Why choose large plastic gears over metal ones?
This article explains their advantages, types, materials, design, manufacturing, and applications. You’ll learn why engineers across industries are switching to plastic gears.
The Advantages of Large Plastic Gears
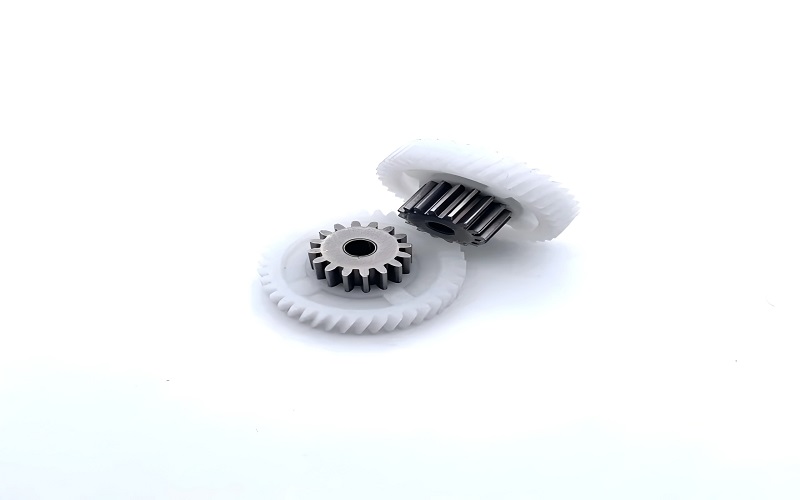
Large plastic gears offer a plethora of advantages over traditional metal gears, making them an attractive option for various applications. One of the most significant benefits is their lightweight nature, which makes them ideal for devices requiring low-mass components. This attribute not only enhances the efficiency of the device but also reduces the overall energy consumption.
Another advantage of plastic gears is their excellent resistance to corrosion and chemicals. Unlike metal gears, which can corrode or degrade when exposed to harsh environments, plastic gears maintain their integrity and performance. This makes them suitable for applications in challenging conditions, such as medical equipment and outdoor devices.
While it’s true that plastic gears generally have a shorter lifespan compared to metal gears, their initial cost and reduced maintenance requirements make them a cost-effective choice for many applications. The combination of affordability, durability, and low maintenance makes large plastic gears a smart investment for any industry looking to optimize performance and reduce costs.
Types of Large Plastic Gears
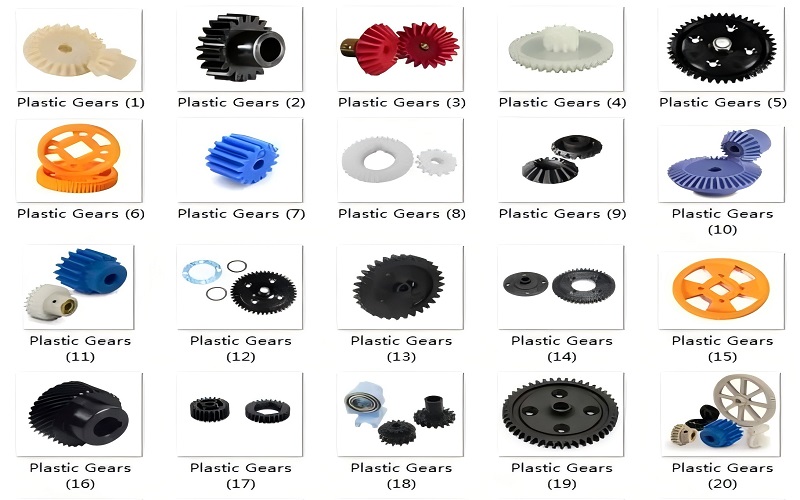
Large plastic gears come in various types, each designed to meet specific needs and applications. The most common type is the plastic spur gear, known for its straight teeth and high efficiency. These gears are cylindrical with teeth that mesh parallel to the shaft, making them ideal for applications requiring precise motion transfer and high accuracy in power transmission, often available as stock items for quick procurement.
Another type of large plastic gear is the plastic bevel gears, which features a cone shape that allows for force transmission between intersecting shafts. The teeth of bevel gears are designed along the surface of the cone, enabling smooth and efficient power transfer in applications where shafts intersect at an angle.
Plastic worm gears consist of a screw-shaped component (worm) that meshes with a gear (worm wheel) to transmit torque between non-intersecting shafts. These gears are particularly useful in applications requiring significant torque reduction and smooth, quiet operation.
Understanding the different types of large plastic gears, including those paired with a pinion in rack-and-pinion systems for linear motion, helps engineers select the most suitable option for their specific needs.
Materials Used in Large Plastic Gears
The choice of materials is crucial in the performance and durability of large plastic gears. Two primary materials used are MC Nylon, also known as Polyamide 6, and Duracon, an acetal copolymer. MC Nylon is renowned for its significant resistance to wear and ability to operate with minimal lubrication, thanks to its inherent lubricity.
Duracon, on the other hand, offers excellent resistance to organic chemicals and is lighter than many metals, making it suitable for various engineering applications. One of the key advantages of Duracon is its lower moisture absorption rate compared to MC Nylon, which helps it maintain its dimensions better over time.
Both materials contribute to the overall resistance of plastic gears to corrosion and rust, making them ideal for applications exposed to moisture and chemicals. By carefully selecting the right material, manufacturers can ensure that their plastic gears perform optimally in their intended applications.
Design Considerations for Large Plastic Gears
Designing large plastic gears requires meticulous attention to detail to ensure optimal performance. One critical consideration is the use of helical gears, which feature angled teeth that provide smoother and quieter operation compared to spur gears. This makes them suitable for high-speed applications where noise reduction is essential.
Backlash is another important factor that must be accounted for in the design of plastic gears. Due to their thermal expansion characteristics, plastic gears require more allowance for backlash than metal gears. Collaborating with skilled manufacturers can enhance the quality assurance of custom large plastic gears, as they utilize cutting-edge technologies and methods to improve performance.
Thermal expansion and moisture absorption are significant factors affecting the dimensions of plastic gears. MC Nylon gears, for example, can lengthen considerably when exposed to varying temperatures, emphasizing the importance of considering thermal effects in their application.
By engaging with experienced manufacturers, innovative design solutions can be developed to address these challenges and improve the functionality of large plastic gears.
Manufacturing Processes for Large Plastic Gears
The manufacturing process of large plastic gears plays a crucial role in their precision and performance. Precision in manufacturing requires careful control over the molding temperature and injection pressure to minimize errors. High-precision plastic gear production often utilizes advanced injection molding machines equipped with sensors to monitor and regulate various molding parameters.
New molding techniques, such as gas-assisted injection and injection-compression molding, are being explored to enhance gear quality and reduce internal stresses. These techniques help produce gears with better dimensional accuracy and improved mechanical properties. Cooling steps during the molding process are also critical, as consistent cooling rates across the mold cavities are necessary to achieve uniform gear precision.
Controlling the environment within the molding area is crucial, as fluctuations in temperature and humidity can significantly impact the dimensional accuracy of large plastic gears. Additionally, the use of high-performance resins and glass fiber-filled composites enables the production of more complex geometries and enhanced strength in plastic gears.
Applications of Large Plastic Gears
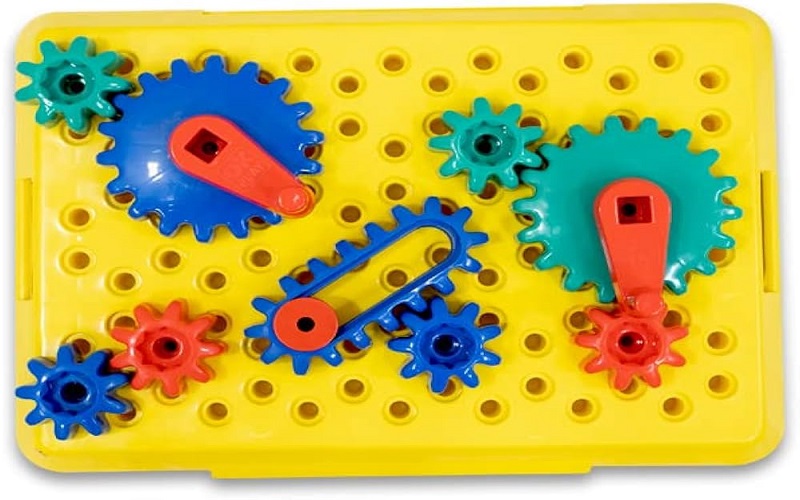
Large plastic gears are incredibly versatile and find utility across various industries. In office automation devices, they enable efficient and quiet operation, making them ideal for printers and copiers. Toys frequently incorporate large plastic gears due to their lightweight and safe characteristics, ensuring both performance and safety for children.
Electric loaders often use large plastic gears to enhance their performance while reducing weight, contributing to energy efficiency and ease of handling. Medical equipment benefits from large plastic gears as they are corrosion-resistant and can operate without lubrication, ensuring reliability and hygiene.
The versatility of large plastic gears makes them suitable for a wide range of applications, demonstrating their utility across various industries.
Maintenance and Lubrication of Large Plastic Gears
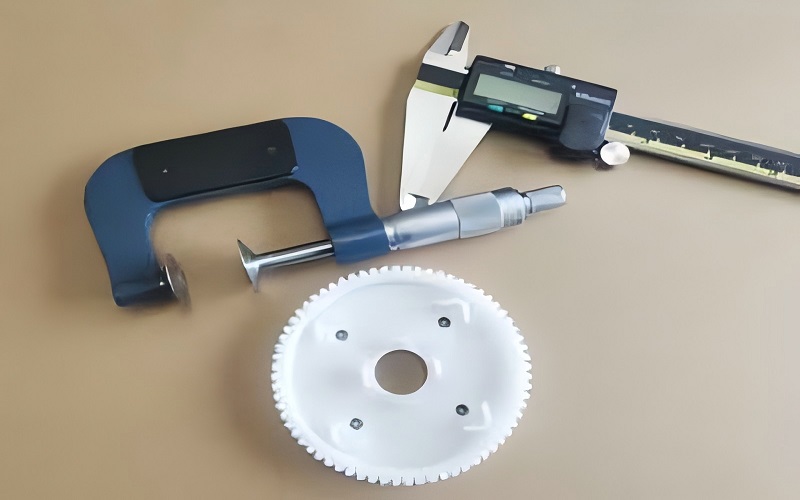
Maintaining and lubricating large plastic gears properly ensures their longevity and performance. Lubrication is particularly crucial in high-speed applications to mitigate heat buildup and reduce friction. Choosing a compatible lubricant prevents damage like stress cracking. Silicone-based and certain synthetic hydrocarbons are generally compatible lubricants for plastic components.
High-viscosity oils can adversely affect plastic gears, so lubricants with lower viscosity ratings are preferable to ensure smooth operation. One of the advantages of large plastic gears is their lower maintenance requirements compared to metal gears, as they tend to self-lubricate and are less prone to wear.
Following proper maintenance and lubrication practices significantly enhances the lifespan and performance of large plastic gears.
Cost-Effectiveness of Large Plastic Gears
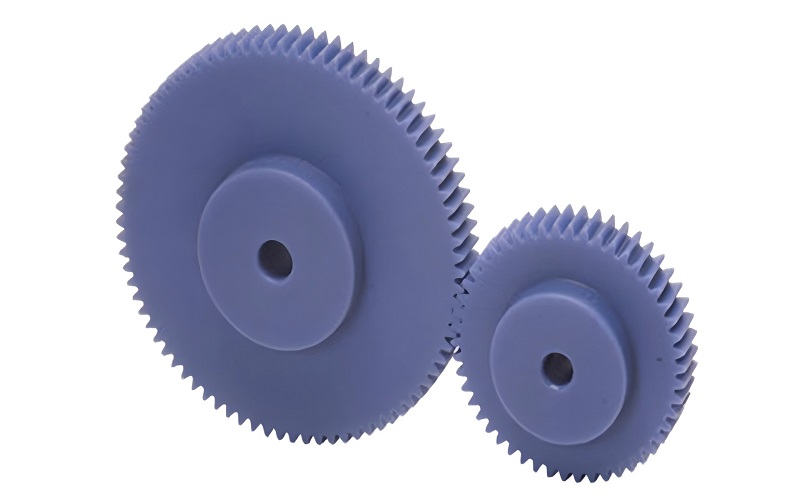
The cost-effectiveness of large plastic gears is one of their most attractive features. These gears are chosen for their affordability, making them ideal for budget-sensitive applications. Plastic gears can achieve significant cost reductions compared to metal gears, with potential savings of 50% to 90% due to the elimination of secondary processing. The lower raw material costs and minimal machining requirements further contribute to their economic advantage, highlighting the price benefits of using plastic gears.
Using synthetic lubricants can enhance the performance of plastic gears in high-temperature and long-duration applications, as they offer better aging resistance. Contrary to common misconceptions, plastic gears require lubrication to minimize friction and wear, which can significantly extend their lifespan. Tests indicate that lubricated plastic sliding bearings can last up to five times longer than those without lubrication.
Avoiding additives like graphite or molybdenum disulfide is crucial, as they can weaken plastic components.
Partnering with Experts for Custom Large Plastic Gears
Collaborating with experienced manufacturers is key to developing custom large plastic gears that meet specific requirements. Collaborating with experts allows for tailored adjustments that address unique operational challenges in gear applications. Accessing expert knowledge ensures that the custom adjustments enhance the performance and reliability of the gears.
The benefits of utilizing expert insights lead to higher quality, optimized solution for large plastic gears in various applications. Working with a skilled team allows businesses to achieve innovative solutions that meet their specific needs and improve overall system functionality.
Summary
In summary, large plastic gears offer numerous advantages, including lightweight nature, resistance to corrosion and chemicals, and cost-effectiveness. Understanding the different types of gears, materials used, and design considerations is crucial for optimizing their performance. The advanced manufacturing processes ensure precision and reliability, making these gears suitable for a wide range of applications.
Partnering with experts for custom solutions enhances the quality and performance of large plastic gears, ensuring they meet specific operational requirements. Embracing the benefits of large plastic gears can lead to innovative and efficient solutions in precision engineering. The future of large plastic gears is promising, and now is the time to explore their potential.
Frequently Asked Questions
What are the main advantages of using large plastic gears over metal gears?
Large plastic gears are advantageous due to their lightweight nature, resistance to corrosion and chemicals, and cost-effectiveness, while also requiring less maintenance. However, it’s important to note they typically have a shorter lifespan compared to metal gears.
What types of large plastic gears are available?
Large plastic gears primarily consist of plastic spur gears, bevel gears, and worm gears, each engineered for specific applications and power transmission requirements. Selecting the right type depends on your project’s unique needs.
What materials are commonly used in the production of large plastic gears?
Large plastic gears are commonly produced using materials like MC Nylon (Polyamide 6) and Duracon (acetal copolymer), which provide excellent wear resistance and chemical stability. Choosing the right material ensures durability and optimal performance in various applications.
What are the key design considerations for large plastic gears?
Key design considerations for large plastic gears include accounting for thermal expansion and moisture absorption, ensuring proper backlash, and collaborating with expert manufacturers to improve gear quality and performance. These factors are crucial for optimizing functionality and durability.
Why is partnering with experts important for custom large plastic gears?
Partnering with experts is crucial for custom large plastic gears as it enables tailored adjustments and innovative solutions that address specific operational challenges, ensuring higher quality and optimized performance. This collaboration ultimately enhances the effectiveness of your applications.