PA 12 Nylon is a key material in 3D printing known for its strength and low moisture absorption. This article details its properties, industrial applications, and 3D printing techniques to help you make the most of PA 12 in your projects.
Understanding PA 12 Nylon Material
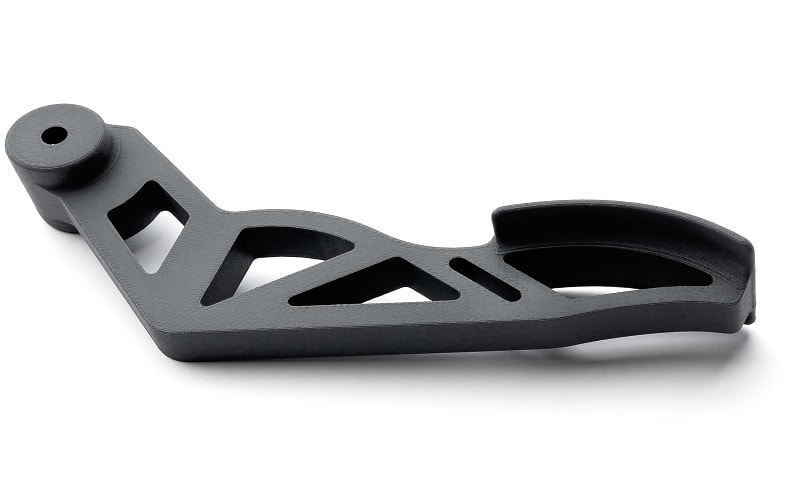
PA 12 Nylon, also known as Nylon 12, is a versatile material that has gained immense popularity in the world of 3D printing. Its unique properties suit a wide range of applications, from aerospace components to consumer electronics. PA 12 Nylon boasts excellent chemical resistance and low moisture absorption, maintaining dimensional stability even in challenging environments.
Renowned for its versatility and robust properties, this material stands out. PA 12 Nylon’s low moisture absorption makes it ideal for applications requiring dimensional accuracy. For both complex assemblies and simple prototypes, PA 12 Nylon provides the reliability and performance needed to bring designs to life.
Mechanical Properties and Specifications
One of the standout features of PA 12 Nylon is its impressive mechanical properties. This material boasts high strength and toughness, making it suitable for demanding applications that require durability and resilience. With a tensile strength of 53 MPa, PA 12 can withstand significant stress without compromising its structural integrity.
PA 12 also exhibits a notched impact strength of 7 kJ/m², demonstrating its ability to endure sudden impacts and stresses without breaking.
Its resilience is further indicated by an elongation at break of 200%, showcasing excellent flexibility and the ability to stretch without fracturing. Thanks to its chemical resistance, the material is also chemical resistant to exposure to oils, greases, and various hydrocarbons, making it ideal for automotive and aerospace applications.
In the automotive sector, PA 12 is commonly used for components like fuel lines and brake tubing due to its strength and chemical resistance. In the aerospace industry, PA 12’s heat resistance and abrasion durability make it suitable for critical components, contributing to the overall safety and efficiency of aircraft.
PA 12 Nylon provides the necessary mechanical properties for designing parts for high-stress environments or everyday items.
3D Printing Techniques with PA 12
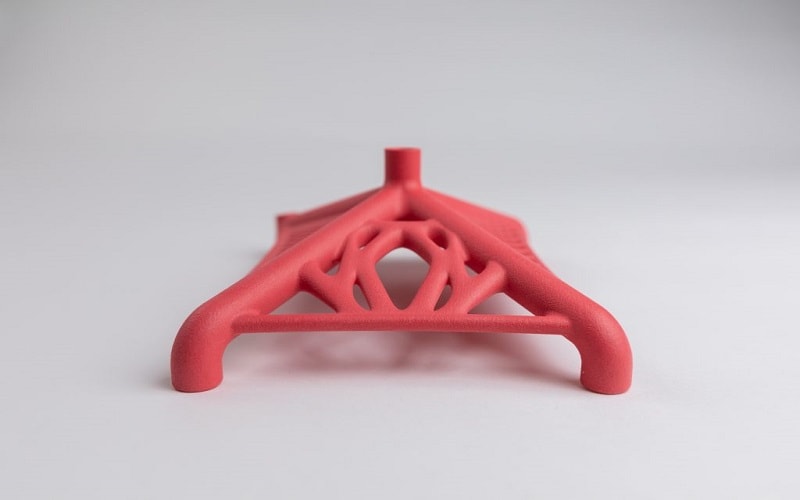
For 3D printing with PA 12 Nylon, two primary techniques stand out: Selective Laser Sintering (SLS) and Multi Jet Fusion (MJF). Each method offers unique advantages, enabling you to choose the best approach for your specific needs. Known for its strength and durability, PA 12 Nylon is highly regarded in 3D printing, especially for functional prototypes and end-use parts.
PA 12 prints offer layer definitions in standard layers of 100-120 µm and high-definition layers of 60 µm, providing flexibility in achieving the desired level of detail and precision. High Speed Sintering (HSS) technology enables the efficient reuse of recycled PA 12 powder, maintaining material properties comparable to new powder.
Detailed specifics of SLS and MJF techniques are outlined below.
Selective Laser Sintering (SLS)
Selective Laser Sintering (SLS) is a widely-used additive manufacturing process for creating PA 12 Nylon parts. The technology involves laying down layers of PA 12 powder, sintered together using a laser.
After each layer is sintered, the printing bed is lowered, enabling the creation of complex and intricate geometries with high precision. Typical layer heights range between 100 – 120 micrometers, but can be as fine as 60 micrometers for detailed parts.
SLS is ideal for producing parts with high mechanical strength and fine feature resolution. Thus, it is well-suited for applications requiring durable and precise components. The ability to create strong, detailed, and intricate parts makes PA 12 Nylon perfect for complex assemblies, enhancing the overall quality of the final product.
Multi Jet Fusion (MJF)
Multi Jet Fusion (MJF) is another advanced 3D printing technology for PA 12 Nylon. MJF produces parts with greater density and reduced porosity compared to SLS, resulting in stronger and more durable components. The versatility of PA 12 in MJF enables the creation of both functional prototypes and end-use components without a support structure, enhancing efficiency.
MJF technology can produce parts with maximum dimensions of 370 x 274 x 375 mm and a layer thickness as fine as 0.08 mm, allowing for detailed and intricate designs.
With a tensile strength of 48 MPa and a heat deflection temperature of 175 °C at 0.45 MPa, PA 12 in MJF offers excellent mechanical properties and thermal stability. These properties make it suitable for a wide range of applications, from intricate electronic components to robust mechanical parts.
Post-Processing Options for PA 12
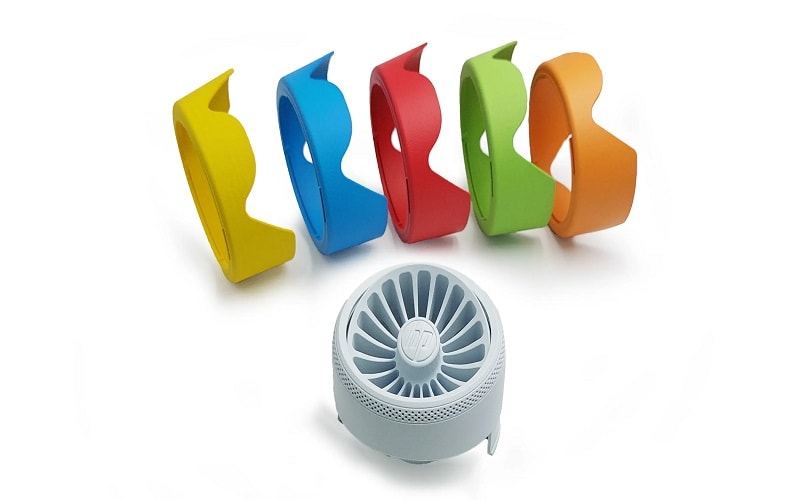
After printing, various post-processing techniques can enhance the appearance and functionality of PA 12 Nylon final parts. Finishing techniques include dyeing, polishing, painting, chemical smoothing, Color Touch, and Color Resist. Each method offers unique benefits, helping you achieve the desired look and feel for your parts.
Dyeing colors PA 12 parts, with the dye penetrating approximately 0.25 mm into the surface, ensuring vibrant and long-lasting colors. Polishing enhances surface smoothness, making PA 12 parts more visually appealing and reducing surface roughness. Chemical smoothing provides a glossy finish, improving the overall quality of PA 12 prints, while spray painting adds a protective color finish, enhancing durability and aesthetics.
These post-processing options help tailor your PA 12 Nylon parts to meet specific requirements and preferences. Whether a smooth, polished surface, vibrant color, or additional protection is needed, the right post-processing technique can significantly impact the final product.
Applications of PA 12 Nylon
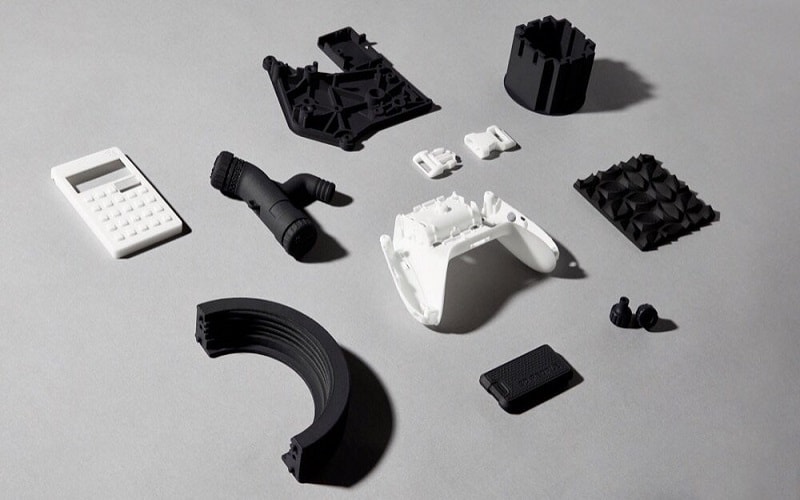
PA 12 Nylon is a versatile plastic with broad additive applications across various industries. Its versatility suits the production of both functional prototypes and end-use parts in additive manufacturing. The material’s robust properties and ease of processing make it suitable for applications ranging from aerospace components to consumer electronics.
Nylon PA 12 enables cheaper and faster production in rapid prototyping compared to traditional manufacturing processes. Recent studies indicate that recycling PA 12 powder waste can significantly lower production costs while supporting sustainability in 3D printing, making it a low cost option.
Specific applications of PA 12 Nylon in various industries are detailed below.
Aerospace and Automotive Industries
In the aerospace sector, PA 12 Nylon is used for components like brackets and ducting due to its lightweight and strong properties. Its resistance to many oils, greases, and fuels enhances its versatility, making it critical for automotive parts. PA 12’s lightweight and fatigue-resistant properties enhance overall efficiency and functionality in demanding environments.
These properties enable the production of parts that contribute to overall efficiency in aerospace and automotive industries. From Piper aircraft to automotive assemblies, PA 12 Nylon is crucial in creating durable and reliable components.
Medical and Prosthetics
Due to its biocompatibility, PA 12 Nylon is also used in creating durable medical devices. Its biocompatibility ensures it does not adversely affect the immune system, making it suitable for various medical applications, including prosthetics and surgical instruments. This attribute is essential for ensuring patient safety and comfort.
Nylon PA 12’s biocompatibility suits various medical applications, including prosthetics and surgical instruments. In the medical field, Nylon PA 12 is used to produce 3D printed prostheses, offering high customization and precision for patients.
Consumer Products and Electronics
PA 12 Nylon’s durability makes it ideal for electronic components, enhancing their lifespan and reliability. Its ability to produce fine-featured components makes it suitable for intricate electronic parts and consumer products. In consumer electronics, Nylon PA 12 is used for its excellent durability and ability to produce fine-featured components.
Integrating PA 12 in consumer products ensures both durability and functionality, making it a preferred material in electronics. With MJF technology, functional prototypes and end-use parts with fine details can be created, meeting high customer quality standards.
Cost and Sustainability Considerations
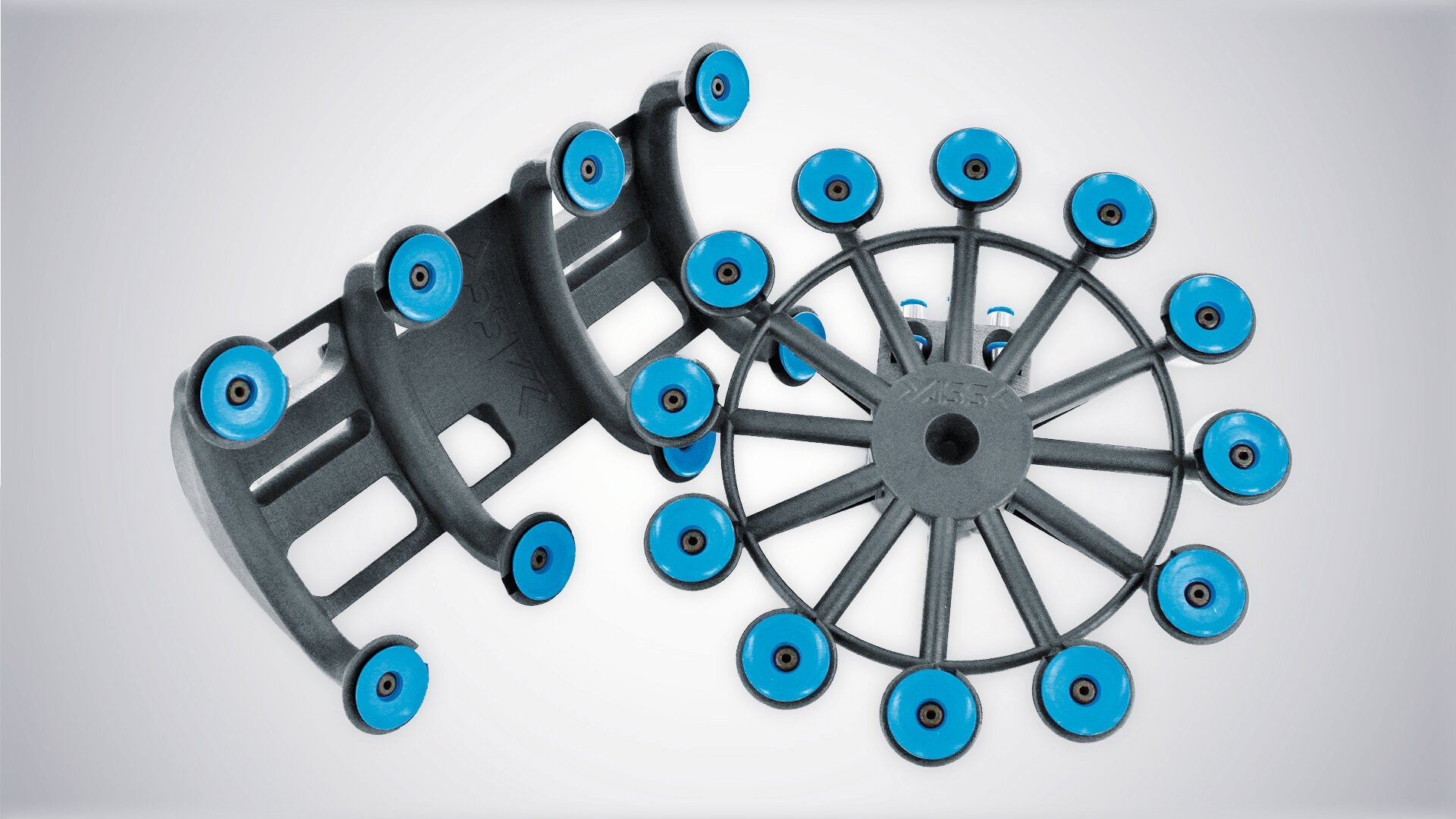
Cost and sustainability are crucial factors when working with PA 12 Nylon. Material costs typically account for about half of the total operating expenses in 3D printing, making recycling PA 12 powder a significant cost-saving measure. A challenge in reusing PA 12 powder is its loss of flowability after printing, leading to increased material waste unless fresh powder is continually added.
PA 12’s lightweight nature contributes to fuel efficiency in automotive applications, offering additional cost savings and sustainability benefits. Recycling PA 12 powder and optimizing its use allows manufacturers to achieve a more cost-effective and environmentally friendly production process, balancing cost and sustainability considerations.
Design Guidelines for PA 12 Prints
Specific design guidelines are crucial to optimize 3D prints with PA 12 Nylon. Wall thickness should be between 2-3 mm to ensure structural integrity and stability. For models with thin walls, adding a support structure is necessary to maintain stability during printing.
Incorporate at least two holes with a minimum diameter of 2 mm for effective powder removal. For more complex holes or ducts, larger diameters are needed to facilitate thorough powder removal.
When designing parts that fit together, allowing at least 0.6 mm of clearance is essential for proper assembly. For interlocking parts, a clearance of at least 0.5 mm is necessary to ensure they can move freely.
Hollowing out solid models can save material and reduce sink marks; this should be done with wall thickness considerations. Additionally, avoid designing large flat surfaces to minimize the risk of warping during the printing process.
By adhering to these design guidelines, you can optimize your PA 12 prints for better performance and quality.
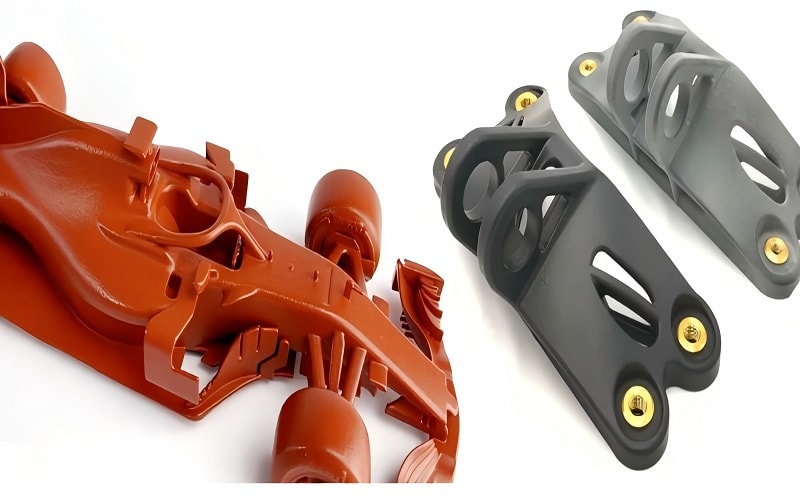
Lead Times and Delivery Expectations
When planning your 3D printing projects with PA 12 Nylon, understanding lead times and delivery expectations is crucial. Lead times for 3D printing with PA 12 nylon start at around 3 business days for standard services. Expedited delivery options can significantly shorten the turnaround time for PA 12 prints, ensuring quick production and delivery of your parts.
Sculpteo offers quick production times for unpolished Nylon PA12 prints, allowing for faster lead times and greater efficiency in your projects. By planning ahead and considering these factors, you can ensure timely delivery and high-quality results for your PA 12 prints.
Summary
In summary, PA 12 Nylon stands out as a versatile and robust material for 3D printing, offering excellent mechanical properties, chemical resistance, and low moisture absorption.
With advanced 3D printing techniques such as SLS and MJF, you can create intricate and durable parts that meet high standards of quality and performance. The various post-processing options further enhance the appearance and functionality of your PA 12 prints.
From aerospace and automotive industries to medical devices and consumer electronics, PA 12 Nylon finds broad applications across different sectors. By following the design guidelines and considering cost and sustainability factors, you can optimize your PA 12 prints for better performance and efficiency. Embrace the potential of PA 12 Nylon and take your 3D printing projects to new heights.
Frequently Asked Questions
What makes PA 12 Nylon a preferred material for 3D printing?
PA 12 Nylon is preferred for 3D printing due to its exceptional chemical resistance, low moisture absorption, and strong mechanical properties, which render it suitable for diverse applications such as aerospace and automotive industries.
What are the mechanical properties of PA 12 Nylon?
PA 12 Nylon possesses excellent mechanical properties, including a tensile strength of 53 MPa, a notched impact strength of 7 kJ/m², and a remarkable elongation at break of 200%. Its high strength, toughness, and chemical resistance render it ideal for demanding applications.
Which 3D printing techniques are best for PA 12?
Selective Laser Sintering (SLS) and Multi Jet Fusion (MJF) are the best 3D printing techniques for PA 12, with SLS providing strength and detail, while MJF enhances density and reduces porosity. Choose SLS for robust parts and MJF for higher quality finishes.
What post-processing options are available for PA 12 Nylon?
Post-processing options for PA 12 Nylon include dyeing, polishing, painting, chemical smoothing, Color Touch, and Color Resist, all of which can significantly enhance both the aesthetic and functional properties of the parts. These techniques are valuable for achieving desired finishes and characteristics.
How can I optimize my designs for PA 12 3D printing?
To optimize your designs for PA 12 3D printing, maintain a wall thickness of 2-3 mm, integrate support structures for thin walls, incorporate holes for powder removal, and ensure proper clearance for fitting parts seamlessly. This approach will enhance the print’s integrity and overall effectiveness.