Large injection molded parts play a vital role in producing durable and complex plastic components. This article explains the process, materials, and techniques used in large-scale injection molding, and how it can save costs and enhance product quality.
Understanding Large Injection Molded Parts
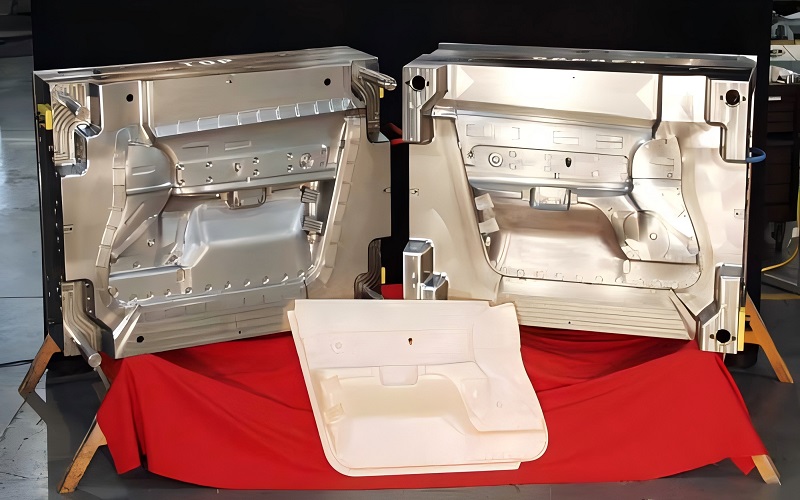
Large part injection molding is a marvel of modern engineering, enabling the mass production of complex and robust components with incredible efficiency. The injection process involves injecting molten plastic resin into a mold cavity under hydraulic pressures that can exceed 20,000 psi, allowing for the creation of large, intricate parts that are both strong and lightweight.
This high-pressure environment is essential for ensuring that every nook and cranny of the injection molds is filled, resulting in precise and consistent parts. Injected molding large parts is a key aspect of this innovative technique.
What makes large part injection molding particularly significant is its cost-effectiveness. Producing large quantities of parts in a single cycle allows manufacturers to achieve economies of scale, lowering the overall cost per unit and making high-quality products more accessible. Various optimization techniques further enhance this efficiency by streamlining the production process, ensuring each part meets stringent quality standards while minimizing waste and downtime.
Different processes within the realm of large part injection molding offer unique benefits. For example, techniques like gas assist molding can reduce internal stresses in the plastic resin, leading to smoother surfaces and enhanced part strength. As we delve deeper into the materials and methods used in this field, it becomes clear that the right combination of technology and expertise can unlock unparalleled manufacturing capabilities.
Key Materials for Large Part Injection Molding
The choice of materials in large part plastic injection molding is paramount, as it directly influences the strength, durability, and application of the final product. From automotive components to industrial equipment, the right plastic resin can replace traditional metal parts, offering benefits like reduced weight and increased energy efficiency.
Common materials used in large part plastic injection molding and blow molding include High-Density Polyethylene (HDPE), molded plastics, acrylic, and nylon, each with its unique set of properties and applications.
Selecting the appropriate material depends on several factors, including the part’s intended use, environmental conditions, and specific performance requirements. For instance, HDPE is favored for its high impact resistance and versatility, making it ideal for items like containers and kitchenware.
Let’s explore these key plastic materials in more detail.
High-Density Polyethylene (HDPE)
High-Density Polyethylene (HDPE) stands out as a top choice in large part injection molding due to its impressive strength-to-density ratio.
This thermoplastic polymer is known for its high impact resistance and ability to withstand a wide range of temperatures, making it suitable for various applications, from sturdy containers to kitchenware. HDPE’s rigidity and affordability also contribute to its widespread use in the food industry, where it meets stringent safety regulations for food contact applications.
One of the notable advantages of HDPE is its versatility. Whether it’s used to produce large plastic parts or intricate molded components, HDPE consistently delivers high performance and durability.
Its resistance to chemicals and impact further enhances its suitability for demanding environments, ensuring that products made from HDPE can endure harsh conditions without compromising quality.
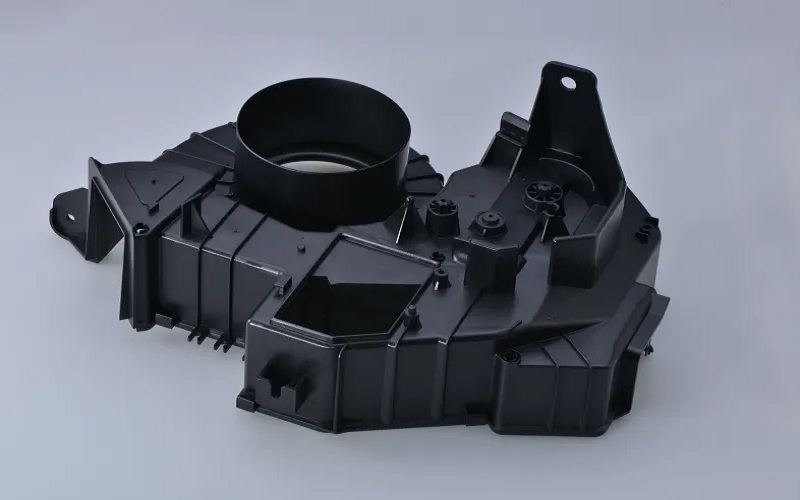
Acrylic (PMMA)
Acrylic, or polymethyl methacrylate (PMMA), is another popular material in large part injection molding, valued for its clarity and durability. This thermoplastic polymer is often used in applications where aesthetic appeal is crucial, such as in automotive lighting, displays, and signage. However, acrylic does have its limitations, particularly in terms of heat resistance and susceptibility to cracking under stress.
Despite these challenges, acrylic remains a favored choice for products that require a combination of visual appeal and structural integrity. Its ability to withstand UV light without yellowing makes it ideal for outdoor applications, ensuring that components retain their appearance and functionality over time.
Understanding the strengths and limitations of acrylic enables manufacturers to make informed decisions about its use in various projects.
Nylon Plastic (PA)
Nylon plastic, or polyamide (PA), is renowned for its strength, flexibility, and versatility, making it a staple in large part injection molding.
This thermoplastic polymer is frequently utilized in automotive and electrical components, where its ability to endure high stress and temperatures is crucial. Nylon’s excellent mechanical properties and resistance to abrasion further enhance its suitability for demanding applications.
In addition to its robust performance, nylon offers significant design flexibility. It can be easily molded into complex shapes, allowing manufacturers to create intricate parts with precision. Whether used in the automotive industry or for consumer electronics, nylon’s combination of strength and adaptability ensures that it remains a go-to material for high-performance applications.
Advanced Techniques in Large Part Injection Molding
Advancements in large part injection molding have introduced a range of techniques that enhance production efficiency and product quality. Techniques like gas assist molding, insert molding, and structural foam molding offer unique benefits, from reducing internal stresses to producing lightweight yet strong components.
These methods leverage scientific molding principles and Design of Experiments (DOE) to achieve precise and consistent results, often requiring special lifting equipment to handle large molds and components safely.
Moreover, the integration of automation and smart technologies is revolutionizing the injection molding industry. Robotics and the Internet of Things (IoT) are streamlining processes, reducing operational risks, and enabling real-time monitoring for improved decision-making.
These advancements ensure optimal clamping pressure, measured in force per square inch, to maintain mold integrity and produce high-quality parts. As we explore these advanced techniques, it becomes evident that innovation is at the heart of modern injection molding practices.
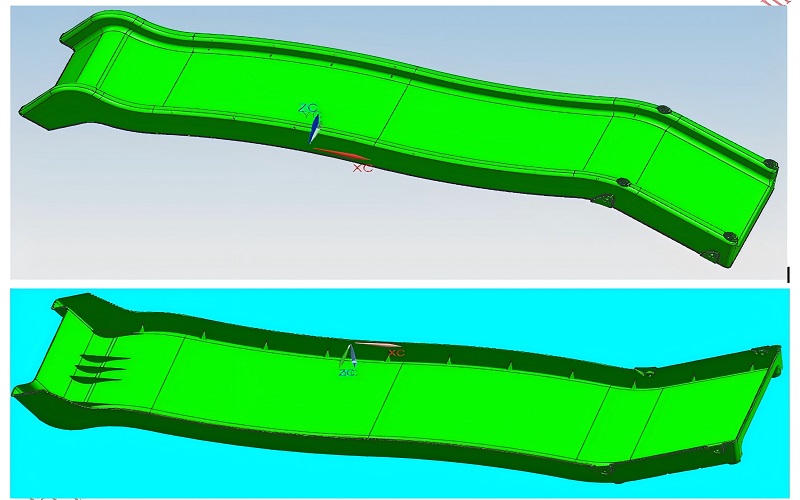
Gas Assist Molding
Gas assist molding is a technique that enhances the injection molding process by introducing pressurized gas into the mold cavity during the injection phase.
This method reduces internal stresses within the plastic resin, allowing for faster flow and improved quality of the molded parts. The result is a smoother surface finish, minimizing the need for secondary finishing processes and enhancing the overall aesthetics of the products.
In addition to its aesthetic benefits, gas assist molding also improves the structural integrity of large injection molded parts. By reducing the amount of material needed and decreasing internal pressure, this technique produces components that are both strong and lightweight, making it an ideal choice for various applications.
Insert Molding
Insert molding is a specialized technique that involves molding plastic around an existing insert piece, such as metal or another type of material. This process creates a strong bond between the plastic and the insert, resulting in a composite part that combines the strengths of both materials. Insert molding is particularly useful in applications where additional strength or functionality is required, such as in electrical components or medical devices.
The primary advantage of insert molding lies in its ability to integrate different materials into a single part, enhancing its overall performance and durability. Carefully selecting the insert materials and optimizing the molding process allows manufacturers to create high-quality components that meet specific performance requirements.
Structural Foam Molding
Structural foam molding is a technique that produces lightweight components by introducing a foaming agent into the plastic resin during the molding process.
The resulting components are lightweight yet maintain their strength and rigidity, making them suitable for various applications, including automotive and industrial equipment. One of the main advantages of structural foam molding is its cost-effectiveness, as it reduces material usage and minimizes waste.
The lightweight nature of structural foam components also contributes to improved energy efficiency in applications where weight reduction is critical. By harnessing the benefits of structural foam molding, manufacturers can produce high-quality, durable parts while optimizing material usage and reducing production costs.
Choosing the Right Injection Molding Machine
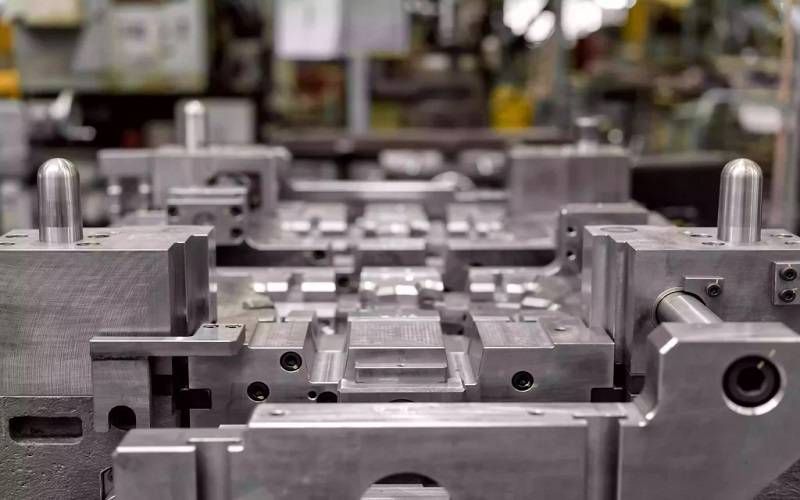
Selecting the right injection molding machine is crucial for achieving optimal production efficiency and product quality. Factors such as clamping force, machine customization, and drive type play a significant role in determining the suitability of the machine for specific applications. For instance, ENGEL’s range of injection molding machines offers clamping forces from 280 kN to 55,000 kN, catering to a wide array of production needs.
Accurately calculating the required clamping force is essential, especially for larger parts that necessitate high tonnage to ensure structural integrity. Moreover, modern injection molding machines are designed to achieve the lowest possible cycle time while maintaining precision, further enhancing production efficiency and providing more clamp force.
Let’s delve into the specifics of large tonnage machines and the various drive types available.
Large Tonnage Machines
Large tonnage machines are indispensable for producing large parts due to their ability to exert the necessary high clamping forces. These machines are designed to handle the significant surface area of large molded parts, ensuring that the mold cavity is filled uniformly and that the final product meets stringent quality standards.
The robust construction of large tonnage machines also ensures that they can withstand the high pressures involved in the large tonnage injection molding process, providing reliable and consistent performance.
The importance of selecting the right tonnage needed cannot be overstated, as it directly impacts the structural integrity and quality of the molded parts. Selecting a machine with the appropriate clamping force enables manufacturers to produce high-quality components that meet specific performance requirements. Tons of attention must be given to these factors.
Drive Types: All-Electric, Hydraulic, Hybrid
The drive type of an injection molding machine significantly influences its performance, energy efficiency, and operational costs. There are three main drive types: all-electric, hydraulic, and hybrid. All-electric machines are becoming increasingly popular due to their energy savings and precision, making them ideal for applications that require high accuracy and repeatability.
Hydraulic machines, on the other hand, offer robust performance and are well-suited for applications that demand high clamping forces. Hybrid machines combine the best of both worlds, offering the energy efficiency of electric machines with the power of hydraulic systems.
Understanding the benefits and limitations of each drive type allows manufacturers to make informed decisions about which machine best meets their specific production needs.
Optimizing the Injection Molding Process
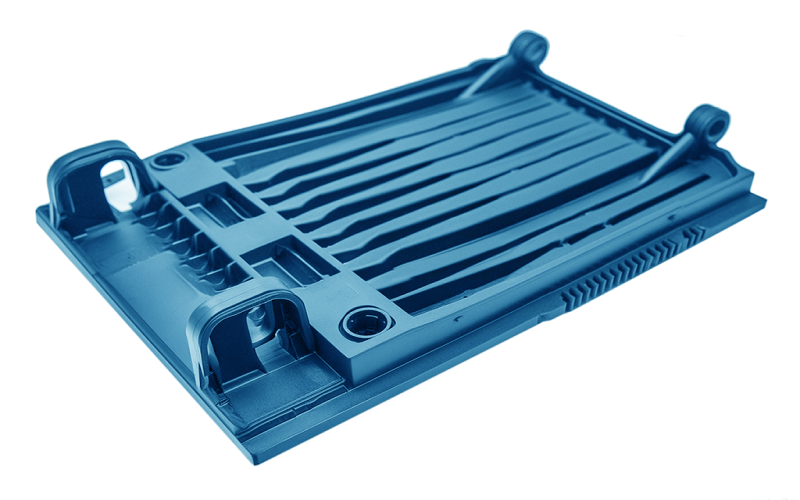
Optimizing the injection molding process is essential for producing high-quality parts efficiently. Key considerations include material handling and preparation, cooling and cycle time management, and surface quality and finishing.
Proper material handling ensures consistency and reduces variability in the final product, while efficient cooling strategies can significantly reduce cycle times without compromising quality. Additionally, achieving high surface quality often requires specific finishing techniques to meet aesthetic and functional standards.
Integrating smart technologies, such as real-time data analysis and AI-driven process control, can further enhance production efficiency and quality. Focusing on these critical aspects enables manufacturers to optimize their injection molding operations and produce high-quality components that meet stringent performance requirements.
Material Handling and Preparation
Proper material handling and preparation are crucial for maintaining the quality and consistency of injection molded parts.
Ensuring that materials are storing parts correctly and prepared adequately can reduce variability and enhance the final product’s performance. For instance, nylon’s moisture absorption properties can affect its performance, making it essential to control humidity levels during storage and preparation.
Effective material handling practices minimize defects and ensure that each batch of molded parts meets the required quality standards, following a general rule. This attention to detail is vital for producing high-quality components consistently.
Cooling and Cycle Time Management
Efficient cooling is a critical factor in reducing cycle times and maintaining the quality of injection molded parts. Techniques such as optimizing cooling line design and using conformal cooling channels can significantly improve the cooling efficiency during the molding process.
These strategies ensure that the molded parts cool uniformly, reducing the risk of warping and other defects, which can be assessed using the melt flow index.
In addition to optimizing the cooling process, selecting optimal cycle parameters and implementing quick mold change systems can further enhance production speed and efficiency. Focusing on cooling and cycle time management enables manufacturers to achieve faster production rates without compromising the quality of the final product.
Surface Quality and Finishing
Achieving high surface quality in injection molded parts is often a key requirement, especially for products where aesthetics are crucial. Techniques such as polishing, coating, and texturing can significantly enhance the appearance and functionality of the parts. These finishing processes ensure that the surface is smooth, free of defects, and meets specific aesthetic standards.
Advanced surface treatment techniques are also essential for improving the durability and performance of the parts. Applying these techniques enables manufacturers to produce high-quality components that not only look good but also perform well in their intended applications, as they are produced with care.
This focus on surface quality and finishing is vital for fulfilling both the aesthetic and functional requirements of large injection molded components, which can be seen as two halves of the overall design.
Innovations in Injection Molding Technology
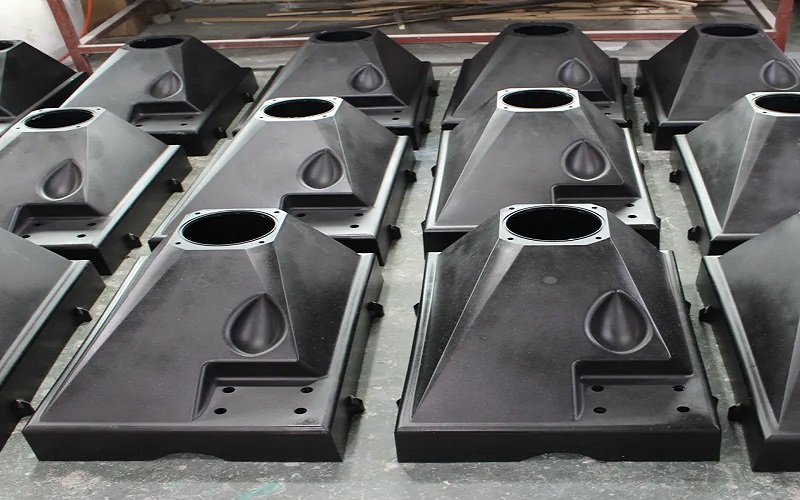
The field of injection molding is continually evolving, with new technologies and innovations enhancing the efficiency and quality of large part production. Energy-efficient machines, for instance, can significantly reduce operational costs and environmental impact by lowering energy consumption by up to 70%. Additionally, the integration of smart manufacturing solutions, such as IoT and AI, allows for real-time monitoring and process optimization, leading to improved production efficiency and quality.
Sustainable practices are also becoming increasingly important in the injection molding industry. Using recycled materials, implementing closed-loop systems, and adopting eco-friendly packaging solutions enables manufacturers to reduce their ecological footprint and contribute to a more sustainable future.
These innovations not only enhance the efficiency and sustainability of injection molding operations but also align with the growing demand for environmentally responsible manufacturing practices.
Energy Efficient Machines
Energy-efficient injection molding machines have become a game-changer in the industry, offering significant reductions in energy consumption and operational costs. These machines are designed to optimize energy use, often reducing consumption by up to 70% compared to traditional machines. The result is a lower carbon footprint and substantial cost savings for manufacturers.
Investing in energy-efficient machinery allows manufacturers to achieve the highest performance while minimizing their environmental impact. This not only benefits the bottom line but also supports sustainability goals, making energy-efficient machines a wise choice for modern manufacturing operations.
Smart Manufacturing Solutions
Smart manufacturing solutions are revolutionizing the injection molding industry by integrating advanced technologies for real-time data collection and process optimization.
These technologies enable manufacturers to monitor production parameters closely, make real-time adjustments, and improve overall efficiency and product quality. The use of AI and IoT, for example, allows for predictive maintenance and energy optimization, further enhancing the performance of manufactured injection molding operations.
Combining smart manufacturing solutions with energy-efficient machines enables manufacturers to create a cohesive ecosystem that supports sustainable and efficient production practices. This integration not only improves operational performance but also aligns with the industry’s move towards fewer companies that focus on more eco-friendly and cost-effective manufacturing solutions.
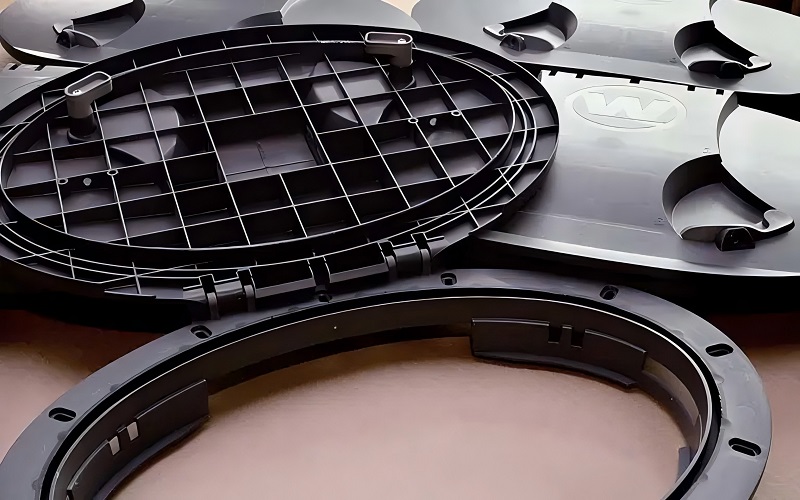
Sustainable Practices
Sustainable practices in injection molding are essential for reducing the environmental impact of manufacturing operations. Incorporating renewable energy sources, such as solar and wind power, can significantly lower energy consumption.
Additionally, using recycled plastics from post-consumer or post-industrial waste helps minimize the environmental footprint of plastic production.
Efficient waste management practices, such as implementing closed-loop systems, allow manufacturers to recycle excess or defective parts back into the production cycle, reducing waste and promoting sustainability.
By adopting these eco-friendly practices, manufacturers can produce high-quality components while contributing to a more sustainable future.
Summary
In summary, large part injection molding is a cornerstone of modern manufacturing, offering the ability to produce complex, high-quality components efficiently and cost-effectively.
By selecting the right materials, utilizing advanced molding techniques, and optimizing the injection molding process, manufacturers can achieve remarkable results that meet stringent quality and performance standards. Innovations in technology and sustainable practices further enhance the capabilities and environmental responsibility of injection molding operations.
As we look to the future, the continued evolution of injection molding technology promises even greater efficiency, precision, and sustainability. By embracing these advancements, manufacturers can stay ahead of the curve and deliver exceptional products that drive progress across various industries. The journey of large part injection molding is a testament to the power of innovation and the relentless pursuit of excellence in manufacturing.
Frequently Asked Questions
Can injection molding be used for large parts?
Yes, injection molding can effectively be used for producing large plastic parts, particularly in industries like automotive, where consistency and quality are essential.
What are the common materials used in large part injection molding?
Large part injection molding commonly uses materials like High-Density Polyethylene (HDPE), acrylic (PMMA), and nylon (PA), selected for their specific properties suited to various applications.
How does gas assist molding improve the quality of injection molded parts?
Gas assist molding enhances the quality of injection molded parts by reducing internal stresses in the plastic resin, resulting in smoother surfaces and greater structural integrity.
Why is selecting the right injection molding machine important?
Selecting the right injection molding machine is crucial as it directly impacts production efficiency, quality, and the ability to meet specific manufacturing requirements. Having the appropriate clamping force and optimized cycle times enhances overall productivity.
What are the benefits of using energy-efficient injection molding machines?
Using energy-efficient injection molding machines can significantly lower energy consumption by up to 70%, which in turn reduces both operational costs and environmental impact while ensuring high performance.