Mold flow analysis helps improve the plastic injection molding process by predicting how molten plastic fills molds and identifying potential issues beforehand.
This leads to better part quality, fewer defects, and more efficient production. In this article, discover the benefits, key components, and real-world applications of mold flow analysis.
Understanding Mold Flow Analysis
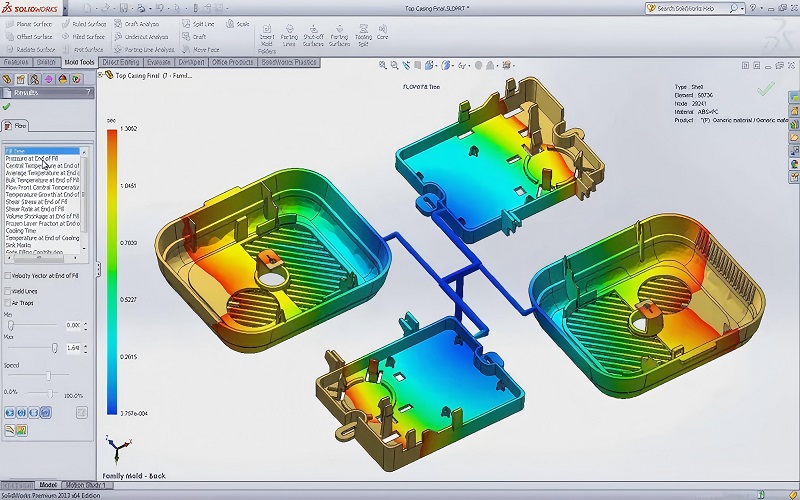
Mold flow analysis is a sophisticated computerized simulation methodology that provides invaluable insights into plastic injection and compression molding. This advanced technique, often accessible through a simplified user interface, helps mold engineers to predict and optimize various aspects of the molding process, significantly enhancing part quality and manufacturability.
Simulating the flow behavior of molten plastic within a mold, this analysis identifies potential issues and areas for improvement, including fiber orientation in reinforced materials, establishing it as a cornerstone in plastic injection molding processes. Modern software often requires an internet connection to access cloud-based simulation tools, ensuring real-time updates and collaboration.
Definition and Purpose
At its core, mold flow analysis evaluates and optimizes designs for single cavity or multi-cavity molds, meticulously assessing part manufacturability, tool design, and material choice, including considerations for fiber orientation in composites. The primary purpose of this analysis is to identify issues such as potential welding, short shots, and air trap problems before they manifest in the actual production process.
This proactive approach, facilitated by a simplified user interface and supported by an internet connection for seamless data integration, ensures that parameters like pressure and fill time are optimized, ultimately enhancing production efficiency and reducing the risk of defects.
Key Components of Mold Flow Analysis
The effectiveness of mold flow analysis hinges on its ability to scrutinize key factors such as pressure, fill time, and melt temperature. These components are critical as they significantly influence the molding process and the quality of the final product.
For instance, pressure and fill time determine how well the mold is filled, while melt temperature affects the viscosity of the material properties, ultimately influencing the flow behavior during injection.
By analyzing these variables, mold flow analysis provides a comprehensive understanding that guides mold designs and optimizations.
When to Use Mold Flow Analysis
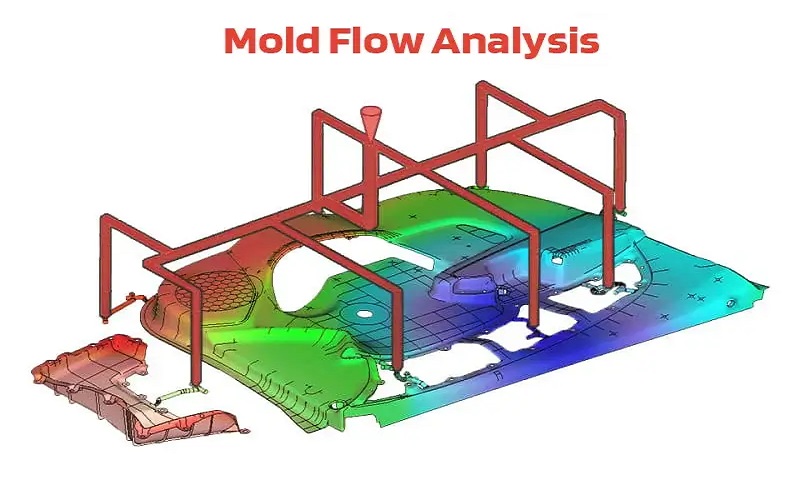
Mold flow analysis is most effective when employed early in the mold design process. Identifying potential issues early allows manufacturers to make adjustments that save time and reduce costs.
However, its utility isn’t limited to the initial stages; mold flow analysis is equally beneficial during design modifications, ensuring that any changes made do not adversely affect the molding process.
Pre-Production Optimization
Conducting mold flow analysis during the early design phase is a proactive measure that can significantly enhance efficiency and part manufacturability. Simulating the molding process, often supported by video tutorials and service providers, allows engineers to predict issues like welding, air traps, short shots, and part warpage.
This foresight allows for design modifications that optimize the flow parameters for different materials, reducing the risk of costly tooling mistakes and enhancing overall product quality.
This early intervention, guided by service teams offering mold flow expertise and visualized through video simulations, not only minimizes the risk of defects like part warpage but also ensures that the final product meets the desired specifications across different materials.
During Design Modifications
When it comes to design modifications, mold flow analysis is an invaluable tool. It provides critical insights that help engineers predict how changes will influence the molding process. Simulating the impact of design alterations on material flow and potential defects, mold flow analysis helps designers make informed decisions to enhance manufacturability.
This ensures that any modified product design does not compromise part quality or functionality, and we can modify it as needed.
Advantages of Mold Flow Analysis
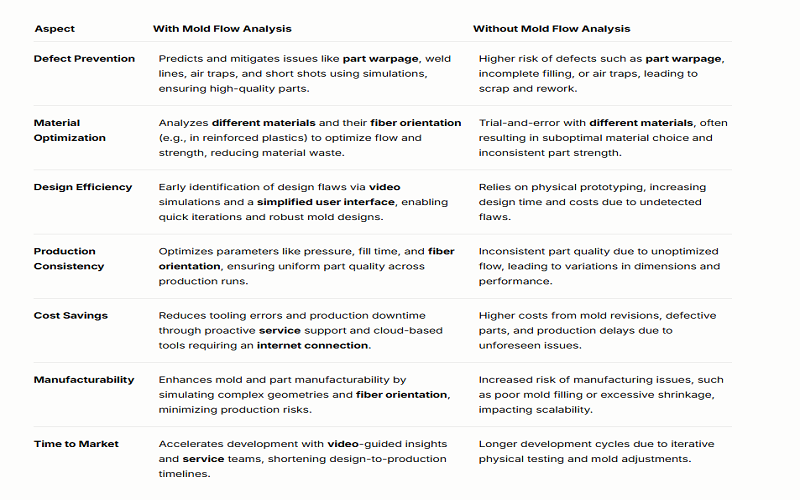
The advantages of mold flow analysis are manifold, making it a crucial preliminary step in the injection molding process.
Here are some key benefits of mold flow analysis:
- Predicts product outcomes regarding quality and functionality
- Helps manufacturers improve production quality
- Reduces defects
- Enhances overall efficiency
By utilizing mold flow analysis, manufacturers can ensure a more streamlined and effective injection molding process with mold inserts.
Let’s delve deeper into how it achieves these remarkable benefits.
Improving Part Quality
One of the most significant benefits of mold flow analysis is its ability to improve part quality. Predicting potential defects like weld lines, air traps, and warpage early in the process allows for timely design adjustments. This proactive approach not only enhances the durability and quality of plastic injection molded parts but also ensures that the final product meets stringent quality standards.
For instance, a specific case study demonstrated how mold flow analysis significantly reduced imperfections in a complex component by optimizing the injection process.
Reducing Cycle Times
Optimizing the filling and cooling processes through mold flow analysis can lead to significant cycle time reduction. Fine-tuning the injection molding process enables manufacturers to achieve faster cooling times, shortening overall production cycles.
This efficiency not only boosts productivity but also reduces time to market, giving manufacturers a competitive edge.
Enhancing Cooling Channel Efficiency
Mold flow analysis plays a pivotal role in designing efficient cooling channels, ensuring uniform temperature distribution during the molding process. Optimizing cooling channel configurations reduces the risk of defects associated with uneven cooling, like warpage and sink marks.
This enhancement in cooling channel efficiency not only improves part quality but also contributes to cycle time reduction, making the entire molding process more efficient.
Addressing Manufacturing Challenges with Mold Flow Analysis
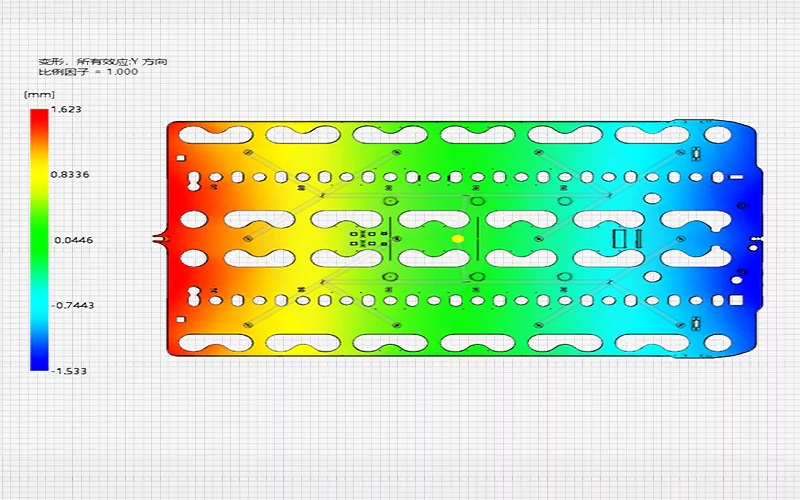
Mold flow analysis is instrumental in addressing various manufacturing challenges encountered during the injection molding process. Identifying potential defects and optimizing factors like runner placement and fill patterns enhances manufacturing efficiency and cost-effectiveness.
This section will explore how mold flow analysis helps in troubleshoot problems, optimizing multi-cavity molds, and achieving runner balancing for better flow.
Troubleshooting Problems
Mold flow analysis is a powerful tool for troubleshooting problems in the molding process. Predicting how resin will fill the mold helps avoid issues like premature freezing of the material. Conducting this analysis early allows for adjustments in design, such as optimal gate placements, which can significantly reduce defects like weld lines and air traps.
For instance, a case study demonstrated that implementing mold flow analysis led to critical design adjustments, successfully minimizing defects in intricate part geometries.
Optimizing Multi Cavity Molds
Optimizing multi-cavity molds is another area where mold flow analysis proves invaluable. Identifying flow imbalances ensures that all cavities fill evenly, preventing defects and promoting consistent part quality.
This evaluation process also includes determining the shrinkage rates of different resins during cooling, leading to improved efficiency and consistency in multi-cavity mold performance.
Runner Balancing for Better Flow
Achieving runner balance is crucial for uniform flow distribution, and mold flow analysis assists in optimizing this aspect. Effective runner balancing ensures consistent material distribution across all cavities, reducing defects and enhancing the overall quality of plastic injection molded parts.
This optimization is vital for maintaining the integrity and functionality of the final product.
Advanced Tools and Techniques in Mold Flow Analysis
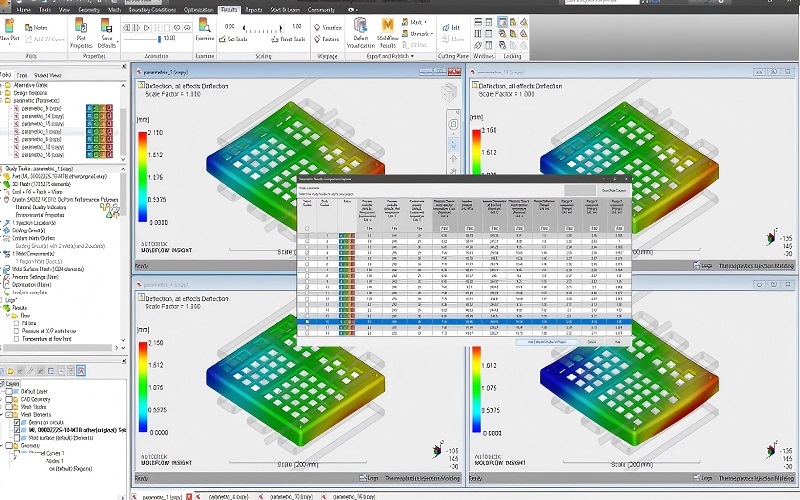
The advancements in mold flow analysis tools and techniques have further enhanced its capabilities. Moldex3D Flow, for instance, provides depth insights into plastic flow behaviors, encompassing effects like fountain flow, inertia, and gravity.
These advanced tools allow for the modeling and importing of cooling and feed systems, offering a comprehensive engineering analysis that’s crucial for optimizing injection molding processes.
Multiple Simulations Concurrently
Running multiple simulations concurrently is a significant advancement in mold flow analysis. Enabling parallel processing of design scenarios, Moldflow Insight provides quicker insights and design validations.
CADMOULD, for example, enhances the efficiency of simulations by utilizing powerful parallelization, optimizing processing times, and allowing for rapid design iterations with simulation software.
Flexible Solving Options
Moldflow offers flexible solving options that cater to different user needs. Users can perform simulations locally, remotely, or through cloud-based servers, providing scalability in processing power and storage. This flexibility ensures that engineers can choose the best solution for their specific requirements, whether they need the convenience of local solutions or the scalability of cloud-based options.
Integration with Other Software
The integration of mold flow analysis with other software tools enhances its capabilities and user experience. CADMOULD, for instance, can seamlessly integrate with simulation tools such as Ansys, providing a comprehensive analysis.
This integrated workflow allows for quicker iterations and improved communication between design and analysis teams, ultimately leading to more efficient production.
Case Studies and Examples
Real-world applications of mold flow analysis highlight its effectiveness in solving practical challenges. Case studies provide tangible examples of how this analysis has been used to improve part quality, reduce defects, and enhance manufacturing efficiency.
Let’s explore two specific examples that showcase the transformative power of mold flow analysis.
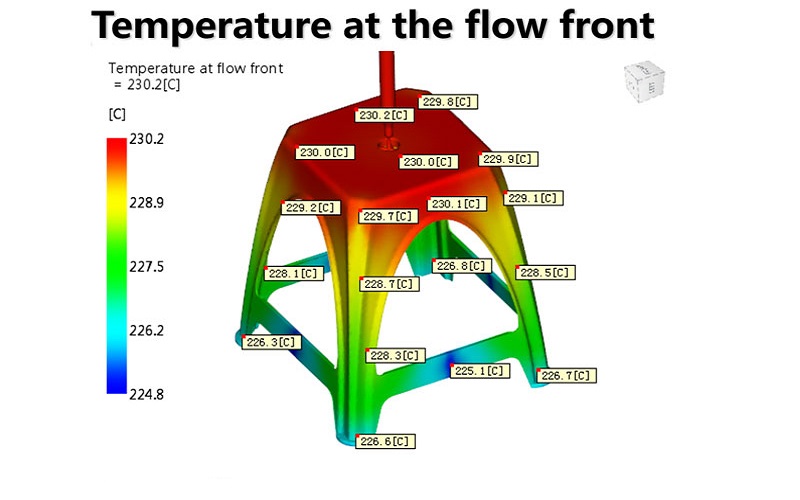
Example 1: Reducing Defects in a Complex Part
In a notable case study, mold flow analysis identified critical defects and errors in a complex part, leading to design adjustments that reduced defects by over 30%. The test analysis pinpointed specific areas where defects were occurring, necessitating changes to the design of the part.
These modifications resulted in significant improvements in part integrity, showcasing the effectiveness of mold flow analysis in reducing defects and enhancing part quality.
Example 2: Optimizing Cooling Channels in Family Molds
Optimizing cooling channels in family molds is crucial for achieving uniform temperature distribution and reducing cycle times. Through mold flow analysis, engineers can simulate various cooling channel configurations to identify the most effective design.
This optimization leads to improved temperature control, enhanced part quality, and reduced defects, ultimately improving production efficiency.
Summary
In conclusion, mold flow analysis is an indispensable tool in the realm of plastic injection molding. By providing deep insights into the molding process, it enables engineers to predict and rectify potential issues, optimize mold designs, and enhance part manufacturability.
The benefits are multifaceted, ranging from improving part quality and reducing cycle times to enhancing cooling channel efficiency. These advantages not only contribute to better product outcomes but also streamline production processes, ultimately leading to cost savings and increased efficiency.
Embracing mold flow analysis is not just a technical upgrade but a strategic move towards achieving excellence in manufacturing. By leveraging advanced tools and techniques, manufacturers can stay ahead of the curve, address complex manufacturing challenges, and deliver high-quality products consistently. As showcased in the case studies, the tangible benefits of mold flow analysis are clear, making it an essential component in the toolkit of any forward-thinking mold engineer.
Frequently Asked Questions
What is Moldflow used for?
Moldflow is used for simulating and analyzing the injection molding process, helping designers optimize material fill and troubleshoot issues like weld and knit lines. This ensures better part quality, reduced cycle times, and enhanced manufacturing efficiency.
What are the levels of certification in Moldflow?
The levels of certification in Moldflow are Associate, Professional, and Expert, each requiring completion of specific training courses. This structured progression ensures users develop a thorough understanding of Moldflow capabilities.
What is a mold flow analysis?
Mold flow analysis is a software simulation that predicts how resin fills a mold during the injection molding process, allowing designers to optimize gate placement and identify potential weak points like knit lines. This analysis is crucial for improving the quality and strength of molded parts.
When should mold flow analysis be used?
Mold flow analysis should be utilized early in the design process and during design modifications to identify potential issues and optimize overall designs effectively. This proactive approach can significantly enhance product performance and manufacturability.
How does mold flow analysis improve part quality?
Mold flow analysis significantly improves part quality by identifying potential defects like weld lines and air traps early in the design process, enabling timely adjustments that enhance the durability and overall quality of the final product.