Mold temperature is a critical factor in the injection molding process that directly affects product quality, efficiency, and production outcomes.
This article explains how to manage mold temperature, its impact on the final product, and provides best practices for optimizing this key parameter.
Understanding Mold Temperature
Mold temperature refers to the surface temperature of the mold cavity and core, which plays a key role in the molding process. It affects the flow of material, the cooling rate, and the quality and stability of the final product.
The right mold temperature can help the product mold better and reduce defects such as warpage, weld marks or dimensional deviations.
Typically, mold temperatures are controlled through heating and cooling systems to maintain a stable processing environment and ensure that the product achieves the desired properties and appearance.
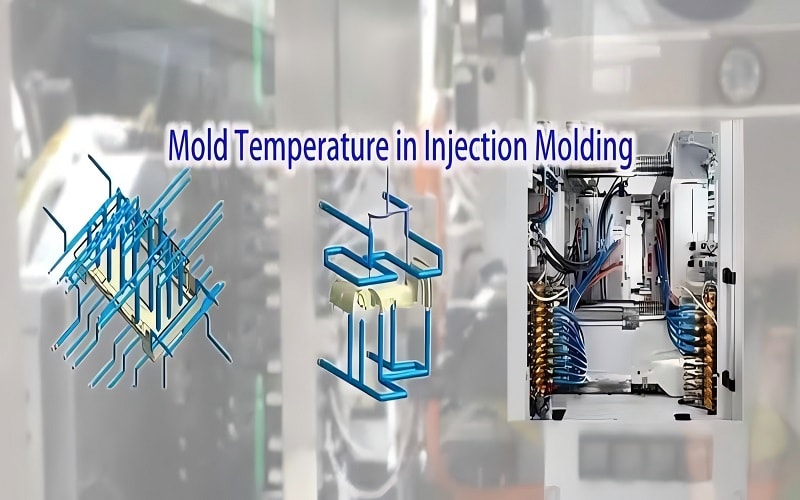
Impact of Mold Temperature on Product Quality
Mold temperature affects the flow of material, the cooling rate, and the quality and stability of the final product. The right mold temperature can help the product mold better and reduce defects such as warpage, weld marks or dimensional deviations.
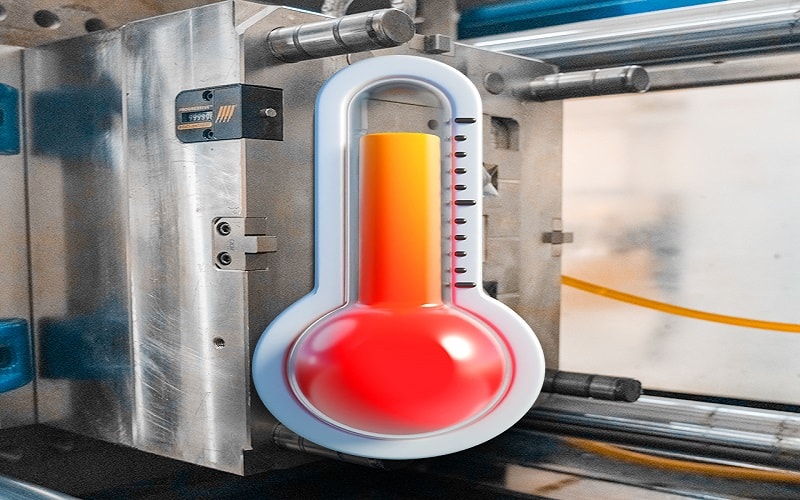
Surface Finish and Appearance
The surface finish and appearance of molded products are directly influenced by mold temperature. Low mold temperatures reduce melt flowability, leading to incomplete filling and a rough surface finish. This can result in products with visible defects and poor aesthetic qualities, which are often unacceptable in industries such as consumer electronics and automotive.
On the other hand, higher mold temperatures generally improve the surface gloss and overall appearance of molded products. In the injection molding of nylon 66, optimized mold temperatures enhance surface quality and structural integrity, making it a preferred choice for automotive parts where both appearance and durability are critical.
Dimensional Accuracy
The temperature of the mold affects the dimensional accuracy of the product. Higher temperatures result in larger shrinkage and smaller dimensions, while lower temperatures result in smaller shrinkage and larger dimensions.
The larger the wall thickness, the more obvious the shrinkage, which may lead to warping or deformation. Keep the temperature uniform to ensure stable product quality.
Mechanical Properties
Mold temperature is important to the quality of plastic parts. Higher temperatures allow the plastic to flow smoothly, reducing internal stress and cracking, and also increase strength, so that nylon parts, for example, will be stronger.
However, if the temperature is too high, the product may warp and distort. Points like the “glass transition temperature” are also critical, determining whether the plastic is hard or soft.
Therefore, the mold temperature should be adjusted appropriately, according to the material to find the balance, in order to make good quality products.
Optimal Mold Temperature Settings
Optimal mold temperature settings are critical for ensuring consistent quality and performance in injection molding.
Maintaining the correct mold temperature helps achieve better surface finishes, dimensional accuracy, and mechanical properties. The recommended mold temperature for specific materials, such as PA66, ranges between 120°F and 220°F.
The optimal mold temperature is influenced by factors such as mold shape, thermal conductivity, fluid flow, temperature control medium, and equipment specifications. Using higher mold temperatures for lower post-molding shrinkage and better surface brightness is recommended for producing precision components.
Measuring the actual temperature within the mold is essential to ensure that the thermal balance is maintained, which directly impacts the quality of the final product.
These factors assist in setting the optimal temperature to achieve the best results.
Material | Optimal Mold Temperature Range (°F) |
Acrylonitrile Butadiene Styrene (ABS) | 104 – 176 |
Polycarbonate (PC) | 176 – 248 |
Polystyrene (PS) | 86 – 140 |
Polyamide (Nylon, PA) | 140 – 212 |
Polyethylene Terephthalate (PET) | 50 – 104 |
Polyethylene (PE) | 68 – 140 |
86 – 158 | 86 – 158 |
158 – 230 | 158 – 230 |
Polyetheretherketone (PEEK) | 320 – 392 |
Determining the Right Temperature
Determining the right mold temperature involves considering several factors. Water-based mold temperature controllers are suitable for lower to moderate temperature requirements and improve energy efficiency in the injection molding process.
For high-temperature applications, oil mold temperature controllers that utilize synthetic oil for effective heat transfer are preferred.
The suggested mold temperature for PA66 injection molding is around 176°F. Mold shape, thermal conductivity, and the temperature control medium significantly influence the correct temperature.
Using higher mold temperatures can reduce post-molding shrinkage and improve surface brightness, essential for precision components. Ensuring the temperature exceeds the melting point of nylon allows for better flowability and molding characteristics, reducing the risk of discoloration and poor product formation.
Adjusting for Different Materials
Different materials require different mold temperatures to achieve optimal results. For example, the optimal mold temperature for nylon 66 is 260°C. Unreinforced nylon materials typically require a mold temperature of 30-40°C, while reinforced nylon materials are best molded at 90-100°C.
Understanding the glass transition temperature (Tg) is crucial in this context, as it marks the transition of a material from a brittle glassy state to a more flexible rubbery state as temperature increases.
Thin-walled or large-area nylon components should ideally be molded at temperatures between 80 and 90 degrees Celsius. This range ensures optimal molding conditions. Mold temperature greatly affects the crystallinity and overall quality of injection molded nylon products.
Higher mold temperatures increase crystallinity, which enhances mechanical properties but can also lead to warping if not controlled properly.
The significance of glass transition temperatures lies in characterizing material behavior and comparing it to the melting temperature of crystalline substances.
Techniques for Controlling Mold Temperature
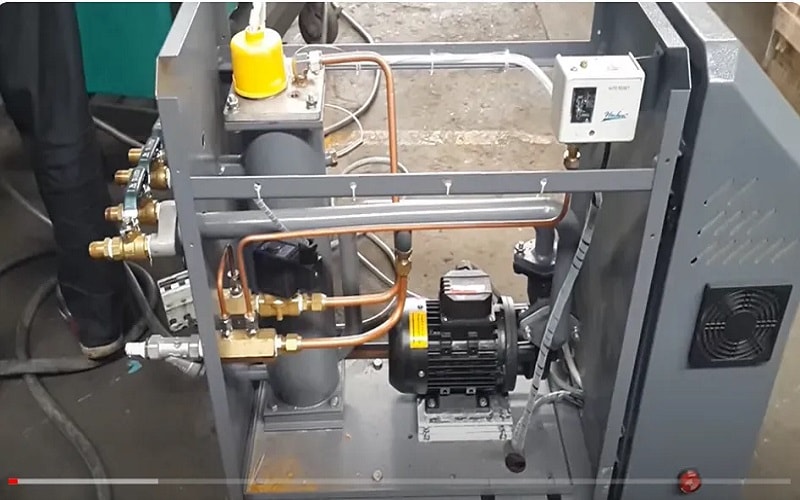
Controlling mold temperature is crucial for achieving high-quality injection molded products. Consistent mold temperature allows for better control over material properties and reduces defects in the final product. Effective management of mold temperature can significantly enhance the quality, durability, and precision of the molded items.
Various techniques can be employed to control mold temperature, including advanced cooling systems and regular monitoring and maintenance. These methods maintain the desired temperature range, ensuring optimal conditions for the injection molding process.
Measuring the actual temperature is essential to verify that the mold and material are within the specified thermal parameters, which helps in maintaining the thermal balance and quality of the final product.
Cooling Systems and Design
Cooling systems must be designed to accommodate complex mold geometries to ensure uniform temperature distribution across the mold surfaces. Conformal cooling allows for better temperature control in complex geometries compared to traditional cooling methods. Cooling channels should be positioned near the thickest areas of the mold to ensure effective cooling.
Wall thickness affects the cooling process significantly, as thicker walls typically require more time to cool and can lead to warping or deformation if not properly managed. Therefore, positioning cooling channels near the thickest areas of the mold is crucial to manage the cooling rate effectively.
Using multiple smaller cooling channels is generally more effective than relying on a single large channel. Additionally, combining cooling channels with strategically placed inserts can enhance heat dissipation in thin-walled parts. Such design considerations are crucial for maintaining thermal equilibrium and preventing defects.
Monitoring and Maintenance
Temperature sensors integrated into molds allow real-time monitoring, providing data to maintain optimal thermal conditions during injection. Measuring the actual temperature is crucial to ensure the thermal balance within the mold, directly impacting the quality of the final product.
Displaying supply and return temperatures on control equipment simplifies monitoring temperature changes. This feature provides valuable insights into the system’s performance. Calibrating temperature sensors regularly ensures accurate readings and effective mold temperature control.
Monitoring cooling system performance regularly helps identify inefficiencies early, reducing production delays. Tools like thermocouples or handheld high-temperature meters measure mold surface temperature, ensuring the mold operates within the desired temperature range.
Common Challenges and Solutions
Managing mold temperature comes with its own set of challenges. Rapid cooling rates can significantly impact the density of glass products produced through injection molding. Variations in cooling rates, including slow cooling, can lead to inconsistent product density, affecting overall performance and quality.
The time allowed for structural relaxation during the cooling phase is crucial for minimizing internal stresses. Higher mold temperatures can enhance crystallinity, thereby affecting tensile strength and shrinkage properties.
Implementing controlled cooling techniques can help maintain consistent structural characteristics and minimize defects in the final product. Addressing these challenges with appropriate solutions ensures successful mold temperature management. Mold temperature and moisture absorption affect the physical properties of materials like polyamides, influencing strength, stiffness, and dimensional stability.
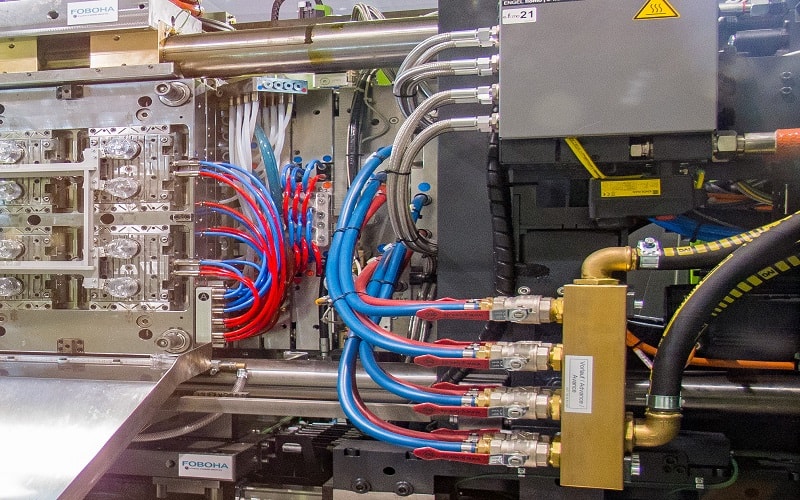
Deformation and Warping
Insufficient cooling and poor mold temperature control can cause warping and deformation in plastic parts. Low mold temperature can exacerbate deformation in nylon parts due to inadequate crystallization. Temperature fluctuations and leaks in mold temperature controllers can significantly impact the efficiency of the injection molding process.
Implementing predictive maintenance strategies can help identify potential mold issues before they lead to production downtime. Controlling mold temperature according to the product’s structural characteristics helps prevent deformation. Additionally, maintaining a higher mold temperature can help prevent warping and internal stress in various molded parts.
Managing Moisture Content
Drying materials like nylon is crucial for controlling moisture absorption and avoiding defects associated with moisture. Utilizing vacuum drying for nylon 66 significantly helps in lowering moisture content, enhancing its performance and processing characteristics. Drying nylon 66 at 90-100°C for about 4 hours is critical to minimize moisture-related defects.
Absorption of moisture by nylon 66 can lead to significant variations in its dimensional stability and overall performance. Lower mold temperatures can lead to reduced crystallinity in nylon, affecting product toughness and elongation. Moisture absorption affects the physical properties of materials like polyamides, influencing their strength, stiffness, and dimensional stability.
Advanced Techniques for Enhanced Control
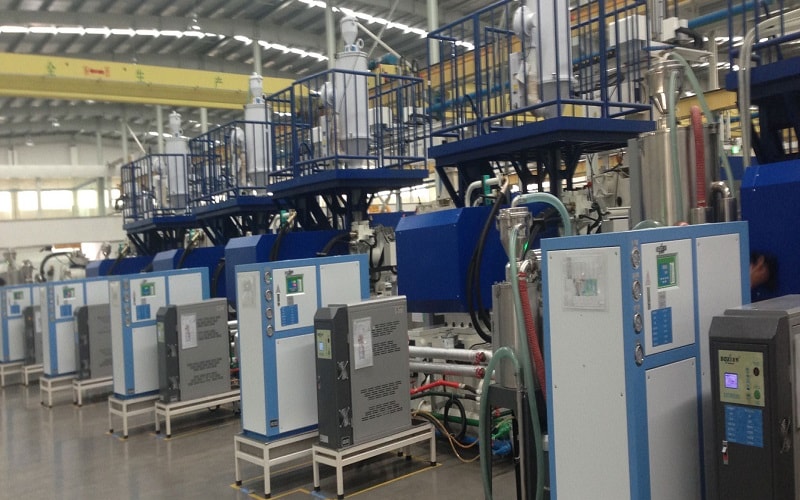
Advanced techniques in injection molding are essential for achieving precise control of mold temperature, significantly impacting product quality and efficiency. Vacuum drying reduces moisture content in materials, leading to higher crystallinity in certain plastics, which can enhance moldability and final product performance. Measuring the actual temperature is crucial to ensure optimal conditions for these advanced techniques.
Effective management of thermal expansion involves careful monitoring and adjusting mold temperatures to ensure dimensional stability and minimize internal stress in molded parts. Implementing vacuum drying and thermal expansion management as part of advanced techniques contributes to the overall success in controlling mold temperature and achieving high-quality injection molded products.
Vacuum Drying
Vacuum drying can significantly decrease the drying time for nylon 66, reducing it from hours to mere minutes, enhancing production efficiency. Vacuum drying at temperatures between 95-105°C for nylon 66 can effectively reduce moisture levels within 6-8 hours, enhancing the material’s crystallinity.
This method can lead to higher crystallinity in nylon 66, improving its mechanical properties. Vacuum drying is thus a valuable technique for enhancing the performance and quality of injection molded products.
Thermal Expansion Management
To manage thermal expansion in plastics, consider the following strategies:
- Preheating materials before processing can be an effective strategy. Understanding the glass transition temperature (Tg) is crucial in managing the thermal behavior of materials, as Tg marks the transition from a brittle glassy state to a more flexible rubbery state.
- Employing materials with lower coefficients of thermal expansion can enhance dimensional stability in molded parts.
- Incorporating fillers or modifying the processing conditions can help control the thermal expansion characteristics of nylon 66.
Managing thermal expansion ensures dimensional stability and minimizes internal stress in injection molded parts. Such strategies help maintain the final product’s integrity and performance.
Case Studies and Real-World Applications
Understanding the importance of mold temperature management benefits from examining real-world applications. Proper management of mold temperature is crucial for achieving high-quality automotive parts. In the automotive industry, optimal mold temperature settings improve the quality and performance of components, resulting in enhanced durability and reduced defects.
Similarly, in consumer electronics, maintaining precise control of mold temperature is essential for producing durable and aesthetically pleasing electronic housings. These case studies highlight the practical applications and benefits of effective mold temperature management.
Measuring the actual temperature in these applications ensures the thermal balance within molds, directly impacting the quality of the final product, particularly in processes like injection molding.
Automotive Parts
Optimal mold temperature settings are critical in the automotive industry to ensure that components meet rigorous performance and durability standards. Precise mold temperature settings lead to enhanced durability and improved fit of automotive components made from materials like PA66.
Using precise mold temperature controls allows manufacturers to produce PA66 components that withstand the demanding conditions of automotive applications. This results in parts that are not only high-performing but also reliable over the long term.
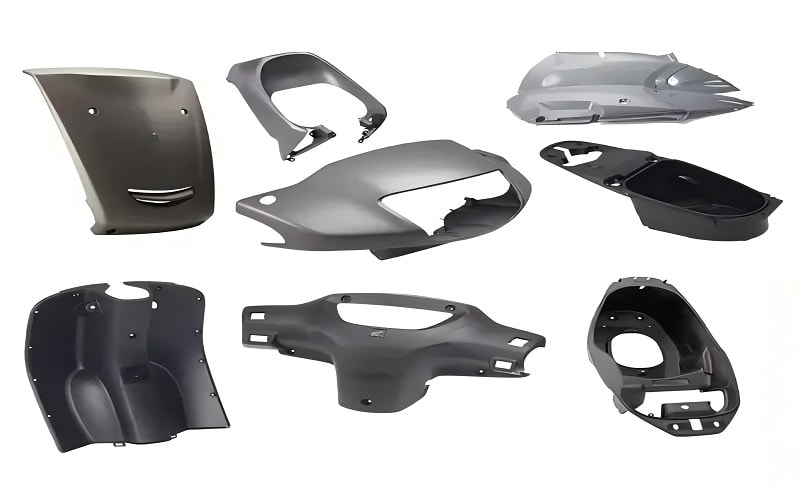
Consumer Electronics
Precise mold temperature control is essential in the production of electronic housings, as it contributes to the aesthetic quality and durability of the final product. Utilizing controlled mold temperatures during the production of electronic housings enhances both the aesthetics and functionality of the final products. This is crucial for consumer electronics, where both visual appeal and performance are key selling points.
Effectively managing mold temperature can lead to products that meet high standards of quality, ensuring consumer satisfaction and brand reputation.
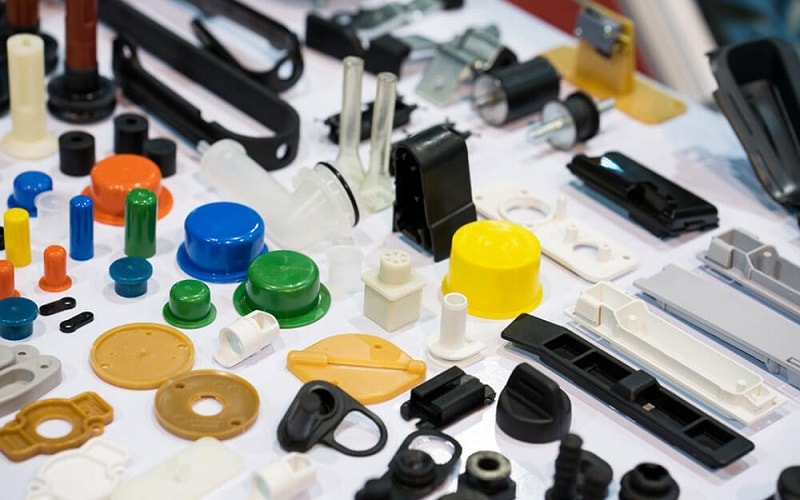
Summary
In summary, managing mold temperature in injection molding is a nuanced but crucial aspect of the manufacturing process. It affects surface finish, dimensional accuracy, and mechanical properties, all of which are vital for the quality and performance of the final product.
Measuring the actual temperature is significant to ensure optimal conditions and high-quality results, as it directly impacts the thermal balance within molds.
Optimal mold temperature settings, tailored to specific materials and applications, are essential for achieving consistent and high-quality results.
Advanced techniques such as vacuum drying and thermal expansion management further enhance mold temperature control, leading to improved efficiency and product quality.
By understanding and implementing these best practices, manufacturers can optimize their injection molding processes, resulting in superior products that meet the stringent demands of industries like automotive and consumer electronics.
Frequently Asked Questions
What temperature can nylon 66 withstand?
Nylon 66 can withstand temperatures typically ranging from 255 to 265 degrees Celsius (491 to 509 degrees Fahrenheit) before melting, maintaining its structural integrity at elevated temperatures.
Why is mold temperature important in injection molding?
Mold temperature is essential in injection molding as it directly influences surface finish, dimensional accuracy, and the mechanical properties of the final product. Maintaining optimal temperatures ensures high-quality and consistent results.
How does mold temperature affect the surface finish of injection molded parts?
Mold temperature significantly influences the surface finish of injection molded parts; higher temperatures enhance surface gloss and appearance, while lower temperatures can result in rough finishes due to decreased melt flowability. Thus, maintaining optimal mold temperatures is crucial for achieving desired surface quality.
What are the recommended mold temperatures for nylon 66?
The recommended mold temperatures for nylon 66 are approximately 260°C for reinforced materials and 30-40°C for unreinforced materials. This ensures optimal processing conditions for the material’s properties.
How can I manage thermal expansion in injection molding?
To manage thermal expansion in injection molding, consider preheating materials, using materials with lower coefficients of thermal expansion, and incorporating fillers or optimizing processing conditions. These strategies will enhance dimensional stability during the molding process.