure sensors provides real-time feedback in process controls, helping to ensure that parts are produced within the desired tolerances. Calibration of variables affecting part quality typically involves temperature, pressure, and holding time, all of which directly impact the final dimensions of the parts.
Effective process controls help manufacturers achieve consistent, high-quality results in the injection molding process.
Measurement Techniques for Verifying Tolerances
Proper measurement and inspection techniques confirm that molded parts comply with specified tolerances. Visual inspection is a straightforward approach to check molded parts for issues like warping and cracking. Automated systems like Coordinate Measuring Machines (CMMs) offer precise measurements for complex molded parts, ensuring all dimensions meet specifications.
First Article Inspection (FAI) involves a detailed check of the initial part produced, ensuring all dimensions meet specifications before full-scale production begins. Manual measurement typically uses tools like calipers and micrometers for simpler parts with fewer critical dimensions.
The thermal expansion rates of plastics typically can complicate the control of tolerances during the cooling phase, making accurate measurement techniques even more critical due to their high thermal expansion coefficient and extreme temperature changes.
Common Challenges in Maintaining Tolerances
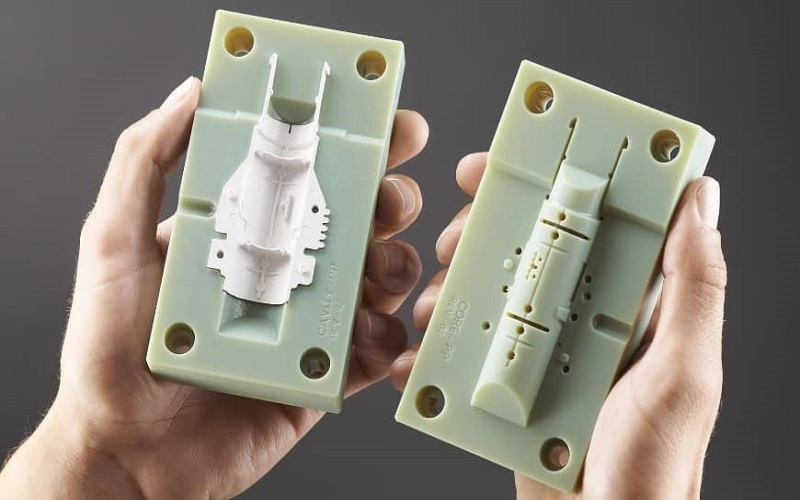
Before:
Maintaining uniform wall thickness is crucial to avoid uneven shrink rates and deformities in injection molded parts. Variations in wall thickness can lead to uneven shrinkage, resulting in warpage and other dimensional inaccuracies. Thick walls may have different shrink rates, complicating tolerance control and leading to potential distortions in the final part.
After:
Maintaining uniform wall thickness is crucial to avoid:
- Uneven shrink rates
- Deformities in injection molded parts
- Warpage
- Other dimensional inaccuracies
- Dimensional stability issues
Thick walls may have slight variations in different wall thickness, complicating tolerance control and leading to potential distortions in the final part, including increasing wall thickness.
Non-uniform cooling causes shrinkage, sink marks, jetting, and warping, affecting dimensional tolerances. Dimensions across a parting line cannot be held to high precision due to mismatches that occur from bisected features. Incorrect placement of ejector pins can lead to unwanted indentations and can rupture the product, causing cosmetic defects and physical aberrations.
Tighter tolerances and more restrictive tolerances can increase manufacturing costs, difficulty in assembly, labor costs, and material waste. Achieving 100% accuracy is difficult, and warping in injection molded parts cannot be completely eliminated. Conducting dimensional checks before a part has cooled sufficiently can lead to inaccurate assessments of restrictive tolerances compliance, further complicating the process.
Advanced Tools and Technologies for Tight Tolerances
Modern tools and technologies ensure tight tolerances in injection molding. Mold flow analysis software, such as Autodesk Moldflow, is commonly used to simulate and optimize the mold design, predicting potential issues and allowing for adjustments before production begins. This helps in achieving precise dimensions and reducing the likelihood of defects.
Temperature sensors assist in maintaining ideal processing conditions, ensuring consistent quality and dimensional accuracy in molded parts. Robotic automation enhances precision in injection molding by minimizing human error throughout the production process.
Leveraging advanced tools and technologies allows manufacturers to achieve tighter tolerances and improve overall injection molded part quality.
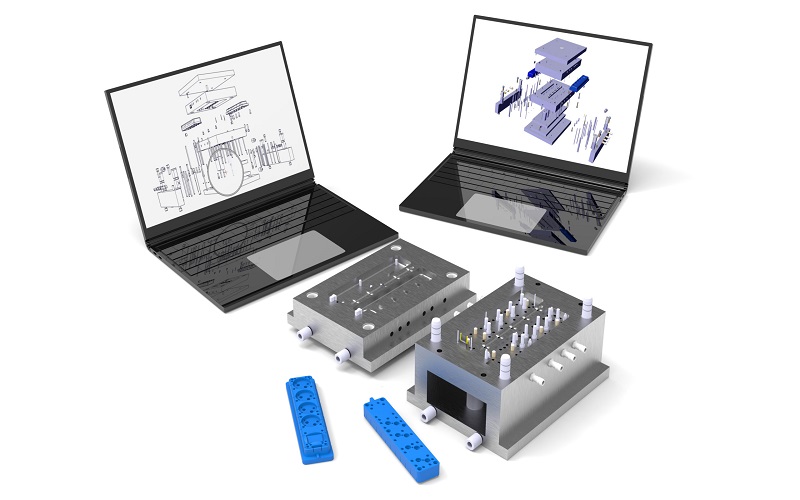
Summary
Mastering injection molding tolerances is a multifaceted endeavor requiring a deep understanding of material properties, part design, and process control.
By adhering to established standards, optimizing key factors, and employing advanced tools and technologies, manufacturers can achieve precise dimensions and ensure the functionality of their injection molded parts.
Embracing these techniques will not only enhance product quality but also pave the way for innovation and efficiency in injection molding projects. Let precision be your guiding star, and elevate your manufacturing process to new heights.
Frequently Asked Questions
Why are injection molding tolerances important?
Injection molding tolerances are essential for the proper fit and function of molded parts, directly impacting the reliability and quality of the final product. Adhering to precise tolerances prevents potential failures and underperformance.
What are the typical tolerances for injection molded parts?
Typical tolerances for injection molded parts generally range from +/- 0.1 mm, with critical applications requiring tighter tolerances of +/- 0.002 inches for enhanced precision and reliability.
How does material shrinkage affect injection molding tolerances?
Material shrinkage directly affects dimensional tolerances in injection molding, as varying shrinkage rates of different resins must be considered during design and processing to achieve precise final dimensions. Properly addressing these factors is essential for maintaining quality and accuracy in molded parts.
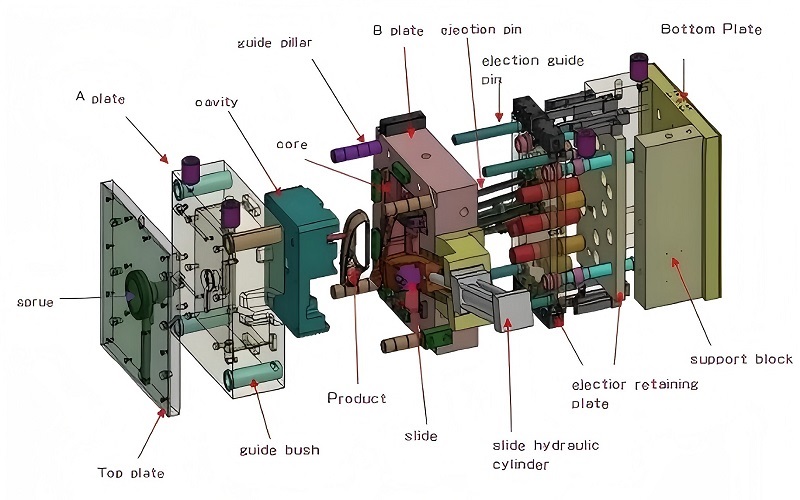
What role does part design play in maintaining tight tolerances?
Part design is essential for maintaining tight tolerances, as aspects such as wall thickness and geometric features directly influence the final product’s accuracy. Incorporating elements like support ribs and coring bosses can further enhance strength while ensuring precise tolerances.
What advanced technologies help achieve tight tolerances in injection molding?
Advanced technologies like mold flow analysis software, temperature sensors, and robotic automation are essential in achieving tight tolerances in injection molding.
They optimize design and processing conditions, reducing human error and ensuring precise dimensions.