Polylactic acid (PLA) is an environmentally friendly material that is changing the manufacturing industry. It comes from renewable sources such as corn starch and sugarcane and is naturally biodegradable, making it a sustainable alternative to conventional plastics.
PLA is attracting increasing attention because it is not only more environmentally friendly than existing petroleum-derived plastics, but also exhibits excellent performance in processing such as injection molding.
This guide explains how to effectively use PLA in injection molding to streamline the manufacturing process and produce high quality products while reducing waste.
Understanding the properties of this material can help improve production technology and contribute to environmental protection. Simple, easy-to-understand procedures will help you master the basics of PLA injection molding and achieve better results in your work.
Understanding PLA Materials
What is PLA?
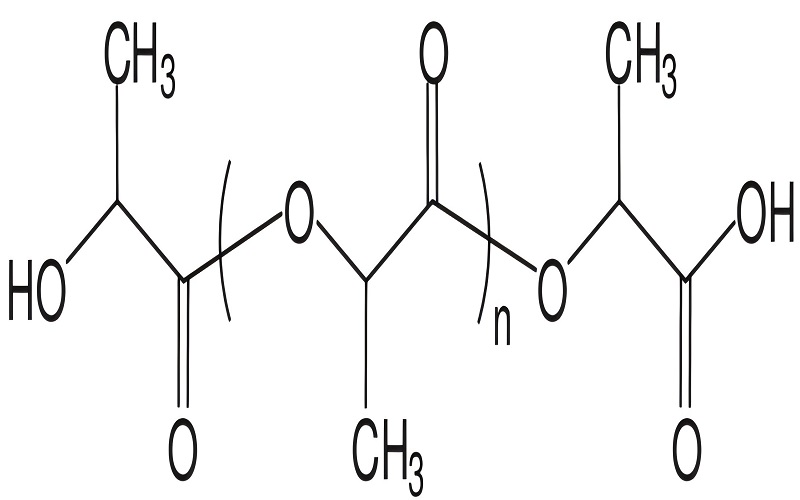
Polylactic acid (PLA) plastic is a novel biodegradable material derived from sustainable plant sources. It is created by fermenting plant starch or sugar to produce lactic acid, which is then polymerized. Because PLA is better for the environment than traditional plastics derived from petroleum, it is gradually replacing them.
Renewable Resources for PLA Production
PLA is produced using natural and renewable feedstocks such as:
- Corn Starch
- Sugarcane
- Tapioca Roots
- Beet Pulp
These materials undergo fermentation to produce lactic acid, which is then polymerized to form PLA.
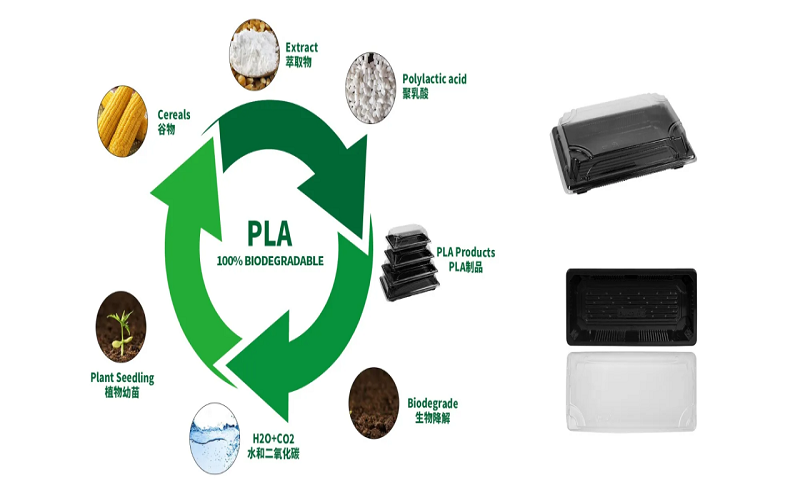
Properties of PLA
PLA materials possess several attributes that make them desirable for various applications:
- Biodegradability: Unlike conventional plastics, PLA decomposes naturally over time, reducing environmental impact.
- Non-toxicity: Safe for use in food packaging and medical devices, ensuring no harmful chemicals leach into consumables or bodily tissues.
- Mechanical Strength: Exhibits excellent tensile and ductile strength, suitable for robust and durable products.
These properties underscore the versatility of PLA in industries ranging from food packaging to healthcare. Its combination of sustainability and performance makes it a preferred choice for manufacturers seeking green solutions.
Here are some detailed properties of PLA:
Property | Value Range | Unit |
Density | 1.24–1.30 | g/cm³ |
Tensile Strength | 50–70 | MPa |
Elongation at Break | 2–10 | % |
Flexural Strength | 80–110 | MPa |
Flexural Modulus | 3.5–4.0 | GPa |
Glass Transition Temp | 55–60 | °C |
Melting Point | 150–160 | °C |
Heat Deflection Temp (HDT) | 55–65 | °C |
Water Absorption | 0.5–0.6 | % |
Biodegradability | Fully biodegradable | – |
Applications of Polylactic Acid (PLA)
Polylactic Acid (PLA) is recognizing considerable acceptance within many industries, because of its sustainability and capability for multiple uses.
PLA injection molding has become the preferred alternative for a compostable product.
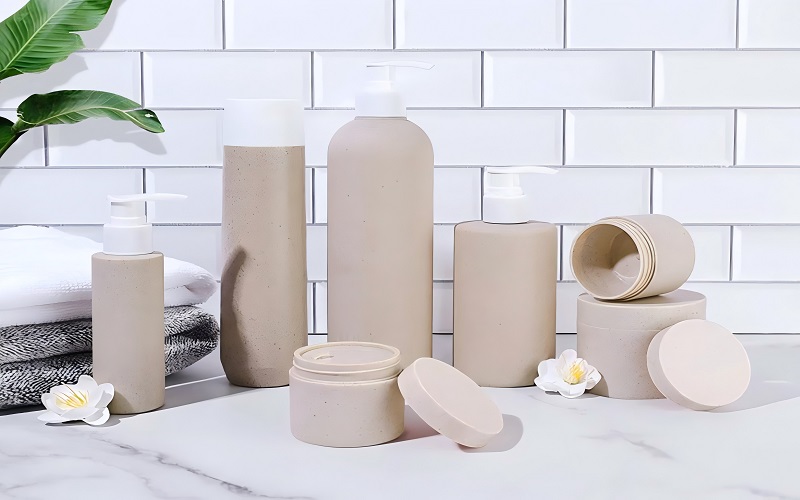
Packaging, Food: PLA characteristics of biodegradability and non-toxicity have made it the appropriate choice or an obviously sustainable choice for food containers, food wrapping, and disposable cutlery. PLA also has the abilities to be used within safe product guidelines to maintain the integrity and safety of consumables.
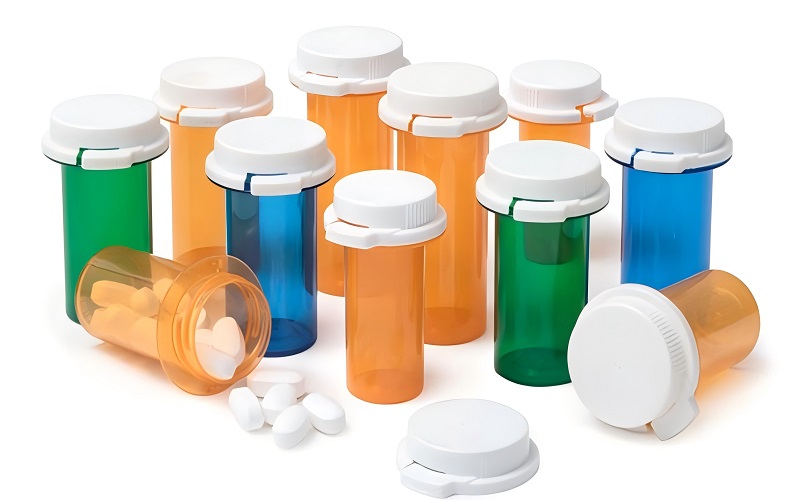
Healthcare: The PLA polymer can be a nursing-friendly product while producing items such as biocompatible devices, surgical sutures, and infusion devices. With the high strength of PLA, it can be produced to be non-irritating, making a reliable biocompatibility medical device for patient safety.
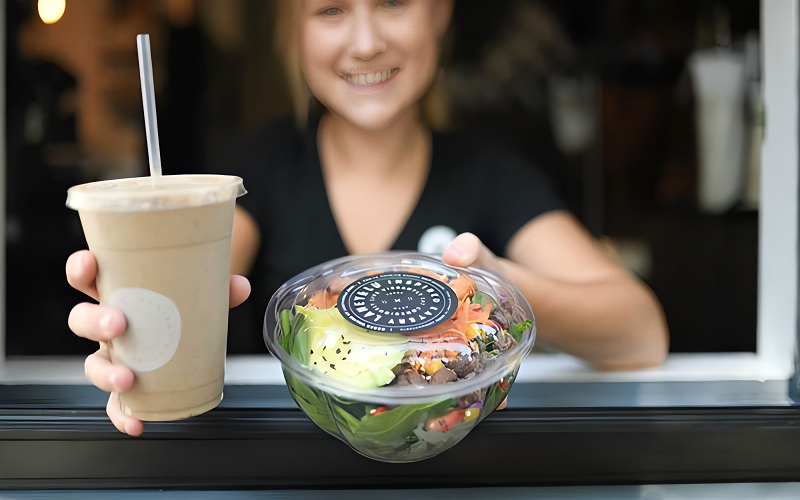
Consumer Goods: can be used in the making of reusable and disposable products, for example: kitchen dishcloths, sanitary goods, floor mats, or items composed of UV resistant PLA fabric. Manufacturing offers the ease of processing PLA into items that are durable and simple in implementation.
Distribution of PLA injection molding in other industries:
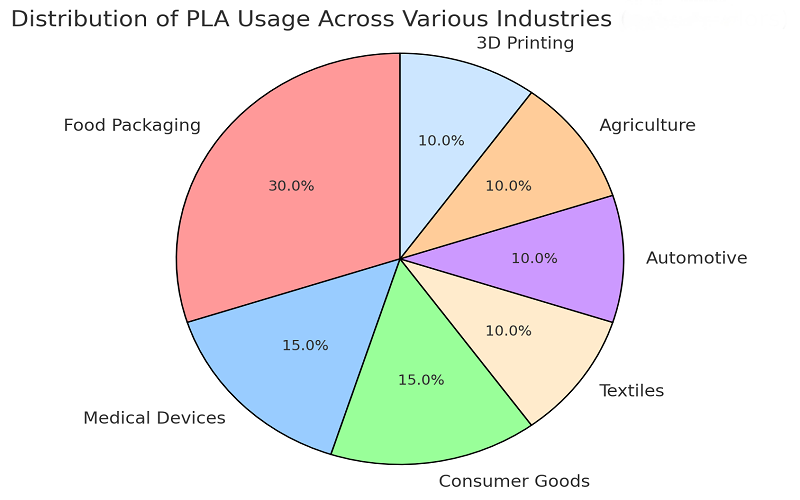
PLA Injection Molding Steps
The process of injection molding PLA material involves several important steps:
- Material Preparation: In order to prevent degradation at high temperatures, PLA resin must first be dried until the moisture content is less than 0.01%. Typical drying temperatures are 50°C to 60°C, approx. 4 hours.
- Dissolving: Heat the PLA to 160°C to 180°C and stir evenly to dissolve.
- Injection: Molten PLA is injected into the mold under high pressure to ensure even filling and reduce defects.
- Cooling: Allow the mold to cool for 30 seconds to several minutes to harden the PLA.
- Deforming and subsequent processing: After cooling, the finished product is taken out and further processed such as deburring or polishing as required.
Special attention must be paid to mold design, injection speed and pressure during the injection process to avoid material deterioration and product failure.
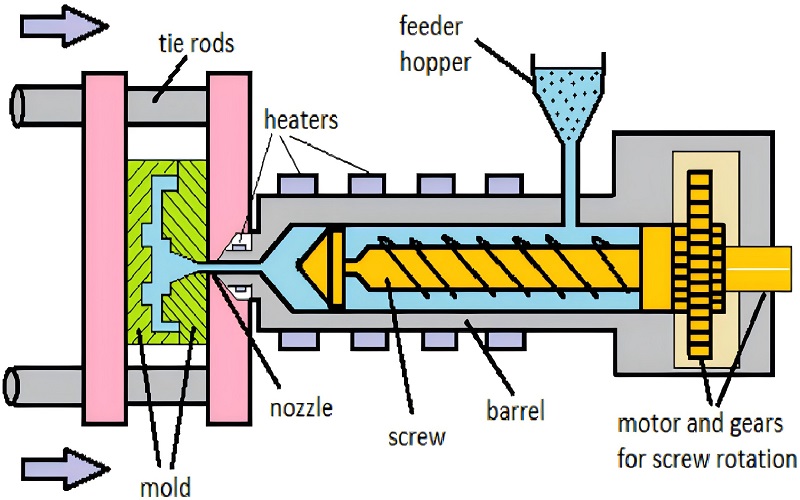
Types of Molds Used for Shaping PLA Products
Different molds are used to cast PLA products, but each has its advantages and disadvantages.
Cold Runner Mold
Advantages: Simple design and low initial cost.
Disadvantages: Creates more waste and is inefficient for mass production.
Hot Runner Mold
Advantages: Keeps the plastic in a molten state within the runner system, which reduces material waste and shortens cycle times by eliminating the need to reheat the plastic in the runners.
Disadvantages: Higher initial setup costs and more complex maintenance.
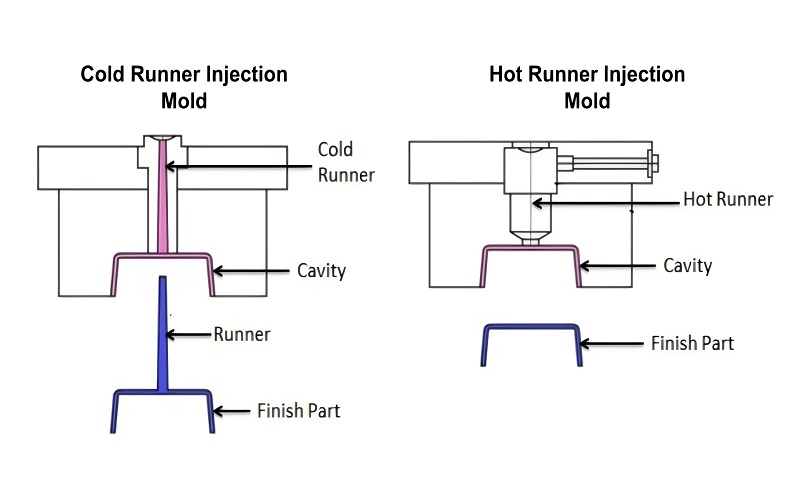
Challenges And Solution Strategy With PLA Resins in Injection Molding
Polylactic acid (PLA) materials pose heat resistant, brittleness and degradation problems for the injection-molding process. These problems may be addressed through:
1. Heat Resistance Improvement
Mold temperature: A mold temperature at 90-100°C facilitates the optimum conditions for PLA to achieve a semi crystalline structure and improve heat resistance.
Heat Resistant Additives: The incorporation of heat resistant additives can enhance the heat stability of the polymer material to properties at elevated temperatures.
2. Brittle Behavior Prevention
Cooling Rate: The cooling of the part in the injection molding process needs to maintain lower cooling rates which control the cooling of the polymer and minimize temperature change which leads to the polymer become brittle.
Mold Design: The optimized design in the cooling channel of the mold reduce heat and, therefore, brittle behavior in the part, to reducing internal stresses present in the part.
3. Hydrolysis & Degradation Prevention
Pre-drying: The PLA requires pre-drying considerations after 24 hrs at 60 °C to utilize less than 0.025% moisture. Pre-drying is critical to prevent hydrolysis and afterwards degradation of the polymer material.
Sealed Storage: PLA requires storage in sealed containers to prevent hydrolysis, hydrolysis is the presence of moisture to complicate material properties, and mechanical properties in the first instance.
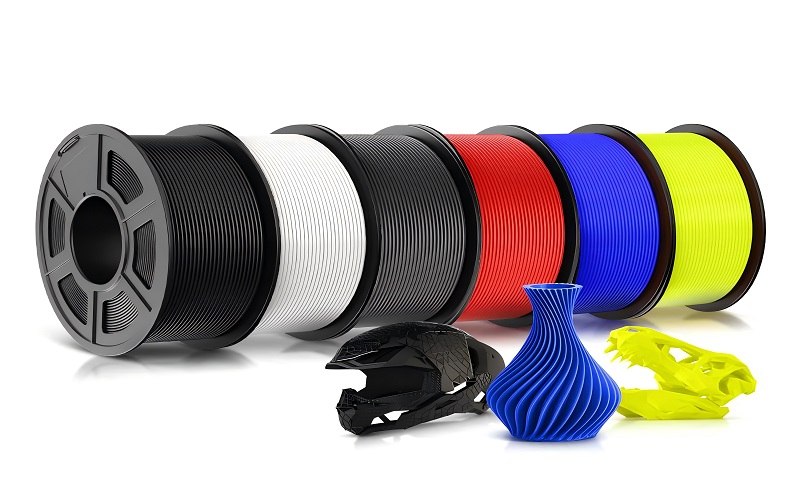
Conclusion
The perfection of PLA injection molding technology is important for the production of sustainable and high quality products. Understanding the properties of PLA and optimizing your processes can provide significant benefits.
Because PLA is very versatile, it is widely used in various fields such as food packaging and medical devices. Mastering these pressing technologies not only ensures product quality, but also supports sustainable development.
Get in touch with us and turn your innovative ideas into reality with this eco-friendly material.
FAQs
What does PLA Stand for, and Why is it Relevant to the Manufacturing Industry?
PLA stands for polylactic acid, a biodegradable and compostable bioplastic made from renewable resources such as corn starch and sugarcane. It is relevant to the manufacturing industry due to its eco-friendly properties, offering a sustainable alternative to traditional petroleum-based plastics.
What are the Main Benefits of Using Hotrunner Systems When Injecting PLA?
Hot runner systems allow manufacturers to process PLA more effectively with reduced waste in most cases over other systems. Hot runner systems allow manufacturers to keep a constant temperature within the hot runner and the mold, minimizing degradation of the polymer, which allows better flow of the PLA resin to create parts with better quality.
How does Having Control of the Mold Temperature Affect PLA Injection Molding?
Having control over the temperature of the mold is critical to obtaining optimal performance from PLA materials. Maintaining control of the temperature of the mold allows the correct flow of the resin at the optimal solidification and dimensional accuracy rates, thereby achieving glossy, high-quality material.
What is the Need for A Good Ventilation System in PLA Injection Molding?
A well-thought-out ventilation system within the mold cavity will aid in venting defects during injection runs with PLA, allowing trapped air pockets or incomplete fills, etc. Also, allowing air to vent means that at least the fill of the mold is more uniform and/or complete.