Polybutylene Terephthalate (PBT) plastic material is a durable, heat-resistant engineering polymer. Used in automotive and electronics, PBT’s key properties like high strength and excellent electrical performance make it essential for many critical applications. This guide explores what PBT is, its properties, and where it’s used.
Defining PBT Plastic
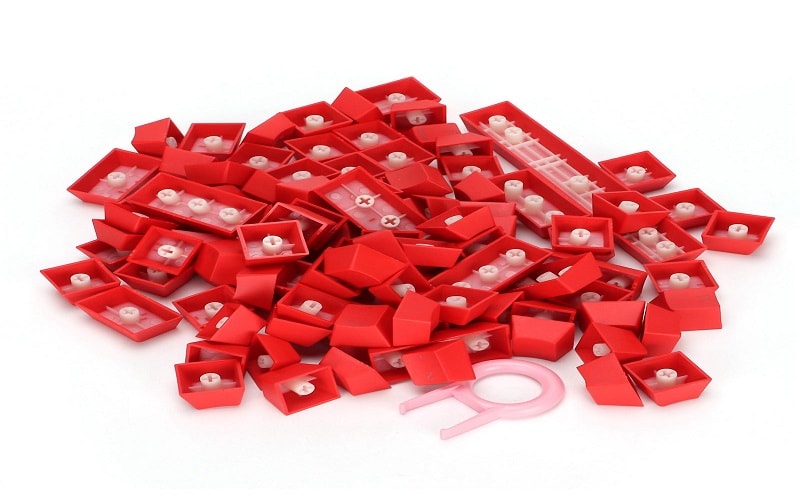
Polybutylene Terephthalate (PBT) is a fascinating material classified as a thermoplastic engineering polymer belonging to the polyester family.
Known for its excellent mechanical properties, PBT boasts:
- High strength
- Stiffness
- Low moisture absorption
- Good creep resistance
These characteristics make it an ideal candidate for various demanding applications. The aromatic rings in its structure contribute significantly to its excellent heat resistance, high heat resistance, and outstanding electrical properties, ensuring its place in high-performance environments.
PBT typically appears as a milky white material, ranging from semi-transparent to opaque, and is synthesized specifically for its unique properties. This synthetic thermoplastic does not only shine in mechanical and electrical aspects but also stands out in its physical properties and PBT material properties, making it a versatile and widely-used material in industries from automotive to electronics.
Key Properties of PBT
Key properties of PBT reveal its full potential for various applications. This high-performance thermoplastic engineering polymer exhibits remarkable physical, thermal, and mechanical properties, making it a preferred choice among engineers and designers.
Its mechanical properties, thermal properties, and chemical resistance are primary factors contributing to its widespread use.
Property | Value/Description | |
Chemical Name | Polybutylene Terephthalate (PBT) | |
Glass Transition Temperature (Tg) | 22°C | |
Melting Temperature (Tm) | 225°C | |
Density | 1.31 g/cm³ | |
Water Absorption | 0.34% | |
Molding Shrinkage Rate | 1.7—2.3% | |
Tensile Strength | 50-80 MPa | |
Flexural Modulus | 2.0-2.8 GPa |
Mechanical Properties
PBT’s mechanical properties are one of its strongest suits. It boasts higher tensile strength compared to many other plastics, making it a robust option for structural applications. Additionally, PBT exhibits high impact strength, particularly when reinforced with materials like glass fibers, which can increase its tensile strength up to threefold and significantly improve its flexural modulus.
This reinforcement not only enhances the overall mechanical performance but also allows PBT to maintain its strength even at low temperatures down to -40 degrees Celsius, contributing to its good creep resistance in various applications.
PBT’s excellent resistance to cracking and dimensional stability make it reliable for automotive and electronic components. Its ability to withstand mechanical stress and maintain structural integrity in demanding environments underscores its role as a high-performance material in numerous industries.
Thermal Properties
PBT excels in thermal properties, withstanding high temperatures effectively. It has an impressive heat resistance, capable of enduring temperatures up to 150 degrees Celsius, making it suitable for applications that require thermal stability. With a melting point of approximately 230 degrees Celsius, PBT ensures reliable performance in high-temperature environments.
Compared to PA66, PBT maintains superior heat resistance along with its strength and stiffness at elevated temperatures. This combination of high heat resistance and excellent mechanical properties makes PBT an ideal choice for components that must perform under thermal stress, such as those found in automotive and electrical applications.
Chemical Resistance
PBT’s significant chemical resistance enhances its suitability for various applications. It exhibits significant resistance to various chemicals at room temperature, including oils, diluted acids, and organic solvents. This resistance ensures that PBT maintains its integrity and performance even when exposed to potentially damaging substances.
PBT maintains its chemical resistance under standard conditions, ensuring reliability in everyday applications. This outstanding resistance to chemicals, combined with its low moisture absorption, makes PBT an excellent choice for components exposed to harsh chemical environments, such as those in automotive and industrial settings.
Manufacturing Process of PBT
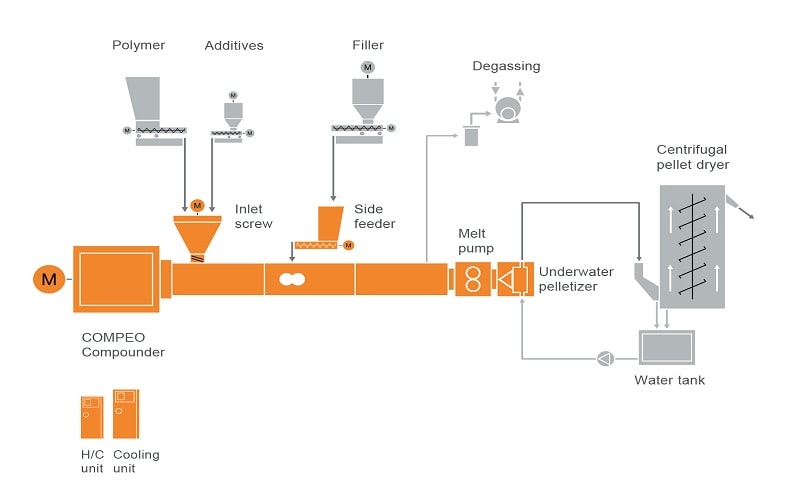
The manufacturing process of PBT is a fascinating journey from raw materials to a high-performance polymer. It starts with core raw materials, specifically butanediol, dimethyl terephthalate, and purified terephthalic acid.
These materials undergo a polymerization process, where they are chemically combined to form the PBT polymer. This process involves the use of catalysts to facilitate the reactions, ensuring efficient and effective synthesis.
During the manufacturing of PBT, byproducts such as tetrahydrofuran (THF) and water are formed. These byproducts are carefully managed to ensure the purity and quality of the final polymer. A thorough understanding of the manufacturing process optimizes PBT properties and ensures suitability for various applications.
Applications of PBT in Various Industries
PBT’s versatility and exceptional properties make it suitable for a broad range of applications across various industries.
From aviation and automotive to electronics and consumer goods, PBT proves to be a valuable material in numerous sectors.
Its characteristics enable replacement of materials like nylon and polypropylene, making it indispensable for many manufacturers.
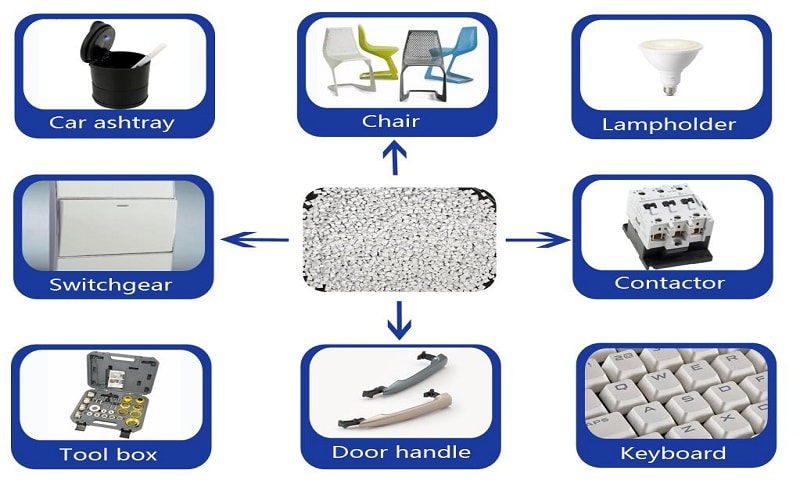
Electrical and Electronic Components
PBT excels in electrical and electronic components due to its excellent insulating properties and high dielectric strength. These attributes make it highly effective in preventing electrical leakage and breakdown in power circuits.
Compared to polyamide66 (PA66), PBT offers better electrical performance and processing characteristics, making it a preferred material for connectors, switches, and other electronic parts.
PBT ensures reliability and safety in electronic components due to its excellent electrical properties. Its ability to maintain performance under electrical stress makes it an ideal choice for modern electronic devices and systems.
Automotive Components
PBT is widely used in the automotive industry, where its excellent mechanical properties and high heat resistance are highly valued. It is commonly found in automotive parts such as wiper covers, mirror housings, and fuel system components.
Additionally, PBT fabric is used in automotive interior components like seat covers, door panels, and headliners, contributing to both functionality and aesthetics.
PBT enhances performance and durability in automotive components, ensuring reliability in demanding environments. Its ability to withstand mechanical stress and high temperatures makes it an indispensable material for modern vehicles.
Consumer Goods and Industrial Uses
PBT’s durability and weather resistance make it an ideal material for consumer goods and industrial uses. It is commonly found in items that require long-lasting performance, such as motor brackets and appliance handles. Its excellent weather resistance allows it to be used in outdoor applications without significant degradation.
Blending PBT with polymers like polycarbonate (PC) enhances its performance. Mixing PBT with acrylonitrile butadiene styrene (ABS) also improves its characteristics. Incorporating flame retardant agents into PBT formulations significantly bolsters its fire resistance, making it suitable for a variety of demanding applications.
Advantages of Using PBT in Injection Molding
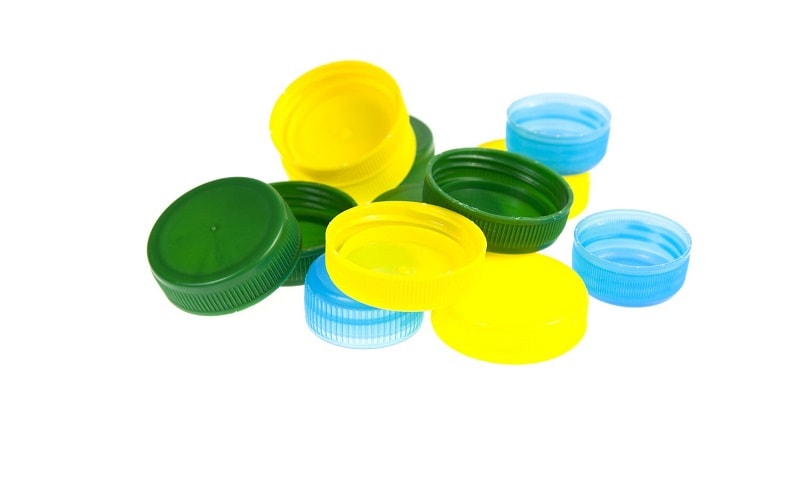
PBT offers numerous advantages when used in injection molding applications. Excellent dimensional stability makes PBT ideal for precision components, ensuring consistent performance and reliability. PBT’s low moisture absorption helps maintain its mechanical properties in various environmental conditions.
PBT’s versatility allows for complex shapes through injection molding, enabling innovative designs. Its strong color retention also helps maintain the aesthetic appeal of molded products over time, making it a preferred choice for manufacturers seeking both functionality and visual appeal.
Disadvantages and Limitations of PBT
Despite its many advantages, PBT does have some limitations. A significant drawback is PBT’s poor resistance to hydrolysis, caused by ester bonds breaking down under long-term high temperatures and moisture. This makes PBT less suitable for applications where it is exposed to humid or wet environments.
PBT is also unsuitable for environments with strong acids or bases due to its lack of resistance to these conditions. Understanding these limitations is crucial for selecting the right material for specific applications and ensuring optimal performance.
Enhancing PBT with Additives and Blends
Additives and blends can significantly enhance PBT’s properties and expand its applications. For instance, UV-stabilized PBT can be achieved by incorporating additives that enhance its resistance to UV radiation. Common additives like glass fibers and other fillers can improve the mechanical properties and heat resistance of PBT, making it even more robust.
Flame retardant additives modify PBT for fire safety, especially in electrical and electronic components. Blending PBT with polycarbonate (PC) or acrylonitrile butadiene styrene (ABS) creates materials with customized flame retardant grades. This process enhances performance for particular applications.
Environmental Impact and Sustainability
The environmental impact and sustainability of PBT are increasingly important considerations. Research is focused on developing biomass-derived sources for PBT production, aiming to reduce reliance on non-renewable resources. Additionally, PBT fabric can be produced using recycled materials, which helps reduce waste and promote sustainability.
PBT fabric is also perceived as a promising choice for environmentally conscious consumers due to its sustainable features. Durability and recyclability reduce PBT’s environmental impact, making it a choice for reducing ecological footprints.

Processing Techniques for PBT
Various processing techniques suit different PBT applications. Injection molding, known for efficiency and ability to produce complex shapes, is the most common method. The recommended injection molding temperature for PBT is 230°C to 270°C, with pre-drying essential to keep moisture below 0.02%.
Other techniques include blow molding for hollow items like bottles and extrusion for profiles and tubes. Compression molding is effective for larger or thicker components, ensuring proper crystallization during cooling.
Comparing PBT with Other Polymers
Comparing PBT with other polymers reveals its strengths and limitations. PBT’s lower glass transition temperature compared to some materials may affect its performance relative to polyamide66 (PA66). However, PBT offers superior mechanical properties and chemical resistance, making it a competitive engineering polymer.
Compared to polypropylene, PBT is heavier and less soft, impacting its applicability in certain areas. It is also less effective in extreme environmental conditions compared to other high-grade plastics.
Yet, its excellent mechanical properties and good mechanical properties, along with its chemical resistance, make it a preferred material for many applications.
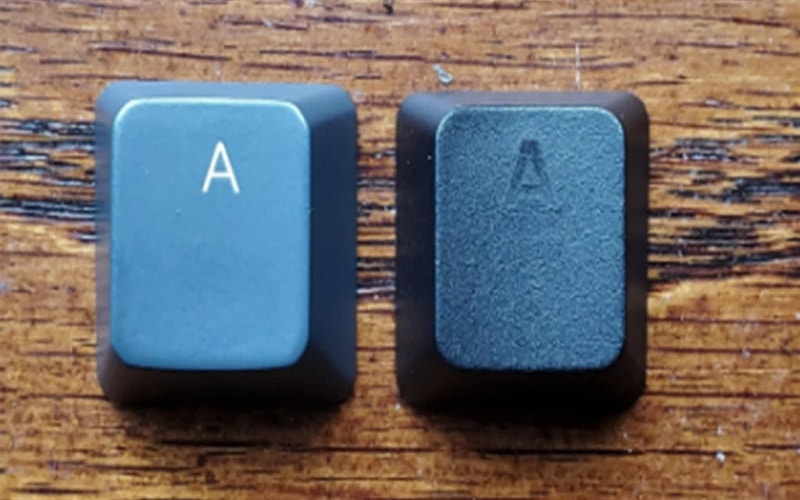
Summary
In summary, PBT plastic stands out as a high-performance material with excellent mechanical, thermal, and chemical properties. Its versatility and adaptability make it an ideal choice for a wide range of applications across various industries. From automotive and electronics to consumer goods and industrial uses, PBT continues to prove its worth.
As we look to the future, the ongoing research into biomass-derived sources and recycled materials will further enhance the sustainability of PBT. By understanding its properties, manufacturing processes, and applications, engineers and designers can fully leverage the potential of PBT to create innovative and sustainable products.
Frequently Asked Questions
What are the key properties of PBT that make it suitable for various applications?
PBT exhibits exceptional mechanical strength, high heat resistance, and notable chemical resistance, rendering it highly suitable for a wide range of industrial applications. These properties ensure its reliability in demanding environments.
How is PBT manufactured?
PBT is manufactured through a polymerization process that utilizes raw materials like butanediol and terephthalic acid, resulting in byproducts such as tetrahydrofuran and water. This method effectively transforms these compounds into the desired polymer.
What are some common applications of PBT in the automotive industry?
PBT is commonly utilized in the automotive industry for components including wiper covers, mirror housings, fuel system parts, and various interior elements such as seat covers and door panels. Its versatility makes it an essential material in automotive manufacturing.
How can the properties of PBT be enhanced?
The properties of PBT can be enhanced by incorporating additives such as glass fibers, UV stabilizers, and flame retardants, or by blending it with other polymers like polycarbonate or ABS. This approach effectively improves its performance characteristics.
What are the environmental benefits of using PBT?
Using PBT promotes sustainability through its production from recycled materials and biomass, while its durability and recyclability further minimize environmental impact. Therefore, its adoption is beneficial for ecological preservation.