Rubber is an important industrial material, widely used in car tires, conveyor belts in industrial production, and medical gloves and IV tubes.
Due to its flexibility and practicality, many people can’t help but associate it with plastic, even thinking that rubber is just a type of plastic.
“Is rubber plastic?” Behind this seemingly simple question lies the mystery of material science.
To uncover the truth, this article will explore the differences and similarities between rubber and plastic,taking you on a journey to unveil their hidden secrets!
What Is Rubber?
Rubber refers to a highly elastic polymer material with reversible deformation.
At room temperature, it exhibits elasticity, capable of undergoing significant deformation under minimal external force and returning to its original shape once the force is removed.
Rubber is a completely amorphous polymer with a low glass transition temperature (Tg) and typically has a very high molecular weight, often exceeding hundreds of thousands.
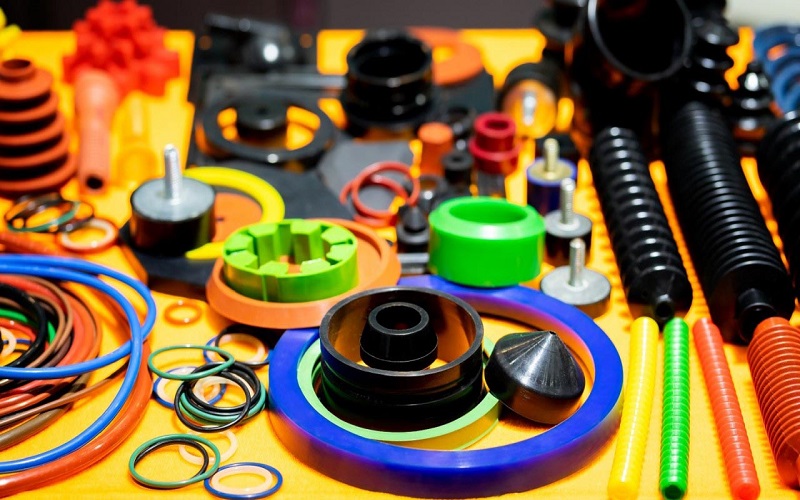
Type Of Rubber
Generally, rubber is categorized into two types:
Natural Rubber: Extracted and processed from the sap of plants such as rubber trees or rubber grass.
Its primary component is cis-1,4-polyisoprene, mixed with small amounts of non-rubber substances like proteins, fatty acids, sugars, and ash.
Synthetic Rubber: Produced through the polymerization of various monomers.
Common types include styrene-butadiene rubber (SBR), butadiene rubber (BR), and neoprene (CR), with their production now far surpassing that of natural rubber.
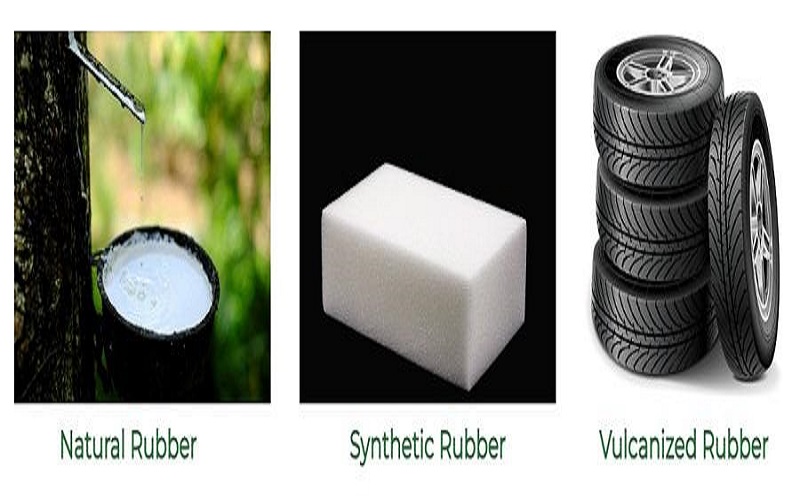
Key Properties of Rubber
Rubber, as a distinctive polymer material, is widely used in industry and daily life due to its exceptional physical and chemical properties.
Below are the primary characteristics of rubber:
- High Elasticity
Rubber’s elasticity is top-notch, allowing it to quickly recover its original shape even after extensive deformation.
Its elongation at break easily surpasses 1000%—sometimes even higher—earning it the title of an “unbreakable” champion.
- Wear Resistance
Rubber boasts impressive wear resistance, maintaining a long service life in environments with friction and abrasion.
This makes it a go-to material for applications like tires, conveyor belts, and sealing rings.
- Susceptibility to Aging
Rubber and its products are prone to aging during processing, storage, and use.
The combined effects of internal and external factors gradually degrade its physical, chemical, and mechanical properties, leading to reduced performance and a shorter lifespan.
- Temperature Sensitivity
Rubber’s performance is highly temperature-dependent. It remains flexible at room temperature, but at extremely low temperatures (below its glass transition temperature, Tg), it hardens and loses elasticity. At high temperatures, it may soften or even break down.
Rubber’s defining traits—high elasticity and wear resistance—make it stand out in dynamic, high-load settings.
However, its sensitivity to temperature and tendency to age limit its scope, though advancements in synthetic rubber continue to address these drawbacks.
How To Process Rubber Materials?
Rubber processing involves key steps like mastication, mixing, calendering or extrusion, molding, and vulcanization, each tailored to specific product needs and supported by various auxiliary operations.
First, raw rubber undergoes mastication to enhance its plasticity, preparing it to blend with additives. Next, during mixing, carbon black and rubber auxiliaries are uniformly combined with the rubber to form a compound.
This compound is then extruded into shaped blanks, which are subsequently paired with calendered or coated textiles (or metal materials) to create semi-finished products.
Finally, vulcanization transforms these pliable intermediates into highly elastic finished goods.
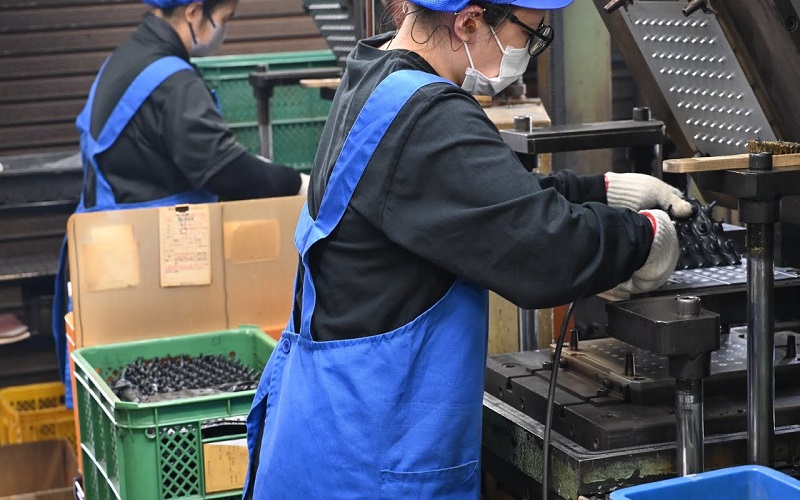
Common Applications Of Rubber Products
Rubber, the foundational raw material of the rubber industry, is widely utilized in producing tires, hoses, tapes, cables, and a variety of other products.
Its applications span multiple fields, as highlighted below:
Transportation
Rubber shines in transportation, primarily in tires, hoses, and seals.
Tires, a standout application, leverage excellent elasticity and wear resistance to absorb shocks effectively, enhancing vehicle stability and comfort.
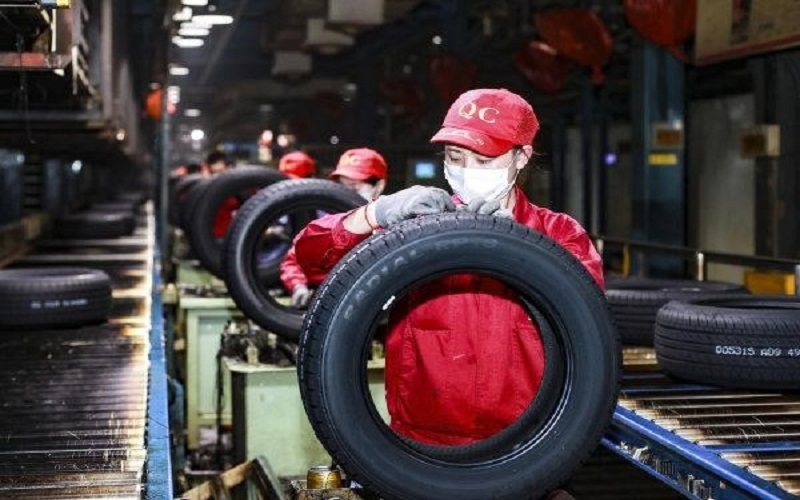
Construction
In construction, rubber transforms into flooring and waterproofing materials.
Rubber floors, prized for their slip resistance, sound absorption, and durability, are common in commercial buildings, schools, and hospitals.
Waterproofing materials, with their corrosion resistance and flexibility, excel in roofing, basements, and water tanks.
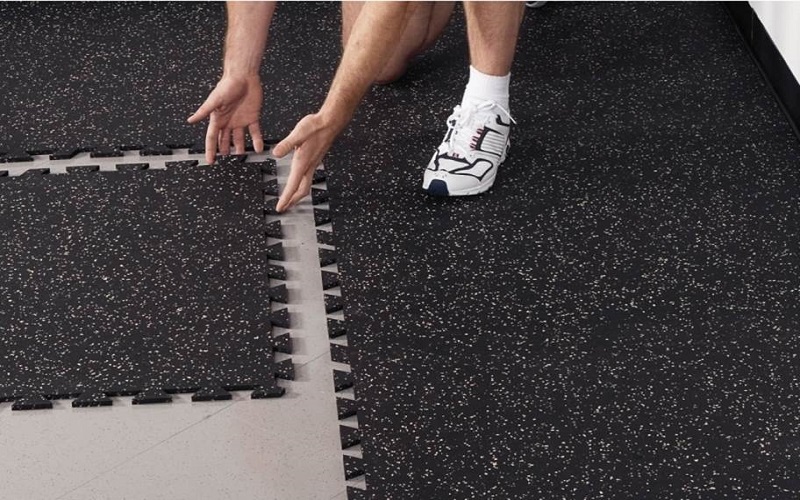
Household Use
Rubber integrates seamlessly into daily life through gloves, mats, and gaskets.
Rubber gloves shield hands from chemicals and bacteria during cleaning, gardening, or lab work, while mats and gaskets reduce friction between furniture and floors, minimizing noise and wear for a cozier home.
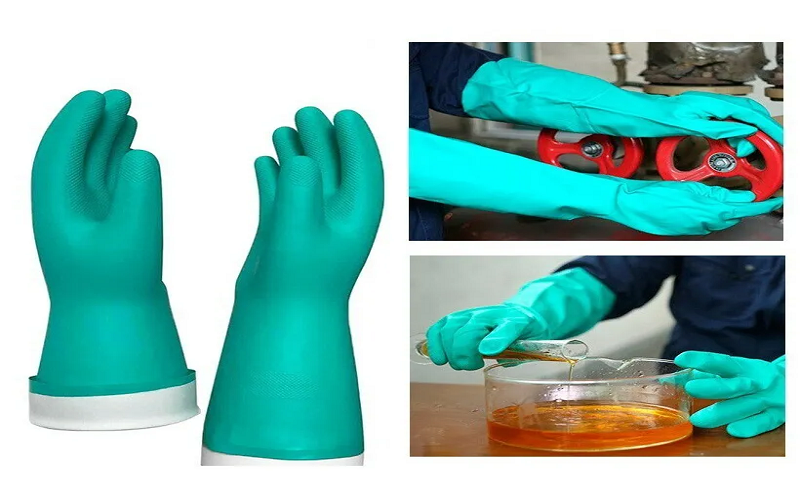
Industrial Production
Rubber plays a vital role in industry, forming conveyor belts, hoses, and pipes. These support efficient production and material transport in sectors like chemicals, petroleum, and food processing.
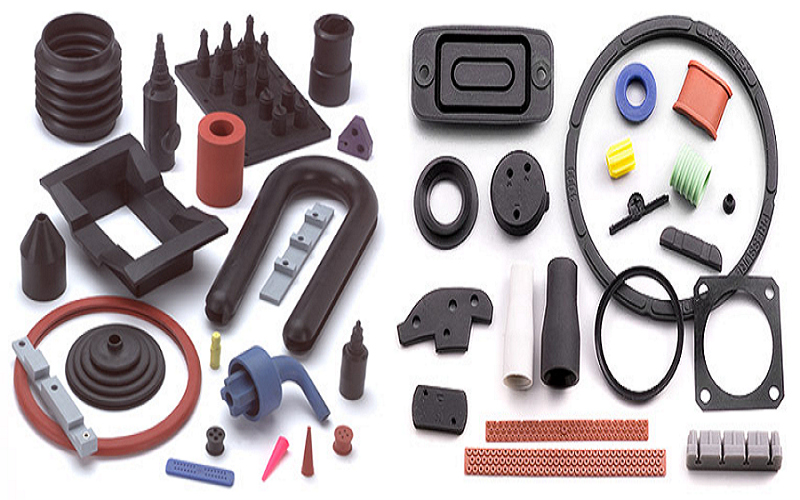
Medical Field
In healthcare, rubber is crafted into surgical gloves, medical devices, and aids.
Surgical gloves, thanks to their superior elasticity and moldability, serve as a trusted protective ally for doctors during operations.
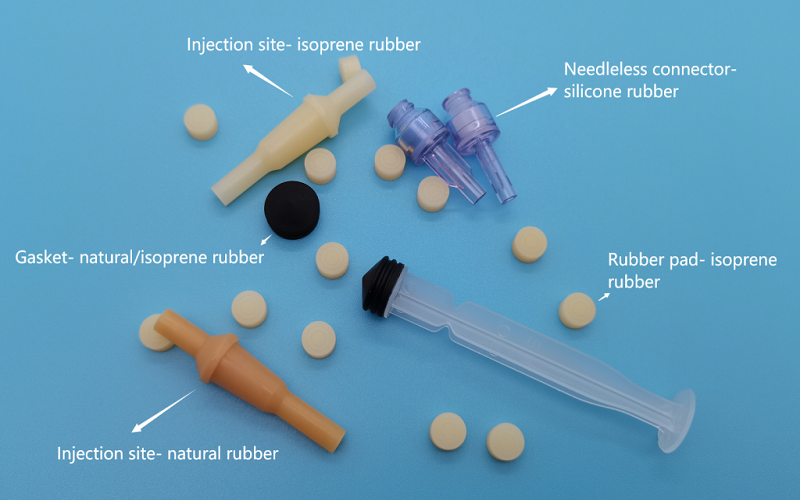
Can Rubber Be Recycled?
As environmental awareness grows, people increasingly value material recycling—so, is rubber a recyclable material? Yes, it is, but the process is far from straightforward.
Compared to the well-established plastic recycling methods , rubber products, often vulcanized into a stable networked structure, resist melting and reshaping.
The typical approach involves grinding them into particles (like rubber powder) for uses such as road surfacing or fillers, but this “downcycling” can’t restore their original properties.
Most vulcanized rubber items, especially tires, end up incinerated or landfilled. Of the roughly 1 billion waste tires generated globally each year, only a small fraction is effectively reused, lagging far behind plastic in efficiency.
Moreover, rubber’s robust chemical structure—featuring nearly irreversible cross-linked bonds after vulcanization—requires energy-intensive pyrolysis or chemical breakdown for disassembly, driving up costs and risking pollution.
Thus, while rubber is theoretically recyclable, its practical reuse remains hampered by technical and economic hurdles.
What Are The Differences Between Plastics And Rubber?
When discussing rubber and plastic, many might assume they’re the same thing—or at least closely related.
However, while both are polymer materials, they differ significantly in several key aspects.
Molecular Structure
Rubber typically features coiled, linear molecular chains that are soft and pliable in their raw state.
After vulcanization, these chains form a networked structure, giving rubber its elasticity and resilience.
Its longer molecular chains and stronger intermolecular forces contribute to superior elasticity and tensile strength.
Plastic, by contrast, has shorter molecular chains with weaker intermolecular connections, resulting in a generally harder texture.
Properties
Rubber is renowned for its high elasticity, capable of stretching dramatically and snapping back, often exceeding a 1000% elongation at break.
It’s flexible and wear-resistant but sensitive to temperature—hardening in extreme cold and softening in heat—and prone to aging.
Plastic, however, emphasizes moldability and stability, typically forming rigid or semi-rigid shapes after processing. Its elasticity is limited (usually under 100%), and it resists drastic temperature changes more effectively.
Processing and Recycling
Rubber processing involves mastication, mixing, and vulcanization. Once vulcanized, it can’t be melted for reuse, so recycling often means grinding it into particles for “downcycled” applications. Plastic, particularly thermoplastics, can be melted and reshaped multiple times, benefiting from a more mature recycling process.
Applications
Rubber’s elasticity makes it ideal for cushioning, sealing, and shock-absorbing needs, while plastic’s hardness and resistance to deformation suit it for structural support and wear-resistant uses.
In Short,Rubber is the “elasticity champion,” excelling in flexible, resilient roles; plastic is the “molding master,” adept at holding shape and withstanding environmental stress.
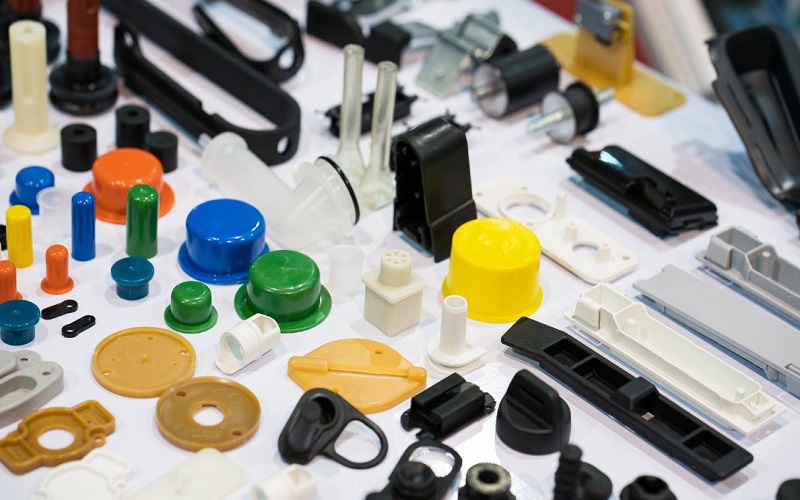
Conclusion
In summary, while rubber and plastic both belong to the polymer material family, they differ starkly in molecular structure, properties, processing methods, and application fields.
Thus, to answer the question “Is rubber a type of plastic?”—clearly, no.
They are two distinct materials, each playing an irreplaceable role in life, rather than being a simple subset of one another.