It is well known that the most widely used materials in the polyamide family are PA6 and PA66.
Despite their similar names, they have significant differences in molecular structure, physical properties, and application scenarios.
PA6, polymerized from caprolactam monomer, has higher moisture absorption and better toughness.
In contrast, PA66, polymerized from hexamethylenediamine and adipic acid monomers, exhibits greater thermal stability and wear resistance.
These differences in monomer sources result in distinct polymer structures and physical properties, making them suitable for different products and industries.
In the following content, we will conduct a comprehensive comparison of PA6 vs PA66, delving into their differences in structure, performance, and applications.
What Is PA6?
PA6, also known as Nylon 6, belongs to the aliphatic polyamide family and is polymerized from caprolactam through ring-opening polymerization.
PA6 is a semi-transparent or opaque milky white particle with excellent properties such as light weight, high strength, wear resistance, resistance to weak acids and alkalis, and resistance to some organic solvents.
Additionally, it is easy to mold and process, making it widely used in the fields of fibers, engineering plastics, and films.
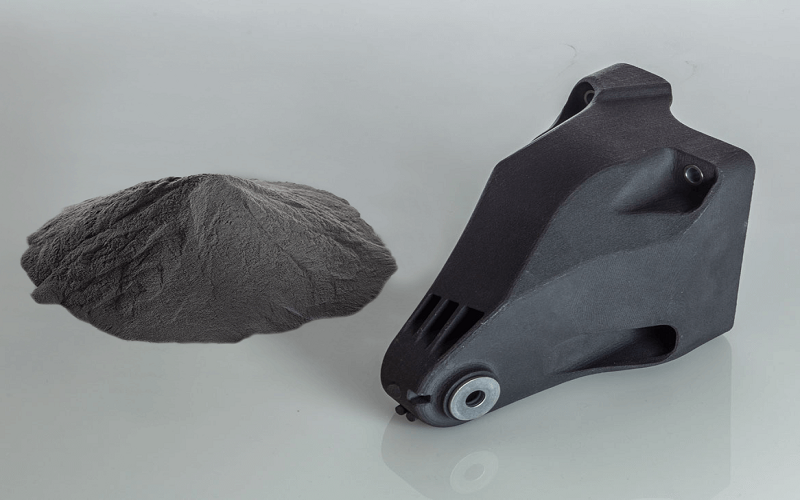
What Is PA66?
PA66, commonly known as Nylon 66, is synthesized from adipic acid and hexamethylenediamine. It is a colorless, transparent, semi-crystalline thermoplastic polymer.
Unlike PA6, PA66 is insoluble in common solvents and only dissolves in specific ones like m-cresol, retaining high strength and rigidity at elevated temperatures.
PA66 is used as an engineering plastic for mechanical components such as gears and lubricated bearings, and can replace non-ferrous metals in machine casings and automotive engine blades.
It is also widely used in synthetic fiber production.
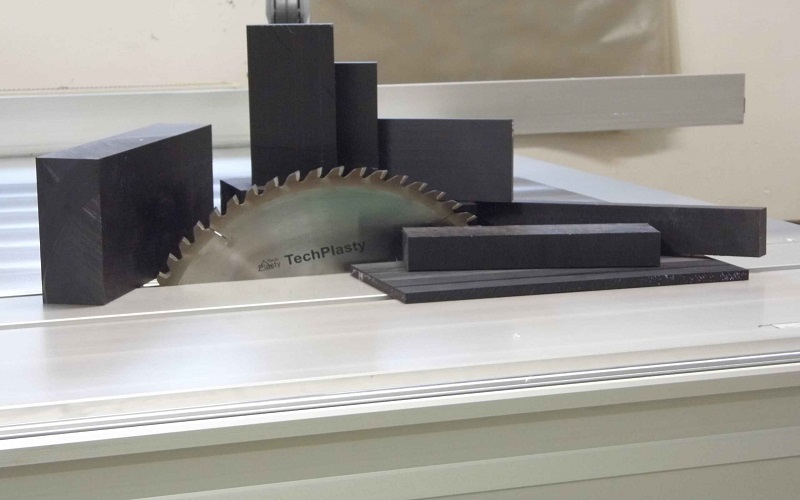
PA6 vs PA66:Molecular Structure
From a molecular structure perspective, PA6 and PA66 have the same ratio of carbon, hydrogen, oxygen, and nitrogen atoms, but their hydrogen bond arrangements differ significantly.
PA6 is formed by the ring-opening polymerization of caprolactam monomers, resulting in head-to-tail connected polyamides, whereas PA66 is polymerized from alternating hexamethylenediamine and adipic acid monomers.
Compared to PA6, PA66 has a higher degree of atomic regularity. The tighter hydrogen bond arrangement in PA66 leads to higher crystallinity.
PA6 has two types of hydrogen bond arrangements, with approximately 50% of the bonds being longer and weaker due to their inclined orientation.
In contrast, PA66 has only one type of hydrogen bond arrangement, where the bonds align in a straight line, forming a robust and densely packed polymer structure.
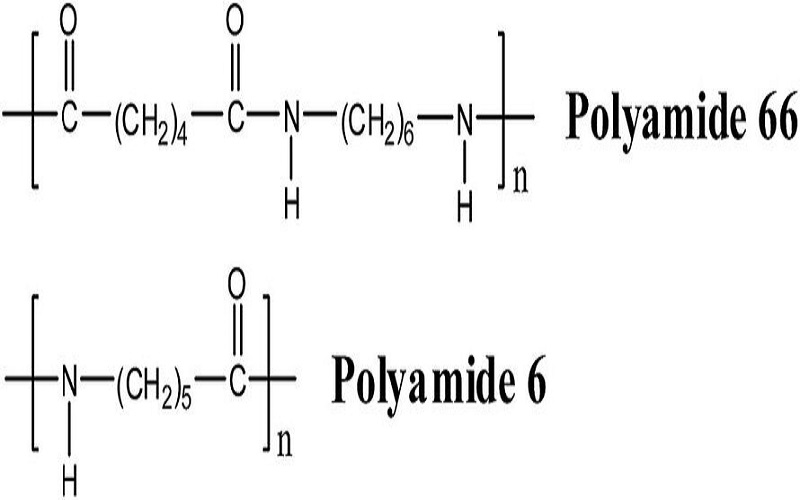
PA6 vs PA66:Properties
Under similar processing conditions, PA66 exhibits higher crystallinity and more ordered structure compared to PA6, resulting in a higher melting point, lower permeability, and greater resistance to deformation.
Additionally, PA66 has lower water absorption and shrinkage, providing better dimensional stability in molded parts.
In contrast, PA6 has a lower melting point and a wider processing temperature range.
PA6 also offers better impact resistance and solvent resistance than PA66, but it has higher hygroscopicity.
Since moisture absorption can affect the properties of many plastic parts, this factor must be carefully considered when designing products with PA6.
To enhance the mechanical properties of PA6, various modifiers are often added.
Glass fiber is the most common additive, and synthetic rubbers such as EPDM and SBR are sometimes incorporated to improve impact resistance.
Below is a data sheet of the physical properties of PA6 and PA66:
Properties | PA6 | PA66 |
Density(g/cm3) | 1.13 | 1.15 |
Melting Point(℃) | 215-220 | 255-265 |
Tensile Strength (MPa) | 70-80 | 80-90 |
Flexural Strength (MPa) | 90-100 | 100-120 |
Impact Strength(kg/m2) | 60 | 22 |
Heat Deflection Temperature(℃) | 68 | 75 |
Elongation (%) | 15-25 | 20-30 |
Water Absorption (%) | 1.2-1.5 | 0.7-0.9 |
Shrinkage (%) | 1.0-1.5 | 0.5-1.2 |
PA6 vs PA66:Processing Conditions
In terms of processing methods, both PA6 and PA66 are suitable for injection molding, extrusion, and blow molding, but the specific processing conditions differ.
In nylon injection molding, the mold temperature for PA6 is typically controlled between 80-90°C, and the injection temperature ranges from 220-260°C.
For PA66, the mold temperature is also controlled between 80-90°C, but the injection temperature ranges from 260-290°C.
It is important to note that PA6 is highly hygroscopic, so it must be thoroughly dried before processing.
If the moisture content exceeds 0.2%, it is recommended to dry the material in hot air at temperatures above 80°C for 16 hours. If the material has been exposed to air for more than 8 hours, it is recommended to perform vacuum drying at 105°C for more than 8 hours.
Parameter | PA6 Injection Molding | PA66 Injection Molding |
Mold Temperature (°C) | 80-90 | 80 |
Injection Temperature (°C) | 220-260 | 260-290 |
Injection Pressure(MPa) | 100-160 | 70-140 |
Injection Speed | High Speed | Fast |
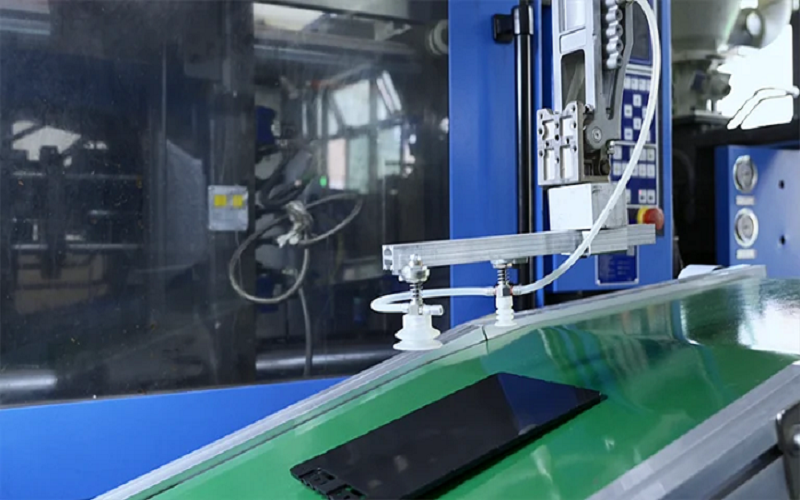
PA6 vs PA66:Applications
Although PA6 and PA66 are widely used across various industries, their specific applications differ due to their unique properties.
Both materials possess excellent weaving and sewing properties. However, PA66 has a higher melting point, better heat resistance, and superior elastic modulus, making it more suitable for manufacturing products that need to withstand heat and strain, such as tire cords, hot water washable fabrics, and woven fabrics.
In the industrial sector, PA6 is suitable for use under light load conditions and can be used in machine instruments, instrument parts, and insulation for wires and cables.
When reinforced with glass fiber, its mechanical properties are enhanced, making it suitable for the production of gears, rollers, and pump impellers.
Compared to PA6, PA66 has lower water absorption, higher strength, and better heat resistance.
It can be used to manufacture handles, high-temperature electronic components, and fasteners, which require impact resistance and high strength.
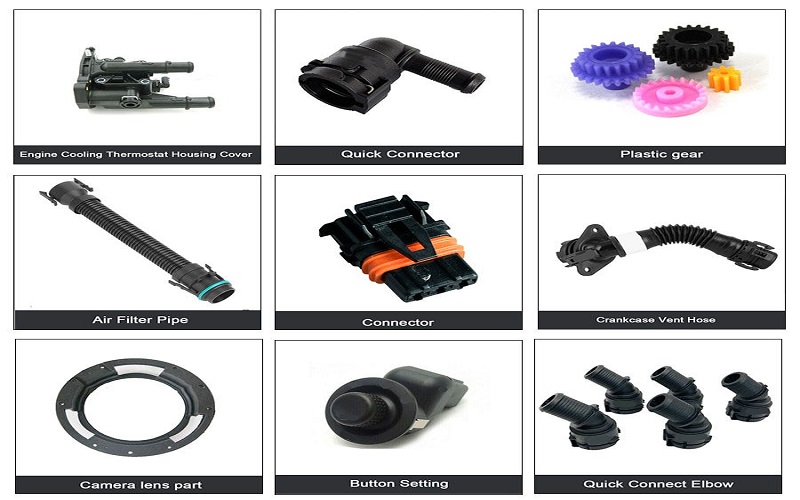
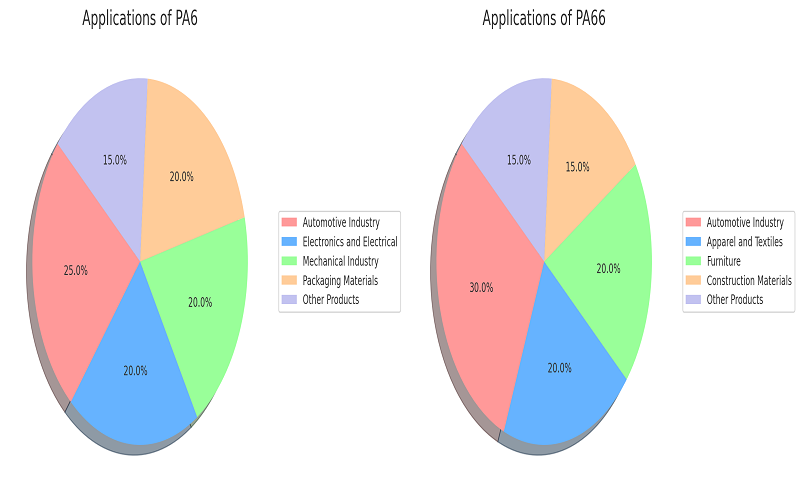
PA6 vs PA66:Cost
The raw material and processing costs of PA6 are generally lower than those of PA66.
Typically, the price of PA6 ranges from $2 to $4 per kilogram, while the raw material price of PA66 is usually between $3 and $6 per kilogram.
Additionally, PA6 has a lower processing temperature and consumes less energy, resulting in lower processing costs.
Although PA66 is more expensive, its superior heat resistance, strength, and dimensional stability make it suitable for high-performance applications.
For cost-sensitive applications, PA6 is the more economical choice, whereas for applications requiring high performance, PA66 is the better option.
Which Is Better,PA6 or PA66?
It’s difficult to judge which of these two materials is more effective, as both PA6 and PA66 have their own advantages, disadvantages, and applicable ranges.
PA6’s strengths lie in its excellent toughness and impact resistance, as well as its broad processing temperature range, although it has high hygroscopicity.
On the other hand, PA66 has a higher melting point, a harder feel, and superior heat resistance, but it lacks the resilience and impact strength of PA6.
For low-cost applications that require good toughness, impact resistance, and high processing flexibility, PA6 is a suitable choice.
For applications that demand high strength, rigidity, and heat resistance, PA66 is the more ideal option.