Insert molding involves molding plastic around a metal or other material insert to create durable components in one step. This guide covers the process, benefits, and applications.
Understanding Insert Molding
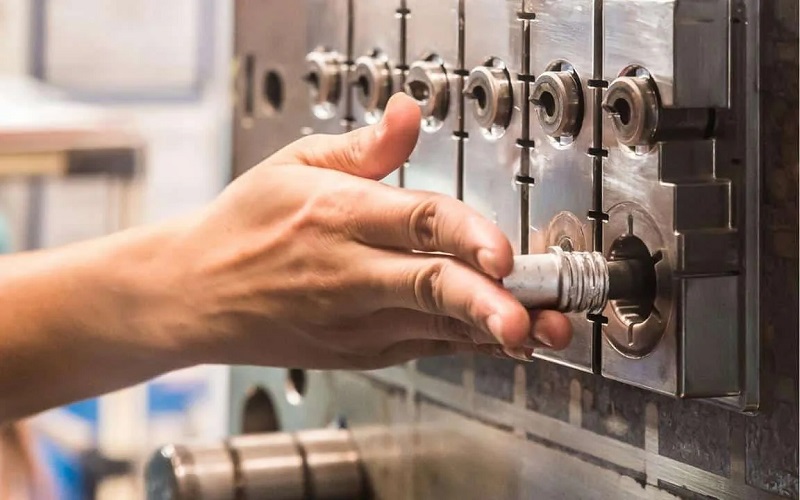
Insert molding is a manufacturing marvel that merges plastic with preformed inserts to produce insert components of exceptional durability and precision in a single step through metal insert molding.
This process involves several key steps:
- Designing a specialized mold
- Positioning the insert
- Injecting plastic around the insert
- Subjecting the product to rigorous quality checks
The result is a robust component that combines the best properties of both materials.
What makes insert molding stand out is its ability to enhance the strength and durability of plastic parts by integrating threaded inserts.
These inserts, which can be metal inserts or otherwise shaped, provide the necessary support and stability, effectively eliminating the need for post-molding assembly and reducing internal stress.
This seamless integration not only simplifies the manufacturing process but also leads to significant cost savings and increased product reliability.
Unlike conventional injection molding, which often requires multiple assembly steps, insert molding streamlines production into a single efficient process. This not only reduces production time but also minimizes labor costs and potential for assembly errors, making it a highly desirable method in various industries.
Key Materials Used in Insert Molding
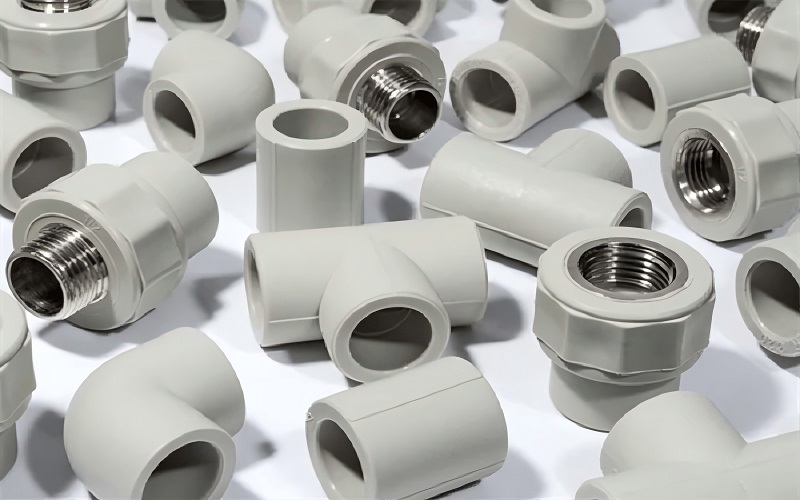
The success of the insert molding process hinges on the careful selection of materials. Common thermoplastic materials like polypropylene, nylon, polycarbonate, and acetal are frequently used due to their strength and favorable processing characteristics.
These materials are chosen for their ability to endure the high temperatures and pressures involved in the molding process, ensuring a strong bond with the inserts.
Thermoset materials such as polyester and epoxy resins also play a crucial role, especially in applications requiring high thermal resistance and structural integrity. Additionally, elastomers like polyurethane and natural rubber offer flexible solutions, catering to applications demanding elasticity and impact resistance.
The compatibility between the insert and plastic material is vital to avoid issues like cracking and ensure a robust final product.
Step-by-Step Insert Molding Process
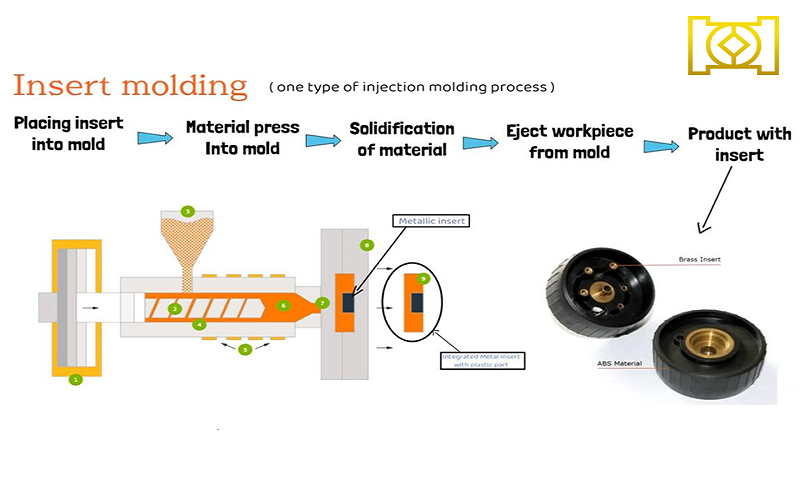
Understanding the step-by-step insert molding process is key to appreciating its efficiency and precision. The process begins with the careful loading of metal inserts into the mold, followed by the injection of molten plastic, cooling and ejecting the molded parts, and finally separating the parts from the sprues.
Loading Metal Inserts into the Mold
The initial step involves loading metal inserts into the mold cavity. This can be done manually or through automated insertion, with each method having its own advantages. Automated insertion significantly enhances production efficiency by ensuring faster and more accurate placement of inserts.
However, manual insertion, though less precise, is often used for low-volume production and is cost-effective for smaller batches.
Positioning the inserts correctly is paramount to ensure effective bonding with the plastic. Factors such as orientation and maintaining the position of the insert are crucial considerations.
Operators must also take safety precautions, such as wearing gloves, to protect themselves from the high temperatures involved in the process.
Injecting Molten Plastic
Once the inserts are in place, the next step is injecting molten plastic into the mold cavity. Using an injection unit, the plastic is injected under high pressure to ensure it completely fills the mold and encapsulates the inserts.
This high-pressure injection is crucial for achieving a strong bond between the plastic and the inserts, as it helps to expel any trapped air that could weaken the final product.
During this phase, it is essential to maintain the set temperature and holding pressure to prevent defects and ensure uniform solidification of the plastic. This meticulous control of the injection parameters is what sets insert molding apart from other molding processes.
Cooling and Ejecting Molded Parts
After the molten plastic has been injected, the next crucial phase is cooling. Maintaining a set temperature during this period is vital to ensure the uniform solidification of the plastic.
Holding pressure is also maintained during cooling to prevent defects such as shrinkage or warping, which can compromise the integrity of the molded part.
After the plastic solidifies, the mold opens. This process enables the removal of the molded part. This step must be executed with precision to avoid damaging the newly formed component.
Ensuring proper cooling and careful ejection are key to maintaining the quality and consistency of the final product.
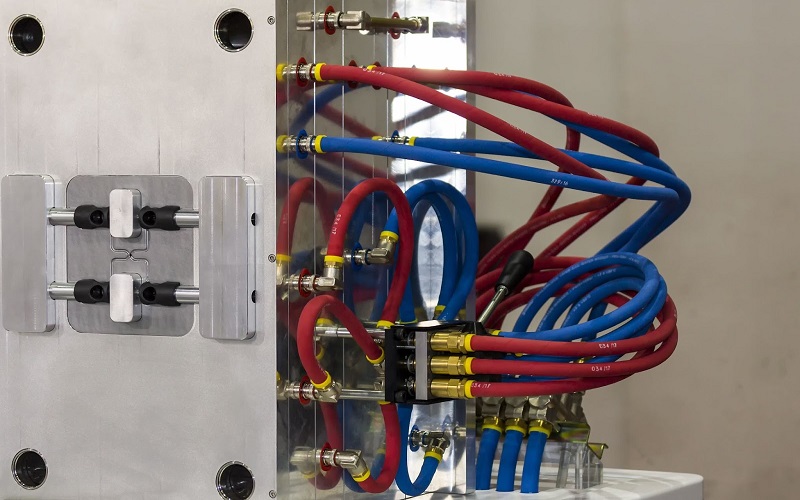
Separating Parts from Sprues
The final step in the insert molding process is separating the molded parts from the sprues. This requires careful attention to detail to avoid damaging the parts.
The sprues are the channels through which the molten plastic flows into the mold cavity, and they must be removed without affecting the integrity of the molded part.
Taking precautions during this separation process is crucial to ensure that the final product maintains its desired properties and appearance. Proper handling and precision are essential to avoid any potential damage or loss of parts during this stage.
Design Considerations for Effective Insert Molding
Designing for insert molding requires careful consideration of various factors to ensure the success of the process. The flexibility offered by insert molding allows for the creation of complex shapes that would be difficult to achieve with traditional metal components. This increased design flexibility is one of the key advantages of insert molding.
Material compatibility is another crucial aspect. Ensuring that the chosen materials can withstand the extremes of temperature and pressure involved in the molding process is essential to avoid adhesion issues and ensure product performance. Additionally, protecting inserts from these extremes helps maintain the integrity of the final product.
Avoiding sharp corners in the mold design is also important to reduce stress on the mold walls and improve the flow of molten plastic, leading to better bonding and overall product quality.
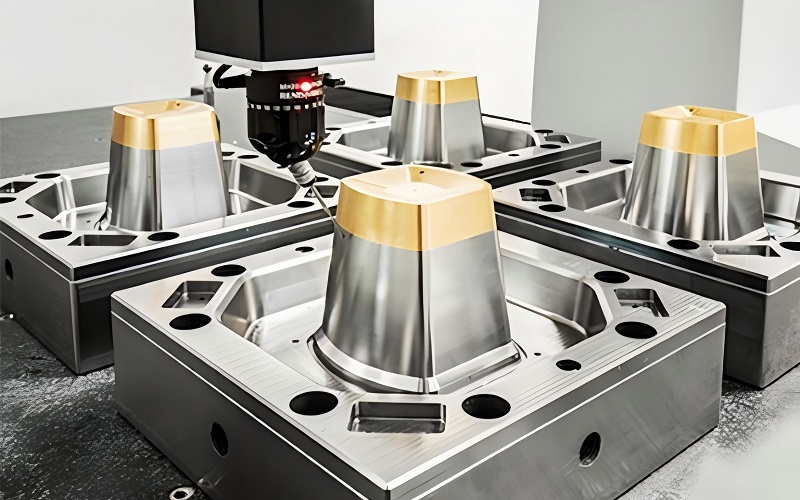
Cost Analysis
Insert molding is a cost-effective manufacturing method due to its ability to eliminate post molding assembly, thereby reducing labor costs and production time.
Automated insertion further enhances cost efficiency by ensuring consistency and precision, although it eliminates post molding assembly with higher initial capital costs.
Important cost factors to consider include the cost of acquiring inserts, operator fees, and the increased price per unit due to the incorporation of inserts. Despite these costs, the overall savings achieved through reduced assembly time and labor make insert molding a favorable choice for many applications.
Properties of Metal Inserts
Choosing the right metal inserts is crucial for the success of the insert molding process. Commonly used materials include brass and steel, which offer durability and compatibility with the high temperatures and pressures involved in molding.
These properties ensure that the inserts can withstand the molding conditions and provide the necessary support to the final product.
The selection of metal inserts also depends on factors such as material choice, dimensions, and surface finish to ensure optimal performance. The mechanical properties of the inserts play a significant role in how metal inserts strengthen the overall strength and reliability of the injection molded parts.
Optimal Insert Location
The placement of inserts within the mold is a critical design consideration that affects the durability and performance of the final product. The intended function of the insert must be taken into account when determining its optimal location to ensure it performs as required.
Maintaining the position of the insert during the molding process is essential to achieve a strong bond with the plastic and ensure the overall quality of the molded part. Proper placement and positioning are key to the success of the insert molding process.
Advantages and Challenges of Insert Molding
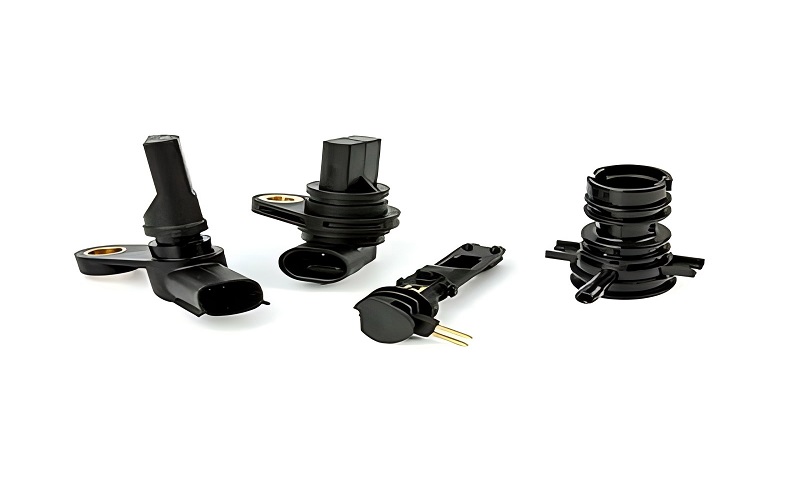
Insert molding offers numerous advantages, including significant cost savings by reducing assembly requirements and labor expenses.
The process enhances product strength by creating strong bonds between plastic and metal components, resulting in durable and lightweight parts. This makes insert molding particularly effective for producing components in the automotive industry, where strength and weight are critical factors.
The automated nature of insert molding ensures consistent product quality across large production batches. This consistency is essential for industries like healthcare, where the ability to sterilize plastic components simplifies the manufacturing process.
However, insert molding also presents challenges, such as increased initial production costs and complexity due to the need for specialized molds. Larger or irregularly shaped inserts can complicate the process, affecting positioning and adhesion. Additionally, the longer production cycle required for insert placement can be a drawback for some applications.
Despite these challenges, the benefits of insert molding make it a valuable technique in many industries.
Diverse Applications of Insert Molding
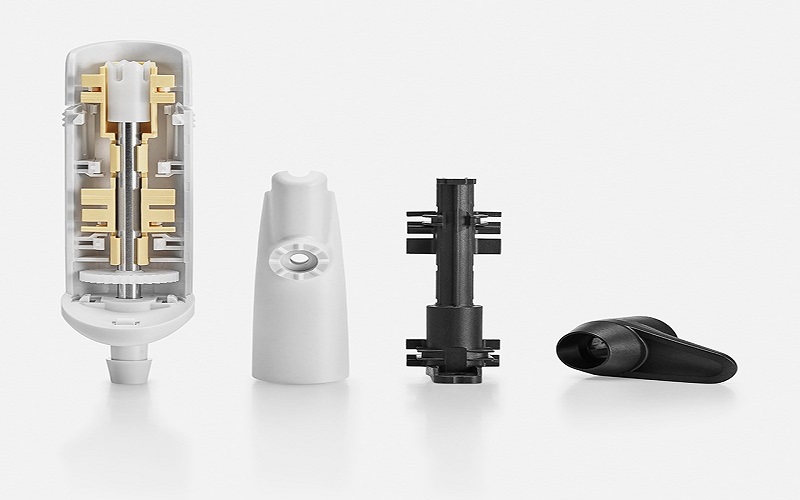
Insert molding is a versatile process employed in various industries, from aerospace to healthcare. In the aerospace industry, it is used to create lightweight and durable parts, such as aircraft seating, which must withstand high stress and frequent use. The ability to integrate multiple components into a single molded part streamlines the manufacturing process and enhances product reliability.
In the defense sector, insert molding is used to produce weaponry, battery packs, and munitions, where durability and precision are paramount. The consumer electronics industry also benefits from insert molding, as it eliminates the need for fasteners and solders, leading to simpler and more efficient designs. Products like digital control panels and assemblies are typical examples of insert molded components in this industry.
Insert molding’s ability to enhance sealing and waterproofing makes it ideal for applications requiring fluid resistance, such as medical devices. The medical industry relies on insert molding to produce sterile and easy-to-maintain components, such as surgical instruments and dental instruments.
Automotive Components
The automotive industry extensively uses insert molding to create lightweight and durable components. Sensor housings and electrical connectors are typical applications that benefit from the strength and precision of insert molding. The ability to incorporate metal inserts into plastic parts ensures that these components can withstand the rigors of automotive use.
Insert molding in automotive manufacturing not only enhances the mechanical properties of the parts but also reduces production costs by eliminating the need for additional assembly steps. This efficiency makes insert molding a valuable technique for producing high-quality automotive components.
Consumer Electronics
In the consumer electronics industry, insert molding plays a crucial role in simplifying designs and streamlining manufacturing. By eliminating the need for fasteners and solders, insert molding allows for the integration of multiple components into a single molded part, leading to more efficient and compact designs.
Product designers in the consumer electronics sector leverage insert molding to create digital control panels, assemblies, and other components that require high precision and reliability. This process not only enhances the final product but also reduces manufacturing costs and production time.
Medical Devices
The medical industry greatly benefits from insert molding, which enables the production of sterile and easy-to-maintain components. Insert molding allows for the creation of precision components, such as surgical instruments and dental instruments, which require high levels of accuracy and durability.
Medical device manufacturers rely on insert molding to produce medical equipment components that can be easily sterilized and maintained, ensuring patient safety and product longevity. This process is essential for creating high-quality medical equipment that meets stringent industry standards.
Comparing Insert Molding and Overmolding
Insert molding and overmolding are two distinct processes, each with its own advantages and applications. Insert molding typically involves a single manufacturing step, where the insert is placed in the mold, and plastic is injected around it. This process offers greater flexibility in material selection and can accommodate a wider variety of non-plastic inserts.
Overmolding, on the other hand, requires two distinct injection phases, making it more costly and time-consuming. However, it allows for the creation of more complex parts with multiple layers or materials.
The choice between insert molding and overmolding depends on the specific requirements of the application, including cost, material compatibility, and desired product characteristics.
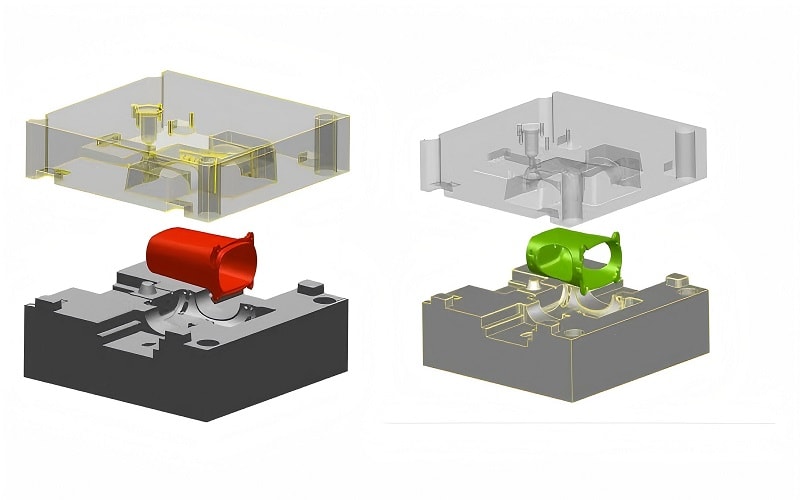
Expert Services for Insert Molding
Choosing professional insert molding services ensures efficient and high-quality production of custom parts. Companies like WayKen employ skilled mold operators, engineers, and quality control experts to deliver excellence in the insert molding process.
These experts provide comprehensive manufacturing analysis and consultative design services to help clients identify potential challenges and ensure product quality.
Professional insert molding services also offer quick production times, with prototypes ready in as little as 15 days. This rapid turnaround, combined with the ability to produce custom parts with high precision, makes expert services a valuable asset for any manufacturing project.
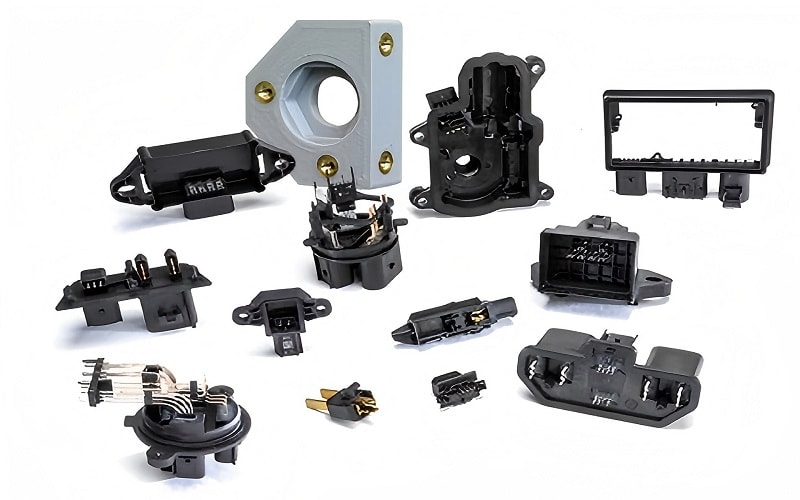
Conclusion
Insert molding is a powerful manufacturing technique that combines the best properties of plastic and metal to create durable and precise components. From automotive parts to medical devices, insert molding offers numerous advantages, including cost savings, increased design flexibility, and enhanced product strength.
By understanding the materials, process, and design considerations involved in insert molding, manufacturers can leverage this technique to produce high-quality products efficiently. Whether you’re in the aerospace, defense, consumer electronics, or medical industry, insert molding can significantly enhance your manufacturing capabilities.
Frequently Asked Questions
What is insert molding?
Insert molding is a manufacturing technique that integrates plastic with preformed metal inserts to produce robust and precise components in one operation. This process enhances the product’s durability and functionality.
What materials are commonly used in insert molding?
Insert molding commonly utilizes materials such as thermoplastics—including polypropylene, nylon, polycarbonate, and acetal—along with thermosets like polyester and epoxy resins. Additionally, elastomers such as polyurethane and natural rubber are employed for more flexible applications.
What are the main advantages of insert molding?
Insert molding significantly reduces assembly time and labor costs, enhances product strength by creating strong bonds between materials, and ensures consistent quality across large production runs. These advantages make insert molding an efficient choice for manufacturing.
How does insert molding differ from overmolding?
Insert molding differs from overmolding in that it combines the insert and plastic in a single injection process, while overmolding involves two separate injection phases. This makes insert molding more efficient and flexible in material choice compared to the more complex and costly overmolding process.
What industries benefit from insert molding?
Insert molding significantly benefits the automotive, aerospace, defense, consumer electronics, and medical devices industries, as it produces durable, lightweight, and precise components essential for these sectors.