Plastic assemblies are essential in creating many everyday products, from smartphones to automotive parts. They involve bringing together multiple plastic components to form a cohesive, functional unit.
Understanding plastic assemblies helps in recognizing their role in product durability and performance. This article explores various types of plastic assemblies, assembly techniques, surface finishes, and key considerations for ensuring high-quality results.
Understanding Plastic Assemblies
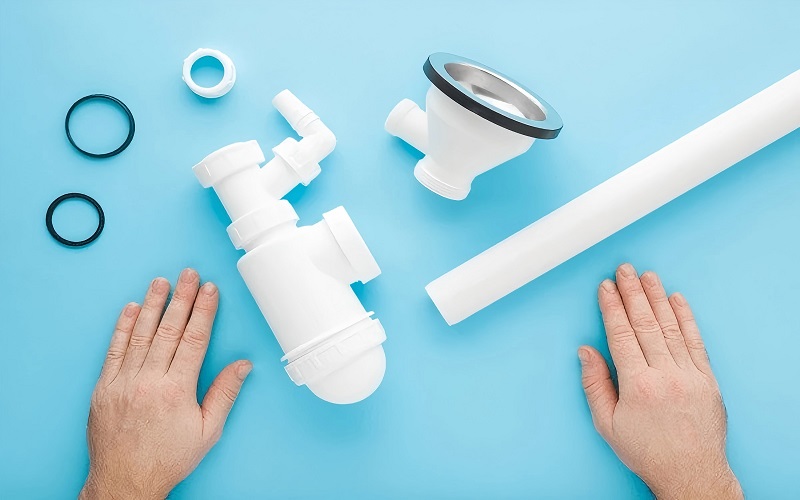
Plastic assemblies are crucial in the manufacturing process, bringing together multiple components, including internal parts, to form a cohesive product through the molding process. Whether it’s a smartphone case or a complex automotive part, these assembled components ensure that each piece fits perfectly and functions as intended from start to end.
The design phase plays a pivotal role in this process, ensuring that all components, including internal parts, are precisely crafted during the molding process to fit together seamlessly during assembly, avoiding issues later in production.
Plastic assemblies are the backbone of many everyday products, from household items to high-tech gadgets. Understanding the fundamentals of plastic assemblies helps in appreciating the complexities involved in creating high-quality, durable products that meet consumer expectations and regulatory standards through to the end of the production cycle.
Types of Plastic Assemblies
Plastic assemblies can utilize various fastening techniques, each with unique applications and benefits. Snap fits are economical and efficient, involving features molded into plastic parts that allow for quick assembly without additional hardware. This method is particularly useful in mass production where speed and cost-efficiency are critical.
Press fits, on the other hand, require elastic deformation for assembly, commonly seen when inserting a dowel pin into a slightly smaller hole. Threaded fasteners, designed specifically for plastics, feature unique geometries that reduce stress and enhance pull-out strength.
Each of these techniques offers distinct advantages, making them suitable for different types of plastic products and machining assembly processes.
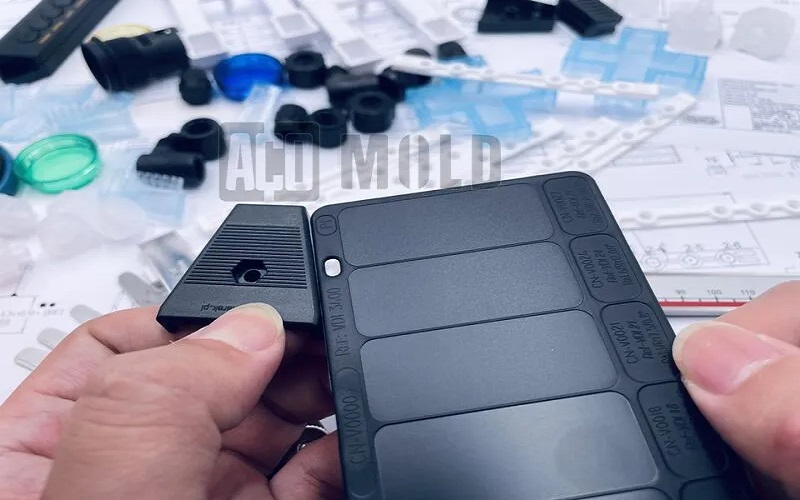
Assembly Techniques for Plastic Parts
Effective assembly methods for plastic parts are essential for enhancing product durability and functionality. Advanced techniques like ultrasonic welding and snap-fit assembly can simplify the joining process.
Ultrasonic welding, also known as fusion bonding, involves heating the edges of plastic parts and applying pressure to meld them together as they cool. This method is particularly effective for creating strong, durable bonds without the need for additional materials.
Adhesives and tapes are also common methods for assembling plastic parts, but they require careful selection to ensure compatibility with the materials used. Solvent welding, another technique, fuses plastic parts by applying a solvent and pressing them together until the solvent evaporates. However, this method carries a risk of stress cracking and requires precise handling.
Utilizing the right assembly techniques can significantly impact the quality and performance of the finished product. Understanding each method’s strengths and limitations allows manufacturers to select the most appropriate technique, ensuring high-quality and reliable plastic assemblies.
Surface Finishes for Plastic Assemblies
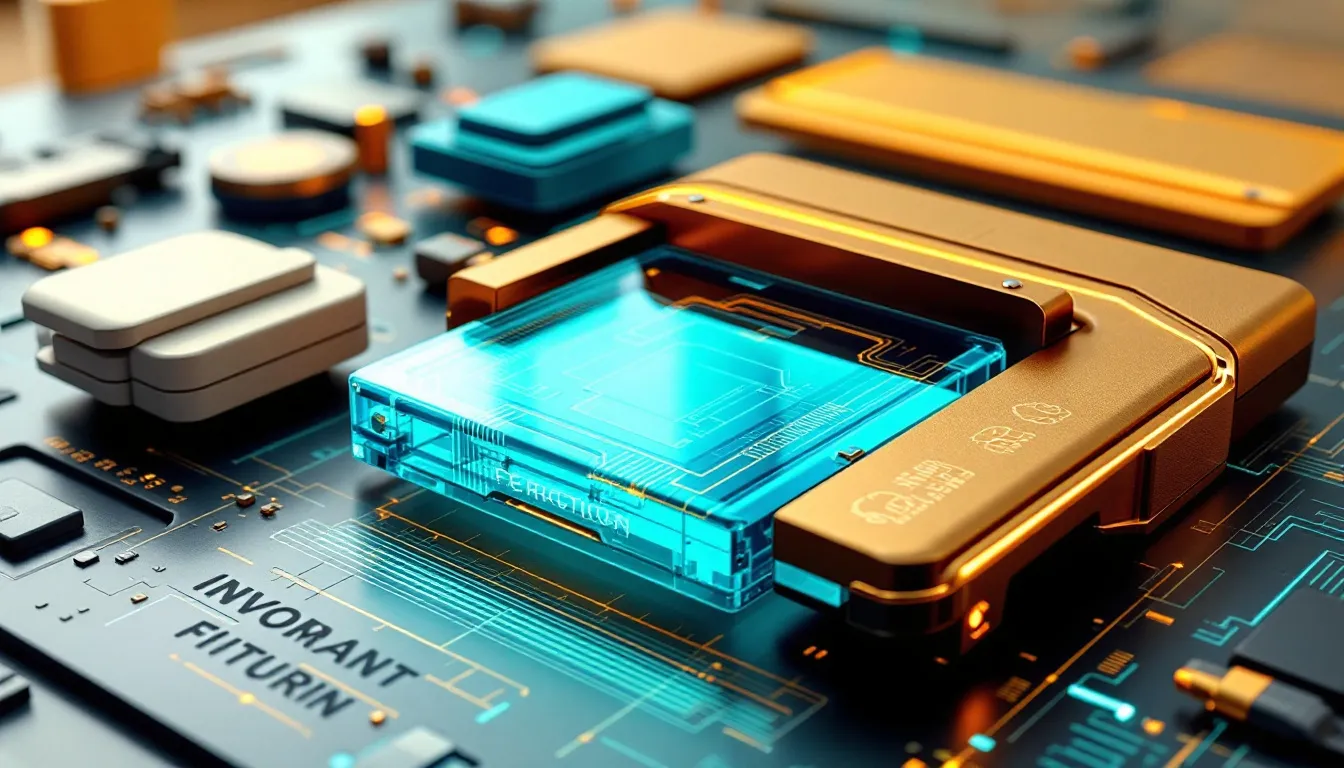
Surface finishes play a crucial role in the appeal and functionality of plastic assemblies. A well-applied surface finish can significantly enhance the aesthetic appeal of a product, influencing consumer purchasing decisions. Surface finishes improve the tactile feel and visual quality of plastic products, making them more attractive and user-friendly.
The choice of surface finish should be considered early in the metal mold-making finishing process to create shape the final product.
There are several types of plastic finishes, each with its unique properties and applications:
- High gloss finishes, which offer a shiny and reflective surface
- Matte finishes, which provide a non-reflective and smooth surface
- Textured finishes, which add a tactile quality and can enhance grip
Each type of finish offers distinct advantages and can be tailored to meet specific product requirements. Understanding these options can help in selecting the most suitable plastic finishing for your plastic assemblies.
High Gloss Finishes
High gloss finishes are achieved through processes like buffing with fine diamond powder suspended in oil using a rotary tool. This method creates a polished, reflective surface that enhances the visual appeal of plastic products. High gloss finishes are particularly desirable for consumer-facing products where appearance is paramount.
These finishes are commonly used in products intended for visible applications, such as electronics casings and automotive interiors. The high gloss surface not only looks attractive but also provides a smoother finish that can be easier to clean and maintain, especially when using coated polish paint. Finishing touches can enhance the overall appeal of these products.
High gloss finishes help products achieve stand out in the market and appeal to discerning customers.
Matte Finishes
Matte finishes are typically created using fine abrasives that produce a non-reflective surface. This type of finish is designed to reduce glare and enhance the appearance of products.
The smooth and even texture of matte finishes contributes to a sleek, sophisticated look that is often preferred in high-end consumer goods, rather than a dull one.
Matte finishes are ideal for products where a subtle, elegant appearance is desired. They are commonly used in home appliances, automotive interiors, and consumer electronics. The non-reflective nature of matte finishes also helps to mask small surface imperfections, making them a practical choice for a wide range of applications.
Textured Finishes
Textured finishes can be created using techniques such as sandblasting or chemical etching. These finishes are not only aesthetically pleasing but also functional. They improve grip, making products easier and safer to handle. Textured finishes are particularly useful for products that require a secure grip, such as hand tools and medical devices.
In addition to improving grip, textured finishes effectively hide surface imperfections and blemishes. This makes them an excellent choice for products that are frequently handled or exposed to harsh conditions. Choosing the right textured finish enhances both the appearance and functionality of plastic assemblies.
Enhancing Functionality with Plastic Finishing Techniques
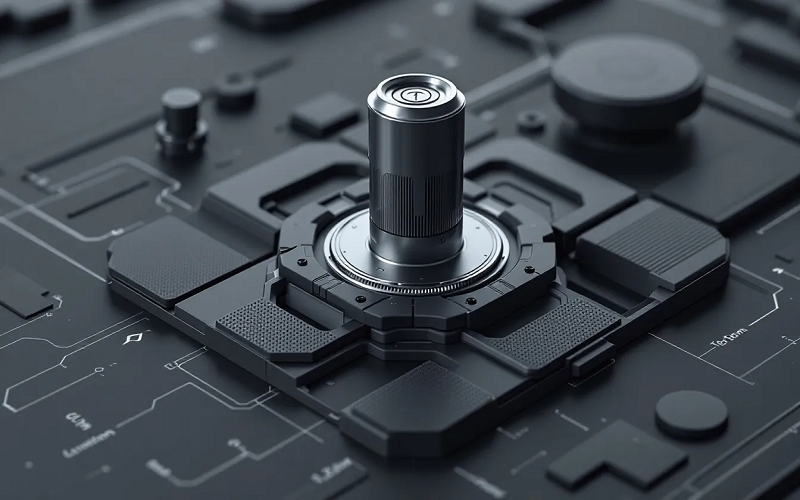
Surface finishes do more than just enhance the appearance of plastic assemblies; they also improve functionality. Textured finishes, for example, provide better grip, making products easier and safer to handle. This is particularly important for products like tools and medical devices, where a secure grip is essential.
A smoother surface finish can reduce friction, leading to improved efficiency in mechanical applications. Additionally, certain finishes can conceal fingerprints and manufacturing marks, maintaining a clean and professional appearance along the line, showcasing the ability to enhance overall quality.
Carefully selecting the appropriate surface finish ensures suited surfaces products that look good and perform exceptionally well in their intended applications.
Quality Control in Plastic Assemblies
Quality control is a critical aspect of plastic manufacturing, ensuring that the final products adhere to established quality standards. Implementing strict quality control measures helps in identifying defects early, thereby minimizing waste and optimizing the manufacturing process.
Techniques such as Statistical Process Control (SPC) are used to gather and analyze data on manufacturing processes, enabling the detection of variations that could compromise product quality.
Visual inspections are also crucial in quality control, helping to spot surface defects like scratches and cracks that might affect the aesthetic and functional aspects of the plastic products. Common quality issues in plastic manufacturing include warping, sink marks, and flashing, each requiring specific prevention and correction strategies.
Addressing these issues helps manufacturers ensure their plastic assemblies meet high standards of quality and reliability, which is essential to support the manufacture of products and solutions that satisfy customer expectations.
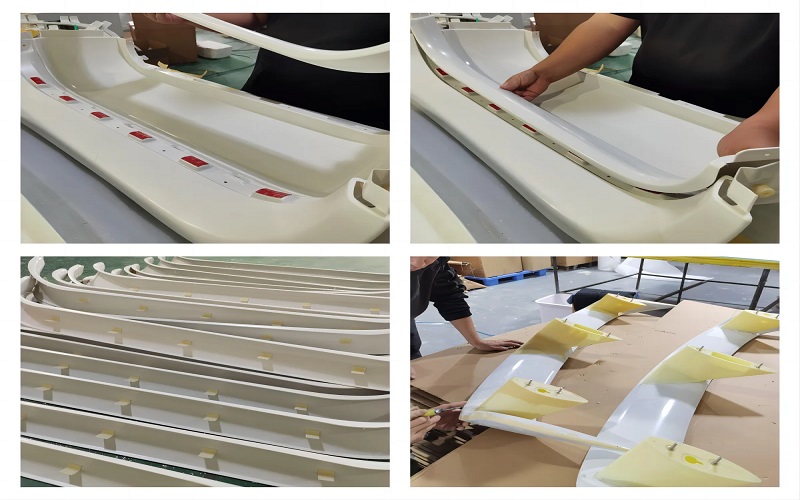
Cost Considerations in Plastic Assembly Processes
Cost considerations are a vital part of the plastic assembly process. Mechanical fasteners, for example, may not be ideal for small assemblies due to the need for creating holes, which can become weak points. Adhesive bonding, on the other hand, provides distinct benefits over other methods, including efficiency, despite requiring time for setting and curing.
Material costs vary based on resin type, quality, and market conditions, impacting overall expenses. The complexity of mold design also directly influences both production costs and the time required for manufacturing.
Considering the total cost of ownership and evaluating factors like mold material and production volume helps manufacturers make better financial decisions beyond simple price comparisons.
Industry Applications of Plastic Assemblies
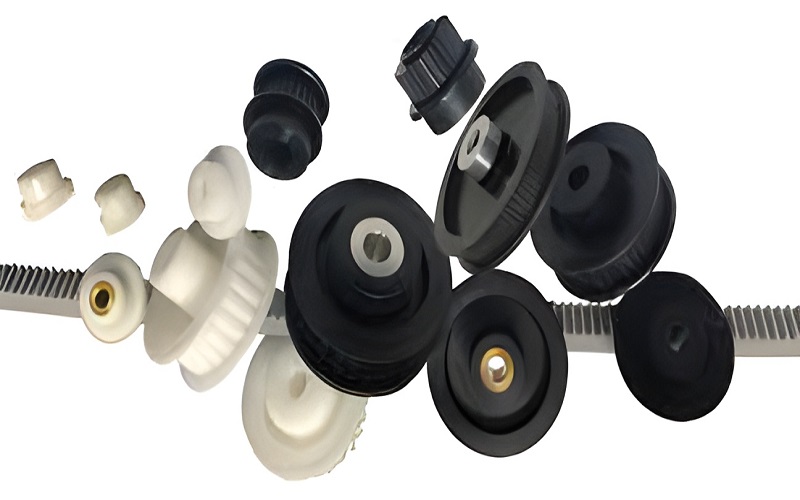
Plastic assemblies are used extensively across various industries, leveraging their versatility, durability, and aesthetic appeal. In the automotive sector, plastic assemblies are used for components like bumpers and dashboard parts, benefiting from reduced weight and improved fuel efficiency. The electronics industry relies on plastic assemblies for producing parts such as casings for telecommunication devices and computer equipment.
Consumer goods, ranging from kitchen appliances to toys, also utilize plastic assemblies to enhance functionality and design flexibility. The medical field employs plastic assemblies for devices like test swabs and prosthetics, requiring strict compliance with safety, quality standards, and technology.
Packaging applications in the food and beverage industry rely on plastic assemblies for containers and utensils, ensuring safety and sanitation during food transport. Each of these applications demonstrates the critical role of plastic assemblies in modern manufacturing.
Choosing the Right Partner for Your Plastic Finishing Services and Assembly Needs
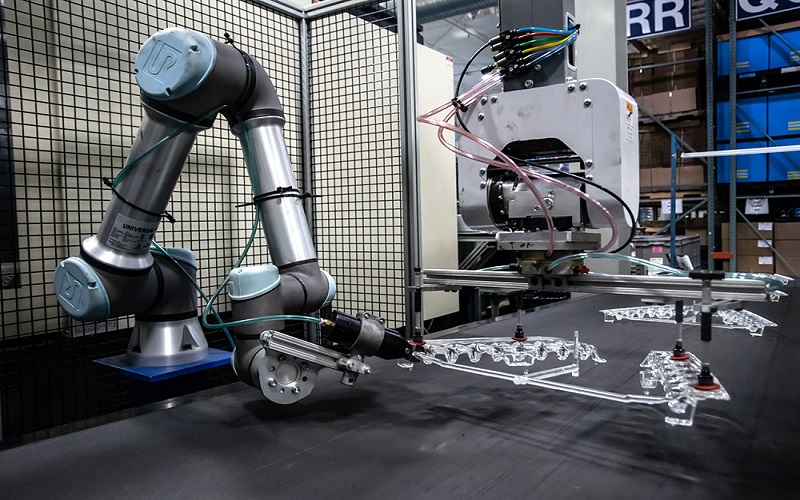
Selecting the right partner for your plastic assembly projects is crucial for success. A trusted partner brings in-depth industry knowledge and specialized expertise in the materials relevant to your project. Evaluating the design and engineering team’s experience with similar projects can indicate their capability in handling your specific requirements.
A reliable partner will also comply with industry standards and certifications, ensuring adherence to quality and safety regulations. Partnering with injection molding that offers assembly services can streamline production, resulting in improved efficiency and cost-effectiveness.
Choosing the right partner ensures that your plastic assemblies meet high standards of quality and performance, especially when utilizing plastic injection molding.
Summary
Throughout this guide, we have explored the multifaceted world of plastic assemblies, from understanding their types and techniques to the importance of surface finishes.
The choice of assembly methods and surface finishes significantly impacts the functionality, appearance, and cost-efficiency of the final product. Quality control measures ensure that plastic assemblies meet stringent standards, while cost considerations guide financial decisions in the manufacturing process.
In conclusion, plastic assemblies play a vital role in various industries, offering enhanced functionality and design flexibility. By selecting the right techniques, finishes, and partners, manufacturers can create high-quality products that meet consumer expectations and stand out in the market.
The future of plastic assemblies looks promising, with continuous advancements in technology and materials driving innovation and excellence.
Frequently Asked Questions
What are the common types of plastic assemblies?
The common types of plastic assemblies are snap fits, press fits, and threaded fasteners, each providing distinct advantages for various applications.
How do high gloss finishes enhance plastic products?
High gloss finishes significantly enhance the visual appeal of plastic products by providing a polished, reflective surface, thereby making them more attractive for consumers. This not only elevates aesthetics but also implies a higher quality perception.
What are the benefits of matte finishes?
Matte finishes significantly reduce glare and create a sophisticated, non-reflective surface, enhancing the overall appearance of products, particularly in high-end consumer markets. This quality makes matte finishes a preferred choice for achieving a more elegant and refined look.
Why is quality control important in plastic manufacturing?
Quality control is crucial in plastic manufacturing as it guarantees that products adhere to quality standards, allowing for early detection of defects and reduction of waste. This ultimately enhances product reliability and customer satisfaction.
How can manufacturers reduce costs in plastic assembly processes?
Manufacturers can effectively reduce costs in plastic assembly processes by choosing efficient assembly methods and optimizing mold designs while considering the total cost of ownership. This approach ensures long-term savings beyond initial expenditures.