When deciding between PC ABS and ABS for your 3D printing projects, it’s important to understand the key differences in the context of PC ABS vs ABS. PC ABS is a blend of polycarbonate and ABS, offering superior mechanical properties and heat resistance.
ABS, on the other hand, is known for its affordability and good impact resistance at lower temperatures. This article will break down their main properties, applications, and how to choose the right one for your needs in the debate of PC ABS vs ABS.
Understanding PC ABS and ABS
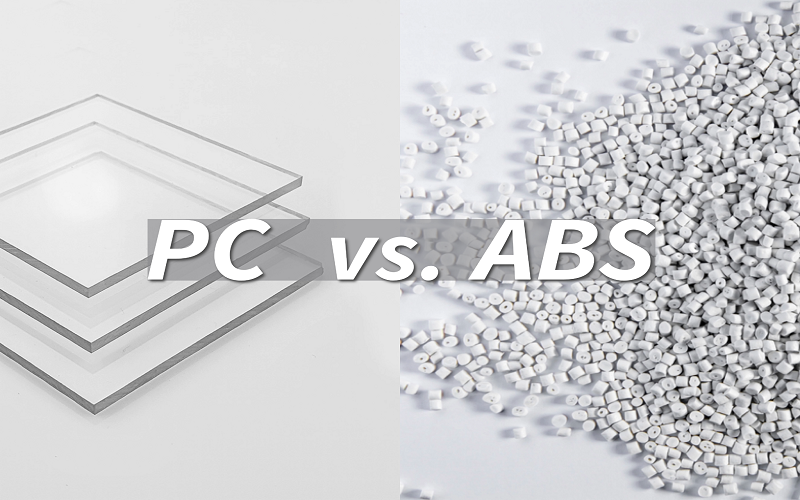
Acrylonitrile Butadiene Styrene Polycarbonate (PC-ABS) is a blend of polycarbonate and ABS that combines the superior qualities of both materials. ABS plastic is recognized for its excellent low-temperature impact resistance and moldability. It also offers chemical resistance and is relatively affordable.
Conversely, PC ABS boasts enhanced mechanical properties and impact resistance, fitting high-performance needs. This combination of features addresses some limitations of each material, providing a balanced solution for various applications.
Composition and Structure
PC ABS is a combination of polycarbonate and ABS. ABS, however, is solely composed of acrylonitrile butadiene styrene. This blend combines the beneficial properties of both materials, with polycarbonate contributing high-temperature resistance, flame retardancy, and excellent electrical insulation.
Although both PC ABS and ABS share a similar chemical composition, their structures and resulting properties diverge significantly. The polycarbonate component enhances the overall performance of PC ABS, making it suitable for more demanding applications.
Key Properties
With superior mechanical strength, PC ABS excels in demanding applications. The combination of ABS and polycarbonate results in improved heat resistance and increased strength. A standout feature of PC ABS is its superior heat resistance over pure ABS.
These enhanced mechanical properties make PC ABS a preferred choice for applications requiring high strength and durability. Typically, the density of PC-ABS ranges between 1.05 and 1.20 g/cm³.
Mechanical Properties Comparison
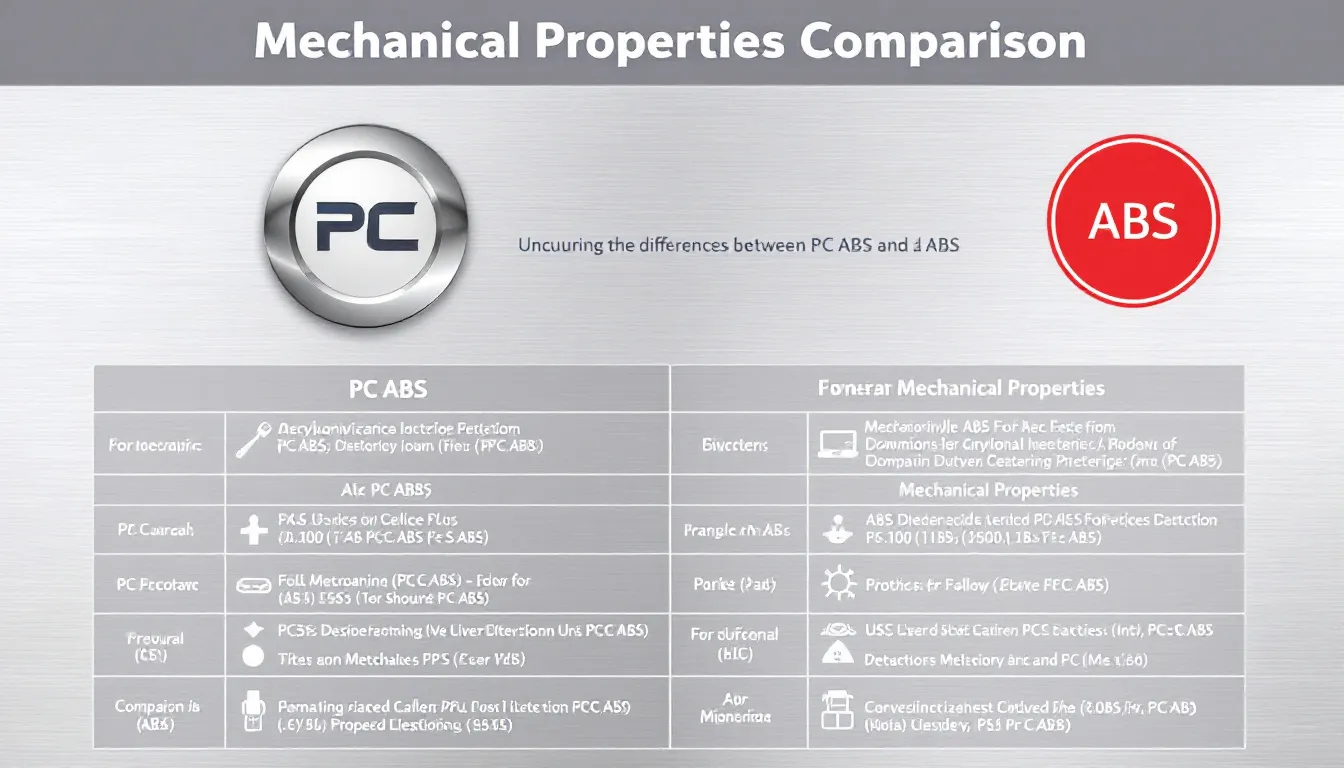
PC ABS offers better mechanical properties compared to ABS, which includes a combination of enhanced strength and durability. Key performance areas where PC ABS excels include mechanical strength and improved processing performance, making it suitable for demanding applications.
Additionally, PC ABS demonstrates superior thermal stability and heat resistance compared to standard ABS, enabling it to maintain structural integrity even under high temperatures. This superior mechanical performance allows PC ABS to be used effectively in high-stress applications, such as automotive and telecommunications.
Impact Resistance
PC-ABS surpasses regular ABS in impact resistance, ideal for demanding uses. Enhanced impact resistance stems from the inherited ABS properties. PC-ABS is designed to provide significant impact resistance, which exceeds that of traditional ABS.
This makes it ideal for applications that experience high-stress conditions. Impact resistance is a critical property for materials used in high-stress applications.
Tensile Strength and Flexural Strength
In terms of tensile and flexural strength, PC ABS outperforms ABS, presenting better mechanical characteristics. PC ABS boasts a tensile strength of 5900 psi, surpassing that of pure ABS.
Moreover, with a flexural strength of around 9800 psi, PC ABS is apt for structural uses. These mechanical properties are crucial in determining material suitability for specific applications.
Durability and Toughness
Derived from a blend of two thermoplastics, PC ABS offers unique properties. It is more durable than ABS. However, it is not as durable as pure PC. At elevated temperatures, PC ABS retains structural integrity better than ABS, suiting high-heat uses.
Additionally, ABS performs well in low temperatures, maintaining good impact resistance and flexibility, while PC ABS can also endure without significant brittleness. Long-term benefits, such as durability and reduced maintenance costs, can offset the higher upfront cost of PC ABS material.
Processing and Manufacturing
Due to reduced flowability, PC ABS can be challenging in injection molding, particularly for complex molds. Yet, it’s extensively used in automotive and electronics industries.
Toy State uses PC ABS to reduce prototyping time in their 3D printing projects. During processing, polycarbonate in PC ABS gradually loses viscosity, impacting manufacturing.
Injection Molding
Injection molding is common for both PC ABS and ABS, each with specific requirements. Enhanced flowability of PC ABS over pure ABS eases molding complex shapes. However, ABS generally requires less precise temperature control than PC ABS during processing.
Addressing PC ABS flowability issues may require adjusting processing parameters or redesigning molds.
3D Printing
The flow characteristics of PC ABS contribute to its effective use in 3D printing processes. Enhanced flow characteristics improve the surface finish quality of PC ABS parts.
Industries such as prototyping, tooling, and production parts can benefit from using PC ABS in 3D printing.
Applications in Various Industries
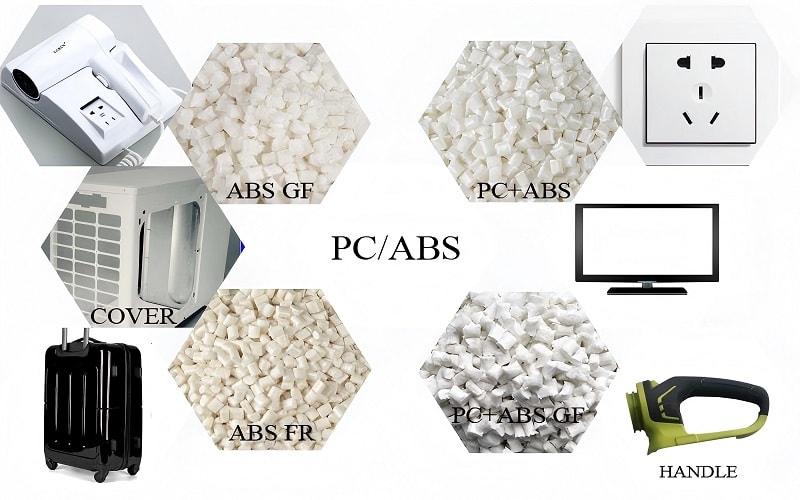
PC ABS and ABS are commonly used in industries such as automotive and electronics. PC ABS finds applications in automotive parts, electronics, and medical equipment.
The versatility of PC ABS ensures strong performance in challenging environments.
Automotive Industry
Automotive components like instrument panels, door panels, grilles, and exterior trims are commonly made from PC ABS. Good weatherability makes PC ABS suitable for automotive interiors and exteriors. The automotive industry prefers PC ABS for its high strength, impact resistance, and dimensional stability.
Excellent impact resistance, heat resistance, and dimensional stability make PC ABS ideal for automotive parts. For enhanced performance, PC ABS is preferred despite its higher cost over pure ABS.
Electronics Industries
PC ABS and ABS materials are widely used in consumer electronics applications. Casings and internal components for laptops, mobile phones, and tablets are common applications. In electronics, pc abs plastic offers impact resistance, heat resistance, flame retardancy, and electrical insulation.
Medical Equipment
PC ABS’s chemical resistance withstands exposure to medical disinfectants. Medical equipment materials must prioritize safety and substance compatibility. Resisting disinfectants prolongs device lifespan and ensures safety in critical situations.
Hence, PC ABS is favored in medical equipment for its chemical resistance and safety.
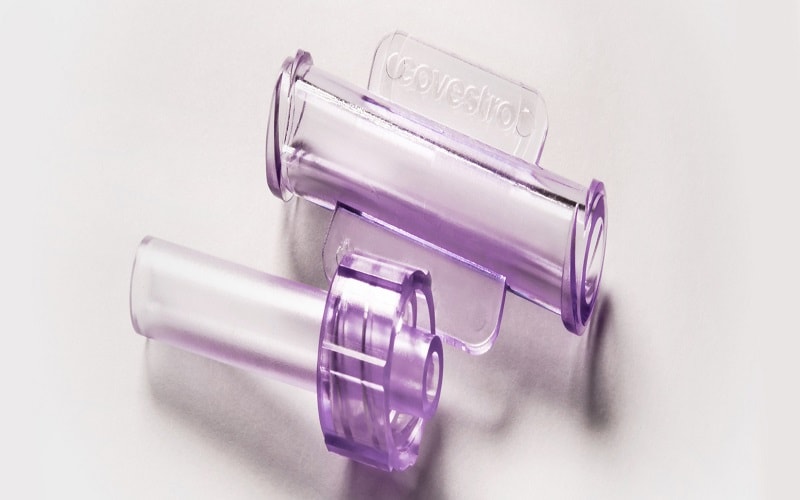
Consumer Goods and Household Appliances
ABS PC is popular for visually appealing consumer products with a range of color options.
Their diverse properties make PC ABS and ABS extensively used in consumer goods and household appliances.
Performance at Different Temperatures
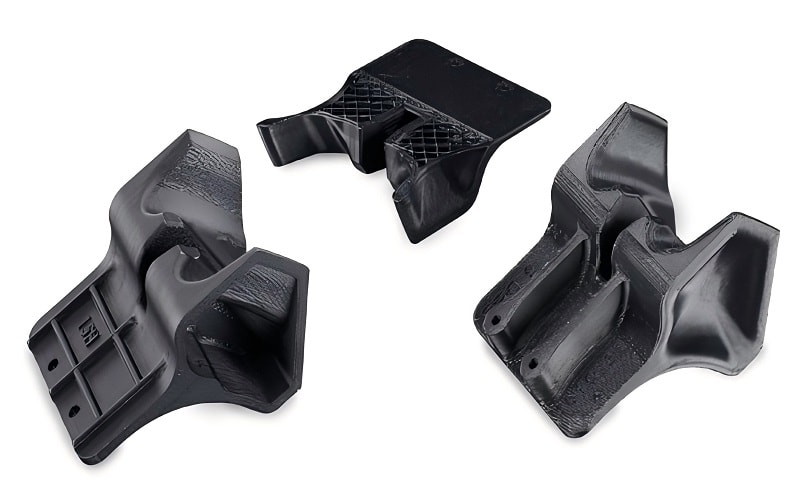
High durability and heat resistance make heat resistant PC ABS with high heat resistance suitable for functional 3D printing parts. Different reactions of PC ABS and ABS under various temperatures impact their application suitability.
PC ABS maintains integrity at high temperatures, outperforming ABS in heat-sensitive applications.
Elevated Temperatures
PC ABS shows superior heat resistance over pure ABS. Thus, it’s more suitable for applications needing thermal stability. Maintaining better durability in harsh environments than ABS, it suits various applications. PC ABS outlasts ABS, especially under changing environmental conditions.
Flame retardant properties make PC ABS ideal for electronic enclosures and high-heat uses. Despite higher costs, PC ABS offers long-term value via enhanced durability and functionality.
Low Temperatures
At lower temperatures, PC ABS retains flexibility and impact resistance, surpassing standard ABS. PC ABS exhibits less brittleness and retains flexibility at low temperatures, unlike ABS. Low temperatures make ABS brittle, reducing its impact strength compared to PC ABS.
PC ABS remains tough at low temperatures, outperforming ABS but not pure polycarbonate.
Choosing the Right Material for Your Project
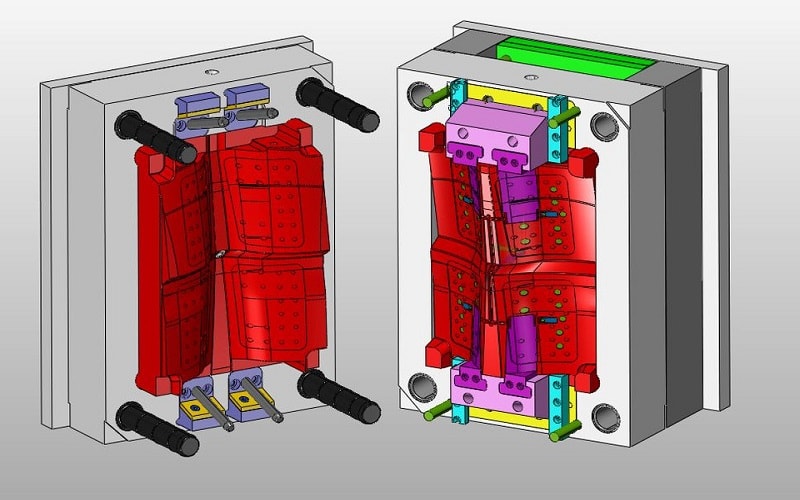
Ease of processing, colorability, and balanced mechanical properties make PC ABS versatile for many applications. Mixing with other materials can enhance its durability and stability for specific projects.
Selecting the right material is vital for a successful 3D printing project. Material selection should consider durability and project requirements for optimal performance.
Factors to Consider
Choosing material based on desired final product characteristics is influenced by processing methods like injection molding or 3D printing. Production efficiency and available processing methods influence material choice.
Considering the end-use environment, such as chemical exposure and temperature extremes, is vital in material selection. Strength and durability are critical mechanical properties for material selection in specific applications.
Cost Considerations
PC ABS costs more than ABS. PC ABS’s higher price can impact cost-sensitive projects.
Yet, PC ABS could be more economical for applications needing better performance than ABS but not the cost of pure PC.
Summary
In summary, both PC ABS and ABS have their unique advantages and applications. PC ABS offers superior mechanical properties and heat resistance, making it suitable for more demanding applications. ABS, on the other hand, is more cost-effective and easier to process.
Choosing the right material for your 3D printing projects requires careful consideration of the specific requirements, processing methods, and cost implications. Ultimately, selecting the appropriate material will ensure the success and quality of your final product.
Frequently Asked Questions
What are the main differences between PC ABS and ABS?
PC ABS combines polycarbonate with ABS, providing enhanced mechanical properties and higher heat resistance than standard ABS. This makes PC ABS a preferable choice for applications requiring greater strength and durability.
Why is PC ABS preferred in high-stress applications?
PC ABS is preferred in high-stress applications due to its superior impact resistance, tensile strength, and durability. This combination of properties ensures it can withstand demanding conditions effectively.
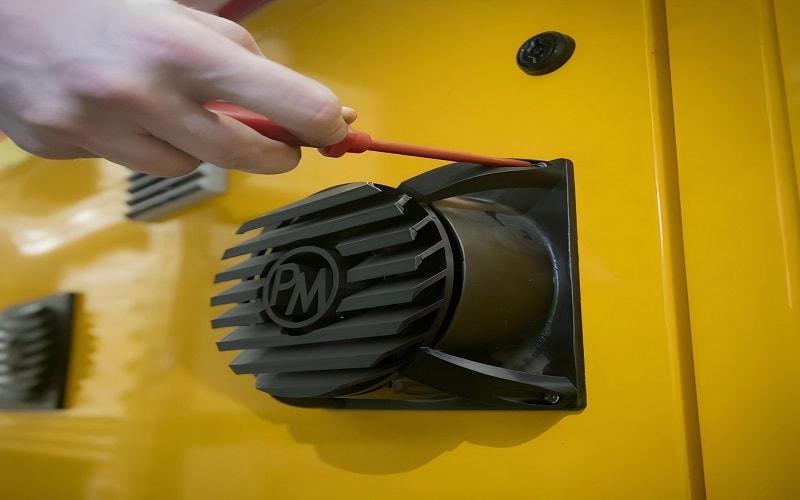
How does PC ABS perform at different temperatures?
PC ABS exhibits superior integrity and flexibility across a range of temperatures, making it preferable to ABS in applications where heat sensitivity is a concern.
What factors should I consider when choosing between PC ABS and ABS for my project?
When choosing between PC ABS and ABS, it is essential to evaluate the project’s mechanical properties, processing methods, environmental conditions, and cost implications to determine the most suitable material. Prioritizing these factors will guide your decision effectively.
Is PC ABS more expensive than ABS?
PC ABS is indeed more expensive than ABS, but its enhanced performance often justifies the additional expense for high-demand applications.