Introduction
CNC plastic machining represents a critical technology in contemporary manufacturing which is capable of providing precise and intricate parts across a variety of industries.
Due to innovative manufacturing processes, CNC plastic machining is not only highly flexible but can also be finished to very exact specifications in high-technology applications such as medical devices, aerospace, automotive, and home appliances.
With continuing advancements in technology, CNC machining demonstrates its ability to effectively drive innovation, developing a vital role in providing complex parts to meet demand for manufacturers and perfecting product quality and competitiveness as it pertains to consumers.
This article discusses key advantages, applications, and best practices for CNC plastic machining.
Understanding CNC Machining
What is Plastic CNC Machining?
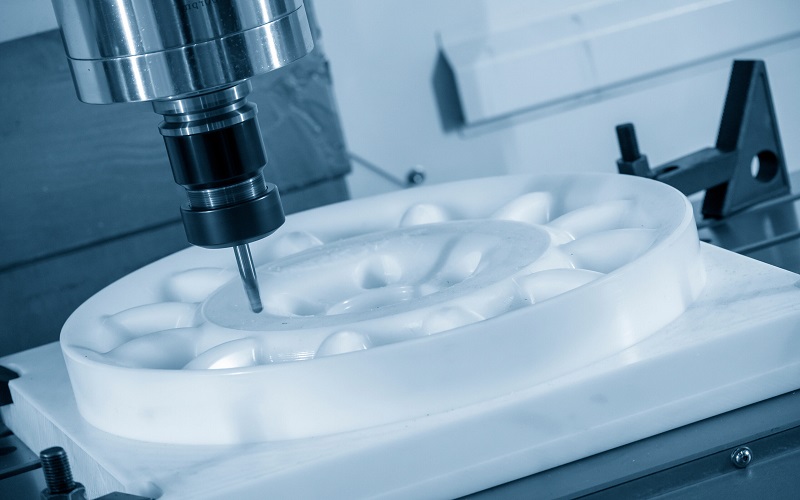
Plastic CNC machining is a manufacturing method that USES a computer-controlled machine to cut blocks or plastic sheets to make parts. Computer controlled design (cad) tells the machine how to cut, so it can make very precise parts.
Advantage of Plastic CNC Machining
CNC machining presents several powerful advantages to conventional manual machining processes:
- Greater precision and accuracy: CNC machines are capable of performing extremely fine and highly detailed machining processes with tolerances often as precise as 0.001″
- Faster production times: Automated processes allow for machines to run continually without employee oversight and lead time is reduced.
- Times production reliability: Reliability in production is increased because the same programming tool is used to develop each part, leaving reduced variability to the components produced.
- Versatile process capability: Within CNC machining, material and object structures can vary widely, accommodating metals, plastics, and composites.
Different Types of CNC Machining
Plastic CNC machining can be classified into various categories according to the processing method and application scenario, mainly including the following common types:
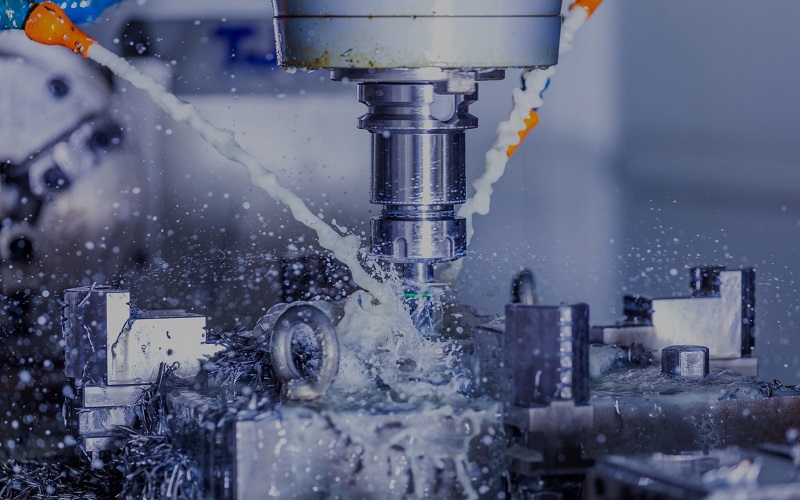
CNC milling: Involves the use of rotary cutters to remove material from the workpiece, ideal for producing complex shapes and intricate features.
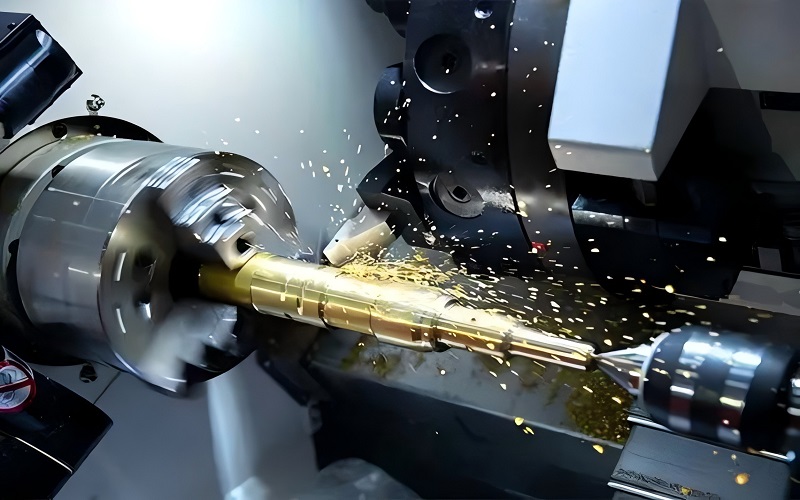
CNC turning: Focuses on creating cylindrical or round parts by rotating the workpiece while cutting material away. It’s commonly used for shafts, bushings, and other round components.
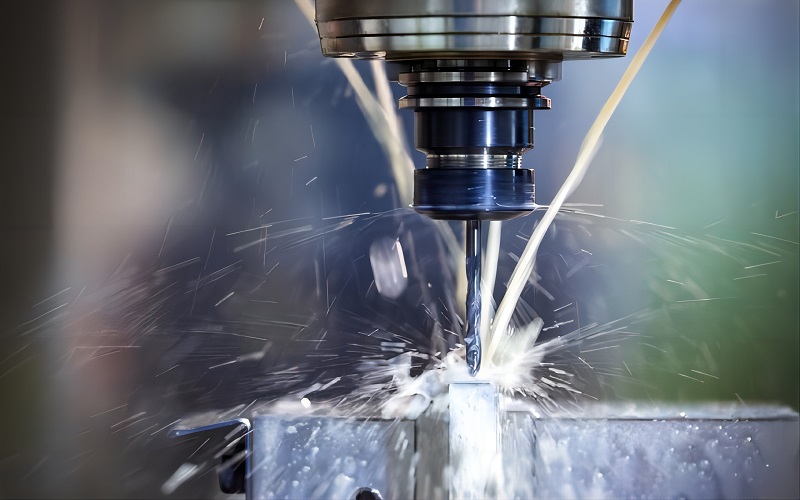
CNC drilling: Involves creating holes in the material with high accuracy. Drilling is often combined with other CNC processes to streamline production.
For plastic components, CNC milling and CNC turning are most frequently used due to their ability to produce parts with high precision and excellent surface finishes, especially when working with materials that have varying degrees of flexibility and hardness.
Industries’ Uses of Plastic CNC Machined Parts
Plastic CNC-machined parts can be used in different industries. Notable applications include:
- Medical industry
CNC-machined plastic parts are used in the medical field in the form of surgical instruments, implants and diagnostic equipment.
Their compatibility with PEEK materials makes them perfectly suitable for use in important medical applications.
- Food and beverage industry
Food-grade components for processing equipment are made from polymers such as teflon and uhmw for the food and beverage industry. These components are characterized by low friction, non-adhesion and wear resistance. They meet hygiene and safety requirements.
- Automotive and aerospace
CNC-machined plastic parts also benefit the automotive and aerospace industries, especially in applications requiring lightweight, high-strength and heat-resistant materials. Gears, bushings, structural parts, etc. are made from dellin and nylon and are usually used to reduce weight and improve fuel efficiency.
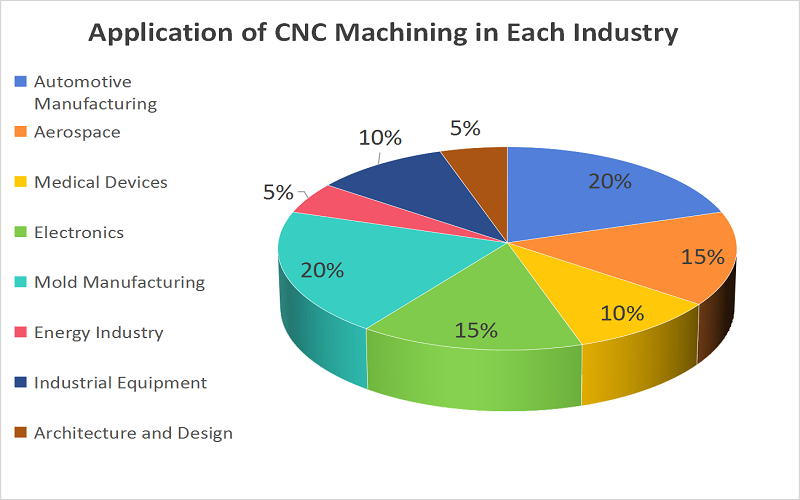
Types of Plastics Used in CNC Machining
When CNC machining plastic, it is important to choose the right material. Different thermoplastics have unique properties for different applications. Here are some commonly used plastic materials and their properties.
1. Polyamide
Nylon, also known as polyamide, is distinguished by its high strength, excellent flexibility and excellent wear resistance. It has excellent durability and is widely used in parts where durability is required, such as automotive parts, industrial gears and bearings.
2. Delrin (polyoxymethylene)
Delrin has excellent dimensional stability and is ideal for machining precision parts. Due to its low friction and wear resistance, it is widely used for mechanical parts such as gears, rollers and rings.
3. PEEK (polyether ketone)
PEEK is a high-performance plastic that resists high temperatures up to 260°C and chemicals. Its excellent biocompatibility allows it to be widely used in aeronautics, automotive, medical devices and even medical implants.
4. Teflon (PTFE)
PTFE is known for its non-stick, high temperature and chemical resistance. It is used in corrosive environments such as joints, seals and bearings or in low-friction areas. Mandatory.
5. UHMW (Ultra High Molecular Weight Polyethylene)
UHMW is known for its excellent impact and abrasion resistance. It is widely used in industrial applications that require high durability and impact resistance, such as conveyors and guides.
Knowledge of the characteristics of these plastics will allow you to choose the best material according to the needs of your project, guaranteeing the best results in terms of durability, performance and product quality.
The Key to Successful CNC Machining
To achieve good results in machining plastic CNC , manufacturers need to understand several important tips to ensure that the whole process runs smoothly and that the products are of high quality. Here are some key points:
1. Choosing the right material
Choosing the right material is the first step to a successful processing. For example, nylon is relatively cheap and suitable for prototyping, while PEEK is resistant to high temperatures and chemicals andis suitable for use in harsh environments.
In general, the material should be chosen according to specific needs, such as the required strength, the temperature it can withstand and whether it is exposed to chemicals.
2. Selection and maintenance of cutting tools
The quality of the tools has a direct impact on the efficiency of plastic machining. We recommend the use of carbide or diamond-coated tools.
This tool not only has a long service life but is also a cleaning tool. Keeping the tool sharp and regular maintenance help prevent thermal deformation, cracking and plastic deformation.
3. Optimization of cutting speed and feed
When machining plastic, the temperature tends to increase. If the cutting speed is too high or the feed quantity is too high, the plastic can bend or melt.
It is therefore necessary to reduce cutting speed and feeding speed to avoid these problems. At the same time, coolants and fans can be used to reduce the temperature and maintain the exact dimensions of the machined parts.
4. Control of ambient temperature and humidity
Plastics are sensitive to ambient temperature and humidity. Significant changes in temperature and humidity can affect the accuracy of parts and material properties.
Thus, especially when machining high-precision parts, machining consistency can be improved by maintaining stable temperature and humidity in the workshop environment.
By following these tips, manufacturers can have better control over CNC plastic machining and ensure high-quality products.
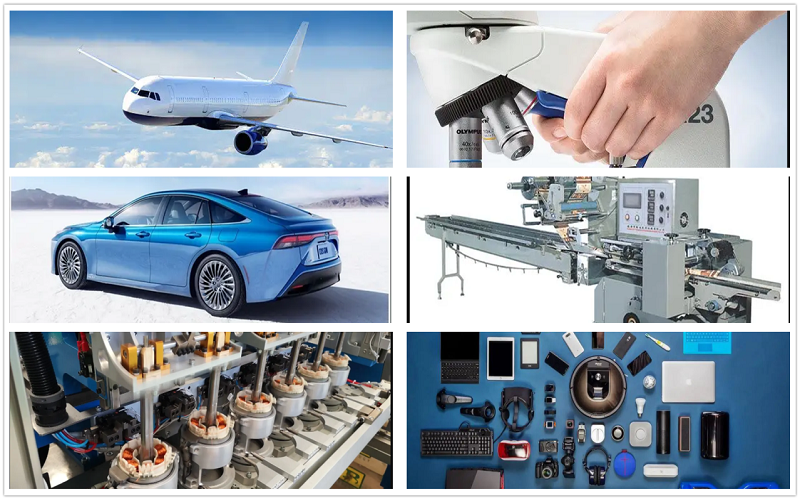
Overcoming Challenges in Plastic CNC Machining
CNC machining of plastics presents particular challenges compared to metal processing. The most common problem is cutting too fast or choosing the wrong tool, which can lead to cracks or chips in the material. To avoid these problems, manufacturers can take the following steps:
Avoid using overly complicated tools. The use of tools with complex shapes can easily cause problems due to excessive pressure on plastics.
Use a coolant or fan to reduce the heat generated during processing and decrease the risk of heat deformation of the material.
Use the optimal slow feeding speed to make the cut smoother and avoid damaging the plastic by removing a large amount of material at once.
These methods help manufacturers reduce machining errors and make the whole process more agile and efficient.
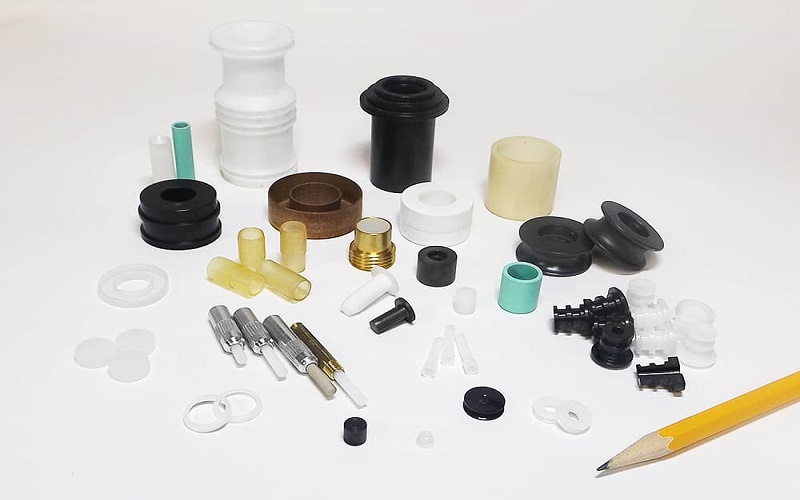
How to Improve Quality Through Surface Treatment Technology?
Surface finish is an important part of plastic CNC machining, especially in industries with high appearance requirements.
- Annealing: Heating the plastic part helps reduce the internal stresses that build up during machining, which can improve the fit and dimensional stability of the part. This is particularly beneficial for higher-performance plastics like PEEK.
- Sandblasting: If a textured surface is desired, sandblasting can create a uniform matte finish that enhances the visual appeal of the part.
- Polishing: For components needing a high gloss finish and to remove surface imperfections, polishing can clean the surface and improve clarity, especially for transparent plastics like acrylic.
With the right surface finishing techniques, plastic parts can look better and perform more effectively, meeting the strict requirements of industries such as medical devices and consumer electronics.
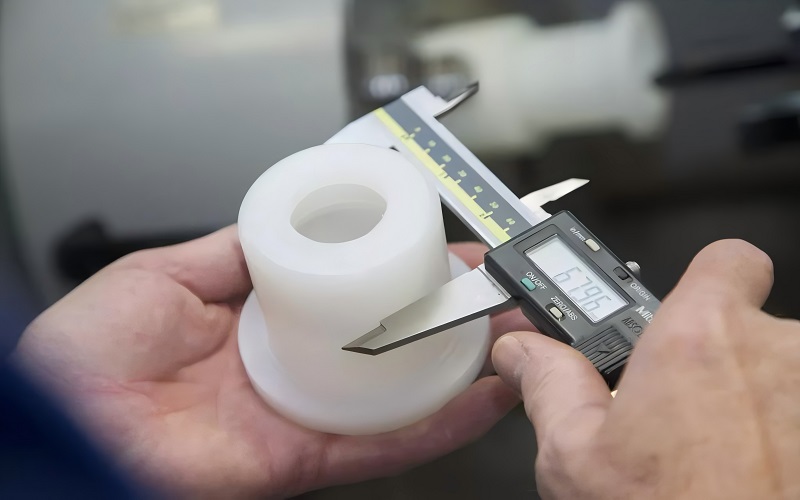
Conclusion
CNC plastic machining, which uses a wide range of plastic materials to provide precise, affordable solutions for various industries, is a major component of modern production. CNC plastic machining plays a role in producing high-quality products.
We are committed to providing state-of-the-art CNC machining and precision part manufacture to meet the needs of our clients that require unique manufacturing. Our technical staff can ensure outstanding quality and consistency in every element since they have extensive experience in both series production and prototyping.
Please feel free to consult us on any topic pertaining to CNC machining!