Mass production is the process of creating large quantities of products quickly and cost-effectively. It uses automated systems and assembly lines to make standardized goods.
In this article, we’ll discuss the methods, benefits, and challenges of mass production.
Understanding Mass Production
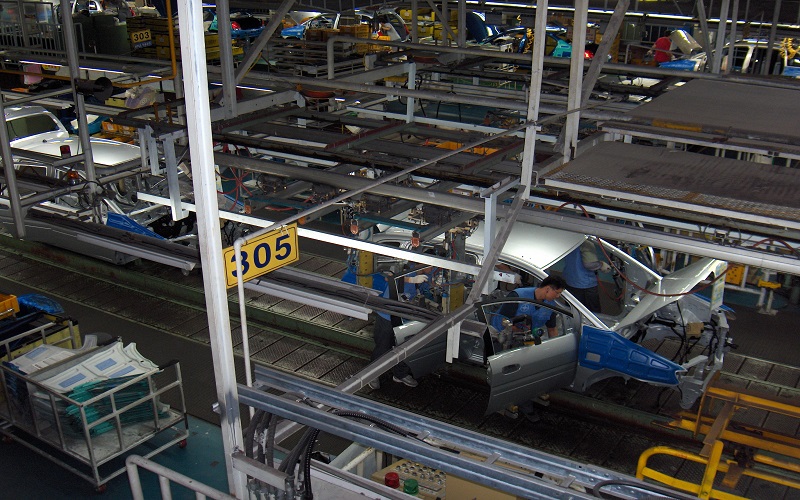
Mass production refers to a manufacturing method designed for large-scale, high-volume production. This approach seeks to lower production costs. As a result, goods become more affordable and accessible to consumers.
Key characteristics include specialization, mechanization, and a relentless focus on speed, efficiency, and consistency. From food to automobiles, mass production systems have touched nearly every aspect of our lives, producing standardized products that meet large-scale demand.
The foundation of mass production lies in the division and specialization of labor, highly automated processes, and the use of assembly lines. These elements enable the production of large quantities of goods with remarkable efficiency.
However, to fully grasp the significance of mass production, we must explore its historical context and the revolutionary techniques that brought it to life.
The Assembly Line Technique
The assembly line technique, developed by Henry Ford, revolutionized manufacturing by significantly improving efficiency and reducing production time. By dividing the production process into smaller, specialized tasks, factory workers could focus on specific roles, enhancing overall productivity.
This method demonstrated that even complex products, like automobiles, could be efficiently manufactured using assembly line techniques.
Assembly lines are particularly effective for producing complex products, such as electronics and automobiles. By organizing processes into a comprehensive assembly line and production lines, manufacturers achieve rapid assembly and high-volume production, meeting large-scale consumer demand with ease.
The efficiency of this technique is evident in the organized sequence of assembly lines, often resembling the skeleton of a fish, ensuring smooth material flow and optimized production.
Historical Context: The Industrial Revolution
The Industrial Revolution marked a pivotal shift from handcrafted goods to mass production techniques. Innovations such as the steam engine and advancements in textile manufacturing played crucial roles in this transition, laying the groundwork for modern mass production.
The textile industry, in particular, saw significant changes with the introduction of mechanized looms and cotton mills, revolutionizing the way fabrics were produced.
Military organizations’ increased demand for uniforms and supplies further accelerated the development of mass production techniques. Before the widespread adoption of these methods, production was often conducted using general tools or basic machinery within homes or small shops.
The Industrial Revolution not only transformed manufacturing processes but also set the stage for the mass production systems we rely on today.
How Mass Production Works
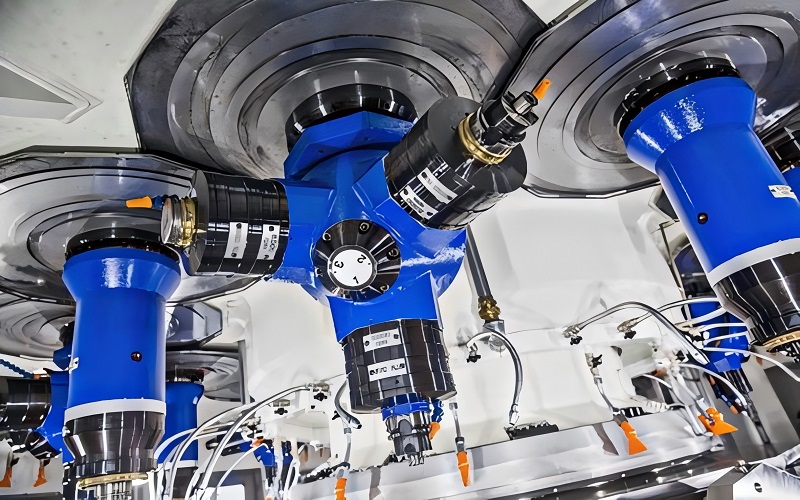
Mass production operates on principles of division of labor, high-volume manufacturing, and efficient material flow. These principles are rooted in mechanization, automation, and repetitive standardized processes that help maintain low production costs. By utilizing precision machining equipment and flow production techniques, mass production ensures efficient and speedy manufacturing operations.
Quality control is a critical aspect of mass production, ensuring that products meet high standards and reliability through defect checks at various stages. Standardization reduces errors and simplifies training for workers, significantly impacting quality assurance.
The high-volume capability of mass production is achieved through mechanization, which maintains careful control of quality standards and allows for the production of large quantities of goods. To understand how these principles come together, we need to explore the role of division of labor and automation technology in detail.
Division of Labor
Specialization of tasks in mass production leads to increased efficiency and reduced production costs. By assigning specific roles to workers, such as sewing, hemming, or finishing, manufacturers can streamline the production process and enhance productivity. This approach not only speeds up the manufacturing operations but also reduces labor costs by minimizing redundant roles.
Mechanization further complements the division of labor by automating routine tasks, allowing fewer workers to produce goods more efficiently. The assembly line method exemplifies this principle, where factory workers focus on specialized tasks, contributing to a smooth and efficient production process.
This division of labor is a hallmark of the industrial revolution, marking a significant leap in manufacturing efficiency.
Automation Technology
Automation technology plays a pivotal role in modern mass production by enhancing precision and operational efficiency. Automated systems reduce labor requirements and enable faster assembly rates compared to traditional methods.
By integrating artificial intelligence, manufacturers can optimize supply chains and enhance predictive maintenance, further improving efficiency and reducing downtime.
The use of automated machines in manufacturing operations ensures high standards of quality control and minimizes defects. Automation technology not only speeds up the production process but also allows for the production of mass-produced items with consistent quality. This technological advancement has become a cornerstone of modern mass production systems, driving efficiency and precision in manufacturing.
Real-World Examples of Mass Production
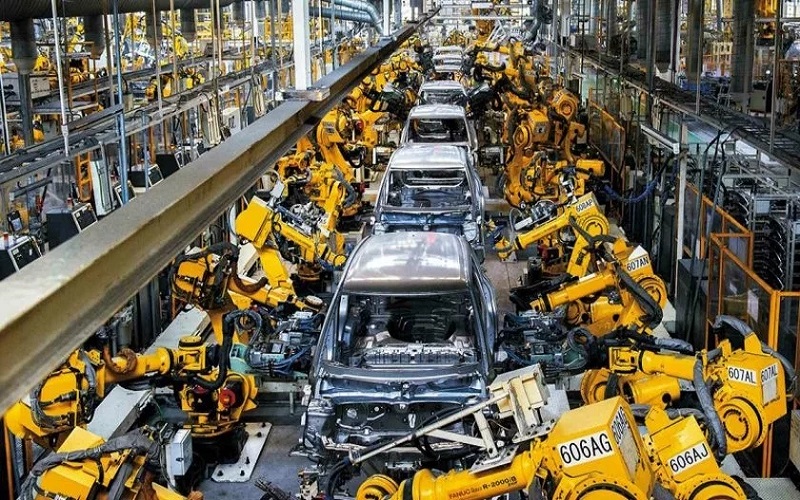
To truly appreciate the impact of mass production, it’s essential to examine real-world examples that highlight its transformative power.
From the automotive industry to consumer electronics, mass production methods have revolutionized how we produce and consume goods. These examples showcase the efficiency and scalability of mass production systems, making products more accessible and affordable for consumers.
The following subsections will delve into specific cases, such as the Ford Motor Company’s production of the Model T and the mass production of consumer electronics, to illustrate the practical applications and benefits of mass production techniques.
Ford Motor Company and the Model T
Henry Ford pioneered the first moving assembly line in 1913, drastically reducing the production time for a car from over 12 hours to just 2.5 hours. This innovation not only increased efficiency but also made the Model T affordable for the average American family. Ford’s mass production system produced over 15 million Model T cars between 1908 and 1927, demonstrating the success of his methods.
The impact of Ford’s innovations on the automobile industry cannot be overstated. By implementing a comprehensive assembly line, Ford Motor Company revolutionized car manufacturing, setting a new standard for production efficiency and affordability. This approach laid the groundwork for modern mass production techniques used across various industries today.
Consumer Electronics
Mass production methods allow companies like Apple to efficiently produce high-volume electronics, such as iPhones. Automated stations perform tasks like soldering and assembling, ensuring precision and consistency in the manufacturing process. This approach not only meets high consumer demand but also maintains the quality and reliability of mass-produced products.
The production of consumer electronics often involves clean rooms and robotic automation to ensure the highest standards of quality control. By leveraging advanced technologies, manufacturers can produce large quantities of electronics with remarkable efficiency, making these products more accessible to consumers worldwide.
Benefits of Mass Production
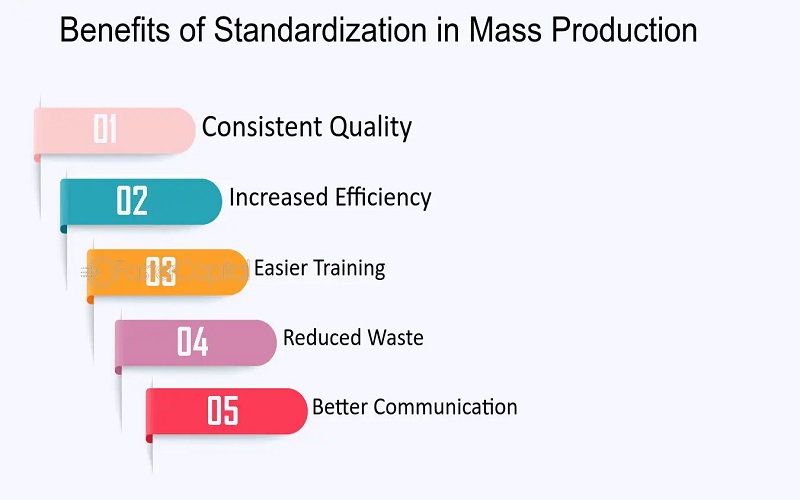
Mass production offers numerous benefits, including cost efficiency, increased productivity, and standardization. These advantages have made mass production a cornerstone of modern manufacturing, enabling companies to produce large quantities of goods at lower costs and with higher consistency.
The following subsections will explore each of these benefits in detail, highlighting how mass production methods contribute to the overall efficiency and affordability of products.
Cost Efficiency
Economies of scale play a significant role in reducing the cost per unit in mass production. By spreading fixed costs over many outputs, manufacturers can achieve lower production costs and higher profit margins. Bulk purchasing of raw materials and automation technology further contribute to cost reductions, making mass produced items more affordable for consumers.
Larger companies particularly benefit from mass production by achieving substantial savings on costs and passing these savings on to consumers in the form of lower cost prices. This cost efficiency not only enhances profit margins but also makes essential goods more accessible to the average consumer.
Increased Productivity
Mass production significantly boosts productivity by enabling faster assembly and higher output. The integration of automation technology and collaborative robots in manufacturing operations enhances efficiency and safety, leading to quicker assembly rates and reduced labor costs. Electrification has also played a crucial role in increasing output for manufacturing processes, with a notable 30% increase in productivity.
High-volume production capacity allows manufacturers to meet mass produce market demand efficiently, ensuring that products are readily available to consumers. This increased productivity is a key advantage of mass production, driving the rapid production of goods and supporting the needs of a growing consumer base.
Standardization and Quality Control
Standardization in mass production ensures that consumers receive uniform products with consistent quality. Quality control measures are integral to the manufacturing process, identifying defects early and maintaining high standards throughout production. The use of mechanization allows for efficient material flow and stringent quality control, minimizing errors and enhancing product reliability.
Consistent quality and reliability are foundational benefits of standardization, helping to build customer trust and brand loyalty. By delivering standardized products, manufacturers can ensure that consumers have confidence in the quality and performance of mass-produced items, further solidifying the advantages of mass production.
Challenges and Disadvantages of Mass Production
While mass production offers numerous benefits, it also presents several challenges and disadvantages. Quality issues, low employee morale, and environmental impact are some of the key concerns associated with mass production.
The following subsections will explore these challenges in detail, highlighting the potential drawbacks of mass production methods and the need for sustainable practices.
High Initial Investment
Mass production requires a significant capital investment to establish effective production capabilities. The setup of mass production systems often involves considerable costs for specialized machinery and facilities, making it a capital-intensive endeavor. This high initial investment can deter smaller enterprises from entering the market, posing a barrier to competition and innovation.
Despite the potential for higher profits and efficient production, the substantial upfront financial commitment required for mass production necessitates careful financial planning and resource allocation. Companies must weigh the benefits of mass production against the significant investment needed to implement these systems effectively.
Inflexibility
Mass production systems are generally rigid, making adjustments to product designs expensive and time-consuming. This inflexibility can be challenging when consumer preferences shift or new market demands arise. Companies may find it difficult to adapt quickly within the constraints of a mass production framework, leading to potential delays and increased costs.
The focus on uniformity and standardization, while beneficial for efficiency, creates inherent limitations in responding to changes. This rigidity can hinder innovation and responsiveness, making it difficult for manufacturers to offer customized or updated products without significant reconfiguration of their production processes.
Environmental Impact
Mass production practices can contribute to significant environmental issues if not properly managed. The emphasis on maximizing production volume often leads to resource depletion and waste generation, posing ecological sustainability challenges. Manufacturing operations that prioritize rapid production and high output may neglect the environmental consequences of their practices.
Addressing these environmental concerns requires a shift towards more sustainable manufacturing methods and practices. Companies must balance the benefits of mass production with the need to minimize their ecological footprint, implementing measures to reduce waste, conserve resources, and adopt greener technologies.
Innovations in Mass Production
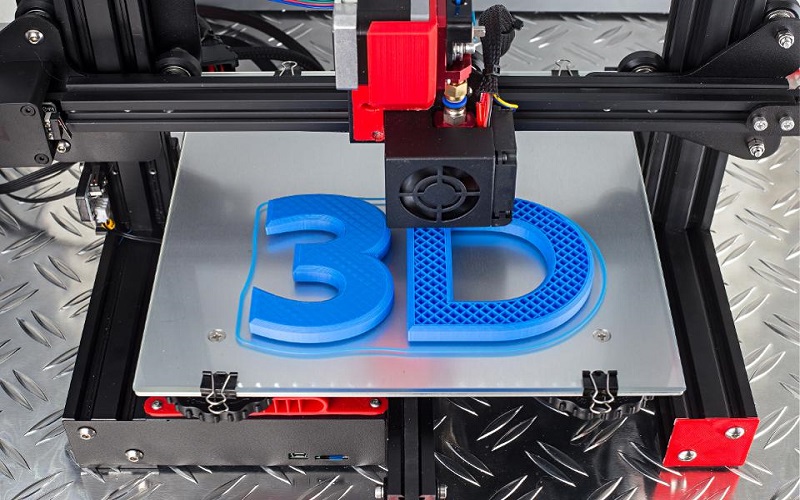
Recent technological innovations have further transformed mass production, enhancing efficiency, precision, and adaptability. Advancements in robotics, artificial intelligence, and 3D printing are at the forefront of this evolution, offering new opportunities for manufacturers to optimize their operations and meet consumer demands.
Robotics and artificial intelligence play pivotal roles in modern manufacturing by automating repetitive tasks and improving precision. These technologies enhance operational efficiency, reduce human error, and enable faster production rates. Additionally, the use of augmented reality for training and maintenance has emerged as a valuable tool, further streamlining manufacturing processes.
The following subsections will explore specific innovations such as 3D printing and the integration of AI and robotics, highlighting their impact on mass production and the benefits they bring to the manufacturing landscape.
3D Printing
Integrating 3D printing into mass production processes offers significant advantages, including the ability to produce intricate parts in a single step. This technology reduces the time and costs associated with traditional manufacturing methods, enabling manufacturers to respond more swiftly to market demands and customization requests.
The integration of artificial intelligence in 3D printing further enhances product quality by enabling real-time error detection and correction during the manufacturing process. This combination of technologies ensures that mass produced items meet the highest standards of precision and reliability, paving the way for innovative and efficient production methods.
AI and Robotics
Robots play a crucial role in modern manufacturing by automating repetitive tasks and ensuring high efficiency. The use of robotics enhances speed and precision in production, minimizing defects and reducing human error. By handling tasks that are monotonous or hazardous, robots also improve workplace safety and allow human workers to focus on more complex and value-added activities.
The integration of artificial intelligence further optimizes manufacturing operations by enhancing predictive maintenance and optimizing supply chains. These advancements enable manufacturers to maintain continuous production flow and minimize downtime, ensuring that mass-produced products are delivered with consistent quality and efficiency.
Mass Customization vs. Mass Production
Mass customization is a production strategy. It merges the cost advantages of mass production with the ability to cater to individual customer needs. While mass production focuses on standardized, low-cost products, mass customization aims to provide personalized options without sacrificing efficiency. This approach allows manufacturers to offer tailored products at scale, meeting diverse consumer preferences while maintaining the advantages of high-volume production.
The following subsections will explore how mass customization is implemented in various industries and provide case studies that illustrate its effectiveness in balancing efficiency and personalization.
Tailored Products at Scale
In the automotive industry, mass customization allows customers to choose specific features and options while the core product remains standardized. This approach enables manufacturers to offer a variety of configurations without compromising on production efficiency. Furniture companies similarly offer customization options for fabrics and components, blending the efficiency of mass production with personalized product choices.
Mass customization effectively combines the benefits of mass production with the ability to meet individual consumer needs. By leveraging specialized machinery and flexible production processes, manufacturers can produce large quantities of tailored products, ensuring that consumers receive exactly what they want without the high costs associated with traditional customization methods.
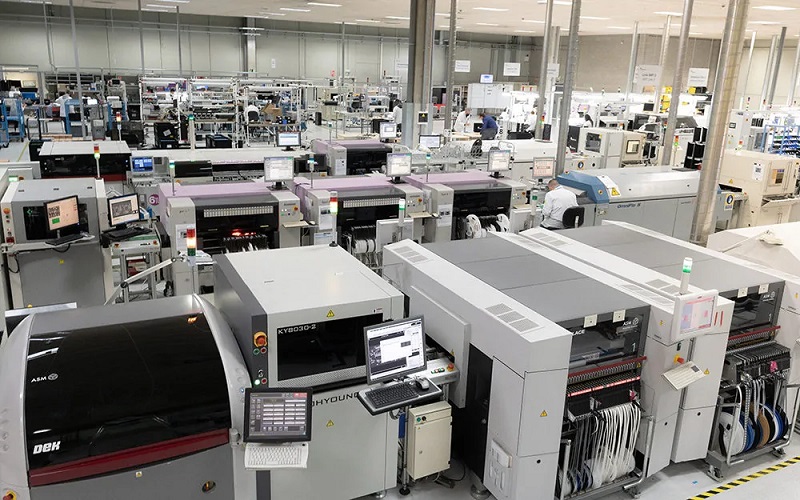
Case Studies
The Ford Motor Company’s introduction of the Model T revolutionized the automotive industry by mass-producing cars at an affordable price while meeting varied consumer needs. This early example of mass customization demonstrated the potential to combine high-volume production with tailored options, setting a precedent for future innovations.
In the realm of consumer electronics, Apple effectively uses mass customization methods to produce high-volume yet personalized products, fulfilling diverse consumer demands. These case studies illustrate the effective implementation of mass customization by leading companies, enhancing both production efficiency and consumer satisfaction.
By adopting mass customization, manufacturers can achieve the best of both worlds: efficiency and personalization.
Summary
Mass production has fundamentally transformed the manufacturing landscape, offering numerous benefits such as cost efficiency, increased productivity, and consistent quality. However, it also presents challenges, including high initial investments, inflexibility, and environmental impact. Innovations in technology, such as 3D printing, AI, and robotics, are continuously shaping the future of mass production, enhancing its efficiency and adaptability.
As we move forward, balancing the advantages of mass production with sustainable practices and the flexibility of mass customization will be crucial. By embracing these advancements, manufacturers can continue to meet the evolving needs of consumers while maintaining high standards of quality and efficiency. The journey of mass production is one of constant innovation, and its impact on our lives remains profound and far-reaching.
Frequently Asked Questions
What is mass production?
Mass production is a manufacturing process focused on the efficient, large-scale production of goods, allowing for lower production costs and greater accessibility for consumers.
How did Henry Ford revolutionize mass production?
Henry Ford revolutionized mass production by implementing the assembly line technique, which dramatically decreased production time for automobiles, thereby making them accessible to the average family. This innovation transformed manufacturing efficiency and consumer accessibility.
What are the main benefits of mass production?
The main benefits of mass production are cost efficiency, increased productivity, and consistent quality achieved through standardization. By implementing these practices, companies can improve their operational effectiveness and deliver reliable products to consumers.
What challenges are associated with mass production?
Mass production faces challenges such as significant initial investment, lack of flexibility to adapt to market shifts, and adverse environmental impacts from resource depletion and waste generation. These factors can hinder operational efficiency and sustainability.
What is mass customization?
Mass customization is a production strategy that merges the efficiency of mass production with the ability to tailor products to individual customer preferences, resulting in customized items at scale. This approach balances cost-effectiveness with personalized offerings.