Styrofoam can be found everywhere in our daily lives. For example, many of the lightweight cups you get when you buy milk tea, the takeout boxes you use to pack your food, and even the cushioning material in your courier packages are Styrofoam. Although these items have long been integrated into our lives, have you ever thought about the question: is Styrofoam considered plastic or not?
Figuring out what Styrofoam is made of, how it relates to regular plastic, and its long-term impact on the environment is actually very important for us to reduce pollution waste.
Next, let’s learn more about the nature of Styrofoam, find out why it’s difficult to recycle, and what we can do in our daily lives to minimize the harm it does to the environment.
What is Styrofoam?
Most of our everyday talk about Styrofoam actually refers to Styrofoam.
It is an expanded material made from Polystyrene (PS). Simply put, during the manufacturing process, polystyrene pellets are heated to soften them and injected with a blowing agent like pentane. The pellets slowly expand as they are heated, forming countless tiny bubbles that, when cooled and solidified, turn into the familiar light, fluffy foam structure.
Styrofoam feels much lighter than ordinary plastic, and because it is lightweight, insulates well, and acts as a cushion, it is widely used in food packaging, disposable tableware, express shock padding, and even building insulation panels.
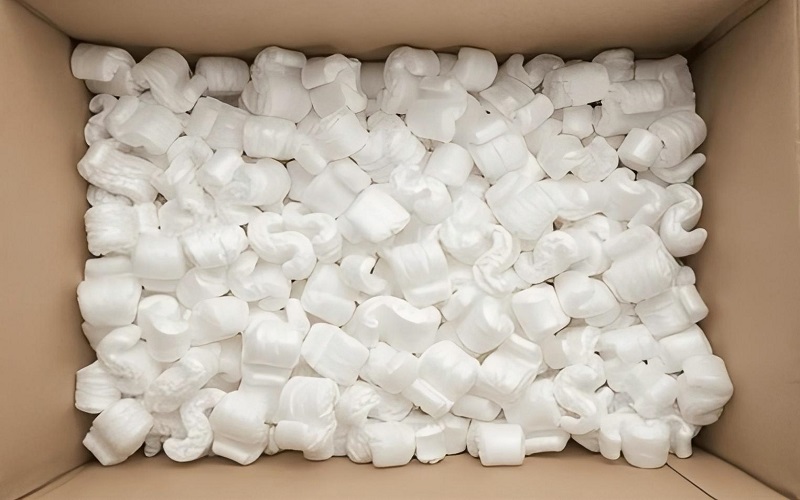
Unique properties of Styrofoam
- Lightweight and floatable: with a density of only 15 – 30 kg/m³, it is easy to transport and is widely used for food insulation and packaging.
- Strong impact resistance: internal bubbles can absorb external forces and protect fragile items such as glassware and electronic products.
- Low cost: Simple and inexpensive to produce, but overuse tends to aggravate environmental pollution.
The following values visualize Styrofoam’s characteristics:
Property | Value |
Density | 15 – 30 kg/m³ |
Thermal conductivity | 0.03 W/(m·K) |
Water absorption rate | ≤ 4% |
Compressive strength | 0.07 – 0.35 MPa |
Impact energy absorption rate | 60% – 75% |
Melting temperature | 240°C – 260°C |
Carbon emissions | 3.1 kg CO₂/kg |
Volume expansion ratio | 40 – 50 times |
Recycling rate | < 1% |
Aging resistance | Brittle under UV exposure |
The Relationship Between Styrofoam and Plastic
Styrofoam is closely related to plastic because, at its core, it is a special form of plastic.
Its main component is polystyrene (PS), a thermoplastic polymer produced through the free radical polymerization of styrene monomers.
It belongs to the family of petroleum-based synthetic plastics. Although the physical structure of Styrofoam changes during its production, its chemical composition remains the same — it is still polystyrene.
Therefore, in essence, Styrofoam is a type of plastic.
Styrofoam Recycling
The Recycling Conundrum
Even though Styrofoam is a plastic, its recycling rate is incredibly low.
- High transportation costs
- High risk of contamination
- Scarce facilities
Styrofoam Recycling in Different Countries
Japan: Some companies have developed advanced recycling methods for Styrofoam. They crush used Styrofoam and dissolve it with special chemicals to turn it back into raw materials, allowing for its reuse in new products.
South Korea: South Korea has established an efficient recycling system for Styrofoam, where the material is sorted and reprocessed into new products. This has helped make their Styrofoam recycling rate one of the highest in Asia.
Canada: In some Canadian cities, there are special recycling stations that collect Styrofoam trays, disposable containers, and packaging materials. The recycled Styrofoam can be transformed into new products like insulation boards and landscaping materials.
United Kingdom: The UK’s Styrofoam recycling rate was initially low, but it has been increasing due to efforts from environmental organizations. By improving recycling systems and raising public awareness, more Styrofoam is now being recycled and reused.
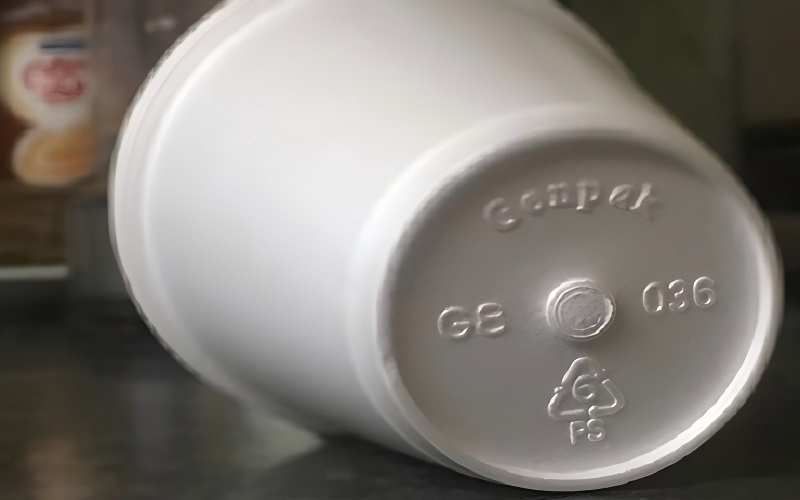
Application Areas for Styrofoam Plastics
Styrofoam demonstrates excellent value in several industries due to its unique properties.
- In the packaging industry, it is widely used as an efficient cushioning material for express foam boxes and electronic product linings, protecting goods from impact and ensuring safe transportation.
- In the construction field, Styrofoam is processed into thermal insulation boards and applied to walls and roofs for heat insulation, effectively improving energy-saving performance and favored by builders.
- In addition, in the food packaging field, Styrofoam is made into disposable lunch boxes and cups, which have become a popular choice in the catering industry due to its lightweight and low-cost features.
However, with the increasing awareness of environmental protection, some regions have begun to restrict the use of Styrofoam due to its difficult-to-biodegrade characteristics, and are gradually promoting biodegradable alternative materials.
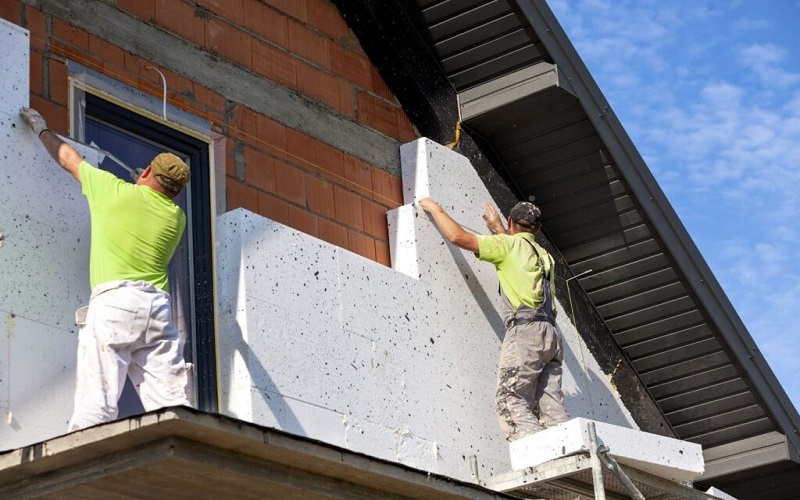
Eco-friendly Alternatives to Styrofoam
As environmental awareness increases, more materials are being used as alternatives to Styrofoam. Here are some common substitutes:
Biodegradable Foam: This foam is made from natural plant materials, such as corn starch, and can break down in the natural environment. It is lightweight and eco-friendly, but the production cost is relatively high.
Paper-based Materials: Paper-based foam materials can replace Styrofoam for packaging and protection. They are recyclable and biodegradable, but they do not perform as well in protection and moisture resistance compared to Styrofoam.
Plant-based Foam: This foam is made from renewable plant materials, such as soy or bamboo. It offers good protection and is environmentally friendly. However, the production cost is high, and the technology is still under development.
Polylactic Acid Foam (PLA): PLA foam is made from plant sugars and is a biodegradable bioplastic. It reduces reliance on petroleum, but it is prone to deformation under high temperatures and requires specific conditions to degrade.
The Role of Styrofoam in Injection Molds
Styrofoam (expanded polystyrene) has some simple and useful functions in plastic mold manufacturing:
- Prototyping: Styrofoam is lightweight and easy to cut, making it great for quickly creating mold samples.
- Foam Models: During injection molding, the foam can melt away, helping form hollow or special-shaped parts.
- Filler Material: It reduces the mold’s weight, makes it easier for plastic to flow, and lowers production costs.
- Insulation: Styrofoam provides insulation, helping the mold maintain a stable temperature for smoother injection.
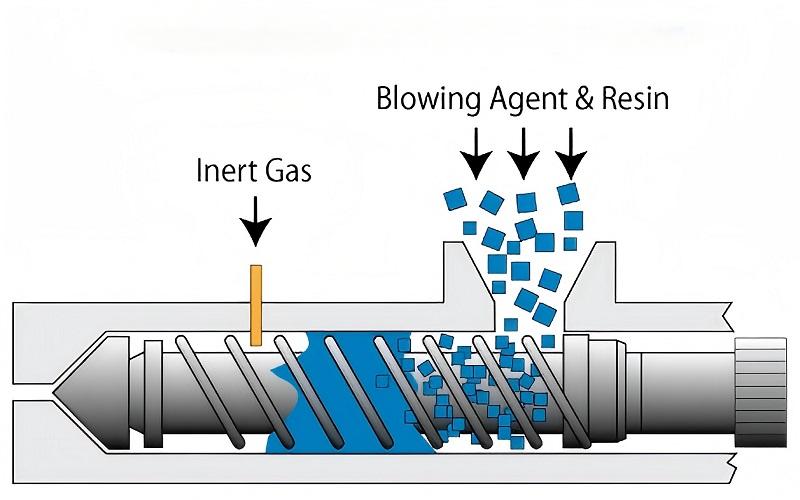
Conclusion
Styrofoam is indeed a member of the plastic family.
It retains the thermoplastic properties of plastic, with the processing potential of regular plastic.
It is easily molded in injection molds and is used in a wide range of packaging and construction applications. If your project requires the use of Styrofoam, please feel free to contact us.