Mold making with CNC machines delivers precision and efficiency. This guide explains which CNC machines are best for mold making CNC, the materials used, and effective techniques for high-quality production.
Understanding CNC Machining in Mold Making
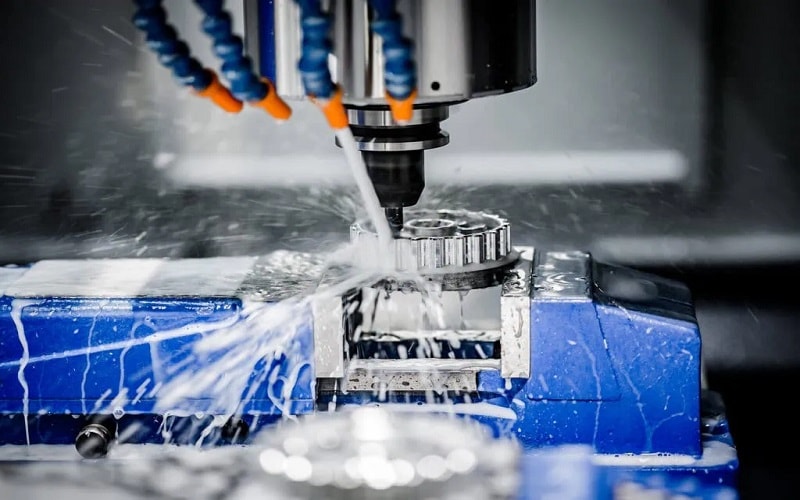
CNC machining has revolutionized the mold industry, providing a level of precision and consistency that was previously unattainable.
The ability to machine complex 3D forms with minimal human error has enabled industries like automotive, aerospace, and consumer products to create intricate designs with ease.
This technology allows for the production of various molds, including stamping dies, forming dies, and injection molds, as well as machine body components for CNC equipment,each tailored to specific manufacturing needs, including injection mold making, injection molding, and mold machining.
One of the significant advantages of CNC machining is its ability to reduce human error, leading to more consistent and reliable results. The use of smaller cutting tools ensures superior surface finishes, which is crucial for high-quality mold production.
Moreover, CNC machines are designed for both 2D and 3D machining, making them versatile tools for creating a wide range of mold designs using different materials.
Beyond precision, CNC machining reduces labor costs and material waste over the long term. The lead times for tooling are generally shorter compared to traditional methods, enhancing overall productivity. As we move forward, we’ll explore the key materials used in CNC mold making and how they impact the manufacturing process.
Key Materials for CNC Mold Making
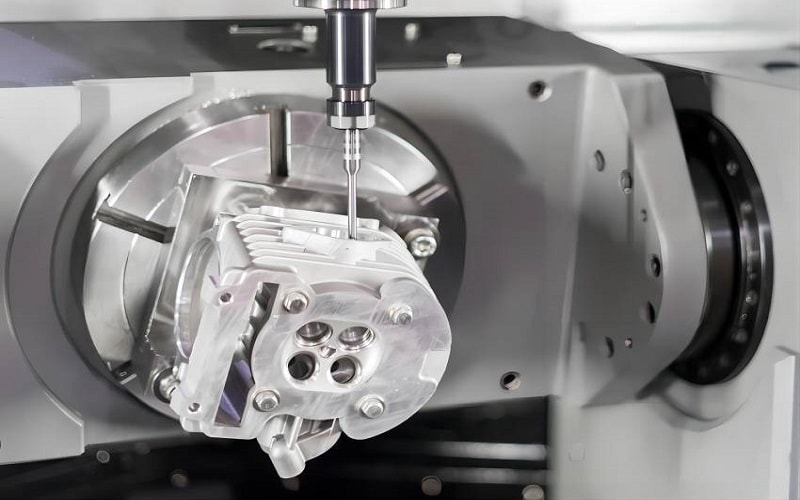
Selecting materials in CNC mold making directly affects the machining process and mold longevity. CNC machining supports a diverse range of mold materials, including both plastics and metals, allowing for flexibility in manufacturing. Each material has its unique properties, making it suitable for different applications.
Aluminum is a popular choice due to its excellent machinability and thermal conductivity. It’s particularly favored for low-volume mold production where quick turnaround times are essential.
On the other hand, steel is known for its strength and wear resistance, making it the material of choice for high-volume production molds. These properties ensure that the molds can withstand repeated use without significant wear and tear.
Composites and plastics are also used in specialized applications due to their unique properties such as corrosion resistance and thermal stability.
Industries are increasingly moving away from traditional wood molds to alternatives like urethane board for applications such as prototyping and thermoforming, driven by the rising costs of wood.
Choosing the right material impacts both the machining process and production cost-effectiveness. Cost-effective materials that meet both functional and budgetary requirements can substantially lower CNC machining costs.
With the right materials in place, the next step is to choose the appropriate CNC machine for the job.
Types of CNC Machines Used in Mold Making
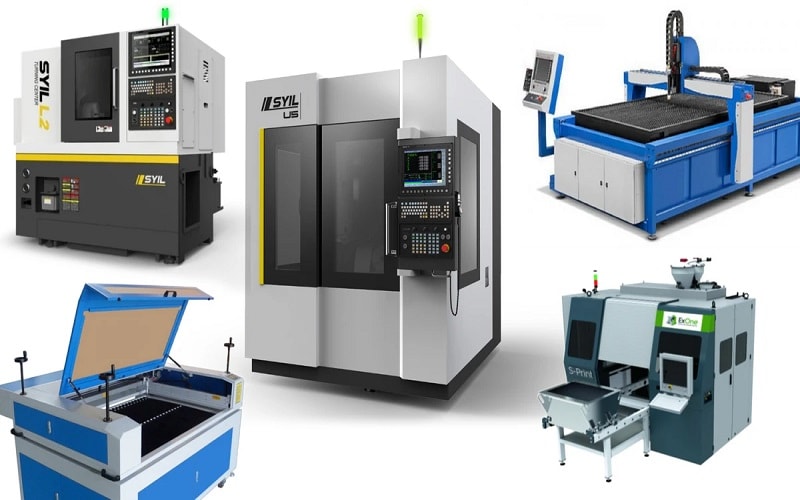
Various CNC machines serve specific roles and offer distinct benefits in mold making. CNC milling machines are among the most commonly used, where the workpiece remains fixed while rotating cutting tools remove material.
This process is essential for creating detailed and complex mold components, with operations such as face milling and peripheral milling being widely used.
CNC lathes operate by rotating the workpiece and using linear motion for cutting tools to shape materials. This process is especially beneficial for making cylindrical components. Examples include threads, tapers, and slots.
CNC turning processes utilize single-point cutting tools to achieve high precision in these shapes, making them indispensable for certain types of molds.
CNC router machine plays a vital role in mold making. These machines are known for their ability to handle a variety of materials, including wood, plastics, and metals. They are particularly effective for creating large and complex molds with high precision.
Selecting the right type of CNC machine according to the project’s needs avoids overspending on unnecessary precision capabilities. With the machines chosen, the focus now shifts to the high precision processes that make CNC machining so effective.
High Precision CNC Machining Processes
High-speed machining (HSM) enhances efficiency by enabling faster metal removal rates with lighter passes. This technique reduces turnaround times due to increased spindle speeds and feed rates, leading to faster cooling and hardening of materials. The result is greater dimensional accuracy and smoother surface finishes, especially when working with hard metals.
Five-axis machining offers significant advantages in accessing difficult geometries within a mold cavity. This capability allows for the machining of complex parts, facilitating tasks like milling holes and pockets that are normal to complex surfaces, thereby improving overall efficiency and surface finish.
Trochoidal milling is another high-precision technique that maintains consistent chip thickness, making it effective for creating deep slots. This method reduces tool wear and improves the overall efficiency of the machining process.
Plunge roughing enables rapid removal of large material volumes by directing the tool straight into the workpiece at high feed rates. Adjusting the feed rate and spindle speed based on the material density being machined ensures effective cutting.
These high-precision techniques are crucial for achieving the desired quality and efficiency in mold production. With these processes in place, the next step involves preparing the CAD designs for machining.
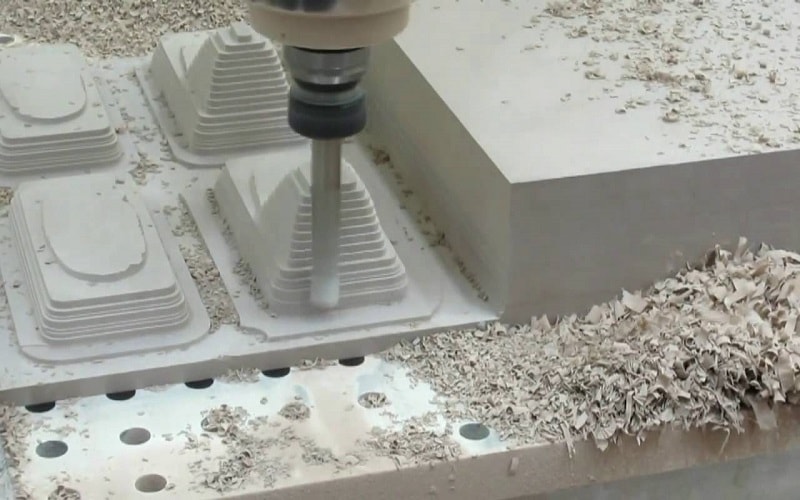
CAD Design and File Preparation for CNC Mold Making
CAD models are the backbone of CNC machining, serving as virtual representations of the final product. These models contain essential code that guides the CNC machine in executing the design.
Before machining, CAD files are converted into machine-readable formats, often generating G-code to direct the machine’s movements.
Simulating the tool path before machining identifies potential issues with speed and cutting parameters, ensuring smoother production. Advanced CAD/CAM software enhances this process by automating essential aspects, such as the layout of mold cooling systems.
With the CAD designs ready, it’s time to set up the CNC machine for production.
Setting Up a CNC Machine for Mold Making
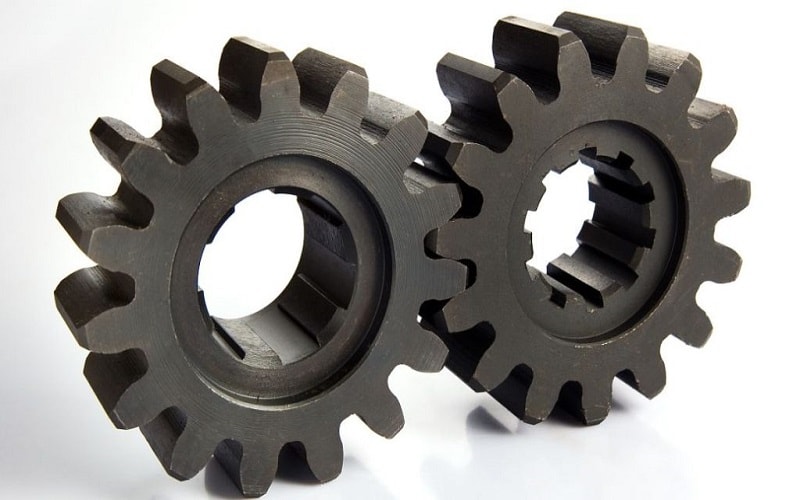
Meticulous preparation is required for setting up a CNC machine for mold making. All drill bits and worksheets must be ready before declaring the machine for operation.
This preparation includes selecting the right cutting tool and ensuring it is properly secured in the collet for accurate machining. The coordinate system in the CAM should have the origin at the top center of the stock for optimal alignment.
A sacrificial layer beneath the stock material protects the CNC machine’s bed during milling. Maintaining machine performance and safety requires cleaning the workspace and removing debris after machining. Setting up tablets and touchscreen interfaces on the shop floor simplifies data entry and helps track machine performance.
The setup process includes adding accessories, feeding worksheets, running the program, and performing inspections. Once the machine is set up, the next step is to operate it to produce parts the molds.
Operating CNC Machines for Mold Production
A qualified technician is required to operate a CNC machine for mold production. The process includes preparing the machine, running the program with all tools in place, and awaiting the final product. This requires careful monitoring to ensure that the machining process proceeds smoothly and that any issues are promptly addressed.
Real-time monitoring maintains quality and allows adjustments to parameters. This ensures that the final product meets the required specifications and quality standards.
With the molds produced, advanced technologies transforming the CNC mold making industry can be explored.
Advanced Technologies in CNC Mold Making
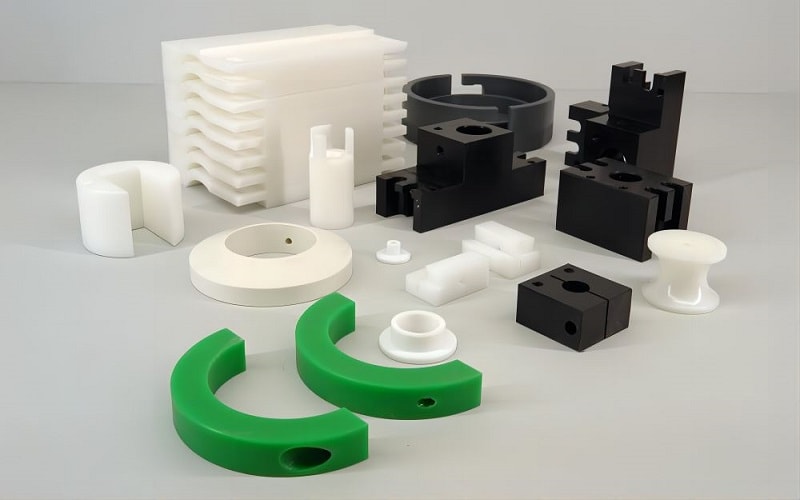
Advanced technologies are continuously transforming CNC mold making, enhancing precision and efficiency. CNC laser cutting machines utilize a highly focused laser beam to perform precise cuts on various materials.
Electrical discharge machining (EDM) employs electrical sparks to gradually erode material into the desired shape. These technologies enable the production of complex shapes with high precision.
Real-time monitoring systems minimize downtime and reduce maintenance costs. AI-driven robotics are now used to automate the polishing of molds, increasing precision and consistency in the process. Innovations in hot runner systems optimize temperature control and reduce scrap rates in mold production.
These advancements boost productivity and performance, significantly evolving CNC technology for mold making. With these technologies in place, CNC machining continues to find applications across various industries.
Applications of CNC Machining in Various Industries
CNC machining’s flexibility allows rapid adaptation to design changes. In the automotive sector, it produces high-precision components and prototypes.
From prototyping parts during R&D to manufacturing components like engine blocks and dashboard panels, CNC processes are integral to the automotive industry.
In aerospace, CNC machining produces components like airfoils and landing gear, requiring high precision due to safety standards. The healthcare industry uses CNC technology to produce surgical instruments and implants requiring exceptional precision.
In the marine industry, CNC machining manufactures parts like hulls and deck structures for boats and watercraft. The electronics sector uses CNC machining for consistent production of intricate components, such as casings for smartphones and laptops.
These industries rely on CNC machining’s precision and efficiency, ensuring high-quality products through effective manufacturing processes. Maintaining this quality requires employing several strategies.
Ensuring Quality and Accuracy in CNC Mold Making
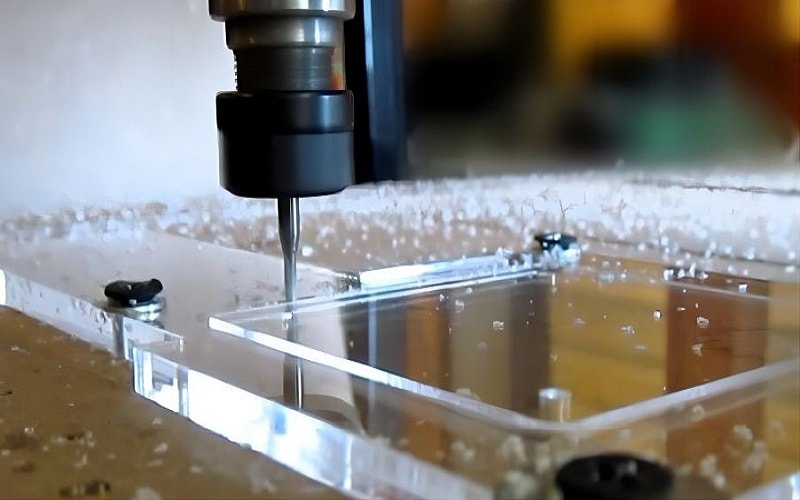
Regular maintenance schedules ensure quality and accuracy in CNC mold making, reducing downtimes and maintaining precision. Keeping cutting tools sharp prevents poor-quality molds and reduces machine stress. Inspecting raw materials before machining ensures they meet necessary quality specifications.
In-process inspections catch potential defects early in the production process. Statistical methods can help oversee machining processes to identify trends and maintain consistent quality. Effective monitoring enhances production efficiency by minimizing downtime and scrap rates.
Controlling environmental factors like temperature and humidity prevents material expansion that could lead to inaccuracies. Training personnel in the latest machining techniques maintains quality control throughout the production process. These strategies enable CNC mold making to achieve high precision and quality.
Cost-Effective Strategies for CNC Mold Making
CNC machining is ideal for low-volume production due to its efficiency in processing single parts. Advanced software optimizes machining paths, lowering machining time and reducing tool wear. Designing parts with machinability in mind reduces machining times and costs.
Engaging suppliers early in the process can yield insights and optimizations that lead to significant cost reductions. Regularly reviewing and optimizing supplier relationships uncovers cost-saving opportunities in material sourcing. Lean manufacturing practices promote ongoing cost reductions by focusing on efficiency and waste elimination.
Analyzing the entire production workflow identifies inefficiencies and opportunities for cost savings. Sustainable manufacturing practices lead to cost savings through energy efficiency and reduced waste. These strategies keep CNC mold making cost-effective while maintaining high quality and efficiency.
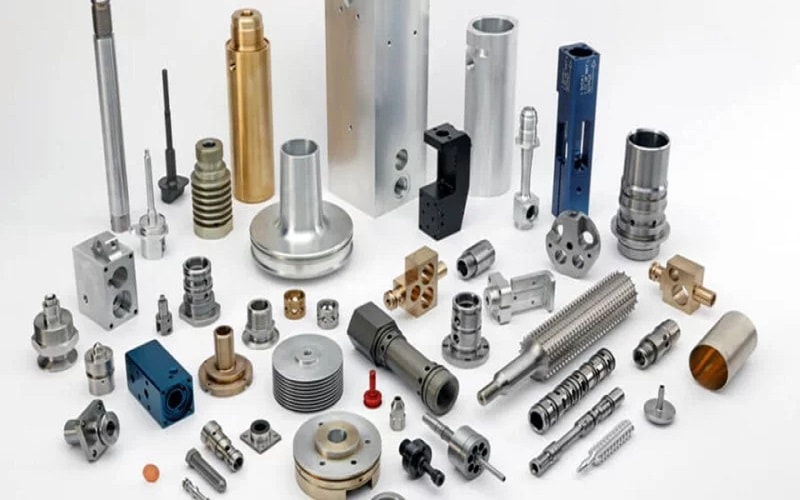
Summary
In conclusion, CNC machining has transformed mold making, offering unparalleled precision and efficiency. From selecting the right materials and machines to employing advanced technologies and ensuring quality, every step in the process contributes to producing high-quality molds.
By adopting cost-effective strategies and staying updated with the latest advancements, manufacturers can maintain a competitive edge in the industry.
The journey of CNC mold making is one of continuous improvement and innovation, ensuring that the molds produced meet the highest standards of quality and accuracy.
Frequently Asked Questions
What are the primary benefits of using CNC machining in mold making?
The primary benefits of using CNC machining in mold making include high precision, reduced human error, and the capability to create complex 3D forms.
This technology also lowers labor costs and material waste, ultimately enhancing productivity with shorter lead times for tooling.
Which materials are commonly used in CNC mold making?
CNC mold making commonly utilizes aluminum for its excellent machinability and thermal conductivity, steel for its strength and wear resistance, and various composites and plastics for their corrosion resistance and thermal stability.
Each material serves distinct purposes based on the specific requirements of the mold application. Traditionally, wood molds were used, but there has been a shift to alternatives like urethane board due to the increasing costs of wood and the need for more cost-effective and efficient materials.
What types of CNC machines are used in mold making?
CNC milling machines, lathes, and router machines are essential in mold making, each serving specific purposes like detailed design creation and shaping cylindrical components for complex molds.
Their versatility in handling various materials and creating precise mold components makes them invaluable in this process.
How do advanced technologies impact CNC mold making?
Advanced technologies significantly improve CNC mold making by increasing precision, efficiency, and reducing maintenance costs through methods such as CNC laser cutting, EDM, and AI-driven robotics.
These innovations ultimately lead to better temperature control and reduced scrap rates in the production process.
Additionally, five-axis machining offers significant advantages by allowing access to difficult geometries within a mold cavity, facilitating tasks like milling holes and pockets that are normal to complex surfaces and improving overall efficiency and surface finish.
What strategies ensure quality and accuracy in CNC mold making?
To ensure quality and accuracy in CNC mold making, it is essential to implement regular maintenance, keep cutting tools sharp, conduct in-process inspections, and utilize statistical methods. Additionally, training personnel in the latest techniques plays a vital role in sustaining high-quality production.